3D printing in jewellery industry
Guide to Jewelry 3D Printing
Two techniques have historically defined jewelry making: handcrafting and lost-wax casting. Both techniques require significant technical expertise, are highly time-intensive, and mistakes in the process can prove expensive.
But today, digital design and 3D printing are primed to disrupt these age-old practices in a major way. Supplementing traditional processes with digital techniques such as jewelry 3D printing brings new possibilities in design and production to jewelers, as well as exciting new customization options for customers.
White Paper
In this white paper, learn how to cast fine jewelry pieces from 3D printed patterns and how direct investment casting, or lost wax casting, works as a moldmaking technique.
Download the White Paper
3D printed jewelry production augments the principles of investment casting, or lost wax casting with the advantages of a digital design and manufacturing process.
With traditional lost-wax casting, jewelry designers hand-carve the original pattern in wax, place the wax pattern in a mold to be burned out, and then pour precious metals like gold or silver into the mold cavity to create the cast piece. To achieve its final appearance, designers polish and finish the cast piece to shine.
With the digital workflow, jewelers use CAD software tools for jewelry design to create the models digitally and a high-resolution 3D printer to produce the 3D printed jewelry patterns that can then be cast in a mold. After burnout of the positive pattern, the process follows the same path as traditional investment casting. Thanks to the digital techniques, the need for time-intensive manual labor is reduced and the design itself is easy to preserve, modify, and recreate when needed.
Sample part
Curious to see our materials firsthand? Click here and we'll ship you a free jewelry sample part printed on our 3D printer.
Request a Free Sample Part
Until now, the complexity of the design and production process made customized jewelry an expensive privilege. With digital tools, however, jewelers have already started offering personalized creations as part of their basic service or as a value add. If you go to a jeweler today and ask for an engagement ring, often you'll have the option to customize a unique design.
3D printed jewelry try-on pieces drastically shorten the feedback loop between designer and customer.
Jeweller and customer can discuss the design together, and an hour later, the customer can hold and try on a real, physical model of the ring. In jewelry retail, on-site digital design combined with the speed of 3D printing has drastically shortened the feedback loop between designer and customer.
Moving from design to production is easier and faster, as hand carving a precious one-off is no longer a requirement. The try-on pieces can be tailored based on the customer’s requests, 3D printed again, and then manufactured with lost-wax casting, which translates to a considerable reduction in the cost of making customized 3D printed jewelry.
With 3D printing, jewelry designers are able to produce designs that would be incredibly difficult to hand carve in the traditional manner. Breakthroughs in castable resins are setting new standards for the quality available through an affordable desktop 3D printer.
3D printing jewelry patterns in Formlabs’ Castable Wax 40 Resin combines the smooth surface finish characteristic of stereolithography (SLA) 3D printing technology with precise print settings. Thanks to a precisely controlled laser, extraordinary design details—delicate filigrees, raised text, and detailed pavé stone settings—can be captured with amazing sharpness.
Stereolithography 3D printing can reproduce complex features that’d be difficult to hand carve.
With these long-established design restrictions now removed, we're seeing entirely new genres of design emerging from jewelers who digital capabilities in the US as well as in South Asia and Asia Pacific, and the Middle East.
Webinar
In this webinar, Patrick Diggins, our Jewelry Vertical Manager, will teach you how Castable Wax 40 can help you push the boundaries of design and production efficiency.
Watch the Webinar
Digital tools are not only making jewelry easier to customize, but also simpler to mass-produce designs.
Vulcanized rubber molds are used to produce wax patterns in quantity for lost-wax casting, but the “master” pattern is traditionally made from an investment cast, hand-carved wax pattern.
3D printers can produce master models that are used to form room temperature vulcanization (RTV) molds and even durable high temperature vulcanized rubber molds.
Directly 3D printed jewelry patterns can be used for room temperature vulcanization (RTV) and vulcanization of high temp natural rubber.
“With the quality that you can get with SLA 3D printing for printing these jewelry pieces, you can jump straight from the 3D printed part to a master mold,” said Formlabs' Jewelry Vertical Product Manager Amos Dudley. “The surface finish is already so smooth that it doesn't require very much finishing. You can use that as the rubber mold for creating the final wax parts that go into production. ”
White Paper
3D printing with high-performance materials allows designers and casters to leverage digital technology in their production processes. Read now to learn how 3D printing can be used in the production of small metal parts.
