3D print foam
FreeFoam, a Revolutionary, Expandable 3D Printable Resin Designed for Volume Production of Foam Parts
Team DM
Platforms
Metal and composites 3D printing 3D printing solutions for health care Industrial-grade polymer 3D printing™
Sand and tooling 3D printing solutions 3D printers for sheet metalMaterials
Breakthrough photopolymer development Advancing 3D printed upcycled woodApps & More
The hydraulic additive manufacturing experts Multi-material powder recoating technology Driving digital transformation in dentistry_Articles
Revolutionary, Expandable 3D Printable Resin Designed for Volume Production of Foam Parts
- Download Spec Sheet
FreeFoam is a new family of photopolymer resins that produces durable and dimensionally accurate closed cell foam parts without tooling – delivering all-new benefits for the automotive, furnishing, footwear, sporting goods, health care and other industries.
Manufacturing Closed Cell Foam without Tooling in an All-New 3D Printing Process
FreeFoam is a new family of photopolymer resins containing heat-activated foaming agents that are 3D printed with Digital Light Processing (DLP). After printing, FreeFoam parts are briefly put into an oven where the foaming agent creates closed cells inside the material in a tightly controlled process. FreeFoam can be programmed to expand a specific amount between 2 to 7 times its original printed size – allowing parts to be shipped in a compact form and expanded on-demand in an oven close to the final point of use or assembly, saving shipping and inventory expenses.
While 3D printers today can process photopolymers into lattice designs that simulate foams, FreeFoam is a true foam containing closed cells that can be printed in as a lattice or as a fully dense design – delivering benefits for a wide range of industrial applications.
See How FreeFoam Works
Your browser does not support the video tag.
[VIDEO]
Delivering all-new benefits for the automotive, furnishing, footwear, sporting goods, health care and other industries.
FreeFoam 3D Printing Production offers a variety of benefits that will change the foam production market.
- 3D prints closed-cell foam products in any volume without tooling
- Manufacture complex foam designs with ease, from lattice designs up to fully dense foam, without trimming or significant waste
- Print your design on a DLP resin 3D printer and then expand the design with accuracy during foaming in an oven at 160-170°C (320-340°F)
- Lightweight existing foam designs to improve product efficiency and reduce shipping costs. You can even ship your foam parts compact and expand or foam them at the final point of assembly or use
- Innovative new material delivers a high strength-to-weight ratio
- Iterate designs as desired, without the penalty of changing tooling
-
Standard automotive seating 3D printed in FreeFoam, developed in partnership with Camaco.
-
This all-new process allows 3D printers to produce much larger final foam parts than the printers’ original build areas and will enable foam products to be shipped at compact sizes and expanded at the final point of assembly or commercial use.
-
Manufacture complex foam designs with ease, from lattice designs up to fully dense foam
Expandable 3D Printable Resin Designed for Volume Production of Foam Parts
FreeFoam is part of the recently launched DuraChain™ category of one-part, one-pot photopolymers that delivers breakthrough elastic and tough material properties through a Photo Polymerization-Induced Phase Separation (Photo PIPS) process. When illuminated during DLP printing, these materials phase separate at the nano level into a material that cures into a resilient, high-performance polymer network. DuraChain enables FreeFoam parts to be foamed with control in an oven without a mold.
FreeFoam will initially be 3D printable exclusively on the ETEC Xtreme 8K top-down DLP system from Desktop Metal’s polymer 3D printing brand.
-
FreeFoam resins contain a heat-activated foaming agent, and are 3D printed into parts like other resins with Digital Light Processing (DLP). However, these parts expand controlled air pores during a quick oven cycle, expanding the part 2-7 times their original size.
Keep Up with the Latest News
Sign Up for Access
Using 3D printed foam & microporous morphology
ARTICLE
Read more
The hole story of 3D-printed foam
Additive manufacturing has long sought a solution to two of the biggest restrictions often faced with traditional materials: rigidity and heaviness. Today, 3D-printed foam and microporous morphology solve for both.
What isn’t there is what makes it great
3D-printed foam is achieved when you print a structure that has breathable pores. It can be firm or pliable, and water-soluble or not, all of which solve common problems faced in 3D printing. In the context of additive manufacturing, microporous morphology is achieved when you print a structure with extremely small pores. For example, Infinite™ Material Solution's Caverna™ PP material has a pore size of 1-4µm (microns).
From the factory floor to the operating room and beyond
3D-printed foam works better than standard cellular materials in terms of durability and long-term mechanical performance, making it an ideal resource in a variety of industries, including transportation, medicine, and aeronautics.
Moving technology forward
From armrests and tray tables to hand breaks and air filters, many interior parts in autos, plane cabins, and train cars require soft, lightweight, and spongy materials.
