3D printing is an example of
What is 3D Printing? - Technology Definition and Types
3D printing, also known as additive manufacturing, is a method of creating a three dimensional object layer-by-layer using a computer created design.
3D printing is an additive process whereby layers of material are built up to create a 3D part. This is the opposite of subtractive manufacturing processes, where a final design is cut from a larger block of material. As a result, 3D printing creates less material wastage.
This article is one of a series of TWI frequently asked questions (FAQs).
3D printing is also perfectly suited to the creation of complex, bespoke items, making it ideal for rapid prototyping.
Contents
- What materials can be used?
- History
- Technologies
- Process types
- How long does it take?
- Advantages and disadvantages
- What is an STL file?
- Industries
- Services
- FAQs
TWI
TWI is an Industrial Membership based organisation. TWI's experts can provide your company with an extension to your own resources. Our experts are dedicated to helping industry improve safety, quality, efficiency and profitability in all aspects of materials joining technology. Industrial Membership of TWI currently extends to over 600 companies worldwide, embracing all industrial sectors.
You can find out more by contacting us, below:
There are a variety of 3D printing materials, including thermoplastics such as acrylonitrile butadiene styrene (ABS), metals (including powders), resins and ceramics.
Who Invented 3D Printing?
The earliest 3D printing manufacturing equipment was developed by Hideo Kodama of the Nagoya Municipal Industrial Research Institute, when he invented two additive methods for fabricating 3D models.
When was 3D Printing Invented?
Building on Ralf Baker's work in the 1920s for making decorative articles (patent US423647A), Hideo Kodama's early work in laser cured resin rapid prototyping was completed in 1981. His invention was expanded upon over the next three decades, with the introduction of stereolithography in 1984. Chuck Hull of 3D Systems invented the first 3D printer in 1987, which used the stereolithography process. This was followed by developments such as selective laser sintering and selective laser melting, among others. Other expensive 3D printing systems were developed in the 1990s-2000s, although the cost of these dropped dramatically when the patents expired in 2009, opening up the technology for more users.
There are three broad types of 3D printing technology; sintering, melting, and stereolithography.
- Sintering is a technology where the material is heated, but not to the point of melting, to create high resolution items.
Metal powder is used for direct metal laser sintering while thermoplastic powders are used for selective laser sintering.
- Melting methods of 3D printing include powder bed fusion, electron beam melting and direct energy deposition, these use lasers, electric arcs or electron beams to print objects by melting the materials together at high temperatures.
- Stereolithography utilises photopolymerization to create parts. This technology uses the correct light source to interact with the material in a selective manner to cure and solidify a cross section of the object in thin layers.
Types of 3D printing
3D printing, also known as additive manufacturing, processes have been categorised into seven groups by ISO/ASTM 52900 additive manufacturing - general principles - terminology. All forms of 3D printing fall into one of the following types:
- Binder Jetting
- Direct Energy Deposition
- Material Extrusion
- Material Jetting
- Powder Bed Fusion
- Sheet Lamination
- VAT Polymerization
Binder Jetting
Binder jetting deposits a thin layer of powered material, for example metal, polymer sand or ceramic, onto the build platform, after which drops of adhesive are deposited by a print head to bind the particles together. This builds the part layer by layer and once this is complete post processing may be necessary to finish the build. As examples of post processing, metal parts may be thermally sintered or infiltrated with a low melting point metal such as bronze, while full-colour polymer or ceramic parts may be saturated with cyanoacrylate adhesive.
Binder jetting can be used for a variety of applications including 3D metal printing, full colour prototypes and large scale ceramic moulds.
Direct Energy Deposition
Direct energy depositioning uses focussed thermal energy such as an electric arc, laser or electron beam to fuse wire or powder feedstock as it is deposited. The process is traversed horizontally to build a layer, and layers are stacked vertically to create a part.
This process can be used with a variety of materials, including metals, ceramics and polymers.
Material Extrusion
Material extrusion or fused deposition modelling (FDM) uses a spool of filament which is fed to an extrusion head with a heated nozzle. The extrusion head heats, softens and lays down the heated material at set locations, where it cools to create a layer of material, the build platform then moves down ready for the next layer.
This process is cost-effective and has short lead times but also has a low dimensional accuracy and often requires post processing to create a smooth finish. This process also tends to create anisotropic parts, meaning that they are weaker in one direction and therefore unsuitable for critical applications.
Material Jetting
Material jetting works in a similar manner to inkjet printing except, rather than laying down ink on a page, this process deposits layers of liquid material from one or more print heads. The layers are then cured before the process begins again for the next layer. Material jetting requires the use of support structures but these can be made from a water-soluble material that can be washed away once the build is complete.
A precise process, material jetting is one of the most expensive 3D printing methods, and the parts tend to be brittle and will degrade over time. However, this process allows for the creation of full-colour parts in a variety of materials.
Powder Bed Fusion
Powder bed fusion (PBF) is a process in which thermal energy (such as a laser or electron beam) selectively fuses areas of a powder bed to form layer, and layers are built upon each other to create a part. One thing to note is that PBF covers both sintering and melting processes. The basic method of operation of all powder bed systems is the same: a recoating blade or roller deposits a thin layer of the powder onto the build platform, the powder bed surface is then scanned with a heat source which selectively heats the particles to bind them together. Once a layer or cross-section has been scanned by the heat source, the platform moves down to allow the process to begin again on the next layer. The final result is a volume containing one or more fused parts surrounded by unaffected powder. When the build is complete, the bed is fully raised to allow the parts to be removed from the unaffected powder and any required post processing to begin.
Selective laser sintering (SLS) is often used for manufacture of polymer parts and is good for prototypes or functional parts due to the properties produced, while the lack of support structures (the powder bed acts as a support) allows for the creation of pieces with complex geometries. The parts produced may have a grainy surface and inner porosity, meaning there is often a need for post processing.
