3D printing adjustable wrench
Wrench best 3D printer files・Cults
wrench size sw5.5 up to sw20 // STL File
€1.25 -30% €0.87
Logitech Driving Force GT Clamp Key-wrench
Free
Fallout 4 Inspired - PipeWrench
€3.44
1/2" Socket Holder
Free
FPV Iflight Quad Wrench Sleeve
Free
Stuffing Gland spanner (25mm and 20mm)
€2.41
SLR/DSLR Pointed Spanner Wrench for Camera and Lens
Free
Wrench Rack for Combination Wrench Sets
Free
Impact Gun Trigger Button - Goodyear Racing 1/2" Air Impact
Free
Tech Wrench Staff
€0. 63
1:64 SCALE FIGURES 6 PACK NO6 (CINDY'S GARAGE) GASSLANDS OR HOTWHEELS POSERS
€5.76
Parkside Hex & Torx Set of Wrenches Wall Holder - Storage Organiser
€3.15
1/4" Hex Bit Wrench Adapter
Free
M4 barrel wrench gunsmith wrench delta ring tool airsoft ar-15
€1.85 -10% €1.66
Kenner Vintage Vehicle Maintenance Energizer 8 Tools
€4
Parkside Adjustable Wrench 200mm Wall Holder
€0.55
Handle for 13mm KStools GEARplus ratchet ring open-end wrench, article no.: 503.4213
€2.04
Slice Mosquito Assembly Jig
Free
PISTON MEN
€0. 50
TAP WRENCH M5 M6 M8
Free
Bench Block
Free
NASA space wrench
Free
Gas cylinder wrench 27 mm
€1.70
Ratchet Wrench and 10mm Keychain
Free
Parametric Wrench
Free
Metric Allen Wrench Holder Mount
Free
enfit feeding bag connector wrench
€1.92
Allen wrench rack for Prusa MMU allen wrenches
Free
PRINT IN PLACE : Hex key (Allen key) ratchet
Free
Wrench for a water purifier (Reverse Osmosis filter) resin tank cap
Free
Stanley Workmaster Allen/Hex Wrench Handles
Free
3.
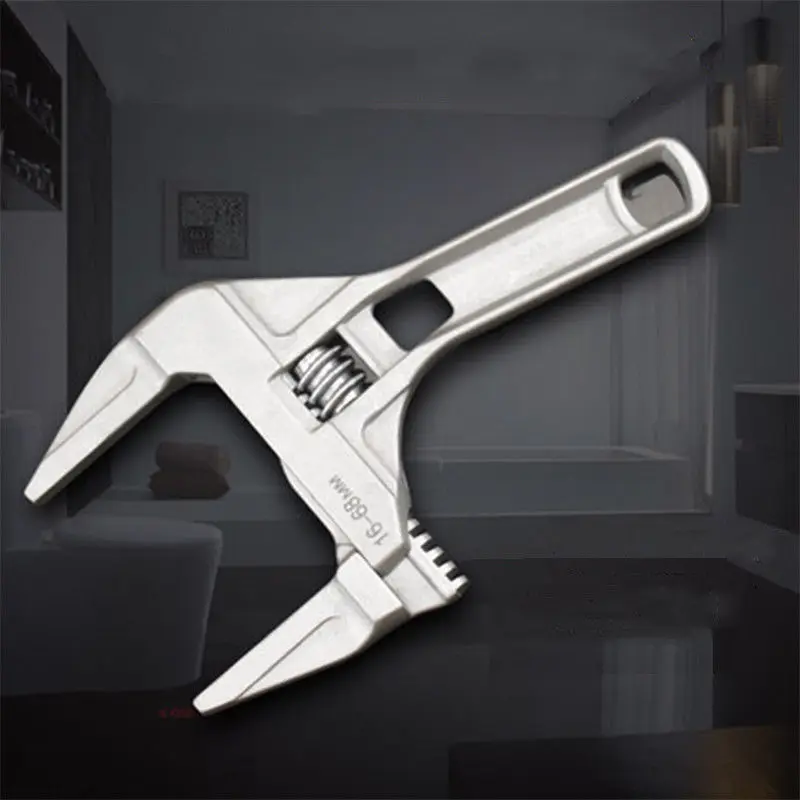
Free
Wrench Set
Free
Triangle key bollard according to DIN 3223
€0.50
Ratchet Wrench Keychain
€1.50 -15% €1.28
Ratchet to Drive Bit Adapter
Free
Mini M3 hex key wrench
Free
Fidget Spinner Spinner Hand Toy
Free
Fully assembled more 3D printable wrench (customizable)
Free
Bike toolkit socket holder repair
Free
Arcade Button Wrench
Free
Tweezers/Paperclip bender
€1. 15
Keychain socked wrench for racing drone propeller
Free
Mixed wrench
Free
32mm wrench / spanner
Free
Assemblable tool holder blocks
Free
Torque wrench
Free
microscope
Free
3D printing hands on: Attempting to print a NASA wrench
It costs about a thousand dollars to loft a pound of anything into space. Scientists, astronauts, and project managers are therefore understandably careful about what they choose to send to the International Space Station.
