3D printing acrylic filament
Why You Should Try Acrylic PMMA Filament – And How to Print it
Are you looking to expand the horizons of your 3D printing? Do you feel that your usual go-to 3D printing filaments are constricting the creativity of your designs?
Maybe you simply need a stronger material that can withstand higher temperatures and produce results that range from translucent to nearly transparent.
If so, PMMA filament may be the solution that you’re looking for.
Let’s take a look at PMMA 3D printing filament, what it is, its benefits and stats, and how it compares with similar transparent 3D printing filament. Then we’ll cover some of the best ways to get great results when printing with it.
What is PMMA Filament?
PMMA, or polymethyl methacrylate, is a strong, lightweight and transparent thermoplastic.
Also known as acrylic, PMMA filament is used commercially as a shatter-resistant alternative to glass under the trade names Plexiglas, Lucite and Perspex.
It has good impact strength, significantly higher than glass, but lower than some stronger and more expensive materials like polycarbonate.
It has less than half the density of glass, but has comparable clarity and UV absorption properties. It finds commercial applications as a glass substitute when extremely high impact strength isn’t necessary, but weight, transparency and cost are issues.
As a result, you’ll find PMMA in automobile headlights, commercial aquariums, ice rink protective glass and more.
We feel it’s definitely an underrated material.
There are several important benefits to using PMMA as a 3D printing material. To begin with, it has a high impact resistance which makes it tough and durable. It’s also extremely rigid with very little flexibility.
So, if you’re going to need to print an object that will stand up to a certain amount of stress without bending or deforming, then PMMA 3D printer filaments are a strong contender.
Its high impact strength means that anything that you print using PMMA will not as likely break if dropped or handled roughly. Think glass, only stronger and less fragile.
Additionally, once printed, PMMA diffuses light wonderfully. Treated right, it can give marvelous results that range from translucent to nearly transparent filament.
In short, here are the main PMMA 3D filament properties:
- Clear, thermoplastic acrylic
- Strong, rigid, lightweight, impact resistant
- Available in several colors, including neutral, red, blue and green
- Acetone soluble
- Generally, not food safe
- PMMA filament temperature prints from 245C to 255C
- Recommended printing bed temperature: from 100C to 120C
A look at the data stats confirms the strength of PMMA. PMMA has a specific gravity of 1.20 g/cm³. This makes it comparable in density to PLA and about one-fifth denser than ABS.
PMMA has a Rockwell hardness of R 105, making it comparable in hardness to ABS and significantly harder than PLA.
However, strength is where PMMA really shines over plastic filament materials. It has a maximum tensile strength of 12,100 psi (83.42 MPa). Compare that to 6500 psi (44.81 MPa) for ABS and 8383 psi (57.8 MPa) for PLA. It also has a maximum compression strength of 17,000 psi (117.21 MPa). By way of comparison, the maximum compression strength of ABS is 6750 psi (46.54 MPA).
With PMMA you have a dense, hard printing material that gives you some significant advantages in the area of strength. Specifically, PMMA is able to handle various stress forces better than plastic filament. This makes it a natural fit for any application that calls for rigidity and inflexibility.
Additionally, the translucency/transparency of PMMA makes it the perfect solution where a clear part or object is desired. Clarity and strength in one package make PMMA a filament that can be a great contender in your 3D printing arsenal.Rigid Ink 1.75mm PMMA Filament spool
If you’re looking for translucent or clear materials, the ones that are available are PETG, Polycarbonate, Natural PLA and ‘Clear’ ABS. Although, clear ABS uses an additive so it’s more likely translucent filament when printed.
Now, before we go on to take a look at some of the best practices to use when 3D printing with PMMA, we need quickly talk about the use of PMMA in investment casting.
PMMA in Investment Casting
Investment casting, as you may know, is a process where a pattern of a part or object is made out of an easily melted material, traditionally wax, and surrounded by a ceramic mixture to create a mold. Molten alloy metal is then poured into the mold, melting and displacing the wax. This forms a perfect metal replica of the wax part or object.
