3D printing demo wrench
3D printing hands on: Attempting to print a NASA wrench
It costs about a thousand dollars to loft a pound of anything into space. Scientists, astronauts, and project managers are therefore understandably careful about what they choose to send to the International Space Station.
Years of careful planning precede any launch and determine the contents of any launch payload. But as we all know, plans change when they encounter reality. So what happens when an astronaut on the space station needs something that didn't get packed into a shuttle payload?
They make do. The most famous example of the make-do spirit was the Apollo 13 mission, where - after an oxygen tank exploded in the command module - the astronauts had to survive in the lunar module. To do so, they had to build a carbon dioxide scrubber adapter from found parts, which consisted of the cover of the flight manual, duct tape, a pair of socks, and various other components.
While emergencies will undoubtedly still happen in space, and creativity and resourcefulness will still be necessary, NASA researchers have been working on an approach that could provide space station astronauts with a supply of objects, tools, and components using 3D printing.
This is an extremely powerful idea. Think about the general-purpose computer. Once it was possible to create one device that could run many different programs, the computer because an enormously flexible machine. It could be built and installed well before all of its uses were defined or even discovered. When a new program was needed, that program could be coded, and the same physical piece of machinery could run everything from inventory replenishment calculations to plotting missile trajectories - which have reached their cultural culmination in the computation of the flight path of small birds aimed at clusters of small, green pigs.
The general purpose computer is a single machine that can run a wide variety of programs. Likewise, a 3D printer is a single machine that can produce a wide variety of objects.
Scientists at NASA have seen the potential. This one machine can live on the space station and generate an almost infinite variety of objects, tools, and parts. Instead of, for example, waiting for the next shuttle mission to loft a special-purpose wrench to the space station, engineers can just email an .STL file to an astronaut on the station, who can print it out and put it to use.
In fact, there is a 3D printer on the space station, made by the firm Made In Space, Inc. The printer is a fused deposition modeling (FDM) printer very similar to the desktop 3D printers we've been using here in the DIY-IT 3D printing discovery series. In fact, one of the test objects printed on the station's 3D printer was just such a wrench, a small socket wrench shown below.
NASA has even made plans of the wrench, in STL format, available online. So, I decided to download the file and give it a run in my MakerBot Replicator. A special shout-out of thanks goes to MakerBot for providing the printer for our DIY-IT discovery series.
Printing the wrench
Printing the wrench turned out to be a very simple project. All I did was load the wrench into my slicing program and send it to the printer. I did, however, run into a number of problems creating an actual working unit, but those problems were limitations in my tools, not in the file or the 3D printing concept.
I have a printer that is designed to print polylactic acid-based plastic, otherwise known as PLA. PLA is biodegradable and based on corn starch. It's a reliable printing material and has the benefit of not only being good to the planet, it doesn't generate the acrid plastic smell that acrylonitrile butadiene styrene (ABS) plastic is known for.
While PLA is an ideal printing material, it is a little more brittle than ABS. There are ABS printers out there, but they often require a heated build plate and an enclosed printing area. My printer has neither. If you want a good example of something created from ABS, think of Lego bricks. There are roughly 400 billion Lego bricks in the world, and all were made from ABS.
NASA's space station 3D printer is also designed to print ABS, so the wrench design was specifically intended for an ABS printer. I tried it on my PLA printer.
I disregarded the design specs in another way as well. I decided to use the slicing defaults of MakerBot desktop, which included setting a 10 percent infill. Infill is the amount of plastic used to fill solid spaces. Rather than filling the entire space with plastic, various infill percentages generate diamond or honeycomb shapes inside the object. These often provide good strength and both reduce the amount of plastic used and the time used to generate the print.
My first print used 10 percent infill, so as soon as I tried to wrench anything with my first printed wrench, it broke.
My second attempt was unsuccessful as well, because after a little while, the print started to warp, lifting up off the print base. This is because, as layers cool, there is a difference in temperature between the lower layers (which are cool) and the upper layers which are warm. The difference tends to pull the print up off the printing base, and so my second wrench print, this time printed with 100 percent infill (or completely solid) failed due to warping.
