3D printing materials abs
Ultimate Materials Guide - Tips for 3D Printing with ABS
Overview
ABS (Acrylonitrile Butadiene Styrene) has a long history in the 3D printing world. This material was one of the first plastics to be used with industrial 3D printers. Many years later, ABS is still a very popular material thanks to its low cost and good mechanical properties. ABS is known for its toughness and impact resistance, allowing you to print durable parts that will hold up to extra usage and wear. LEGO building blocks are made from this material for that same reason! ABS also has a higher glass transition temperature, which means the material can withstand much higher temperatures before it begins to deform. This makes ABS a great choice for outdoor or high temperature applications. When printing with ABS, be sure to use an open space with good ventilation, as the material tends to have a slight odor. ABS also tends to contract quite a bit as it cools, so controlling the temperature of your build volume and the part inside can have major benefits.
- Low Cost
- Good impact and wear resistance
- Less oozing and stringing gives models smoother finish
- Good heat resistance
- Heavy warping
- Needs heated bed or heated chamber
- Produces a pungent odor while printing
- Parts tend to shrink leading to dimensional inaccuracy
Hardware Requirements
Before 3D printing with ABS make sure your 3D Printer meets the hardware requirements listed below to ensure the best print quality.
Bed
Temperature: 95-110 °C
Heated Bed Required
Enclosure Recommended
Build Surface
Kapton tape
ABS Slurry
Extruder
Temperature: 220-250 °C
No special hot-end required
Cooling
Part Cooling Fan Not Required
Best Practices
These tips will help you reduce the chances of common 3D printing issues associated with ABS such as warping and fumes.
Control Warping
One of the most common print quality issues with ABS is warping. As the plastic cools from its extrusion temperature down to the room temperature, this change in temperature causes the plastic to shrink and contract. This can be particularly troublesome for the first layer, as this change in size can frequently cause the part to separate from the bed, ruining the print. You can minimize this effect using a proper build surface heated to 110º C. The build platform will transfer some of its heat to the first few layers of your part, which will prevent them from shrinking and separating from the bed. It is also common to set the extruder temperature about 10 to 20 degrees higher for the first few layers of your print, which can also help reduce the risk of separation. Simplify3D gives you complete control over your bed and extruder temperatures, so you easily set the desired values on a per-layer basis using the Temperature tab of your process settings. While these changes can help with the bottom layers of your print, taller parts may have issues as the layers get further away from the bed.
When printing larger parts, consider adding an enclosure around your printer to maintain a higher temperature around your print. The enclosure can also prevent wind drafts that could rapidly cool the part during printing. If you’ve followed these steps, but you’re still having trouble with warping and separation, our Print Quality Guide has an entire section dedicated to warping which can give you even more information on the topic: How to Prevent Warping.
Using Brims and Rafts
When printing large parts, or thin delicate parts, you may find that you still have trouble getting these parts to properly adhere to the bed. In these cases, adding a brim or a raft to your print can be a great way to anchor these part to the build platform and prevent warping. A brim will add several rings of plastic around your model on the first few layers, creating extra surface area to hold down the edges of your part. Using a raft will actually print an entirely new plastic structure underneath your print, which can be removed after the print is completed. The rafts in Simplify3D were heavily optimized for Version 4.0 allowing them to print faster and use more material, but you may still find that a brim is faster for larger parts. If you want to learn more about these options, we have an in-depth article that explains all of the differences between rafts, skirts, and brims to help you get started.
Print In a Well Ventilated Area
Printing with ABS is known to produce a strong odor with fumes that could potentially be harmful if inhaled in large quantities. Avoid confined spaces and place your printer in a well-ventilated area to avoid these issues. Newer 3D printers may include a separate air-filtration system or HEPA filter that can deal with these fumes right from the source. If you printer doesn’t include these features or you’re limited in where you can place it, consider opening a window or using a flexible air duct from your local hardware store to help route the fumes outside.
Pro-Tips
- Bed adhesion can be improved by using an ABS slurry.
You can make this slurry on your own by mixing small pieces of ABS filament with acetone and applying the mixture on the bed. There are also several pre-packaged versions of the product that can be purchased.
- When doing a dual extrusion print, PLA can be a good break-away support material as it does not adhere strongly to ABS.
Get Started with ABS
Here are a few tips to help you get started with ABS. You can view some common applications below, select from a typical sample project, or even view popular filament brands if you’re looking to stock up on this low cost material.
