3D printing companies pittsburgh
3D Printing Service for Pittsburgh, Pennsylvania
CapabilitiesCustom Online 3D Printing ServicePennsylvaniaPittsburgh
High Quality Pittsburgh, Pennsylvania 3D Printing | 60+ Materials Available
Endless Options
Choose from millions of possible combinations of materials, finishes, tolerances, markings, and certifications for your order.
Easy to Use
Get your parts delivered right to your door without the hassle of sourcing, project management, logistics, or shipping.
Quality Assurance
Our number one job at Xometry is making your custom parts to your specifications.
Your Pittsburgh, Pennsylvania 3D Printing Service: 3D Prototypes and Production Parts
A Global Leader in Industrial-Grade 3D Printing
Xometry is an industry-leading 3D printing service. Whether you need prototypes or production parts, we can make them for you in as fast as a day. We are your one-stop-shop for accurate, precise custom 3D printed parts at a low cost. Upload your 3D CAD file to get a quote and lead time within seconds. We use the latest additive manufacturing processes to build affordable functional prototypes & end-use parts in over 60 metals and plastics.
We offer eight high-quality 3D printing processes including selective laser sintering, fused deposition modeling, stereolithography, direct metal laser sintering, polyjet, Carbon DLS, binder jet metal, and HP Multi Jet Fusion. We use commercial and industrial-grade printers such as Stratasys Fortus 900mc and Fortus 450 FDM, EOS Polymer Laser Sintering (SLS) and DMLS, Concept Laser, SLM Solutions, 3D Systems, ExOne, and more.
Xometry's High Quality 3D Printing Services
Selective Laser Sintering (SLS)
Selective Laser Sintering (SLS) is a powerful 3D printing technology that produces highly accurate and durable parts that are capable of being used directly in end-use, low-volume production, or for rapid prototyping.
An additive manufacturing layer technology, SLS involves the use of a high power laser (for example, a carbon dioxide laser) to fuse small particles of plastic powders into a mass that has a desired three-dimensional shape. The laser selectively fuses powdered material by scanning cross-sections generated from a 3-D digital description of the part (for example from a CAD file or scan data) on the surface of a powder bed. After each cross-section is scanned, the powder bed is lowered by one layer thickness, a new layer of material is applied on top, and the process is repeated until the part is completed.
Download the SLS Design Guide.
Stereolithography (SLA)
Stereolithography (SLA) is a robust 3D printing technology that produces extremely accurate and high-resolution parts that are capable of being used directly in end-use, low-volume production, or for rapid prototyping.
SLA is an additive manufacturing process that focuses an ultraviolet (UV) light on a vat of photopolymer resin. It offers higher resolution printing than many other 3D printing technologies, allowing customers to print parts with fine details and surface finishes. SLA 3D printing is a highly-versatile platform for making custom parts in prototype and production settings; often acting as a stand-in for injection-molded plastic parts.
Xometry offers both standard and high-resolution options for fine detail parts, and can also print larger sized parts and products, with some materials offering up to a 58" inch build area. In addition, Xometry's manufacturing partner network allows us to offer a larger variety of materials than other 3D printing companies - we offer a wide range of both Accura and Somos brand materials.
Download the SLA Design Guide.
Fused Deposition Modeling (FDM)
Fused Deposition Modeling (FDM) is a 3D printing technology widely known for its speed, accuracy, and competitive cost. A machine precisely extrudes melted plastic filament to create a part. Parts are very rigid, especially compared to Selective Laser Sintering (SLS), which makes them a great fit for projects with a rigidity requirement. Xometry's FDM solution offers large build volumes up to 24″ x 36″ x 36″, a variety of colors, and a diverse selection of production-grade thermoplastics — from ABS to Polycarbonate to Ultem.
Download the FDM Design Guide.
HP Multi Jet Fusion (HP MJF)
HP Multi Jet Fusion is a new 3D printing technology that produces highly accurate and durable parts that are capable of being used directly in end-use, low-volume production, or for rapid prototyping. Since the process uses well-established 2D printing ink-jetting, it has remarkably fast layer times compared to other powder bed fusion technologies.
Download the HP Multi Jet Fusion Design Guide.
PolyJet 3D (PJ3D)
PolyJet 3D is a 3D printing technology known for its customizable material properties and excellent surface finish. It works by jetting UV curable resin onto a build tray in a process that is somewhat similar to inkjet printing. PolyJet 3D printing offers one of the most advanced industrial 3D printing solutions available, producing parts with incredible precision and speed. It also supports a wide variety of build materials including rigid and rubber-like plastics. Xometry's PolyJet solution has a maximum build envelope of 19. 3 × 15.4 × 7.9 in. (490 × 390 × 200 mm) in a variety of colors and materials.
Download the PolyJet 3D Design Guide.
Direct Metal Laser Sintering (DMLS)
Direct Metal Laser Sintering (DMLS) is an 3D metal printing technology that builds prototype and production metal parts from a CAD file using a laser to selectively fuse a fine metal powder in either stainless steel or aluminum materials. A DMLS machine is capable of producing highly complex features and all-in-one assemblies using metal materials that would be difficult to achieve with subtractive manufacturing techniques.
Our DMLS metal 3D printing service typically offers build volumes up to 250 x 250 x 325 mm, but we may be able to accommodate larger part volumes upon request in the quote. (See our Manufacturing Standards for more details) A good first step is to find out the cost of the parts you need using DMLS and compare them to other 3D printing processes and CNC machining.
