3D printing data storage concerns
3D Printing: A Cybersecurity Concern
Skip to content
Cybersecurity
Posted by Goldberg Segalla
Additive manufacturing, more commonly known as 3D printing, is a process of making three-dimensional solid objects from a digital model. Additive manufacturing is already used in a number of critical fields, such as medicine, aerospace, civil engineering, and industrial manufacturing.
3D printers are often internet-connected, and increasingly open-sourced. And because of that, you can virtually 3d print pretty much anything through a 3d printing service.
Confidentiality and privacy concerns are the most direct consequence of a data breach involving a 3D printer. This could compromise confidential data such as schematics and software code for products. For example, an individualized medical device may contain personally identifiable information and a data breach may trigger security and privacy laws – think HIPAA, various data breach notification requirements, or even Federal Trade Commission actions. It is not difficult to appreciate how security of 3D printing has tremendous value in industrial additive manufacturing sectors such as aerospace, automotive, and defense.
To that end, the U.S. Department of Defense recently provided seed funding for the Digital Manufacturing Design and Innovation Institute (DMDII) to launch a “Cyber Hub for Manufacturing” intended to tackle the issue of cyber-espionage attacks against the manufacturing sector. While this effort is specifically geared toward compliance with DOD protocols, the cybersecurity practices have much broader applicability and constitute just one example of efforts to develop cybersecurity infrastructure around this emerging technology.
The product integrity issues, however, may be an even bigger concern than privacy issues. Creation of defects in products built by 3D printers as a result of a hack can have real-world effects in ways many other cyberattacks cannot. For example, if the digital file that includes the code from which the printer generates the physical object is corrupted, the ultimate physical product may fail. This failure could lead to injuries, property damage, litigation, or product recalls. Even worse, the defect in the product may not be immediately identifiable. It is essential that 3D printers and all connected devices have protections to secure both digital designs and code as well as the integrity of the physical product.
The challenges to cybersecurity protection of both the digital and physical sides of the growing additive manufacturing industry should be on the mind of those designing and making 3D printed materials; those incorporating 3D printed materials into their own products for sale or use; and insurers. Traditional product liability law could potentially even lead a court to find that a manufacturer or seller of a 3D printed product is strictly liable, even if it did not know or have reason to suspect a manufacturing defect.
These product integrity issues are certainly on the mind of cybersecurity professionals looking at these concerns. For example, researchers are hard at work developing systems to verify the integrity of 3D printed objects. For example, a team of researchers from Georgia Tech and Rutgers University developed a three-layer system to verify that 3D printed objects have not been compromised by using acoustic measurements, printer component tracking, and detectable nanorods. Their system works independently from corporate computer networks to remove one of the major gateways to cybercrime.
At the very least, basic cybersecurity hygiene is critically important for manufacturers in the 3D printing space. Protecting 3D printing environments defends against a broad spectrum of other potential legal concerns including intellectual property, personal information, and product integrity. Those in the field should take heed.
3D printingcybersecurityFederal Trade Commission (FTC)
How 3D printing could pose a threat to your privacy
Skip to main contentWhen you purchase through links on our site, we may earn an affiliate commission. Here’s how it works.
3D printing was first employed as a fast and inexpensive way to create prototypes before manufacturing. However, in the past few years, 3D printers have become significantly cheaper and more readily available to the average consumer. These days, users around the world are taking advantage of 3D printers to create all kinds of different objects which can be purchased online or printed yourself if you have the necessary equipment and materials.
While 3D printing has tremendous potential when it comes to being able to create objects at home without the need to travel to a store, the technology could also pose a “grave and growing threat” to individual privacy due to the potential for 3D printed objects to reveal private information about individuals. TechRadar Pro spoke with Dr. James Griffin from the University of Exeter and Dr Annika Jones from Durham University to learn more about their research on the potential privacy threats posed by 3D printing.
