Maintaining and troubleshooting your 3d printer pdf
š„ The definitive guide to solving 3D printing problems by Bitfab
š¤¬Having problems with your 3D printer? Youāve come to the right place.
In Bitfab we have prepared the definitive guide to solve all your 3D printing problems. Thousands of hours of professional 3D printing behind our back to help you with the setbacks you have with your printer.
And we not only give you the keys to diagnose your printing errors but also the best tips to prevent them from reappearing, fix your printer and calibrate. Pictures, videos and our best tips in a mega article.
š Enjoy the guide and use the index if you want to go to directly to the part that interests you.
š What do you want to read?
𤬠The most common defects and problems in 3D printing
We have put together a collection of the most common problems that arise when using our 3D printer. They are the same problems that we commonly encounter in our online 3D printing service, and so we have quite a bit of experience dealing with and solving them.
A well calibrated printer, correct lamination and an experienced operator are key to avoiding these problems. By having that you will be able to solve any printing problem.
If you experience any of these issues, follow the instructions we give you and if you still canāt solve them, you have the comment box at the end of the article to tell us your doubts.
ā Warping, the first layer peels off and the parts bend
Warping is a decreasingly common problem, as the vast majority of modern printers have hot beds. In any case, warping can be caused by the following factors:
- Lack of adhesion to the bed: this can occur due to incorrect height of the nozzle in relation to the base, or poor leveling; but also lack of adhesion to the printing surface.
- Thermal contraction of the upper layers, which when āshrinkingā pull on the lower layers. If this occurs, the print surface may even break if it is a BuildTak type, as the sticker will be torn off the bed.
This can also happen with glass. This happens mostly with materials such as ABS or Nylon, and it is very difficult for it to happen when printing PLA.
Depending on our problem we can look for a solution accordingly:
For the lack of adhesion there are several solutions. If we are using a glass base, it is highly recommended to use some adhesive to increase the fixation of the part. Some known adhesives are the famous Nelly hairspray, or its more professional version 3Dlac. If we are using ABS we can apply a layer of the mixture known as ABS slurry which we can make ourselves by dissolving ABS in a container with acetone.
If your problem is related to thermal contraction, increasing the adhesion will not help you too much since, as we have said, the ABS when deformed can even break our printing base. To solve this problem we can simply cover the printer with whatever we have at home. A large box can work, as well as a more professional enclosure made in a closet.
The idea in this case is to enclose the heat generated by the bed, so that there is not much difference between the temperature of the first layers and the temperature of the upper layers, which are farther away from the heat of the bed.
Hereās an article that we made explaining this problem more in depth: How to avoid warping and cracking in my 3D prints.
ā Cracking or delamination
Following on from the above problem is cracking or delamination. We talk about cracking when the layers of a part are not well joined, resulting in these layers being separated (hence the name delamination). This problem can be caused by two different reasons:
- Poor adhesion between the layers: the layers do not stick properly to each other.
- Thermal shrinkage: the layers stick together well, but a difference in temperature between different sections of the part causes it to deform, which can cause some layers to separate.
If the problem is lack of adhesion, it is usually due to low of temperature. Most filaments have a temperature range in which they can be printed.
Within this range, lower values will give us a better aesthetic appearance, since the deposition will be ācleanerā. Conversely, higher values will give us better layer adhesion. Printing materials such as ABS at less than the proper temperature often leads to cracking when trying to bond two layers without applying enough heat.
To check if our part is cracking due to lack of adhesion between the layers, we can try to raise the temperature and/or reduce the speed of the layer fan, as excessive cooling can also affect it negatively. Some materials, like ABS, will always be prone to cracking and will be more difficult to control; others like PLA are very easy to print without cracking.
On the other hand, if our problem is thermal contraction the solution is more complicated, as we must manage to create a warmer environment in our printing area. The optimal solution would be to cover our printer, as indicated in the previous point. This can result in some problems, since an excessive temperature can lead to failures in the electronics: missing steps or losing printing artifacts⦠it can also cause clogging, since there is not enough difference in temperature between the cold zone and the hot zone of the hotend.
In general, avoiding draughts (and the consequent temperature variations) and covering our printer will help, but we must be careful to avoid the problems mentioned.
ā Layer shift
Layer shifting is a problem that occurs in the form of a displacement on some axis at a certain height. It can occur in the X-axis, the Y-axis or even both simultaneously. The most common causes of layer shifting are:
- Excessive temperature in the motors, or drivers: the electronics in general are not designed to operate continuously at a very high temperature.