Download the White Paper
When new technology is finally made available to the public, it usually comes with a high price tag and a complicated interface, restricting it to users with deep pockets and technical savvy. Previous generations of jewelry 3D printers required both significant maintenance and a skilled operator in addition to thousands of dollars of investment that limited them to the largest jewelry manufacturers and casting houses. Nevertheless, Dudley notes, “3D printing has become much more affordable, offering unique opportunities to independent jewelry makers.”
The lower cost and higher-quality jewelry 3D printing technology have made the digital workflow a viable method of manufacturing. “In the coming years, we're going to see a growing trend in that segment, with smaller jewelers adopting these technologies and becoming less centralized,” Dudley said.
This shift to increasingly competitive independent jewelers will continue as the industry becomes more familiar with castable resin 3D printing. Historically jewelry 3D printing has been dominated by complex and expensive wax 3D printers. With affordable desktop jewelry 3D printers like the Form 3+, the technology is becoming available to more jewelers, especially smaller independent ones.
Interactive
Try our interactive ROI tool to see how much time and cost you can save when 3D printing on Formlabs 3D printers.
Calculate Your Savings
Owing to the formerly high cost of large-scale jewelry 3D printers and the perceived barrier-to-entry of digital jewelry design, 3D printed jewelry, despite its potential, currently represents a relatively small fraction of the market.
Nevertheless, with increasingly easy to use and accessible jewelry 3D printers, the digital workflows in the jewelry market are poised for growth. Desktop stereolithography 3D printers are an important component in this expansion.
High-resolution desktop 3D printers, like the Formlabs Form 3+, have made jewelry 3D printing accessible for independent designers as well as large casting houses.
“SLA resins have a reputation for being cheaper, but also less functional than wax. At Formlabs, we're looking to break that impression with products that are more foolproof and eliminate some of the extra work that’s still present in the jeweler's workflow,” Dudley said.
New, easy-to-use materials like Castable Wax 40 Resin are easing the learning curve, leading to greater adoption of the workflow and the subsequent expansion of the market.
3D printed jewelry is not just a matter of technology. The newer cohorts of jewelry designers entering the industry have started education with digital methods, including training on 3D printers, as opposed to the traditional ones.
“They're going to be looking for the printer that really meets their needs,” Dudley said. “I think then we'll start to see more adoption as they take over from the currently embedded user base.”
3D printing in jewelry has a bright horizon. With the wider industry adoption of workflow techniques, the arrival of new generations of designers skilled in them, and the creation of new, more foolproof materials and hardware, we're seeing the stage set for a major positive disruption.
Request a Jewelry Sample Part
Jewelry 3D printing applications | Hubs
This article discusses how 3D printing is being used to produce high detail, custom jewelry through investment casting and direct metal printing.
3D Printing techniques
3D printing is typically used to create jewelry via 2 methods; investment casting and direct printing.
Investment casting
One of the most popular methods of producing jewelry via 3D printing is the investment casting process. Investment casting produces parts through an 8 step process:
There are several requirements for a 3D printing technology to successfully produce jewelry molds for investment casting. These are:
- The technology must be capable of producing parts with a very high level of detail and minute, intricate features.
- The material used to print the pattern must be able to be completely eliminated at the burnout/melt stage. Leftover remnants of the original pattern material have a detrimental effect on the quality of the final cast part. Because of this there are strict burnout procedures for most 3D printed castable resins.
(image courtesy of Formlabs)
Based on these requirements the two most suitable technologies and their associated materials for producing 3D printed patterns for investment casting are summarised below:
SLA/DLP
SLA and DLP are both vat photopolymerization techniques that photocure a UV sensitive resin one layer at a time to produce a solid part. SLA and DLP are capable of producing smooth, high detail parts from castable resins that have a very low remaining ash percentage after burnout. Both SLA and DLP require support to accurately print parts. Support material generally has a detrimental impact on the surface of a print it is in contact with and must be removed once the print has been completed. Some of the more common SLA/DLP investment casting materials are presented in the table below:
Technology | Material producer | Material name |
---|---|---|
SLA | Formlabs | Castable resin |
SLA | DWS | DWS DC Series resins |
SLA | 3D Systems | VisiJet SL Jewel |
DLP | Envisiontec | PIC 100 C |
DLP | B9 Creator | B9R-4-Yellow Resin |
DLP | MoonRay | Castable resin |
DOD
Drop-on-demand printing is a material jetting technique that uses 2 print jets; one to deposit a wax-like material over a build surface and another to deposit dissolvable support. The wax is deposited one layer at a time and a solid part is built up. DOD printers print at very high level of detail and offer several advantages over SLA/DLP printers including:
- - Dissolvable support resulting in less post-processing and a better pattern surface finish. - Patterns are printed with a wax-like material meaning the pattern is melted rather than burnt out eliminating the issues that arise with resin ash.
