3D printing materials types
Guide to 3D Printing Materials: Types, Applications, and Properties
3D printing empowers you to prototype and manufacture parts for a wide range of applications quickly and cost-effectively. But choosing the right 3D printing process is just one side of the coin. Ultimately, it'll be largely up to the materials to enable you to create parts with the desired mechanical properties, functional characteristics, or looks.
This comprehensive guide to 3D printing materials showcases the most popular plastic and metal 3D printing materials available, compares their properties, applications, and describes a framework that you can use to choose the right one for your project.
Interactive
Need some help figuring out which 3D printing material you should choose? Our new interactive material wizard helps you make the right material decisions based on your application and the properties you care the most about from our growing library of resins.
Recommend Me a Material
There are dozens of plastic materials available for 3D printing, each with its unique qualities that make it best suited to specific use cases. To simplify the process of finding the material best suited for a given part or product, let’s first look at the main types of plastics and the different 3D printing processes.
There are the two main types of plastics:
-
Thermoplastics are the most commonly used type of plastic. The main feature that sets them apart from thermosets is their ability to go through numerous melt and solidification cycles. Thermoplastics can be heated and formed into the desired shape. The process is reversible, as no chemical bonding takes place, which makes recycling or melting and reusing thermoplastics feasible. A common analogy for thermoplastics is butter, which can be melted, re-solidify, and melted again. With each melting cycle, the properties change slightly.
-
Thermosetting plastics (also referred to as thermosets) remain in a permanent solid state after curing. Polymers in thermosetting materials cross-link during a curing process that is induced by heat, light, or suitable radiation. Thermosetting plastics decompose when heated rather than melting, and will not reform upon cooling. Recycling thermosets or returning the material back into its base ingredients is not possible. A thermosetting material is like cake batter, once baked into a cake, it cannot be melted back into batter again.
The three most established plastic 3D printing processes today are the following:
-
Fused deposition modeling (FDM) 3D printers melt and extrude thermoplastic filaments, which a printer nozzle deposits layer by layer in the build area.
-
Stereolithography (SLA) 3D printers use a laser to cure thermosetting liquid resins into hardened plastic in a process called photopolymerization.
-
Selective laser sintering (SLS) 3D printers use a high-powered laser to fuse small particles of thermoplastic powder.
Video Guide
Having trouble finding the best 3D printing technology for your needs? In this video guide, we compare FDM, SLA, and SLS technologies across popular buying considerations.
Watch the Videos
Fused deposition modeling (FDM), also known as fused filament fabrication (FFF), is the most widely used form of 3D printing at the consumer level, fueled by the emergence of hobbyist 3D printers.
This technique is well-suited for basic proof-of-concept models, as well as quick and low-cost prototyping of simple parts, such as parts that might typically be machined.
Consumer level FDM has the lowest resolution and accuracy when compared to other plastic 3D printing processes and is not the best option for printing complex designs or parts with intricate features. Higher-quality finishes may be obtained through chemical and mechanical polishing processes. Industrial FDM 3D printers use soluble supports to mitigate some of these issues and offer a wider range of engineering thermoplastics or even composites, but they also come at a steep price.
As the melted filament forms each layer, sometimes voids can remain between layers when they don’t adhere fully. This results in anisotropic parts, which is important to consider when you are designing parts meant to bear load or resist pulling.
FDM 3D printing materials are available in a variety of color options. Various experimental plastic filament blends also exist to create parts with wood- or metal-like surfaces.
The most common FDM 3D printing materials are ABS, PLA, and their various blends. More advanced FDM printers can also print with other specialized materials that offer properties like higher heat resistance, impact resistance, chemical resistance, and rigidity.
Material | Features | Applications |
---|---|---|
ABS (acrylonitrile butadiene styrene) | Tough and durable Heat and impact resistant Requires a heated bed to print Requires ventilation | Functional prototypes |
PLA (polylactic acid) | The easiest FDM materials to print Rigid, strong, but brittle Less resistant to heat and chemicals Biodegradable Odorless | Concept models Looks-like prototypes |
PETG (polyethylene terephthalate glycol) | Compatible with lower printing temperatures for faster production Humidity and chemical resistant High transparency Can be food safe | Waterproof applications Snap-fit components |
Nylon | Strong, durable, and lightweight Tough and partially flexible Heat and impact resistant Very complex to print on FDM | Functional prototypes Wear resistant parts |
TPU (thermoplastic polyurethane) | Flexible and stretchable Impact resistant Excellent vibration dampening | Flexible prototypes |
PVA (polyvinyl alcohol) | Soluble support material Dissolves in water | Support material |
HIPS (high impact polystyrene) | Soluble support material most commonly used with ABS Dissolves in chemical limonene | Support material |
Composites (carbon fiber, kevlar, fiberglass) | Rigid, strong, or extremely tough Compatibility limited to some expensive industrial FDM 3D printers | Functional prototypes Jigs, fixtures, and tooling |
Stereolithography was the world’s first 3D printing technology, invented in the 1980s, and is still one of the most popular technologies for professionals.