Download the DMLS Design Guide.
Carbon DLS™
Carbon DLS™ uses digital light projection, oxygen-permeable optics, and programmable liquid resins to produce products with end-use durability, resolution and surface finish. This 3D printing technology is called Digital Light Synthesis™, or DLS for short. Another legacy term for the process is Continuous Liquid Interface Production (CLIP). Along with Carbon’s custom liquid resins, DLS unlocks new business opportunities and product designs previously impossible, including mass customization and on-demand inventory of end-use products.
Carbon bridges, and sometimes substitutes, for processes like Urethane Casting and Injection Molding service production, because the materials are urethane-based or epoxy-based, giving excellent mechanical properties. There are even elastomer and silicone resins that outperform most additive manufactured rubber-like materials.
The typical build area is 7.4” x 4.6” x 12.8”. Parts with dimensions exceeding 4” x 4” x 6” will require manual review.
Download the Carbon DLS Design Guide.
Metal Binder Jetting
With binder jetting, an inkjet print head quickly deposits a bonding agent onto a thin layer of powdered particles -- either metal, sand, ceramics or composites. This process is repeated, layer-by-layer, using a map from a digital design file, until the object is complete. Binder jetting is offered through our Digital RFQ Marketplace through Xometry's partnership with ExOne.
Download the Binder Jetting Design Guide.
Locations near Pittsburgh, Pennsylvania
Morgantown
West VirginiaYoungstown
OhioJohnstown
PennsylvaniaCanton
OhioAltoona
PennsylvaniaAkron
OhioState College
PennsylvaniaCleveland
OhioErie
PennsylvaniaHagerstown
MarylandColumbus
OhioHarrisburg
PennsylvaniaBuffalo
New YorkBethesda
MarylandCharlottesville
VirginiaSilver Spring
MarylandArlington
VirginiaCollege Park
MarylandCorning
New YorkAlexandria
Virginia
Ready to start making custom 3D printed parts?
3D Printing Service Pittsburgh, PA | Instant Quotes Online
Our 3D printing capabilities
We have over 90 3D printing shops in our network and are well known for manufacturing high-quality parts at competitive prices, from rapid prototyping with Fused Deposition Modeling (FDM) to functional end parts made with Selective Laser Sintering (SLS) or Multi Jet Fusion (MJF).
Gallery of 3D printed parts manufactured by Hubs
With over 65,000 customers from every industry, including aerospace, defense, robotics, medical, machinery, automotive and electronics, we have extensive experience meeting a diverse range of 3D printing requirements, from prototyping to production: Visual aids, concept models, injection-molding prototypes, form-fit & function prototypes, tooling and casting patterns, jigs, grips and fixtures, and durable end parts.
HP PA 12 - Dyed Black
Customer | True North Design |
Purpose | Structural and vacuum EOAT components |
Process | SLS / MJF |
Unit price | $69.23 / $34.33 |
Industry | Automotive |
Prototyping PLA
Customer | Allision Conner |
Purpose | End caps and cable strain relief for sheet metal enclosure |
Process | FDM |
Unit price | $7.![]() |
Industry | Industrial Automation |
HP PA 12
Customer | US Hammer |
Description | A part for gasoline engine powered jackhammers |
Process | MJF |
Unit price | $22.18 |
Industry | Construction |
Markforged Onyx - Black
Customer | Autocom Manufacturing |
Purpose | A production part for 3D printed lathe gantry gripper fingers |
Process | FDM |
Unit price | $48.86 |
Industry | Automotive |
PC Stratasys - white
Customer | Terumo medical corporation |
Purpose | Prototyping parts used for a disposable electrical device |
Process | FDM |
Unit price | $55.![]() |
Industry | Medical |
Formlabs Clear Resin
Customer | Aversan Inc |
Purpose | A prototyping part of an injection molded component for an automated door mechanism |
Process | SLA |
Unit price | $29.83 |
Industry | Aerospace |
HP PA 12 - Dyed Black
Customer | True North Design |
Purpose | Structural and vacuum EOAT components |
Process | SLS / MJF |
Unit price | $69.23 / $34.33 |
Industry | Automotive |
Prototyping PLA
Customer | Allision Conner |
Purpose | End caps and cable strain relief for sheet metal enclosure |
Process | FDM |
Unit price | $7.![]() |
Industry | Industrial Automation |
HP PA 12
Customer | US Hammer |
Description | A part for gasoline engine powered jackhammers |
Process | MJF |
Unit price | $22.18 |
Industry | Construction |
Markforged Onyx - Black
Customer | Autocom Manufacturing |
Purpose | A production part for 3D printed lathe gantry gripper fingers |
Process | FDM |
Unit price | $48.86 |
Industry | Automotive |
PC Stratasys - white
Customer | Terumo medical corporation |
Purpose | Prototyping parts used for a disposable electrical device |
Process | FDM |
Unit price | $55.![]() |
Industry | Medical |
Formlabs Clear Resin
Customer | Aversan Inc |
Purpose | A prototyping part of an injection molded component for an automated door mechanism |
