3D printing submarines
US Navy eyes 3D printing for submarine parts to ease burden on strained industrial base
ARLINGTON, Va. — Among the top risks to the critical Columbia-class ballistic missile submarine program is fragility in key parts of the industrial base.
Additive manufacturing, better known as 3D printing, could fix that.
The U.S. Navy plans to pair suppliers who cannot keep up with demand with additive manufacturing companies who can print parts around the clock to boost the supply, a service program official said Jan. 31. This effort would be aimed at the most fragile parts of the submarine-industrial base: companies that do castings, forgings and fittings, in particular.
Matt Sermon, executive director of Program Executive Office Strategic Submarines, said this would help these companies — some of them the sole sources of components to the Navy — by removing pressure to increase production rates as they’re struggling to keep up with the current workload.
The industrial base today builds two Virginia-class attack submarines a year, is working through construction of a single Columbia-class sub and helps maintain in-service subs.
But fabrication has already begun on the first Block V Virginia-class sub with a mid-body Virginia Payload Module that increases the construction workload by about 25%. The Navy will buy its second Columbia-class submarine in 2024 and start one-per-year production in 2026, translating to a spike in work for the prime shipyards and their supply base. The Navy has started referring to this time of consistently buying one ballistic missile submarine and two general-purpose submarines every single year as the “1-plus-2″ years.
If the demand for parts can’t be reduced, then “let’s go additively manufacture the components in that space, such that by the time we get to the 1-plus-2 years, we will have reduced demand signal in castings, forgings and fittings,” Sermon said in his remarks at an American Society of Naval Engineers event.
Today, the Navy certifies individual parts to go on submarines. That part-by-part qualification won’t work going forward, Sermon said, advocating for the Navy to instead qualify materials and processes used for additive manufacturing rather than the parts that result from it.
But the Navy has struggled to do this. For aviation programs, additive manufacturing advocates sought permission to print noncritical parts — but the Navy wouldn’t allow it. The aircraft carrier John C. Stennis hosted the first-ever advanced manufacturing lab onboard, but used the laser scanning and additive manufacturing tools to print parts for the ships in the strike group, not the aircraft.
Putting printed parts on a submarine is as risky a proposition as putting them on aircraft, with both communities having strict standards to keep sailors safe in the air and under the ocean. But Sermon said the engineering community is now onboard. The technical warrant holders are part of ongoing discussions, and Naval Sea Systems Command’s engineering and logistics directorate has accompanied the program office on site visits to companies that demonstrate additive manufacturing best practices.
“Additive manufacturing gives you a better material, a better steel, than [working with raw materials],” he said. “It is complicated, and microstructures … are complicated and do change some fundamental concerns of ours. We will have to change how we do nondestructive testing in many cases — not because it’s bad, but because it’s different, and we have to understand that.”
150924-N-PN275-061 APRA HARBOR, Guam (Sept. 24, 2015) The Los Angeles-class attack submarine USS City of Corpus Christi (SSN 705) maneuvers into position to moor alongside the submarine tender USS Emory S. Land (AS 39) to complete repair maintenance actions. Emory S. Land is a forward deployed expeditionary submarine tender on an extended deployment conducting coordinated tended moorings and afloat maintenance in the U.S. 5th and 7th Fleet area of responsibility. (U.S. Navy Photo by Mass Communication Specialist Seaman Zachary A. Kreitzer/Released)
The effort to put printed parts on submarines began in November, and Sermon said the Navy will install the first parts on an in-service submarine this calendar year.
He told Defense News after his remarks that the program office has a ranked list of six to 10 components they’d like to print, based on a list of “trouble components” consistently unavailable at the public shipyards when they’re needed for a submarine maintenance availability.
The vendors who make the parts won’t be cut out of the process. Rather, they’ll help with the engineering and have the option to do the printing if they have the capability — though Sermon said most of the companies involved don’t. If the original manufacturer can’t do the additive manufacturing itself, the Navy will pair it with a small business that can.