SLA parts have the highest resolution and accuracy, the clearest details, and the smoothest surface finish of all plastic 3D printing technologies. Resin 3D printing is a great option for highly detailed prototypes requiring tight tolerances and smooth surfaces, such as molds, patterns, and functional parts. SLA parts can also be highly polished and/or painted after printing, resulting in client-ready parts with high-detailed finishes.
Parts printed using SLA 3D printing are generally isotropic—their strength is more or less consistent regardless of orientation because chemical bonds happen between each layer. This results in parts with predictable mechanical performance critical for applications like jigs and fixtures, end-use parts, and functional prototyping.
SLA offers the widest range of material options for plastic 3D printing.
SLA 3D printing is highly versatile, offering resin formulations with a wide range of optical, mechanical, and thermal properties to match those of standard, engineering, and industrial thermoplastics.
Formlabs Materials | Features | Applications |
---|---|---|
Standard Resins | High resolution Smooth, matte surface finish | Concept models Looks-like prototypes |
Clear Resin | The only truly clear material for plastic 3D printing Polishes to near optical transparency | Parts requiring optical transparency Millifluidics |
Draft Resin | One of the fastest materials for 3D printing 4x faster than standard resins, up to 10x faster than FDM | Initial Prototypes Rapid Iterations |
Tough and Durable Resins | Strong, robust, functional, and dynamic materials Can handle compression, stretching, bending, and impacts without breaking Various materials with properties similar to ABS or PE | Housings and enclosures Jigs and fixtures Connectors Wear-and-tear prototypes |
Rigid Resins | Highly filled, strong and stiff materials that resist bending Thermally and chemically resistant Dimensionally stable under load | Jigs, fixtures, and tooling Turbines and fan blades Fluid and airflow components Electrical casings and automotive housings |
Polyurethane Resins | Excellent long-term durability UV, temperature, and humidity stable Flame retardancy, sterilizability, and chemical and abrasion resistance | High performance automotive, aerospace, and machinery components Robust and rugged end-use parts Tough, longer-lasting functional prototypes |
High Temp Resin | High temperature resistance High precision | Hot air, gas, and fluid flow Heat resistant mounts, housings, and fixtures Molds and inserts |
Flexible and Elastic Resins | Flexibility of rubber, TPU, or silicone Can withstand bending, flexing, and compression Holds up to repeated cycles without tearing | Consumer goods prototyping Compliant features for robotics Medical devices and anatomical models Special effects props and models |
Medical and dental resins | A wide range of biocompatible resins for producing medical and dental appliances | Dental and medical appliances, including surgical guides, dentures, and prosthetics |
Jewelry resins | Materials for investment casting and vulcanized rubber molding Easy to cast, with intricate details and strong shape retention | Try-on pieces Masters for reusable molds Custom jewelry |
ESD Resin | ESD-safe material to improve electronics manufacturing workflows | Tooling & fixturing for electronics manufacturing Anti-static prototypes and end-use components Custom trays for component handling and storage |
Ceramic Resin | Stone-like finish Can be fired to create a fully ceramic piece | Engineering research Art and design pieces |
Explore Formlabs SLA Materials
Sample part
See and feel Formlabs quality firsthand. We’ll ship a free sample part to your office.
Request a Free Sample Part
Selective laser sintering (SLS) 3D printing is trusted by engineers and manufacturers across different industries for its ability to produce strong, functional parts. Low cost per part, high productivity, and established materials make the technology ideal for a range of applications from rapid prototyping to small-batch, bridge, or custom manufacturing.
As the unfused powder supports the part during printing, there’s no need for dedicated support structures. This makes SLS ideal for complex geometries, including interior features, undercuts, thin walls, and negative features.
Just like SLA, SLS parts are also generally more isotropic than FDM parts. SLS parts have a slightly rough surface finish due to the powder particles, but almost no visible layer lines.
SLS 3D printing materials are ideal for a range of functional applications, from engineering consumer products to manufacturing and healthcare.
The material selection for SLS is limited compared to FDM and SLA, but the available materials have excellent mechanical characteristics, with strength resembling injection-molded parts. The most common material for selective laser sintering is nylon, a popular engineering thermoplastic with excellent mechanical properties. Nylon is lightweight, strong, and flexible, as well as stable against impact, chemicals, heat, UV light, water, and dirt.
Material | Description | Applications |
---|---|---|
Nylon 12 | Strong, stiff, sturdy, and durable Impact-resistant and can endure repeated wear and tear Resistant to UV, light, heat, moisture, solvents, temperature, and water | Functional prototyping End-use parts Medical devices |
Nylon 11 | Similar properties to Nylon 12, but with a higher elasticity, elongation at break, and impact resistance, but lower stiffness | Functional prototyping End-use parts Medical devices |
TPU | Flexible, elastic, and rubbery Resilient to deformation High UV stability Great shock absorption | Functional prototyping Flexible, rubber-like end-use parts Medical devices |
Nylon composites | Nylon materials reinforced with glass, aluminum, or carbon fiber for added strength and rigidity | Functional prototyping Structural end-use parts |
Explore Formlabs SLS Materials
Sample part
See and feel Formlabs SLS quality firsthand. We’ll ship a free sample part to your office.