Process | SLA |
Unit price | $29.83 |
Industry | Aerospace |
HP PA 12 - Dyed Black
Customer | True North Design |
Purpose | Structural and vacuum EOAT components |
Process | SLS / MJF |
Unit price | $69.23 / $34.33 |
Industry | Automotive |
Prototyping PLA
Customer | Allision Conner |
Purpose | End caps and cable strain relief for sheet metal enclosure |
Process | FDM |
Unit price | $7.![]() |
Industry | Industrial Automation |
HP PA 12
Customer | US Hammer |
Description | A part for gasoline engine powered jackhammers |
Process | MJF |
Unit price | $22.18 |
Industry | Construction |
Markforged Onyx - Black
Customer | Autocom Manufacturing |
Purpose | A production part for 3D printed lathe gantry gripper fingers |
Process | FDM |
Unit price | $48.86 |
Industry | Automotive |
PC Stratasys - white
Customer | Terumo medical corporation |
Purpose | Prototyping parts used for a disposable electrical device |
Process | FDM |
Unit price | $55.![]() |
Industry | Medical |
Formlabs Clear Resin
Customer | Aversan Inc |
Purpose | A prototyping part of an injection molded component for an automated door mechanism |
Process | SLA |
Unit price | $29.83 |
Industry | Aerospace |
HP PA 12 - Dyed Black
Customer | True North Design |
Purpose | Structural and vacuum EOAT components |
Process | SLS / MJF |
Unit price | $69.23 / $34.33 |
Industry | Automotive |
Prototyping PLA
Customer | Allision Conner |
Purpose | End caps and cable strain relief for sheet metal enclosure |
Process | FDM |
Unit price | $7.![]() |
Industry | Industrial Automation |
HP PA 12
Customer | US Hammer |
Description | A part for gasoline engine powered jackhammers |
Process | MJF |
Unit price | $22.18 |
Industry | Construction |
Markforged Onyx - Black
Customer | Autocom Manufacturing |
Purpose | A production part for 3D printed lathe gantry gripper fingers |
Process | FDM |
Unit price | $48.86 |
Industry | Automotive |
PC Stratasys - white
Customer | Terumo medical corporation |
Purpose | Prototyping parts used for a disposable electrical device |
Process | FDM |
Unit price | $55.![]() |
Industry | Medical |
Formlabs Clear Resin
Customer | Aversan Inc |
Purpose | A prototyping part of an injection molded component for an automated door mechanism |
Process | SLA |
Unit price | $29.83 |
Industry | Aerospace |
HP PA 12 - Dyed Black
Customer | True North Design |
Purpose | Structural and vacuum EOAT components |
Process | SLS / MJF |
Unit price | $69.23 / $34.33 |
Industry | Automotive |
Prototyping PLA
Customer | Allision Conner |
Purpose | End caps and cable strain relief for sheet metal enclosure |
Process | FDM |
Unit price | $7.![]() |
Industry | Industrial Automation |
HP PA 12
Customer | US Hammer |
Description | A part for gasoline engine powered jackhammers |
Process | MJF |
Unit price | $22.18 |
Industry | Construction |
Markforged Onyx - Black
Customer | Autocom Manufacturing |
Purpose | A production part for 3D printed lathe gantry gripper fingers |
Process | FDM |
Unit price | $48.86 |
Industry | Automotive |
PC Stratasys - white
Customer | Terumo medical corporation |
Purpose | Prototyping parts used for a disposable electrical device |
Process | FDM |
Unit price | $55.![]() |
Industry | Medical |
Formlabs Clear Resin
Customer | Aversan Inc |
Purpose | A prototyping part of an injection molded component for an automated door mechanism |
Process | SLA |
Unit price | $29.83 |
Industry | Aerospace |
HP PA 12 - Dyed Black
Customer | True North Design |
Purpose | Structural and vacuum EOAT components |
Process | SLS / MJF |
Unit price | $69.23 / $34.33 |
Industry | Automotive |
Prototyping PLA
Customer | Allision Conner |
Purpose | End caps and cable strain relief for sheet metal enclosure |
Process | FDM |
Unit price | $7.![]() |
Industry | Industrial Automation |
HP PA 12
Customer | US Hammer |
Description | A part for gasoline engine powered jackhammers |
Process | MJF |
Unit price | $22.18 |
Industry | Construction |
Markforged Onyx - Black
Customer | Autocom Manufacturing |
Purpose | A production part for 3D printed lathe gantry gripper fingers |
Process | FDM |
Unit price | $48.86 |
Industry | Automotive |
PC Stratasys - white
Customer | Terumo medical corporation |
Purpose | Prototyping parts used for a disposable electrical device |
Process | FDM |
Unit price | $55.![]() |
Industry | Medical |
Formlabs Clear Resin
Customer | Aversan Inc |
Purpose | A prototyping part of an injection molded component for an automated door mechanism |
Process | SLA |
Unit price | $29.83 |
Industry | Aerospace |
HP PA 12 - Dyed Black
Customer | True North Design |
Purpose | Structural and vacuum EOAT components |
Process | SLS / MJF |
Unit price | $69.23 / $34.33 |
Industry | Automotive |
Prototyping PLA
Customer | Allision Conner |
Purpose | End caps and cable strain relief for sheet metal enclosure |
Process | FDM |
Unit price | $7.![]() |
Industry | Industrial Automation |
HP PA 12
Customer | US Hammer |