- We've put together a list of the best 3D modeling software around
- These are the best all-in-one printers on the market
- Also check out our roundup of the best portable printers
How has 3D printing evolved over the last few years and how close is the technology to mainstream adoption?
3D printing has evolved exponentially, and is now reaching a stage where we can see people starting to use it in everyday activities. The mainstream technologies could still be criticised for being a bit basic, but extremely capable printers are dropping in price all the time. Don’t be surprised if within the next ten years, you have a fast 3D printer capable of printing complicated metal and plastic objects in your garage (and this time, it isn’t just hyperbole!)
(Image credit: Shutterstock)Why does 3D printing pose a threat to individual privacy and could it be more invasive to user privacy than the Internet of Things (IoT)?
3D printing doesn’t per se pose a threat to privacy (although we have heard [unsubstantiated] rumours of printers passing information about prints back to manufacturers). The issue we have raised is in the use of watermarks to reveal information about the activities of users. For example, a watermark embedded onto a 3D printed object could be tracked and traced through photographs online, e.g. through google image search. If this were, say, a piece of jewellery, it might be a way to track the movements of an individual; likewise, some 3DP implants could be traced through the use of x ray equipment. The files themselves could also be searched for online. The possibilities are, ultimately, endless.
Similar technologies can be employed by the IoT, indeed, there is some overlap. However, the interesting thing about 3D watermarks is that they could be on an analogue physical object, and they can be different for every single print. In effect, it could allow for a blockchain or Google search for physical objects – imagine that! As the IoT becomes more predominant, then these devices could recognise 3DP watermarks, in effect bringing together the 3DP analogue world and the digital world. If, as one would expect, 3DP becomes mainstream in the future, then we can see that the use of 3DP watermarks in conjunction with IoT could become rather common and a critical component in our everyday lives.
How can the origins of 3D printed objects be traced and would this be easy to do without technical knowledge?
Right now this is not so easy, but I am sure this will quickly change. There is a market incentive to implement watermarks into 3D prints – e.g. to find out how consumers use 3DP objects, in exactly the same way that online content providers use watermarks to know how their content is being used.
In summary - watermarks might assist governments in surveillance; they can assist companies to find out what consumers want; they could enable an individual to spy on another. We argue that we should be wary of some of the uses to which watermarks could be put.
However, there are some extremely beneficial uses. One which is becoming apparent through our research is that watermarks can be used in medical devices. They could be used in ensuring the quality of the source materials, and they can be used to ensure the continued stability of a print (e.g. 3D printed organs etc).
Can you tell us a bit more about the 30 in-depth interviews you conducted with representatives from Chinese 3D printing companies?
We had funding from the UK Arts and Humanities Research Council, the Newton Fund and the Ningbo Science and Technology Bureau to carry out these interviews in China. This was achieved through the University of Nottingham’s Ningbo campus. We interviewed companies mainly in Shanghai and Beijing. Separately to this research, I have spoken to similar companies in the UK and the parallels in the concerns and issues raised was striking.
Are watermarking technologies currently being used in schematics for 3D printed objects uploaded to platforms such as Thingiverse?
Not to my knowledge, but watermarks can be platform agnostic. You could put a watermark into any file, without the knowledge of the platform. Platforms could take advantage of a watermark (e.g. for licensing purposes) if they so wish though.
What kind of regulations do you think should be put in place to protect the privacy of users when it comes to 3D printing?
Our main concern is to raise the issue. It would be great if regulation could be achieved without government intervention, but it might become necessary if these privacy issues become significant – which we think they could do, very quickly. Given the global nature of the Internet, it would be useful to have some guidance at international level, e.g. in a voluntary code which would be associated with a kitemark. The trouble with our current law is that there is protection (probably!) available for digital watermarks for copyright works, but that protection does not take into account privacy concerns. Indeed, it could be making matters worse by protecting privacy invading technologies. Similarly, the scope of the current law is likely to only cover copyright works, and not the more beneficial uses of watermarks in e. g. bioprinted technologies.
