Chemical resistant 3d printer filament
Chemical-resistant materials: A beginner's guide
Adam Kohut23 July 2020
Applications
Chemical-resistant materials are vital for many 3D printing applications. Corrosive chemicals can’t permeate their surface or cause degradation, making them ideal for industrial or end-use parts. There are several different chemical-resistant materials to choose from, each with specific benefits.
Why is chemical resistance important?
“Chemical resistance” means that materials can fulfil their function, even in harsh working environments. Chemical-resistant materials don’t require surface treatment; they are able to withstand exposure to chemicals such as bases, solvents, and acids.
Without chemical-resistance, a material may erode, soften, or become misshapen. This is due to the chemical’s molecules diffusing within the material and pushing the polymer chains apart. When this happens, it reduces functionality, and may damage other surrounding parts.
Common uses of chemical-resistant materials
Chemical-resistant materials play an important role in packaging applications, particularly in the packaging of cleaning agents, reagents, and other chemicals. They’re also useful for manufacturing tooling. During use, jigs and fixtures are often exposed to chemicals (liquid, gas or solid). Chemical resistance ensures they don’t degrade over time.
Some automotive parts are created using chemical-resistant materials
Many industries require end-use parts to be chemically resistant. Automotive parts, for example, are often exposed to oil or chemicals used for cleaning or maintenance. When created with chemical-resistant material, exposure to even harsh chemicals isn’t a problem.
What else should you know?
The main factors that influence a polymer’s chemical resistance
A material’s chemical resistance is impacted by several different factors. These include:
the molecular structure of the polymer
the time of exposure to a chemical
the temperature at the time of exposure
the nature of the chemical
the stress applied to the material
Chemical resistance depends on the application
Materials are usually only resistant to certain types of chemical. For example, Nylon isn’t adversely affected by acetone, but can be damaged by water. Conversely, PETG isn’t affected by water, but acetone will degrade it. Every material has different properties, and it’s vital to choose the right one for the job.
Materials with good chemical resistance
Several materials have excellent chemical resistance, such as PP, PVDF, and Nylon. PETG is unaffected by water-based chemicals, and (like CPE and CPE+) has good resistance against common chemicals such as alcohol and weak acids.
PP | Most chemicals (except acetone and fluorinated/chlorinated chemicals) |
PET(g) / CPE(+) | Alcohols (EtOH, IPA), water, acids and bases |
Nylon | IPA, Solvents (acetone, glycerol) |
ABS | Water, some acids and bases, alcohols |
TPU | Water (salts), glycol and fuels |
PC | Water and alcohols |
PLA / Tough PLA | Water |
PVDF | Solvents (chlorinated, aliphatic, aromatic), strong acids, weak bases, halogens, strong oxidants |
The above table refers to general characteristics of the listed material. Chemical resistance strongly depends on the design and formulation of a 3D printed part. A fragile part, for example, will not last long against chemical liquids as a massive print.
Things to note when using chemical-resistant materials
It’s vital to consider temperature, as most diffusion processes are temperature dependent
Amorphous thermoplastic polymers, when exposed to chemicals, may crack. This can lead to part failure
When choosing a material, think about the concentration of the chemicals, and the mechanical load
Our chemical-resistant material partners
Arkema
Arkema FluorX™ is a tough, semi-crystalline fluoropolymer made from Arkema’s Kynar® PVDF. It is formulated for printability, and is a great option for parts subjected to demanding conditions, such as solvents, acids, fire, and UV radiation.
"Kynar® PVDF is the material of choice for many harsh chemical environments,” Steven Serpe, Market Manager, Specialty Powders and 3D Printing at Arkema, said. "Fluoropolymers are well known for chemical resistance, but ability of Kynar® PVDF to be easily processed via many methods including 3D printing makes it stand out in the chemical processing industry for applications like piping, lining, pumps, and other fluid handling equipment."
BASF
PP GF30 contains special glass fibers that are designed for filament making and 3D printing. This will ensure the printed objects are functionally working under certain temperature and mechanical loads.