Direct metal laser sintering (DMLS), selective laser melting (SLM) and electron beam powder bed fusion (EBPBF) are similar to SLS, except these processes create parts from metal, using a laser to bond powder particles together layer-by-layer. While SLM fully melts the metal particles, DMLS only heats them to the point of fusion whereby they join on a molecular level. Both SLM and DMLS require support structures due to the high heat inputs required by the process. These support structures are then removed in post processing ether manually or via CNC machining. Finally, the parts may be thermally treated to remove residual stresses.
Both DMLS and SLM produce parts with excellent physical properties - often stronger than the conventional metal itself, and good surface finishes. They can be used with metal superalloys and sometimes ceramics which are difficult to process by other means. However, these processes can be expensive and the size of the produced parts is limited by the volume of the 3D printing system used.
Sheet Lamination
Sheet lamination can be split into two different technologies, laminated object manufacturing (LOM) and ultrasonic additive manufacturing (UAM). LOM uses alternate layers of material and adhesive to create items with visual and aesthetic appeal, while UAM joins thin sheets of metal via ultrasonic welding. UAM is a low temperature, low energy process that can be used with aluminium, stainless steel and titanium.
VAT Photopolymerization
VAT photopolymerization can be broken down into two techniques; stereolithography (SLA) and digital light processing (DLP). These processes both create parts layer-by-layer through the use of a light to selectively cure liquid resin in a vat. SLA uses a single point laser or UV source for the curing process, while DLP flashes a single image of each full layer onto the surface of the vat. Parts need to be cleaned of excess resin after printing and then exposed to a light source to improve the strength of the pieces. Any support structures will also need to be removed and additional post-processing can be used to create a higher quality finish.
Ideal for parts with a high level of dimensional accuracy, these processes can create intricate details with a smooth finish, making them perfect for prototype production. However, as the parts are more brittle than fused deposition modelling (FDM) they are less suited to functional prototypes. Also, these parts are not suitable for outdoor use as the colour and mechanical properties may degrade when exposed to UV light from the sun. The required support structures can also leave blemishes that need post processing to remove.
The printing time depends on a number of factors, including the size of the part and the settings used for printing. The quality of the finished part is also important when determining printing time as higher quality items take longer to produce. 3D printing can take anything from a few minutes to several hours or days - speed, resolution and the volume of material are all important factors here.
The advantages of 3D printing include:
- Bespoke, cost-effective creation of complex geometries:
This technology allows for the easy creation of bespoke geometric parts where added complexity comes at no extra cost. In some instances, 3D printing is cheaper than subtractive production methods as no extra material is used. - Affordable start-up costs:
Since no moulds are required, the costs associated with this manufacturing process are relatively low.The cost of a part is directly related to the amount of material used, the time taken to build the part and any post processing that may be required.
- Completely customisable:
Because the process is based upon computer aided designs (CAD), any product alterations are easy to make without impacting the manufacturing cost. - Ideal for rapid prototyping:
Because the technology allows for small batches and in-house production, this process is ideal for prototyping, which means that products can be created faster than with more traditional manufacturing techniques, and without the reliance on external supply chains. - Allows for the creation of parts with specific properties:
Although plastics and metals are the most common materials used in 3D printing, there is also scope for creating parts from specially tailored materials with desired properties. So, for example, parts can be created with high heat resistance, water repellency or higher strengths for specific applications.
The disadvantages of 3D printing include:
- Can have a lower strength than with traditional manufacture:
While some parts, such as those made from metal, have excellent mechanical properties, many other 3D printed parts are more brittle than those created by traditional manufacturing techniques. This is because the parts are built up layer-by-layer, which reduces the strength by between 10 and 50%. - Increased cost at high volume:
Large production runs are more expensive with 3D printing as economies of scale do not impact this process as they do with other traditional methods. Estimates suggest that when making a direct comparison for identical parts, 3D printing is less cost effective than CNC machining or injection moulding in excess of 100 units, provided the parts can be manufactured by conventional means. - Limitations in accuracy:
The accuracy of a printed part depends on the type of machine and/or process used.Some desktop printers have lower tolerances than other printers, meaning that the final parts may slightly differ from the designs. While this can be fixed with post-processing, it must be considered that 3D printed parts may not always be exact.
- Post-processing requirements:
Most 3D printed parts require some form of post-processing. This may be sanding or smoothing to create a required finish, the removal of support struts which allow the materials to be built up into the designated shape, heat treatment to achieve specific material properties or final machining.
An STL file is a simple, portable format used by computer aided design (CAD) systems to define the solid geometry for 3D printable parts. An STL file provides the input information for 3D printing by modelling the surfaces of the object as triangles that share edges and vertices with other neighbouring triangles for the build platform. The resolution of the STL file impacts the quality of the 3D printed parts - if the file resolution is too high the triangle may overlap, if it is too low the model will have gaps, making it unprintable. Many 3D printers require an STL file to print from, however these files can be created in most CAD programs.
Due to the versatility of the process, 3D printing has applications across a range of industries, for example:
Aerospace
3D printing is used across the aerospace (and astrospace) industry due to the ability to create light, yet geometrically complex parts, such as blisks. Rather than building a part from several components, 3D printing allows for an item to be created as one whole component, reducing lead times and material wastage.
Automotive
The automotive industry has embraced 3D printing due to the inherent weight and cost reductions. It also allows for rapid prototyping of new or bespoke parts for test or small-scale manufacture. So, for example, if a particular part is no longer available, it can be produced as part of a small, bespoke run, including the manufacture of spare parts. Alternatively, items or fixtures can be printed overnight and are ready for testing ahead of a larger manufacturing run.