Given how long it takes for prints to complete (roughly five hours each), I ran out of time after two prints. You can watch my video at the beginning of the article to see the process in more depth.
Even though the project failed for me, I learned some valuable lessons. I gained a tangible lesson about the strength of the plastic and the relationship between infill percentage and strength. I got a chance to experiment with an actual tool design intended for the space station. I learned a bit about how warping takes place as you increase the infill percentage - and I learned more about build plate adhesion. Finally, I learned that even though this project didn't succeed in the time frame I had available, the discovery process is just that, all about discovery. By attempting this project, I learned a lot and had fun doing it.
If you decide to try making the wrench, especially if you do it with ABS, please let me know how it worked for you in the comment area below.
By the way, I'm doing more updates on Twitter and Facebook than ever before. Be sure to follow me on Twitter at @DavidGewirtz and on Facebook at Facebook.com/DavidGewirtz.
Free STL file UFS-085 Joker Style Wera Wrench
UFS-069 Try Square & Corner Clamp Assembly Combo 02
€0.62
UFS-084A Hex Bit - Wera Like Handle with Collet
Free
UFS-035 Screwdriver using Hex Bit - Driver & Stubby
Free
UFS-059 Table Vise
Free
UFS-118 Polygon Fox Dice Tower
Free
UFS-011 Flashlight Holder - Velcro Strap
Free
UFS-112 Squeeze Fan Tighter Tolerance Fit for Gears
Free
UFS-094 T-Handles Hex Allen Key Wrench
Free
Best 3D printer files of the Tools category
Deactivated
Temperature Sensor Mount Waterdrop Design
Free
Low Cost YouTube Subscriber Display - Sits on a monitor, no soldering required
Free
Eve - Fruit picker
Free
Shredder V8 Gears
Free
CİTROEN C5 BARDAKLIK ( CUP HOLDERS) DESIGN IS RENEWED
€20
MP3 Bike Horn
Free
100$ foldable Drone (Bugs 3 Shell) Simple Build
Free
Best sellers of the category Tools
ENDER 3 S1/PRO SPRITE, V3 AIR DUCT 5015 OR 4020
€2. -20% €2.16 70
INDICATOR FOR BEST BED LEVELING FOR ENDER 3 V2
€2.87
3D Printed Strain Wave Gear (Harmonic Drive)
€4.99
Scissor Paint Rack
€5.30
PET-Machine, make Your own filament from plastic bottles at home!
€15
Fire Hydrant Stash Container
€1.92
ARTEMIS -> Magazine for Alligator 2 || 6.5" Arrows || Repeating crossbow
€6.25
Bambu AMS Stand for Placing raised 2nd Unit behind
€1.15
ENDER 3 S1/PRO SPRITE, HOTEND 4020 OR 5015 FAN PROBE NO Y OFFSET
€2. -20% €1.83 29
Fast-Print Paint Bottle Rack (6 Sizes)
€2.91 -20% €2.33
3D Printer Tool Holder V3.0
€1.06
PRECISION DIAL INDICATOR 3D PRINTING DIY
€1.90
FLSUN v400 display holder
€4.99
Cut-Man - PET bottle cutter with handle!
€3.49
Ender 3, 3 V2, 3 pro, 3 max, dual 40mm axial fan hot end duct / fang. CR-10, Micro Swiss direct drive and bowden compatible. No support needed for printing
€1.62
phone ring holder
€0. 90
Would you like to support Cults?
You like Cults and you want to help us continue the adventure independently? Please note that we are a small team of 3 people, therefore it is very simple to support us to maintain the activity and create future developments. Here are 4 solutions accessible to all:
ADVERTISING: Disable your AdBlock banner blocker and click on our banner ads.
AFFILIATION: Make your purchases online by clicking on our affiliate links here Amazon.
DONATE: If you want, you can make a donation via PayPal.
WORD OF MOUTH: Invite your friends to come, discover the platform and the magnificent 3D files shared by the community!
How metal 3D printers work. Overview of SLM and DMLS technologies. additive manufacturing. 3D metal printing.