"Chemical resistance is the degree to which your printed part retains its mechanical properties and shape when it comes in contact with chemicals or solvents. For example, PAHT CF15 has chemical resistance properties against lubricants, whilst ASA shows resistance properties against cleaning agents and Ultrafuse 316L against all organic solvents among others,” Roger Sijlbing, Head of Sales Additive Extrusion Solutions at BASF, said. “In many cases the chemical resistance is not only a question of material & chemical combination but includes rather application temperatures and dwell time. BASF 3D Forward AM is working on an overview for end-users to assess the chemical resistance of our materials for FFF printing. Currently our chemical experts provide information concerning the chemical resistance of our products on request.”
DSM
Arnitel® ID 2045 is a highly flexible TPC (thermoplastic copolyester) that can be used in a broad range of applications. It has better UV and chemical resistance compared to others of its type, such as TPU (thermoplastic urethane).
Solvay
Solef® PVDF AM Filament is a tailor-made fluorinated semi-crystalline additive manufacturing material for best printing results of parts that need chemical resistance, high thermal and environmental stability, and good mechanical properties.
"Solef(R) PVDF AM Filament is not only resistant to a broad range of harsh chemicals such as inorganic and organic acids, aliphatic and aromatic hydrocarbons, crude oil, fuels and alcohols, and ethers, but also intrinsically fire retardant, UV and temperature resistant up to 130°C,” Sophia Song, Business Incubation - Additive Manufacturing at Solvay, said. “This unique combination of properties with the ease of printing the material enables the access to a broad range of applications."
Interested in learning more about Ultimaker’s temperature-resistant material partners? Visit the chemical-resistant materials page on the Ultimaker Marketplace.
You can also explore Ultimaker’s range of 3D printers that are compatible with chemical-resistant materials.
Discover Ultimaker 3D printers
Chemical resistant 3D printer filaments
The more we delve into the world of filaments and the possibility of their use in various industries and sectors, the more often we think about chemical "durability". The field of research in this aspect is not yet developed - and some experiments are burdened with a long term of feasibility. What does it mean?
Author: Tomasz Garniec
Chemical resistance is a long-term change of the working environment from neutral to „harmful”. Consequently, there are many disputes over the interpretation of the meaning of the word „long-term”. Is a few or a dozen hours enough – should we conduct multi-week or even multi-year tests? For example, one of the questions with no clear answer is how long the operation of, for example, the water environment will affect the printouts – bearing in mind and knowing the tendency of filaments to be hygroscopic. But that’s not what I’m going to do today. In a short publication I will describe those filaments that show „resistance” to everything – I meaning – chemicals. I will also try to explain if there is a difference between the filament and the printout that was made of it.
Chemical resistant 3D filament
Some of You may ask why filaments can behave differently than prints. Explanation: in the printing process, they are subjected to high temperature and pressure – which directly changes their internal structure and some properties. Based on the research, it can be clearly said that the treatment of the printing process affects the primary filament, which has a lower resistance than the print made from it.
Among the many aspects of chemical resistance, the one responsible for resisting the action of alcohols and acids is the key. These are the two elements that occur most frequently in the environment and which determine the use and application of a given filament and printout. “Superfilaments” are those which do not change their dimensions, consistency and properties in both alcoholic and acidic environments. Such filaments are PP, PPS (also PPSU), PAEK (PEEK, PEKK) and PEI.
3D Printing in Polypropylene
The „easiest” to print from the above-mentioned is PP – i.e. Polypropylene. However, it requires the use of industrial solutions common in highly professional printers and personalized adhesives. It is a filament characterized by high flexibility and durability, and at the same time even a long-term change of the working environment does not affect its chemical resistance and dimensions. Polypropylene is the most common material in the production of bottles or other tanks. More and more often it is used in the production of orthoses, laboratory containers, but also elements exposed to long-term impact, e.g. a changing of natural environment and used in the production of car parts such as bumpers or covers. As it is neutral in contact with food, it is widely used in the food industry.