In 2019, all of the Formula 1 constructor teams used additive manufacturing to print parts for their race cars. While those parts weren’t porous, the ability to print foam-like parts that can withstand heat and form complex geometries opens up even more potential for 3D printing in the sport. One such promising application: air filters that can be printed to the specification of the tight and awkward spaces within and around the driver’s cockpit.
3D-printed foam is incredibly well suited for off-the-ground uses as well. In an industry where every ounce must be accounted for, the relatively lower weight of 3D-printed foam makes it a material of great interest to those in aeronautics.
In a test on a remote-control plane comparing the performance of three different wing materials — traditional foam, 3D-printed PLA, and 3D-printed foam made from colorFABB’s LW-PLA (lightweight polylactic acid) — the latter performed as well as a traditional wing and better than the PLA wing. As 3D printing becomes more adopted and commonplace in all industries, the speed to prototype and create lighter end products will be of great use in aeronautics.
“
For aeronautics, the barrier to entry is high due to regulations, but lightweight 3D printing will play an important role. Every gram matters when you’re trying to get an airplane in the air.
— Jeff Cernohous, Infinite
Advancing medicine, one pore at a time
Developments in manufactured porous materials make it a go-to in the medical industry. Its resemblance to bones, breathability, and varying density offer great advantages in medical research and hospitals. In a field where time is often of the essence, 3D printing can put these materials into the hands of doctors and scientists quicker than ever.
In 2020, COVID-19 wreaked havoc on supply chains, creating medical supply shortages. In response, a team at the University of Louisville designed a unique solution: a novel 3D-printed swab made of a pliable resin material.
3D printing also allows for the creation of realistic models, enabling researchers to study new devices in clinical situations and establish their effectiveness before they are introduced to patients. The technology is also being used for orthotics and prosthetics.
“
Lightweight, breathable, and compliant microporous foams should have a tremendous impact in creating truly custom, comfortable prosthetics.
— Brandon Cernohous, Infinite
Space: A frontier made for 3D-printed foam
Since 2014, the International Space Station has had a 3D printer onboard. When a new or replacement part is necessary, printing it is far easier than waiting for it to arrive from Earth. Because square footage and time onboard ships and space stations are at a premium, the ability to create parts on-demand instead of bringing them along makes 3D printing a vital part of space exploration. And because many of those parts need to be strong, lightweight, breathable, or insulating, 3D-printed foam with microporous morphology is an ideal fit.
“
Resupplying from Earth is cost and time prohibitive.
— Niki Werkheiser, NASA’s Marshall Space Flight Center
When French astronaut Thomas Pesquet flew to the International Space Station, he brought with him 3D-printed parts, including packaging for meals. These parts were designed from a recyclable, edible foam made from PHA, a naturally occurring polymer. Capabilities like these hold great interest as the space exploration industry looks forward to a longer, more distant time in space.
Running to the future
Most athletic gear needs to be breathable, pliable, and water-resistant. With 3D printing, sportswear manufacturers can achieve these qualities in their products, including various parts of sneakers. Insoles need to offer support while also providing the right amount of responsiveness for a runner’s movements. In the future, 3D printing can allow for individual customization of shoes at a speed and accessibility not seen before.
In collaboration with 3D printing specialist Materialise, Adidas is working on a shoe designed to the specifications of an individual runner’s footprints. According to Eric Liedtke of Adidas: “Our 3D-printed mid-sole not only allows us to make great running shoes but also to use performance data to drive truly bespoke experiences, meeting the needs of any athlete.”
Related resources
-
The cost savings of additive manufacturing
Compared to traditional methods, additive manufacturing can be more cost effective in purchasing materials, rapid prototyping, and producing end-use parts.
3D Printing
FFF
Cost Savings
Soluble Core
Support Material
Printers
Automotive
Aerospace
End-Use Products
-
Additive manufacturing in the medical & dental industries
Part III of this four-part series examines the ways in which additive manufacturing is impacting medical training, patient treatment, and healthcare
3D Printing
FFF
Jigs & Fixtures
Rapid Prototyping
Support Material
Medical & Dental
-
Caverna™ PP: 3D printable foam
Read our paper about Caverna PP, our 3D printable foam.
See its specs, applications, and adhesion traits.
3D Printing
FFF
Cost Savings
Soluble Core
Automotive
Education & Research
Medical & Dental
Aerospace
End-Use Products
-
Open vs closed systems in additive manufacturing
Should you invest in an AM system that’s tried and true, or one that’s more flexible? Explore your options in this in-depth comparison of open and closed systems.