Request a Free Sample Part
Different 3D printing materials and processes have their own strengths and weaknesses that define their suitability for different applications. The following table provides a high level summary of some key characteristics and considerations.
FDM | SLA | SLS | |
---|---|---|---|
Pros | Low-cost consumer machines and materials available | Great value High accuracy Smooth surface finish Range of functional materials | Strong functional parts Design freedom No need for support structures |
Cons | Low accuracy Low details Limited design compatibility High cost industrial machines if accuracy and high performance materials are needed | Sensitive to long exposure to UV light | More expensive hardware Limited material options |
Applications | Low-cost rapid prototyping Basic proof-of-concept models Select end-use parts with high-end industrial machines and materials | Functional prototyping Patterns, molds, and tooling Dental applications Jewelry prototyping and casting Models and props | Functional prototyping Short-run, bridge, or custom manufacturing |
Materials | Standard thermoplastics, such as ABS, PLA, and their various blends on consumer level machines.![]() | Varieties of resin (thermosetting plastics). Standard, engineering (ABS-like, PP-like, flexible, heat-resistant), castable, dental, and medical (biocompatible). | Engineering thermoplastics. Nylon 11, Nylon 12, and their composites, thermoplastic elastomers such as TPU. |
Beyond plastics, there are multiple 3D printing processes available for metal 3D printing.
-
Metal FDM
Metal FDM printers work similarly to traditional FDM printers, but use extrude metal rods held together by polymer binders. The finished “green” parts are then sintered in a furnace to remove the binder.
SLM and DMLS printers work similarly to SLS printers, but instead of fusing polymer powders, they fuse metal powder particles together layer by layer using a laser. SLM and DMLS 3D printers can create strong, accurate, and complex metal products, making this process ideal for aerospace, automotive, and medical applications.
-
Titanium is lightweight and has excellent mechanical characteristics. It is strong, hard and highly resistant to heat, oxidation, and acid.
-
Stainless steel has high strength, high ductility, and is resistant to corrosion.
-
Aluminum is a lightweight, durable, strong, and has good thermal properties.
-
Tool steel is a hard, scratch-resistant material that you can use to print end-use tools and other high-strength parts..
- Nickel alloys have high tensile, creep and rupture strength and are heat and corrosion resistant.
Compared to plastic 3D printing technologies, metal 3D printing is substantially more costly and complex, limiting its accessibility to most businesses.
Alternatively, SLA 3D printing is well-suited for casting workflows that produce metal parts at a lower cost, with greater design freedom, and in less time than traditional methods.
Another alternative is electroplating SLA parts, which involves coating a plastic material in a layer of metal via electrolysis. This combines some of the best qualities of metal—strength, electrical conductivity, and resistance to corrosion and abrasion—with the specific properties of the primary (usually plastic) material.
Plastic 3D printing is well-suited to create patterns that can be cast to produce metal parts.
With all these materials and 3D printing options available, how can you make the right selection?
Here’s our three-step framework to choose the right 3D printing material for your application.
Plastics used for 3D printing have different chemical, optical, mechanical, and thermal characteristics that determine how the 3D printed parts will perform. As the intended use approaches real-world usage, performance requirements increase accordingly.
Requirement | Description | Recommendation |
---|---|---|
Low performance | For form and fit prototyping, conceptual modeling, and research and development, printed parts only need to meet low technical performance requirements.![]() Example: A form prototype of a soup ladle for ergonomic testing. No functional performance requirements needed besides surface finish. | FDM: PLA SLA: Standard Resins, Clear Resin (transparent part), Draft Resin (fast printing) |
Moderate performance | For validation or pre-production uses, printed parts must behave as closely to final production parts as possible for functional testing but do not have strict lifetime requirements. Example: A housing for electronic components to protect against sudden impact. Performance requirements include ability to absorb impact, housing needs to snap together and hold its shape. | FDM: ABS SLA: Engineering Resins SLS: Nylon 11, Nylon 12, TPU |
High performance | For end-use parts, final 3D printed production parts must stand up to significant wear for a specific time period, whether that’s one day, one week, or several years. Example: Shoe outsoles. | FDM: Composites SLA: Engineering, Medical, Dental, or Jewelry Resins SLS: Nylon 11, Nylon 12, TPU, nylon composites |
Once you’ve identified the performance requirements for your product, the next step is translating them into material requirements—the properties of a material that will satisfy those performance needs. You’ll typically find these metrics on a material’s data sheet.