Common Applications
- Cases or Project Enclosures
- Toys or Action Figures
- Automotive hardware
Sample Projects
- Lego Bricks
- Door Catch
- Fidget Spinner
Popular Brands
- Hatchbox ABS
- FormFutura ABS pro, EasyFil ABS, TitanX
- eSun ABS, ABS+
- HobbyKing ABS
All you need to know about ABS for 3D printing
Published on June 6, 2019 by Carlota V.
ABS for Acrylonitrile Butadiene Styrene is a thermoplastic polymer quite common in the industry. It is mainly known for its good impact resistance at low temperatures and for creating lightweight parts. Mainly used in the household appliance sector, it is also found in boat hulls, decoration pieces, toys, and especially in the famous bricks developed by LEGO. ABS plastic is also very popular in the FDM 3D printing market – as it is the most widely used material in this sector with PLA.
Today, we give you an overview of the main characteristics of ABS plastic for 3D printing, including its printing parameters and applications.
Legos are manufactured with ABS
The production process
One of the first plastics to be used with industrial 3D printers, it was developed around 1990. This thermoplastic polymer is what is called a ‘terpolymer’ and obtained most often by polymerization of acrylonitrile and styrene in the presence of polybutadiene – generally 20% acrylonitrile, 25% butadiene and 55% styrene. Manipulating these proportions can therefore modify the properties of ABS; styrene, for example, is the element that gives ABS its rigidity and brilliance, while butadiene gives it its impact resistance and low temperature properties.
The plastic injection industry is one of the main consumers of ABS plastic: the material has good rigidity, high impact resistance and great lightness, while remaining very affordable in terms of price. It has also been a popular material in the 3D melt-deposited printing market for some years now, one of the first filaments used in the sector with PLA – both materials are easier to print than other technical and inexpensive thermoplastics.
ABS plastic is widely used in injection moulding | Credits: Plastic Precision Molding
The characteristics of ABS filaments in 3D printing
Available in the form of filaments with a diameter of 1.75 mm or 2.85 mm and in several colours, ABS has interesting properties for many industries that want to 3D print functional parts or prototypes. Although it is more difficult to print than PLA, ABS remains a very popular material for 3D printing professionals due to its resistance to impact and high temperature (between -20°C and 80°C). It is opaque, offers smooth and shiny surfaces and can be welded by chemical processes using acetone.
ABS has a melting temperature of around 200°C, it is therefore recommended that the extrusion temperature be between 230 and 260°C. The use of a heating plate (between 80 and 130°C) is mandatory: it is a plastic that shrinks on contact with air, causing the part to shrink (or warp) and thus detaching itself from the plate. For large parts, it is even advisable to use a special adhesive such as Kapton or an adhesive lacquer. Finally, a 3D printer with a closed enclosure is preferable because ABS plastic emits particles that can be dangerous for the user.
A heating plate is necessary to avoid the phenomenon of warping
In terms of printing supports, ABS is easily printed with HIPS, a material that has the same tray and extrusion temperatures. This material dissolves quickly in D-Limonene, a lemon-based solvent.
Little post-processing is required when printing with this thermoplastic polymer, a key advantage that will save time in the production of complex parts. It can be painted and resists well to time with few observed deformations. Finally, it is a material that must be kept dry because it absorbs moisture from the air, which will make it much more difficult to print.
Solutions such as the PolyBox allow to keep the filaments protected from humidity
The main manufacturers
Many players now offer ABS plastic in the form of filaments; among the main ones are the well-known supplier Stratasys, the Chinese Esun but also Ultimaker, FormFutura, Innofil3D, etc. There is a wide selection of colours, with prices ranging from 15 to 60€ depending on the brand.
Be aware that there are loaded filaments where additives are added to ABS: for example, ABS based on carbon fibres or aramid fibres, better known as Kevlar. These fibres, for example, reduce the warping phenomenon of ABS and therefore provide greater precision. Carbon, on the other hand, reinforces the initial mechanical properties of the material. These more technical materials are generally more expensive and have different printing parameters.
Several manufacturers now offer ABS plastic
Finally, although ABS plastic is mainly used in FDM 3D printing, there is an ABS resin for stereolithography that has the same mechanical properties as the ABS thermoplastic.
Did this help? Let us know in a comment below or on our Facebook and Twitter pages! Sign up for our free weekly Newsletter, all the latest news in 3D printing straight to your inbox!
types, applications and features
3D printing enables rapid and cost-effective prototyping and production of models for a wide range of applications. But choosing the right 3D printing technology is only one side of the coin. Ultimately, the ability to create models with the required mechanical properties, functional characteristics or appearance will depend on the materials.