3D Printing
FFF
Cost Savings
Printers
Education & Research
Medical & Dental
Aerospace
-
Material knowledge: common 3D printer filaments guide
Learn the basics of additive manufacturing materials.
3D Printing
FFF
Rapid Prototyping
Support Material
Automotive
Education & Research
Medical & Dental
Aerospace
End-Use Products
Explore all Resources
New material for 3D printing that is 40 times larger
If you want to create a large structure, you need to first make a lot of parts that can be 3D printed, move them, combine and weld them. But this may change soon.
A research team at the University of California San Diego is developing a resin that is 40 times larger than its original 3D printed volume. Not only 3D printers, but all machines, cannot process more than the size of the machine. If you want to make a big object, you need to take it apart somewhere and then put it back together somehow. David Wirth, Jonathan Pokorsky and colleagues at UC San Diego wanted to develop an expandable resin that could be used to print large objects on an inexpensive, commercially available 3D printer. The development team stated, “We have developed a foaming photopolymer resin for manufacturing that can be expanded after printing to produce parts up to 40 times their original volume. This allows us to produce designs that are significantly larger than the build volume of the 3D printer that made them.”
The San Diego group has chosen 2-hydroxyethyl methacrylate as the base material for the resin material used in 3D printers. It contains cross-linkers, they help the material to hold during expansion. In the next step, they had to come up with the optimal concentration of the photoinitiator, as well as choose an appropriate blowing agent for the 2-hydroxyethyl methacrylate compound. The team used a non-traditional blowing agent that is commonly used in conjunction with polystyrene-like polymers. Expansion occurs due to carbon dioxide bubbles from di-tert-butyl dicarbonate, they are formed throughout the entire volume of the product. Di-tert-butyl dicarbonate must dissolve well in the liquid polymer in order to be evenly distributed in the future product.
During testing, an Anycubic Photon 3D printer was used. The designed model was printed and heated at 200°C for about 10 minutes. The volume was reported to have increased by up to 4000% compared to a freshly 3D printed item. The scientists first used the formula to 3D print a hollow, latticed sphere. Heating the sphere in the oven caused the volatile component of the resin to bubble up as a gas. This created a porous, polystyrene foam that was 40 times the volume of the original printed object. Then there was a screw wind turbine, 3D printed and then expanded to the intended size. The hull of the boat was then also printed in the same scale before being expanded.
In an article published in ACS Applied Materials & Interfaces, the team describes how they developed the resin, printing parameters, and some of the mechanical properties of the 3D printed foams.
Researchers believe that this material is useful in areas such as construction and architecture, aerospace, energy and biomedicine. In particular, since it floats on water, it can be used for levitation devices and life-saving appliances.
← Solutionix C500 - the most convenient 3D scanner | Photopolymer 3D printing technologies: description, pros and cons →
STL file 2.2/3.0" tire insert (foam) for Rock Racing (U4)・3D printer design for download・Cults
Share Add to ? Quality of creation: 0. 0/5 (0 votevotes)
Ratings of participants on printability, usefulness, level of detail, etc.
- 👁 295 views
- ♥ 0 i like s
- 0 downloads
- 0 comments
- 0 makes
3D Model Description
To be clear, my designs are copyrighted. You are not permitted to distribute or sell any of my designs without prior written permission from me. Even if you changed my original design. Thank you.
This is a TPU print tire insert model for 2.2/3.0" wheel diameter (short track style) tires for RC Racing rigs such as Axial Yeti, Axial Bomber, Axial Wraith, Losi Rock Rey, Losi Hammer Rey and etc. Optimized for 5.75" tires (Proline U4 Hyrax).
Model has 3 plies that provide progressive tire surface resistance, from soft to hard in the center. This allows RC cars to have great traction while keeping the shape of the tire, adding grip and making the car predictable during races. This insert is designed for racing and is stiffer to keep the rig stable at speed.
These models cannot be stretched on the X/Y axis (insert diameter) as this will affect the design, but you can stretch them on the Z axis (insert width) if you want to fit them in a wider or narrower tire or wheel .
Carefully read the 3D printing settings as it is very important to get the desired result. Each print will take ~6 hours . If you need help, please visit my Facebook page: https://www.facebook.com/groups/d440rc.
You can sell 3D printed parts designed by D440RC, but you must follow four simple rules: 1) respect the brand, make it clear that this is a D440RC design, and don't change the original name/brand to help advertise the purchase of the model in Cults, 2 ) you must buy/download the models you want to sell, 3) the prints must be of good quality, 4) you can only sell 3d printed parts, you can NOT sell/give away the models/files, they are yours alone.