- Lack of power in the motors, usually caused by a very low voltage value in the drivers.
- Mechanical failure: it can happen that we have some of our beltās teeth broken, or there is some debris on the shafts that can cause a jam in the movement of our printer.
Sometimes a wrongly tightened component can also cause layer displacement defects when the whole shaft moves freely.
A general advice would be to put heatsinks, and if possible ventilation, to the drivers of our board. These components basically take care of sending all the necessary air flow to the motors, so they tend to heat up. Likewise, if our printer operates in very hot environments it would be appropriate to add some heatsink to the X and Y axis motors as well. If the drivers are very hot, you will usually hear a knock, knock, knock on the motors when the drivers are briefly disconnected to give them time to cool down.
Additionally, you can check if your printer has drivers with adjustable voltage, and if so, you can increase this voltage slightly by carefully turning the potentiometer on each driver. Be careful when doing this, and always do it with the printer turned off or using a ceramic screwdriver to avoid short-circuiting with a metal screwdriver. If you turn up the power on the motors too much you risk falling into the overheating problem again.
Finally, check that the shafts of your printer are clean and free from obstructions. Also check that the belts and bearings are not too tight (if the bearings are tightened with flanges or screws). Shafts that do not move well, over-tightened belts⦠cause motors to work harder and may lose steps.
ā Z-wobble
This problem can be difficult to identify, as it is often not easy to distinguish it from a simple inconsistency in the extrusion. To identify it we must look at whether this inconsistency is repeated on a regular basis. If it seems random, or just noise in general, your problem is probably not z-wobble but an extrusion problem. Conversely, if there seems to be a pattern that repeats periodically such as waves on the surface, you may well have a problem with your Z-axis.
This problem is mostly due to structural failures in the construction of the machine, and is difficult to solve without making major modifications to our machine chassis. First of all check that all the parts are properly assembled, maintaining the perpendicularity and making sure that there are no loose screws.
Try to tighten all the screws on the couplers that connect the z-axis motors to the spindles. Also check that there is no wobble between the spindle and the trapezoid nut. It is complicated to give a correct solution, because the axis needs some freedom to move to compensate small errors in the chassis, such as corners that are not perfectly perpendicular.
A good solution that is not too expensive is to replace the motor-coupler-spindle assembly with a motor with a built-in spindle. We can also add reinforcements to our printer so that the frame of the printer does not wobble at the top.
ā Stringing
Stringing is one of the most common problems in novice parts in the world of 3D printing, so if your parts have a lot of strings donāt worry, itās totally normal and quite easy to solve.
Stringing appears when, as the hotend moves between two sections of our print, a small amount of plastic drips off and sticks to both sections, leaving a small thread in between.
This problem can be caused by the use of a bad quality hotend, but usually the machines have a hotendsn of sufficient quality, so the problem almost always comes from bad lamination in the slicer.
The most important parameters you should check in your slicer to minimize the stringing are the following:
- Temperature
- Retraction distance
- Retraction speed
Temperature is a vital factor and probably one of the 5 most important settings in your profile. If you have a lot of stringing you are almost certainly melting at too high a temperature. Remember that all materials have a range of temperatures in which they can be printed, so try lowering the temperature and bringing it closer to the lower limit recommended by the manufacturer. If you are already using a very low temperature and still have stringing, check the following points.
While it is not possible to āsuckā plastic out of the nozzle, as no negative pressure can be created, it is possible to minimize the pressure on the nozzle by pulling the filament out of the hot zone of our hotend. The shrinkage distance is very dependent on our printer, as both the melter and extruder and the type of extrusion (direct or bowden) must be considered. Most bowden printers perform well with a shrinkage value between 3mm and 6mm, and direct extrusion printers between 0.5mm and 2mm.
The speed of retraction is another important factor, as the higher the speed the lower the stringing. This speed will depend on the motor of our extruder and also on the type of extrusion (1:1 vs 3:1 like the Titan extruder). Generally values between 40 mm/s and 60 mm/s usually work, but if you have any doubt, please ask in a forum or group dedicated to your specific printer.
Additionally, almost all slicers or laminators have different more advanced settings that can help reduce the stringing, but these will only be of importance if the three previous ones are well adjusted. This is a very broad topic and we could make an exclusive guide about this problem, so if you want to see it, leave us a comment!
ā Overheating, curling
One of the easiest problems to diagnose is overheating.