This comprehensive guide provides information on the most popular plastic and metal 3D printing materials available, compares their properties and applications, and provides guidance on how to select the most suitable material for your project. nine0003
Interactive Material
Need help choosing your 3D printing material? Our new interactive materials wizard will help you select the right material from our growing range of polymers, based on your intended application and the properties that matter most to you.
Get material recommendations
Dozens of plastic materials are available for 3D printing. Each of them has unique properties suitable for specific applications. To make it easier to find the best material for a particular model or product, let's first look at the main types of plastics and the various 3D printing processes. nine0003
There are two main types of plastics:
-
thermoplastics are the most common type of plastics.
The main feature that distinguishes them from thermosetting plastics is their ability to withstand multiple melting and solidification cycles. Thermoplastics can be heated and shaped into desired shapes. This process is reversible because no chemical bond is formed. As a result, they can be recycled or melted down and reused. Thermoplastics can be compared to butter: it melts and hardens many times. With each melting cycle, the properties of thermoplastics change slightly. nine0003
-
thermoset plastics (also called thermosets) remain permanently solid after polymerization. The polymers in thermosetting plastics are crosslinked during the polymerization process, which is induced by heat, light, or appropriate radiation. Thermoset plastics decompose when heated, rather than melt. In addition, they do not change their shape when cooled. It is not possible to recycle thermosetting plastics or restore the material to its original state. Thermosetting is like pie dough: once baked, the pie cannot be melted back into dough.
nine0003
The three most common plastic 3D printing processes today are:
-
Fused Deposition Modeling (FDM) 3D printers melt and extrude thermoplastic filaments, which the printer's nozzle deposits layer by layer on the work area.
-
The Stereolithography (SLA) 3D Printer uses a laser to photopolymerize thermoset liquid polymers into a hardened plastic. nine0003
-
The Selective Laser Sintering (SLS) 3D Printer is equipped with a high power laser to sinter fine particles of thermoplastic powder.
How-to video
Can't find the 3D printing technology that best suits your needs? In this video tutorial, we compare Fused Deposition Modeling (FDM), Stereolithography (SLA), and Selective Laser Sintering (SLS) technologies in terms of the top factors to consider when purchasing. nine0003
Watch video
Fused fusion modeling (FDM), also known as fused filament manufacturing (FFF), is the most common form of consumer grade 3D printing, fueled by the rise of hobbyist 3D printers.
This method is well suited for making basic experimental models, as well as for quickly and inexpensively prototyping simple products, such as parts that are usually machined. nine0003
Consumer grade FDM has the lowest resolution and accuracy of any other plastic 3D printing process, making it unsuitable for printing complex designs or models with intricate features. It is possible to improve the surface quality of models printed using this technology using chemical and mechanical polishing processes. FDM-based industrial 3D printers, which offer a wider range of engineering thermoplastics, can solve these problems, but are also much more expensive. nine0003
Each layer is formed with a thermoplastic thread. Sometimes, if the layers are not completely adjacent to each other, there may be voids between them. As a result, anisotropic models are obtained, which is important to consider when designing products that must withstand load and be resistant to tension.
FDM 3D printing materials are available in a variety of colors. There are also various experimental mixtures of thermoplastic threads designed to create models with a surface that mimics wood or metal. nine0003
The most common materials for 3D printing in FDM technology are ABS (acrylonitrile butadiene styrene), PLA (polylactic acid) and various mixtures of these polymers. More advanced FDM printers can also print on other materials with different properties, such as increased temperature and chemical resistance, impact resistance, and rigidity.
Material | Features | Methods of use | |||||
---|---|---|---|---|---|---|---|
ABS (acrylonitril-butadien-styrol) | Strong and durable Thermal and impact-resistant need for a heated printing platform | Easiest media to print with FDM technology Strong, tough but brittle Less resistant to temperature and chemicals The biodegradable does not have a smell of | Conceptual models Realistic prototypes | ||||
PETG (polyethylenertalatlatglycol) | is compatible with low printing temperatures . ![]() | Waterproof application Clip-on components | |||||
nylon | Hard, durable and light Strong and partially flexible heat -resistant and shockproof Complex for printing using FDM | Functional Prototypes Basement models | TPU (thermal polyurate) | 9008 9008 9008 9008 9008 9008 9008 9008 Excellent vibration dampingFlexible Prototypes | |||
PVA (polyvinyl alcohol) | Soluble support structure material The material for supporting structures | ||||||
impact -resistant polystyrene | The material for creating soluble supporting structures, the most commonly used with ABS | Material for supporting structures | |||||
Composit materials (carbon, composite composite materials are dissolved in water. Kevlar, fiber optic) | Strong, tough and incredibly hard Only compatible with some expensive industrial 3D printers based on FDM technology | Functional prototypes Clamping fixtures, fixtures, tooling |
Invented in the 1980s, stereolithography is the world's first 3D printing technology and is still one of the most popular among professionals today.