Another interesting filament solution is PPS or PPSU – i.e. polyphenylene sulfide. It is a well-known and increasingly used alternative to PEEK, which has really good adhesive properties between the layers, which affects its strength in each axis. The offer of Omni3D includes, for example, Thermec Zed, which represents this group of filaments, and which does not dissolve in any substance at temperatures below 200°C. It is used in the production of tanks in which „aggressive” substances are deposited. As a much cheaper alternative to PEEK, we find it in the automotive industry (brake fluid reservoir), in automation as part of production lines, but also more and more often used in the electronics industry, e. g. as the so-called „Heatbreak”. Unlike many filaments, PPS (PPSU) prints are characterized by a very low moisture absorption.
3D printout from ThermecZED on Factory 2.0
3D printing with PEEK – mechanical, chemical and temperature resistance
The PAEK family is a group of industrial filaments with increased strength parameters. So called Polyaryletherketone. PEEK belongs to this family! One of the most durable filaments in use today and the desire of many industries. Its chemical name is PoliEtherEtherKeton. In addition to excellent mechanical properties, it is flame-retardant and extremely resistant to chemical agents. The disadvantages of PEEK are its printing conditions, in most cases we need to use high-temperature post-process treatment, and rapid cooling during printing process, which significantly affects the difference in strength in different axes (in particular, the adhesiveness between layers). An alternative to PEEK is belonging to PAEK – PEKK – i. e. PoliEtherKetonKeton. Printouts from this filament are characterized by a similar, although lower strength than PEEK, but do not require costly and long-term post-process thermal processing (heating in a high-temperature oven) and are much easier to print. Which does not mean that everyone can print them – the indispensable elements of its processing are high extrusion temperature and a completely heated chamber. The Omni3D’s – PEKK-A that we can find in the offer is an excellent example.
The last group are filaments from the PEI family – i.e. polyetherimides. Extraordinary filaments, often referred to as those that change the rules of the game and bring 3D printing to the next level. They are characterized not only by very high chemical resistance, even at much higher temperatures than 200°C, but also abrasion resistance and non-flammability. For filaments from this group, the areas of application are the widest. From medicine, automotive to the aerospace industry. Acids or alcohols for Ultemu (PEI) prints are „neutral” or almost neutral.
To sum up – if chemical resistance is the most important for You – You need to consider in what environment and how long Your printout will be affected by. You do not operate at high temperature, but the interaction of acids and alcohols is an important element – choose PP – low cost, relatively easy printing will ensure full satisfaction. If You are looking for a filament that will be very durable and hard – Your choice should be PPS (PPSU) – for example Thermec Zed (see case-study Volkswagen with ThermecZed).
If You want more and costs don’t matter, one of from the PAEK or PEI families should be Your choice. Chemical resistance, coupled with other properties, is what can take Your project to the next level.
Want to know more about 3D printing?
Contact us and discover the possibilities of industrial 3D printers
Contact:
LinkedIn: Tomasz Garniec
m. +48 886 618 588
e-mail: [email protected]
TPU plastic for 3D printer eSUN eTPU-95A black (1.
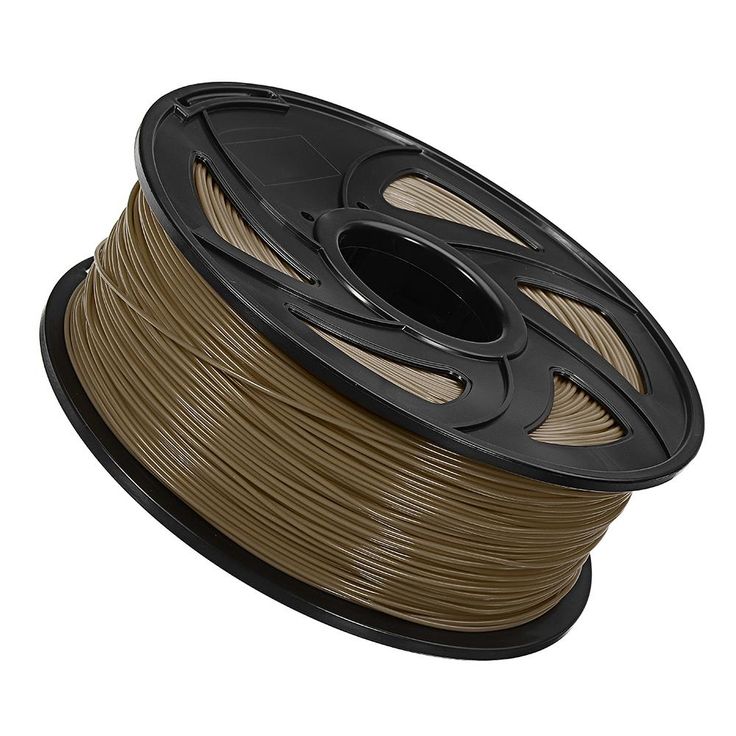
TPU plastic for 3D printer eSUN eTPU-95A black (1.75 mm) 1 kg.
