3D printers for metal parts
The Metal X 3D Printing System
An accessible end-to-end metal 3D printing solution for functional metal parts, next-day.
Request a Quote
The Metal X System is an accessible way to fabricate complex metal parts in a wide variety of advanced metals.
Simple, Yet Powerful
The Metal X is one of the most intuitive metal 3D printers available today. Print a wide range of materials from stainless steels to copper with minimal training on a closed workflow. Scaling up capacity is easy; just add printers.
Safe and Affordable
The Metal X is designed to be safe to use and accessible for all fabricators. It costs several times less than DMLS metal 3D printing systems and requires no dedicated operator, no powder management system, and minimal PPE.
Quality Parts, Fast
The Metal X is purpose-built for consistent part quality and a seamless user experience. Markforged combines superb software, materials research, and an advanced motion system to deliver industrial-grade parts quickly and reliably.
Specs
From design to fully functional
metal parts in as few as 28 hours.
Physical Dimensions
Width | 575 mm |
Depth | 467 mm |
Height | 1120 mm |
Weight | 75 kg / 165 lbs |
Build Volume
Width | 300 mm |
Depth | 220 mm |
Height | 180 mm |
Printer primary Specs
- Printing Process
- Metal FFF
- Z Layer Resolution
- 50 μm - 125 μm (Post-Sinter)
- Printing Media
- Bound Powder Filament
- Internal Part Geometry
- Closed Cell Infill (Triangular) or Solid Parts
- Print Bed
- Heated, Auto Leveling, Replaceable Print Sheets
Wash & Sinter
Wash-1
- External Dimensions:
- 609 x 685 x 1,067 mm
- Weight:
- 136 kg (300 lbs)
- Washing Time:
- 12-72 hrs typical
- Solvent:
- Opteon SF-79
- Working Volume:
- 356 x 254 x 203 mm
Sinter-2
- External Dimensions:
- 1,200 x 700 x 1,500 mm
- Weight:
- 350 kg (772 lbs)
- Run Time:
- 17-31 hours
- Sintering Volume:
- 18,356 cu cm
- Peak Internal Temp.
:
- 1,300° C / 2,372° F
Materials
Compatible Materials
- Release Material
- Ceramic — Becomes Powder During Sintering Process
- Media (Spools)
- Bound Powder Metal Filament
System Details
Metal X PrinterThe Markforged Metal X is a new kind of metal printer. By printing metal powder bound in a plastic matrix, Markforged has eliminated many of the safety risks associated with traditional metal 3D printers. That means no loose powder, no lasers, and none of the traditional safety precautions. It’s safe to use in a shop environment with minimal facility upgrades.
In practice, the Metal X is essentially a very advanced FFF 3D printer. Featuring a precision machined gantry, a heated chamber and print bed, and advanced extrusion hardware, the Metal X is equipped to reliably print you durable parts. It is intentionally designed, with wear components and consumables — including print sheets, nozzles, and brushes — accessible and trivial to swap.
The Wash-1 is a solvent-based debinding system. It primarily uses Opteon SF-79, a high-performance fluid designed to offer superior cleaning power, higher efficiency, and safety in an environmentally sustainable way — Opteon SF-80 or Tergo Metal Cleaning Fluid can be substituted if needed.
The Wash-1 operates with simple ventilation and features an extremely simple user experience. It’s been tested and verified as a shop-safe system.
Sinter-2 and Sinter-1The Markforged Sinter-2 and Sinter-1 are highly optimized tube furnaces used for sintering 3D printed metal parts. They provide leading edge sintering reliability and run times and are equipped with advanced safety features. The Sinter-2 is more advanced than the Sinter-1 — featuring a larger working volume, more precise temperature control, and a mechanical door interlock.
The Sinter-1 and Sinter-2 typically have run times between 26 and 31 hours. However, the Sinter-2 can process small parts in express mode, where it can sinter up to 250g of parts in just 17 hours.
Download Datasheet
Materials
From stainless steel to copper,
choose from a wide range of strong,
durable, and capable materials.
Desktop 3D Printers Designed for Professionals
Desktop 3D Printer Series
Professional desktop 3D printers built with the versatility to test design concepts and build strong end use parts. Our platform covers a wide range of applications - varying from flexible and elastic to strong and rigid.
Compare 3D Printers Talk to an Expert
Drive innovation. Right from your desktop.