Models printed with stereolithography printers have the highest resolution and accuracy, the sharpest detail and the smoothest surface of any other plastic 3D printing technology. Resin 3D printing is a great option for producing highly detailed prototypes that require tight tolerances and smooth surfaces such as molds, templates, and functional models. Models printed using SLA technology can be easily polished and/or painted after printing, resulting in highly detailed finished products. nine0003
Models printed on SLA 3D printers are generally isotropic: their strength is more or less constant and independent of orientation, since chemical bonds occur between each layer. This results in models with predictable mechanical characteristics critical for applications such as fasteners, fixtures, finished products, and functional prototypes.
Stereolithography supports a wide range of plastic 3D printing materials. nine0003
SLA 3D printing is versatile and provides a wide range of optical, mechanical and thermal properties that match those of standard, engineering and industrial thermoplastics.
Materials of FORMLABS | Characteristics | Methods of use | |
---|---|---|---|
Standard polymers | High resolution Smote, matte surface | Conceptual models 958 Conceptual models | Conceptual Models Realistic prototypes |
Clear Resin | The only truly transparent material for 3D printing from plastics can be polished to almost full optical transparency | models, which should be optically transparent | |
DRAFT REDI | One of the fastest 3D printing materials Prints 4x faster than standard resins and 10x faster than FDM | Initial prototypes Rapid iterations | |
Tough Resin and Durable Resin | Materials that are tough, strong, functional and dynamic Able to withstand compression, tension, bending and impact without breaking Various materials with properties similar to ABS | Enclosures and Enclosures Clamps and Mounting Devices Connectors Wear Prototypes | |
Rigid Resins | Highly filled, stiff and strong material, resistant to bending Resistant to temperature and chemicals Maintains dimension under load | Clamping and clamping fixtures, tooling Turbines and fan blades Fluid/air components Electrical enclosures and enclosures used in the automotive industry | |
High Temp Resin | High temperature resistant High Precision | Hot Air, Gas, and Liquid Components Heat Resistant Fasteners, Housings, and Fixtures Molds and Inserts | |
Flexible Resin and Elastic Resin | Flexibility of Rubber, TPU, or Silicone compression Withstand many successive cycles without wear | Consumer product prototypes Foldable structures for robotics Medical devices and anatomy models Props and models for special effects | |
Medical and dental resins | A wide range of biocompatible resins for the manufacture of medical and dental products | Dental and medical products, including surgical templates, dentures and prosthetic limbs | |
Lost Wax and Vulcanized Rubber Casting Materials Easy to cast, allows for intricate designs and retains shape well | Products for trying on Models for reusable press forms Jewelry to order | ||
Ceramic Resin | Surface System, similar to the Firing Personal Product, the possibility of firing for creating a real ceramic product | Technical survival Unique articles 908 |
Sample
Experience Formlabs print quality for yourself. We will send a free print sample directly to your office. nine0003
Request a free sample
Selective laser sintering (SLS) 3D printing is a technology trusted by engineers and manufacturers across industries to create durable and functional models. With its low model cost, high performance, and use of common materials, this technology is well suited for a wide range of applications, from rapid prototyping to low-volume production, limited trial runs, or custom-made products. nine0003
The green powder supports the model during printing and eliminates the need for special support structures. As a result, SLS is ideal for complex geometries, including internal features, undercuts, thin walls, and negative draft features.
Like stereolithography, SLS produces more isotropic models than FDM models. Models created with SLS technology have a slightly rough surface due to powder particles, but have almost no visible layer lines. nine0003
SLS 3D printing materials are ideal for a range of functional applications, from consumer product design to manufacturing and healthcare applications.
Compared to FDM and SLA technologies, SLS technology allows the use of a limited number of materials. However, the available materials have excellent mechanical properties. They have strength comparable to die-cast models. The most common selective laser sintering material is nylon, a popular engineering thermoplastic with excellent mechanical properties. Nylon is light, strong and flexible, resistant to impact, heat, chemicals, UV radiation, water and dirt. nine0003
Material | Description | Methods of use |
---|---|---|
Nylon 12 Powder | Strong, hard and durable Siberian, Solp. water | Functional prototypes End use products Medical devices |
Nylon 11 Powder | Similar properties to Nylon 12 Powder. Possesses greater elasticity, elongation at break and impact resistance, but less rigidity | Functional prototypes Products for the final use of Medical devices |
TPU | Flexible, elastic, elastic resistant to deformation High resistance to ultraviolet Excellent damping capacity | .![]() Medical devices |
Nylon composites | Nylon materials reinforced with glass, aluminum or fiberglass for greater strength and rigidity | Functional Prototypes Structural End-Use Products |
Sample
Experience Formlabs SLS print quality for yourself. We will send a free print sample directly to your office.
