3D styrofoam printer
FreeFoam, a Revolutionary, Expandable 3D Printable Resin Designed for Volume Production of Foam Parts
Team DM
Platforms
Metal and composites 3D printing 3D printing solutions for health care Industrial-grade polymer 3D printing™
Sand and tooling 3D printing solutions 3D printers for sheet metalMaterials
Breakthrough photopolymer development Advancing 3D printed upcycled woodApps & More
The hydraulic additive manufacturing experts Multi-material powder recoating technology Driving digital transformation in dentistry_Articles
Revolutionary, Expandable 3D Printable Resin Designed for Volume Production of Foam Parts
- Download Spec Sheet
FreeFoam is a new family of photopolymer resins that produces durable and dimensionally accurate closed cell foam parts without tooling – delivering all-new benefits for the automotive, furnishing, footwear, sporting goods, health care and other industries.
Manufacturing Closed Cell Foam without Tooling in an All-New 3D Printing Process
FreeFoam is a new family of photopolymer resins containing heat-activated foaming agents that are 3D printed with Digital Light Processing (DLP). After printing, FreeFoam parts are briefly put into an oven where the foaming agent creates closed cells inside the material in a tightly controlled process. FreeFoam can be programmed to expand a specific amount between 2 to 7 times its original printed size – allowing parts to be shipped in a compact form and expanded on-demand in an oven close to the final point of use or assembly, saving shipping and inventory expenses.
While 3D printers today can process photopolymers into lattice designs that simulate foams, FreeFoam is a true foam containing closed cells that can be printed in as a lattice or as a fully dense design – delivering benefits for a wide range of industrial applications.
See How FreeFoam Works
Your browser does not support the video tag.
[VIDEO]
Delivering all-new benefits for the automotive, furnishing, footwear, sporting goods, health care and other industries.
FreeFoam 3D Printing Production offers a variety of benefits that will change the foam production market.
- 3D prints closed-cell foam products in any volume without tooling
- Manufacture complex foam designs with ease, from lattice designs up to fully dense foam, without trimming or significant waste
- Print your design on a DLP resin 3D printer and then expand the design with accuracy during foaming in an oven at 160-170°C (320-340°F)
- Lightweight existing foam designs to improve product efficiency and reduce shipping costs. You can even ship your foam parts compact and expand or foam them at the final point of assembly or use
- Innovative new material delivers a high strength-to-weight ratio
- Iterate designs as desired, without the penalty of changing tooling
-
Standard automotive seating 3D printed in FreeFoam, developed in partnership with Camaco.
-
This all-new process allows 3D printers to produce much larger final foam parts than the printers’ original build areas and will enable foam products to be shipped at compact sizes and expanded at the final point of assembly or commercial use.
-
Manufacture complex foam designs with ease, from lattice designs up to fully dense foam
Expandable 3D Printable Resin Designed for Volume Production of Foam Parts
FreeFoam is part of the recently launched DuraChain™ category of one-part, one-pot photopolymers that delivers breakthrough elastic and tough material properties through a Photo Polymerization-Induced Phase Separation (Photo PIPS) process. When illuminated during DLP printing, these materials phase separate at the nano level into a material that cures into a resilient, high-performance polymer network. DuraChain enables FreeFoam parts to be foamed with control in an oven without a mold.
FreeFoam will initially be 3D printable exclusively on the ETEC Xtreme 8K top-down DLP system from Desktop Metal’s polymer 3D printing brand.
-
FreeFoam resins contain a heat-activated foaming agent, and are 3D printed into parts like other resins with Digital Light Processing (DLP). However, these parts expand controlled air pores during a quick oven cycle, expanding the part 2-7 times their original size.
Keep Up with the Latest News
Sign Up for Access
Desktop Metal unveils new expandable foam 3D printing material, FreeFoam
0Shares
3D printer manufacturer Desktop Metal has debuted FreeFoam, a new 3D printable photopolymer resin family that contains heat-activated foaming agents.