Requirement | Description | Recommendation |
---|---|---|
Tensile strength | Resistance of a material to breaking under tension. High tensile strength is important for structural, load bearing, mechanical, or statical parts. | FDM: PLA SLA: Clear Resin, Rigid Resins SLS: Nylon 12, nylon composites |
Flexural modulus | Resistance of a material to bending under load.![]() | FDM: PLA (high), ABS (medium) SLA: Rigid Resins (high), Tough and Durable Resins (medium), Flexible and Elastic Resins (low) SLS: nylon composites (high), Nylon 12 (medium) |
Elongation | Resistance of a material to breaking when stretched. Helps you compare flexible materials based on how much they can stretch. Also indicates if a material will deform first, or break suddenly. | FDM: ABS (medium), TPU (high) SLA: Tough and Durable Resins (medium), Polyurethane Resins (medium), Flexible and Elastic Resins (high) SLS: Nylon 12 (medium), Nylon 11 (medium), TPU (high) |
Impact strength | Ability of a material to absorb shock and impact energy without breaking. Indicates toughness and durability, helps you figure out how easily a material will break when dropped on the ground or crashed into another object.![]() | FDM: ABS, Nylon SLA: Tough 2000 Resin, Tough 1500 Resin, Grey Pro Resin, Durable Resin, Polyurethane Resins SLS: Nylon 12, Nylon 11, nylon composites |
Heat deflection temperature | Temperature at which a sample deforms under a specified load. Indicates if a material is suitable for high temperature applications. | SLA: High Temp Resin, Rigid Resins SLS: Nylon 12, Nylon 11, nylon composites |
Hardness (durometer) | Resistance of a material to surface deformation. Helps you identify the right “softness” for soft plastics, like rubber and elastomers for certain applications. | FDM: TPU SLA: Flexible Resin, Elastic Resin SLS: TPU |
Tear strength | Resistance of a material to growth of cuts under tension. Important to assess the durability and the resistance to tearing of soft plastics and flexible materials, such as rubber. | FDM: TPU SLA: Flexible Resin, Elastic Resin, Durable Resin SLS: Nylon 11, TPU |
Creep | Creep is the tendency of a material to deform permanently under the influence of constant stress: tensile, compressive, shear, or flexural.![]() | FDM: ABS SLA: Polyurethane Resins, Rigid Resins SLS: Nylon 12, Nylon 11, nylon composites |
Compression set | Permanent deformation after material has been compressed. Important for soft plastics and elastic applications, tells you if a material will return to its original shape after the load is removed. | FDM: TPU SLA: Flexible Resin, Elastic Resin SLS: TPU |
For even more details on material properties, read our guide to about the most common mechanical and thermal properties.
Once you translate performance requirements to material requirements, you’ll most likely end up with a single material or a smaller group of materials that could be suitable for your application.
If there are multiple materials that fulfil your basic requirements, you can then look at a wider range of desired characteristics and consider the pros, cons, and trade-offs of the given materials and processes to make the final choice.
Try our interactive material wizard to find materials based on your application and the properties you care the most about from our growing library of materials. Do you have specific questions about 3D printing materials? Contact our experts.
Recommend Me a Material
Ultimate Materials Guide - Tips for 3D Printing with PETG
Overview
PETG is a Glycol Modified version of Polyethylene Terephthalate (PET), which is commonly used to manufacture water bottles. It is a semi-rigid material with good impact resistance, but it has a slightly softer surface which makes it prone to wear. The material also benefits from great thermal characteristics, allowing the plastic to cool efficiently with almost negligible warpage. There are several variations of this material in the market including PETG, PETE, and PETT. The tips in this article will apply to all of these PET-based filaments.
- Glossy and smooth surface finish
- Adheres well to the bed with negligible warping
- Mostly odorless while printing
- Poor bridging characteristics
- Can produce thin hairs on the surface from stringing
Hardware Requirements
Before 3D printing with PET / PETG make sure your 3D printer meets the hardware requirements listed below to ensure the best print quality.
Bed
Temperature: 75-90 °C
Heated Bed Recommended
Enclosure Not Required
Build Surface
Glue Stick
Painter’s tape
Extruder
Temperature: 230-250 °C
No special hot-end required
Cooling
Part Cooling Fan Required
Best Practices
These tips will help you reduce the chances of common 3D printing issues associated with PET / PETG such as stringing, oozing, and poor bed adhesion.
Invest In a Good Build Surface
Some 3D printers come with a glass bed or blue painter’s tape installed on the bed. Although these surfaces might work fine for PETG, we recommend using a heated build platform for best results. The heated bed can significantly improve the first layer adhesion, making things much easier for future prints. Many of these heated beds come with a glass surface, allowing you to print directly on the bed without needing to apply any additional layers of tape or glue.