Medical
The medical sector has found uses for 3D printing in the creation of made-to-measure implants and devices. For example, hearing aids can be created quickly from a digital file that is matched to a scan of the patient's body. 3D printing can also dramatically reduce costs and production times.
Rail
The rail industry has found a number of applications for 3D printing, including the creation of customised parts, such as arm rests for drivers and housing covers for train couplings. Bespoke parts are just one application for the rail industry, which has also used the process to repair worn rails.
Robotics
The speed of manufacture, design freedom, and ease of design customisation make 3D printing perfectly suited to the robotics industry. This includes work to create bespoke exoskeletons and agile robots with improved agility and efficiency.
TWI has one of the most definitive ranges of 3D Printing services, including selective laser melting, laser deposition, wire and arc additive manufacturing, wire and electron beam additive manufacturing and EB powder bed fusion small-scale prototyping, and more.
Additive Manufacturing
TWI provides companies with support covering every aspect of metal additive manufacturing (AM), from simple feasibility and fabrication projects to full adoption and integration of metal AM systems.
Laser Metal Deposition
TWI has been developing LMD technology for the last ten years. For full details of our capabilities in this area, and to find out more about the process and the benefits it can bring to your business.
Selective Laser Melting
TWI has been developing selective laser melting technology for the last decade. Find out full details of our capabilities in this area and the benefits it can bring to your business.
Can 3D Printing be used for Mass Production?
While there have been great advances in 3D printing, it still struggles to match other manufacturing techniques for high volume production. Techniques such as injection moulding allow for much faster mass production of parts.
Where is 3D Printing Heading in the Future?
As 3D printing technology continues to improve it could democratise the manufacture of goods. With printers becoming faster, they will be able to work on larger scale production projects, while lowering the cost of 3D printing will help its use spread outside of industrial uses and into homes, schools and other settings.
Which 3D Printing Material is most Flexible?
Thermoplastic polyurethane (TPU) is commonly deemed to be the most flexible material available to the 3D printing industry. TPU possesses bendable and stretchy characteristics that many other filaments do not have.
Which 3D Printing Material is the Strongest?
Polycarbonate is seen as the strongest 3D printing material, with a tensile strength of 9,800 psi, compared to nylon, for example, with just 7,000 psi.
Why is 3D Printing Important?
3D printing is important for the many benefits it brings. It allows users to produce items that have geometries which are difficult or impossible for traditional methods to produce. It also allows users with a limited experience to edit designs and create bespoke, customised parts. On-demand 3D printing also saves on tooling costs and provides an advanced time-to-market. 3D printing is important for industries such as aerospace, where it can create lightweight yet complex parts, offering weight saving, the associated fuel reductions and a better environmental impact as a result. It is also important for the creation of prototypes that can advance industry.
Will 3D Printing Replace Traditional Manufacturing?
3D printing has the capability to disrupt traditional manufacturing through the democratisation of production along with the production of moulds, tools and other bespoke parts. However, challenges around mass production mean that 3D printing is unlikely to replace traditional manufacturing where high volume production of comparatively simple parts is required.
Are 3D Printing Fumes Dangerous?
3D printing fumes can be dangerous to your health as the process produces toxic filament fumes. These emissions are produced as the plastic filaments are melted to create the product layer-by-layer. However, correct procedures such as ensuring sufficient ventilation or using extractors can solve this issue.
Related Frequently Asked Question (FAQs)
What are the Pros and Cons of 3D Printing?
The demand is growing due to some of the revolutionary benefits that it can provide. Like almost all technologies it has its own drawbacks that need considering.
How Long Does 3D Printing Take?
There are several factors that determine the time it takes to 3D print a part. These include the size, height, complexity and the printing technology used.
Can 3D Printing Use Metal?
Yes, it is possible to 3D print items from metal. There are several types of process which fall under the heading of metal additive manufacturing.
What is Additive Manufacturing?
Additive manufacturing (AM) is a computer controlled process that creates three dimensional objects by depositing materials, usually in layers.
7 Examples of 3D Printing in the World Today
More and more, 3D printers are becoming much cheaper to purchase, and many experts don’t expect it to be too long before they become a commonality in households across the world. Manufacturing companies are also taking notice of the powerful abilities these machines provide companies and their production processes. Seemingly everyday brings forth another development that expands the limits of 3D printing. From medical devices to aircraft parts to shoes, 3D printing can virtually create anything you can thing of, it’s just a matter of scale. Below are 7 real-world examples of 3D printing that can be seen today.
Your Source for 3D Printers: NeoMetrix Technologies, Inc.
1. Prosthetic Limbs & Body PartsNeoMetrix 3D Prints Custom Prosthetics for Marathon Runner.
3D printing has had a significant impact across the medical industry, from producing custom prosthetic legs for a marathon runner, to creating a model of the human heart to aide surgeons to making a new tail for an alligator that had its tail bitten off as a baby. Recently, a team from Northwestern University Feinberg School of Medicine in Chicago successfully conducted an experiment in which a mouse with 3D printed ovaries actually successfully birthed healthy pups. This is an incredible breakthrough, as there is now substantial belief that this could potentially work with humans given further research and experimentation.
Here’s some examples of 3D printing‘s benefits in the medical industry:
- Open Bionics Introduces Affordable Prosthetic Arm
- Medical Researchers Develop Revolutionary 3D Printed Cornea
- Development of Quick Connect Prosthetic Joints
Believe it or not, 3D printing has the ability to produce entire houses in buildings. This is a remarkable feat for the technology because it could potentially save lives when areas are enduring tough times from things such as natural disasters and war because emergency shelters can be constructed quickly and on-demand using 3D printing technology. How fast can they be built? In Moscow, Russia, a team used 3D printing to create a 400 square foot house in less than a day, just to point out one instance of the production speed.
