3D printing future of manufacturing
Is 3D printing the future of manufacturing? – Northbridge Insurance
The world of manufacturing is constantly evolving and changing. And 3D printers may be the next big step.
3D printing, or additive manufacturing, is a process that allows for a three-dimensional solid object to be created from a digital file. For years, when the technology was first introduced, it appeared to be more of a novelty than a practical tool, creating one-off trinkets and souvenirs. But now, with lower costs and technological advances, 3D printing is within more people’s reach and has already been used in a number of interesting ways, ranging from medical applications to shoe production.
But like any other relatively new technological advancements, there are both pros and potential drawbacks. Here we examine those consequences, and look at where 3D printing is now and where it might be headed.
The current state of things
The 3D printing market has been steadily growing over the years. The primary market, including 3D printing systems, materials, supplies, and services, has grown at least 30 per cent each year from 2012 to 2014, according to a report published by the Consumer Technology Association (CTA) and the United Parcel Service (UPS).
The report, titled “3D Printing: The Next Revolution in Industrial Manufacturing,” found that two thirds of manufacturers already use 3D printing in some way, and 25 per cent had plans to adopt the technology in the future. Corporations cited prototyping, product development, and innovation as their top reasons for using 3D printing.
The consumer electronics and automotive industries each contribute 20 per cent of the total 3D printing revenue, using the technology primarily during the prototyping phase of production, according to the report published by the CTA and UPS. But some are expanding outside of just prototyping. For instance, smartphone manufacturers have begun using 3D printing for some component parts.
The medical industry is the third largest 3D printing market, contributing 15 per cent of the total 3D printing revenue. The industry uses the technology for mass customized finished goods, such as hearing aids. 98 per cent of hearing aids worldwide are now manufactured using 3D printing.
Despite all of this, 3D printing has not taken over much of the manufacturing landscape, with less than one per cent of all manufacturing output being 3D printed today.
Currently, less than one per cent of all manufacturing output is being 3D printed.
The arguments for and against
Currently, 3D printing is most commonly used for producing prototypes because changes are typically easier and cheaper to make compared with having to reset tools in a factory. The technology is ideal for low-volume production, such as craft items like jewellery or customized products like prosthetics. Dental crowns and hearing aid buds are already being made by the million with 3D printers.
It’s also great for producing lightweight and complex shapes for high-value products ranging from aircrafts to racing cars. This is because the printer deposits material only where it’s needed. GE has already spent $1.5 billion on the technology in order to make jet engine parts, among other things.
But some believe that 3D printing may never be fully embraced by the manufacturing industry because it’s so time consuming; some complex items can take up to two days to create. Currently, the cost of equipment and materials for 3D printing is also quite high, and the choice of materials available is a fraction of the variety used in conventional methods.
During a keynote presentation at the Canadian Manufacturing Technology Show, Kirk Rogers, technology lead at the GE Center for Additive Technology in Pittsburgh, warned that additive manufacturing may not supplant traditional manufacturing entirely. Of the parts GE makes at additive manufacturing centers, he said, 85 per cent have required traditional manufacturing technologies, like machining.
What the future could hold
While 3D printing may not be taking over the entire manufacturing industry just yet, analysts predict there will be a great deal of growth and the market will be worth 32.78 billion USD by 2023.
Analysts have predicted the 3D printing industry will be worth 32.7 billion USD by 2023.
Many manufacturers have already started to explore the market to see what potential may be there. Adidas, for instance, has started to use a form of 3D printing called “digital light synthesis” in order to produce the soles of trainers, pulling them fully formed from a vat of liquid polymer. This method will be used in some new Adidas factories in Germany and America in order to produce one million pairs of shoes annually to market more quickly than conventional processes would allow.
The economics of metal printing could be changed by 3D printing too, with a new technique called bound-metal deposition. The technique can build objects at a rate of 500 cubic inches an hour compared to one to two cubic inches an hour when using a typical laser-based metal printer.
The full consequences of 3D printing in the manufacturing industry are hard to predict. But based on what’s happened already in the industry and what analysts expect to see in the coming years, it seems safe to say that we haven’t seen 3D printing used to its full potential just yet.