Compare Our Desktop 3D Printer Models.
Onyx One™
Our core desktop printer for functional plastic parts with stunning surface finish.
Materials
Plastic
Onyx™
Specs
+320 x 132 x 154 mm build volume
+100 µm - 200 µm layer height
+Precision ground composite print bed
MSRP
$4,990
Talk to an Expert
Onyx Pro™
Our enhanced desktop printer for stunning prototypes, tools, and production parts.
Materials
Plastic
Onyx™
Precise PLA
Smooth TPU
Continuous Fiber
Fiberglass™
Specs
+320 x 132 x 154 mm build volume
+100 µm - 200 µm layer height
+Precision ground composite print bed
MSRP
$9,600
Talk to an Expert
Mark Two™
The best desktop printer for stunning prototypes, tools, high performance end-use parts, and replacement parts.
Materials
Plastic
Onyx™
Nylon White™
Precise PLA
Smooth TPU
Continuous Fiber
Continuous Carbon Fiber™
Aramid Fiber (Kevlar®)*
Fiberglass™
HSHT Fiberglass™
Specs
+320 x 132 x 154 mm build volume
+100 µm - 200 µm layer height
+Precision ground composite print bed
MSRP
$19,900
Talk to an Expert
Dupont™ and Kevlar® are trademarks and registered trademarks of E. I. du Pont de Nemours and Company
What can I build on a desktop 3D printer?
Micro carbon fiber filled nylon offers excellent heat resistance, surface finish, and chemical resistance
APPLICATIONS
- Functional Protos
- Production Covers
- Fit checks
- Job Aids
Learn more
Stiff, strong, and extremely light, carbon fiber reinforcement yields parts capable of replacing machined aluminum.
APPLICATIONS
- Custom production
- Bridge production
- High performance end-use parts
- High-strength tooling
Learn more
HSHT Fiberglass delivers the highest impact resistance and heat deflection temperature of our continuous fibers, and can be used for low-temp molds.
APPLICATIONS
- Welding fixtures
- Ruggedized enclosures
- Low-temp molds
- Forming tools
Learn more
Inexpensive and 11 times stiffer than ABS, this is the perfect entry level continuous fiber for 3D printing functional parts.
APPLICATIONS
- Workholding tools
- Functional Prototypes
- Moderate strength end-use parts
Learn more
Extremely durable and extremely resistant to catastrophic damage, Kevlar is an excellent choice for harsh environments.
APPLICATIONS
- Workholding tools
- Ruggedized enclosures
- Flexures
Learn more
Rubber-like material for high quality, flexible, impact-absorbent parts on demand.
APPLICATIONS
- Seals and gaskets
- Shock absorbers
- Wheels and treads
- Belts
Learn more
Colorful, cost-effective, and easy to print thermoplastic for design validation
APPLICATIONS
- Concept models
- Fit Checks
- Color-coded indicators
Learn more
Unmatched versatility
Our Desktop Series printers unlock production-grade performance and affordable prototypes, all on the same platform. Our most popular printing plastic, Onyx™, gives you a great start in material properties with excellent surface finish. Our selection of continuous fibers take our parts far beyond the mechanical and thermal properties of everyday FFF printing plastics, Smooth TPU 95A provides an efficient way to make high quality flexible parts in low-to-medium volumes, while Precise PLA delivers effective, reliable prototypes at an affordable price. No matter what properties you’re looking for, our desktop 3D printers have the right material for the job.
How does CFR 3D printing work?
Talk with a
Desktop expert
Let us put together an additive manufacturing solution to suit your needs.
Precise metal 3D printing on order in Sprint 3D
Metal 3D printing - additive manufacturing of metal products, which is rightfully one of the most promising and rapidly developing areas in 3D printing as such. The technology itself originates from the conventional sintering of materials used in powder metallurgy. But now it has become more perfect, accurate and fast. And today SPRINT3D offers you metal printing on 3 D printer on really favorable terms. But first, a little information about the production process itself and its capabilities.
Selective Laser Fusion Technology
SLM or Selective Fusion Technology is a type of direct metal printing that achieves a density of 99.5%. The difference is especially noticeable when compared with models obtained by conventional casting. This indicator is achieved due to the introduction of the latest technologies in the hardware part:
- The use of special rollers for compacting powders and, as a result, the possibility of using powders with a particle size of 5 microns.