The problem with wax patterns is that they are formed using injection molding and typically carry a five-figure price tag and require a two-month lead time to produce. 3D printing has revolutionized the investment casting process by slashing the time and cost of producing patterns.
Read more: lost wax casting in 3D printing
Using a 3D printer and a material like PMMA, a pattern of an object can be completed in under a week for a couple of hundred dollars or pounds, and with potentially greater detail than is available using wax.
Upon contact with the molten metal, the PMMA burns to ash, leaving very little residue behind. If you do any type of metal casting using a mold, you owe it to yourself to try PMMA as a pattern material.
How to 3D print with PMMA filament
If you’re wondering how to 3D print with PMMA, it all comes down to keeping an eye on a couple of things.
Temperature
PMMA will print anywhere from 245°C to 255°C. However, at lower temperatures, the flow can be inconsistent with blobbing occurring.
At higher temperatures, at or near 250°C, the flow becomes consistent and printing is easier.
You’ll want to heat your printing bed to prevent warping. A temperature of around 100°C is optimal. There can be some shrinkage with PMMA during cooling. Because of this, you might want to consider enclosing the printing chamber to better regulate cooling speed with transparent 3D printer filament.
Speed
If you’re looking to maximize the transparency of PMMA, then you want to keep an eye on your printing speed and printing temperature.
Play around with your PMMA filament settings to get the clearest results. As we discussed, PMMA can flow inconsistently and blob at lower temperatures. These inconsistencies can produce bubbling and unevenness in the print line.
These inconsistencies, as they layer throughout the object being printed, eventually begin to reduce the clarity of the material, turning it from transparent to translucent. In extreme cases, the object being produced can even become opaque. Higher printing temperatures reduce inconsistent flow.
Optimal PMMA filament print speeds are:
Slower printing speeds, 30 mm/sec or less, and ensuring your printer’s belts are tight and there’s no vibration on the printer allow for proper material alignment. All of these things lead to increased clarity in the object you are printing.
We want to make sure that your printing jobs come out right the first time, every time. After all, ruined print jobs waste time and materials. That’s why low-quality print filament is a false economy. It may cost you less up-front, but ends up costing you much more in time and the material you lose from failed prints.
Other articles you may be interested in:
- Best 3D printer filament: buyer’s guide and all filament types compared
- 3D printer materials compared
- PLA Filament guide
PMMA: 3D Printing Materials Overview | by Zmorph SA
PMMA is not only a transparent 3D printing filament but also exhibits some interesting features that make it a great choice for UV resistant models and casings. Read below to learn about PMMA.
ZMorph VX & 3D printed PMMA model.PMMA stands for polymethyl methacrylate. It’s a thermoplastic material featuring scratch and impact resistance, high tensile and flexural strength, and UV tolerance. PMMA is transparent and tough and can be used in many ways in 3D printing. More on applications later.
PMMA is also called acrylic or acrylic glass because it resembles the traditional glass, but thanks to its properties it can be successfully 3D printed. It’s half as dense as glass and its impact strength is much lower, but it’s lighter, cheaper, and maintains transparency, which can be beneficial in certain instances.
PMMA is one of the less popular 3D printing filaments and is not as easy to print as PLA or ABS. That being said, you can successfully create PMMA models using ZMorph VX All-In-One 3D Printer if you follow these tips.
By default, Voxelizer software doesn’t show PMMA preset in 3D printing settings. You can add it from the filament library, though. Click the icon with a filament and find the PMMA preset (see the picture below).
Voxelizer screenshot showing filament settings.Other settings such as durability or infill depend on your own preferences. The more infill you use the less transparent your model will be.
PMMA needs adhesive glue to stick properly to the printing bed. Consider an adhesive agent if the first layer fails.
The printing temperature from PMMA ranges between 230 and 250ºC and the bed temperature of the 3D printer should be set to 60ºC. Low temperature may cause blobs that distort the material transparency.
Because PMMA requires a stable 3D printing temperature it’s best to close the plastic covers of ZMorph VX. Printing with open covers may result in defects in your model.
Feel free to mingle with the printing speed settings. Slower 3D printing usually results in better layers and material alignments thus making the PMMA more transparent.