- We've also highlighted the best 3D printer
Sign up to theTechRadar Pro newsletter to get all the top news, opinion, features and guidance your business needs to succeed!
Contact me with news and offers from other Future brandsReceive email from us on behalf of our trusted partners or sponsorsTechRadar is part of Future US Inc, an international media group and leading digital publisher. Visit our corporate site .
© Future US, Inc. Full 7th Floor, 130 West 42nd Street, New York, NY 10036.
REC Wiki » Common Extrusion 3D Printing Problems and Solutions
FDM/FFF A 3D printer is a complex machine, and 3D printing filaments can vary greatly in properties. As a result, it may be difficult for a novice user to identify the causes of defects in printed products. Especially for such cases, we have prepared a guide with a list of the most common problems and solutions.
Table of Contents:
- No feed
- Problems with laying the first layer
- Model falls off the table during 3D printing
- Model deformation during 3D printing
- Skip layers or recesses in the walls
- Beads on surfaces
- Bundle
- Ringing
- Sagging of individual elements of model
- Thin gaps between walls
- Irregularities or holes in the top layer
- Web
- Model cannot be separated from table
1.
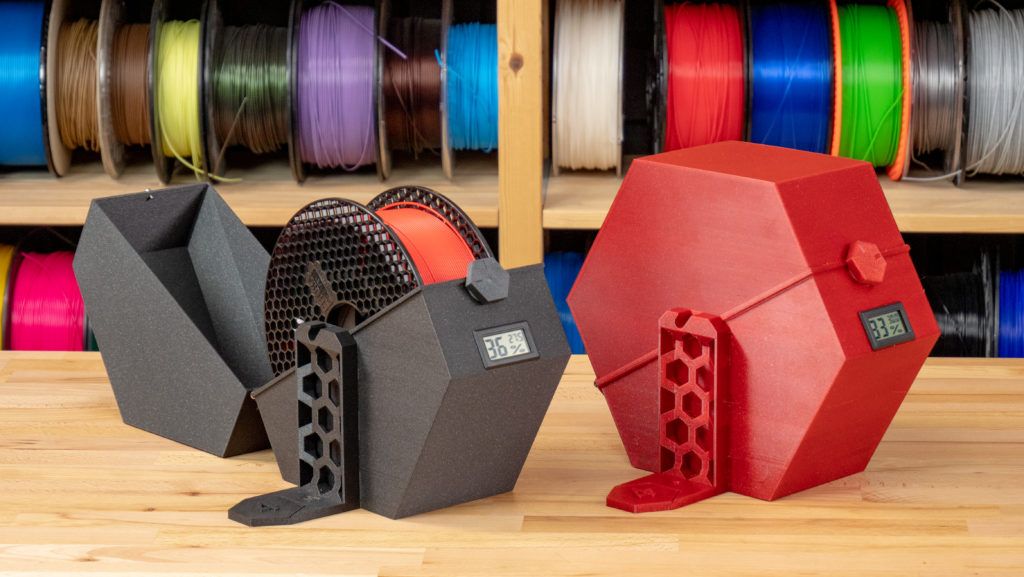
There may be several reasons. The first is a broken filament. Make sure the filament is threaded into the push mechanism of the extruder (feeder).
The second possible cause is insufficient extrusion temperature. Check the temperature of the hot end and compare with the settings recommended by the filament manufacturer. nine0003
Third nozzle clogged. It can occur due to the formation of soot or scale when the plastic is overheated. Solved by cleaning the nozzle with a needle, soaking in a suitable solvent and / or igniting the nozzle.
Fourth Insufficient distance between nozzle and worktable surface. In other words, the nozzle rests on the table. It appears at the very beginning, when you try to lay the first layer. Solved by calibration. The procedure for "zeroing" varies from printer to printer, but calibration instructions should be in the instruction manual. nine0003
Fifth - manufacturing defect or deformation of the bar. Unload the extruder and check the filament for thick or thin filaments that could prevent the filament from feeding into the throat of the hot end or from engaging with the feed gears.