As we can see in the image, melting our plastic at an excessive temperature will cause the parts to look deformed, with the center of the layer sunken. This is because when melted at too high a temperature, the material does not have time to cool down, and that is why the layers can collapse or sag.
These deformations will be much more pronounced in small areas, such as small peaks of our part, where instead of a clean figure, a deformed churro will remain.
The solution to this problem is simple: lower the temperature. We must also play with the values of the layer fan, since a high temperature can favor a more fluid extrusion and we can compensate this temperature with a good cooling. In this way the material will be cooled down quickly and we will be able to obtain optimal results.
ā Elephantās foot
The elephant foot is a defect consisting of the expansion in the horizontal plane of the first layers of our part. It can occur due to two things or, normally, a combination of both: the nozzle is too close to the bed or the temperature of the bed is too high.
If the nozzle is too close to the bed, it is obvious that the first layers will be more flattened and therefore expand in the XY plane. To solve this problem we must correctly level our first layer, as indicated in a previous section of this article.
An excessive bed temperature (say, 90 or 100 degrees for PLA) can cause the newly deposited plastic to expand and deform, causing this very characteristic effect.
ā Ghosting, ringing
The best article on this topic on the internet is the 3D Campy post by 3DSpana about ghosting, because he dedicated himself to try different combinations and components, taking pictures of the results, so you can see how decreasing the weight of the axes affects ghosting. If you prefer it on video, hereās the summary:
š Keys to print correctly with your printer
Youāve seen the list of problems weāve collected. Now you have to know how to DO things.
Knowing your printer and laminator is the key to error and defect-free printing, so here are some tips to avoid problems and help you diagnose and fix them:
ā Printing speeds
One of the most common mistakes we find on beginners is wanting to print too quickly on their first parts.
The printing speed is one of the most important printing parameters to obtain the best printing quality and an excess of speed affects the part very negatively for many reasons: vibration, extrusion problems, overheating, loss of stepsā¦
One of the first things you have to do when you encounter a problem is to reduce the printing speed to see if it is solved. We usually print almost all parts between 40 and 60mm/s, no more is needed for most cases. In a printing service the most important thing is reliability and when you are looking for reliability it is best to print at reasonable speeds so you donāt have to throw the parts away.
It is not necessary to print your parts at 100mm/s, especially the first ones. Yes, we all know someone who does it and gets it done, but itās not the best way to make sure they come out right.
ā Bed adjustment and leveling
Learning to set the bed correctly level and the extruder at the right height is one of the first steps we take with a new 3D printer.
Hereās what a properly adjusted bed looks like: the height of the first layer has to be correct across the entire surface of the bed.
First layer too close
If your first layer is too close to the printing surface, you can cause jams, scratches on the bed, parts with the wrong dimensions, elephant footā¦
Correct first layer
When the first layer is correct, the threads deposited by the extruder touch each other and are not too flat against the bed.
First layer too separate
A very separate first layer can be noticed by the separate threads.
Parts printed in this way are usually detached from the bed or warp.
And how do you properly level a hot bed? Our preferred technique is paper in the corners. It is not necessary to have a printer with self-leveling, the best thing is to have a reliable and well calibrated printer to print with quality.
ā How to prevent and fix extruder clogging
Extrusion jams are the number one cause of failure on a farm like ours. You may have mastered your printer but the jams are always going to be there, so itās critical to understand them and be able to prevent and fix them.
If you donāt yet understand how a 3D printer extrusion works and what the common terms for referring to them are, you can first check out our guide to 3D extruders.
Causes for clogging
Clogs arise from many different causes, sometimes in conjunction with each other. I believe the best way to solve them is to first understand all those causes and then try a series of techniques that can help fix them.
- Contamination at the tip and print canal. Impurities that are deposited in the print canal or at the tip of the nozzle and hinder or completely block the flow of the filament.
- PTFE/teflon degraded. Teflon hotends in the hot zone require maintenance of the Teflon, which when degraded clogs the filament flow.
- Extruder problems. Maybe your extruder is not working properly:
- Too much tension or too little tension in the dock
- Low voltage in the driver that does not give enough power to the motor
- Dirty thrust wheel, with teeth covered with filament debris
- Any loose or broken parts
- Scratching the filament. This is very, very important to understand. When we see the scratched filament, nibbled by the extruder wheel, it is not always the cause of the clogging. All printing clogs, whatever the cause, end up scratching of the filament. And only those clogs that are due to spring tension and excessive shrinkage are the root cause of the clog itself.