In addition to this, 3D printing is also enabling the development of new architectural designs and visions that before were never possible. The design innovations are seemingly limitless. In Holland, there will soon be a small neighborhood consisting solely of 3D printed homes.
3. Food3D printing is even breaking design barriers in the culinary arts. Using a plastic 3D printer, users can actually print chocolate based off a digital design from 3D software. Companies have even 3D printed edible foods using ice cream, cookie dough, marzipan and hamburgers.
4. Firearms & MilitaryA very controversial topic has been the ability to 3D print fully functional firearms. Defense Distributed’s “Liberator” has been subject of hot discussion as it is a working plastic gun, created using 3D printing technology. Many believe this to be an extremely dangerous ability as there is the potential for any person with a 3D printer and the design blueprints can produce their own guns.
3D printed flip-top valve on the T-45 Goshawk breathing mask. Photo by Emanuel Cavallaro via NAVAIR.
In a more positive light, branches of the U.S. Military have benefited greatly from this ability. Already we have seen many instances of how 3D printing can aide soldiers in the battlefield and potentially save lives:
- U.S. Marine Corps Turns to 3D Printing
- U.S. Army Explores 3D Printing Stealthy Squid Drones
- U.S. Navy Will Depend On 1,000 3D Printed Parts by the End of 2018
- Marine Corps Seeks to 3D Print Drones, Save Thousands
- 3D Printed F-35 Part Saves U.S. Marines $70,000
- Department of Defense Unveils 3D Printed Drones Deployable from Fighter Jets
- EDA to Assess Usage of 3D Printing in Military Operations
NeoMetrix Firearm Case Studies:
- 3D Scanning and Reverse Engineering a Handgun Grip
- 3D Scanning & Reverse Engineering a Pistol Grip
- Development of a Magazine-fed Shotgun
- Reverse Engineering a Gun Component
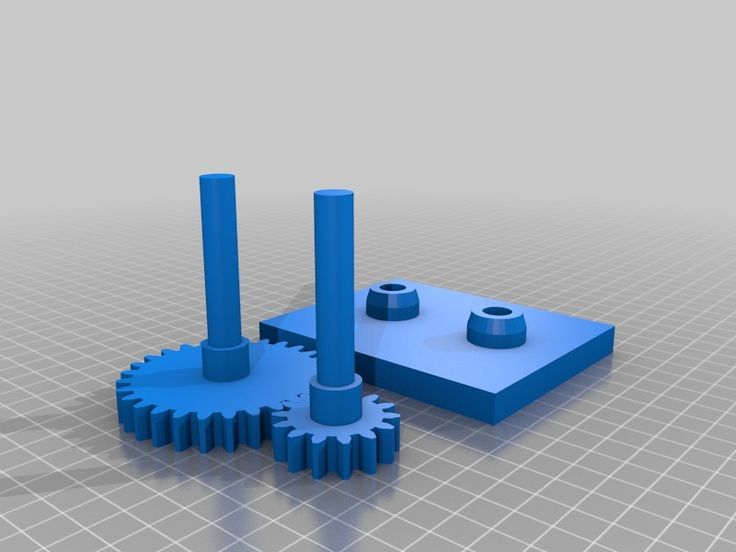
3D printing has become an extremely disruptive force in the manufacturing world, and many refer to it as the manufacturing solution of the future. The automotive and aeronautical industries, to name a couple, have experienced the benefits of 3D printing technologies first hand, and are beginning to integrate it into their production processes. The ability to 3D print both replacement parts and functional, new parts saves them significant, time and money.
- Choose 3D Laser Scanners for Manufacturing Quality Control
- Disruptive 3D Printing Forces Companies to Reconsider Manufacturing
- 3D Printing Yields Huge Savings in Tooling Costs for GM
- 3D Printing Growth Surpasses Traditional Manufacturing
- 3D Printing: Moving from Prototyping to Production
- 3D Printing: The Benefits of a Growing Technology
Additive manufacturing technologies even have impact in music. Already, we have seen working violins, flutes, banjos and more produced using 3D printing. At Sweden’s Lund University, the first ever live concert featuring all 3D printed instruments has taken place, and the show was a smashing success. In addition to complete instruments, 3D printing can also be used to create accessories such as custom mouthpieces.
Perhaps the most intriguing thing about 3D printing is that users can basically create anything that they can design in 3D software. Some examples of how NeoMetrix has enabled out customers to bring their designs to reality are:
- 3D Modeling and Printing Game Characters for Superhero 2044
- Reverse Engineering & 3D Printing Commemorative SunRail Bridge
- Reverse Engineering & 3D Printing “Spirit of America” Awards for Inspired Bronze
- 3D Scanning, Reverse Engineering & 3D Printing American Flag Pins
20 Use Cases for 3D Printing
3D printing has progressed so rapidly in recent years that we will soon stop talking about what can be created using additive manufacturing. It will be easier to mention what cannot be done. Yes, this list will continue to grow rapidly. But for now, let's take a look at some examples showing the wide range of 3D printing possibilities. We warn you in advance: the list is far from complete.
Fruit
A gift for impatient parents
Young parents often experience an irresistible desire to acquire all sorts of items, one way or another related to their child, even if not yet born. The Japanese company Fasotec offers future parents models of unborn babies made from images of real fetuses obtained using magnetic resonance imaging. The finished model consists of two materials - a fetal figurine made of white photopolymer, and a transparent material that imitates the shape of the mother's womb. At around $1,275, the fun isn't cheap, but Fasotec already has some competition. So, 3D Babies offers a similar service for only $200, although the size of the finished model is much smaller, and the quality is not quite on the same level. nine0003
Although the desire to get such a model may seem a bit strange, there is a perfectly logical explanation. As it turns out, the idea was originally aimed at giving blind parents the opportunity to "look" at the ultrasound of the unborn child.
