Carbon composite 3d printer
Ultimate Materials Guide - 3D Printing with Carbon Fiber
Overview
Carbon fiber filaments use tiny fibers that are infused into a base material to improve the properties of that material. Several popular filaments can be bought with carbon fiber fill including PLA, PETG, Nylon, ABS, and Polycarbonate. These fibers are extremely strong and cause the filament to increase in strength and stiffness. This also means that the 3D printed parts will be much lighter and more dimensionally stable, as the fibers will help prevent shrinking of the part as it cools. Print settings, such as printing temperature, speed, bed adhesion, and extrusion rates will be very similar to the normal settings used for the base material that the fibers were added to (for example, the stock PLA settings would be a good starting point for PLA-based carbon fiber filament). However, due to the added fibers, these specialty materials are more likely to clog and can require special hardware to avoid damaging the printer.
- Increased strength and stiffness
- Very good dimensional stability
- Lightweight
- Abrasive and requires hardened steel nozzle
- Increased oozing while printing
- Increased brittleness of filament
- Higher tendency to clog
Hardware Requirements
Carbon fiber filled filaments have the same requirements as the base filament it is infused with. The hardware requirements listed below are for carbon fiber filled PLA filament.
Bed
Temperature: 45-60 °C
Heated Bed Optional
Enclosure not required
Build Surface
Painter’s tape
PEI
Glass plate
Glue stick
Extruder
Temperature: 200-230 °C
Requires Wear Resistant Hardened Steel Nozzle
Cooling
Part Cooling Fan Required
Best Practices
These tips will help you reduce the chances of common 3D printing issues associated with carbon fiber filled filaments such as clogging and the nozzle wearing down.
Upgrade to Hardened Steel Nozzle
The carbon fibers in these filaments can be extremely abrasive. In many cases, the carbon fibers are actually harder than the brass nozzles used on most 3D printers, so trying to print these materials with a stock nozzle could damage the printer. Instead, plan on upgrading to a hardened steel hotend. These hotends can resist the added wear from the fibers, however, they also tend to be less thermally conductive than their brass counterparts. You may need to set the extruder temperature as much as 40° hotter than usual, which also helps with reducing the chance of a clog. Reducing the fan speed can also be useful to prevent thermal issues with the steel nozzles.
Adjust Retraction Settings to Avoid Clogs
Since the filament is full of small fibers that won’t melt, the chances of a nozzle clog are greatly increased over the base material. We recommend reducing your retraction distance or disabling retractions all together, as the retractions can increase the change of a buildup of fibers inside the extruder assembly. If you want to minimize the number of retractions that are performed, Simplify3D includes a very useful setting that will actually adjust the travel path of the extruder to stay within the interior of the part so that no retraction is needed. You can enable this setting by turning on the “avoid crossing outline for travel movements” option on the Advanced tab of your process settings.
Reduce the Print Speed for Consistent Results
Using a slower print speed can be a big benefit for carbon fiber filled materials, as the extruder will be under less stress, and has a higher chance of pushing small clogs through the nozzle if they start to form. Try reducing your print speed by 25-50% to see what value works best for your specific brand of plastic. If you still experience clogs after making these changes, we have an entire section on our Print Quality Guide dedicated to this issue that includes several other tips to help troubleshoot this issue: How to Fix a Clogged Extruder.
Use a Guided Filament Path
Carbon fiber filled filaments tend to be far more brittle than the base filament and can snap easily if they are forced through tight corners, or rub on sharp edges of the printer frame. Make sure that the entire filament path, from the spool to the nozzle, consists only of gentle curves, with no sharp turns or areas where the filament will be dragged along a surface. Using a PTFE guiding tube, or ensuring that the filament spool is in a strategic place with regards to the extruder can help reduce the chance of filament breakage.
Pro-Tips
- Nozzles with larger diameters (0.5mm or more) are far less likely to clog, as the fibers will fit through the larger nozzle hole much more easily.
- If the nozzle seems to clog right away after printing the first layer or two, try increasing the first layer height. If the nozzle is too close to the bed, this will create increased back-pressure while printing these layers that can cause the fibers to build up and clog the nozzle temporarily.
Get Started with Carbon Fiber Filled
There are many unique applications for this speciality material. We’ve compiled a few tips below to help you get started.
Common Applications
- R/C Vehicles
- Functional prototypes
- Decorative pieces
- Lightweight Props
Sample Projects
- F16
- Formula 1 Car
- Quadcopter
- Darth Revan’s Mask
Popular Brands
- Proto-Pasta Carbon Fiber Reinforced PLA
- Matterhackers NylonX
- 3DXTECH
10 Best Carbon Fiber 3D Printers In 2023
- Last Updated: January 19, 2023
- Pat Nathaniel
Do you like heavy metal? Then you’ll love carbon fiber.
Carbon fiber 3D printers can create parts as strong as metal out of lightweight reinforced plastic. And they do it at a fraction of the cost.
But you need the right kind of 3D printer to print with carbon fiber filaments. Using an inadequate printer with these advanced materials will only result in broken components and expensive maintenance.
Read on to learn what the best carbon fiber 3D printers are in 2022.
Qidi Tech X-Plus
Check Latest Price
MakerBot METHOD X Carbon Fiber Edition
Check Latest Price
Ultimaker S5
Check Latest Price
Table of Contents
- Best Carbon Fiber 3D Printers At A Glance
- 1. MakerBot METHOD X Carbon Fiber Edition (Best Choice)
- 2. Qidi Tech X-Plus (Best Value)
- 3. Ultimaker S5 (Premium Choice)
- 4. XYZ PartPro300 xT (Beginner-Friendly)
- 5. Raise3D Pro3 (Most Reliable)
- 6. Fusion3 Edge (Best Large-Format)
- 7. Pulse XE (High Performance)
- 8. Markforged Mark Two (Best For Strongest Parts)
- 9.
Delta WASP 2040 Industrial X (Fastest)
- 10. Desktop Metal Fiber
- Printing with Carbon Fiber-Reinforced Filament
- Chopped Carbon Fiber vs. Continuous Carbon Fiber
- Is 3D Printed Carbon Fiber Strong?