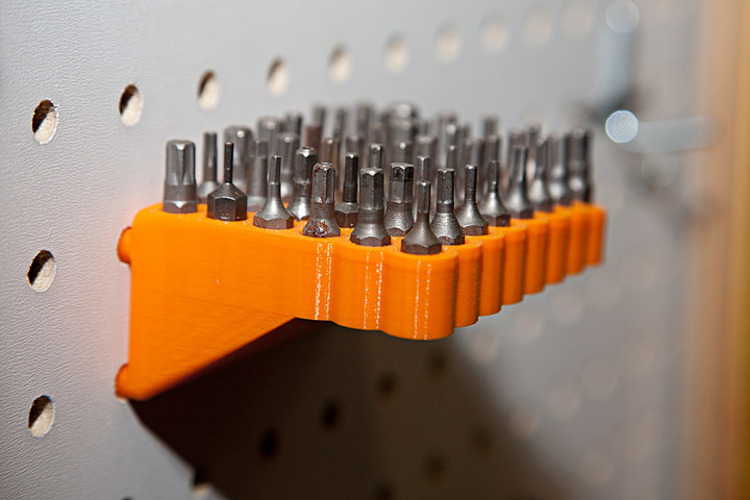
Metal 3D printing. Additive technologies.
SLM or DMLS: what's the difference?
Hello everyone, Friends! 3DTool is with you!
BLT metal 3D printer catalog
Selective laser melting ( SLM ) and direct metal laser sintering ( DMLS ) are two additive manufacturing processes that belong to the family of 3D printing using the powder layer method. The two technologies have much in common: they both use a laser to selectively melt (or melt) metal powder particles, bonding them together and creating a pattern layer by layer. In addition, the materials used in both processes are metals in granular form.
The differences between SLM and DMLS come down to the basics of the particle bonding process: SLM uses metal powders with a single melting point and completely melts the particles, while in DMLS the powder consists of materials with variable melting points.
Specifically:
SLM produces single metal parts while DMLS produces metal alloy parts.
Both SLM and DMLS technologies are used in industry to create final engineering products. In this article, we will use the term "metal 3D printing" to summarize the 2 technologies. We will also describe the main mechanisms of the manufacturing process that are necessary for engineers to understand the advantages and disadvantages of these technologies.
There are other manufacturing processes for producing dense metal parts, such as electron beam melting (EBM) and ultrasonic additive manufacturing (UAM). Their availability and distribution is rather limited, so they will not be presented in this article.
How 3D printing with SLM or DMLS metal works.
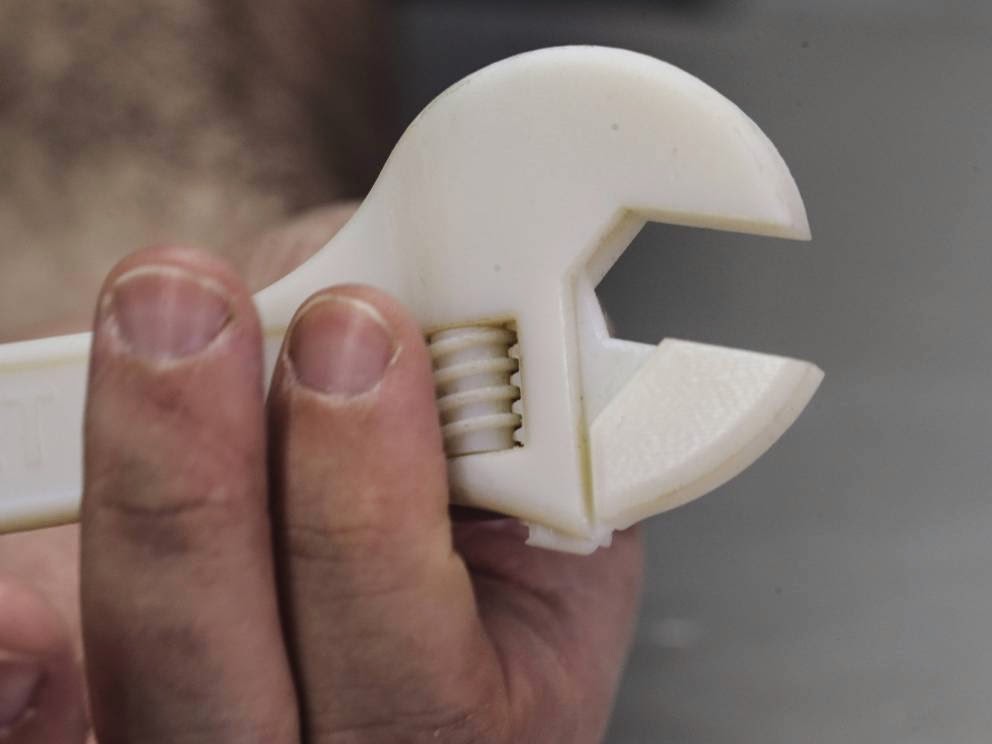
How does metal 3D printing work? The basic manufacturing process for SLM and DMLS is very similar.