Want to learn more about current trends in manufacturing? Check out our blog on the topic! Or visit our Manufacturers’ Insurance page and find out how our experts can help your business today!
This blog is provided for information only and is not a substitute for professional advice. We make no representations or warranties regarding the accuracy or completeness of the information and will not be responsible for any loss arising out of reliance on the information.
Share on email
Share on linkedin
Share on twitter
Why is 3D printing the future of manufacturing
Additive Manufacturing and the future
Looking at stories from the media, there are many predictions that 3D printing is an integral part of the future of manufacturing.
Currently, the technology is rapidly being adopted in many areas of industry and as time moves forward, we shall start seeing the technology being implemented in many use cases not only limited to organisations.
The excitement for the technology is mainly stemming from one simple old economic term which is “Economies of scale“.
Similar to many technologies before it, most of the innovations begin in large institutions and then as the proliferation of the technology grows, economies of scale come into play.
You only have to look at the history of computing itself to see this trend. The first machines were large and clunky and as time went on, more and more developments lead to cheaper methods of production which lead to costs decreasing and finally the computer becoming affordable to the average home.
In terms of current historical comparison, we are at the syndication stage, where the largest adopters of 3D printing technology are institutions and early adopters are aiming to create more value from the technology.
Being a product that is catered to the manufacturing field, this is the logical focus of the market currently. Despite the largest segment being hobbyists, organisations will receive the most value from 3D printing in a number of ways.
Firstly, 3d printing gives companies the capability of in-house manufacturing at the fraction of the price.
Building hardware is hard and the biggest in the initial stage is being able to quickly build prototypes at a reduced cost. 3D printing eliminates many factors, such as expensive machining tools or the route that many companies take which is outsource parts out.
The disadvantage of this approach is simply costs that can arise from reiterations in design and also time, where companies need to compete with other companies that have also orders from the same outsourced firm. In addition, the process of delivery of the request prototype adds to the total lead time of the product development cycle.
The different 3D printing techniques.
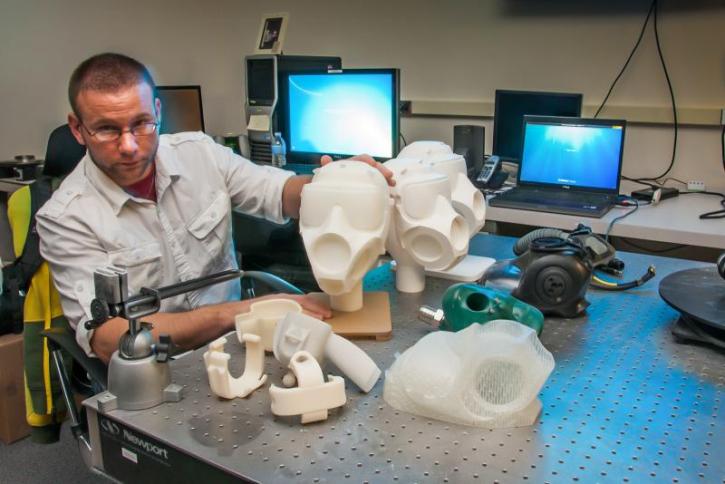
There are a several 3d printing technologies that are used widely in the manufacturing world. We shall focus on the top 3 3D printing techniques and why organisations decide one over another.
Learn more about the 3d printing techniques
Fused Deposition Modelling (FDM)
Also known as Fused Filament Fabrication, this 3D printing technique is the most widely used technique. Its based on spools of plastics or a composite material that is melted and extruded out to create layers.
Companies use this technique due to it being the most user friendly method and that its the only method that offers production-grade thermoplastics like PLA, NYLON and others.
This means parts produced with FDM have in some cases better mechanical properties than other printing methods. Parts produced with FDM have better heat, impact and chemical resistance than other plastic based 3d printing techniques.
Additionally FDM printers in general are less expensive and the materials for the printing process are easily sourced and affordable.
Companies can produce both visual prototypes, functional parts for prototypes and in many cases, tooling for many manufacturing firms.
The disadvantage of FDM is that parts have less detail than other printing techniques, so uses for highly detailed small objects is a little more difficult to reproduce with FDM.