- Bulk density increase to help compact end products.
- Creates a rarefied atmosphere of inert gases, which ensures maximum purity of the material, no oxidation, and eliminates the risk of introducing third-party chemical compounds into the composition.
But most importantly, the modern 3 D Metal Printer makes it easy to customize the configuration for printing with a specific metal powder. Thus, even with inexpensive material, you can get a first-class result. But only if you use high-quality modern equipment. And here we are ready to surprise you too!
Metal 3D printing B SPRINT 3D
3D printing with own 3D printers
The largest working area is 280x280x350 mm
layer thickness up to 15 micron
3D with various types of metals
Delivery throughout Russia and CIS countries
installations for 3 D metal print, which we use
Production quality is a key requirement that we set ourselves. Therefore, in our work we use only professional equipment with wide possibilities for metal printing. Let's take a closer look at each of the production units.
Production unit SLM 280HL
SLM 280HL is a development of the German company SLM Solutions GmbH, which uses the technology of layer-by-layer laser melting of powder metal materials. The installation is equipped with a large working chamber and allows you to create 3D objects with dimensions of 280x280x350 mm. Among the main advantages of printing with this unit are:
- Small minimum thickness of the applied layer - 20 microns.
- Filling the working chamber with an inert gas, which allows you to work with various reactive metals.
- Print speed up to 35 cm/hour.
- Construction layer thickness – 30 and 50 µm.
- Power - 400 W.
A special highlight is the patented powder feed system, which delivers significantly faster print speeds than most production machines in the same price range. We use the following materials in production:
- Stainless steel (domestic 07X18H12M2 (Polema), 12X18H10T and imported 316L).
- Tool steel (imported 1.2709).
- Heat-resistant alloys 08KhN53BMTYu (similar to Inconel 718, produced by Polem) and EP 741 (produced by VILS).
- Cobalt Chrome (COCR)
The SLM 280HL 3D printer can be used to create all kinds of metal components, prototypes and end products. If necessary, we can provide small-scale production.
ProX 100 production unit
ProX 100 is a compact 3 D metal printing unit developed by the American company 3D Systems. It uses direct laser sintering technology, which ensures high speed and precision of production. Among the main characteristics it is worth highlighting:
- The size of the working chamber is 100x100x80 mm.
- Construction layer thickness – 20 and 30 µm.
- Power - 50 W.
ProX 100 allows you to create prototypes that cannot be developed by standard methods, provides short lead times, guarantees the absence of material porosity and high part density. In addition, we note the standardized quality of all products, regardless of their structure. At the moment, the model is actively used in dentistry when creating high-precision prostheses, but it has found wide application in other industries:
- Manufacture of engines and their individual parts.
- Development of medical equipment.
- Printing jewelry and even contemporary art.
In printing, we use the KX28M6 cobalt-chromium alloy (Polem's production), originally developed for additive technologies when creating endoprostheses.
Metal 3D printing - current application
Many experts argue that 3D printing as such has not yet fully revealed its potential. For example, Elon Musk plans to use technology in the colonization of Mars to build administrative and residential buildings, equipment and technology right on the spot. And this is quite real, because already now the technology of three-dimensional metal printing is actively used in various industries: The high precision of production and relatively affordable price have made 3D printing very relevant in this industry.
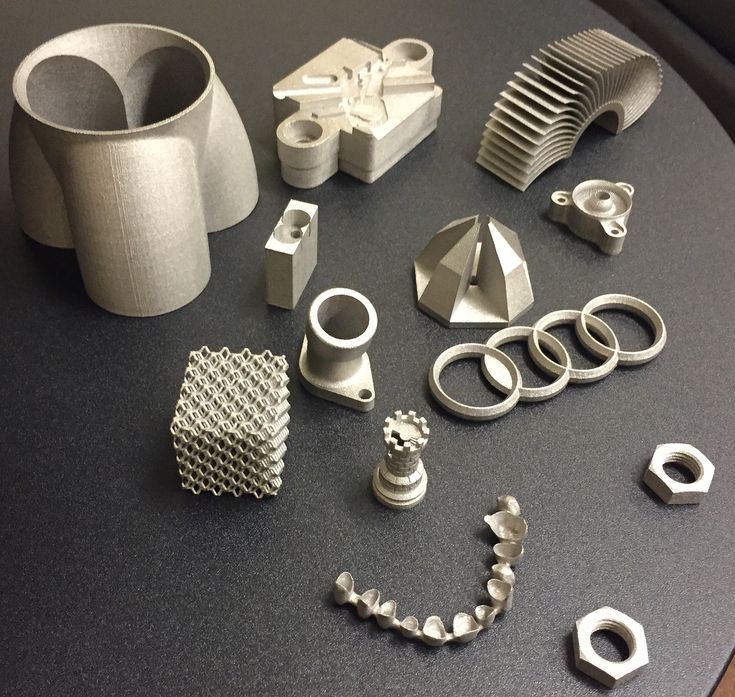
And this is only a small part of what can be created on modern equipment. Almost all metal products that you need can be created using metal 3D printing technology. And if this service is relevant for you, contact SPRINT3D. We will undertake work of any complexity and volume. And most importantly - we will provide first-class results!