1. The printing chamber is first filled with an inert gas (such as argon) to minimize the oxidation of the metal powder. It then heats up to the optimum operating temperature.
2. A layer of powder is spread over the platform, a powerful laser makes passes along a predetermined path in the program, fusing the metal particles together and creating the next layer.
3. When the sintering process is completed, the platform moves down 1 layer. Next, another thin layer of metal powder is applied. The process is repeated until the entire model is printed.
When the printing process is completed, the metal powder already has strong bonds in the structure. Unlike the SLS process, parts are attached to the platform via support structures. The support in metal 3D printing is created from the same material as the base part. This condition is necessary to reduce deformations that may occur due to high processing temperatures.
When the 3D printer's chamber cools down to room temperature, excess powder is removed manually, such as with a brush. The parts are then typically heat treated while they are still attached to the platform. This is done to relieve any residual stresses. They can then be further processed. The removal of the part from the platform occurs by means of sawing.
Scheme of operation of a 3D printer for metal.
In SLM and DMLS, almost all process parameters are set by the manufacturer. The layer height used in metal 3D printing varies from 20 to 50 microns and depends on the properties of the metal powder (fluidity, particle size distribution, shape, etc. ).
The basic size of the print area on metal 3D printers is 200 x 150 x 150 mm, but there are also larger sizes of the working area. Printing accuracy is from 50 - 100 microns. As of 2020, metal 3D printers start at $150,000. For example, our company offers 3D metal printers from BLT.
metal 3D printers can be used for small batch production, but the 3D printing capabilities of such systems are more like those of mass production on FDM or SLA machines.
The metal powder in SLM and DMLS is recyclable: typically less than 5% is consumed. After each impression, the unused powder is collected and sieved, and then topped up with fresh material to the level required for the next production.
Waste in metal printing, are supports (support structures, without which it will not be possible to achieve a successful result). With too much support on the manufactured parts, the cost of the entire production will increase accordingly.
Adhesion between coats.
3D metal printing on BLT 3D printers
SLM and DMLS metal parts have almost isotropic mechanical and thermal properties. They are hard and have very little internal porosity (less than 0.2% in 3D printed condition and virtually non-existent after processing).
Metal printed parts have higher strength and hardness and are often more flexible than traditionally made parts. However, such metal becomes “tired” faster.
3D model support structure and part orientation on the work platform.
Support structures are always required when printing with metal, due to the very high processing temperatures. They are usually built using a lattice pattern.
Supports in metal 3D printing perform 3 functions:
• They form the basis for creating the first layer of the part.
• They secure the part to the platform and prevent it from deforming.
• They act as a heat sink, removing heat from the model.
Parts are often oriented at an angle. However, this will increase the amount of support required, the printing time, and ultimately the overall cost.
Deformation can also be minimized with laser sintering templates. This strategy prevents the accumulation of residual stresses in any particular direction and adds a characteristic surface texture to the part.
Since the cost of metal printing is very high, software simulations are often used to predict how a part will behave during processing. These topology optimization algorithms are otherwise used not only to increase mechanical performance and create lightweight parts, but also to minimize the need for supports and the likelihood of part distortion.
Hollow sections and lightweight structures.