Invented by Texas-based materials specialist Adaptive3D, a Desktop Metal subsidiary acquired in 2021, FreeFoam can be programmed to expand anywhere between 2 to 7 times its original printed size without any tooling. The result is the production of tunable and durable closed cell foam parts, which are expected to see extensive use in sectors such as automotive, furniture, sporting goods, footwear, and healthcare.
Initially available exclusively on the ETEC Xtreme 8K DLP 3D printer, FreeFoam will be showcased at Foam Expo North America in Michigan from June 28-30. The Expo will feature a 3D printed FreeFoam car seat developed in partnership with Camaco.
“FreeFoam is one of the most exciting and commercially significant photopolymer solutions to come to market in the industrial printing space in years,” said Ric Fulop, founder and CEO of Desktop Metal. “The market for conventionally manufactured foam has many challenges – from expensive molds that limit designs to dense and heavy foams that absorb water and are expensive to ship and drive, to the inability to easily dial in strength and Shore hardness values in specific foam designs.”
A 3D printed FreeFoam car seat before (left) and after (right) expansion.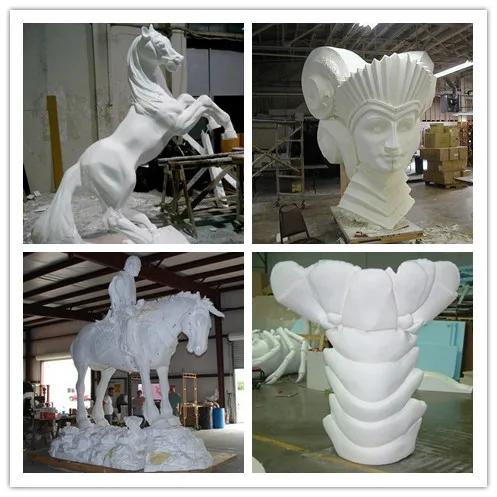
The expansion of Desktop metal
Based in Massachusetts and founded in 2015, Desktop Metal quickly became well-known in the additive manufacturing sector for its portfolio of metal binder jet 3D printers. Since going public on the NYSE in December 2020, the company has gone through a period of rapid growth with a plethora of acquisitions.
The expansions include the establishment of Desktop Health and wood 3D printing firm Forust. The firm bought out DLP 3D printer OEM EnvisionTEC in January 2021, which was rebranded to ETEC shortly after. Desktop Metal also acquired recoating system developer Aerosint and hydraulics firm Aidro a few months later.
August 2021 saw one of Desktop Metal’s biggest plays yet, when it announced the acquisition of competing binder jet 3D printer OEM ExOne for $575 million. The deal was approved in November, combining two of the industry’s leading binder jet firms.
3D printing custom foam parts with FreeFoam
According to Desktop Metal, more than 1.5 billion lbs. of foam is produced every year for bedding, seating, and a whole host of furnishing products. Conventional foam production involves cutting blocks of foam into smaller shapes as needed, which places a huge limitation on the geometries that can be produced while also resulting in significant waste from the trimmings.
Developed as part of Desktop Metal’s DuraChain product line, FreeFoam is designed to address these issues, enabling manufacturers to 3D print their foam products in any shape they desire. The resin can be 3D printed like any other via the DLP process, and expanded on-demand when heated at temperatures of 160 – 170°C in an oven.
The key to FreeFoam is the dispersed foaming agents contained within, which create closed cell pores throughout the material’s microstructure. These pores can expand to up to seven times their printed sizes depending on the exact grade of resin. Desktop Metal intends to offer several grades of the offering with different Shore hardness values and other properties such as water resistance.
Ultimately, customers will be able to 3D print parts much larger than the build volumes of the printers used to print them, slashing shipping space requirements and saving on logistical costs.
Fulop adds, “We’re especially excited to reveal our FreeFoam innovation in Metro Detroit, where our new foam material can help lightweight cars and trucks while preserving the performance and comfort expected in foam seating. With FreeFoam, Desktop Metal is ready to liberate the foam market from its many challenges.”
FreeFoam is set for broad commercial availability in 2023.