3D printed light diffusor made on ZMorph VX.Because of the transparency, PMMA has several specific applications. It’s used for optical apparatuses, UV resistant models, chemical equipment, lamps, casings and many more.
Below you can see a 3D printed sample of PMMA model. It’s a lighting diffuser that can be attached to your photo camera lamp. It was 3D printed using ZMorph VX and PMMA filament.
3D printed PMMA light diffusor.3D printed PMMA light diffusor.3D printed PMMA light diffusor.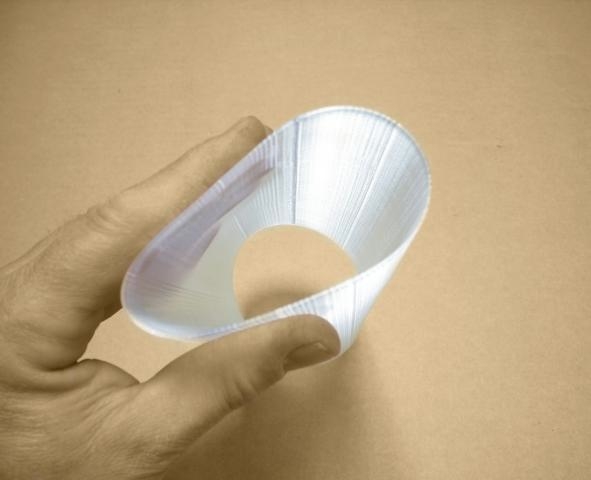
Melted 3D printing filaments such as PMMA emit fumes that may cause dizziness and are unhealthy to breathe in. Always remember to ventilate the room with the 3D printer properly and avoid working in the nearest scene. In fact, it’s best to avoid being in the same room while the machine is 3D printing to minimize the amount of fumes you may inhale.
ZMorph VX operates on high temperatures, the Single Extruder heats up to 250ºC, and you may burn yourself easily if you touch the machine. Wait until the unit cools down before taking out your prints.
Remember about proper ventilation while 3D printing.In case you missed it, we’ve recently published ZMorph Materials Library. A comprehensive, 100-pages document on almost 50 materials available for ZMorph VX Multitool 3D Printer. Learn about their most important features and applications, and discover the technical data.
3D printing (exclusive) to order in Moscow
Description
Branding and advertising are among the widest applications for 3D printing. Most often, additive technologies are used in the manufacture of souvenirs, but little by little this approach is being adapted to the production of large forms: signs, plates, signs. 3D printing is difficult to compete with traditional methods in these areas, but it successfully complements laser cutting and milling where it is difficult or impossible to use sheet materials.
Benefits of 3D printing in advertising
- Simplify production. Many manipulations are performed manually or with the help of expensive equipment (for example, cutting and gluing side plates). The 3D printer immediately prints the body of the product, you only need to supplement it with the front part.
- Combination of materials. The equipment can be filled with two threads of different textures, which gives an original effect. The addition of UV-resistant filaments saves on protective treatment of the structure and extends its service life.
- Minimization of the human factor.
The result of the work does not depend on the skill and well-being of the employee, but on the quality of raw materials and printing.
- Making complex shapes. Volumetric structures with a pronounced relief are difficult to make from classic sheet materials. 3D printing provides almost unlimited possibilities for design imagination.
Technologies used
Our production arsenal includes a Diamond-Tech 640 x 640 3D printer that works with PLA and PETg filaments. The equipment with the same success copes both with printing miniature letters up to 5 cm high, and with the production of three-dimensional structures up to 0.6 m high. Among its features:
- accurate calculation of the cost of work and the timing of the order - the printer immediately indicates the required volume of polymer thread and the duration of the process;
- the ability to print beveled sidewalls - the side parts of the structure with different areas of the front and back;
- alternate printing option, which uses threads of different colors;
- compatible with many file formats, including ARTCUT, STL, CDR and SVG.
Using Diamond Tech to mold the rims, two to five light strips can be obtained in a variety of combinations. The palette includes 3 opaque options and over 50 translucent shades. This set is sufficient for the production of both classic letters and original designs - for example, signs with luminous sides or contour lighting.