Weapons
Functional 3D printed receiver from AR-15 without any numbers
The possibility of 3D printing of weapons has seriously alarmed law enforcement agencies around the world. After all, even simple FDM printers allow you to create all-plastic guns. Although such a weapon is primitive, even a disposable pistol with a single cartridge in the hands of a criminal can cost someone a life, and it is impossible to trace such a weapon. However, there are also people who believe that 3D printing of weapons should be allowed. Thus, the US Constitution gives citizens the right to freely carry weapons, although certain restrictions still apply. The non-profit organization Defense Distributed, which released the Liberator plastic pistol into the public domain, went further by unveiling the design of the lower receiver of the AR-15 carbine. AR-15 is actually a civilian counterpart, even a prototype of the M-16 automatic rifle, which is in service with several countries of the world. The lower part of the receiver bears the registration number - this is the only part of the rifle that cannot be purchased as a spare. Thus, the printing of this part can bypass the need to register weapons. Some countries have already banned the 3D printing of weapons, although it is not entirely clear how to apply this ban in practice. nine0003
Clothes
One of Snezhana Gross' designs
Some consumables for 3D printing, especially soft photopolymers, are quite suitable for making clothes and even underwear. The bra in the illustration was laser sintered from nylon. This design from Continuum Fashion aims to showcase the possibilities that 3D printing opens up for couturiers. However, don't think this is an experimental model: the company offers finished products for sale on the Shapeways website. nine0003
Russian designers did not bypass the new technology either: Snezhana Gross demonstrated casual wear designs integrating functional 3D printed components.
Art
Easy to print. Take a picture - as lucky
Would you like a replica of the Venus de Milo? No problem, just choose the material and printing method. True, marble is not yet on the menu, but sandstone imitators are already available. Gypsum was one of the first materials for 3D printing. A three-dimensional image of the original can be obtained using a regular photo and then converted to 3D. In addition, more and more 3D scanners have recently appeared on the market, including portable hand-held options that can capture images of large objects. It remains a mere trifle - to agree on a stereo photo session with the security of the Louvre. nine0003
Although, if you are too lazy to make digital models yourself, you can always download them.
Products
What's for breakfast?
Although giant hot dogs are still far away, 3D printers have already learned how to print minced meat. An example of this is the Foodini culinary printer, a simple and practical device using syringe extrusion. Moreover, printing is possible not only with minced meat, but also with any pasty product - dough, cheese, tomato puree. The only thing that Foodini is not yet capable of is heat treatment. It is to be expected that soon there will be devices that combine 3D printing with refrigeration units and, say, microwave ovens. Then sci-fi tales of "replicators" can come true. One press of a button, and the device will lay out the desired pizza and bake it to the delight of the user. Just one question: do you like thin dough or fluffy? nine0003
Characters
Parts of models used to animate ParaNorman's protagonist
Whether it's a miniature version of a giant robot from a favorite manga, a creepy alien creature from Alien, or a Keanu Reeves action figure (as in a black cape and sunglasses, and with a beard and a sandwich sitting on a bench), 3D printing allows you to create replicas of game and movie characters for the delight of fans. And the fact that such souvenirs can be printed even on household 3D printers opens up great opportunities for those who like to collect such models - after all, not all of them are available for sale. Do you want a model of a rare aircraft? Print it. nine0003
And what is most interesting, this application has already had the opposite effect. ParaNorman cartoon characters were still printed. Like the new RoboCop suit. True, inside it was still stuffing from a person. But why stop at simple visualization?
Home Robots
Early Terminator Prototype
The advent of inexpensive Arduino boards made it possible to design a wide variety of electronic devices at home. Here are your own 3D printed robots. You printed the case, inserted the servos and the board, and you have a new au pair. But what about people who do not understand programming or elementary soldering? Scientists from the Massachusetts Institute of Technology are developing a project aimed at automating the design and construction of domestic robots. Ideally, the user will only have to set the necessary functions for the future device, after which the system will compile the required design and send it to print. A few hours later, it will be possible to pick up a ready-made device - a robot-spider for wiping chandeliers or a machine for turning pancakes. nine0003
Aviation
3D printed part used in Chinese fifth generation fighter aircraft prototypes
The toy airplanes we have already mentioned. What about real ones? There is also a place for additive manufacturing in the aircraft industry, although here one cannot do without expensive industrial plants capable of creating high-quality parts, including all-metal ones. Leading aircraft manufacturers, including Boeing and Lockheed Martin, are already testing laser sintering and melting technologies for the production of ventilation systems, structural components and even jet engine parts. Chinese engineers, on the other hand, set to work on a real scale, creating installations for the additive production of parts weighing up to 300 tons. nine0003
Space
Dragon v2 is Space's latest creation
The space industry is not far behind the aviation industry in its interest in 3D printing. NASA has successfully tested titanium rocket engine nozzles, and a few weeks ago, Elon Musk, the head of the private space company SpaceX, held a presentation of the new Dragon v2 orbiter, which also uses engines with 3D printed parts.
Bioprinting
Biopens can help treat fractures
Vessels, tissues, whole organs - several companies are simultaneously developing the production of organic imitators that are completely similar to natural tissues. Although transplantation of 3D printed organs is still far away, work in this direction is underway. In parallel with the production of organic tissues from scratch, methods are also being developed to restore damaged tissues, such as cartilage or bone. Devices called "biopens" are able to apply living cells to damaged areas, promoting their healing. nine0003
Prostheses
Titanium orthopedic prostheses with a porous structure for improved osseointegration
What if the tissues cannot be restored? 3D printing can help with prosthetics. Thus, the Swedish company Arcam creates installations for electron-beam melting, which make it possible to create virtually monolithic metal products, including titanium. Titanium orthopedic prostheses have become one of the most sought-after products created on the devices of this company - according to company statistics, their number exceeds thirty thousand copies. nine0003
Not only that, 3D printed limbs can compete with high-tech designs with one difference - their cost cannot be compared. How many people can afford a tens of thousands of dollars of prosthetic hands? How about a $50 fully functional prosthesis? And it's possible.