Description | A part for gasoline engine powered jackhammers |
Process | MJF |
Unit price | $22.18 |
Industry | Construction |
Markforged Onyx - Black
Customer | Autocom Manufacturing |
Purpose | A production part for 3D printed lathe gantry gripper fingers |
Process | FDM |
Unit price | $48.86 |
Industry | Automotive |
PC Stratasys - white
Customer | Terumo medical corporation |
Purpose | Prototyping parts used for a disposable electrical device |
Process | FDM |
Unit price | $55.![]() |
Industry | Medical |
Formlabs Clear Resin
Customer | Aversan Inc |
Purpose | A prototyping part of an injection molded component for an automated door mechanism |
Process | SLA |
Unit price | $29.83 |
Industry | Aerospace |
HP PA 12 - Dyed Black
Customer | True North Design |
Purpose | Structural and vacuum EOAT components |
Process | SLS / MJF |
Unit price | $69.23 / $34.33 |
Industry | Automotive |
Prototyping PLA
Customer | Allision Conner |
Purpose | End caps and cable strain relief for sheet metal enclosure |
Process | FDM |
Unit price | $7.![]() |
Industry | Industrial Automation |
HP PA 12
Customer | US Hammer |
Description | A part for gasoline engine powered jackhammers |
Process | MJF |
Unit price | $22.18 |
Industry | Construction |
Markforged Onyx - Black
Customer | Autocom Manufacturing |
Purpose | A production part for 3D printed lathe gantry gripper fingers |
Process | FDM |
Unit price | $48.86 |
Industry | Automotive |
PC Stratasys - white
Customer | Terumo medical corporation |
Purpose | Prototyping parts used for a disposable electrical device |
Process | FDM |
Unit price | $55.![]() |
Industry | Medical |
Formlabs Clear Resin
Customer | Aversan Inc |
Purpose | A prototyping part of an injection molded component for an automated door mechanism |
Process | SLA |
Unit price | $29.83 |
Industry | Aerospace |
HP PA 12 - Dyed Black
Customer | True North Design |
Purpose | Structural and vacuum EOAT components |
Process | SLS / MJF |
Unit price | $69.23 / $34.33 |
Industry | Automotive |
Prototyping PLA
Customer | Allision Conner |
Purpose | End caps and cable strain relief for sheet metal enclosure |
Process | FDM |
Unit price | $7.![]() |
Industry | Industrial Automation |
HP PA 12
Customer | US Hammer |
Description | A part for gasoline engine powered jackhammers |
Process | MJF |
Unit price | $22.18 |
Industry | Construction |
Markforged Onyx - Black
Customer | Autocom Manufacturing |
Purpose | A production part for 3D printed lathe gantry gripper fingers |
Process | FDM |
Unit price | $48.86 |
Industry | Automotive |
PC Stratasys - white
Customer | Terumo medical corporation |
Purpose | Prototyping parts used for a disposable electrical device |
Process | FDM |
Unit price | $55.![]() |
Industry | Medical |
Formlabs Clear Resin
Customer | Aversan Inc |
Purpose | A prototyping part of an injection molded component for an automated door mechanism |
Process | SLA |
Unit price | $29.83 |
Industry | Aerospace |
HP PA 12 - Dyed Black
Customer | True North Design |
Purpose | Structural and vacuum EOAT components |
Process | SLS / MJF |
Unit price | $69.23 / $34.33 |
Industry | Automotive |
Prototyping PLA
Customer | Allision Conner |
Purpose | End caps and cable strain relief for sheet metal enclosure |
Process | FDM |
Unit price | $7.![]() |
Industry | Industrial Automation |
HP PA 12
Customer | US Hammer |
Description | A part for gasoline engine powered jackhammers |
Process | MJF |
Unit price | $22.18 |
Industry | Construction |
Markforged Onyx - Black
Customer | Autocom Manufacturing |
Purpose | A production part for 3D printed lathe gantry gripper fingers |
Process | FDM |
Unit price | $48.86 |
Industry | Automotive |
PC Stratasys - white
Customer | Terumo medical corporation |
Purpose | Prototyping parts used for a disposable electrical device |
Process | FDM |
Unit price | $55.![]() |
Industry | Medical |
Formlabs Clear Resin
Customer | Aversan Inc |
Purpose | A prototyping part of an injection molded component for an automated door mechanism |
Process | SLA |
Unit price | $29.83 |
Industry | Aerospace |
Instant, online 3D printing quotes
-
Upload a CAD to start (STEP, STP, IGES, IGS, SLDPRT, 3DM, SAT, STL, OBJ or X_T)
-
Price updates in real-time as you change materials, lead time, etc..
-
No hidden costs. Our instant quotes are not just indications, but the actual price, and include shipping and customs up front.
Learn about how our quoting algorithm works
Our ordering process
Receive instant quote
Upload your CAD to our online quoting platform
Confirm specs
Configure your part specifications and select a lead time that suits your schedule
Production
We select the best manufacturer for your order, and production begins immediately
Quality control
We take full responsibility for making sure your parts are manufactured according to our standards
Delivery
Our 3D printing service has been rated 4.9/5
Over 287 customers are satisfied with our 3D printing service.