Liquid acrylic 3D printing
The innovative 3D printing technology is best complemented by another modern method based on the use of liquid acrylic. Volumetric letters are printed on a Diamond Tech printer, the back walls are produced by milling, and the front part is treated with a special composition.
How does this happen:
- The workpiece prepared for processing is fixed on one of the tables of the drying platform. The working field is presented in two standard sizes: 1200*1500 mm with six Philips UV lamps and 1500*2340 mm with twelve lamps included.
- After filling the tank with raw materials, the autosampler is included in the process.
Based on the given parameters, he measures the required volume of liquid acrylic and distributes it over the front surface of the workpiece.
- Under the influence of ultraviolet lamps, liquid acrylic takes a solid form. The curing of the composition without color pigment takes about 60 minutes. If there is a color pigment in the solution, the time increases to 80 minutes.
The flooded front side perfectly keeps on the surface without additional fastening to the sidewalls. Good adhesion is ensured by the material of the filaments used in the 3D printer and the special paint used to process the inside of the aluminum profile. The latter also provides a uniform distribution of illumination over the entire area of the structure.
Advantages of Liquid Acrylic and Diamond Tech
The technology minimizes the impact of the human factor, speeds up the production process and eliminates the appearance of defects. When cured, liquid acrylic forms a smooth and durable surface without chips or other defects. Ready-made signs are only slightly inferior to neon signs in terms of the spectacular glow.
The milky color of liquid acrylic looks much brighter than the traditional sheet version due to the addition of translutens. To create different shades, the manufacturer offers more than 15 options for pigment pastes, which are mixed in different proportions. The required color scheme is selected according to the factory formula, which eliminates deviations from the specified color.
You can leave an application for the manufacture of a sign using 3D printing technology by calling +7 (495) 645-21-70 in Moscow.
Video
3d printing of volume letters, filling with liquid acrylic
Interior sign with three-dimensional letters - Calibri
25th anniversary of Apricot company
FDM/FFF Consumables
FFF technology has many advantages, including the relative simplicity of the design of printers and the affordability of both devices and consumables. Moreover, the range of materials is perhaps the widest among all available technologies. As a rule, thermoplastics are used for printing, but there are exceptions - composite materials containing various additives, but based, again, on thermoplastics. In this section, we will try to talk about the most widely used materials in more detail, starting with the most popular types.
- 1 Polylactide (PLA)
- 2 Acrylonitrile butadiene styrene (ABS)
- 3 Polyvinyl alcohol (PVA)
- 4 Nylon
- 5 Polycarbonate (PC)
- 6 High density polyethylene (HDPE)
- 7 Polypropylene (PP, PP)
- 8 Polycaprolactone (PCL)
- 9 Polyphenylsulfone (PPSU)
- 10 Polymethyl methacrylate (Acrylic, plexiglass, acrylic, PMMA)
- 11 Polyethylene terephthalate (PET, PET)
- 12 High impact polystyrene (HIPS)
- 13 Wood Simulators (LAYWOO-D3, BambooFill)
- 14 Sandstone Simulators (Laybrick)
- 15 Metal Simulators (BronzeFill)
Polylactide (PLA, PLA)
Polylactide is one of the most widely used thermoplastics due to several factors. Let's start with the fact that PLA is known for its environmental friendliness. This material is a lactic acid polymer, which makes PLA a completely biodegradable material. The raw materials for the production of polylactide are corn and sugar cane. At the same time, the environmental friendliness of polylactide causes its fragility. Plastic easily absorbs water and is relatively soft. As a rule, PLA models are not intended for functional use, but serve as designer models, souvenirs and toys. Few practical industrial applications include the production of food packaging, drug containers and surgical sutures, as well as use in bearings that do not carry high mechanical loads (for example, in modeling), which is possible due to the material's excellent slip coefficient.