An even more common application of additive manufacturing is in dental prosthetics. If you have recently had a crown or bridge placed, it is possible that they were cast from models created with a stereolithography printer that prints with photopolymer resins. nine0003
Musical instruments
3D printed musical instruments
Guitars? Flutes? Drums? Easy. Broke your oboe - print a new one. Of course, professional musicians can argue: plastic guitar? Not seriously. But who said that all tools have to be made of plastic? The same neck can be printed from wood resin, similar in density to natural wood. You can even print a composite carbon fiber core. And as far as simply decorating your favorite harpsichord, 3D printing can work wonders here. It would be fantasy! nine0003
Shoes
Luc Fusaro's stylish trainers
Eight-time world sprint champion Usain Bolt is famous for his love of gold. This includes not only medals, but also cars and even shoes. During his contract with renowned manufacturer Puma, Bolt wore signature gold-plated sneakers. And more recently, engineer and designer Luke Fusaro has taken on the development of sports shoes that Usain would like. Its distinctive feature is its golden color. Oh yes - and it's also designed for 3D printing. The use of additive manufacturing has one important bonus, namely the ability to produce shoes that are precisely tailored to the size and contours of the athlete's foot. Such shoes are produced by laser sintering, although this technology has already had a competitor. nine0003
Drugs
3D printing can facilitate the production of mixed drugs and help with drug testing on living tissues often in combination with tissue engineering. Thus, the Organovo company directs its efforts to create artificial human liver tissues to test new drugs for toxicity without risk to human health. But the drugs themselves can also be printed by binding the drugs with a gel material. As a result, we get ordinary-looking pills, but with a complex content of drugs, tailored to a particular patient. nine0003 Cars
Doc Brown is introduced to 3D printing. That's about the reaction you'd expect.
Most automotive components can be printed, but it's not economically viable when it comes to mass production. But for prototyping new cars, 3D printing is great. As, however, for the production of unique machines or components. For example, you can print replacement parts for low-volume, discontinued models. Where else can you find parts for, say, the DeLorean that inspired the Back to the Future time machine? The only small company still making parts for this car is in Texas. Shipping parts can cost more than the machine itself, quite inexpensive. nine0003
Customization
Maximum glamor at minimum cost
Why not take a finished product and add decorative elements? Turn your bike into a work of art for everyone to envy. Gold-plated openwork fasteners on a black chassis will make passers-by look back. But it is not necessary to stop at the decorative aspect! Maybe you are not satisfied with the seat? Why not print a new one? Or add more comfortable handles? Klaxon style 1910s?
Furniture
One of Joris Laarman's clever designs
Toy furniture? No, not only. The advent of composite materials for FDM printing makes it possible to print "wooden" furniture, almost indistinguishable from the real thing. Actually, the material Laywoo-D3 could not do without real wood in the form of micro-sawdust. This stuff even smells like wood! Finished products are easily machined and varnished.
Or do you prefer metal furniture? Dutch designer Joris Laarman has created his own machine for metal 3D printing, without the use of expensive powders, vacuum chambers and lasers. The device draws with metal in the air, allowing you to create elegant interlaced designs. nine0003
Jewelry
Beautiful and functional
A clear demonstration of the precision of 3D printing is its application in jewelry. It should be said right away that not all technologies are suitable for this task. Widespread FDM printers are attractive due to their cost-effectiveness, but in terms of print quality they do not reach the standards of jewelry production. The most popular choice is laser (SLA) and projector (DLP) stereolithography - installations using these technologies allow printing photopolymer parts of extraordinary accuracy. Such products are used as master models when creating jewelry casting molds, greatly simplifying the production process. nine0003
But there is also an option for direct additive manufacturing of jewelry: laser sintering and melting technologies make it possible to create finished products from metal powder, including precious metal powders. True, the cost of such installations and materials is often too high for widespread use even by jewelers.
Construction
3D printing of buildings will help solve housing problems experimenting with the construction of concrete "boxes". True, these attempts are still quite primitive, because a real house will also need infrastructure - drainage, wiring ... Andrey Rudenko's attempts to build a full-fledged house are very promising. Andrey designed his own printer capable of printing with commercially available cement mixtures. Moreover, he already had competitors. Thus, the BetAbram company plans to put on sale printers for printing buildings up to 16x9m. The issue price is about $44,000 for the largest of the three models. True, "more" is not necessarily "better". Spanish developers are trying to go in the direction of miniaturization of 3D construction printers, creating robots that can use already built building elements as a working support.
Which method will be the most practical, time will tell. But if any of them succeeds, the construction industry can make a qualitative breakthrough, expressed in increased savings, safety and speed of building construction. nine0003
3D printers
What else can I print with a 3D printer? Another 3D printer! Even if not entirely yet: the necessary electronic and electromechanical components are not yet subject to printing, but this is only a matter of time. Almost all materials used or close analogues have already been tested by various additive manufacturing methods. It remains only to wait for the appearance of machines capable of using the full range of consumables. Then the RepRap project, which gave impetus to the development of compact self-replicating 3D printers, will come to a logical conclusion. nine0003
Article prepared for 3DToday.ru
Examples of positive and negative applications of a 3D printer
Every year 3D printing becomes more and more popular. The 3D printer, as a tool for turning a digital model into a physical object, is gaining popularity, outperforming other production methods in many ways due to its affordability.
But do not forget that a 3D printer is just a tool. A lot depends on how this tool will be used. nine0003
Available 3D printing technologies
All 3D technologies can be conditionally divided into 4 types.