3D Print Settings
The model uses Ultimaker Cura slicer infill templates to simulate soft layers, giving the user full flexibility to configure the splint insertion as desired. The model includes a 3mf file that can be opened as a "project" in Cura and includes print settings.
Infill UP or DOWN in Cura settings if you want a softer or harder infill. Around 6% is usually good, but depends on the material used.
This must be printed in TPU (tested with Overture TPU 92A and 95A), 0.4mm nozzle, number of wall lines 1, NO gap filling between walls, no top/bottom layers, inner ring support and 0.2~ 0.28 layer height . Make sure your TPU settings work well. Printing gyroid filler.
Open the 3mf Cura project file ( Open as project ). It must be ready to print on Ender3 printers.
3D Printer File Information
- 3D Design Format : 3MF and STL Folder details close
- 2.2_3.0 x 5.75 Racing (PL Hyrax U4).stl
- Project 2.2_3.0 x 5.75 Racing (PL Hyrax U4).3mf
Find out more about
formats - Publication date : 2022-09-23 18:30
Copyright
©
Tags
Author
designs 27
Downloads 510
Liked designs 5 Subscribers 54
Contact
D440RC designs parts for Radio Control devices. When some parts deserve to be shared, will be posted here. Usually, designs are focused on RC Crawlers and U4RC (so far), but there's no plan to limit to other stuff (e.g. drones).
Free designs can be found here: https://www.myminifactory.com/users/danielanguita
You are invited to this group to provide feedback on designs, ask questions, and enjoy the hobby with us!
1.9" ZigZag foam for RC scale tracks
18.21 €
Class 0 and 1 tire insert (foam) for RC scale crawler
17.12 €
2.2" tire insert (foam) for RC scale crawler
17.12 €
1.0" TIRE INSERT (TWO STAGE FOAM) FOR 1/24 SCX24 RC Crawler
12,10 €
SCX6 2.9" tire insert (foam) for large crawlers
18.96 €
NextLevelFoam 1.
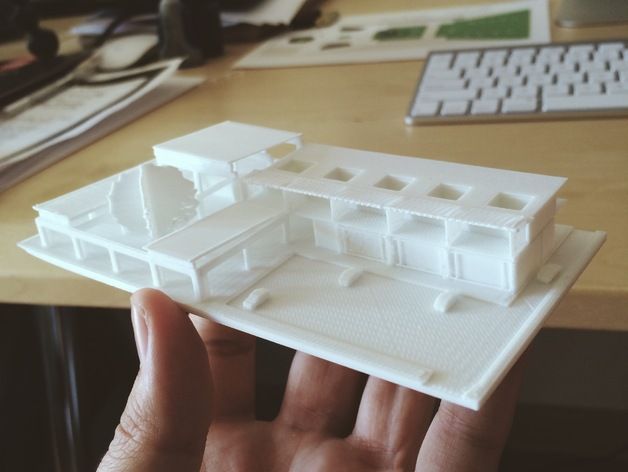
€18.54
1.9 x 5.4" tire insert (foam - PL Boggers) for RC scale crawler
6,08 €
Chassis PUMA - SCX24 LCG Kit
13.49 €
Best 3D Printer Files in the Miscellaneous Category
Quad Surfboard Fins
Free
Electric car VAZ-2802-01 1:87
Free
Mate Thanos
Free
Mate Batman
Free
Rocket Bank
Free
Micro Gas Mask / Respirator V5 (Altoids 9)
Free
Balalaika (Russian Stringed Instrument)
Free
Miner with side cart
28. 77 €
Bestsellers in Miscellaneous category
Giarados - articulated sea serpent
1,50 €
Predator-inspired movable mask
6.20 €
hinged shenron
3 €
Gnome Yes (No support)
€2.49 -twenty% 1.99 €
Christmas house
6.97 €
ItsLitho "Pure" Personalized Lithophane Christmas Ball
1.90 €
Speeder-Pad support on FLSUN V400 and FLSUN SuperRacer
3 €
WORLD CHAMPIONSHIP OF SPACE
5. 23 €
Personalized Christmas ball made of lithophane ItsLitho "Swirl"
1,90 €
Charizard - Pokemon with flexible articulation (seal in place, without supports)
3 €
Adderini - 3D printed repeating slingbow / crossbow pistol
12.50 €
4th planet Fighting pre-Olympic god
12 €
CHRISTMAS TREE v2
1,50 €
Mickey Christmas night light Litophane
3,50 €
ItsLitho "Drop" personalized lithophane Christmas ball
1,90 €
Key holder for middle finger
1 €
Do you want to support Cults?
Do you like Cults and want to help us continue our journey on our own ? Please note that we are a small team of 3 people , so support us in keeping the activity going and making future designs is very easy.