One of the most important factors for 3D printing applications is the low melting temperature of only 170-180°C, which contributes to relatively low power consumption and the use of inexpensive brass and aluminum nozzles. As a rule, extrusion is carried out at 160-170°C. At the same time, PLA solidifies quite slowly (glass transition temperature is about 50°C), which should be taken into account when choosing a 3D printer. The best option is a device with an open case, a heated work platform (to avoid deformation of large models) and, preferably, additional fans to cool the fresh layers of the model.
PLA has low shrinkage, i.e. loss of volume on cooling, which helps to prevent warping. However, shrinkage has a cumulative effect as the dimensions of printed models increase. In the latter case, the build platform may need to be heated to evenly cool the printed objects.
The cost of PLA is relatively low, which adds to the popularity of this material.
Acrylonitrile butadiene styrene (ABS)
ABS is perhaps the most popular thermoplastic used in 3D printing, but not the most common. This contradiction is explained by certain technical difficulties that arise when printing ABS. The desire of craftsmen to use ABS is determined by the excellent mechanical properties, durability and low cost of this material. In the industry, ABS plastic is already widely used: the production of car parts, cases of various devices, containers, souvenirs, various household accessories, etc.
ABS plastic is resistant to moisture, acids and oil, has a fairly high temperature resistance - from 90°C to 110°C. Unfortunately, some types of material are destroyed by direct sunlight, which somewhat limits the application. At the same time, ABS plastic is easy to paint, which allows you to apply protective coatings on non-mechanical elements.
Despite a relatively high glass transition temperature of around 100°C, ABS has a relatively low melting point. Actually, due to the amorphous nature of the material, ABS does not have a melting point, as such, but 180 ° C is considered an acceptable temperature for extrusion, which is on the same level as the above-described PLA. The lower temperature spread between extrusion and glass transition allows ABS to cure faster than PLA.
The main disadvantage of ABS plastic can be considered a high degree of shrinkage during cooling - the material can lose up to 0.8% of its volume. This effect can lead to significant deformations of the model, twisting of the first layers and cracking. To combat these unpleasant phenomena, two main solutions are used. First, heated work platforms are used to help reduce the temperature gradient between the lower and upper layers of the model. Secondly, ABS 3D printers often use closed housings and control of the background temperature of the working chamber. This makes it possible to maintain the temperature of the applied layers at a level just below the glass transition threshold, reducing the degree of shrinkage. Full cooling is carried out after receiving the finished model.
The relatively low stickiness of ABS may require additional bonding aids such as adhesive tape, polyimide film, or applying a solution of ABS in acetone to the platform just prior to printing. For more information on how to avoid warping, see How to Avoid Warping 3D Printed Models.
While ABS does not pose a health risk at room temperature, heating plastic releases acrylonitrile fumes, a poisonous compound that can irritate mucous membranes and cause poisoning. Although the amount of Acrylonitrate produced in small scale printing is negligible, it is recommended that you print in a well ventilated area or use an exhaust hood. It is not recommended to use ABS plastic for the production of food containers and utensils (especially for storing hot food or alcoholic beverages) or toys for small children.
The good solubility of ABS in acetone is very useful, as it allows large models to be produced piece by piece and then glued together, greatly expanding the capabilities of inexpensive desktop printers.
Polyvinyl alcohol (PVA)
Polyvinyl alcohol is a material with unique properties and special applications. The main feature of PVA is its water solubility. 3D printers equipped with dual extruders have the ability to print models with PVA support structures. Upon completion of printing, the supports can be dissolved in water, leaving a finished model that does not require mechanical or chemical roughening. Similarly, PVA can be used to create water-soluble master patterns for molds and molds themselves.
The mechanical properties of PVA are quite interesting. At low humidity, plastic has high tensile strength. With increasing humidity, strength decreases, but elasticity increases. The extrusion temperature is 160-175°C, which allows the use of PVA in printers designed for printing with ABS and PLA plastics.
Since the material easily absorbs moisture, it is recommended to store PVA plastic in dry packaging and, if necessary, dry before use. Drying can be done in a pottery kiln or an ordinary oven. As a rule, drying of standard coils takes 6-8 hours at a temperature of 60-80°C. Exceeding 220°C will cause the plastic to decompose, which should be taken into account when printing.