Sixth - Insufficient feeder pinion pressure. The pressure must be strong enough for reliable feeding, but not excessive to avoid deformation of the bar and the previous problem. As a rule, the clamping action is adjusted by means of a spring and a special screw. nine0003
Seventh - chewing the filament in the feeder. It is characteristic only for very soft, elastic materials. It is solved by reducing the feed rate, ideally requires the completion of the extruder in order to reduce the distance between the feed gears and the throat of the hot end.
2. Problems with the first layer
Partial peeling, gaps, "vermicelli" or severe unevenness when laying the first layer indicate incorrect table alignment. In various 3D printers, the problem is solved in different ways - from manually adjusting the platform inclination with adjusting screws to automatically generating a surface grid with software compensation during printing. Check the alignment instructions in the 3D printer's instruction manual. nine0003
3. The model falls off the table during 3D printing
Each plastic requires certain conditions for stable adhesion to the surface of the table. Some materials stick well to glass, others need masking tape, in some cases additional adhesives are required - glues, varnishes. In addition, heavily shrinkable materials require the stage to be heated during 3D printing. Check the recommended surfaces and adhesives for the selected material, as well as the recommended stage temperature if the material requires heating. nine0003
4. Deformation of the model during 3D printing
Deformations can manifest themselves in different ways. One option is the so-called “elephant foot” (pictured above), that is, a thickening at the bottom of the model. It arises due to insufficiently rapid cooling of the layers: the lower layers do not have time to harden and spread under the weight of the material applied over them. It is solved by increasing the blowing and / or reducing the print speed. Also check the table heating settings, it may be worth lowering them. nine0003
The second option is the twisting of the layers (warping), characterized by the detachment of the edges of the model from the table, in extreme cases, even the complete detachment of the model from the working surface. It is caused by heat shrinkage, it is treated primarily by observing the temperature regime of the table and using additional adhesive agents. 3D printing of products from polymers with high heat shrinkage, if possible, should be carried out on 3D printers not only with heated tables, but also with closed chambers. If this is not possible or the background temperature stabilization is not enough, try adding an external contour in the slicer - a skirt or a raft, which increase the contact area of the model with the table, and also try to reduce the filling density of the model. nine0003
The third option is shifts or incorrect layer geometry. Make sure that there are no drafts that could cause uneven shrinkage of the model, if necessary, either use a heat chamber or print a protective outline around the model. In pronounced cases, such defects are usually associated with mechanical problems: insufficient fixation of the pulleys, worn bearings, insufficient lubrication, friction or insufficient belt tension, and so on. Requires careful checking of nodes. nine0003
5. Missing layers or notches in the walls
Typically caused by insufficient extrusion. Check the feed settings and hot end temperature, check that the Teflon tube in the thermal barrier (if any) is not deformed, and try lowering the print speed to allow the extruder to melt the filament. It is also worth checking the cleanliness of the nozzle, soot on the walls inside it can prevent the passage of the filament.
6. Beads on surfaces
Caused by material feed rate too high, i. e. overextrusion. Decrease the plastic feed rate (flow) in the slicer settings.
7. Delamination
Caused by insufficient layer cohesion and/or uneven shrinkage. This is usually solved by increasing the temperature regime: a higher extrusion temperature will provide increased adhesion of the layers, and an increase in the table temperature will help combat heat shrinkage. The presence of a closed chamber in a 3D printer is also of great importance. Typically, this problem occurs with open type printers. nine0003
8. Ringing
Ripples on surfaces, also known as “ringing”, can be both the result of vibrations and a sign of mechanical problems, such as extruder play, twisted shafts, insufficient belt tension. In most cases, it is caused by excessive vibrations and is solved by reducing the print speed.