The future is here!
You may be interested in
How metal 3D printers work. Overview of SLM and DMLS technologies. additive manufacturing.
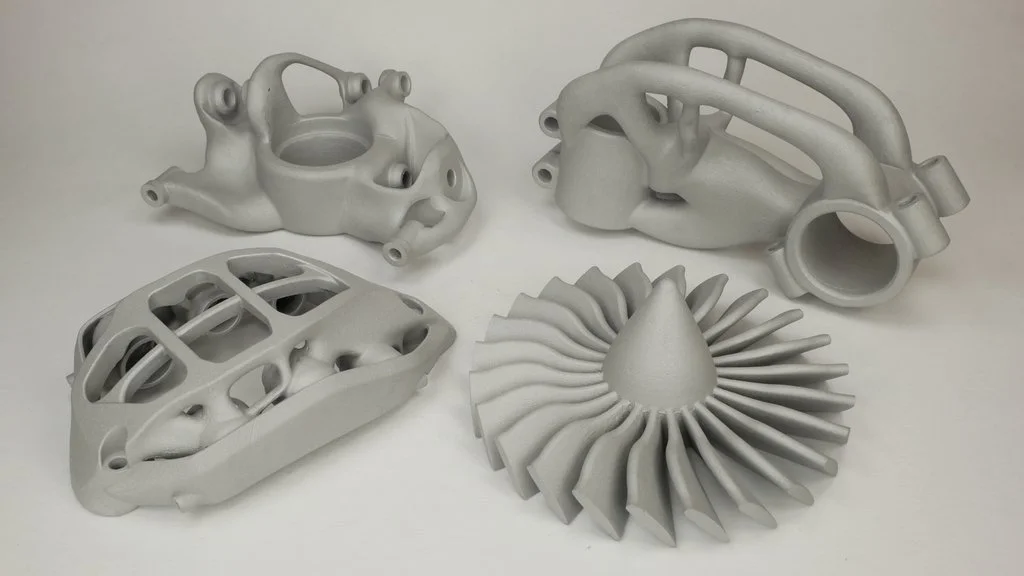
Metal 3D printing. Additive technologies.
SLM or DMLS: what's the difference?
Hello everyone, Friends! 3DTool is with you!
BLT metal 3D printer catalog
Selective laser melting ( SLM ) and direct metal laser sintering ( DMLS ) are two additive manufacturing processes that belong to the family of 3D printing using the powder layer method. The two technologies have much in common: they both use a laser to selectively melt (or melt) metal powder particles, bonding them together and creating a pattern layer by layer. In addition, the materials used in both processes are metals in granular form.
The differences between SLM and DMLS come down to the basics of the particle bonding process: SLM uses metal powders with a single melting point and completely melts the particles, while in DMLS the powder consists of materials with variable melting points.
Specifically:
SLM produces single metal parts while DMLS produces metal alloy parts.
Both SLM and DMLS technologies are used in industry to create final engineering products. In this article, we will use the term "metal 3D printing" to summarize the 2 technologies. We will also describe the main mechanisms of the manufacturing process that are necessary for engineers to understand the advantages and disadvantages of these technologies.
There are other manufacturing processes for producing dense metal parts, such as electron beam melting (EBM) and ultrasonic additive manufacturing (UAM). Their availability and distribution is rather limited, so they will not be presented in this article.
How 3D printing with metal SLM or DMLS works.