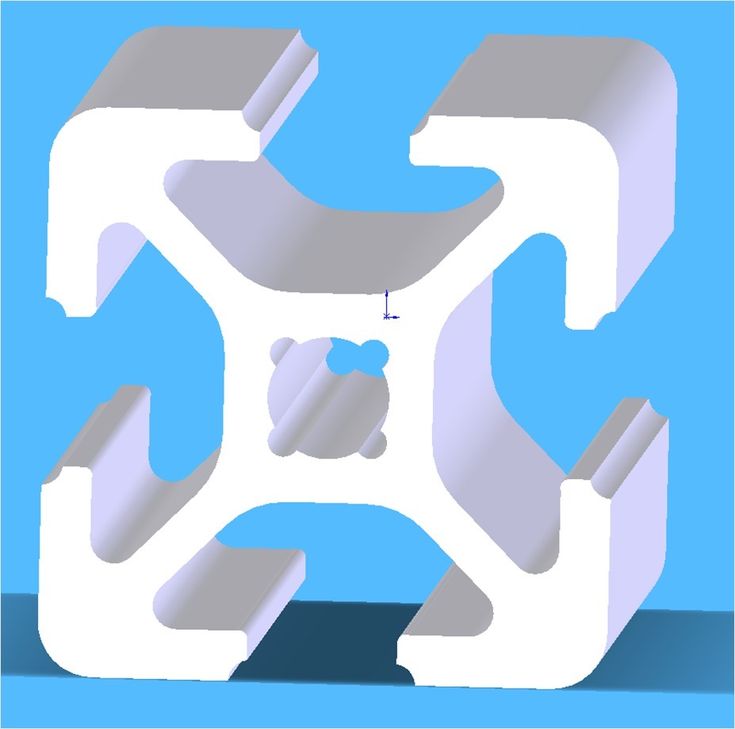
“Fantastic prints, really helped me a lot directly as well.”
“Great print quality and expertise. Thanks for the speedy service!”
“I’m very happy with the service. My order arrived earlier than the estimated delivery date.”
“This was my first experience in anything 3D printed, and I feel it turned out pretty great, so thank you!”
“Great help, item was printed quickly and good quality. ”
“Prints came out great, packaged well. Very happy. ”
“Professional, great communication, and top quality parts!”
“Very prompt and communicated about the parts well. Gave me feedback to adjust the model so it would print better. Print quality was high and shipped quickly.”
“Received the parts a day early and they look good!”
“Incredibly fast service, very high quality parts”
“Once again, beyond happy with the prints and the service.”
“Fantastic work! Was able to turn around the parts faster than was originally estimated!”
“Great service, quick turn around time and knowledgeable hub. ”
“Andrews print quality and communication is top notch!”
“Printed very quickly with little to no issues, post processing will go much easier.”
“Extremely knowledgeable staff, and top quality FDM prints. ”
“Very quick and effortless experience, thanks!”
“Quality of the parts is spectacular, and I was thoroughly impressed with the professional level and quality of packaging.”
“The printed part is great. The dimensions are accurate. The surface finish is better than I expected. Overall very good service.”
“Was willing to do whatever it took to make the parts right. Nice quality print.”
“Good quality part. Quick turnaround. No issues.”
“Part turned out perfect. Could not be happier!”
“The parts were exactly what I ordered, and work great! The was a delay with printing due to a machine breakdown, but there was good communication throughout the delay.”
“Quick service. Part quality was very good.”
“Hubs worked with me to get the highest quality delivered very fast.
Thanks”
Show more reviews
Show less reviews
Teams build better parts
Create your Hubs team and start collaborating
Read more
The Hubs Standard - consistent quality, every time
Hubs takes the stress out of manufacturing by guaranteeing the quality and consistency of every part. Each order is dimensionally and visually inspected to make sure it meets the Hubs Standard.
3D printing materials
We can generate instant 3D printing quotes for 25+ plastics. For metal 3D-printed parts, you can request a quote from our parent company, Protolabs.
Available materials
SLS
PA 12 Glass filled PA 12
Desktop FDM
Prototyping PETG Prototyping ASA Prototyping TPU Prototyping ABS Prototyping PLA
Desktop SLA
Formlabs Standard Resin Formlabs Clear Resin Formlabs Tough Resin 2000 Formlabs Rigid Resin 4000 Formlabs Grey Pro Resin Formlabs Flexible Resin 80A Formlabs High Temp Resin Formlabs Durable Resin
MJF
HP PA 12 Glass filled HP PA 12
Industrial FDM
Markforged Onyx ABSplus Stratasys ULTEM 9085 Stratasys Stratasys ASA ABS M30 Stratasys ULTEM 1010 Stratasys
Industrial SLA
Accura 25 (PP-like) Accura ClearVue Accura Xtreme White 200 (ABS-like)
3D printing locations near Pittsburgh, PA
Monessen, PA Morgantown, WV Pittsburgh, PA
Weirton, WV Wheeling, WV Johnstown, PA
Youngstown, OH Canton, OH Altoona, PA
Parkersburg, WV
The 3D Printing Handbook
No one understands 3D printing like us - our founders literally wrote the book. Click here to download the sample chapters.
Buy the book from Amazon
FAQ's
How much does your 3D printing service cost?
The cost of your 3D printed parts depends on factors such as part volume, part complexity, choice of material, which 3D printing technology is used, and if any post processing is required. For more details on these cost factors, see our article on the cost of 3d printing. To check the cost of your 3D printed part, simply upload a CAD (.STL) file and select your material and 3D printing technology to receive a quote within seconds.
How do you guarantee the quality of my prints?
Your parts are made by experienced 3D printing shops within our network. All facilities are regularly audited to ensure they consistently meet the Hubs quality standard. We include a standardized inspection report with every order and offer a First Article Inspection service on orders of 100+ units.
We have partners in our network with the following certifications, available on request: ISO9001, ISO13485 and AS9100.
Follow this link to read more about our quality assurance measures.
How do I select the right 3D printing process for my prints?
You can select the right 3D printing process by examining which materials suit your need and what your use case is.
By material: if you already know which material you would like to use, selecting a 3D printing process is relatively easy, as many materials are technology specific.
By use case: once you know whether you need a functional or visual part, choosing a process is easy.