ESUN eTPU-95A (chemical name: thermoplastic polyurethane) is a chemical resistant elastic 3D printer filament that can be widely used in industries that require the combination of rubber and plastic properties.
Thread diameter: 1.75 mm
Colour: black
Weight: 1 kg.
Goods receipt notice
SKU: eTPU-95A175B1 Categories: ESUN, TPU, Flex Tags: esun, eTPU-95A, TPU, 3D printer filament, 3D printer plastic, 3D printer filament, Black
- Description
- Details
- Origin of goods
- Reviews (0)
Description
Thread diameter: 1. 75 mm
Colour: black
Weight: 1 kg.
ESUN eTPU-95A (chemical name: thermoplastic polyurethane) is a chemical resistant elastic 3D printer filament that can be widely used in industries that require the combination of rubber and plastic properties.
eTPU-95A is a soft, flexible plastic that retains its original shape and shape, providing exceptional wear resistance, high impact strength, and good corrosion resistance to many industrial oils and chemicals. In addition, it is resistant to UV radiation, which allows it to be used in functional models. Finished products have a pleasant to the touch surface.
⚠ Attention! Engineering layer ic. Not suitable for Bowden type extruders. Printing stability on home printers is not guaranteed!
Key benefits of eSUN plastic
eTPU-95A- Flexible and soft
- Strong and durable
- High flexibility
- High strength
- High impact resistance
Applications:
- functional prototypes
- automotive parts and components
- medical devices and accessories
- protective covers
- shoe industry
Material Properties
eSUN eTPU-95A3D Printable Plastic | eSUN eTPU-95A |
Density (g/cm3) | 1.![]() |
Thermal distortion temperature (℃,0.45MPa) | – |
Melt flow index (g/10min) | 1.2(190℃/2.16kg) |
Tensile strength (MPa) | 35 |
Elongation at break (%) | ≥800 |
Flexural strength (MPa) | – |
Flexural modulus (MPa) | – |
Izod impact strength (kJ / ㎡) | – |
Durability | 9/10 |
Easy to print | 6/10 |
Recommended print settings
eSUN eTPU-95ANozzle temperature (℃) | 220 – 250℃ (Recommended 240℃) |
Table temperature (℃) | 45 – 60°C |
Airflow model | 100% |
Print speed | 20-50 mm/s |
Heated table | optional |
Table top/adhesion | masking tape, 3D printing adhesive varnish, PVP glue stick |
Features
eSUN eTPU-95AFlexible | yes |
Elastic | yes |
Impact resistant | yes |
Soft | yes |
Composite | no |
UV resistant | no |
Waterproof | no |
Soluble | no |
Heat resistant | no |
Chemical resistant | no |
Aging resistance | yes |
Dry | yes |
Heated platform required | no |
Other | Recommended to dry at 55℃ for more than 4 hours, direct extruder printing at low speed |
Useful Information for eSUN Series Plastics
eTPU-95APlastic documentation for eSUN 3D printer
eTPU-95ADownload: Technical documentation for plastic for eSUN eTPU-95A 3D printer
eSUN
eTPU-95A for owners of Picaso 3D printersProfile for Picaso Designer X – Plastic eSUN eTPU-95A
Profile parameters
Profile designed by Picaso 3D
Download: Profile for Picaso Designer X - Plastic eSUN eTPU-95a
Examples of printing with plastic 3D printer Esun
ETPU-95A
Product Origin , Hubei China
Importer in the Republic of Belarus:
IE Shalashenko Evgenia Alexandrovna
Legal address: 222728, Minsk region. Dzerzhinsky district, Shatili village, st. Central, 4
The choice of plastic for a 3D printer is very important, especially when the goal is to print a functional model with certain properties. It will be a shame if the printed gear breaks almost immediately, or the decorative model quickly loses its beauty.