Stereolithography (SLA)
Stereolithography is the oldest printing technique that offers a few different use cases and also operates slightly in the polar opposite of FDM.
SLA uses liquid resins and creates a sliced section of an object that is then hardened using a UV laser.
SLA parts are more accurately produced and offer great tolerance advantages to 3d printed parts.
They are best used for creating highly detailed prototypes for companies that require it, however their costs for both printer and material is higher than FDM.
A further challenge is the use of toxic liquid resins which offer parts that have less mechanical properties than other methods.
Selective laser sintering (SLS)
Selective Laser Sintering uses a powder material that is then hardened with a laser.
Each cross section is built up in the same fashion as SLA but the difference is that SLS machines (DMLS) have also the option of metallic parts that then require a sintering step to harden the finished part.
Parts produced have great mechanical properties and this method can create visual prototypes,functional prototypes and end-use parts.
The disadvantage however is its only used for short production runs due the extreme high cost of both the printer and materials. Additionally, the handling of the powder material can be dangerous if not stored properly.
So, why are so many companies adopting 3D printing?
There are a number of reasons and the biggest is when we look at the concept of economies of scale (where savings are generated by the more you produce).
We see that 3D printing has lowered the minimum efficient scale of production, which is a game-changer for manufacturers.
The minimum efficient scale in manufacturing can be surmised as the lowest amount that an organisation needs to manufacture but still being able to benefit from economies of scale by being able to offer the product at a competitive price.
A simple example would be, if a car company were to produce a small number of vehicles, the average cost of a car would be immensely high because of fixed costs, such as labour costs, rent and others.
If the car manufacturer were to produce a large number of vehicles, then the cost per unit would be lower since fixed costs are spread across the larger number of units.
To better understand this, we need to then look at the relationship between unit average cost and marginal costs.
Marginal costs put simply is the cost associated with producing one extra unit and the change it produces to total costs for that product.
Expanding on the car manufacturing industry, a car company factory at full capacity would need another production line to produce one extra car which would mean the new line being categorized as a marginal cost. By adding the extra line, the cost of producing extra cars would decrease.
This is a key important figure for many manufacturers because it helps them determine the optimal production number for their business.
How does 3D printing relate to the economy?
3D printing is a technology that has a lower efficient scale due to a few properties.
Firstly, 3D printing reduces labour costs because it can be highly automated, where a small team can run a line of printers easily without overseeing each element, affording them to work on other tasks. Secondly, 3D printing can produce highly complex geometric parts in a single process.
What does this mean? Looking at standard production methods, such as injection modelling or CNC machining, many of these technologies require multiple steps to produce items that have complex shapes and in many cases, these technologies cannot achieve the same complexity as 3D printing.
Many parts would require multiple production runs to get the desired results which would increases costs.
Additionally, to be able to create these objects, organisations need highly trained staff which also adds to their fixed costs.
3D printing can produce parts, allow for changes without requiring extra tools or equipment in comparison to other methods.
The future possibilities are exponential and this is why the world is fixated on the technology.
3D printing turns the head on standard manufacturing. Most production innovations since the industrial revolution have been incremental and have been catered to improving upon the previous generations.
Improvements were created through what others had done before, improving production lines, improving inventory systems and other standard manufacturing processes.
3D printing, on the other hand, looks at the physics of producing items, where one machine can produce items simply, quicker and easier than before without using systems of the past.
This is the reason why many companies are focusing on technology and why its potential is highly valued in the manufacturing industry.
Latest tesitmonials
3D printing and the future of small-scale production
Modern desktop 3 D-printing began a little over 10 years ago when a community of enthusiasts arose RepRap. The goal of the project was to "self-copy", replicate the components of the 3D printers themselves. The task was to small-scale production of 3 D-printers on the same 3 D-printers. The idea was picked up and developed by the Czech engineer and entrepreneur Josef Prusa. He created the biggest farm 3 D-printers to print plastic parts produced by his factory 3 D-printers. The total number of printers in his factory reaches 1000 pieces; the achievement was even registered in the Guinness Book of Records.