9. Sagging of individual elements of the model
Manifested when building hinged structures - horizontal (the so-called "bridges") or inclined. FDM/FFF 3D printers are not able to print in the air, so if the angles are too high or the length of the horizontal elements is too long, the addition of support structures (supports) is required. Check the slicer settings and use the automatic support building feature. If the plastic sags even at low angles or when printing short bridges, try lowering the print speed or increasing the airflow to allow the material to harden. nine0003
10. Thin gaps between the walls
The problem appears mainly when building thin contours and is associated with a fixed width of the laid lines, depending on the settings and nozzle diameter. For example, when laying a wall with a thickness of two or three lines, there may be no problems, but when laying a wall with a thickness of two and a half lines, a gap may appear. Some slicers dynamically adjust line widths to help avoid this problem. Otherwise, you will either have to change the nozzle diameter, or manually modify the 3D model, or change the scale. nine0003
11. Irregularities or holes in the top layer
Caused by insufficient thickness and/or too slow cooling of the top layer when printing over partial inner fill. To prevent the material from sagging, try increasing the airflow, if holes appear, try increasing the thickness of the top layer through the appropriate setting in the slicer.
12. Spider web
Appears as fine hairs on the surface of the model or between individual areas. Caused by insufficient retract (reverse) of the material when the head is idle. Try increasing the retract value in the slicer settings. If the problem cannot be solved programmatically, don't be discouraged: the web is quite easy to separate manually after the 3D printing is completed. nine0003
13. Model does not separate from the platen
In some cases, especially when printing on glass plates, adhesion to the platen may be excessive and even damage either the model itself or the platen if excessive force is applied. To avoid such problems, try applying glue or varnish as a release layer before printing, after cleaning the work surface with a suitable solvent, and also take your time and allow the model to cool completely after printing is completed. Remember that cooling is accompanied by shrinkage, and therefore after a while the model may separate from the table on its own. In extreme cases, separate the product after cooling with a sharp, thin blade (scraper or knife), being careful not to damage the surface of the table. nine0003
5 common problems in a 3D printing shop
Large variety of printing materials.
Working with a lot of media means you have at least a few spools of each material in your shop. These can be coils from one or more manufacturers, coils from one or from different production batches. Unfortunately, at the moment, there are actually no standards for the production of filament for 3D printing, except, perhaps, the standard for the diameter of the rod. Temperature characteristics may vary slightly for one type of plastic from different manufacturers. This is primarily due to the fact that each manufacturer of materials for 3D printing uses different raw materials from their suppliers. Also, different manufacturers of materials can use different types of dyes for the filament, and dyes can have a rather strong effect on the physical and chemical properties of materials. But even if you work with only one manufacturer of 3D printing plastic, there is no guarantee that the print settings will always be the same, as raw materials, dyes and production parameters may change with the manufacturer over time. Therefore, when opening a new coil, it is advisable to perform at least 2 material tests: for the amount of plastic flow required (flow) and for the optimal printing temperature (temperature tower). nine0003
Differences in settings between different cartridges can be significant, sometimes resulting in printing defects or even damage to the print head. The situation becomes more complicated if you have not one printer, but, for example, ten, and you urgently need to place an order from a new reel, but there is no time for tests. In this case, you will have to trust your experience: try to set the optimal parameters and be ready to correct the settings during printing.
Conclusion: do not neglect testing the new coil, it will save you time and nerves and you will be able to use all the good quality material for 3D printing. Use materials from reliable manufacturers. Check the new coil yourself, empirically, because reviews on the Internet cannot always give you a complete and truthful picture. nine0003
Hot end wear.
When working with a large fleet of constantly running 3D printers, the problem of nozzle wear always comes up unexpectedly. Now on the market of raw materials for 3D printing, there are structurally rigid composite and metal-filled materials that can increase, in a short time of their use, the nozzle diameter from 0. 4mm to 0.6mm.