Request a free sample
Different 3D printing materials and processes have their own advantages and disadvantages that make them suitable for different scenarios. The following table provides a brief overview of some of the main features and factors to consider. nine0092
Poor detail
Limited conformance to design design
High cost of industrial devices if precision and high performance materials are required
Basic experimental models
Production of special end-use products using professional industrial devices and materials
Templates, molds and tooling
Dental products
Prototypes and molds for casting jewelry
Props and models
Small-scale production, production of limited trial runs, creation of products to order
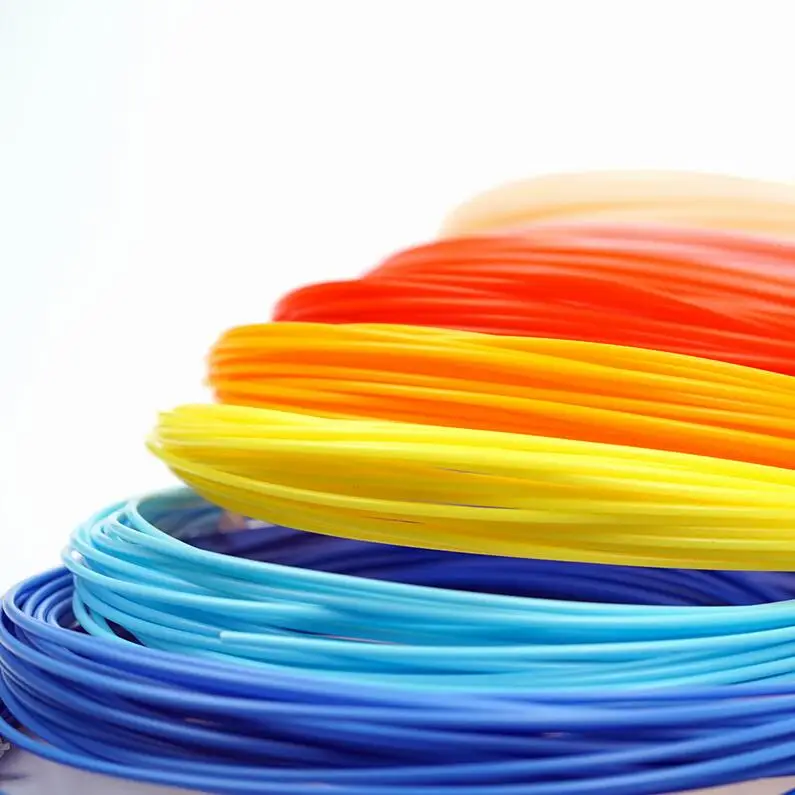
There are several 3D printing processes not only from plastics, but also from metals.
Metal FDM printers are similar in design to traditional FDM printers, but use extruded metal rods held in place by a resin binder. The finished models are in an intermediate state and then sintered in an oven to remove the binder.
SLM and DMLS printers are similar to SLS printers, but instead of polymer powders, they fuse metal powder particles layer by layer using a laser. 3D printers based on SLM and DMLS technologies can create strong, precise and complex metal products, making this process ideal for the aerospace, automotive and medical industries.
-
Titanium is a light metal with excellent mechanical properties. It is strong, hard and highly resistant to heat, oxidation and acids. nine0003
-
stainless steel has high strength, ductility and corrosion resistance.
-
aluminum is a lightweight, durable, strong metal with good thermal properties.
-
Tool Steel is a hard, scratch-resistant material that can be used to print end-use tools and other high-strength products. nine0003
- nickel alloys have high tensile, creep and tensile strength, as well as heat and corrosion resistance.
Compared to plastic 3D printing technologies, metal 3D printing is much more expensive and difficult, and therefore beyond the reach of most companies.
As an alternative to casting workflows that produce metal models cheaper and faster than traditional methods and provide greater design freedom, SLA 3D printing is well suited. nine0003
Another alternative is galvanization of SLA printed models. It involves applying a layer of metal to plastic using electrolysis. This combines some of the best qualities of metal (strength, electrical conductivity, corrosion and abrasion resistance) with the special properties of the base (usually plastic) material.