An example of printing on a BLT 3D printer
Unlike polymer powder melt processes such as SLS, large hollow sections are not typically used in metal printing as the support would be very difficult to remove, if at all possible.
For internal channels larger than Ø 8 mm, it is recommended to use diamond or teardrop cross-sections instead of round ones, as they do not require support. More detailed recommendations on the design of SLM and DMLS can be found in other articles on this topic.
As an alternative to hollow sections, parts can be made with sheath and cores, which in turn are machined using different laser power and pass speeds, resulting in different material properties. The use of sheath and cores is very useful when making parts with a large solid section, as it greatly reduces printing time and reduces the chance of warping.
The use of a lattice structure is a common strategy in metal 3D printing to reduce part weight. Topology optimization algorithms can also help design organic lightweight shapes.
Consumables for 3D metal printing.
SLM and DMLS technologies can produce parts from a wide range of metals and metal alloys, including aluminum, stainless steel, titanium, cobalt, chromium and inconel. These materials meet the needs of most industrial applications, from aerospace to medical applications. Precious metals such as gold, platinum, palladium and silver can also be processed, but their use is of a minor nature and is mainly limited to jewelry making.
The cost of metal powder is very high. For example, a kilogram of 316 stainless steel powder costs approximately $350-$450. For this reason, minimizing part volume and the need for supports is key to maintaining optimal manufacturing cost.
The main advantage of metal 3D printing is its compatibility with high-strength materials such as nickel or cobalt-chromium superalloys, which are very difficult to machine with traditional methods. Significant cost and time savings can be achieved by using metal 3D printing to create a near-clean shape part. Subsequently, such a part can be processed to a very high surface quality.
Metal post-processing.
Various post methods. treatments are used to improve the mechanical properties, accuracy and appearance of metal printed products.
Mandatory post-processing steps include the removal of loose powder and support structures, while heat treatment (heat annealing) is typically used to relieve residual stresses and improve the mechanical properties of the part.
CNC machining can be used for critical features (such as holes or threads). Sandblasting, plating, polishing, and micro-machining can improve the surface quality and fatigue strength of a metal printed part.
Advantages and disadvantages of metal 3D printing.
Pros:
1. Metal 3D printing can be used to make complex custom parts, with geometries that traditional manufacturing methods cannot provide.
2. Metal 3D printed parts can be optimized to increase their performance with minimal weight.
3. Metal 3D printed parts have excellent physical properties, metal 3D printers can print a wide range of metals and alloys. Includes difficult-to-machine materials and metal superalloys.
Cons:
1. Manufacturing costs associated with metal 3D printing are high. The cost of consumables is from $ 500 per 1 kg.
2. The size of the working area in metal 3D printers is limited.
Conclusions.
• Metal 3D printing is most suitable for complex, one-piece parts that are difficult or very expensive to manufacture using traditional methods, such as CNC.
• Reducing the need for building supports, will significantly reduce the cost of printing with metal.
• 3D printed metal parts have excellent mechanical properties and can be made from a wide range of engineering materials, including superalloys.
And that's all we have! We hope the article was useful to you.
Catalog of 3D printers for metal BLT
You can purchase metal 3d printers, as well as any other 3d printers and CNC machines, by contacting us:
• By email: Sales@3dtool. ru
• By phone: 8(800)775-86-69
• Or on our website: http://3dtool.ru
Also, don't forget to subscribe to our YouTube channel:
Subscribe to our groups in social networks:
In contact with
Seven reasons to use 3D printing technology in education
The development of modern technologies does not bypass educational institutions. Ceiling projectors in the 1930s, pocket calculators in the 19s70s, personal computers in the 2000s - technology has always been used to engage in learning and prepare students for postgraduate realities.
The era has come when 3D printing will completely change the idea of classrooms and laboratories. Advances in 3D printing have made the technology more convenient and accessible, helping to increase its popularity in educational circles.
Workers in almost any scientific discipline have the opportunity to use 3D printing as part of the educational process, both in classic face-to-face seminars and in online classes. The thoughtful integration of this technology into educational spaces will enable educators to improve academic performance by developing student analytical and critical thinking skills.