- Ideal Designs for Carbon Fiber 3D Printers
- Tips for Successful Carbon Fiber Printing
- Pros and Cons of Carbon Fiber 3D Printers
- Go Strong, Go Carbon Fiber
Best Carbon Fiber 3D Printers At A Glance
1. MakerBot METHOD X Carbon Fiber Edition (Best Choice)
2. Qidi Tech X-Plus (Best Value)
3. Ultimaker S5 (Premium Choice)
4. XYZ PartPro300 xT (Beginner Friendly)
5. Raise3D Pro3 (Most Reliable)
6. Fusion3 Edge (Best Large Format)
7. Pulse XE (High Performance)
8. Markforged Mark Two (Best for Strongest Parts)
9. Delta WASP 2040 Industrial 4.0 (Fastest)
10. Desktop Metal Fiber
3D Printer Type: FDM | Materials: Tough, PLA, PVA, PETG, Nylon, Nylon Carbon Fiber | Build Volume: 190 x 190 x 196 mm
If you’re only ever going to buy one carbon fiber 3D printer, make it the MakerBot METHOD X Carbon Fiber Edition (CFE). This machine brings you everything you could need.
With a minimum layer resolution of 20 microns, this printer creates surface details few FDM printers can match. That quality is due to the enclosed chamber that guarantees uniform heating.
METHOD X CFE also features dual extruder printing and can print water-soluble supports. It ships with three different extruders, each optimized for different filaments. You can print with practically any filament you want.
This fully production-ready printer supports everything from basic PLA to high-performance materials, even from third parties. It can even print parts good enough to replace metal. If you can dream it, METHOD X CFE can print it.
But wait, we haven’t gotten to the best part yet.
METHOD X CFE is automated to a mind-blowing degree. Material loading, bed leveling, Z-axis and nozzle calibration… The printer takes care of it all on its own and saves you hours in print preparation. Just hit Start and move on with your day.
If we have to nitpick to find downsides, you have to wait a bit for parts to cool down due to the heated chamber. As a professional quality (pro-quality) printer, METHOD X CFE is also pricey.
Note that MakerBot recently announced its merger with Ultimaker. The companies say they will keep manufacturing their respective printers, but we’ll have to wait and see what future support will be like.
But if you want to print carbon fiber filaments, get the MakerBot METHOD X CFE. It’s simply the best carbon fiber 3D printer available.
- Extreme dimensional accuracy and detail
- Supports plenty of materials
- Almost everything is automated
- Expensive
- Small build volume
- Uncertain future support
Check Latest Price
2.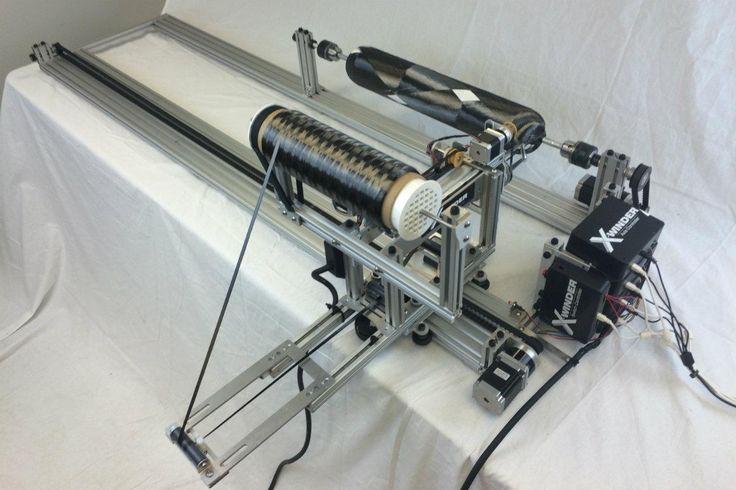
3D Printer Type: FDM | Materials: PLA, ABS, PETG, TPU, Nylon, Carbon Fiber & Polycarbonate | Build Volume: 270 x 200 x 200 mm
Whoever said there’s no such thing as affordable quality hasn’t seen Qidi Tech’s X-Plus. This printer serves up incredible flexibility at a price point well below $1,000. The machine achieves that versatility by essentially having two sides to it.
What exactly does that mean?
X-Plus ships with two swappable extruders — A and B. Similarly, it has a double-sided flexible printing bed and two filament holders.
Extruder A, combined with the A-side of the print platform and the external filament holder, makes printing regular filaments a breeze. The outside filament holder smoothly feeds PLA, ABS, or TPU filament into the machine.
But it’s the B-side where things get advanced. Extruder B is specifically designed for harsher advanced materials, like nylon or carbon fiber filament. You place carbon fiber materials into the internal filament holder within the ventilated enclosed chamber, which keeps their temperature steady for excellent print quality.
With X-Plus, you also get a very generously sized print chamber — well beyond what you’d expect at this price. You can easily print either large-scale parts or a whole bunch of small components from carbon fiber-reinforced filaments right at home. If you’re dreaming of an advanced 3D printing station in your garage, X-Plus makes your dreams come true.
But the low price shows in some things. The user manual and online resources are pretty poorly translated and occasionally devolve into non-English. Luckily, the company’s excellent customer service will quickly answer any questions.
Qidi Tech X-Plus is your printer of choice for reliable carbon fiber printing that won’t break the bank.
- Affordable price
- Large print volume
- Great customer service
- Supports a wide range of materials
- Poorly translated documentation
- Overtly sticky print platform
Check Latest Price
3.
3D Printer Type: FDM | Materials: Tough PLA, TPU 95A, ABS, Nylon, TPU | Build Volume: 330 x 240 x 300 mm
Are you serious about carbon fiber 3D printing? Do you want to make pro-quality parts with a pro-quality machine at your home? Ultimaker S5 will keep you in business — with a capital B.
S5 is a popular machine among such huge companies as Volkswagen and Ford, and for a good reason. Its impressive collection of features makes it an “always-on” production powerhouse.
The S5 has swappable print cores and ships with three different ones. You can change them as needed to print with more than 200 filaments of different thicknesses and properties. Simply pop in the hardened print core and you’re ready to print carbon fibers.
But S5 goes much further in productivity.
With its dual extruders, S5 can print two different filaments at once. It can also automatically swap between the extruders on the fly to deliver accurate and multi-color parts. You can easily fill the S5’s massive print chamber with huge carbon fiber components.