Sermon noted during the panel the multiple benefits of embracing additive manufacturing. First, it addresses capacity issues during the 1-plus-2 years, when a lack of parts could jeopardize construction and repair timelines.
In the longer run, however, he said that working through the processes and the certification of printed parts will enable the Navy and industry to design the next-generation submarine, dubbed SSN(X), with additive manufacturing in mind — potentially reducing the program’s cost or generating a better or more survivable part.
About Megan Eckstein
Megan Eckstein is the naval warfare reporter at Defense News. She has covered military news since 2009, with a focus on U.S. Navy and Marine Corps operations, acquisition programs and budgets. She has reported from four geographic fleets and is happiest when she’s filing stories from a ship. Megan is a University of Maryland alumna.
Share:
More In Naval
General Dynamics, Amazon, Cisco form coalition to spur 5G adoption
The fifth generation of wireless technologies promises exponentially faster speeds as well as the capacity to accommodate more and more-advanced devices.
Q&A with Mart Noorma, the new director of NATO’s cyber brain trust
"In cyberspace, especially," Noorma says, "there are all kinds of new, incoming threats, and we have to be prepared."
Air Force Research Lab awards $76 million for lunar experimentation
AFRL expects the Oracle satellite to launch in 2025 and have a two-year mission life.
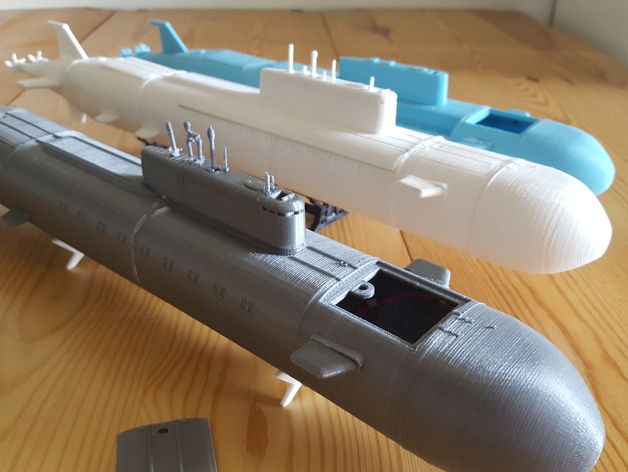
Army showcases space-enabled targeting system at Project Convergence
Raytheon and Palantir are developing competing prototypes for the Tactical Intelligence Targeting Access Node, a key element of JADC2.
Why the Space Force is getting serious about on-orbit servicing
The newest service is making organizational shifts and upping its engagement with companies developing on-orbit logistics technology.
U.S. Navy Submarines to Have 3D Printed Parts Starting This Year - 3DPrint.com
At the beginning of last month, the U.S. Navy announced it was awarding six contracts to defense firms and research institutions, to study applications of additive manufacturing (AM) that could potentially enhance protection of navy technologies. That funding is intended to benefit the Naval Surface Warfare Center (NSWC). At the end of last month, it was announced that AM will also be used more frequently on the Navy’s underwater weapons systems, in an attempt to ease some of the supply-chain difficulties increasingly faced by manufacturers of components for the U. S.’s submarines.
The Navy will be acting as a liaison between AM companies capable of handling the strict demands of military engineers, and current suppliers who are having trouble keeping up with demand. The lags in part availability are especially worrisome, as further constraints are also anticipated in the intermediate future. This is due largely to what naval procurers refer to as “1-plus-2” years: years starting in 2026, when the Navy is scheduled to annually produce one ballistic submarine and two general-purpose submarines. This intensified production schedule is mainly resultant from construction to be done on the not-yet-in-commission Columbia-class of subs, the first of which was purchased in 2020. The second will be purchased in 2024; when work on that is completed, at the end of 2025, the 1-plus-2 years are set to begin.