Nylon
Nylon is attractive due to its high wear resistance and low coefficient of friction. Thus, nylon is often used to coat friction parts, which improves their performance and often allows them to function without lubrication. Following the widespread use of nylon in industry, additive manufacturing has also become interested in the material. Attempts to print with nylon have been made almost since the early days of FDM/FFF technology.
In reality, there are several types of nylon produced by different methods and with slightly different characteristics. The most famous is nylon-66, created by the American company DuPont in 1935. The second most popular option is nylon-6, developed by BASF to circumvent the DuPont patent. These two options are very similar. In terms of 3D printing, the main difference is the melting point: Nylon-6 melts at 220°C, while Nylon-66 melts at 265°C.
Many hobbyists prefer to use commercially available nylon threads such as trimmer wire. The diameter of such materials often corresponds to the diameter of standard FFF materials, which makes their use tempting. At the same time, these products are usually not pure nylon. In the case of trimmer rods, the material consists of nylon and fiberglass for an optimal combination of flexibility and rigidity.
Fiberglass has a high melting point, and therefore printing with such materials is fraught with high nozzle wear and plugging.
Recently there have been attempts to commercially develop nylon-based printing materials specifically for FDM/FFF applications, including Nylon-PA6 and Taulman 680. These grades are extrudable at 230-260°C.
Since nylon readily absorbs moisture, store consumables in vacuum packaging or at least in a container with water-absorbent materials. A sign of excessively damp media will be steam escaping from the nozzle during printing, which is not dangerous, but may degrade the quality of the model.
When printing with nylon, it is not recommended to use a polyimide desktop coating as the two materials fuse together. As a coating, you can use adhesive tape with wax impregnation (masking tape). The use of a heated bed will help reduce the possibility of deformation of the model, similar to printing with ABS plastic. Due to the low coefficient of friction of nylon, extruders with studded feeders should be used.
The nylon layers have excellent adhesion, which minimizes the chance of delamination of models.
Nylon is difficult to bond, making it difficult to print large multi-piece models. Alternatively, fusion of parts is possible.
Since nylon can release toxic fumes when heated, we recommend that you print in a well-ventilated area or use an exhaust fan.
Polycarbonate (PC)
Polycarbonates are attractive due to their high strength and toughness, as well as resistance to high and low temperatures.
The potential health risk of printing is worth noting: the toxic and potentially carcinogenic compound bisphenol A is often used as a raw material. .
The extrusion temperature depends on the printing speed to avoid cracking, but the minimum temperature at 30mm/sec can be considered as 265°C. When printing, the use of polyimide film is recommended for better adhesion to the desktop surface. The high susceptibility of polycarbonate to deformation requires the use of a heated platform and, if possible, a closed housing with heating of the working chamber.
Polycarbonate is highly hygroscopic (easily absorbs moisture), which requires storage in dry conditions to avoid the formation of bubbles in the applied layers. For extended printing in humid climates, even the print spool may need to be stored in a moisture-proof container.
High Density Polyethylene (HDPE)
Arguably the most common plastic in the world, polyethylene is relatively rare among 3D printed materials. The reason for this is the difficulty in layer-by-layer manufacturing of models.
Polyethylene melts easily (130-145°C) and hardens quickly (100-120°C), as a result of which the applied layers often do not have time to set. In addition, polyethylene is characterized by high shrinkage, which provokes the twisting of the first layers and the deformation of the models as a whole during uneven solidification. Printing with polyethylene requires the use of a heated platform and a working chamber with accurate temperature control to slow down the cooling of the applied layers. In addition, you will need to print at high speed.
Difficulties in use are more than offset by the cheapness and availability of this material. Recently, several devices have been developed for processing plastic waste from HDPE (bottles, food packaging, etc.) into standard filaments for printing on FDM/FFF printers. Examples are FilaBot and RecycleBot. Due to the simplicity of design, RecycleBot devices are often assembled by 3D craftsmen.
Melting polyethylene releases harmful vapors, so it is recommended to print in well-ventilated areas.