FreeFoam’s closed cell microstructure.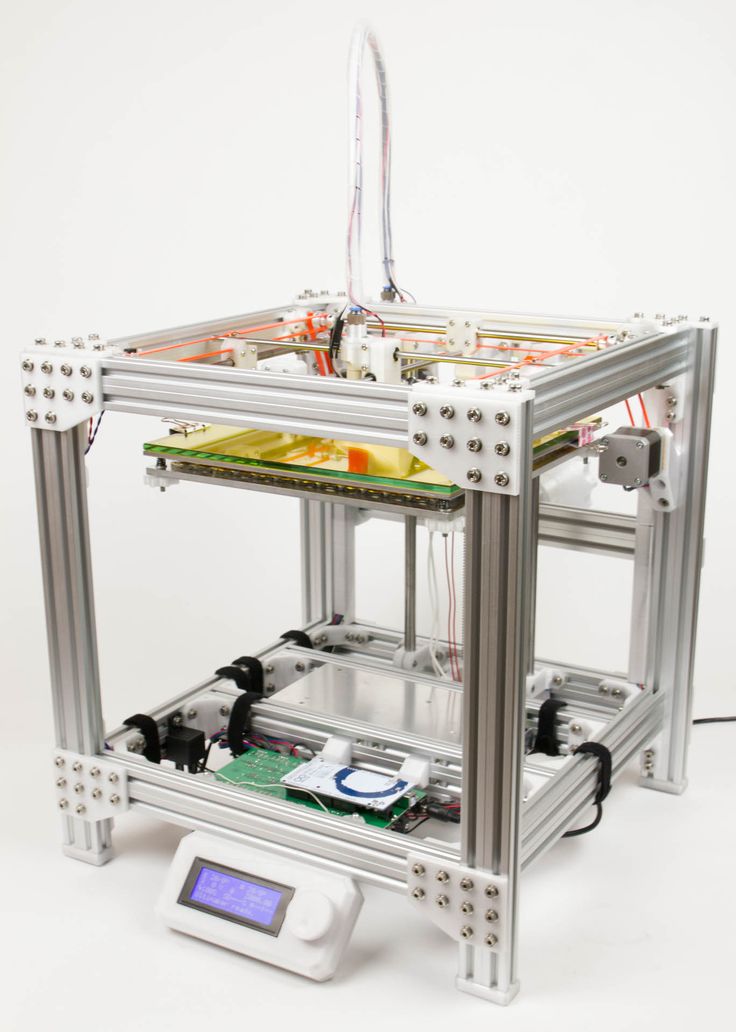
Subscribe to the 3D Printing Industry newsletter for the latest news in additive manufacturing. You can also stay connected by following us on Twitter, liking us on Facebook, and tuning into the 3D Printing Industry YouTube Channel.
Looking for a career in additive manufacturing? Visit 3D Printing Jobs for a selection of roles in the industry.
Featured image shows a 3D printed FreeFoam car seat before (left) and after (right) expansion. Photo via Desktop Metal.
Tags Adaptive3D aerosint Aidro Camaco Desktop Metal ETEC Xtreme 8K Exone Forust FreeFoam Ric Fulop
Kubi Sertoglu
Kubi Sertoglu holds a degree in Mechanical Engineering, combining an affinity for writing with a technical background to deliver the latest news and reviews in additive manufacturing.
High-quality foam and plastic figures in Sprint 3D!
We live in a time when advertising drives progress, the economy and even the social sphere. The number of various advertising media is simply huge. Some of them are more effective, others are less. We want to draw your attention to one of the types of advertising (and not only). Our theme is figures made of foam and plastic.
plastic and polystyrene life figures can serve as both advertising and decoration. They can be used almost everywhere: on the street, in shopping and entertainment centers, exhibition areas, cafes and restaurants, in landscape gardening areas, etc. Even in office or residential premises, they will find a place as part of the interior.
In our company you can order turnkey production of life figures - from the development of a three-dimensional model to the actual production. We offer a look at what it is, what is the difference between plastic and foam figures, and why their use is relevant right now.
