3D printing systems melbourne
Careers at 3D Systems | 3D Systems
Why 3D Systems?
Meaningful work, passionate and bright people, and a company that supports your life from day one. There’s a lot to explore at 3D Systems, we hope you’ll join us.
Be part of a team with brainpower, heart, and grit.
We have a diverse team with some of the world’s most dynamic and forward-thinking talent. Not only do we have the brainpower, we have people with heart, grit and a ton of curiosity. And the cornerstone of our work is to lead, explore, and innovate with the utmost integrity.
Be you, at your best.
We care about treating people right and we know that life is more than work. This is why we approach rewards and benefits at a personal level so that you have the resources you need to take care of yourself and be you, at your best. See a few of the rewards and benefits we offer.
Write your own story.
-
E-Verify
3D Systems participates in E-Verify ENGLISH/SPANISH (PDF)
Right to Work (English)
Right to Work (Spanish)
Equal Employment Opportunity
3D Systems is an Equal Opportunity Employer. All qualified applicants will receive consideration for employment without regard to race, color, religion, sex, sexual orientation, gender identity, national origin, disability, or status as a protected veteran.
EEO is the Law
3D Systems Employment Opportunity, Anti-Discrimination, & Anti-Harassment Policy
Pay Transparency Nondiscrimination Provision
-
Accessibility and Accommodations
In compliance with the ADA Amendments Act, if you have a disability and would like to request an accommodation in order to apply for a position with 3D Systems, please call 803-326-3933.
Federal Employment Laws
Applicants have rights under Federal Employment Laws:
Family and Medical Leave Act (FMLA)
Employee Polygraph Protection Act (EPPA)
3D Systems commitment to gender equality in the workplace 2021 – Phenix Systems, Riom-France
Equality in the workplace means ensuring the absence of any discrimination within a company.
The challenge for any company is to achieve true equality between men and women at work, in particular through action against day-to-day sexism at work, equal pay, gender parity at management level, and a gender-balanced workforce.
Under the law on freedom of choice in professional careers, the index uses five indicators for companies to monitor their commitment to workplace gender equality. These are:
- Equal Pay
- Pay Increase between the genders
- Promotions of each gender
- Pay increase when returning from maternity leave
- Number of woman amongst the 10 most highly paid employees in the company ( in France)
For 2021, 3D Systems has achieved 60/100.
Link to the gender equality website: https://www.gouvernement.fr/index-de-l-egalite-femmes-hommes-comment-ca-marche
Support : 3D Printing Systems
Support : 3D Printing SystemsHow can we help you today?
Enter your search term here. ..
Knowledge base
UP 3D Printers
General 8
-
What is support material, what is it made of and why do I need it?
-
How does the UP 3D printer's print head (Extruder) work?
-
How do I stop my model from lifting/warping?
-
What is 'warping' and why does it happen?
-
Air Printing
UP Mini 4
-
UP Mini User Manual
-
Getting Started - First print
-
3D printed parts for UP Mini 1
-
Upgrade for UP Mini 1
UP Mini 2 5
-
UP Mini 2 User Manual
-
Getting Started - First print
-
3D printed parts for UP Mini 2
-
UP Mini Maintenance and Support Videos
-
How to replace the Extruder Rainbow Cable to the Print Head
UP Plus 2 5
-
UP Plus 2 User Manual
-
Getting Started - First print
-
3D Printed Parts for UP Plus 2
-
UPgrade for UP Plus/2
-
UP Plus 2 Maintenance and Support Videos
UP Box 6
-
UP BOX User Manual
-
Getting Started - First print
-
3D printed parts for UP Box
-
Upgrades for your UP Box
-
UP Box Maintenance and Support Videos
UP300 2
-
UP300 User Manual and Quick Start Guide
-
3D printed parts for UP300
X5 0
Filament 2
-
PLA Tips and Tricks
-
3D Printing with Nylon filament
Software - UP Studio 7
-
Where can I download UP 3D Printer software?
-
What version of software should I download?
-
How to check what version of UP Studio your currently using?
-
Resetting the SD Card using UP Studio
-
How to Connect to your WiFi 3D printer
Software - UP! 5
-
How to install printer drivers in Windows?
-
How to disable signature driver enforcement in Windows 8.
1?
-
How to adjust the support angle in the UP software.
-
How to update my printer's ROM? [UP Plus/Mini]
-
Model out of print range
3D Scanners
ScanMaster Body 2
-
Installation Manual
-
Kit Assembly Instructions
ScanMaster Plus 1
-
ScanMaster Plus Manual
Emblaser 2
Getting started 1
-
Emblaser 2 Manuals and documentation
LightBurn 1
-
Getting Started
Materials 2
-
How to import and create material profiles or databases - Lightburn
-
How to import the material database - LaserWeb
Help Desk Software by Freshdesk Support Desk
An overview of the Raise3D MetalFuse 3D printing system with print examples.
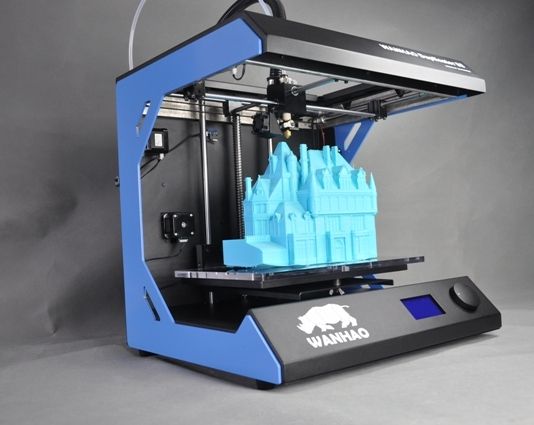
This year, Raise3D released the MetalFuse metal 3D printing system, consisting of a Forge1 3D printer, a D200-E catalytic resin removal station, and an S200-C vacuum furnace. We have already published a review of this system, here we would like to share our personal experience of using MetalFuse.