Years of careful planning precede any launch and determine the contents of any launch payload. But as we all know, plans change when they encounter reality. So what happens when an astronaut on the space station needs something that didn't get packed into a shuttle payload?
They make do. The most famous example of the make-do spirit was the Apollo 13 mission, where - after an oxygen tank exploded in the command module - the astronauts had to survive in the lunar module. To do so, they had to build a carbon dioxide scrubber adapter from found parts, which consisted of the cover of the flight manual, duct tape, a pair of socks, and various other components.
While emergencies will undoubtedly still happen in space, and creativity and resourcefulness will still be necessary, NASA researchers have been working on an approach that could provide space station astronauts with a supply of objects, tools, and components using 3D printing.
This is an extremely powerful idea. Think about the general-purpose computer. Once it was possible to create one device that could run many different programs, the computer because an enormously flexible machine. It could be built and installed well before all of its uses were defined or even discovered. When a new program was needed, that program could be coded, and the same physical piece of machinery could run everything from inventory replenishment calculations to plotting missile trajectories - which have reached their cultural culmination in the computation of the flight path of small birds aimed at clusters of small, green pigs.
The general purpose computer is a single machine that can run a wide variety of programs. Likewise, a 3D printer is a single machine that can produce a wide variety of objects.
Scientists at NASA have seen the potential. This one machine can live on the space station and generate an almost infinite variety of objects, tools, and parts. Instead of, for example, waiting for the next shuttle mission to loft a special-purpose wrench to the space station, engineers can just email an .STL file to an astronaut on the station, who can print it out and put it to use.
In fact, there is a 3D printer on the space station, made by the firm Made In Space, Inc. The printer is a fused deposition modeling (FDM) printer very similar to the desktop 3D printers we've been using here in the DIY-IT 3D printing discovery series. In fact, one of the test objects printed on the station's 3D printer was just such a wrench, a small socket wrench shown below.
NASA has even made plans of the wrench, in STL format, available online. So, I decided to download the file and give it a run in my MakerBot Replicator. A special shout-out of thanks goes to MakerBot for providing the printer for our DIY-IT discovery series.
Printing the wrench
Printing the wrench turned out to be a very simple project. All I did was load the wrench into my slicing program and send it to the printer. I did, however, run into a number of problems creating an actual working unit, but those problems were limitations in my tools, not in the file or the 3D printing concept.
I have a printer that is designed to print polylactic acid-based plastic, otherwise known as PLA. PLA is biodegradable and based on corn starch. It's a reliable printing material and has the benefit of not only being good to the planet, it doesn't generate the acrid plastic smell that acrylonitrile butadiene styrene (ABS) plastic is known for.
While PLA is an ideal printing material, it is a little more brittle than ABS. There are ABS printers out there, but they often require a heated build plate and an enclosed printing area. My printer has neither. If you want a good example of something created from ABS, think of Lego bricks. There are roughly 400 billion Lego bricks in the world, and all were made from ABS.