3D body figures in Sprint 3D
Our figures are more durable than concrete figures and withstand extreme temperatures
Any sizes of figures
Coordination of 3D-model before execution
Execution of realistic figures of any complexity
Professional painting (full color, monochrome, metal effect)
High speed of execution throughout Russia and
CIS countries
Styrofoam figures: light, durable and inexpensive
Styrofoam has been used for more than a decade to create various decorative elements and original advertising. Light weight, ease of shaping the desired shape by milling, low cost - only a small part of the advantages of foam as a production material.
Styrofoam can be used to produce products of almost any shape and size. And thanks to the metal frame and a special anti-vandal fiberglass coating, they are characterized by very high strength with low weight.
We can make almost anything for you:
- figures of people, animals, game characters, movie and cartoon characters in almost photographic quality;
- whole compositions of figures and elements of any complexity and size;
- other items and objects having an advertising or decorative function.
Just contact us and let us know which shapes you need. We will develop a unique 3D model for you, approve it together with you, after which we will make a figure based on it by milling. We paint and process all products ourselves so that they get a complete look.
Right now, custom-made foam plastic figures made by us are used in the promotion of goods and services, as decoration, as unusual elements of photo zones, etc.
Plastic figures: maximum strength and durability
If you plan to actively use advertising figures, transport them regularly or place them for a long time in areas where they will be exposed to aggressive external influences, your choice is plastic. Yes, these pieces will be heavier than foam pieces , but they are even more durable. Sun, rain, cold, sun - they don't care. Although we emphasize that thanks to the anti-vandal coating, our foam figures are almost in no way inferior to plastic ones.
One of the main differences between foam and plastic figures is in the production method. The process is almost identical except for the manufacturing method itself:
- Preparing a 3D model.
- 3D printed product.
- Processing and painting, giving the figure a complete look.
- Vandal-resistant coating of the entire product for increased durability.
As in the case of foam plastic, thanks to 3D printing technology, plastic opens up the widest possibilities for creating unique shapes: people, animals, geometric elements of any complexity, product layouts and much more. There are practically no restrictions.
Buy life figures in our company and get maximum benefits
Our main advantages are price and quality. Thanks to the full production cycle, we provide customers with a truly individual approach, standardized quality of all products and fair prices without markups.
Working with us, you get:
- unique products that fully meet your wishes;
- the ability to use your own layouts, sketches and other developments;
- clear pricing without involving third parties in the production process;
- quick calculation of the cost without its subsequent unforeseen increase;
- strict adherence to the deadlines for the manufacture of plastic and foam figures without "force majeure".
Our offer will interest everyone who works in advertising, product and brand promotion, decoration, landscape design and so on. Even if you just decide to decorate your own house, cottage or garden with original products that will last more than 20 years and will please the eye, please contact us. Let's discuss all the details and start manufacturing.
If you still have questions, you do not know what to choose - plastic or foam, or just want to get a preliminary consultation from a specialist, please contact us during business hours in any way convenient for you.
Styrofoam Shaped Cutting Machines
Styrofoam Shaped Cutting Machines using modern, computerized technologies, allow you to create almost any product of the most complex shape, quickly, accurately and relatively inexpensively. 3D shape cutting of foam plastic is used to create: three-dimensional letters, logos (3D logos), signs, graphics, inscriptions for outdoor and indoor advertising, store props and window dressing, exhibition stands, fair stalls, decor elements, scenery, for example, for theater or cinema, P.O.P. displays for points of sale, replicas of commercial products, thematic props, architectural scale models, pipe insulation, columns, precast concrete structures, etc.
Make your ideas a reality...
MACHINE APPLICATIONS
CNC foam cutters can be used to cut a wide variety of products and can cut almost anything from (EPS) foam or extruded polystyrene (XPS)
The limit of machine tools is your imagination!
Some of the most common uses:
Forms made by thermal cutting (hot string method) do not undergo thermal expansion, so they cannot crack in the cold or deform in the heat.