- Tip scratching the base. If the first layer is too low, it can interrupt the flow of the melted plastic and quickly cause a clog in the extrusion system.
- Watch out for shrinkage. A part with a lot of very fast retractions can end up scratching the filament. And long, slow retractions can overheat the cold zone of the extruder and cause clogging as well. In general, retractions wonāt cause your clogs, but you should always keep an eye on them.
- Poor cooling. Cooling is a fundamental variable in all-metal hotends. If your extruder is 100% metal like the E3D V6 you have to be very careful with this and with excessive shrinkage.
Unclog the nozzle with acupuncture needles
The technique of passing an acupuncture needle through the printhead is most useful if the real cause of your clog is an impurity. The nozzles themselves last many hundreds or even thousands of hours of use, so you will almost never have to change them.
Most likely a particle has been deposited in the nozzle and you should be able to get it out with the needle. We heat the head and stick the needle while hot, and then pull out the filament with the particles that might be causing the clogging embedded in the molten filament.
Repeat this process until the plastic comes out of the nozzle again easily.
Hot and cold pulling
The pulling takes a little longer to do than using the acupuncture needle, but it cleans the impurities better and also takes away the filth not only from the tip, but from the whole interior of the hotend.
They are easier to explain with a video like the one below:
Teflon switching
In hotends with Teflon liner it is necessary to change this component, in general, every several hundred hours. The Teflon or PTFE liner is a small tube that goes in the hot zone of your hotend to guide the filament in the last centimeters of run, and that is degraded due to the temperature it reaches. Changing it is a job that you will have to learn to do to properly maintain your printer.
Before the tube degrades completely, you will notice that your printer is having more and more trouble printing, the filament thread that comes out is thinner and itās harder for it to deposit material on the parts that you print faster.
In every printer the change of Teflon is different, but here is the example of the Hephestos 2 from BQ to help you understand it better.
Adjusting the printing parameters
There are clogs that can occur because our laminate is not well adapted to the type of part and printer we are going to use.
To allow your printer to extrude more easily you can try:
- Printing slower
- Printing at a higher temperature
- Printing thinner layers
- Reducing the flow rate if you have more than 100%
These are all tricks that reduce the requirements on the extruder and melter because they require less flow through the hotend and heat the plastic to make it more fluid.
Retractions can also influence extrusion problems:
- Too many or too fast retractions can result in scratching of the filament in the extruder.
- Too long or too slow retractions can cause cooling problems in your melter (especially if it is all-metal) or end up clogging the plastic in the cold zone of the melter.
If you donāt know how to fix it, dissasemble the extruder and hotend
The best way to attack a mechanical problem that you donāt know how to solve is to proceed to disassemble what you want to fix. Taking apart a hotend and an extruder is quite simple and will allow you to see inside what is happening and reflect on the problem.
When you dismantle your extruder you will notice that there are some broken parts, dirt somewhere, some loose screwsā¦
If you disassemble the hotend you will be able to see the state of the Teflon, the tension of the hotend threads and if there is print residue deposited in the filament canal.
In either case, take the opportunity to clean the parts to prevent errors in the future.
š Thatās it for the 3D printing troubleshooting guide by Bitfab
Thank you so much for getting this far.
If you have any doubt or a different problem just put it in the comments and we will help you solve it, or maybe even add it to the rest of the problems š
š Greetings and thanks again!
3D Printer Troubleshooting Guide | MatterHackers
Use this guide to help you identify and solve the most common issues that may occur while 3D printing.
Updated on January 3, 2023
by
MatterHackers
When printing, unexpected challenges may arise that will need to be resolved in order to complete a successful print. Ā Often times, the appropriate response to a printing issue is not immediately apparent.Ā This guide outlines some of the most common issues faced by 3D printing practitioners and highlights steps that may be taken to resolve those issues.