NASA's space station 3D printer is also designed to print ABS, so the wrench design was specifically intended for an ABS printer. I tried it on my PLA printer.
I disregarded the design specs in another way as well. I decided to use the slicing defaults of MakerBot desktop, which included setting a 10 percent infill. Infill is the amount of plastic used to fill solid spaces. Rather than filling the entire space with plastic, various infill percentages generate diamond or honeycomb shapes inside the object. These often provide good strength and both reduce the amount of plastic used and the time used to generate the print.
My first print used 10 percent infill, so as soon as I tried to wrench anything with my first printed wrench, it broke.
My second attempt was unsuccessful as well, because after a little while, the print started to warp, lifting up off the print base. This is because, as layers cool, there is a difference in temperature between the lower layers (which are cool) and the upper layers which are warm. The difference tends to pull the print up off the printing base, and so my second wrench print, this time printed with 100 percent infill (or completely solid) failed due to warping.
Given how long it takes for prints to complete (roughly five hours each), I ran out of time after two prints. You can watch my video at the beginning of the article to see the process in more depth.
Even though the project failed for me, I learned some valuable lessons. I gained a tangible lesson about the strength of the plastic and the relationship between infill percentage and strength. I got a chance to experiment with an actual tool design intended for the space station. I learned a bit about how warping takes place as you increase the infill percentage - and I learned more about build plate adhesion. Finally, I learned that even though this project didn't succeed in the time frame I had available, the discovery process is just that, all about discovery. By attempting this project, I learned a lot and had fun doing it.
If you decide to try making the wrench, especially if you do it with ABS, please let me know how it worked for you in the comment area below.
By the way, I'm doing more updates on Twitter and Facebook than ever before. Be sure to follow me on Twitter at @DavidGewirtz and on Facebook at Facebook. com/DavidGewirtz.
astronaut needs a wrench, NASA sends a model to print it / Sudo Null IT News This is not the first attempt at 3D printing, but finally Zero-G has a practical use. Usually, it can take months from requesting a tool for the ISS to arriving on a space truck, but here it was made on site within a few tens of minutes.
The Zero-G 3D printer was delivered to the ISS on September 22 as part of the two tons payload of the SpaceX Dragon unmanned spacecraft. The first item was printed on November 24th. It was a trial model just to test the operation of the printer - a small panel with the name of the manufacturer of the Made In Space device and the NASA logo.
The scenario when something breaks on a manned station somewhere far in space, and the astronaut only has to replace the broken part with a printed sample based on a model received from Earth or stored on a computer hard drive, is very attractive. As part of the Future Engineers competition, many more models will be printed on the ISS.
At least 21 items have already been printed, their shape is shown above. All of them will return to Earth to study the effects of long-term microgravity on the 3D printing process - they will be compared with similar samples made under the gravity of our planet. The study will improve the future performance of 3D printers in space.
Made in Space overheard Wilmore mention the need for a wrench over the radio. So they created a model of it and sent the file to NASA, which in turn sent the data to the ISS.
Made in Space co-founder Mike Chen details the simple process of sending items to the ISS "by email". On Earth, a model is created, usually this is done in the Autodesk Inventor package. The file is converted to the G-code format available for the 3D printer.
The files are then sent from the office in Moffett Field (California) to NASA. The space agency, in turn, sends data to the ISS from the operations support center in Huntsville. The item is crafted in layers in the Microgravity Science Glovebox on board the station.
Zero-G by Made In Space
3D printing can become an important part of expeditions to other planets, when just waiting a few weeks or months for the next supply truck will not work - the device will be millions of kilometers from home, which including excludes real-time audio and video communication. If an object is suddenly needed on board a spacecraft, station or in a space colony, then it will have to be made there.