The Columbia-class is set to replace the Ohio-class, which has been in commission since 1981; Columbia is expected to replace Ohio in 2031. It is hoped that gradual upticks in adoption of AM will take some of the burden off of manufacturers of parts for Virginia, the latest class of U.S. submarines to already be in use, allowing suppliers to handle the dual load, as well as the maintenance of in-service vessels. The greatest change to naval policy involved in the plan is that, whereas previously the Navy had to certify individual parts to be used on submarines, it will now certify the materials and processes involved in AM production of each part. Instead of monitoring the end-result, it will now monitor the plan for each part in advance.
In a statement at an event for the American Society of Naval Engineers, Matt Sermon, executive director of Program Executive Office Strategic Submarines, said, “[AM] gives you a better material, a better steel, than [working with raw materials]. It is complicated, and microstructures…are complicated and do change some fundamental concerns of ours. We will have to change how we do nondestructive testing in many cases — not because it’s bad, but because it’s different, and we have to understand that.
”
An artist rendering of a Columbia-class sub.
Sermon told Defense News that, while the vendors responsible for making parts will have the option to print those components designated to start being produced by AM if they have that ability, most of the vendors currently supplying parts for submarines don’t. Nevertheless, they’ll still be helping with engineering the parts. Sermon also said that the program office has made a list of six-to-ten parts slated for printing. These are “trouble components,” those which are most often unavailable when they’re needed for maintenance.
Although all of this seems far in the future, the Navy will start using 3D printed parts on in-service submarines this year. Assuming all goes well, as much production capacity will be replaced by AM as is needed to take the pressure off of conventional manufacturers when the 1-plus-2 years start. Moreover, as Sermon pointed out, the next class of Navy submarines could be engineered specifically with AM in mind.
The fact that the U.S. Navy will be acting as an Xometry of sorts for defense manufacturers, along with their ultimately accepting a change in policy that procurers had until now been resistant to, is just the latest illustration of exactly how crucial the pivot toward AM is becoming to the military as a whole. Additionally, when it comes to picking winners, the military has quite a track record. It doesn’t “pick” winners so much as it creates them. So any company paired up by the Navy with a conventional manufacturer can be expected to have longevity. Another memorable moment in that great military Keynesian experiment known as the U.S.A.!
Stay up-to-date on all the latest news from the 3D printing industry and receive information and offers from third party vendors.
Tagged with: columbia sub • columbia submarines • Columbia-class • Marine 3D printing • maritime 3D printing • military 3d printing • navy • submarines • us navy • virginia submarines • Virginia-class
Please enable JavaScript to view the comments powered by Disqus.
3DNews Technologies and IT market. News cars, motorcycles, vehicles... The Germans begin mass production of parts for... The most interesting in the reviews 02/27/2020 [17:43], Gennady Detinich Additive technologies are moving from laboratories to factories. In a number of cases, 3D printing is beneficial not only for the production of prototypes, but also for mass production of parts. And modern 3D printing technologies have developed so much that “printed” parts are no longer inferior to cast, stamped or machined products in terms of strength and reliability. 3D printed submarine hydraulic block element According to Naval News, the German concern ThyssenKrupp Marine Systems, which is a manufacturer and supplier of warships and submarines, plans to expand the production of components for submarines using 3D printing. The 3D printing technology and necessary equipment for the Kiel plant will be provided by ThyssenKrupp's TechCenter Additive Manufacturing (in Mülheim an der Ruhr, North Rhine-Westphalia). Completion of the deployment of 3D production in Kiel is scheduled for June this year. The transition to 3D printing removes all the constraints that traditional manufacturing processes impose on component designers. This gives you more freedom when modeling and allows you to produce parts faster and at a lower cost. After the launch of 3D printing production, the company expects to mass-produce small batches of parts for both new submarines and spare parts for ships in operation. The ThyssenKrupp TechCenter Additive Manufacturing became the first marine 3D printed component manufacturer in the world to achieve DNV GL certification last summer. Source: If you notice an error, select it with the mouse and press CTRL+ENTER. Related materials Permanent URL: https://3dnews.ru/1004732 Headings: News Hardware, cars, motorcycles, vehicles, Tags: 3d printing, military equipment, additive manufacturing ← В past To the future → |
How I invented the bicycle, or rather a submarine controlled via mobile Internet / Sudo Null IT News brand new iphone and decided to make it myself.