In this case, I would note the marketing talent of Josef Prusz , because his company produces about 100,000 printers a year: production can hardly be called small-scale. However, he continues to print plastic components for his printers on them. Thus, their reliability is emphasized, because printing is part of the testing process, on the one hand, and on the other hand, it demonstrates to customers the quality of models made on a 3D printer. The effectiveness of such an approach from the point of view of the production itself is negligible. A single injection molding machine would easily handle this task, saving a lot of space and electricity, and there would be no need for a large number of jobs.
Opportunities 3 D-printing for small-scale production
What are the possibilities of desktop 3D printing for small-scale production? I note right away that this article is about desktop 3D printers. I will not consider industrial systems in it, since they are in a different price category, both for the equipment itself and for printing materials.
First, let's talk about what can be produced on 3D printers. Usually we are talking about small plastic elements, plugs, clamps, housings, holders and other similar elements. The choice is to order a mold or 3D print the elements. It is easy to make a choice by calculating the cost of a mold, the cost of products obtained on an injection molding machine and the cost of printing the same product on a 3D printer of the required circulation.
You need to understand: how many units of production per unit of time do you need to produce and, accordingly, how many and what kind of 3D printers will be needed for this task? Having made such an initial analysis and having previously understood that 3D printing is what suits you, you should carefully start choosing equipment.
If you already know what you are going to print, the choice becomes easier. If you plan to produce models with different tasks in the future, you should carefully analyze the possible options before buying. The main factor influencing the choice of equipment is the presence or absence of certain functionality in future models. The printer should print with materials that will ensure the functionality of your products. For example, a future part must withstand a certain heating or cooling temperature, be strong, rigid, wear and impact resistant, or, conversely, soft, rubber-like, elastic, flexible. The more versatile a 3D printer is, the more expensive it is. Indeed, for printing various types of plastic, printers are equipped with closed chambers, interchangeable extruders, perforated platforms, feed mechanisms with adjustable filament pressure, etc.
Solutions based on FDM/ FFF technologies
This is the FDM/FFF printing technology most commonly used today for small-scale production. Let's look at a few technological solutions that manufacturers offer. The most affordable and suitable for printing simple models from plastics such as PLA or PETG is a solution based on budget printers such as CrealityEnder-3. These are very simple models that are installed on racks.
3D printing farm in Creality3D
Among the advantages of this solution: the ability to quickly deploy it in almost any suitable place, quickly increase the number of printers to increase the productivity of the farm. Of the minuses: the impossibility of printing with engineering plastics, the need to manually remove models, as well as the impossibility of remote monitoring and control over printing.
The next level of small-scale production organization is a printer farm capable of handling the most diverse tasks. For example, a farm built on the basis of Raise3DPro2 3D printers. Each such printer is equipped with two extruders, a closed camera and a built-in webcam for remote monitoring. On such printers, you can easily change the "manufactured" models. Today it can be simple plugs made of PLA plastic, and tomorrow it will be complex models made of carbon fiber or nylon gears. The disadvantages include only the high cost of equipment and the remaining need to shoot finished models manually.
3D printing farm at 2050.AT
Another solution is a printer-based farm with two independent IDEX type extruders. In the photo below you can see a similar farm based on Raise3DE2 printers. The solution has the added benefit of increasing productivity: each printer can print two identical models at the same time instead of one. The disadvantages remain the same: the need to shoot models manually and the rather high cost of the printers themselves. The benefits are the same - plus increased productivity.
3D Printing Farm at 3D.RU
If small-scale production is one of the possible applications for the previous solutions, then the printer that will be discussed next is created specifically for this task. The TierTimeX5 model is a mini conveyor with 12 interchangeable pads for long continuous printing. After the printing of the model or models is completed, the platform moves off the platform, a new one takes its place, after which printing can continue. In this case, both the same and different models can be printed. The printer also supports a print queue: different employees can send jobs to it, they will be executed as they arrive. Models from the sites will still have to be removed manually, so it’s too early to talk about full automation.
Of the minuses, it is worth noting the high cost of equipment and its low productivity. For comparable money, you can buy up to 10 printers of the same level, but their performance will be 10 times greater. True, they will take up much more space; keeping track of 10 printers is also much more difficult than keeping track of one. At the same time, it should be taken into account that if one of the 10 printers breaks down, you still have 9 more. If the only printer breaks down, you are left without equipment for an indefinite period of time - depending on the repair time.