Next year, Made In Space plans to replace the 3D printer with a larger model. The European Space Agency will also launch its own printer in 2015.
astronaut needs a wrench, NASA sends a model to print it Adjustable wrench on a 3d printer
A ratchet wrench has been 3D printed aboard the International Space Station. This is not the first attempt at 3D printing, but finally Zero-G has a practical use. Usually, it can take months from requesting a tool for the ISS to arriving on a space truck, but here it was made on site within a few tens of minutes.
The Zero-G 3D printer on the ISS on September 22 is among the two tons of SpaceX Dragon unmanned spacecraft payload. First class November 24th. It was a trial model just to test the operation of the printer - a small panel with the name of the manufacturer of the Made In Space device and the NASA logo.
The scenario when something breaks on a manned station somewhere far in space, and the astronaut only has to replace the broken part with a printed sample based on a model obtained from the Earth or stored on a computer hard disk to fix, is very attractive. As part of the Future Engineers competition, many more models will be printed on the ISS.
At least 21 items have already been printed, their shape is shown above. All of them will return to Earth to study the effects of long-term microgravity on the 3D printing process - they will be compared with similar samples made under the gravity of our planet. The study will improve the future performance of 3D printers in space.
Made in Space overheard Wilmore mention the need for a wrench over the radio. So they created a model of it and sent the file to NASA, which in turn sent the data to the ISS.
Made in Space co-founder Mike Chen a simple process for sending items to the ISS "by email". A model is created on Earth, usually done in the Autodesk Inventor package. The file is converted to the G-code format available for a 3D printer.
The files are then sent from the office in Moffett Field (California) to NASA. The space agency, in turn, sends data to the ISS from the operations support center in Huntsville. The item is crafted in layers in the Microgravity Science Glovebox on board the station.
Zero-G by Made In Space
3D printing can become an important part of expeditions to other planets, when just waiting a few weeks or months for the next supply truck will not work - the device will be millions of kilometers from home, which also excludes real-time audio and video communication . If an object is suddenly needed on board a spacecraft, station or in a space colony, then it will have to be made there.
Next year, Made In Space plans to replace the 3D printer with a larger model. The European Space Agency will also launch its own printer in 2015.
Friends, a little introduction!
Before reading the news, let me invite you to the largest community of 3D printer owners. Yes, yes, it already exists, on the pages of our project!
By engraving "do not copy" on the keys of high security locks, Schlage locks wanted to create another obstacle for those who would like to make a copy of a key that not everyone can copy anyway. Instead, there were people who took this inscription as a challenge.
At the Def Con hacker conference on Saturday, MIT students David Lawrence and Eric Van Albert plan to release code that allows anyone to create a 3D-printable computer model of any Primus key, despite the manufacturer's best efforts to prevent copying specially designed keys. Armed with a conventional scanner and their software, they were able to create accurate computer models of the keys, which they then printed in titanium or nylon on online 3D printing services such as Shapeways and i.Materialize. You can learn more about such services at.
Schlage's Primus locks are positioned as locks for use in places where a high level of security is required: Schlage advertised these locks as being used in government offices, healthcare centers and prisons. Part of this high level of security is due to the two lanes, one on the edge of the key and one in the middle. Each of these two tracks has its own set of locking pins in the lock. Mark Weber Tobias, one of the world's most famous lockpicking experts, wrote that he uses Primus locks both at home and at work.
Of course, Lawrence and Van Albert's program does not allow you to open any doors locked with one of these locks. It just allows its users to easily copy a key that was previously very difficult to forge. However, the same MIT students insist that it is possible to get a working copy of the key without ever touching the original. It has long been no secret that you can create an exact copy of the key even on the basis of photographs, sometimes even from photographs taken at a distance of many tens of meters. (See, for example, the Sneakey project). By studying user manuals and Schalge patents, Lawrence and Van Albert learned to recognize two codes in the form of keys: a 6-digit code that corresponds to cutouts on the edge of the key, and a 5-digit code encrypted by cutouts on the key plane. Having recognized and put these codes into the program, you can create a copy of the key.