If you’re looking for more dual extruder 3D printers check out our article here.
But one of the best things about the S5 is how easy it is to use. You can quickly set up the machine with the large touchscreen and it comes with advanced automated features, like bed leveling. Ultimaker’s Cura software unlocks further control options.
Of course, all this comes at a price, which is very high. S5 is also a big machine, so it can’t fit in just any living room corner.
Anybody looking to run a professional carbon fiber printing business from home can’t go wrong with Ultimaker S5. After all, it’s built for professionals.
- Massive filament range
- Dual extruders
- Easy to use
- Huge print volume
- Industrial-level price tag
- Occasional software issues
- Mediocre print speed
Check Latest Price
4.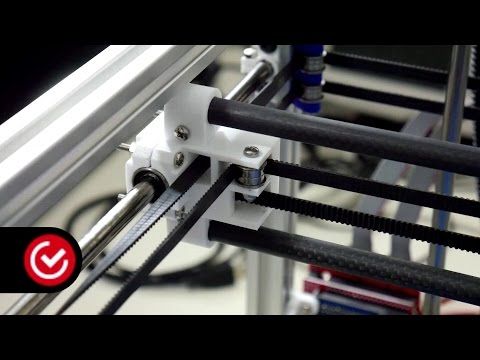
3D Printer Type: FFF | Materials: Carbon PLA, Nylon, Metallic, PETG, ABS, TPE, PLA & Tough PLA | Build Volume: 295 × 300 × 300 mm
PartPro300 xT by XYZprinting is a carbon fiber 3D printer for people who don’t want to spend much time operating the machine itself. This printer could borrow the famous slogan of Ronco rotisserie ovens — just set it and forget it.
PartPro300 xT comes with a hardened steel nozzle on each of its dual extruders as the default option. The nozzle tolerates high temperatures and abrasive materials. It makes printing durable and detailed parts very easy.
And as you’re about to find out, “easy” is the key word here.
XYZprinting has gone above and beyond to make PartPro300 xT as simple to use as possible. The printer is easy to set up thanks to extensive automated features, including bed leveling and calibration. You’ll be printing as soon as you pull the machine out of the box and let it calibrate itself.
As a unique feature, PartPro300 xT has a separate enclosed filament holder that fits two giant three-kilogram filament spools. You can keep printing for a long time before you have to go through the hassle of replacing the spools. The printer also has a convenient resume function in case you lose power during printing.
The external filament chamber takes up quite a bit of space, though. Additionally, you can’t print with both extruders if you want to make the most of the big printing chamber.
XYZprinting PartPro300 xT is your choice if you want to make detailed carbon fiber printing as easy as possible.
- Very easy to use
- Extensive automation
- Big print chamber
- Supports a lot of materials
- Supports a lot of materials
- Smaller print volume with dual extrusion
Check Latest Price
5.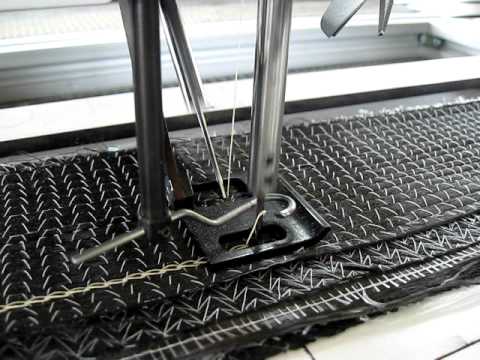
3D Printer Type: FFF | Materials: PLA, ABS, HIPS, PC, TPU, TPE, PETG, ASA, PP, PVA, Nylon, Glass Fiber Infused, Carbon Fiber Infused, Metal Fill & Wood Fill | Build Volume: 300 x 300 x 300 mm
Raise3D Pro3 looks like it could take an atomic blast with just a shrug. The sturdy appearance is a great indicator of what you can expect. If it’s reliability you’re after, here you go.
Pro3 is a workhorse in every sense of the word. It will keep printing for hours with steadily excellent print quality.
How does the printer achieve that?
The automatic bed leveling and calibration certainly help. So do the dual extruders that heat up to 300°C, which is enough to process a wide selection of filaments, including harsh carbon fiber-reinforced materials, without jams or clogs.
Those extruders give Pro3 an impressive 10-micron minimum layer height. Contributing to the predictable print quality is also the HEPA-filtered enclosed chamber with air circulation management. It keeps the temperature stable while filtering out excess noise and printing fumes.
Imagine safely running a printer in the same room and still hearing your thoughts. That’s not something many carbon fiber printers can achieve. Trust me, a quiet 3D printer is like a bidet. It’s something you didn’t know you needed in your life.
Maintenance is also a cinch. You can swap the printer hot ends literally within seconds. The printer automatically pauses prints if you open the chamber door and has power loss recovery features. Pro3 also includes the smart EVE assistant system that helps you troubleshoot problems for a quick fix.
True to its tank-like nature, the printer is bulky and kind of slow, though. And that’s a great way to wrap things up. Raise3D Pro3 is like a stubborn turtle — it prints steadily and reliably, come what may.
- As reliable as they come
- Consistently good print quality
- Dual extrusion
- Quiet and filtered enclosure
- Bulky
- Print speed is slow-ish
Check Latest Price
6.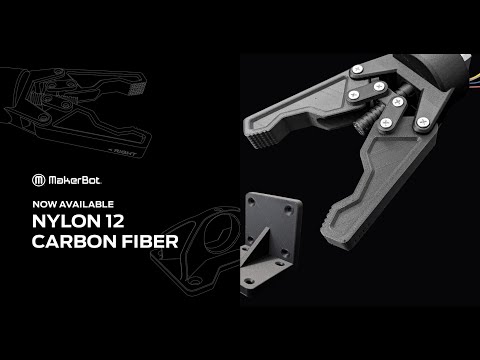
3D Printer Type: FFF | Materials: PLA, ABS, ASA, Reinforced Materials including Carbon Fiber, Kevlar, and Fiberglass, Flexible, Nylons, PET/PETG & Polycarbonate | Build Volume: 355 × 355 × 368 mm
Do you like big parts and you cannot lie? If so, when Fusion3 Edge walks in with itty-bitty detail quality and a huge print chamber in your face, you’re about to get sprung.