Not extruding at the start of the printĀ | Print not sticking to bedĀ | Jammed nozzle/clogged extruderĀ | Pillowing, e.g. incomplete top layer fills, top layer holes/gapsĀ |
Smashed first layer, aka elephantās foot; bulging first layerĀ | Warping or coner liftingĀ | Layer separation or warping within the partĀ | Shifted layers or leaning printsĀ |
Stringing / hairy printsĀ | Overhangs or sagging sections in the printĀ | Support material difficult to removeĀ | Under extrusion, e.g. not extruding enough plastic or insufficient materialĀ |
Grinding filament and/or extruder motor skippingĀ | Small features not printedĀ | Scars on top surfaceĀ | Blobs and/or pimples on exterior surfaceĀ |
Weak infillĀ | Stops extruding in the middle of a printĀ | Infill showing on exterior of printĀ |
The guide is organized into a table with the following format. Ā
Issue/Title | This highlights the action of a printer or print result that is not optimal or correct. This is comparable to a medical examination where the doctor inquires about the symptoms or behavior the patient is exhibiting or experiencing while being ill. |
Example Image/Graphic | This is an image or graphical representation of the issue. |
Issue Details | This provides additional information on the issue from actions during printing or the results upon completion. |
Cause and Suggested Solutions | This lists in order from highest to lowest probability the source or cause of the issue and suggested solutions to follow for issue resolution. |
Not extruding at the start of the print
Print not sticking to bed
Jammed nozzle/clogged extruder
Pillowing, e.g. incomplete top layer fills, top layer holes/gaps
Smashed first layer, aka elephantās foot; bulging first layer
Warping or corner lifting
Layer separation or warping within the part
Shifted layers or leaning prints
Stringing / hairy prints
Overhangs or sagging sections in the print
Support material difficult to remove
Under extrusion, e. g. not extruding enough plastic or insufficient material
Grinding filament and/or extruder motor skipping
Small features not printed
Scars on top surface
Blobs and/or pimples on exterior surface
Weak infill
Stops extruding in the middle of a print
Infill showing on exterior of print
How to Level Your Print Bed
If you are specifically running into issues that relate to having an unlevel printing surface, please refer to ourĀ Anatomy of a 3D Printer: Bed Leveling article - it has comprehensive solutions for any type of leveling system!
Click here:Ā The Anatomy of a 3D Printer: Bed Leveling
Troubleshooting Guide Not Extruding At The Start Of The Print Issue/Title | Not extruding at the start of the print |
Example Image / Graphic | |
Issue Details | Print grooves left in bed with no filament and/or flaky or intermittent lines of filament on the first and subsequent layers |
Cause 1 | Incorrect extruder calibration/offset |
Suggested Solutions 1 |
|
Cause 2 | Clogged extruder/nozzle |
Suggested Solutions 2 |
|
Issue/Title | Print not sticking to bed |
Example Image / Graphic | |
Issue Details | Insufficient bed adhesion |
Cause 1 | Bed is not level |
Suggested Solutions 1 |
|
Cause 2 | Incorrect nozzle calibration/offset |
Suggested Solutions 2 |
|
Cause 3 | Improper bed surface or settings for filament |
Suggested Solutions 3 |
|
Issue/Title | Jammed nozzle/clogged extruder |
Example Image / Graphic | |
Issue Details | Extruder is unable to feed filament through nozzle and is often accompanied by a grinding or āclickingā sound from the feed motor |
Cause 1 | Heat creep for PLA |
Suggested Solutions 1 |
|
Cause 2 | Particle or carbonized filament blocking nozzle |
Suggested Solutions 2 |
|
Issue/Title | Pillowing, e.g. incomplete top layer fills, top layer holes/gaps |
Example Image / Graphic | |
Issue Details | Pillowing is usually PLA filament specific |
Cause 1 | Layer cooling too fast for PLA |
Suggested Solutions 1 |
|
Issue/Title | Smashed first layer, aka elephantās foot; bulging first layer |
Example Image / Graphic | |
Issue Details | Side profile of the printed part shows a bow near the bottom or next to the surface that was adjacent to the print bed |
Cause 1 | Bed is not level |
Suggested Solutions 1 |
|
Cause 2 | First layer height is too low |
Suggested Solutions 2 |
|
Cause 3 | Extrusion rate for the first layer is greater than 100% |
Suggested Solutions 3 |
|
Issue/Title | Warping or corner lifting |
Example Image / Graphic | |
Issue Details | Edge near the bottom of the print or surface adjacent to the print bed is not level or flat |
Cause 1 | Materials, e. |
Suggested Solutions 1 |
|
Cause 2 | Design of part has sharp corners or thin areas |
Suggested Solutions 2 |
|
Issue/Title | Layer separation or warping within the part |
Example Image / Graphic | |
Issue Details | Layers do not adhere to previously printed layers and pulls from print bed |
Cause 1 | Print temperature is set too low |
Suggested Solutions 1 |
|
Cause 2 | Too much layer cooling during and after deposition |
Suggested Solutions 2 |
|
Cause 3 | Ambient air temperature is too cold and uneven |