Polypropylene (PP, PP)
Polypropylene is a widely used plastic used in the manufacture of packaging materials, utensils, syringes, pipes, etc. The material has a low specific gravity, is non-toxic, has good chemical resistance, is resistant to moisture and wear, and cheap enough. Among the disadvantages of polypropylene, one can note the vulnerability to temperatures below -5 ° C and to direct sunlight.
The main difficulty in printing with polypropylene is the high shrinkage of the material during cooling - up to 2.4%. For comparison, the shrinkage of the popular but already problematic ABS plastic reaches 0.8%. Although polypropylene adheres well to cold surfaces, it is recommended to print on a heated platform to avoid deformation of models. The minimum recommended extrusion temperature is 220°C.
Polypropylene printing filaments are sold by Orbi-Tech, German RepRap, Qingdao TSD Plastic. Stratasys has developed a polypropylene simulant optimized for 3D printing called Endur.
Polycaprolactone (PCL)
Polycaprolactone (aka Hand Moldable Plastic, Mold-Your-Own Grips, InstaMorph, Shapelock, Friendly Plastic, Polymorph, Polymorphus, Ecoformax) - biodegradable polyester, characterized by an extremely low melting point of about 60 ° C . In practice, this property creates certain problems in 3D printing, since not all 3D printers can be configured to work at such low temperatures. Heating polycaprolactone to the usual extrusion temperatures (about 200°C) causes a loss of mechanical properties and may lead to breakage of the extruder.
Polycaprolactone is non-toxic, making it suitable for use in the medical industry and biodegradable. When ingested, polycaprolactone breaks down, which makes printing with this material safe. Due to the low melting point, there is no danger of burns when touching fresh models. The high plasticity of the material makes it possible to reuse.
Polycaprolactone is not suitable for creating functional mechanical models due to its viscosity (glass transition temperature is -60°C) and low heat resistance (melting point is 60°C). On the other hand, this material is perfect for the production of mock-ups and food containers.
The material sticks easily to the surface of even a cold working table and is easy to paint.
Polyphenylsulfone (PPSU)
Polyphenylsulfone is a high strength thermoplastic used extensively in the aviation industry. The material has excellent chemical and thermal stability and practically does not burn. Polyphenylsulfone is biologically inert, which makes it possible to use this material for the production of tableware and food containers. Operating temperature range is -50°С - 180°С. Plastic is resistant to solvents and fuels and lubricants.
For all its merits, polyphenylsulfone is rarely used in 3D printing due to its high melting point, reaching 370°C. Such extrusion temperatures are beyond the power of most desktop printers, although printing is theoretically possible using ceramic nozzles. Currently, the only active user of the material is Stratasys, which offers industrial Fortus installations.
Polymethyl methacrylate (Acrylic, plexiglass, acrylic, PMMA)
Polymethyl methacrylate is a well-known organic glass. The material is durable, moisture resistant, environmentally friendly, easy to glue, plastic enough and resistant to direct sunlight.
Unfortunately, acrylic is not suitable for FDM/FFF printing for a number of reasons. Acrylic is poorly stored in the form of spools of thread, as constant mechanical stress leads to the gradual destruction of the material. To avoid bubbles, the print resolution must be high, with a precision almost impossible for home printers. Acrylic's rapid curing requires strict environmental control of the working chamber and high print speeds. Again, the print speeds of FDM/FFF printers are inversely related to print resolution, which exacerbates the problem.
However, attempts are being made to print with acrylic, and some of them are producing relatively positive results. However, when creating sufficiently strong models, it is not yet possible to avoid the formation of bubbles and achieve the usual transparency of the material. At the moment, the best results with acrylic are shown by another printing technology - multi-jet modeling (MJM) from 3D Systems. In this case, a photopolymer version of acrylic is used. Stratasys has also made significant progress using its own photopolymer acrylic simulant VeroClear on Objet Eden printers. It is hoped that the high demand for acrylic will lead to the emergence of composite materials based on polymethyl methacrylate, designed specifically for FDM/FFF printing.
Polyethylene terephthalate (PET, PET)
Polyethylene terephthalate - this complex name hides a material used for the production of plastic bottles and other food and medical containers.