Plastic 3D printing is well suited for creating templates that can be cast to produce metal models. nine0003
With so many materials and options available for 3D printing, making the right choice can be difficult.
We provide a 3-step process for selecting the right material for 3D printing.
Plastics used for 3D printing have different chemical, optical, mechanical and thermal characteristics that affect the properties of 3D printed models. As you move from the intended use case to the actual operating environment, the performance requirements increase accordingly. nine0003
Requirement | Description | Recommendations |
---|---|---|
Low Efficiency | Example: Prototype mold for a ladle for ergonomic testing. | FDM PLA SLA: Standard Resins, Clear Resin (transparency), Draft Resin (fast) |
Medium Efficiency | For validation or pre-production use, printed models should have properties as close as possible to those of final production models , for functional testing, but do not meet stringent requirements regarding service life. Example: housing for electronic components to protect against sudden impacts. Functional characteristics include the ability to absorb impact energy. In addition, the body must snap into place and retain its shape. nine0003 | FDM ABS SLA: Engineering Resins SLS: Nylon 11 Powder, Nylon 12 Powder, TPU |
High Efficiency | Final 3D printed models need to be highly stable to achieve end use products to wear and tear over a certain period of time, whether it be a day, a week or several years.![]() Example: shoe soles. Functional features include rigorous cycling and unloading life testing, color fastness over many years, and tear resistance, among other things. nine0003 | FDM Composites SLA: Engineering, Medical, Dental or Jewelry Resins SLS: Nylon 11 Powder, Nylon 12 Powder, TPU, Nylon Composites |
material requirements: material properties that will satisfy these requirements. These indicators are usually given in the technical specifications of the material. nine0003
Requirement | Description | Recommendation | |
---|---|---|---|
Tensile strength | Resistance of material to fracture under tension. High tensile strength is important for structural, load-bearing, mechanical or static models. | FDM PLA SLA: Clear Resin, Rigid Resin SLS: Nylon 12 Powder, Nylon Composites | |
Flex Modulus | Material resistance to bending under load.![]() | FDM PLA (high), ABS (medium) SLA: Rigid Resin (high), Tough Resin and Durable Resin (medium), Flexible Resin and Elastic Resin (low) SLS: Nylon composite materials (high value), Nylon 12 Powder (medium value) | |
Elongation | Material resistance to tensile failure. Allows you to compare the degree of stretching of flexible materials. It also indicates whether the material is stretched or immediately destroyed. nine0092 | FDM ABS (medium), TPU (high) SLA: Tough Resin and Durable Resin (medium), Flexible Resin and Elastic Resin (high) SLS: Nylon 12 Powder (medium), Nylon 11 Powder (medium), TPU (high) | |
Impact strength | The ability of a material to absorb impact and its energy without breaking. Shows toughness and durability. Allows you to determine how easily the material breaks when it falls to the ground or collides with another object.![]() | FDM ABS, Nylon SLA: Tough 2000 Resin, Tough 1500 Resin, Gray Pro Resin, Durable Resin SLS: Nylon 12 Powder, Nylon 11 Powder a certain load. Indicates whether the material is suitable for high temperature applications. | SLA: High Temp Resin, Rigid Resin SLS: Nylon 12 Powder, Nylon composites |
Hardness (durometer) | Material resistance to surface deformation. Allows you to determine the right degree of plasticity for soft plastics such as rubber and elastomers for a particular application. | FDM TPU SLA: Flexible Resin, Elastic Resin SLS: TPU | |
Tear resistance | Material resistance to notching under tension. This indicator is important for evaluating the durability and wear resistance of soft plastics and flexible materials such as rubber. nine0092 | FDM TPU SLA: Flexible Resin, Elastic Resin, Durable Resin SLS: Nylon 11 Powder, TPU | |
Creep | Creep is the tendency of a material to permanently deform under the influence of constant stress: tension or bending, compression, shear .![]() | FDM ABS SLA: Rigid Resin SLS: Nylon 12 Powder, Nylon 9 composites0092 | |
Compression set | Irreversible deformation after material compression. An important indicator for soft plastics and applications where flexibility is needed. Indicates whether the material will restore its original shape after the load is removed. | FDM TPU SLA: Flexible Resin, Elastic Resin SLS: TPU |
For more information on material properties, see our guide to the most common mechanical and thermal properties. nine0003
By converting performance characteristics into material requirements, you can most likely find out which material, or small group of materials, is right for your application.