In this article, we explore seven benefits of using 3D printing technology with Formlabs 3D printers to create a real interactive learning environment, unleash creativity, prepare students for combat, and more.
Seven reasons for introducing 3D printing technology into the educational process:
- 1. Creation of an interactive learning environment;
- 2. Development of creativity and innovation;
- 3. Improved perception of the real world;
- 4. Preparation for postgraduate practice;
- 5. Involvement in digital processes;
- 6. Development of problem solving skills;
- 7. Development of design thinking.
Creating an interactive learning environment
Students enjoy immersing themselves in the learning process if the learning environment makes them participants in this process. Material presented through slides can at best only arouse interest and hold attention for a short time. 3D printing technology makes learning dynamic by encouraging students to develop critical thinking skills while designing models. Interactive sessions allow you to explore advanced topics in more depth while developing practical skills such as decision making and problem solving. In addition, 3D printing is accessible to students with different perceptions of the material, which means that kinesthetic and visual learners will equally experience all the benefits of this approach to learning.
For example, 3D printing is included in almost all engineering courses. Students learn 3D printing technology for product development and prototyping, creating functional assemblies and mechanisms, etc. Practicing engineers work on a similar principle. This means that students are given the opportunity, through hands-on experience, to understand what the real job of an engineer is.
Stereolithography (SLA) 3D printing is ideal for custom designs such as anatomy for biology or other medical subjects.
3D printing can be introduced into the educational process not only in engineering areas. In the field of teaching, there are many opportunities for using 3D printing: biology students can print anatomical models of organs, future chemists can study the structure of molecules from their 3D models, graphic designers can create 3D versions of their creative works, historians can recreate historical artifacts, architects - print 3D models of building designs.
Despite the spread of distance learning, the opportunity to gain practical skills has been preserved thanks to technology. A case in point was the case of Michael Silver, professor of architecture at the University of Kentucky College of Design and Architecture, who prints and mails models of buildings his students have been working on. Having physical models of objects helps students analyze their own concepts and ideas. As a result, despite the remote format of classes, 3D printing made it possible to maintain the important principle of “immersion in the process”.
Developing creativity and innovation
Creativity, often underestimated, is nevertheless a critical skill for any successful student. It affects the ability to generate new ideas and develop innovative solutions. 3D printing technology is entirely based on creative skills, encouraging students to find solutions to problems through 3D printing, design models using computer-aided design (CAD) programs, and work on optimizing the printing process. In addition to this, students can color the finished models, further revealing their creative potential.
3D stereolithography (SLA) printed finished products feature smooth surfaces, incredible detail, and ease of painting.
At the University of Massachusetts Lowell, Professor Yoko Oda uses 3D printing to improve his curriculum in 3D design, sculpture, 3D modeling and animation. One of the latest significant developments in the world of sculpture is the use of virtual reality (VR) technology in combination with 3D printing. VR is breaking down the boundaries of 3D design, allowing professional artists and students to create their own 3D artwork using software such as Oculus Medium. Professor Yoko's students can create a 3D object in virtual reality in 30 minutes and then print the finished work on a 3D printer. 3D printing opens up new possibilities for innovation in the creative world.
Improving the perception of the real world
Institutes of higher education are required to prepare their students for "real life" in the profession outside the institution. Therefore, it is extremely important for future specialists to understand how to apply the acquired skills in their work. “It is better to see once than hear a hundred times” - this is exactly where 3D printing can help!
Dental students from Turkey practice dental nerve removal on 3D specimens.
Pre-made 3D objects can also be part of anatomy teaching. At the University of Canakkale Onsekiz Mart in Canakkale, Turkey, 3D printing of dental models has made it possible to teach dentistry remotely.
“The Formlabs Form 3B printer is a great machine with a large print platform that can make 80 molars in 9 hours. The finished models are characterized by a high degree of detail and accuracy of the originals, which made it possible to use the models as demonstration samples,” says Mr. Yosunchyr.