The material has a high chemical resistance to acids, alkalis and organic solvents. The physical properties of PET are also impressive with high wear resistance and tolerance to a wide temperature range from -40°C to 75°C. Among other things, the material is easily machined.
Printing with PET is somewhat problematic due to the relatively high melting point of up to 260°C and significant cooling shrinkage of up to 2%. Using PET as a consumable requires approximately the same conditions as printing with ABS.
Achieving transparency of models requires rapid cooling to pass the glass transition threshold of 70°C - 80°C.
The material has become the focus of attention of 3D craftsmen using used containers as raw materials for home production of 3D printing consumables. Recycling devices such as FilaBot or RecycleBot are used to make threads.
High impact polystyrene (HIPS)
High impact polystyrene is widely used in industry for the production of various household products, building materials, disposable tableware, toys, medical instruments, etc.
When 3D printed, polystyrene exhibits physical properties very similar to the popular ABS plastic, making it an increasingly popular material among 3D craftsmen. The most attractive feature of polystyrene is the difference from ABS in terms of chemical properties: polystyrene is quite easily amenable to the organic solvent Limonen. Since Limonene has no effect on ABS plastic, it is possible to use polystyrene as a material for building soluble support structures, which is extremely useful when building complex, interlaced models with internal supports. Compared to the convenient, water-soluble polyvinyl alcohol (PVA) plastic, polystyrene compares favorably with relatively low cost and resistance to humid climates that make PVA difficult to work with.
Be aware that some ABS manufacturers mix slightly cheaper polystyrene into their consumables. Accordingly, models made from such materials can be dissolved in Limonene along with supporting structures.
When polystyrene is heated to extrusion temperature, toxic fumes can be released, so printing in a well-ventilated area is recommended.
Wood simulants (LAYWOO-D3, BambooFill)
LAYWOO-D3 is a recent development for printing wood-like models. The material consists of 40% natural wood chips of microscopic size and 60% binder polymer. The LAYWOO-D3 is very easy to handle, being virtually warp-free and does not require the use of a heated platform. According to the manufacturers, the polymer is non-toxic and completely safe.
The unique material properties allow for different visual results when printing with different nozzle temperatures. The operating temperature range is 180°C-250°C. As the extrusion temperature increases, the shade of the material becomes progressively darker, allowing it to simulate different types of wood or annual rings.
Finished models are excellent for mechanical processing - grinding, drilling, etc. In addition, the products are easily painted, and unpainted models even have a characteristic woody smell.
Unfortunately, the cost of the material is almost four times higher than the price of popular materials such as PLA and ABS plastics. As popularity is projected to grow, the material should become more accessible.
Alternative materials are currently being developed and tested, such as BambooFill from the Dutch company ColorFabb.
Sandstone simulants (Laybrick)
Composite material from the inventor Kai Parti, responsible for the revolutionary wood simulant LAYWOO-D3. This time, Kai set his sights on sandstone imitation, using a tried and tested method of mixing a binder with a filler, in this case mineral.
Laybrick allows you to produce objects with different surface textures. At low extrusion temperatures of the order of 165°C-190°C, the finished products have a smooth surface. Increasing the printing temperature makes the material rougher, up to a high degree of resemblance to natural sandstone at extrusion temperatures above 210°C.
The material is easy to work with no need to heat the work platform, does not show significant deformation when shrinking and does not produce toxic fumes when heated. The only drawback can be considered a rather high cost of the material, which is largely due to limited production.
Metal Simulators (BronzeFill)
Metals have attracted additive manufacturing enthusiasts since the early days of 3D printing technology. Unfortunately, printing with pure metals and alloys causes a lot of difficulties that are insurmountable for most 3D printing methods. Fully functional metal products can only be produced using technologies such as SLS, DLMS or EBM, which require the use of industrial plants that cost hundreds of thousands of dollars. At the same time, metal imitators are successfully used in 3D inkjet printing (3DP), where products are formed from metal powders, the particles of which are held together by an applied binder material. In FDM/FFF printing, metal simulants are just emerging.
An interesting example is BronzeFill, which is actually a transparent PLA plastic filled with bronze microparticles.