Layer by layer welding with molten material.
The principle of operation is similar to the familiar glue gun. The print media is melted to a semi-liquid state in the print head and applied with a nozzle to the print surface where it solidifies. This is how the finished 3D model “grows” layer by layer on the printing table. Not only thermoplastics can be used as consumables, but, for example, chocolate, icing, concrete, etc. nine0003
This is the most common type of printer. Inexpensive FDM printers are often used as home assistants. This is facilitated by an inexpensive price and a variety of consumables.
Selective curing of resin (photopolymer printers).
The material used is a photopolymer resin that hardens under the influence of UV radiation. As a source of UV radiation, a thin laser beam, a DLP projector or an LCD screen with a UV matrix, or any other design can be used. For example, some industrial 3D printers apply a photopolymer using thin nozzles and immediately illuminate it with a UV lamp. nine0003
Previously, these printers were quite expensive. Today, with advances in technology, photopolymer 3D printing has become affordable and photoresin printers have become popular as home hobby printers.
Selective bonding of powdered material.
On the print head of the printer there are several nozzles through which a binder is supplied, which is selectively applied to the powdered material. Various materials can be used as a material: for example, gypsum or metal powders. But gypsum is most often used. nine0003
Since dye can be added to the "glue" during printing, such printers are usually used for the production of color demonstration models or souvenirs.
Laser sintering of powdered materials.
The youngest technology, but with great potential for use in large-scale production. With the help of a laser or a heated print head, selective sintering of the metal powder occurs in an environment filled with an inert gas. nine0003
These are already serious industrial printers that are used for the production of functional metal assemblies and parts. Currently, such 3D printers are actively used in the aerospace industry.
Unethical use
3D piracy
Where there is duplication of objects, there are always disputes about copyright and piracy.
The production of any product is a long and painstaking work, and often more than one person. Before you get a finished decorative product, for example, a figurine, you need to think through everything to the smallest detail. Usually, before modeling, the artist draws a lot of sketches, the details of clothing and accessories are thought out. Only after that the 3D modeler gets to work and begins painstakingly recreating the 3D model. nine0003
Functional models are often redesigned by engineers after the prototype has been made. There can be a very long way between the initial idea and a stable working mechanism. And it’s very disappointing when such work is simply copied and posted in the public domain.
LEGO
It was one of the first mass manifestations of "3D piracy". At that time, 3D printing was only gaining popularity, and many users, having printed a dozen figurines, were looking for a useful application for a 3D printer. Given the low plastic consumption, the printed LEGO blocks were very inexpensive. nine0003
3D printed LEGO bricks
Despite the far from ideal surface, many were satisfied with such a copy. Some have argued that the accuracy of a home FDM printer is not enough for the bricks to fit well with the original LEGO, but for most users everything fit perfectly.
At the moment, LEGO is actively removing models that copy the original sizes of the famous bricks and men from the network. On popular sites, only custom elements of LEGO-men and LECO are left that are not the original size. nine0239
Custom heads for Lego people
Games Workshop
Games Workshop, which produce the most expensive table soldiers in the world, sued Thomas Valenti (USA) back in 2012. Thomas has modeled, printed and made publicly available several miniatures based on the Warhammer universe. The court sided with Games Workshop and the models had to be removed. nine0003
3D Printed Chaplain
3D model of a chaplain from Warhammer 40k
Games Workshop went one step further by banning fans from creating art and other work based on the original settings and characters. As a boycott, users of the Warhammer 40,000 section on Reddit are proposing to abandon the company's products as much as possible - print game figures on 3D printers, use paints from other companies, or switch to other universes. nine0003
Hollywood
The production of modern films is not a cheap pleasure, and film companies try to recoup their costs not only by showing them in cinemas, but, for example, by producing souvenirs.
DreamWorks has an entire consumer goods division that helps recoup the cost of a movie if it fails at the box office. Film companies recognize that fan-made productions often surpass the official "souvenir" in accuracy and detail. nine0003
DC Universe Batman fan model
Many film companies are closely following the development of 3D printed merchandise, but do not yet know how to respond. For example, Paramount Pictures, Marvel Studios and Warner Bros. They themselves began to upload models for 3D printing to the network, before the release of new films.
Weapon Seal
Weapon Seal
24-year-old law student Cody Wilson was the first to make a gun on a 3D printer. Cody designed and 3D printed a combat pistol on his own. After 8 years, the idea of making firearms using 3D printing has not only not died out, but flared up with a bright fire. nine0003
It started in Texas in 2012. It was there that the company Defense Distributed was registered, the ideology of which was the development of models of firearms that anyone could make on a home 3D printer.
Guns
Liberator
The first “swallow” was the Liberator - a compact plastic pistol printed on a 3D printer from ABS plastic. The only thing that could not be made on a 3D printer was the striker, which was successfully replaced by an ordinary nail. The first printed pistol was made on a Stratasys Dimension SST 3D printer. nine0003
Liberator - the name is borrowed from a cheap pistol that was developed in 1942 in the USA.
The Liberator fired a fairly weak .380 ACP round and could only last a dozen rounds at most.
Failed Liberator
Zig Zag
In the spring of 2014, a video appeared on the Internet with a man shooting from a plastic revolver with a huge drum. The video greatly stirred up all of Japan. nine0003
Zig Zag
Unknown was Yoshitomo Imura (Yoshitomo Imura) - 28-year-old employee of the Shonan Institute of Technology. Despite Imuru's claim that he fired blanks on the tape, he was arrested and sentenced to 2 years in prison.
The Zig Zag design was a reimagining of revolvers popular in the 19th century, which used a rotating .38 caliber barrel block mounted on a pistol grip. nine0003
Washbear
In 2015, mechanical engineering student James Patrick posted a video online showing a 3D printed PM522 Washbear in operation.