It is important to understand whether the printer will be able to work with the selected plastic. Some materials (most often engineering) require certain conditions for successful printing.
First, decide which model you want to print. What properties should it have? Does the model need to be durable? Or is it a master model for further replication, in which the quality of the surface is important?
90% of 3D printers use 1.75 diameter filament. 3mm diameter is rare, but it is better to check in advance which size is used in your printer.
PLA
PLA (Polylactide) is the most popular and affordable 3D printer plastic. PLA is made from sugar cane, corn, or other natural raw materials. Therefore, it is considered a non-toxic, biodegradable material.
Extruder temperature - 190-220 degrees. Table heating is not needed, but if the printer's table has a "heater" for better adhesion, you can heat it up to 50-60 degrees. PLA is very easy to work with. The only requirement is to blow the model. There is practically no shrinkage in this material. When printed, it is practically odorless, and if it smells, it smells like burnt caramel.
Pros:
-
Does not shrink. This makes it easy to build prefabricated or huge models without changing dimensions.
-
There are no specific requirements for a 3D printer. Any working 3D printer will do. PLA doesn't need a heated table or a closed case.
-
Non-toxic. Due to this, during printing it does not smell or has a barely perceptible aroma of burnt caramel.
-
Diverse color palette.
Cons:
-
PLA is poorly sanded and machined.
-
It begins to deform already with a slight heating (about 50 degrees).
-
Fragility. Compared to other materials, PLA is very brittle and breaks easily.
-
Decomposes under the influence of ultraviolet radiation. Of course, it will not fall apart into dust, but it can become more brittle and fade.
PLA is perfect for making dimensional or composite models. For example, decorative interior items, prototyping, electronics cases, etc.
Recently, PLA+ has appeared on the market. It may differ from conventional PLA in improved performance. For example, more durable, with improved layer adhesion.
Dummy turbine
Decorative coasters
ABS
ABS (acrylonitrile butadiene styrene) is the second most popular plastic for 3D printing due to its properties, availability and low price.
Extruder temperature - 220-240 degrees. The temperature of the table is 80-100 degrees. For printing, a heated table is required at the printer. It is desirable to have a closed chamber, because ABS "does not like" drafts. Due to a sharp temperature drop, it can “unstick” from the table or crack in layers. ABS can smell bad when printing, so it is recommended to use the printer with a closed chamber and filters, or print in a well-ventilated area.
Pros:
-
Good strength characteristics allow the production of functional prototypes from ABS.
-
Simple mechanical and chemical processing. ABS is easy to sand and drill, and with an acetone bath you can achieve a perfectly smooth surface.
-
It is currently the most inexpensive type of plastic for 3D printing.
-
Large selection of colors and shades.
Cons:
-
High shrinkage.
Because of this, it can be problematic to manufacture overall products.
-
Printing requires a heated bed and a closed chamber. Without this, the ABS may peel off the table or crack in layers.
-
During the printing process, ABS can smell bad. Therefore, it is recommended that you print in a ventilated area or use the printer with a sealed chamber and filter.
ABS is an engineering plastic. It is suitable for the manufacture of simple functional products.
ABS after chemical treatment in an acetone bath
RU model in ABS
ABS+ differs from conventional ABS in improved strength characteristics (elasticity, rigidity, hardness), less shrinkage and sometimes resistance to certain oils and solvents (eg gasoline).