As Lawrence says:
All you need is a friend who works at the establishment who can take a picture of the key, and it could even be a picture of the key hanging from a key ring on someone's belt. Forgery of keys becomes like pirated distribution of films: someone has to get this information, however, then everyone can use this information.![]()
Although we are talking about Primus locks, Lawrence and Van Albert argue that the same technique can be applied to any high-security lock:
We want to convey to people that this is easy to do with any lock, regardless of its price tag. As for the Primus locks, it didn't take that long. In the future, it will be easy to find models on the Internet for making copies of almost any type of key.
Lawrence and Van Albert refer to a recent story with published photographs of New York's fire elevator keys, which give access to many of New York's electrical panels, elevator control panels, and subway entrances. These photos were published in a New York newspaper last fall. It is quite ironic that the newspaper article was written to warn the public that these keys, handed out to the city's electricians and firefighters, could easily fall into the wrong hands, however, a high-resolution photo of the keys themselves made it possible for everyone to print a copy for themselves. these same keys on a 3D printer. The editors quickly realized their mistake, and immediately removed the photo from their website, but it was too late, and the images of the keys managed to spread throughout the network.
I must say that this is not the first case of printing a copy of the key on a 3D printer. In 2011, an Apple engineer wrote a program that allows, based on key measurements, to create a three-dimensional model suitable for printing on 3D printers. True, then it was about ordinary keys, which are not difficult to make in any of the many special shops.
Last year, at the HOPE hacker conference, a hacker known as "Ray" showed that he could 3D print a working copy of the keys to highly secure handcuffs. Usually access to handcuff keys is limited, but they are all identical so that one policeman can remove the handcuffs fastened by another policeman, which makes this system quite vulnerable, because now it is possible to make a copy of these small keys for yourself, and hide it on your body, so that you can free yourself if necessary.
As for the problem with the Schlage keys, Lawrence and Van Albert have no easy solution. They believe that in the age of 3D printing, the concept of high-security mechanical locks will be outdated. Instead of mechanical locks in places where a high level of security is required, electronic locks with unique cryptographic keys, which are harder to counterfeit, should be used.
We hope that if we show the world that any mechanical lock can be bypassed by simply downloading a few numbers from the Internet, the transition to stronger security methods will happen faster, says Van Albert.
We recently reported that when the patents for laser sintering technology expire in 2013, there will be low-cost consumer 3D printers using this technology. But this technology allows you to print metal! And if now, in order to print a key on a 3D printer, you will most likely have to order printing from large companies, then in a couple of years everyone will be able to buy a metal-printing 3D printer and print as many copies of keys as they like.
Recently, 3D printers have become widespread in the world, they print the most incredible things. One of the business ideas that we want to offer you today is related to 3D printing, namely the printing of house keys on a 3D printer. This business idea belongs to the American company KeyMe. So far, this company is developing its business only in New York, but soon they plan to enter the world market with their startup.
How it works
At first glance, everything looks quite simple - you need to take a couple of photos of your key on both sides (preferably put the key on a white sheet of paper), save them to your smartphone, then register an account in the KeyMe service and if you suddenly lose the key, then order a 3D printing service.
Is it safe?
The founders of KeyMe assure that the service is protected in the best possible way and their customers have nothing to fear. In principle, they can be trusted, because it will not be possible to register an account in KeyMe just like that, because. it is tied to the bank card and the place of residence of the owner , and you can store the key photo in your smartphone or in the cloud storage provided by the company. Quite an impressive level of security, isn't it?
Where can I print the key
If you have your own 3D printer, you can print the required key, completely free of charge, simply by using The KeyMe App, which can be downloaded from Google Play or the App store.
Well, if you don't have your own printer yet, you can order a duplicate key service and the courier will bring your key within an hour. You can also print the key yourself at special kiosks that are installed throughout New York (there are about 100 of them in the city). In such a kiosk, you can print the key in just a couple of minutes, but you will need to pass fingerprint authentication. By the way, access to data only after confirmation with a fingerprint is also one of the levels of protection that KeyMe is proud of.
Using KeyMe you can print the most unusual keys
In addition to simple house keys, you can print, for example, a car key, although such a service will cost more - from 20 to 60$.