Calibrate Retraction Settings to Reduce Stringing
One of the few common issues that we see with PETG is stringing. These strings are thin hairs, similar to a spider web, that run between the different surface of your 3D print. Preventing these strings requires precisely calibrated retraction settings, so make sure to adjust your retraction distance and speed for the best results. Simplify3D also includes several useful features that can further reduce stringing. The first is called Coasting, which works by reducing the pressure in the nozzle right before the end of a segment. This way, when moving to the next segment, there is less pressure in the nozzle, so you are less likely to see stringing and oozing during that move. Another great option can be found on the Advanced tab of your Simplify3D process settings. By enabling the “avoid crossing outline for travel movements” option, the software will automatically adjust the travel movements of your print to stay on top of the interior of your model as much as possible. This means that the strings stay inside of your part where no one can see them, instead of being on the outside of your model.
If you are looking for more tips to reduce stringing, we have an entire section dedicated to this issue on our Print Quality Guide: How to Reduce Stringing and Oozing.
Optimize Extruder Settings to Prevent Blobs and Zits
When 3D printing at higher temperatures associated with PETG, you may notice small blobs or zits on the surface of your model. These print defects typically occur at the beginning or end of each segment, where the extruder has to suddenly start or stop extruding plastic. There are several ways to eliminate these print defects such as enabling “Extra Restart Distance” or “Coasting” options located in the Extruder tab. Simplify3D also includes an option to perform a dynamic retraction, where the filament is retracted while the extruder is still moving. This completely eliminates blobs that are typically formed from a stationary retraction. To learn more about these features and other tips for reducing blobs on the surface of your print, please refer to our Print Quality Guide.
Pro-Tips
- The glossy surface of PETG is especially useful when using rafts. The part separates easily from the raft and maintains a clean surface finish.
- Try disabling your part cooling fan for the first few layers of the print to prevent warping. This trick especially works well for larger prints.
Get Started with PET / PETG
Now that you are ready to start printing with PET / PETG, here are a few ideas to help you get started – from common applications to popular filament brands.
Common Applications
- Water proof applications
- Snap fit components
- Planter Pot
Sample Projects
- Self-watering Planter
- Water Bottle
- Snap Fit Parts
Popular Brands
- ColorFabb PETG
- eSun PETG
- E3D Spoolworks Edge
- Hatchbox PETG
- HobbyKing PETG
What is the best plastic for 3D printing? Let's figure it out together!
Plastic for 3D printing
After purchasing your own FDM 3D printer, as well as in the course of choosing it, it becomes necessary to choose the right plastic for 3D printing. But how to do this if you are new to 3D printing and have little to no understanding of this issue? Plastic for printing on a 3D printer is in most cases the main component of successful product reproduction. Therefore, we will not save on knowledge, and will tell you how to choose the best plastic for 3D printing.
Types of plastic for a 3D printer
First of all, we need to consider the types of plastic for a 3D printer. Plastic for 3D printing, or filament, is produced in the form of a thin thread with a diameter of 1.75 mm and 3 mm. Most often, filaments with a thickness of 1.75 mm are used in the basic configuration, but some manufacturers of 3D printers provide the ability to install a 3 mm plastic feed system. Plastic for 3D printing has many varieties, among which the most common are ABS and PLA plastic.
Plastic for 3D printing: varieties
By popularity in the Ukrainian market, the following types of plastic for 3D printing can be distinguished:
- PLA (PLA) or polylactide.
Organic and short lived. Suitable for 3D printing of decorative products, but not able to withstand high mechanical loads;
- ABS (ABS) or acrylonitrile butadiene styrene. It has a long life and excellent mechanical properties. Heat-resistant and used for industrial purposes. Shrinks on cooling. It is recommended to print in ventilated areas;
- PVA (PVA) or polyvinyl alcohol. A water-soluble material that is used as a support;
- Nylone (Nylon). An alternative to ABS plastic, suitable for many engineering structures. When printing with nylon, it is recommended to ventilate the room;
- HIPS (High Impact Polystyrene). In terms of physical properties, it is a cross between PLA and ABS. May also emit toxic fumes when printed.
Other questions and answers about 3D printers and 3D printing:
What is the best plastic for a 3D printer?
In fact, there are many more types of plastic for 3D printing. This can include flexible, fluorescent and luminescent filament, wood and metallized materials. But in practice, such consumables are rarely used and are needed for narrowly specific purposes. Metallized plastics are interesting in their own right, but they are at the initial stage of development and are inferior in performance to ordinary reinforced materials. “And what plastic is best for a 3D printer?” - you ask. You should choose based on specific goals. If you intend to print decorative elements that will not be subject to payload, you can look at PLA plastic. If your goal is to print gears, structural parts and other things, look at reinforced materials for 3D printing.
What plastic to print with?
Please note that not every printer supports the full range of 3D printing materials. Before buying a specific filament, check the specifications of your own device to avoid wasting money. The rest is up to you and your imagination. A huge range of colors and shades of plastic is available for sale, matte and glossy, semi- and fully transparent materials. Such a variety will allow you to make almost any product to your taste.