PM522 Washbear
The PM522 visually resembled a children's pistol from a science fiction movie, but at the same time the pistol had a strong and rigid frame. Washbear is also safer than its predecessors. At rest, the firing mechanism was not in line with the primer, so the PM522 was protected from accidental firing, for example, when dropped. The only metal part was the nail that replaced the striker. nine0003
Rifle
Grizzly
Canadian with the nickname CanadianGunNut, ThreeD Ukulele or simply Matthew, inspired by the Liberator project, designed and posted his project - Grizzly. Grizzly is an ABS+ plastic rifle. It took the Canadian 3 days to design the rifle and another 27 hours to manufacture it using a Stratasys Dimension 1200es industrial 3D printer.
Grizzly 9 Rifle0008
The first version of the Grizzly had a smooth and straight .22 barrel. But this turned out to be not a very good decision, and the barrel cracked after the first shot. Subsequently, Matthew replaced the barrel with a tapered barrel with rifling inside.
Plastic “cutting” could not affect the ballistics of the bullet in any way, but added strength to the barrel.
Shotgun
Liberator 12k
The Liberator 12k is a 12-round shotgun made by a well-known, in narrow circles, enthusiast in the world of 3D printing - Jeff Rodriguez. nine0003
Liberator 12k
Rodriguez managed to create a simple and at the same time reliable design, "mixing" a pistol and a pump-action shotgun in the design of the Liberator 12k. A huge plus for manufacturing and reliability was the absence of small parts in the shotgun mechanism.
Since the plastic was not strong enough, Rodriguez reinforced the design of the Liberator 12k with metal pins and added metal tubes inside the barrel and drum. The metal parts were purchased from a regular hardware store, so anyone could easily make a Liberator 12k with their home 3D printer. nine0003
Semi-automatic weapons
Shuty-MP1
The first sign was the Shuty-MP1, a semi-automatic pistol made by an amateur gunsmith with the nickname Derwood, in April 2017.
Shuty-MP1
Shuty AP-9
The Shuty AP-9 still uses a pistol barrel, but the trigger and return spring are taken from the civilian version of the M16. This improved the reliability of the rifle. nine0003
Ethical use
Despite the negative examples of application, 3D printing is actively used in many areas, helping to save time and create products that cannot be produced by other methods.
Medicine
Implants
Metal-printing 3D printers are actively used in medicine for the manufacture of titanium implants. For example, a patient needs to have a hip joint implant made. According to the results of CT, the necessary area of bone tissue replacement is agreed with the doctors and a prosthesis model is created that is ideal for this patient. After all approvals, the finished model is sent for printing. nine0003
3D model of implant
The main areas of 3D printing of implants in medicine are maxillofacial surgery, traumatology, orthopedics, oncology and veterinary medicine. A big advantage over classical methods of manufacturing implants is the ability to create a cellular or porous structure. This allows for better integration of the prosthesis into the bone tissue.
nine0007 Samples of printed implants and pins
Dentures
The manufacture of even a relatively simple traction prosthesis is a rather laborious and lengthy process. 3D printing has reduced costs and accelerated the production of prostheses. In addition, it became possible to customize the prosthesis.
Customized child prostheses
Some enthusiasts are modeling and posting models and detailed instructions for assembling traction prosthetic hands and fingers in the public domain so that any user can print and make a prosthesis at home. nine0003
Simple traction prosthetic hand model
Production
Building custom drones
Aerialtronics is a small Dutch company that specializes in building unique, customized drones. Aerialtronics manufactures and develops unique drones, the characteristics of which can vary depending on the needs of the customer. nine0003
Initially, a basic concept model was designed, which consists of a platform and a set of elements that can be changed at the request of the customer. Changes can affect almost any part of the drone. The customer can choose the number of motors and their power, payload, flight time, supported software and much more.
Aerialtronics base model
But any, even minor changes in the characteristics and design of the drone required the manufacture of new elements and design changes. Classical manufacturing methods turned out to be quite laborious and long. To save time and money, a Stratasys uPrint SE Plus 3D printer was purchased. nine0003
Drone Assembly
Thanks to 3D printing, it was possible not only to speed up production, but also to devote more time to improving individual components, because the finished model is ready the next morning. Rapid manufacturing allows you to print a part, test it, make the necessary changes to the 3D model and make a new sample. Aerialtronics engineers manage to manufacture and test 8-10 variants of a part in a few days in order to achieve maximum quality. nine0003
Prototyping
Gas turbine prototyping.
Prototyping by traditional methods is often time consuming and expensive. Because of this, the price of an error in calculations and 3D modeling can be very expensive.
For example, the production of turbine engine parts is usually based on careful preparatory calculations, but even this does not always prevent errors in the production of a test prototype. After all, even the most modern software methods cannot replace physical tests. But due to the high cost (over $20,000), it becomes impossible to produce multiple prototypes for testing. nine0003
Turbine Technologies (Wisconsin, USA) and its subsidiary Kutrieb Research have found a way out - 3D printing. Thanks to the 3D Systems ProJet 3D printer, it was possible to reduce the cost of prototyping by about 10 times to $2,000.
3D model and printed part of turbine
A turbine model is printed on a wax 3D printer, tested and then cast from metal. In addition to the cost, it was possible to significantly speed up production. After all, the production of traditional stencils with filling in molds took up to 5 weeks, and the 3D printed model is ready by the morning. nine0003
Totals
Despite the unethical side of 3D printing, there are still more positive use cases. 3D printers have become indispensable assistants in various industries - from home hobbies to serious industries. With the help of 3D printers, unique products are made that could not be obtained using other machines.
Popularization of 3D printers is a matter of time. But do not forget that 3D printing is just a tool, just like a drill or a hammer. It depends only on the user how it will be used.