Although it makes the machine itself big, Edge offers a massive build volume. The 368 x 368 x 343 mm print chamber can house pretty enormous parts. Thanks to its pro-level print quality, you could easily make spare parts for cars or any other machines at home.
Oh yes, the print quality. Let’s talk about that.
Instead of your usual screw-in hardened steel nozzle, Edge uses a single swappable surgical steel print tube. The fascinating print head configuration heats up to 320°C and handles carbon-fiber-reinforced filament without a problem.
Consequently, the printer has an impressive print speed and produces sharp details. It’s also less prone to leakage than a regular nozzle.
Edge is an open platform printer, so it works with practically any third-party filaments. The high hot end temperature means you can feed it pretty much anything.
The enclosed and HEPA-filtered enclosure makes Edge a quiet machine and reduces emissions. You can put it in an office or a classroom without worrying about noise or smells.
You better make space for the printer, though, because it’s really huge. It also comes with a price tag that rivals the printer in size.
But you can’t print big without a big machine. Fusion3 Edge is definitely the way to go if you want a large-format carbon fiber 3D printer.
- Large print volume
- Open material platform
- Fast print speed
- Quiet
- Automated maintenance reminders
- Pricey
- Needs a lot of space
- The print head could be prone to clogs
Check Latest Price
7.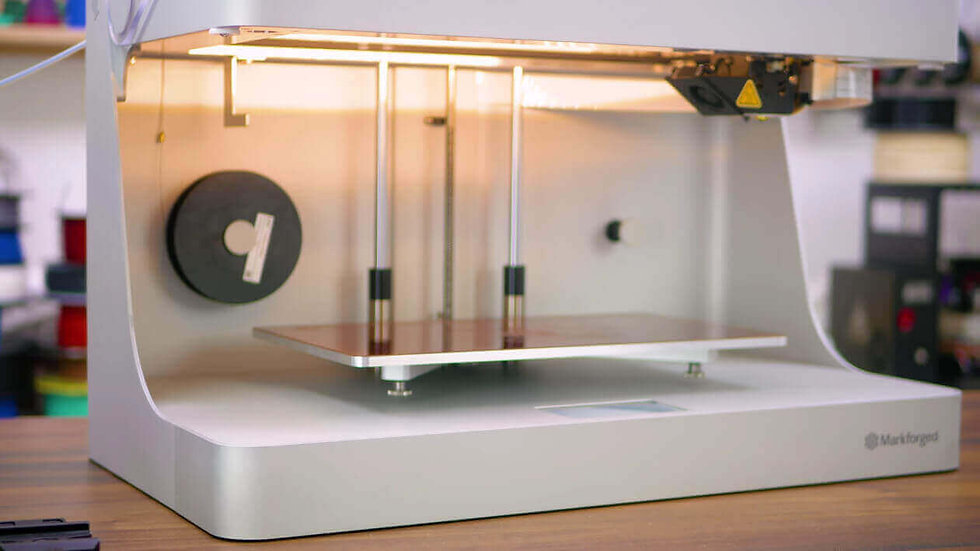
3D Printer Type: FDM | Materials: PVA, PLA, ABS, Nylon, Bronze PLA, Brass PLA, Wood PLA, Copper PLA, TPU, PETG , Carbon Fiber, Fiberglass, Aluminum PLA, Magnetic Iron PLA, ColorFabb XT CF20 (PET-G), CopperFill, BronzeFill, WoodFill, CorkFillr, Flexfill 98A TPU, PLA 3D870 (APLA) | Build Volume: 250 x 220 x 215 mm
Those looking for a high-performance machine to produce carbon fiber prints shouldn’t miss Pulse XE. It’s a real gem of a carbon fiber 3D printer — literally.
Pulse XE has an optional nozzle that’s tipped with an Olsson Ruby. This jewel-tipped nozzle is built to withstand abrasive materials, like nylon and carbon fiber filaments. Another thing contributing to Pulse XE’s high performance is how easy it is to start printing. The machine comes with every component pre-installed and it’s ready to print right out of the box.
Not only are the prints high quality, so are the printer’s parts. Pulse XE is built from well-crafted, high-quality materials and needs little maintenance.
Just plug it in and after a short automatic calibration, you’re good to go for years.
As an interesting quirk, Pulse XE is designed to work specifically with MatterHackers’ MatterControl software. The features the application unlocks give the printer incredible versatility — if you have a dedicated computer.
Unfortunately, Pulse XE does have a couple of downsides.
First, it moves the print bed horizontally during printing. This method gives it a sluggish print speed since fast movements could cause layer misalignment. The detail quality can make up for the lack of speed, though.
Second, Pulse XE doesn’t come with an enclosed chamber. Exposure to room temperature air could lead to layer separation and there’s nothing to filter out printing fumes.
But at less than $1,500, Pulse XE is an affordable high-performance carbon fiber printer. With an added enclosure, it can only get better.
- Affordable price
- Easy and quick setup
- Low maintenance
- Detailed prints
- Slow print speed
- Needs a computer
- No closed enclosure
- Small build volume
Check Latest Price
8. Markforged Mark Two (Best For Strongest Parts)3D Printer Type: CFF | Materials: Onyx, Carbon Fibre, Fibreglass, Nylon, Kevlar, High Temp. Fibreglass | Build Volume: 320 × 132 × 154 mm
Markforged Mark Two is here to show you what heavy-duty means. When you need the roughest and toughest parts, this machine will deliver in spades.
Unlike most carbon fiber 3D printers that use chopped carbon fiber filament, Mark Two uses continuous carbon fiber printing. Using a second extruder, it feeds a steady strand of carbon fiber between material layers, giving parts uniform strength. Not only that, but Mark Two can also reinforce parts with kevlar or fiberglass.
And the result?
Parts that are more than twice as tough as aluminum.
The heavy-duty theme carries over to Mark Two’s general habitus. It’s a professionally-built, sturdy machine with an enclosed heated print chamber. This gives the parts a high print quality and contributes to their incredible strength.
So, if you’ve ever wanted to run a home factory to make spare engine parts for cars or motorcycles, this is your machine.
But do note that Mark Two is an industrial machine to boot. It doesn’t have automatic calibration, so you’ll have to dial in all the settings manually. Fortunately, the large and responsive touchscreen makes setup easier.