If several materials meet your basic requirements, a broader range of desired characteristics, as well as the advantages and disadvantages of these materials and processes, can be considered for the final selection.
Use our interactive material wizard. It will help you select the right materials from our growing range of polymers for your application and the properties that matter most to you. Do you have specific questions about 3D printing materials? Contact our experts. nine0003
Get material recommendations
3D Printing Materials | A wide variety of materials
Materials for 3D printing! To date, the main materials for printing on a 3D printer are PLA and ABS plastic. Both materials have long established themselves on the market and are used for printing on a 3D printer using layer-by-layer material build-up technology.
ABS (ABS) plastic is a plastic formed during the polymerization of substances such as acrylonitrile (A) with butadiene (B) and styrene (S). nine0003
PLA plastic, or as it is also called biodegradable plastic, is an aliphatic polyester with a monomer in the form of lactic acid. The materials for the production of such plastic are rapidly renewable resources - corn or sugar cane, that is, starch or cellulose.
PVA plastic. The well-known PVA glue is transferred from a dry state to a liquid of the desired consistency, then melted using special equipment and formed into PVA threads or special granules that are used for 3D printing. nine0003
An even newer material, Nylon, is resistant to a wide range of chemicals and solvents. The materials discussed above are known to everyone who is associated with the 3D technology market.
These are the most commonly used materials. But manufacturers have stepped far ahead, and are already using a wide variety of materials for printing on a 3D printer, for example, clay, resin, seaweed, and more. etc.
Here is a list of the most unexpected and creative materials for 3D printing:
White Resin from Formlabs:
3D Printing Materials
3D printing equipment manufacturer Formlabs introduces a new material - White Resin. The company has recently launched two new 3D printing materials, Clear Resin and Gray Resin. The main feature of the White Resin material is the striking white and opaque color of the material, as well as the exceptional smoothness of the surface of the printed object. In addition, this material is ideal for subsequent staining. nine0003
Titanium Powder for 3D Printing Auto Parts:
British metalworking company Metalysis has released a new cheap titanium powder that is suitable for 3D printing of auto parts and parts. Until now, the most popular materials for 3D printing have been plastics, due to the high cost of producing titanium powders. But recently, Metalysis has found a new, low-cost way to produce titanium powder, which could become the most sought after in the manufacture of equipment and machinery in the aerospace, defense and automotive industries. nine0003
For the production of titanium powder, Metalysis uses rutile, which is electrolyzed directly into titanium powder. This method of obtaining a powder makes it possible to change, if necessary, the size of the powder granules, its purity, morphology and the proportion of the content of alloying elements in the composition.
Metal plastic for ColorFabb 3D printer:
Materials for 3D printing
BronzeFill and CopperFill are two new filaments from the premium Dutch manufacturer colorFabb. Their key feature is the addition of bronze and copper powder to the plastic, which gives the filament additional rigidity, as well as a pleasant metallic sheen and smoothness. To the touch, the model obtained as a result of printing will very much resemble a metal one. nine0003
Bronzefill and CopperFill can be polished to a beautiful metallic sheen just like any other hard bronze and copper items. After polishing, the visible streaks that remain after printing disappear, and the bronze or copper item begins to shine.
Bronze and copper plastic for 3d printing is ideal for metal prototyping and very durable models in industry, architecture, design and other fields.
One of the most amazing materials is graphene:
3D Printing Materials
A 3D printable material with incredible potential for applications in various fields (molecular programming, solar energy, etc. ), it can change the lives of many people. In this regard, the Canadian research company Lomiko Metals Inc. announced the opening of a new special laboratory Graphene 3D Labs Inc., which will focus on the development of high-performance materials based on graphene. Information about the material: graphite or graphene is entirely composed of carbon atoms, but 1 mm of graphite contains about 3 million layers of graphene. Graphite has a three-dimensional crystal structure, while graphene is a two-dimensional crystal 1 atom thick. nine0003
3D Printer Wood Filament:
3D Printing Materials
Dutch 3D printing material company colorFabb has launched WoodFill wood filament. Wooden threads WoodFill are available in two types - Fine (Delicate) and Coarse (Rough). The main difference between these threads is the quality of processing of wood fibers. WoodFill Fine uses finely ground wood particles, WoodFill Coarse threads are thicker - based on coarsely ground wood particles. Wooden threads allow you to print beautiful and original vases, decorative elements and interior items. Finished objects are highly durable and produced in a short time. WoodFill filaments are made up of 30% pine wood fibers and 70% PLA plastic. nine0003
Seaweed 3D Printer Filament:
3D Printing Materials
Le Fabshop is the first company in the world to introduce SWF filaments - "green" filaments based on seaweed.