Remember that if you need to buy plastic for 3D printing - 3DDevice store is at your service! We offer a wide range of different materials in all possible color options and are ready to provide advice when choosing a filament.
If you have additional questions that we have not covered, write to us by e-mail and we, if necessary, will add your questions! Best regards, 3DDevice team. We also provide 3D modeling, 3D scanning and 3D printing services. We work all over Ukraine! If you have any questions, please contact us in any way convenient for you. Contacts are listed here. We look forward to collaborating!
Return to the main
90,000 types of plastic for 3D printerHome4 / Useful / Plastic types for 3D printer
09.04.2021
Content
-
- PLA ABS
- HIPS PVA Nylon Every year 3D printing becomes more popular and accessible. Previously, a 3D printer was more like a complex CNC machine, but now manufacturers are meeting users.
-
Does not shrink. This makes it easy to build prefabricated or huge models without changing dimensions.
-
There are no specific requirements for a 3D printer. Any working 3D printer will do. PLA doesn't need a heated table or a closed case.
-
Non-toxic. Due to this, during printing it does not smell or has a barely perceptible aroma of burnt caramel.
-
Diverse color palette.
-
PLA is poorly sanded and machined.
-
It begins to deform already with a slight heating (about 50 degrees).
-
Fragility. Compared to other materials, PLA is very brittle and breaks easily.
-
Decomposes under the influence of ultraviolet radiation. Of course, it will not fall apart into dust, but it can become more brittle and fade.
-
Good strength characteristics allow the production of functional prototypes from ABS.
-
Simple mechanical and chemical processing. ABS is easy to sand and drill, and with an acetone bath you can achieve a perfectly smooth surface.
-
It is currently the most inexpensive type of plastic for 3D printing.
-
Large selection of colors and shades.
-
High shrinkage.
Because of this, it can be problematic to manufacture overall products.
-
Printing requires a heated bed and a closed chamber. Without this, the ABS may peel off the table or crack in layers.
-
During the printing process, ABS can smell bad. Therefore, it is recommended that you print in a ventilated area or use the printer with a sealed chamber and filter.
-
Less shrinkage than ABS.
-
Ease of machining.
-
The matte surface looks very advantageous on decorative products.
-
Food contact allowed (but be sure to check with a specific manufacturer for certificates)
-
For printing, you need a printer with a heated table and a closed chamber.
-
More flexible and less durable than ABS. Because of this, it will not be possible to produce functional products.
-
Small palette of colors.
-
Excellent sinterability of layers.
-
PETG is very strong and wear resistant. Good impact resistance.
-
Virtually no smell when printing.
-
Non-toxic.
-
Little shrinkage.
-
slight shrinkage
-
Transparency. After treatment with solvent, limonel or dichloromethane, beautiful transparent products with an almost smooth surface can be obtained.
-
Easily processed mechanically or chemically.
-
Allowed contact with food.
-
High strength and wear resistance.
-
High slip factor.
-
Heat resistance compared to other 3D printing plastics.
-
High resistance to many solvents.
-
Good for mechanical processing.
Perfectly polished and drilled.
-
Some fillers (eg clay) are abrasive. For such plastics, the standard brass nozzle cannot be used. Will have to buy a harder steel nozzle.
-
Some decorative plastics can clog the small nozzle (0.4 or less). For them, you need to use a “thicker” nozzle.
-
Hardness and strength.
-
Low flammability or non-combustibility.
-
High precision due to low shrinkage.
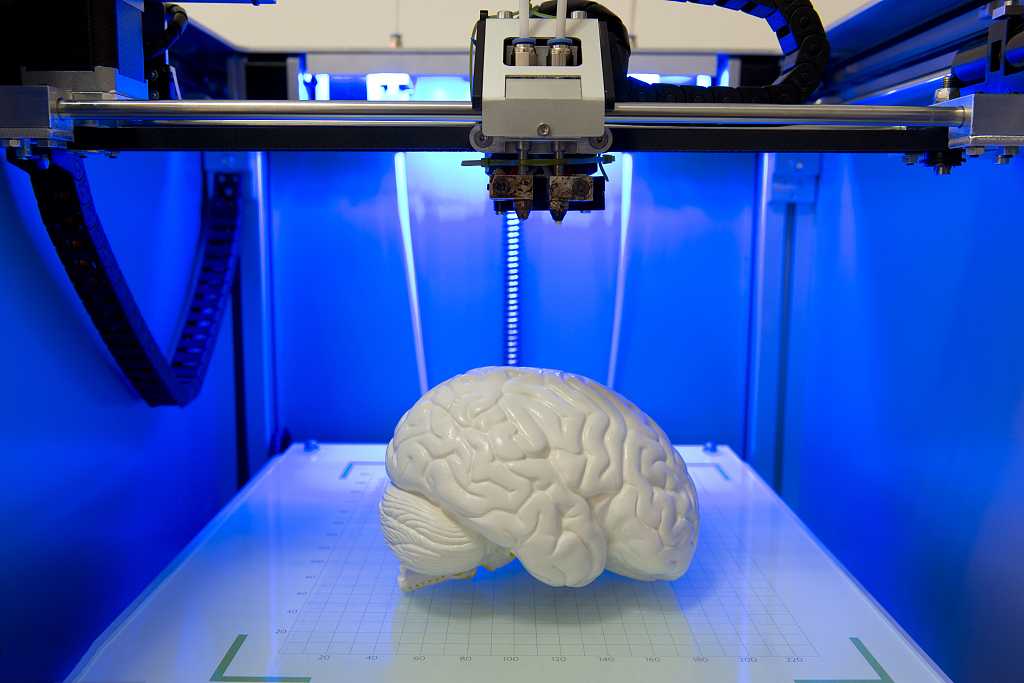
The choice of plastic for a 3D printer is very important, especially when the goal is to print a functional model with certain properties. It will be a shame if the printed gear breaks almost immediately, or the decorative model quickly loses its beauty.