3D printing of organs, cells and other elements of biology and medicine uses polymers specially developed for the healthcare industry, such as Elastic Resin or BioMed Clear Resin. For students of medical specialties, 3D printing technology makes it possible to train operations on finished models. Thus, the high degree of detail of printed objects allows teams of surgeons to plan complex operations.
Postgraduate training
3D printing skills are valued by employers. This technology is used not only in the engineering and manufacturing fields. 3D printing affects many professional areas, from the entertainment industry to jewelry making. According to the report of the research company, the volume of the global 3D printing market in 2019. amounted to 11.58 billion dollars. In addition, the market is projected to grow at a CAGR of more than 14% between 2020 and 2027. In 2018, about 1.4 million 3D printers were shipped worldwide. This figure is expected to reach 8 million units by 2027.
Such a strong growth in the introduction of 3D printers into work processes determines the increase in demand for 3D design skills among graphic design students. 3D printing would not be possible without designers creating models. With the increasing demand for custom-made products, custom design is becoming more relevant than ever. Research and development activities also involve the possession of skills and knowledge about 3D printing. The production of consumer goods requires intensive analytics. 3D printing technology will allow professionals to identify opportunities to reduce costs and improve process performance in their project. The creation of models is also in demand in the field of biology, ranging from the manufacture of three-dimensional sculptural elements to the design of organ models. 3D printing is highly relevant for architecture and construction professionals as they rely heavily on the development of "prototypes".
Students who have knowledge of 3D printing are more prepared for the future work. By mastering 3D printing as part of their studies, students develop creativity, which will allow them to easily cope with professional duties in the future.
Digital Engagement
In today's digital world, students need to be able to effectively use the available technological opportunities. Often, modern technologies are perceived as a negative factor that distracts from the educational process, however, with their correct application, students will be able to interact more productively with the outside world. At the same time, there is no need to be limited to a specific specialization, since technological modernization has affected many areas of professional activity: from fine arts to factory production. Incorporating the study of 3D printing technology into the curriculum will allow students to better navigate digital workflows. The concept of 3D printing encompasses more than just the knowledge of a 3D printer. During the training, students comprehensively study this phenomenon, analyzing all the processes completely, from designing a model in a CAD program to post-processing of the finished product.
For example, you can study photogrammetry, i.e. a scientific and technical discipline that deals with determining the size and other characteristics of objects from their photographic images. Several photographs of an object, building or person taken from different positions are used as the basis for measurements. Then, using automatic algorithms, the images are transferred to a 3D model.
Developing Problem Solving Skills
3D printing technology can handle real-world problems. So, a solution was found to the shortage of personal protective equipment (PPE) and medical supplies for sampling during the COVID-19 coronavirus pandemic. Similarly, it is possible to build work within the classroom. 3D printing will undoubtedly be an incentive to develop problem solving skills in students. At the initial stage of working on their 3D printing project, the author needs to answer the following questions:
- What will the 3D object I print be used for?
- What should you pay attention to when creating a model, choosing materials, processing a finished object?
- How to organize the 3D printing process in such a way that it is most efficient and productive?
These are just some of the questions that need to be answered early in the project. Problems like these require a critical approach. Students will have the opportunity to go from an abstract idea to a real three-dimensional object by analyzing how these concepts relate to each other. By working on prototyping, students will be able to assess how close their project will be to the intended goal, without focusing only on its functionality. 3D printing allows you to solve problems using a logical systems approach, further developing creative thinking.
Development of design thinking
Design thinking is more than just a buzzword. This phenomenon is defined as “an iterative process in which we seek to understand the user, disprove assumptions, rethink the problem in order to find non-obvious alternative solutions.” Design thinking is not a fast-paced trend, but a truly effective approach that is already being adopted by major brands such as Apple and Google. How is 3D printing related to design thinking?
Collaboration and interaction is a key principle of the design thinking methodology. 3D printing opens up opportunities for collaborative creative experimentation among students in group projects. Working on a common 3D printing project, its participants adopt each other's vision and work style. Iteration is another key to design thinking. 3D printing allows students to upgrade their designs based on the results of previous versions and the feedback gathered.
Conclusion
3D printing is a multidisciplinary technology that allows you to develop a wide variety of skills.