Technology | Material producer | Material name |
---|---|---|
DOD | Solidscape | Solidscape Model and Support |
(image courtesy of Solidscape)
Direct printing
A much less popular method of producing jewelry via 3D printing is directly printing parts from metal powder. Parts are able to be printed via gold, silver or platinum alloys and then require a significant amount of post-processed to an appropriate finish. Direct printing of jewelry is generally more expensive than investment casting, even for one-off pieces, and requires a very high level of precious powder management.
DMLS/SLM
Direct metal laser sintering (DMLS) or selective laser melting (SLM) are powder bed fusion techniques used for the production of metal parts. To accurately produce parts DMLS/SLM require a significant amount of support to be included on the part during printing. High temperatures result in high levels of stress meaning parts are often susceptible to warping or deformation. This leads to significant post-processing being needed to remove the support and finish the surface where it was attached.
Technology | Material producer | Material name |
---|---|---|
DMLS | Cookson Precious Metals | ALNP000 18k 3N Yellow Gold Powder |
(image courtesy of Romanoff West)
Ready to transform your CAD file into a custom part? Upload your designs for a free, instant quote.
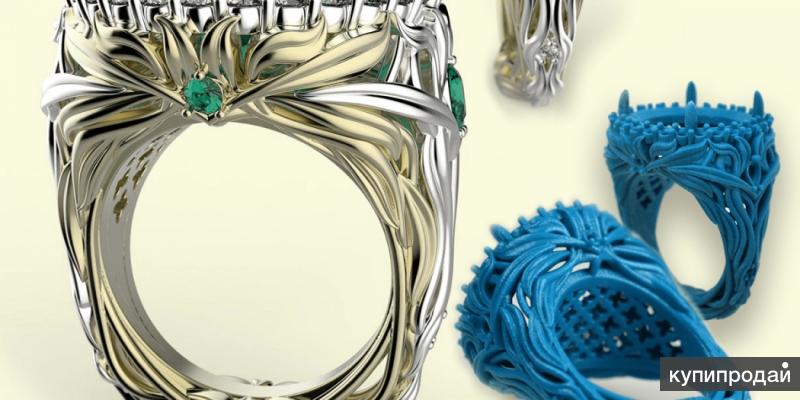
Application of 3D technologies in the jewelry industry
Jewelry industry
Author: Nikita Kudryashov
Author: Nikita Kudryashov
3D printing and 3D scanning in the jewelry industry | Benefits of additive manufacturing | Implementation of 3D technologies in enterprises
The uniqueness of jewelry is that it belongs both to the field of art and to mass production. The profession of a jeweler implies not only original creative thinking, but also high skill and scrupulousness in work. And if we talk about the specifics of this industry, then the first place here is to ensure the highest accuracy of products. The jewelry industry has a difficult task - to embody the perfect creation of the master in serial jewelry.
3D printing in jewelry is about precision, productivity and simplicity
“Jewelry precision” is a concept that perfectly describes one of the advantages of additive technologies: 3D modeling and 3D printing allow you to quickly create products of the most complex shape, including very small ones that best match the original model. It is logical that with the advent and development of 3D technologies, jewelry enterprises began to show keen interest in new opportunities. In recent years, additive methods have proven their effectiveness in various fields - in the aerospace, oil and gas, shipbuilding, mechanical engineering, metalworking, science and education industries. In the first lines of this list is the jewelry industry.
We talked about the importance of 3D technologies for jewelry making with an expert in 3D technologies, Nikita Kudryashov.
- Can you please tell us how 3D printing is used to create jewelry?
- Today, the jewelry industry uses two main technologies for obtaining master models and finished products - investment casting and burnt models. The first of these is the simplest and most common: wax models are created on a 3D printer using multi-jet modeling technology (MJP) for subsequent production of master models. When casting on burnt models, the product is grown from a liquid photopolymer by laser stereolithography or multi-jet modeling.