HIPS
HIPS (high impact polystyrene) - originally conceived as a soluble support plastic for materials with high printing temperatures. For example for ABS or Nylon.
The extruder temperature is 230-260 degrees. The temperature of the table is 80-100 degrees. It is desirable to have a closed camera for a 3D printer.
Pros:
-
Less shrinkage than ABS.
-
Ease of machining.
-
The matte surface looks very advantageous on decorative products.
-
Food contact allowed (but be sure to check with a specific manufacturer for certificates)
Cons:
-
For printing, you need a printer with a heated table and a closed chamber.
-
More flexible and less durable than ABS. Because of this, it will not be possible to produce functional products.
-
Small palette of colors.
Most often, HIPS is used for its intended purpose for printing on 2x extruder printers as a support for ABS. It dissolves perfectly (though not very quickly) in limonel.
Sometimes HIPS is used as an independent material. Products from it are not very durable, but this plastic is loved for easy post-processing. HIPS can be used for models that will subsequently come into contact with food (not hot).
Using HIPS as a Soluble Support
Decorative vase made of HIPS
PVA
PVA (polyvinyl alcohol) is a material that was developed as a water-soluble support for PLA.
Extruder temperature - 190-210. Table heating is not required. PVA is a slightly "capricious" material, it is not recommended to overheat it and print at high speeds.
PVA is very hygroscopic and dissolves in ordinary water. Therefore, it is only used as a support for PLA or other plastics with print temperatures close to PVA.
Soluble PVA Support
Add to compare
Item added to compare Go
Manufacturer | Tiger3D |
Add to compare
Product added to compare Go
Manufacturer | Tiger3D |
Add to compare
Product added to compare Go
Manufacturer | Esun |
Add to compare
Product added to compare Go
Manufacturer | Esun |
PETG
PETG (polyethylene terephthalate) combines the best properties of PLA and ABS. It is easy to work with, it has a low percentage of shrinkage and excellent sintering of the layers.
Extruder temperature - 220-240 degrees. Table temperature - 80-100 degrees. During the printing process, the model must be well blown.
Pros:
-
Excellent sinterability of layers.
-
PETG is very strong and wear resistant. Good impact resistance.
-
Virtually no smell when printing.
-
Non-toxic.
-
Little shrinkage.
Cons:
PETG is perfect for printing functional models. Due to its low shrinkage, it is often used to make large or composite models. Due to its low toxicity, PETG is often used for products that will come into contact with food.
Cookie cutters and patterned rolling pin
SBS
It is a highly transparent material. At the same time, it is durable and resilient. SBS is a low toxicity plastic. It can be used to print food contact models.
Extruder temperature - 230 -260 degrees. Table temperature - 60-100 degrees. You can print without the closed case on the printer.
Pros:
-
slight shrinkage
-
Transparency. After treatment with solvent, limonel or dichloromethane, beautiful transparent products with an almost smooth surface can be obtained.
-
Easily processed mechanically or chemically.
-
Allowed contact with food.
Cons:
SBS is excellent for translucent vases, children's toys and food containers. Or functional things that require transparency, such as custom turn signals for a motorcycle or car, lamps or bottle prototypes.
Vases are perfectly printed with a thick nozzle (0.7-0.8) in one pass (printing in 1 wall or spiral printing in a slicer).
![]()
Models of bottles after chemical treatment
Nylon
Nylon (polyamide) is considered the most durable material available for home 3D printing. In addition to good abrasion resistance and strength, it has a high slip coefficient.
Extruder temperature - 240-260 degrees. The temperature of the table is 80-100 degrees. Nylon is a very capricious and hygroscopic material - it is recommended to dry the coil with plastic before use. For printing, you need a printer with a heated table and a closed chamber, without this it will be difficult to print something larger than a small gear.
Pros:
-
High strength and wear resistance.
-
High slip factor.
-
Heat resistance compared to other 3D printing plastics.
-
High resistance to many solvents.
-
Good for mechanical processing.
Perfectly polished and drilled.
Cons:
Nylon is perfect for making wear-resistant parts - gears, functional models, etc. Sometimes nylon is used to print bushings.