Suggested Solutions 3 |
|
Cause 4 | Printer is printing too fast |
Suggested Solutions 4 |
|
Issue/Title | Shifted layers or leaning prints |
Example Image / Graphic | |
Issue Details | Layers shift in the z-direction as print progresses |
Cause 1 | Printer is printing too fast |
Suggested Solutions 1 |
|
Cause 2 | There nozzle is getting caught on raised or warped sections of the print |
Suggested Solutions 2 |
|
Cause 3 | There are loose pulleys on the x-axis and/or y-axis |
Suggested Solutions 3 |
|
Cause 4 | Belts are skipping teeth on the x-axis and/or y-axis |
Suggested Solutions 4 |
|
Issue/Title | Stringing / hairy prints |
Example Image / Graphic | |
Issue Details | Filament in the hot end of the extruder continues to ooze out of the nozzle during non-print moves |
Cause 1 | Slow extruder movement between sections of a part or more than one part |
Suggested Solutions 1 |
|
Cause 2 | Length of filament retraction is too short |
Suggested Solutions 2 |
|
Cause 3 | You are printing with PET |
Suggested Solutions 3 |
|
Cause 4 | Printer crosses gaps when moving from one place to another |
Suggested Solutions 4 |
|
Issue/Title | Overhangs or sagging sections in the print |
Example Image / Graphic | |
Issue Details | Unsupported or protruding part faces may not print properly or not print at all |
Cause 1 | Design of model or positioning of part |
Suggested Solutions 1 |
|
Issue/Title | Support material difficult to remove |
Example Image / Graphic | |
Issue Details | Removing supports is difficult due to fused support material with the initial part layers and often results in pitted initial layers once supports are removed |
Cause 1 | No gap or layer height offset between support layer and initial part layer |
Suggested Solutions 1 |
|
Issue/Title | Under extrusion, e. |
Example Image / Graphic | |
Issue Details | Under extrusion is identified by āsilkyā residue or gaps between extrusion lines or layers |
Cause 1 | Printer settings for filament size is incorrect |
Suggested Solutions 1 |
|
Cause 2 | Filament extrusion temperature is too low |
Suggested Solutions 3 |
|
Cause 3 | Nozzle or extruder may be clogged or not properly calibrated |
Suggested Solutions 3 |
|
Issue/Title | Grinding filament and/or extruder motor skipping |
Example Image / Graphic | |
Issue Details | Noise from the feed motor makes a grinding or clicking sound |
Cause 1 | Heat creep from the extruder that creates a ābulbā at the end of the filament between the gear and the extruder |
Suggested Solutions 1 |
|
Issue/Title | Small features not printed |
Example Image / Graphic | |
Issue Details | |
Cause 1 | |
Suggested Solutions 1 |
|
Issue/Title | Scars on top surface |
Example Image / Graphic | |
Issue Details | Filament residue is āleakedā upon the top of the print surface |
Cause 1 | Lack of z-lift or retraction between moves |
Suggested Solutions 1 |
|
Issue/Title | Blobs and/or pimples on exterior surface |
Example Image / Graphic | |
Issue Details | Ā |
Cause 1 | Ā |
Suggested Solutions 1 |
|
Issue/Title | Weak infill |
Example Image / Graphic | |
Issue Details | Ā |
Cause 1 | Ā |
Suggested Solutions 1 |
|
Issue/Title | Stops extruding in the middle of a print |
Example Image / Graphic | |
Issue Details | Ā |
Cause 1 | Ā |
Suggested Solutions 1 |
|
Issue/Title | Infill showing on exterior of print |
Example Image / Graphic | |
Issue Details | Infill structure is visible on the top, bottom or sides of a printed part |
Cause 1 | Infill shows on top or bottom surfaces due to insufficient number of top/solid bottom layers or wrong layer speeds |
Suggested Solutions 1 |
|
Cause 2 | Infill shows on side surfaces due to insufficient number of perimeters or too much infill overlap |
Suggested Solutions 2 |
|
Article Tags
- 3D Printing
- Firmware
- 3D Design
- MatterControl
- Press Releases
- Small Business
- Automotive
- E3D
- Jewelry Making
- Engineering
- Entertainment Industry
- MatterControl Touch
- ESD Materials
- NylonX
- BCN3D
- Open Source
- Crafty Pen
- Digital Fabrication Anatomy
- How To
- Hardware and Upgrades
- Tips and Tricks
- Weekend Builds
- Top Ten
- Education
- Tech Breakdown
- Women in 3D Printing
- Project Ideas
- Advanced Materials
- Reference
- Pulse Dual Extrusion
- Product Spotlight
- Aerospace
- Jobs
- Military & Government
- Multi-Tool Machines
- Getting Started
- Healthcare
- How To Succeed With Any 3D Printing Material
- Creality3D
- Architecture
- 3D Printer Reviews
- Hacker of the Month
Related Products
View all related products3d printer maintenance
3DPrintStory     3D printing process     3d printer maintenance
3d printer, like any other piece of equipment, needs maintenance. And if you havenāt done it until today, itās better to start right after reading this short article. nine0005
I won't categorize maintenance into daily, weekly, or monthly because each of you types at a different rate. For someone, a 3d printer can stand turned off all week, while for someone it works 24 hours a day. Therefore, to a greater extent, you yourself have to determine how often you will carry out maintenance on your 3d printer.