Mark Two works only with Markforged’s proprietary Onyx nylon material, which is expensive. That only adds to the printer’s staggering retail price, so you better be serious about continuous carbon fiber printing.
But if you are and you have the money, go right ahead. Anyone looking for an industrial-level carbon fiber printer to make incredibly strong parts won’t find a better machine.
- Professional print quality
- High part strength
- Continuous carbon fiber technology
- Intuitive controls
- Not affordable on a hobbyist budget
- Proprietary materials
- Manual calibration
Check Latest Price
9.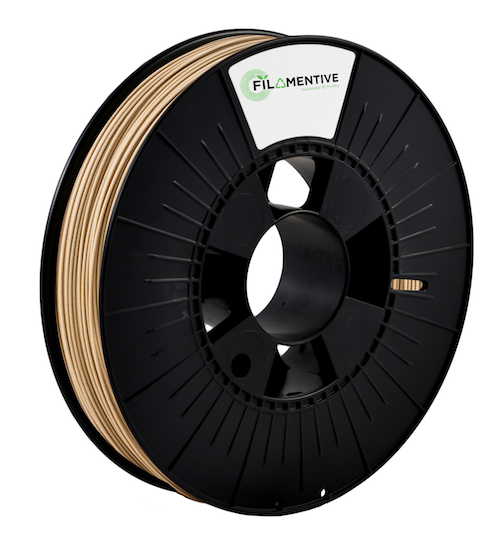
3D Printer Type: FFF | Materials: ASA, ABS, High-Impact PS, PETG, TPU, TPE, Polypropylene, Polycarbonate, PC+ABS, PPS, PMMA, PVA, PA, PA Carbon & PLA | Build Volume: 200 x 200 x 400 mm
Who says industrial-quality carbon fiber printers have to cost a fortune and be difficult to use? Certainly not Delta. Their WASP 2040 Industrial X printer offers simple, professional productivity at a surprisingly affordable price.
WASP 2040 has a unique movement mechanism when compared to other printers on this list. Three robotic arms move the extruder around, which lets you easily print curved geometries.
This should make the printer more difficult to calibrate, but Delta has included advanced automatic calibration to make using the WASP easy. As a result, it reaches amazing speed while being simple to operate.
But with speed comes poor print quality, right? Not in this case.
Delta’s Hot and Cold technology maintains a steady temperature in the printing chamber while cooling down the machine’s components. You won’t have to waste time and money by constantly replacing burnt-out parts.
The printer’s dual gear filament driver pushes material through the nozzle at a steady pressure. It gives the WASP great detail quality while reducing clogs. With WASP 2040, you can just print without worrying about maintenance.
Now, WASP 2040 isn’t exactly cheap, but it’s very affordable considering everything you get. It supports a wide range of third-party filaments, so you can save money by using cheaper materials.
The printer retails for around $5,000, so it’s a fantastic option if you’re looking for industrial-level capabilities at a great value.
- Great value
- Wide material support
- Fast print speed
- Easy to use
- Noisy
- Rather expensive, despite the value
Check Latest Price
10.
3D Printer Type: Micro Automated Fiber Placement (uAFP) | Materials: Nylon (PA6), PEEK, and PEKK, which can be reinforced by carbon fiber- and fiberglass μAFP tapes | Build Volume: 310 × 240 × 270 mm
Buying your own carbon fiber 3D printer can be a tough decision. If you’d rather rent one instead, Desktop Metal Fiber might be the solution you’re looking for.
Instead of selling the machine, Desktop Metal provides the Fiber printer on a subscription basis. The three-year contract runs about $5,000 per year and delivers you a machine that’s ready to use out of the box.
And we really mean that. Fiber has two different settings available, one for entry-level users and another opt-in control scheme for advanced operators. It’s a printer that grows with your skills and gives you exactly the level of control you need.
But what about the part quality? Well, you have nothing to worry about.
The unique subscription model nets you a printer that makes extremely strong parts. Fiber uses continuous carbon fiber technology, meaning that it feeds a continuous strand of carbon fiber between part layers. It can even alter the direction the fiber runs for extra strength.
Fiber can use nylon, PEKK, or PEEK as the base material for carbon fiber composite materials, so you have options. It’s unfortunate that the printer is locked to Desktop Metal’s materials, though.
The subscription model might not be for everybody, but it’s an interesting sales model. Desktop Metal Fiber is a high-quality, professional carbon fiber 3D printer for the adventurous printer user.
- Continuous fiber technology gives strong parts
- Professional part detail and quality
- Simple usability
- Only available through a subscription model
- Very bulky
- No third-party materials
Check Latest Price
Printing with Carbon Fiber-Reinforced Filament
Carbon fiber can make for incredibly tough but lightweight parts. But you can’t get successful results even with the best carbon fiber 3D printer if you don’t understand the material you’re working with.
So, what exactly is carbon fiber?
We often think of sleek and shiny carbon fiber as modern, but carbon fiber was first made all the way back in 1860. The material consists of carbon atoms bonded together into thin but long chains. But when you print with “carbon fiber” filaments, you’re not actually printing with just carbon fiber.
Instead, 3D printers use either carbon fiber composites or reinforcement. But how do these two technologies differ from each other?
Chopped Carbon Fiber vs. Continuous Carbon Fiber
When most people talk about “carbon fiber filaments,” they generally mean chopped carbon fiber filament. As it says on the label, manufacturers mix short carbon fibers into the base material to make these materials
The most common base for chopped carbon filament is PLA. This thermoplastic creates accurate surface details but isn’t very sturdy — unless you mix it with carbon fibers. The presence of the carbon fiber material gives the filament enhanced mechanical characteristics.
Not every carbon fiber filament is PLA, though. For example, Onyx — the proprietary material Markforged Mark Two relies on — is based on nylon. Nylon is naturally strong, so you can imagine how strong it gets with carbon fibers. The downside is nylon’s high melting temperature and abrasiveness, but then again you need a reinforced nozzle to print carbon fiber in the first place.
The second carbon fiber technology is continuous carbon fiber reinforcement. If your 3D printer uses this technology, it will feed a continuous strand of carbon fiber into the part you’re printing alongside the thermoplastic filament. The web of continuous carbon fiber makes for extremely sturdy prints, but you need a specialized (and typically expensive) printer with dual extruders.