- LABELING AND 3D LOGO — How many times have you faced the challenge of creating complex 3D logos? And all known methods, such as cutting with a saw, knife, cutter, seem to work, but require subsequent processing of the material, leave a lot of dust and small chips, and as a result require additional costs. Our CNC machines will perform such work easily, quickly and with a clean, ready-to-paint surface.
- ARCHITECTURAL ELEMENTS - Styrofoam architectural elements such as moldings, finials, railings, keystones, parapet caps, balusters, moldings are gaining more and more popularity in design studios and architectural studios. In the final form, the elements can be covered with a reinforcing mesh, primer or mortar and painted in the desired color. The light weight of structures, easy installation, manufacturing precision and environmental friendliness make architectural elements made of foam plastic an indispensable part of any design.
- EXTERNAL WALL INSULATION - CNC foam cutting machine on the construction site? Why not? The machines are made of aluminum profile systems, which allows you to disassemble / assemble the machine very quickly and without much effort in any workshop or on a construction site. This is the best way to produce external wall insulation on site, which results in time savings and high quality thermal insulation, as well as improving your professional level in front of a client or customer.
- FAIR, CINEMA AND THEATER DECORATIONS — There is no more useful way to create fair stalls, cinema and theater decorations than CNC thermal equipment (hot string cutting method). The speed, cleanliness and precision of cutting CNC machines allows you to create every scenery and scenography in the shortest possible time and without spending a lot of money.
WHAT IS CNC?
CNC foam cutting machine is a (Computer Numerical Control) computer controlled machine for cutting any shape from foam or extruded polystyrene foam. The heated wire (typically Nichrome alloy) is moved along the Y and X axes by micro-stepping motors (actuators) controlled by the computerized system. This ensures perfect precision, fast processing and consistently excellent quality.
's precise mechanisms and advanced electronic motion control allow the operator to cut any shape, as long as its dimensions match the dimensions of the material. There is also the possibility of designing and cutting several different projections of the same shape, resulting in very attractive 3D shapes. The rotary table allows you to cut, for example, spheres, the lathe is indispensable for cutting columns, even more possibilities come with the use of a device for shaped tools (wire).
CONTROL SOFTWARE
Unique software made especially for our CNC foam cutting machines comes free with all P60, T-Series! and MW Series! models. The software has a very simple and intuitive interface, so even the most inexperienced user can easily and quickly learn how to use the software in a matter of hours. The basic version has 11 language versions.
Key features:
- Support formats:
— HPGL.plt (e.g. CorelDraw)
— dxf (e.g. AutoCad)
— RAW 3D (e.g. Rhinoceros 3D)
— EPS/AI (e.g. AdobeIllustrator)
— dxf 3D (e.g. AutoCad ) - Auto connection of objects and generation of paths.
- Adjustable parameters.
- Complete accessories control: Turntable and Lathe.
- Manual control of all axes (X, Y and Z).
- Unlimited material and economical configuration options.
- Auto stop on break; continued after wire change.
- Advanced redundancy module.
- Simulation of the cutting process.
- Unlimited free updates.
Requirements:
- Availability of PC
- Windows XP, Vista, 7, 8, 10
- Any graphics program with HPGL.plt or .dxf export, such as Corel Draw, AutoCAD, etc.
- Free serial port (USB)
MODELS AVAILABLE
We offer the Foam Shaper in 3 configurations:
- P60-Series! = 1 cutting wire, fixed wire length 60 cm.
- T-Series! = 1 or 2 cutting wires, wire length: 60, 130, 150, 250 or 300 cm. Huge range of optional accessories.
- MW Series! = 10 cutting wires, wire length: 130, 250 or 300 cm
In P60-Series! wire length is always 60 cm ( Z axis ). In the other two series ("T" and "MW"), the numbers after the letters T or MW (e.g. T 1300, T 3000, MW 2500, etc.) = wire length in mm ( Z axis ).
Axis:
- Wire length = machine width = Z axis
- Machine height = Y axis = always approx. 122-129 cm for our machines
- Last dimension is X axis = machine length (not to be confused with wire length = Z axis).