Another printer option designed specifically for low volume production is the Creality3DCR-30 PrintMill ribbon type. The printer is created on the principle of a conveyor belt: models can be printed endlessly and fall into the box themselves, you just have to remember to change the plastic. Human participation is minimal, but due to the complex design, where printing is carried out at an angle of 45 °, there are many restrictions on the geometry of models, the location of supports and other nuances. But this is the most automated process of all possible today, especially given the modest budget for the purchase.
In an effort to fully automate small-scale production, manufacturers and builders of 3D printing factories or small-scale production add various equipment. In particular, to automate the removal of models, “cobots” (collaborative robots) are used, which are programmed to remove the platform along with the printed model and install a new printing platform, after which printing resumes. This is an insanely expensive solution that does not really improve productivity and can only be justified in countries with incredibly high wages.
3D Printing Farm VooDooManufacturing | 3D Printing Farm VooDooManufacturing |
Another possible solution for the complete automation of the small-scale production process using 3D printing was presented by the Latvian company MassPortal. She created a portal system for this task. The printers are installed in a rack, where the manipulator arm removes the platforms with finished models and transfers them to a special storage rack. The solution almost completely automates the entire process, but the cost is so high, and the system itself is so cumbersome that it is not worth talking about its effectiveness for a wide range of tasks.
Photopolymer Solutions
All of the solutions discussed earlier in this article were based on FDM/FFF technology, which involves printing with molten plastic filament.
Recently, photopolymer 3D printers are gaining popularity, which print on the principle of forming a model from a liquid photopolymer. From the point of view of small-scale production, this technology has a number of advantages. First of all, performance. The technology allows you to illuminate the entire layer at once - in this way, the printer spends the same time printing one or any other number of models that fit into the construction area. Whereas earlier desktop photopolymer printers had modest pad sizes and, accordingly, their production potential was not very high, already this year a number of models with a large print area and high detail were introduced, for example, the PhrozenSonicMega 8K printer model.
Printing models in the photo lasted 3.5 hours. It is quite easy to calculate the performance of the printer. In this case, even one printer is a mini-factory and is capable of solving serious production problems. Also important is
but note that, unlike FDM / FFF printers, all photopolymer 3D printers are initially universal - you can print on them with any resins available on the market or even those that will appear in the future.
It should come as no surprise that the creators of 3D printing farms were inspired by the huge opportunities that were opening up and many small-scale productions were created based on such equipment. For example, the British company Photocentric has opened the largest such center in Europe based on its LCMmagna model. It came in handy during the pandemic, when it was necessary to urgently establish the production of elements necessary for the treatment of patients, for example, replacement valves for ventilators.
Unfortunately, it can't do without significant disadvantages, but let's talk about everything in order. First of all, this is the process of post-processing of printed models, which consists of washing the models in alcohol and subsequent illumination in a UV camera. Without these procedures, the model will not acquire the final quality. Processes cannot be automated, they require a lot of labor — this must be taken into account when choosing equipment. In addition, it should be taken into account that the cost of photopolymer resin is on average 3 times more than plastic for 3D printing, respectively, the cost of the resulting products will be higher. Another factor that must be taken into account is the need for special preparation of the installation site for printers, the availability of high-quality ventilation and the possibility of waste disposal.
Summary
In summary, even a single 3D printer is a suitable solution for small-scale production. 3D printing is ideal for small-scale production. The main thing is to choose the right equipment, calculate the payback period and the cost of the final product. Based on this, it will be possible to draw a simple conclusion whether you solve your problems or create new problems. Before making a decision, I would advise you to do a test print, understand the performance of the printer, the cost of the material and the quality of the finished product. This will allow you to make the right decision before buying.
what's next for 3D printing
The future of 3D printing
Even now, the prospects for 3D printing are extremely promising. Scientists are actively developing existing 3D printing techniques, developing new technologies and types of materials, and finding new areas of application. Many call 3D printing the technology of the future, and for good reason. The technique is able to completely turn the usual way of life, changing the way most things are produced. In fact, a 3D printer is a real multifunctional factory, small and compact. Due to this, the future of 3D printing can definitely be called successful.