So, what’s the bottom line?
Continuous carbon fiber reinforcement generally gives you stronger parts, since the carbon fiber filament hasn’t been broken into a billion tiny bits. On the other hand, chopped carbon fiber filament is usually much cheaper. It can still be very strong, but the strength will ultimately depend on how much carbon fiber is mixed into the filament.
Is 3D Printed Carbon Fiber Strong?
Source: Youtube 3D Printer AcademyCarbon fiber’s main selling point is that it produces strong and durable parts. But is that really true?
When people talk about the “strength” of carbon fiber, they often actually mean “rigidity.” In this sense, yes — carbon fiber-reinforced filaments can create extremely rigid parts. With the right material and carbon fiber 3D printer, you can make parts that are more rigid than metal.
That said, carbon fiber-reinforced 3D printed parts are not flexible. It will take a lot to get them to bend, but once they do, the parts will easily snap and break.
The bottom line about carbon fiber parts’ strength is this — they will not bend. We mean that in both a positive and negative sense.
Ideal Designs for Carbon Fiber 3D Printers
Source: Youtube The 3D Print GeneralAlthough carbon fiber parts can snap, you shouldn’t take it as a downside. In fact, carbon fiber is one of the best materials to use for parts that you don’t want to bend.
Let’s put it this way. Big-name aerospace and automotive manufacturers — like Ford and Boeing — use carbon fiber 3D printers. They wouldn’t do that unless the technology delivered first-class parts.
But carbon fiber has much to offer you even at home. You can print carbon fiber parts that will perform fantastically as:
- Supports
- Cases or shells
- Tools
- Propellers
- Gears
Carbon fiber 3D printers are particularly popular with drone and RC car enthusiasts. The lightweight and high toughness of the material are tailor-made for these kinds of uses.
Tips for Successful Carbon Fiber Printing
Printing technical materials like carbon fiber isn’t quite as straightforward as with plain plastics. The properties of carbon filament make the printing process more involved and demand more from your printer.
Here are some tips that help you get high-quality carbon fiber parts:
- Use a Hardened Nozzle: Chopped carbon fiber is very abrasive and can quickly wear down low-end printer nozzles. Make sure whichever printer you use has a hardened steel nozzle or another kind of high-performance nozzle.
- Tweak Retraction Settings: The carbon fibers within the filament won’t melt during printing and they can clog your nozzle. It’s a good idea to use low or no retraction to avoid material oozing and clogging your printer.
- Lower the Print Speed: Some of the listed printers can reach very high speeds, but you can’t print carbon fiber in a rush. A lower print speed can give you better detail quality and prevent nozzle clogs.
- Up the Nozzle Size: Nozzles with bigger diameters (0.
5 mm or more) are better for carbon fiber printing. They let the fibers pass through more easily and further prevent clogging issues.
- Increase Temperature: Hardened steel nozzles are less thermally conductive than brass ones. Set your hot-end temperature a bit higher than the filament’s recommended setting to keep the material flowing smoothly.
Pros and Cons of Carbon Fiber 3D Printers
- High part strength and rigidity
- Low part weight
- Very little shrinking
- High heat and abrasion resistance
- Expensive printers and materials
- Prone to clogging and oozing
- Potentially brittle parts
- Abrasive filaments need a hardened steel nozzle
Go Strong, Go Carbon Fiber
So, there you have it. Carbon fiber 3D printing lets you make industrial-strength parts with relative ease. Carbon printers aren’t the cheapest machines on the market, but they’re a great investment for any printer user who likes and wants their parts as tough as they come.
We’ve covered many printers, though. If that’s a bit too much to take in, here are our recommendations for the best 3D printers for carbon fiber in different categories.
For a budget carbon fiber 3D printer, pick Qidi Tech X-Plus or Pulse XE. If you need pro-level productivity, Ultimaker S5 or Markforged Mark Two are for you. In case you’re after simple usability, buy XYZ PartPro300 xT. And finally, as the cream of the crop, MakerBot METHOD X Carbon Fiber Edition is the best choice.
Armed with any of these printers, you’re ready to start producing parts that stand out from the rest with their toughness and durability.
Carbon Fiber 3D Printing Guide: Printers and Materials
Bicycles, race cars, drones and tennis rackets all have a variety of applications and require high strength and durability without added weight. This combination of properties is typical of carbon fiber composites, which are used in everything from Formula 1 racing car chassis to lightweight road bike frames.
Since many 3D printers commonly use polymer-based materials, including various composites, many people ask the question, "Can a 3D printer print carbon fiber?". nine0003
Indeed, there are two methods by which 3D printing can be used to create carbon fiber parts: supporting traditional fabrication methods with 3D printed molds, or direct 3D printing of carbon fiber composites. In this article, we'll look at traditional fabrication methods as well as new workflows for 3D printed carbon fiber molds and direct 3D printed carbon fiber composite parts.
Combining traditional carbon fiber parts with 3D printing
Carbon fiber is a composite material traditionally made by weaving long strands of carbon fibers together and then bonding them with a polymer. The yarns can be woven strategically so that the strength is directed along one specific vector, or so that the final product has multiple strengths in all directions. The resulting material is then molded into the desired end product using one of three processes: wet laid, pre-laminated, or resin transfer molding (RTM). nine0003
Wet Laid
Wet laid carbon fiber sheets are cut and pressed in a mould, then dyed with a liquid resin that cures to bind the sheets into the desired final shape. This method requires the least equipment and is the easiest to master for a beginner. Because most of the work can be done by hand, this is one of the cheapest methods, but the trade-off is that the resulting parts are less accurate to the master mold than parts made by other methods. nine0003
Prepreg lamination
In this method, the carbon fiber is already impregnated with resin and then placed in a mold that uses pressure and heat to form the final shape. This method is the most expensive due to the need for specialized equipment to store and process the pre-impregnated sheets, as well as a heated and pressurized forming machine. These factors also make it the most repeatable and consistent, and thus the most suitable for serial production of carbon fiber parts. nine0003
Resin transfer molding (RTM)
In RTM molding, the dry fiber is inserted into a two-part mold. The mold is clamped, after which high-pressure resin is injected into the cavity. This method is usually automated and is used to produce large volumes of products.