For more help, read our guide to selecting the right 3D printing process. Find out more about Fused Deposition Modeling (FDM), Selective Laser Sintering (SLS), Multi Jet Fusion (MJF) and Stereolithography (SLA).
How can I reduce the cost of my 3D prints?
In order to reduce the cost of your 3D prints you need to understand the impact certain factors have on cost. The main cost influencing factors are the material type, individual part volume, printing technology and post-processing requirements.
Once these have been decided, an easy way to further cut costs is to reduce the amount of material used. This can be done by decreasing the size of your model, hollowing it out, and eliminating the need for support structures.
To learn more, read our full guide on how to reduce the cost of 3D printing.
Where can I learn more about 3D printing?
Our knowledge base is full of in-depth design guidelines, explanations on process and surface finishes, and information on how to create and use CAD files. Our 3D printing content has been written by an expert team of engineers and technicians over the years.
See our complete engineering guide to 3D printing for a full breakdown of the different 3D printing technologies and materials. If you want even more 3D printing, then check out our acclaimed 3D printing handbook here.
We have an extensive range of online resources developed to help engineers improve their capabilities.
Introductory guides
Design guides
Material guides
Applications
CAD & file preparation
Post processing & finishing
Our other manufacturing capabilities
CNC machining
CNC machining
Milling (3-, 4- & full 5-axis), turning and post-processing
-
50+ metals and plastics & 10 surface finishes
-
Tolerances down to ±.0008” (0.020 mm)
-
Lead times from 5 business days
See our CNC machining services
Put your 3D printed parts into production today
Get an instant 3D printing quote
3D PRINTED HEADS HELP UNIVERSITY OF PITTSBURGH IMPROVE MRI SCANNING The information obtained from the process can be used to determine, among other things, whether certain implants are suitable for use with the scanner.
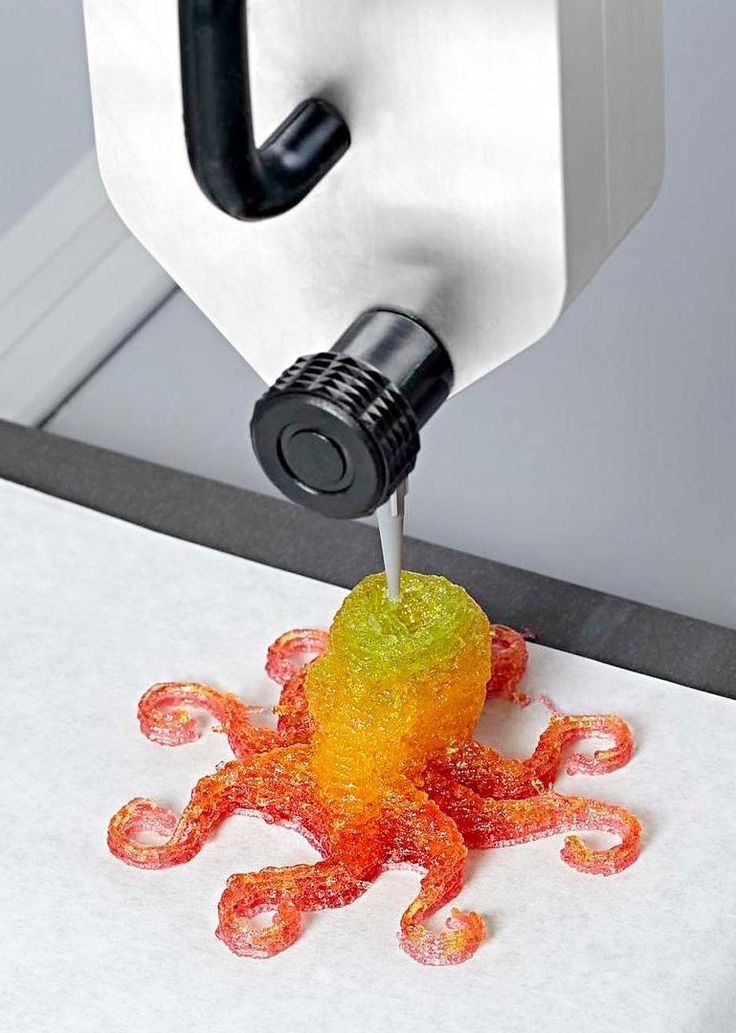
“From 3d mri data package and 3d digitized segmented images to 3d photo printing.” Image and description provided by RF Research Center.
MRI Scan The
MRI Scanner used in Swanson RF Research Center is a Tesla 7th generation one-piece MRI scanner. And it is, according to University of Pittsburgh Associate Professor of Bioengineering Tamer Ibrahim, "one of the most powerful clinical MRI machines in the world." However, the system's caveats include a potentially dangerous increase in outgoing heat transmitted by the scanner and insufficient image transparency. Ibrahim explains: “As you move from a smaller field to a larger one, the output images become less informative and localized heat becomes even more dominant. We wanted to develop a model of a humanoid head to help us better understand the challenges of implementing a safer way to test images.
Model building
To create the model, the RF Research Center team 3D scanned a volunteer's head. Further, it was divided into appropriate segments (parts), namely, the brain, arteries, neck, tendons, etc. Through segmentation, the team identified parts for 3D printing (face/skull) and plexuses that could be added after to fill the head and simulate the nature of the secondary electromagnetic field of living matter.