It is important to understand whether the printer will be able to work with the selected plastic. Some materials (most often engineering) require certain conditions for successful printing.
First, decide which model you want to print. What properties should it have? Does the model need to be durable? Or is it a master model for further replication, in which the quality of the surface is important?
90% of 3D printers use 1.75 diameter filament. 3mm diameter is rare, but it is better to check in advance which size is used in your printer.
![]()
PLA
PLA (Polylactide) is the most popular and affordable 3D printer plastic. PLA is made from sugar cane, corn, or other natural raw materials. Therefore, it is considered a non-toxic, biodegradable material.
Extruder temperature - 190-220 degrees. Table heating is not needed, but if the printer's table has a "heater" for better adhesion, you can heat it up to 50-60 degrees. PLA is very easy to work with. The only requirement is to blow the model. There is practically no shrinkage in this material. When printed, it is practically odorless, and if it smells, it smells like burnt caramel.
Pros:
Cons:
PLA is perfect for making dimensional or composite models. For example, decorative interior items, prototyping, electronics cases, etc.
Recently, PLA+ has appeared on the market. It may differ from conventional PLA in improved performance. For example, more durable, with improved layer adhesion.
Dummy turbine
Decorative coasters
ABS
ABS (acrylonitrile butadiene styrene) is the second most popular plastic for 3D printing due to its properties, availability and low price.
Extruder temperature - 220-240 degrees. The temperature of the table is 80-100 degrees. For printing, a heated table is required at the printer. It is desirable to have a closed chamber, because ABS "does not like" drafts. Due to a sharp temperature drop, it can “unstick” from the table or crack in layers. ABS can smell bad when printing, so it is recommended to use the printer with a closed chamber and filters, or print in a well-ventilated area.
Pros:
Cons:
ABS is an engineering plastic. It is suitable for the manufacture of simple functional products.
ABS after chemical treatment in an acetone bath
RU model in ABS
ABS+ differs from conventional ABS in improved strength characteristics (elasticity, rigidity, hardness), less shrinkage and sometimes resistance to certain oils and solvents (eg gasoline).
HIPS
HIPS (high impact polystyrene) - originally conceived as a soluble support plastic for materials with high printing temperatures. For example for ABS or Nylon.
The extruder temperature is 230-260 degrees. The temperature of the table is 80-100 degrees. It is desirable to have a closed camera for a 3D printer.
Pros:
Cons:
Most often, HIPS is used for its intended purpose for printing on 2x extruder printers as a support for ABS. It dissolves perfectly (though not very quickly) in limonel.
Sometimes HIPS is used as an independent material. Products from it are not very durable, but this plastic is loved for easy post-processing. HIPS can be used for models that will subsequently come into contact with food (not hot).
Using HIPS as a Soluble Support
Decorative vase made of HIPS
PVA
PVA (polyvinyl alcohol) is a material that was developed as a water-soluble support for PLA.
Extruder temperature - 190-210. Table heating is not required. PVA is a slightly "capricious" material, it is not recommended to overheat it and print at high speeds.
PVA is very hygroscopic and dissolves in plain water. Therefore, it is only used as a support for PLA or other plastics with print temperatures close to PVA.
Soluble PVA Support
Add to compare
Item added to compare Go
Manufacturer | Tiger3D |
Add to compare
Product added to compare Go
Manufacturer | Tiger3D |
Add to compare
Product added to compare Go
Manufacturer | Esun |
Add to compare
Product added to compare Go
Manufacturer | Esun |
PETG
PETG (polyethylene terephthalate) combines the best properties of PLA and ABS. It is easy to work with, it has a low percentage of shrinkage and excellent sintering of the layers.
Extruder temperature - 220-240 degrees. Table temperature - 80-100 degrees. During the printing process, the model must be well blown.
Pros:
Cons:
PETG is perfect for printing functional models. Due to its low shrinkage, it is often used to make large or composite models. Due to its low toxicity, PETG is often used for products that will come into contact with food.