Z axis = machine width = cutting wire length Examples: If you do not know which model will suit your needs, or are unsure of your choice, send us request with information (required dimensions, number of cutting wires and the need for additional equipment), and we will comment on your choice or recommend you a specific model specifically for your needs.
X axis = machine length
Y axis = machine height Small) model is 122 cm long (X axis)
Accessories
Depending on the application, we can offer a range of accessories that you can equip your CNC foam cutting machine with. The list below provides basic information about the availability and use of additional options for various models.
Rotary table
Availability: P60, T-Series! and "MW-Series!
Usage: sequential cutting (2.5 D) for non-standard symmetrical and non-symmetrical shapes, spheres, columns, miter cuts, etc.
Lathe
Availability: P60, T-Series! and "MW-Series!
Usage: circular cutting, all kinds of columns, threads, grooves, etc.
Shaped wire device
Availability: P60, T-Series! and "MW-Series!
Usage: all types of engraving, turning, hollow and symmetrical shapes, etc.
Double Wire Device
Availability: T-Series!
Use: 2 cutting wires allow you to cut 2 identical pieces at the same time.
Pneumatic wire tensioner
Availability: T-Series! for 2.5 and 3.0 m widths
Usage: replaces the standard spring tensioner for higher cutting speeds and quality.
Titanium Alloy Wire
Availability: T-Series! and "MW-Series! 1.3 meters wide or more.
Use: to replace standard NiCr wire for higher cutting speeds and quality.
Independent cutting axis control
Availability: T-Series!
Use: for cutting all types of cones.
GALLERY
CUTTING THREAD
0003 300 - 500 degrees Celsius. Depending on the width of the foam cutting machine (i.e. the length of the cutting wire), it is recommended to use nichrome wire of the following diameters: 0.15, 0.25, 0.45 and 0.55 mm. The Foam Shaper is supplied with a free 100 gram spool of cutting wire.
Multi-wire foam cutting machines MW-Series! and T-Series! , can be equipped with pneumatic tensioner wire or stronger tensioners to allow higher quality titanium alloy wire. Although titanium alloy wire is a little more expensive than standard NiCr nichrome wire, nichrome wire is less frequently replaced (on average, it lasts 5-6 times longer than NiCr wire) and it is much more resistant to stretching at high temperatures, which leads to more high speed and improved cutting quality. Wire of Titanium alloy is available, at an additional cost for all MW-Series! and T-Series! looms 1. 3 meters wide and wider.
FOAM SELECTION
There are two types of foam that are best suited for hot wire foam cutting machines: hot drinks, refrigerators, thermal insulation, packaging, etc. Styrofoam consists of 98% air and 2% polystyrene. Polystyrene granules are heated with steam so that they rapidly expand (foam) and form a block (in a special form) of low density. Such material is not expensive and light, usually weighing 15-30 kg per cubic meter. Expanded polystyrene does not lose its properties over time and can be completely recycled, with subsequent reuse.
Extruded Polystyrene (XPS) has the same chemistry as expanded polystyrene but is produced using a different technology, resulting in less air pockets and more uniform foam. Often pink, blue, green, etc. Extruded polystyrene is ideal for making any display panels.
Why Styrofoam?
There are several reasons why the above materials are so widely used. As a rule, foam is:
-
Cheap.
-
Lightweight.
-
Ideal for outdoor and, as with EPS material, indoors.
-
Possibility of application of various coatings (water-based paints, cement coatings, metal coatings, etc.).
-
Durable Use - When properly applied, coatings can last for decades.
WARRANTY
All CNC foam cutters come with an “unlimited” 5 year warranty.
- Warranty covers all electronic and mechanical parts and software.
- The only thing not covered by the warranty is cutting wire.
- All spare parts are presented on an EXW (ex-works) basis.
- Most spare parts are shipped to customers on the same day (or next day) when the warranty claim is confirmed.
For more information please contact us on !
Send request
Send request
Delivery of equipment
Delivery of equipment
We sell and ship CNC equipment worldwide!
Each foam cutting machine is regarded as a separate project and, depending on the configuration of the machine, its production, assembly can take from 3 to 6 weeks.