3D printed carbon fiber parts
For each of the three previous methods, 3D printing can be used to reduce costs and improve production times. All three traditional manufacturing methods require the use of a mold or multiple molds, which are traditionally created through labour-intensive subtractive processes such as wood, foam, metal, plastic or wax. 3D printing offers an alternative way to make molds. 3D printed molds are customizable and are more efficient and cost effective for small batch or custom production. nine0003
For applications requiring live prototypes, such as the automotive and aerospace industries, the iterative process can require hundreds of different shapes. Producing such iterations with traditional manufacturing methods can be costly and time consuming, so 3D printing provides an efficient way to produce small batches. Although 3D printed molds are not as suitable for high-volume production as metal molds, they can be created in-house, reducing costs, speeding up product development and validation, and short-term production. nine0003
Carbon fiber molds can be made in a variety of ways, but the smooth surface and wide choice of materials for SLA 3D printers make them a common choice for mold making in the factory. SLA-created parts have virtually no layer lines or porosity, so carbon fiber sheets can be pressed tightly into the mold without the fear of creating a textured surface.
Panoz, a manufacturer of racing and sports cars, needed a custom race car cabin duct to bleed the air out of the cabin and cool the temperature inside. In collaboration with DeltaWing Manufacturing, they used a Formlabs SLA 3D printer to print a high temperature resin part and then manually molded that printed part using high temperature epoxy for tooling. By using 3D printing, DeltaWing avoided outsourcing the costly metal mold for this custom carbon fiber part, reducing overall costs and delivery times. nine0003
Carbon fiber wing duct next to two piece mold printed with High Temp Resin made by DeltaWing Manufacturing.
Direct Carbon Fiber 3D Printing
Looking for the best carbon fiber 3D printer? There is a strong demand for workflows that combine the strength, durability and wear resistance of traditional carbon fiber parts with the maneuverability, geometric capabilities and cycling of 3D printing. Therefore, it is not surprising that there are many companies offering 3D printing using carbon fiber, with two methods currently available: printing using chopped or continuous fibers. nine0003
Chopped Carbon Fiber 3D Printing
Chopped Fiber refers to 3D printing composite plastic materials that are impregnated with small pieces of carbon fibers. These crushed fibers add strength to the composite, which can be carbon fiber filament for FDM modeling or nylon powder for SLS 3D printing.
The main advantages of chopped carbon fiber reinforced materials over other types based on polymers are that they are strong, light, heat resistant and less prone to deformation. Compared to traditionally molded carbon fiber parts, chopped fiber 3D printing provides increased geometric flexibility in part design, especially in SLS 3D printing, potentially eliminating the labor involved with traditional molding or opening up innovative new opportunities for users to incorporate this material into the working process. nine0003
The Formlabs Fuse 1+ 30W SLS 3D Printer enables this type of carbon fiber 3D printing with Nylon 11 CF Powder, the strongest material in the Formlabs SLS material library. Fuse 1+ 30W is the most affordable high performance SLS printing option for shredded carbon fibers. Although traditional industrial SLS machines also offer some carbon fiber materials, the initial implementation costs negate much of the added value of 3D printing carbon fiber parts over RTM or prepreg lamination methods. nine0003
Formlabs Nylon 11 CF Powder is strong, lightweight and heat resistant making it ideal for the automotive, aerospace and manufacturing industries .
Many FDM 3D printers can handle carbon fiber filaments, but these materials are more difficult to print than standard ABS or PLA filaments, resulting in more clogs and more maintenance as the brass nozzles wear out. FDM 3D printers specifically designed to grind carbon fiber filaments are also available but are more expensive. nine0003
The main limitation of chopped-fiber printed parts using both SLS and FDM technologies is that they should be considered as more durable 3D printed parts, rather than a true alternative to traditional woven and continuous carbon fiber parts. fibers. They also provide the greatest increase in strength by positioning them in the X-plane direction for SLS printing, and in the XY-plane direction for FDM printing. Traditional methods of creating carbon fiber parts provide multidirectional strength through careful planning and placement of different carbon fiber sheets in a preform. nine0003
Carbon Fiber Continuous 3D Printing
Carbon Fiber Continuous 3D Printing is available on some dedicated FDM 3D printers, and the resulting parts are close in strength to traditional carbon fiber parts, but similar to chopped fiber printers FDM, only in the XY plane. In such printers, continuous filaments of carbon fiber are mixed with a thermoplastic and the filaments can be applied strategically to selectively pressurize certain planes or axes. This method can use either a dual extruder nozzle to lay down a combination of carbon fiber and polymer filaments, or a 2-in-1 in which one nozzle lays down the carbon fiber filaments and the other heats and extrudes the filament. nine0003
Continuous carbon fiber 3D printing offers an alternative comparable to traditional molded carbon fiber parts, albeit with limited design freedom. While these parts are incredibly strong, strength only appears in the XY planes and the models must be oriented so that their strength matches the direction of the applied force. In designs where possible, this method can be used to replace aluminum parts, as well as to create durable manufacturing aids or end-use parts. nine0009
Applications for 3D printed carbon fiber parts
The high strength, light weight, and impact, heat and chemical resistance of carbon fiber printed parts make them ideal for a variety of applications where 3D printing has never been was not considered. Now, these plastic and carbon fiber composite parts can withstand the heat generated by automotive or aerospace engine components, be used as a replacement for machined aluminum parts and manufacturing fixtures, and produce durable and impact-resistant equipment. nine0003
3D printed carbon fiber parts are ideal for rapid prototyping, the production of wear-resistant and durable production fixtures such as tooling and fixtures, and for low-volume production of durable end-use parts with complex geometries.
3D printing technology has opened up new possibilities in design and manufacturing, and 3D printing of carbon fiber composites has further expanded these possibilities, allowing users in the automotive, aerospace, defense, and manufacturing industries to quickly and efficiently produce high-strength, heat-resistant, geometrically flexibility. By bypassing traditional machining or molding processes, these users can more easily create custom parts, replacement parts and functional prototypes. Although carbon fiber printed parts are not a complete replacement for traditional technologies due to the single plane of added strength, they are still stronger than almost all other plastics, making them exceptionally useful in many applications. nine0003
The right process for producing carbon fiber parts by molding or directly by 3D printing depends largely on the specific application and factors such as part design, production volume, and more. SLS 3D printing with shredded fibers offers the best option for those who want to produce parts that are strong, but not necessarily to the same degree as traditional molded carbon fiber parts.