Have you ever heard of preventive maintenance? This is one of the pillars of the concept of general equipment care, the essence of which is that after the equipment has been used for a certain period of time, preventive inspections, various types of scheduled repairs and revisions are made, excluding the possibility of equipment operation in conditions of progressive wear. So you and I, as owners of one piece of equipment or a whole fleet of 3d printers, must track down the precursors of major malfunctions - whether it is extraneous noise during printer operation or an unscrewed screw. nine0005
Technical inspection of the 3d printer
Therefore, the first thing we will talk about today is the control and inspection of the 3d printer components to identify deviations that lead to breakdowns, which in turn can lead to equipment downtime. What should you pay attention to first of all?
Extruder. It is worth checking it for leakage of the plastic melt and the nozzle-cylinder interface, so the accumulation of polymeric material can form either from above or below the heating block. In case of detection, at least pull the nozzle, or rather, disassemble and clean all elements from polymer material. By noticing the leaking nozzle in time, we can prevent the failure of the thermistor heaters. nine0005
From the extruder, move on to the inspection of the kinematics. First to the shafts. Be sure to control the appearance of wear on the shafts, as it often happens that the user does not notice that the linear bearing is wedged, and corresponding marks, scuffs appear on the shafts. Up to a certain point, or rather, depth, they can be removed by grinding, and then not. Therefore, the sooner such wear is diagnosed, and the linear bearing is replaced, the less likely it is to get an expensive shaft replacement. nine0005
Just like shafts, belts are subject to wear. This can be either wear on the working surface of the belt or damage to the cord. In any case, during the inspection, check the condition and tension of the belt. Why tension? Because once you pull the belt, you can break the integrity of its cord. Naturally, such a belt will need to be changed. If you notice the wear of the belt in time, you will have time to order it and the 3d printer will not stand idle, waiting for the spare part to arrive.
Speaking of belts, it's worth checking stepper motor pulleys along with them. Namely, whether there is no idle rotation. If necessary, tighten the lock screws. Always check the kinematics of the 3d printer for any play. For the most part, play will affect the quality of the surface of the printed product, but this check should not be neglected. Take the carriage and move your hands to a break, try to pull it. If you do not notice characteristic knocks, then everything is in order. If you notice, then check the tension of the screws. Axes misalignment during 3D printing can also lead to both linear bearing failure and high shaft wear. nine0005
|
You should also check if the fan for blowing the 3d printer board and the extruder heatsink is working. I understand that in some models of 3d printers, the manufacturer did not worry about ease of maintenance, but this should not be neglected, as overheating can lead to failure of the stepper motor drivers.
If you have something to add to the inspection list, write about it in the comments, and we will go directly to maintenance. nine0005
3d printer maintenance
What actually needs to be serviced?
Let's start with cleaning. More specifically, from cleaning the filament feed mechanism. There are several ways to get it contaminated. You can get rid of one of them very easily by installing a so-called filament filter. It is a box with a sponge placed inside, which is designed to clean the bar from accumulated dust and other contaminants. A very simple thing. Link to the 3d model on Thingiverse. If you have a bowden extruder, you can clean the filament feed tube from dust by simply blowing it. nine0005
Your 3d printer table also needs to be kept clean. I periodically wipe it with a cloth dipped in acetone. It is better to do this procedure with a glove in order to avoid skin contact with acetone.