3D model of jewelry in Rhinoceros
- What is the technological process?
– A three-dimensional model of a future piece of jewelry is created and worked out in specialized software. The design is developed, as a rule, in the Rhinoceros program, after which the 3D model is loaded into the Materialize Magics software product. This is where error checking and mesh fixing comes in to prepare the models for placement on the printer build platform. The next step is to send these models for 3D printing.
- Is 3D scanning used in the jewelry industry?
– Yes, definitely. 3D scanners (for example, Solutionix D700) are an indispensable solution if reverse engineering is required, that is, if the task is to restore or recreate a certain product, say, a historical one.
- What are the main advantages of additive manufacturing over traditional methods in jewelry?
- First of all, it is the speed of obtaining master models due to the high speed of printing. Now you do not need to manually make each ring separately on milling machines. It takes a lot of time.
Additive methods give us the opportunity to create unique models of future products with a geometry of any complexity. For a jewelry designer, this opens up simply limitless horizons.
The wax melting process itself is very simple, it does not require any super-equipment. In addition, we can print a stencil for casting the final product right away - there is no need to make a master model.
And one more important point: using 3D technologies, we get rid of the costs associated with the loss of precious metals.
- That is, we save both time and labor costs. How long does it take to 3D print?
– Building in the printer takes approximately six hours. After that, the model is cast, then we make minor adjustments, and that's it - the master model is ready.
High-precision 3D printing: master model and finished product, consisting of 1100 settings for stones of the same size
- Jewelry is compact, so you can make a lot of pieces at once?
- That's right, up to thirty different models are placed on the printer platform. Moreover, they are completely different - complex, light, rings, bracelets, and so on ... In this sense, there are no restrictions.
– What can you say about the situation in the industry? How actively are additive technologies being introduced at enterprises?
– In our experience, all jewelers know what 3D printers are and what opportunities they bring, and many are thinking about buying them. No one needs to be told why. Everyone is well aware that additive technologies speed up the process of obtaining the final product at times, that it is easier, that a large number of technologists who will spend long hours making master models and finished products are not needed.
3D printing is now being used by both large and medium-sized enterprises. If you ask how they worked seven years ago, when traditional methods were used, the answer is unequivocal - there were completely different production volumes! This also applies to small companies: even if a designer manually makes one ring a day, he simply prints it on the printer, casts it, and that’s it.
- The benefits of 3D technology are clear. Does it have any downsides?
- The disadvantages include the high cost of equipment and materials, large investments. But, on the other hand, milling jewelry machines are also not cheap.
- Don't such expenses deter jewelers?
- For an individual entrepreneur, this may be a lot of money, but for some large-scale production - a penny. But even in small-scale production, everything speaks in favor of 3D printing: both time and money are saved for the production of products. In addition, there are compact budget solutions.
- To summarize...
– If to formulate everything that has been said about additive methods in the jewelry industry briefly, then I would limit myself to three weighty words: accuracy, productivity, simplicity.
Article published on 06/27/2017, updated on 05/27/2022
How 3D printing will change the jewelry industry « Treasures of St.
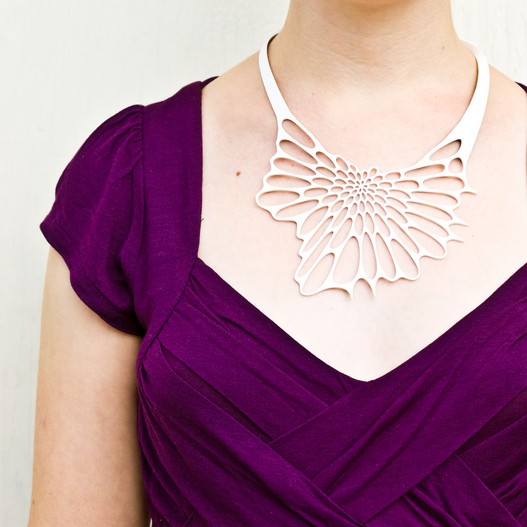
Three-dimensional printing is one of the revolutionary inventions that have become quite widespread in recent years. It can fundamentally change the traditional jewelry industry, and today we will talk about what changes await us in the next five years.
In 1983, American engineer Charles Hull discovered a new printing method to create three-dimensional objects. 3D printers work on the principle of layer-by-layer “growing” of a solid model and form an exact copy of a digital 3D prototype. Unlike a two-dimensional printer that outputs two-dimensional information to a sheet of paper, its three-dimensional counterpart is already capable of outputting information in three dimensions at once, that is, creating three-dimensional physical objects.