After modeling in CAD, the partial void of the head/skull was printed in 3D DSM Somos resin on a Stratasys system. In the final step, the artificial skull was filled with fluid through specially designed and reusable ports. The complete process is described in detail in Design and Fabrication of a Realistic Humanoid Heterogeneous Head Model for MRI Purposes, which has been publicly printed by PLOS One. Sossena Wood, Narayanan Krishnamurthy, Tales Santini, Shailesh Raval, Nadim Farhat, John Andy Holmes and Tamer S. Ibrahim are the authors.
3D printed head or human
It took the team several months to plan and achieve most of the exact combinations of the parts of the head model. Then, the model was compared with the head of a volunteer in a laboratory MRI. The result showed that “While our humanoid heterogeneous model does not show the full picture in comparison with electromagnetic fields in the living body of a volunteer, it is much more adequate than a spherical humanoid heterogeneous model or other assembled heterogeneous works” Therefore, further research needs to explore more deeply the potential of the MRI model, which today is still suitable for use in electromagnetic devices.
What's next for medical imaging?
3D printing inspires many 3D data innovations in the medical industry. While it is not uncommon to create a custom model generated from CT or MR scan data, more and more efficient and intuitive approaches are required to prepare and process the data. which is compatible with the medical data standard DICOM data.
Fitted images show head model "From 3T MRI data package and 3D digitized segmented images to 3D photo printing". Image and description provided by RF Research Center
3D printing market. Is it time to buy shares? / Habr
In this article I would like to talk about companies, each of which is a "unicorn". Shares of two of the three can already be bought on the New York Stock Exchange. There is a pattern: they were all born in the large Boston metropolitan area. And if Silicon Valley is a Mecca for software startups, then Boston, and especially the Massachusetts Institute of Technology (MIT), is the Medina for manufacturing innovation.
I'll make it clear right away: I'm not going to analyze the entire 3D printing market, but will focus on some of the most notable representatives of the desktop 3D printing segment. But even here everything is very arbitrary, since in the process of improving technology, products flow smoothly from one category to another, and roughly three main categories can be distinguished: desktop, professional and industrial. So…
In 2011, three American students founded Formlabs in their garage. It was headed by Max Lobowski. Born into a family of engineers - emigrants from Ukraine, he was interested in robotics and new technologies from his youth, attended various specialized additional classes in high school. After earning a bachelor's degree from Cornell University, he went on to graduate school at MIT, where he began designing his desktop 3D printer, which is both powerful and affordable.
Max Lobowski The friends were able to quickly get an angel investment, with which they launched their first product, the Formlabs Form 1 printer, in 2013. On the Kickstarter crowdfunding platform, they managed to raise almost $ 3 million from more than 2,000 bakers from around the world, who were excited about the new product, which promised to make 3D printing accessible to almost everyone. At that time, there were models of printers on the market using the technology of illumination with a laser beam of photopolymer resin (SLA) with a price of 100 thousand dollars, Formlabs offered a printer for 1500 dollars. The company, of course, faced a lot of difficulties in the production of the first batch, but it managed to ship the printers to all buyers. And even though they were far from perfect, this made it possible to attract round A investments in the amount of 19million dollars and return the "angel" money.
The company then continued to improve its product and create an ecosystem like Apple, which includes 3D printers themselves, consumables (resins for various tasks), software for preparing models for printing, and post-processing equipment. In 2019, the company's turnover reached $100 million, in May 2021 it received $150 million in a round of E from the SoftBank Investment Advisers fund, valuing the company at $2 billion. After that, there was talk of an IPO, which would be an absolutely logical step, since investment funds are planning this in the future for 7-10 years, and this period has already come for investors of the first round.
However, despite high market expectations, Max Lobowski said in an interview with BizJournals that he is in no rush to go public: “We would rather take our time and better prepare to be a great public company… We make more money than all 3D -companies taken together that have gone public with the help of SPAC (a procedure that allows startups to go public by merging with another private company). However, when I look at really large, successful, long-term public projects, which is what we are aiming for, I see that they are on a completely different level in terms of predictability and profitability than we are.” These are serious words, and apparently the head of the company has reason to pronounce them. Most likely, the forecast of the company's capitalization in the region of 4-6 billion dollars with a successful initial offering, which will make it the largest company in the market, because even the result of the veteran and long-term market leader - 3DSystems as of August 2021 is no more than 3.5 billion. dollars.
Unlike the students at Formlabs, Markforged was founded by older guys. However, even here it was not without MIT. MIT alumnus Mark Greg encountered 3D printing while his company was doing a job for the US Navy. Experiments in the field of improving the quality of products led him to the idea of creating a printer that could reinforce the printed model with carbon fiber to make it strong and suitable for use under load.
The company was founded in 2013, and already in 2014 at the Solidworks World exhibition, the startup presented its first product - the Mark One printer, which had two extruders and could reinforce the printed model with nylon, fiberglass and even Kevlar. Later, The Digital Forge, a cloud-based print management platform, was introduced, and already in 2017, MarkForged announced the release of a Metal X desktop metal 3D printer worth $100,000, while competitors' counterparts cost a million. In 2020, the company's turnover amounted to $70 million, and the management decided to bring the company to an IPO using SPAC. The company introduced the concept of additive manufacturing 2.0 to potential investors, allowing the production of finished products rather than prototypes, paving the way for 3D printing to the production of goods. The volume of this market is estimated by experts at 13 trillion dollars.
Based on the Wholers Report, in 2020 the company predicted the growth of the additive technologies market at an average rate of 27%, which means that in the next 8 years from the current 18 billion dollars, the market will grow to 118 billion in 2029 from 10 multiple growth of own revenue up to 700 million dollars already in 2025.