3D printers can significantly reduce production costs, thereby reducing the cost of products. Judging by the growing trend towards the popularization of 3D technologies, raw materials for 3D printing will become the main commodity unit in the future. In general, the prospects for 3D printing are defined for many areas. And now we will try to reveal them as much as possible.
The future of 3D printing
If you try to imagine the future of 3D printing, the imagination paints a rather interesting picture. Given the great interest of scientists in the 3D bioprinting technique, which is one of the most promising 3D printing technologies, the production of artificial organs on a 3D printer is not far off. It is also safe to say that the future of 3D printing will bring us dramatic changes in areas such as:
- Construction. 3D printing of houses, or contour construction, attracts many with its futurism and simplicity. The first steps in this direction have already been taken. The pioneers in 3D printing of houses were the Chinese, followed by the government of Dubai who discovered contour building. The first 3D printed office building has already been built in this city of the future, and an entire block is planned to be printed in the near future. And just recently, the first printed house in Europe was created on a 3D printer;
- Electronics. When listing the prospects for 3D printing, this point should be given special attention. Scientists believe 3D printing of electronics is the future of digital device manufacturing, and with good reason.
Graphene properties and its application in additive manufacturing are currently being actively researched. A huge breakthrough in this area is the creation of a graphene battery with an unlimited service life on a 3D printer;
- Automotive and aerospace industry. The future of 3D printing is largely based on its ability to reproduce almost any element of varying complexity. In this regard, 3D printing is already widely used in the development of aircraft, machines and satellites. The ISS even has its own 3D printer, not to mention a number of successful 3D printing of cars.
- Pharmaceutical industry. Yes, yes, you can imagine. The future of 3D printing is in the manufacture of tablets and other medicines. This is confirmed by epilepsy pills legalized in the USA, made according to a special technique. The essence of this perspective of 3D printing is the gradual release of active substances, so that instead of many tablets, you can drink just one.
- Food industry.
3D food printers are gradually gaining space in cafes and restaurants. While this is probably one of the most raw 3D printing technologies out there, it has potential. Food 3D printers are especially interesting for the possibility of making food for astronauts, as well as the freedom to display culinary talent. This is confirmed by the amazing 3D-printed desserts of our compatriot.
Other questions and answers about 3D printers and 3D printing:
- Finance Which 3D printer manufacturers are best?
- Finance Which 3D printer is better to buy?
The future of 3D printers
Now let's try to imagine the future of 3D printers. There are several important points to be noted here. Below we list the most likely scenarios for the future of 3D printers.
- Improving the reliability and quality of instruments. Surely, many users are looking forward to this, because most of the existing models of 3D printers cannot boast of uninterrupted operation and the absence of printing errors;
- Large-scale distribution.
It is certain that the future of 3D printers will please us with their popularization. Even now, one can observe a growing trend towards the use of 3D printing in almost all areas of industry. In parallel with the fact that more and more users learn about the possibilities of technology, the demand for desktop 3D printers is also growing;
- Availability. In continuation of the previous paragraph, it is worth noting that the growing demand for 3D printers will lead to lower prices for these devices. The use of 3D printing for domestic purposes is gaining momentum, which brings new equipment manufacturers to the market. Naturally, such a step will entail a reduction in the cost of devices;
- Enlargement of the construction area. 3D printing of large-sized objects has long occupied the minds of developers. Of course, this applies to industrial 3D printers, because the functionality of 3D printing at this scale will allow you to create full-fledged components, for example, cars and aircraft;
- Expanding the range of available materials.
The future of 3D printers depends a lot on 3D printing materials, because more means more possibilities. The development of special equipment and related materials is being carried out by many companies, and news about the release of new polymers is constantly appearing.
3D technologies of the future
Summing up, it remains to consider only 3D technologies of the future. These include various futuristic scenarios that, to one degree or another, are already beginning to develop today. These include the technique of virtual reality, 3D scanning to create the perfect clothes and shoes, 3D printed makeup, and more. In a way, 3D technologies of the future also include bioprinting. By the way, scientists are talking about building the first 3D printed settlement on the Moon and Mars, so the prospects for 3D printing are also relevant outside the Earth.
This was a list of the main scenarios for the future of 3D printing. Let's see how they are destined to come true.