If this is not noticed in a timely manner, it will be difficult to achieve a good quality of the printed model. Deviation from the desired diameter, although it is unpleasant, is not the worst thing. Practice shows that a slight offset from the desired nozzle diameter does not greatly affect the printing of large models with simple geometry that do not require high precision in the development of elements. It is much worse when the nozzle is ground unevenly, because of this, the incoming material lies unevenly on the layer. The printed surface may go in waves or have other defects visible to the eye. It's pretty easy to notice that a nozzle is malfunctioning: when you load plastic into the extruder, you can see how the flowing material bends and twists at the outlet of the nozzle. nine0003
Output: constantly monitor the state of your hotend. Before printing, push the plastic through the extruder, watch the flow of material coming out of the nozzle. If the material flows out unevenly, then we can say with confidence that there is a problem with the extruder, which is best solved at the start of 3D printing. 3D printer nozzles are a consumable item, stock up on replacements if you have a lot of printing to do.
Use of nozzles with different diameters on 3 D printers.
As a rule, different orders can be printed with nozzles with different outlet diameters. For example, models with fine details are best printed with nozzles with a diameter of 0.2mm, and for rough technical details with 100% plastic filling, it is much more profitable to use nozzles with diameters of 0.6-1mm. If you have one printer, then changing one nozzle to another is not a big deal: you heat up the hot end, remove the material, unscrew the nozzle, and screw in a new one. Since most nozzles have slightly different heights (especially if the nozzles are of different types: e3d or mk8), after changing from one to another, it is usually necessary to re-calibrate the 3D printer bed. nine0003
If you use a whole fleet of 3d printers, then you will have to change nozzles for different orders often, which means you need to try to optimize this task.
Conclusion: sign on your printers the nozzle diameter that is currently set. Select printers for "coarse" and "fine" printing, where nozzles of large and small diameters will stand, respectively. Use special tools: the nozzle is much easier to remove with a socket head. Organize the storage of your working nozzles, use cash registers. nine0003
Table wear on 3 D printers.
This type of problem is a combination of two things: incorrect print head alignment relative to the 3D printer bed, and excessive adhesion of the material to the bed. In the first case, when your 3D printer is poorly calibrated and printing starts “on the table”, glass surfaces or film coatings wear out, and the printer’s hot end may also suffer because of this, as the nozzle clings to the table surface. In this case, the table can be damaged so much that defects will form on the first layers of the models - chips and dents of the table will be imprinted on the finished part. If you need a smooth, even surface on the model, this will spoil all the work done. nine0003
The second reason for table wear is increased adhesion of parts to the table. If, for example, you print a material with high adhesion (PetG, TPU, PLA, etc.) using 3D printing glue on a heated table, then the finished part, even after complete cooling, may well pick up a piece of sticker or even glass , depending on the type of printable surface.
Conclusion: Precise calibration of the table and setting up the print of the first layer of the model is half the success of all printing and the key to a long life of the 3D printer working surface. Always take into account the characteristics of the printed material, select the correct settings for the first layer of printing. nine0003
Overlapping and jumping thread diameter.
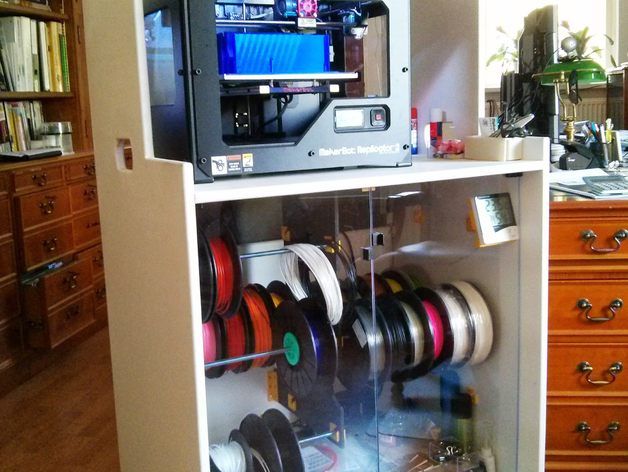