Formlabs Fuse 1+ 30W with Nylon 11 CF Powder enables low-funding, fast-paced businesses to quickly iterate and produce end-parts with strength and better mechanical properties than traditional plastics. They can also functionally test their parts and then redesign with only minor CAD changes, improving their product performance and getting to market faster. nine0003
ALL YOU NEED TO KNOW ABOUT CARBON FIBER 3D PRINTING
top sellers
-
Bearing 604UU U604ZZ
U-bearing U604ZZ 604UU 4*13*4
35.
00 UAH
nine0123 -
Buy epo3d+ 3D printer nine0121
Epo3d+ Ukrainian FDM 3D printer on HIWIN rails. Thanks to reliable...
UAH 35,000.00
-
ABS granules
ABS granules for extrusion
400.00 UAH nine0003
-
PLA
PLA environmental plastic from Plexiwire.
100% advance payment....
UAH 375.00
-
Buy ABS plastic (ABS) nine0121
ABS plastic from Plexiwire. 100% prepayment. Free shipping...
UAH 220.00
-
Mini motor reducer 12v 100 rpm
high torque mini electric motor. Its size...
150.00 UAH
-
Nozzle for 3D printer 1.75 mm, for E3D and MK8 hotends
Nozzle for 3D printer 1.75 mm 0.2/0.3/0.4/0.5
35.00 UAH
nine0130 -
PETG plastic for 3D printer
PETG plastic from Plexiwire.
100% prepayment. Free...
UAH 360.00
-
SHF-20 shaft support nine0121
SHF-20 shaft support is used for CNC
60.00 UAH
-
A4988 stepper motor driver
35.00 UAH
nine0123
Thermal mat for 3D printing 200 x 200 mm
3D printing thermal pad
150.00 UAH
Buy epo3d 3D printer
Ukrainian epo3d 3D printer built on the basis of modern kinematics...
UAH 18,000.00
All best sellers
Information nine0003
ALL YOU NEED TO KNOW ABOUT CARBON FIBER 3D PRINTING
Before you get started with carbon fiber 3D printing, here are some basic information we've put together just for you. Read on and learn about the advantages, disadvantages, history and applications of carbon fiber 3D printing.
CARBON FIBER AS A MATERIAL
Carbon fiber comes in many shapes. Can be used together with resin and molds; it can be combined with polymers in composite form. It has been used for everything from light bulbs to high-performance racing cars - and has even been tested on rockets flying to Mars. Despite its wide range of applications, the most obvious advantage of carbon fiber is its high strength to weight ratio. nine0003
History
Carbon fibers were first discovered by Thomas Edison in the late 19th century for use as the filament in early light bulbs. In the late 1950s, the Union Carbide Corporation first recognized the strength advantages that could be achieved with additional processing methods. Over the next 50 years, manufacturing technology advanced further, and today carbon fiber has become a ubiquitous high performance product, from racing cars to airplanes. nine0003
Production
Generally, all carbon fiber is produced using a six step process. PAN (polyacrylonitrile) is obtained as a by-product of petroleum and is generally the material of choice for carbon fiber production. PAN is mixed with other ingredients and converted into fibers up to 10% of the thickness of a human hair. The fibers are then oxidized to stabilize the bond before undergoing carbonization, during which the fibers are heated to 1000°C to remove impurities. The surface is then treated to improve adhesion before the final sizing step, in which the fibers are coated and spun into threads of varying thicknesses. nine0003
These yarns can then be further processed in a variety of ways, depending on the end use. The yarn can be woven into sheets or, in the case of 3D printing, it can be cut into short fibers, mixed with a base polymer, and then extruded into a filament for a 3D printer.
Pre-cut carbon fiber for 3D printing resin
3D PRINTING WITH CARBON FIBER
3D printing with carbon fiber means choosing the right composites. The base polymer can determine the final properties of the part, as well as considerations that need to be taken into account when 3D printing. Below you will see various carbon fiber 3D printer composites and some of their strengths and weaknesses. nine0003
Nylon Carbon Fiber PA CF
Nylon Carbon Fiber is one of the most popular composites when it comes to 3D printer. This is because nylon already has desirable properties for engineering applications. It has a high degree of strength and high temperature resistance. It also has a high degree of strength that balances out the brittleness of the carbon fiber itself. A potential disadvantage of nylon is its hygroscopicity, which makes it even more important to have a protected environment for nylon carbon fiber spools such as a mylar bag and a sealed material compartment. nine0003
Carbon fiber ABS. ABS CF
ABS is a well known material due to its wide application in injection molded consumer products. In carbon fiber 3D printing, ABS works as a solid base polymer due to its properties. ABS carbon fiber also tends to have a very nice surface finish, which is almost always welcome whether the application is a prototype or part of a final product. One disadvantage of this connection is that it requires a heated 3D printer chamber, which is usually only found in higher end 3D printers. nine0003
Carbon fiber PETG CF
PETG is a material known for its resistance to chemicals and moisture in general, making it a good composite resin for 3D printers under exposure conditions. Examples of such applications include parts that may come into contact with coolants or simply products that will be used outdoors in rainy climates.
Carbon fiber PEEK CF
PEEK is one of the most efficient thermoplastics ever invented.
PEEK-CF thread includes carbon fibers for added strength. Chopped carbon fiber gives printed parts high rigidity and dimensional stability. This material provides long term performance up to 240°C including exceptional chemical resistance. These properties make it particularly suitable for metal replacement in critical end-use applications such as oil and gas, aerospace and automotive. The flammability of PEEK-CF is low, as well as the emission of smoke and toxic gases. nine0003
Due to its high mechanical properties, PEEK-CF is used for critical applications, in some cases even allowing the replacement of metal parts of the structure.
(Alternative) Fiberglass
Carbon is not the only filler for 3D printer composites. Fiberglass is an alternative to carbon fiber 3D printing when a more flexible end product is required. It can be combined with many materials of the same type and can provide high strength in the same way as carbon fiber. nine0003
BENEFITS
➜ Strong and lightweight: Carbon fiber's best known property is its strength to weight ratio, which is why it is often used in high performance products.