The table lift screw also needs to be cleaned of dust and dirt before being lubricated. As for the lubricant itself, I read a lot of opinions on this matter and came to the conclusion that the best choice is ordinary Litol-24. I use it both for lubricating screws and for lubricating linear bearings. We lower the table down, apply lubricant to the screw above the nut, then raise the table to the upper end position and apply lubricant from below the nut and drive the table again. Then, if excess grease has formed, remove them. nine0005
Also take the time to extruder. Clean the model fan and radiator from dust and dirt. The best way to do this is with a vacuum cleaner. In my 3d printer, the manufacturer did not bother about the ease of removing the extruder, so this procedure is quite time consuming.
Pay attention to the shafts. If your linear bearing seals are working well, then you should see a buildup of dust mixed with grease in the end positions of the axles. It is worth deleting it as it accumulates. The easiest way to do this is with a paper towel. nine0005
Moving on to the lubrication of linear bearings. In theory, they should be stuffed with the right amount of grease at the factory. Moreover, this basic packing is calculated for the entire life of the bearing, but whether the Chinese do it or not is unknown. When I bought linear bearings, I found that they are only covered with a liquid lubricant to prevent corrosion, so itās better to remove and stuff the same lithol inside, because it doesnāt make sense to smear it on the guides, since the seals will simply remove it and nothing will get inside. nine0005
Do not neglect the maintenance of your 3d printer and it will serve you faithfully for a long time! I hope the material was useful to you.
PICASO 3D Designer PRO 250
The PICASO 3D Designer PRO 250 User Manual will guide you through the operation of this professional grade 3D printer.
The first three sections show you how to properly and safely unpack and set up your printer. The following sections describe procedures for loading media, 3D printing, maintenance, and hardware troubleshooting. nine0076
In addition, this instruction manual will show you how to set up and start using your Designer PRO 250 today. Also, thanks to this manual for the PICASO 3D Designer PRO 250 3D printer, you will also get acquainted with the Polygon 2.0 and KISSlicer PRO software.
Author: | PICASO 3D |
Publisher: | PICASO 3D |
Website: | picaso-3d.![]() |
Free download (direct link) |
Description Designer PRO 250
- How the 3D printer works
- JetSwitch Technology
- Specifications
- Diagram Designer PRO 250
Setting up PICASO 3D Designer PRO 250
- Unpacking Designer PRO 250 3D printer
- PICASO 3D Designer PRO 250
- Removing the protective ties and connecting to the mains
Start: loading 3Dp plastic, testing
- Display. Control. 3D printer menu
- Consumables used for 3D printing
- Tips for proper storage and use of plastic
- Plastic installation in Designer PRO 250 nine0142 Checking print platform calibration after shipping
- Checking nozzle alignment after shipping
- Test print on Designer PRO 250 printer
Working with Polygon 2.
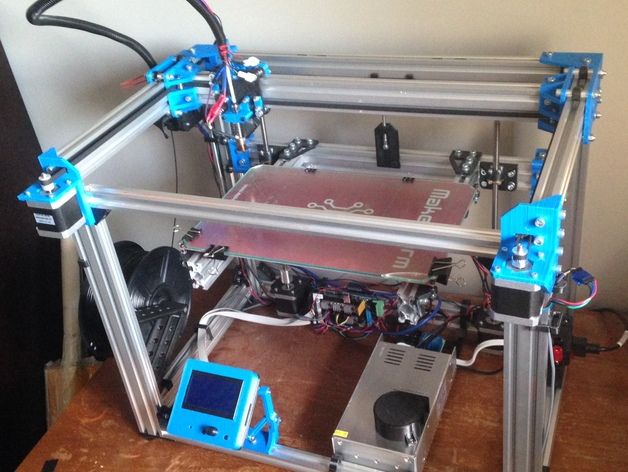
- Polygon 2.0. Download and install [Download from the official website]
- First run of the program
- Description of functions and menus
Work with Kisslicer Pro software
- KISSlicer PRO. Download and installation [Download from the official website]
- Description of functions and menus of the program
Printing a 3D model on the Designer PRO 250
- Loading a 3D model and preparing a job for printing
- Starting printing. Removing Model
- Preparing and printing a two-color model
Maintaining the Designer PRO 250 PICASO printer
- Applying varnish to the 3D printer bed
- Replacing the nozzle on the PICASO 3D Designer PRO 250 printer
- 3D printer nozzle alignment
- Calibration 0X and 0Y
- Valve replacement
- Print platform calibration
- Firmware update
- Preparing the 3D Printer for Shipping
- Troubleshooting Designer PRO 250 Printer
At the end of this manual, the manufacturer recommends that users use (if possible) the latest software version for the best and most stable operation of their 3D printer of this model.