3D printing has exploded in the past few years, driven by the mass production of 3D printers at more affordable prices, the development of digital technologies and the expansion of the list of materials used in printing. They say that the third industrial revolution is just around the corner.
Jewelry belongs to the category of products that can be created with 3D printers today. Amazon.com, the number one U.S. online supermarket, already has a section for 3D merchandise, where "printed" jewelry has a whole "shelf" in its own category called "jewellery for those who keep up with fashion."
This is a great opportunity for independent designers looking to tap into a large consumer market. Printing your own designer jewelry is already becoming a fashion trend in the West.
The list of materials for the production of jewelry using 3D printing is also constantly expanding. For example, New York-based Shapeways, a 3D printing hub for designers and developers, added platinum, 18k gold, 14k rose gold, and 14k white gold to its range of metals that can be used for 3D printing. Today, this company offers the widest selection of materials for 3D printing of jewelry.
US President Barack Obama, in his 2013 State of the Union address, said that 3D printing has great potential to revolutionize the manufacturing method by which almost everything is made.
What does all this mean for the traditional jewelry industry?
From the point of view of the end user, this is simplicity, convenience and high speed of receiving your order. For example, you have lost one of your earrings and want to order a replacement for the lost one. Using 3D printing, you can simply purchase a file with a three-dimensional model of your earrings (CAD file) and print the missing pair at home on your own 3D printer or contact one of the printing centers. True, if there are stones in the earrings, you will need the help of a jeweler who will install them in the product.
From a jewelry retailer's point of view, there are also many advantages. First, there is no need to spend money on inventory and its maintenance. It will exist in virtual form, as a catalog of designs and accompanying samples. It will be enough for the seller to stock up on raw materials, materials and computer files to make an order.
High print-on-demand speeds mean that the need for stockpiles of finished goods is reduced, so manufacturers can cut costs for warehouse space, storage, and warehousing personnel.
3D printing will allow manufacturers to significantly reduce the cost of production, in particular by reducing labor costs. In other words, instead of jewelry masters, the main work will be done by ... industrial printers. In small-scale and piece production, this can reduce the cost by 2-3 times.
“With our platform, the cost and labor savings are phenomenal. There is no longer a jeweler with a blowtorch on our bench. We enable consumers to create jewelry in real time,” Forbes quotes Eddie Bakhash, CEO of New York-based jewelry company American Pearl.
American Pearl is one of the pioneers of 3D printing in the jewelry world. The company offers the service of recreating a piece of jewelry from its photograph. First, a 3D computer model of the product is prepared. Then a three-dimensional printer based on it forms an exact copy. The polisher and stone setter complete the process by presenting a sparkling duplicate of the piece to the client. Ideal for restoring lost family values, for example. American Pearl has a patented computer-aided design (CAD) system and a Solidscape T-76 3D printer.
3D printing has the potential to bring production back to countries that today mostly import goods. The main problem of competitiveness, in particular, of American jewelry manufacturers is the high cost of labor in the United States. They cannot compete with cheap foreign production (read: China, Thailand and India) in the cost of production.
3D printing solves this issue simply - the printer does not need to pay a salary, only the purchase price and materials.
In addition, there will be localization of production, it will be concentrated closer to the consumer. Hence, the reduction of costs for cargo transportation and all other logistics of finished products. It is likely that the role of large mass production centers will also gradually decline.
Manufacturers, both small and large, will find it much easier to turn ideas into working models and marketable products. The flexibility of 3D printing-based manufacturing will allow production of test batches without the high cost of a new production process.
Of course, the spread of 3D printing will raise many new questions. What will happen to the jewelry profession? After all, 3D printers will be able to perform many jewelry functions faster and cheaper than a person, while avoiding the mistakes inherent in people.
How will brands protect intellectual property? Xeroxing jewelry from Tiffany, Cartier and other luxury brands from a technological point of view is not difficult based on photographs and promotional items. The answers are yet to be found.
3D printing opens up new possibilities for the jewelry industry. By incorporating it into the process, manufacturers will be able to reduce production costs, increase production efficiency and flexibility, and offer customers a million options for making jewelry truly personal and unique. In the next 5 years, we will see the rise of new names and designers successfully putting 3D printing to the service of their creative talent.