Forge1 3D Printer
Features of the MetalFuse system appear even at the stage of preparing the model for printing. The Forge1 printer works with its own ideaMaker for Metal slicer, which uses unique printer and media profiles.
Unlike preparing a model for conventional FDM printing, Forge1 requires an increase in part dimensions by 19% in the XY axis and 22% in the Z axis, due to volumetric shrinkage during the sintering step.
Also, ideaMaker for Metal has a built-in function for calculating the time of subsequent cycles of processing the part - cleaning and baking. The cleaning time is calculated from the thickness of the largest part of the lot.
The Forge1 printer is based on the Raise3D Pro3 model, but has noticeable design differences: a high U-shaped spool portal and a massive dome. The presence of the U-shaped portal is due to the high weight of the coil of metal-containing filament - 3 kg. That is why a vertical material feed system using roller holders is used for stable printing.
Forge1 uses tempered glass as the print platform surface, as the integrity of the first layer is very important. Small cracks, roughness and non-uniform texture on the surface can lead to defects at the stage of cleaning and sintering of the part.
The metal-containing filament BASF Ultrafuse 316L used by us for printing has rather low adhesive properties when printing on glass. In the first tests, we used PVA-pencil glue and polyamide printing glue, but using these compositions we were not able to achieve stable printing results. We were able to obtain high-quality adhesion of the first layer only when using a special adhesive for BASF Ultrafuse 316L - Magigoo Pro Metal.
Forge1 has a dual extruder: the first nozzle is for the base material, the second nozzle is for printing ceramic supports. The support material is destroyed during the sintering process and makes it easy to remove the part from the main metal supports without the use of additional tools.
Like other models of Raise3D 3D printers, Forge1 has a built-in webcam connected to the RaiseCloud cloud service. It allows you to remotely control the printing process via a browser or mobile application, which is especially important given the cost of metal-filled printing materials.
Part cleaning in station D200-E
The next step in the processing of parts after printing is acid catalytic cleaning. The D200-E station removes the binder polymer, after which the parts become very brittle, consisting only of metal particles.
Removal of the binding polymer occurs by etching with an acid solution of alcohol and oxalic acid while heating the D200-E chamber to 125 degrees. The reaction also requires the supply of nitrogen, which is used as a stabilizer.
Before the start of the cycle, it is necessary to weigh all the details, since it is by weight loss that the quality of cleaning is checked. The required minimum weight loss is 10%. For more accurate measurements, it is recommended to separate the parts from the glass surface of the Forge1 printing table with water, and wash off the adhesive residue on the first layer with water. After complete drying, parts can be weighed.
In menu D200-E, a recipe is created with the cleaning time specified in the slicer. The main menu shows all key indicators, as well as the total cleaning time and the duration of the individual steps.
Sintering parts in the S200-C furnace
At the stage of baking the part in a vacuum furnace, we get a steel product that corresponds to the more expensive and complex technology of metal injection molding (MIM). When the correct settings are set, the porous structure of the cleaned parts is sintered, which gives compaction and volumetric shrinkage.
A necessary condition for high-quality sintering of products is the evacuation of the furnace chamber, so a vacuum pump is connected to the furnace separately.
Cooling the oven electronics and power supply requires the S200-C to be connected to a water chiller.
Argon is used as a stabilizer for the sintering process. It is also necessary to connect an air compressor to the S200-C to control the valves that accompany the operation of the vacuum pump.
The S200-C has a similar interface to the D200-E catalytic treatment station, making it easier to work with MetalFuse devices. The sintering time primarily depends on the type of material (BASF Ultrafuse 316L or BASF Ultrafuse 17-4 PH) as well as on the dimensions of the largest part of the lot.
Inside the furnace chamber there is a graphite heating circuit and a graphite box with shelves and a door also made of graphite. The choice of graphite is due to the high thermal stability of the material and uniform thermal conductivity. Parts for sintering must be placed on ceramic plates, since contact between hot metal and graphite is unacceptable.
After sintering, a predictable volumetric shrinkage occurs, and the parts themselves acquire the characteristics of steel, both in physical properties and in appearance.
Totals
The MetalFuse system is an excellent solution for small batch production of steel products, as well as for unique one-of-a-kind orders. The size of the D200-E and S200-C chambers - 200x200x200mm allows the production of small and medium-sized parts. Despite the fact that the MetalFuse system consists of three devices, it is not difficult to learn how to work with it due to the similarity of the printing process with standard FDM technology, as well as convenient and easy-to-learn device interfaces. Given the cost of the system and consumables, MetalFuse is rightfully considered one of the best metal printing solutions in terms of price-quality ratio.
Metal 3D printing | DMLS Printer | Additive manufacturing equipment
Equipment Additive Manufacturing Equipment
What is additive metal manufacturing?
Eplus 3D Additive Metal Manufacturing
Metal 3D printing equipment and supplies
Eplus3D metal printers, from entry-level models to multi-laser machines, can be used for industrial grade additive manufacturing.