New materials from Proto-Pasta:
Recently, scientist Aaron Crum and mechanical engineer Dustin Crum launched the Proto-Pasta project, which developed three new materials for use in a desktop 3D printer: Carbon Fiber Reinforced PLA ( PLA reinforced with carbon fiber), High Temperature PLA (high temperature PLA) and Polycarbonate-ABS (ABS with polycarbonate alloy). Compared to all known types of plastic - ABS and PLA, the presented materials have improved performance characteristics and are affordable. Carbon Fiber Reinforced PLA is more resistant to high temperatures than regular PLA. Polycarbonate-ABS (PC-ABS) is characterized by high elasticity and bending strength. nine0003
Rubber material for stereolithography:
Materials for 3D printing
This is a rubber based material ideal for stereolithography printing, the new material has a wide color gamut, allows you to print objects in high resolution, odorless, easy to peel, available from price.
Silk 3D Printing Material:
3D Printing Materials
Another 3D printing material was created from raw silk. The raw silk has been sourced from sustainable sources and treated with epoxy. The silk-based material is flexible and highly durable, thin and light, ideal for 3D printing applications. nine0003
Polished and Raw Brass for 3D Printing Materials:
3D Printing Materials
Shapeways has introduced two new materials to the world at once - Polished Brass and Raw Brass. Polished Brass is a material with a smooth, glossy bright yellow surface. Products printed with its help, then covered with 22 carat gold, are almost indistinguishable from real gold jewelry. Raw Brass is ideal for 3D printing antique or antique-style objects, and is also useful for jewelry prototyping and functional parts. nine0003
Shapeways Soft Plastic:
3D Printing Materials
Shapeways has developed a new soft plastic called Elasto Plastics for use in the production of summer footwear. Elasto Plastics has a milky white color, the material is very flexible, has an uneven grainy surface and is quite strong.
In our online store ac5ffgxkeg.lceqo.ccwc.finefive.ru there is an excellent analogue of Elasto Plastics - this is a unique flexible plastic from a Ukrainian manufacturer - PLASTAN 9 plastic0003
The second analogue - FlexibelPolyEster (FPE) - is a rubber-like elastic plastic thread designed specifically for printing on a 3D printer
Transparent resin for a 3D printer:
Materials for 3D printing stereolithography, according to the technology of layering transparent resin and strengthening the layers with a special laser.
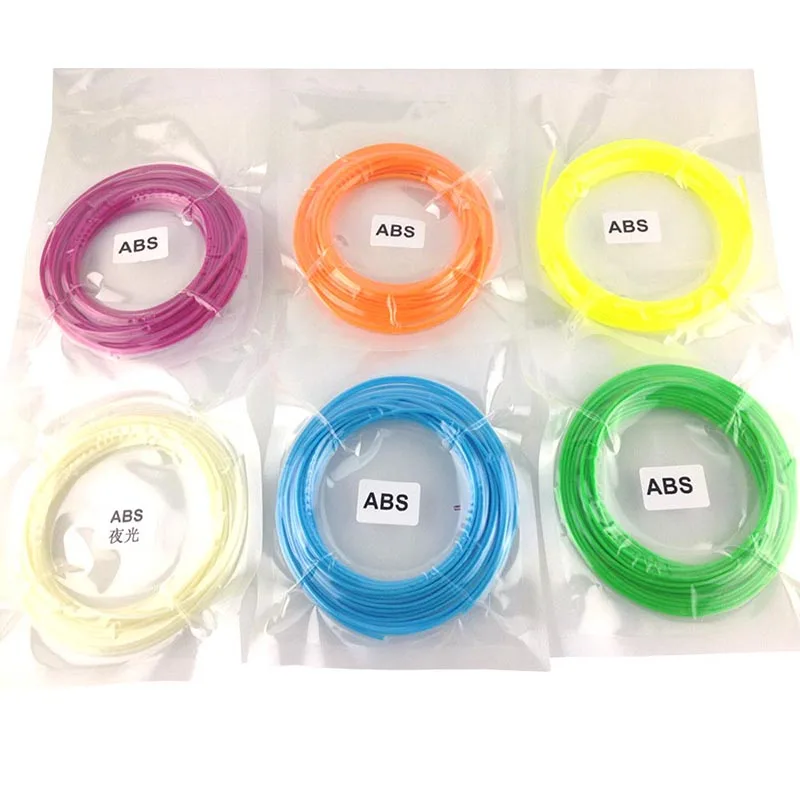