It is controlled via the Internet, and now the mobile Internet covers a large area of Russia. Small reservoirs are completely covered with it, and from the shores of large ones there is Internet even tens of kilometers from the coast.
Elon Musk also announced the creation of the worldwide Internet.
I decided to print the boat on a 3D printer, the models are made in compass_3d. The code is written in python 3.
Link to github.
Equipment and supplies
• 3d printer
• Single board computer Raspberry pi
• 4g modems (2 pieces)
• laptop (2 pieces 1st - transmitter, 2nd - server)
• Servo motors
• webcam
• engine
• accumulators Pb
• other (relay, soldering iron, sensors, adhesives, paints, sealants...).
Parts
As already mentioned, the details are printed on a 3D printer with a layer of 0.3 mm nozzle 0.4 mm
on an aluminum table with a backing of bf2 glue for better adhesion, the longest parts were printed for about 14 hours. Assembly drawing below.
Sealing
Servo motors and drive motor are sealed with silicone sealant and grease for tightness. The boat itself, due to the size of its parts and the tendency of abs plastic to shrink (resizing after printing), cracked in places, these places are covered with pvc glue, in places of bolted joints silicone sealant for aquariums.
Power supply
As a power source - two series-connected 6 v lead batteries capable of delivering 3.3 AmH, lead batteries are used due to the fact that they are cheaper, fewer contacts for charging need to be taken outside the boat and they are also heavy (the boat is too voluminous, and its average density should be around 1000 kg/m**3).
Data communication
Now about the main thing, data transfer.
Since water absorbs EMW, you need to bring the modem to the top, so that boat works with a float.
In the local network, a server is installed at home, transmitting everything that comes to it from one address to another. At the moment, the boat is transmitting video, and the control team's laptop. It's all organized through sockets.
Since I wanted to do as much as possible, so that it would be more interesting , and in order to reinvent the wheel , then, as I said, I did the video transmission myself, so without inventing anything better, I decided to transmit not video, but frames to jpg. One picture is passed, then the stop word “stop” is poisoned, and since it does not occur in jpg, the code easily separates where and when to show the picture.
while bytes('stop','utf-8') not in data: image_result.write(data)#writes a 1 KB image to a file data = sock.recv(1024)#receives data from the server 1 Kb if bytes('stop','utf-8') in data: image_result.write(data[:data.index(bytes('stop','utf-8'))])#writes to the file what came before the stop word
Image playback and camera reception using opencv. There is no compression yet, so the delay is as much as 9-13 seconds. Control buttons are written using Tkinter.
3D bottom model
While uploading the 3D model on github, I saw what the stl file consists of, and decided to write code also to create a 3d model of the bottom relief from the list of distances to it taken by an ultrasonic range finder (which is not yet installed).
example tetrahedron.stl in txt
solid
facet normal 0 0 0
outer loop
vertex 0 0 0
vertex 2 0 0
vertex 1 1 2
end loop
endfacet
facet normal 0 0 0
outer loop
vertex 2 0 0
vertex 1 2 0
vertex 1 1 2
end loop
endfacet
facet normal 0 0 0
outer loop
vertex 0 0 0
vertex 1 2 0
vertex 1 1 2
end loop
endfacet
facet normal 0 0 0
outer loop
vertex 0 0 0
vertex 1 2 0
vertex 2 0 0
end loop
endfacet
ENDSOLID
Next are the photos interesting and not very
9000 9000 9000
This is actually all I wanted to tell, my main idea for those who did not understand was the creation of an apparatus that allows you to receive information from under the water at a great distance from the control laptop.