Cookie cutters and patterned rolling pin
SBS
It is a highly transparent material. At the same time, it is durable and resilient. SBS is a low toxicity plastic. It can be used to print food contact models.
Extruder temperature - 230 -260 degrees. Table temperature - 60-100 degrees. You can print without the closed case on the printer.
Pros:
Cons:
SBS is excellent for translucent vases, children's toys and food containers. Or functional things that require transparency, such as custom turn signals for a motorcycle or car, lamps or bottle prototypes.
Vases are perfectly printed with a thick nozzle (0.7-0.8) in one pass (printing in 1 wall or spiral printing in a slicer).
![]()
Models of bottles after chemical treatment
Nylon
Nylon (polyamide) is considered the most durable material available for home 3D printing. In addition to good abrasion resistance and strength, it has a high slip coefficient.
Extruder temperature - 240-260 degrees. The temperature of the table is 80-100 degrees. Nylon is a very capricious and hygroscopic material - it is recommended to dry the coil with plastic before use. For printing, you need a printer with a heated table and a closed chamber, without this it will be difficult to print something larger than a small gear.
Pros:
Cons:
Nylon is perfect for making wear-resistant parts - gears, functional models, etc. Sometimes nylon is used to print bushings.
Nylon gear
Add to compare
Product added to compare Go
Manufacturer | Tiger3D |
Add to compare
Product added to compare Go
Manufacturer | Tiger3D |
Add to compare
Product added to compare Go
Manufacturer | Esun |
Add to compare
Product added to compare Go
Manufacturer | Bestfilament |
Soft plastics
FLEX (TPU, TPE, TPC) is a material similar to silicone or rubber. It is flexible and elastic, but at the same time tear-resistant. For example, TPE is a rubbery plastic, while TPU is more rigid.
FLEX are printed at a temperature of 200-240 (depending on the material). A heated table is not required. On printers with direct material feed (feed mechanism on the print head), there are usually no problems with printing. On a bowden feeder (the feed mechanism is located on the body), printing with very soft plastics can be difficult. Usually it is necessary to additionally adjust the clamping of the bar. The main nuance is the very low print speeds - 20-40mm.
Pros:
Cons:
Depending on the type of FLEXa, the models can be flexible or rubber-like. This material, depending on its softness, can be used to print gaskets, insoles, belts, tracks or other models that require flexibility or softness.
FLEX belt
Trainers with flexible soles
Wheel for RC model
Decorative plastics
Decorative plastics are PLA plastics with various fillers (wood or metal shavings). Or with dyes selected to imitate different materials. Since the base of the plastic is PLA, it is very easy to print.
Extruder temperature - 200-220 degrees (depending on the manufacturer). A heated table is not required.
Pros:
Cons:
Depending on the filler, different material properties are obtained. Plastics that use only dye do not require additional processing. Materials with "fillers" may sometimes require additional post-processing.
Plastics with metal fillers after printing must be processed with a metal brush. Then the Metal content will show through and the model will resemble a metal casting.![]()
Plastics with metallic powder
These plastics are often used for printing key chains, decorative models and interior details.
If the plastic has a high content of wood dust, then it is recommended to use a larger nozzle diameter (0.5 or more), a smaller nozzle can quickly become clogged during printing.
Wood-filled plastic ground
Plastic key rings with copper dust
Engineering plastics
These are nylon-based plastics with fillers that improve strength, heat-resistant and other characteristics, help to achieve less shrinkage of the material. For example - carbon fiber, carbon fiber or fiberglass.
Extruder temperature - 240-300 degrees (depending on the manufacturer). Table temperature - 90-110 degrees. Since plastics are based on nylon, the requirements for printing are similar. This is a heated table and a closed printer case.
Pros:
Cons:
3D printers use brass nozzles, some plastics can quickly “waste” it during printing. For such materials it is recommended to use steel nozzles.
These are highly specialized plastics used for a specific task, depending on the filler. For example, functional parts that do not lose their shape when heated, are resistant to many solvents, etc.
Functional Carbon Fiber Composite Prototype
Composite frame
Polycarbonate ashtray
Totals
This is of course not the whole list of materials for 3D printing. There are many highly specialized engineering and decorative plastics for specific tasks.
Manufacturers are constantly trying to replenish the range of materials for 3D printing. Already familiar materials are improved for more comfortable printing. There are many interesting decorative plastics imitating different materials - ceramics, clay, wood, metals.
And of course, the assortment of engineering plastics is constantly updated. Now there are many interesting materials for highly specialized tasks - for example, burnable plastic with a low ash content for subsequent casting in metal.
Burnout plastic
Before buying a coil, read the information on the website of the manufacturer or seller. There you can find some nuances of printing for a particular plastic. The manufacturer indicates the recommended temperature range on the box. Sometimes, for quality printing, it is recommended to print several tests to adjust the temperature settings, retract, etc.
Try to store the started coil in silica gel bags.