On July 15, 2021, MarkForged was listed on the New York Stock Exchange under the ticker MKFG. The placement was estimated at 2 billion dollars, but a month later the shares lost a little in price, and the current capitalization is about 1.5 billion dollars. The question remains: is it worth buying shares of a company that plans to be unprofitable for at least another 2 years (the company predicts a turnover of about $100 million this year).
On the one hand, there are enough companies on the market trading at even higher multiples, and on the other hand, 3D printing is not yet such a mature technology that one can be sure of the 100% success of exactly the concept that MarkForged offers. In fact, the company itself considers the emergence of new technologies as one of the risks that could undermine its current technological superiority. In general, investors are now positive about the future of 3D printing. They were impressed by how the technology performed in the first, most difficult months of the pandemic, when production chains were disrupted and many transport arteries stopped working. With the help of 3D printing, it was quickly possible to establish the production of urgently needed valves for ventilation, protective masks, adapters and much more. The concept of distributed production immediately turned from a beautiful idea into a real necessity. So, as always, the coin has two sides, but if you are interested in stocks with great potential, you should at least take a closer look at this company and the market of additive technologies in general.
The last one in my story is DeskTop Metal. Formlabs was created by MIT students, Markforged - MIT graduates, DeskTop Metal was created by experienced entrepreneurs Rick Fulop and Johan Mayerberg, as well as 4 (!) MIT professors. Going to the goal, Rick Fulop founded 6 different companies, also headed an investment fund. Johan Maierberg has been a lead engineer for various companies and became the CTO of DeskTop Metal.
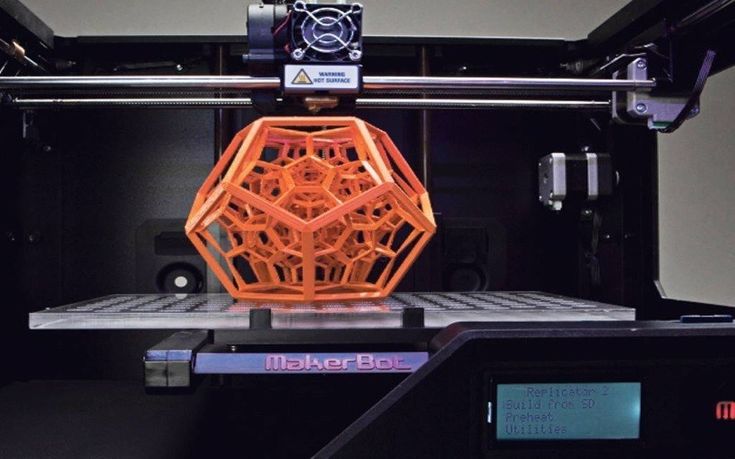
The company entered the IPO on December 10, 2020 under the same SPAC scheme and in its presentation for potential investors outlined the following parameters: planned turnover in 2025 - 942 million dollars, reaching operating profit in 2023, and also indicated that , which plans to spend a significant portion of the proceeds on acquisitions of other 3D printing companies.
Capitalization on the New York Stock Exchange at the time of its IPO on December 10 was a fantastic $6 billion. During the placement, $580 million was raised and the company was assigned the laconic ticker DM. Already in February 2021, the shares rose even more, and the company's capitalization exceeded $8 billion. DM has said it will be the first company in 3D printing history to have a capitalization of over $10 billion. Having received huge funds at its disposal, already in January 2021, DM announced the first takeover deal: the German manufacturer of professional photopolymer 3D printers EnvisionTEC (founded in 2002 and is one of the oldest on the market) was bought for $ 300 million. For me, this choice was not obvious, it is difficult to find something in common between DM and EnvisionTEC and it will be difficult to achieve a significant synergistic effect from this transaction. EnvisionTEC has continued to operate under its own brand as a 100% subsidiary of DM and plans to release a number of new models for its key customers - dental clinics and jewelry companies. Also during this year, several small companies specializing in the production of materials and software were bought. DM expands its patent base due to this and gathers under its wing the best ideas and people. The most high-profile acquisition was the $575 million purchase announced in August of another public company, the American ExOne. Established in 2005 in Pittsburgh, it specializes in the production of industrial 3D printers for creating injection molds from sand and other materials. It is also noteworthy that she managed to commercialize a patent for this technology, issued by MIT back in 1993 year. In this case, we can say that the product lines of DM and ExOne are closer to each other and they have already presented a joint portfolio based on the products of both companies, in which one product complements the other.
It would be logical to assume that DM stock skyrocketed after such high-profile acquisitions, but in reality the opposite happened. Since its peak in February, the shares have fallen 4 times and are now trading at $8 a share, and the capitalization is slightly over $2 billion. Apparently, the first euphoria of investors gave way to a more sober approach to the current results of the company. Perhaps this was influenced by the dissatisfaction of some ExOne shareholders, who considered the sale price of the company unfair and were preparing a class action lawsuit against management in order to block the deal.
Should I buy DM stock now that it has fallen so much, or wait for further decline? I would say that their current level is very comfortable for entry, but, of course, such investments also have a certain risk. This is despite the fact that the company has reported strong first half results, which DM expects to generate over $100 million in revenue this year.
Summing up, I would like to say that a number of stock analysts consider what is happening in the market of additive technologies to be a "renaissance". The market came into motion after the pandemic, which gave everyone hope that the technology was ripe for serious tasks, and that the situation in the industry of 2013-2014 would not repeat itself.