Nylon gear
Add to compare
Product added to compare Go
Manufacturer | Tiger3D |
Add to compare
Product added to compare Go
Manufacturer | Tiger3D |
Add to compare
Product added to compare Go
Manufacturer | Esun |
Add to compare
Product added to compare Go
Manufacturer | Bestfilament |
Soft plastics
FLEX (TPU, TPE, TPC) is a material similar to silicone or rubber. It is flexible and elastic, but at the same time tear-resistant. For example, TPE is a rubbery plastic, while TPU is more rigid.
FLEX are printed at a temperature of 200-240 (depending on the material). A heated table is not required. On printers with direct material feed (feed mechanism on the print head), there are usually no problems with printing. On a bowden feeder (the feed mechanism is located on the body), printing with very soft plastics can be difficult. Usually it is necessary to additionally adjust the clamping of the bar. The main nuance is the very low print speeds - 20-40mm.
Pros:
Cons:
Depending on the type of FLEXa, the models can be flexible or rubber-like. This material, depending on its softness, can be used to print gaskets, insoles, belts, tracks or other models that require flexibility or softness.
FLEX belt
Trainers with flexible soles
Wheel for switchgear model
Decorative plastics
Decorative plastics are PLA plastics with various fillers (wood or metal shavings). Or with dyes selected to imitate different materials. Since the base of the plastic is PLA, it is very easy to print.
Extruder temperature - 200-220 degrees (depending on the manufacturer). A heated table is not required.
Pros:
Cons:
-
Some fillers (eg clay) are abrasive. For such plastics, the standard brass nozzle cannot be used. Will have to buy a harder steel nozzle.
-
Some decorative plastics can clog the small nozzle (0.4 or less). For them, you need to use a “thicker” nozzle.
Depending on the filler, different material properties are obtained. Plastics that use only dye do not require additional processing. Materials with "fillers" may sometimes require additional post-processing.
Plastics with metal fillers after printing must be processed with a metal brush. Then the Metal content will show through and the model will resemble a metal casting.![]()
Plastics with metallic powder
These plastics are often used for printing key chains, decorative models and interior details.
If the plastic has a high content of wood dust, then it is recommended to use a larger nozzle diameter (0.5 or more), a smaller nozzle can quickly become clogged during printing.
Wood-filled plastic ground
Plastic key rings with copper dust
Engineering plastics
These are nylon-based plastics with fillers that improve strength, heat-resistant and other characteristics, help to achieve less shrinkage of the material. For example - carbon fiber, carbon fiber or fiberglass.
Extruder temperature - 240-300 degrees (depending on the manufacturer). Table temperature - 90-110 degrees. Since plastics are based on nylon, the requirements for printing are similar. This is a heated table and a closed printer case.
Pros:
-
Hardness and strength.
-
Low flammability or non-combustibility.
-
High precision due to low shrinkage.
Cons:
3D printers use brass nozzles, some plastics can quickly “waste” it during printing. For such materials it is recommended to use steel nozzles.
These are highly specialized plastics used for a specific task, depending on the filler. For example, functional parts that do not lose their shape when heated, are resistant to many solvents, etc.
Functional Carbon Fiber Composite Prototype
Composite frame
Polycarbonate ashtray
Totals
This is of course not the whole list of materials for 3D printing. There are many highly specialized engineering and decorative plastics for specific tasks.
Manufacturers are constantly trying to replenish the range of materials for 3D printing. Already familiar materials are improved for more comfortable printing. There are many interesting decorative plastics imitating different materials - ceramics, clay, wood, metals.
And of course, the assortment of engineering plastics is constantly updated. Now there are many interesting materials for highly specialized tasks - for example, burnable plastic with a low ash content for subsequent casting in metal.
Burnout plastic
Before buying a coil, read the information on the website of the manufacturer or seller. There you can find some nuances of printing for a particular plastic. The manufacturer indicates the recommended temperature range on the box. Sometimes, for quality printing, it is recommended to print several tests to adjust the temperature settings, retract, etc.
Try to store the started coil in silica gel bags.