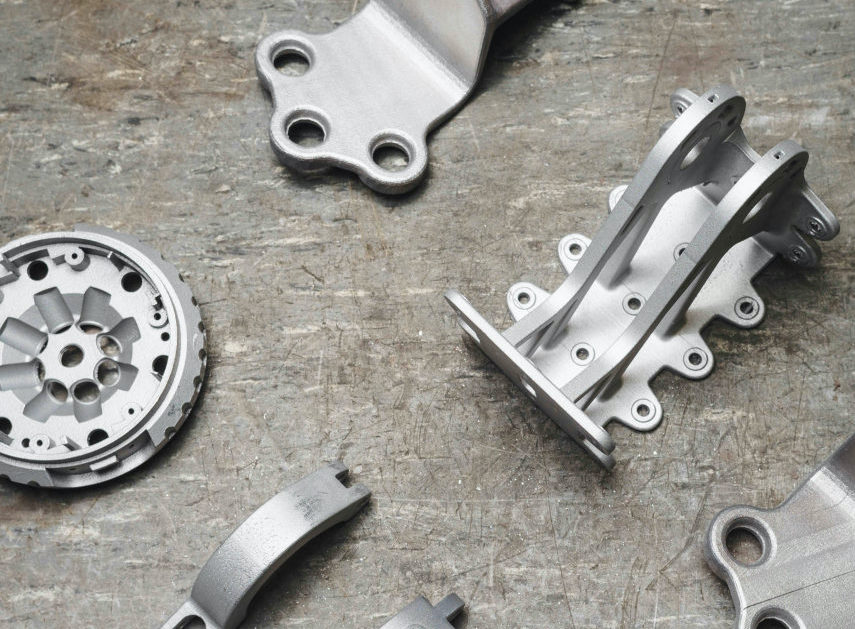
How does metal 3D printing work? The basic manufacturing process for SLM and DMLS is very similar.
1. The printing chamber is first filled with an inert gas (such as argon) to minimize the oxidation of the metal powder. It then heats up to the optimum operating temperature.
2. A layer of powder is spread over the platform, a powerful laser makes passes along a predetermined trajectory in the program, fusing the metal particles together and creating the next layer.
3. When the sintering process is completed, the platform moves down 1 layer. Next, another thin layer of metal powder is applied. The process is repeated until the entire model is printed.
When the printing process is completed, the metal powder already has strong bonds in the structure. Unlike the SLS process, parts are attached to the platform via support structures. The support in metal 3D printing is created from the same material as the base part. This condition is necessary to reduce deformations that may occur due to high processing temperatures.
When the 3D printer's chamber cools down to room temperature, excess powder is removed manually, such as with a brush. The parts are then typically heat treated while they are still attached to the platform. This is done to relieve any residual stresses. They can then be further processed. The removal of the part from the platform occurs by means of sawing.
The scheme of the 3D printer for metal.
In SLM and DMLS, almost all process parameters are set by the manufacturer. The layer height used in metal 3D printing varies from 20 to 50 microns and depends on the properties of the metal powder (fluidity, particle size distribution, shape, etc.).
The basic size of the print area on metal 3D printers is 200 x 150 x 150 mm, but there are also larger sizes of the working area. Printing accuracy is from 50 - 100 microns. As of 2020, metal 3D printers start at $150,000. For example, our company offers 3D metal printers from BLT.
metal 3D printers can be used for small batch production, but the 3D printing capabilities of such systems are more like those of mass production on FDM or SLA machines.
The metal powder in SLM and DMLS is recyclable: typically less than 5% is consumed. After each impression, the unused powder is collected and sieved, and then topped up with fresh material to the level required for the next production.
Waste in metal printing, are supports (support structures, without which it will not be possible to achieve a successful result). With too much support on the manufactured parts, the cost of the entire production will increase accordingly.
Adhesion between coats.
3D metal printing on BLT 3D printers
SLM and DMLS metal parts have almost isotropic mechanical and thermal properties. They are hard and have very little internal porosity (less than 0.2% in 3D printed condition and virtually non-existent after processing).
Metal printed parts have higher strength and hardness and are often more flexible than traditionally made parts. However, such metal becomes “tired” faster.
3D model support structure and part orientation on the work platform.
Support structures are always required when printing with metal, due to the very high processing temperatures. They are usually built using a lattice pattern.
Supports in metal 3D printing perform 3 functions:
• They form the basis for creating the first layer of the part.
• They secure the part to the platform and prevent it from deforming.
• They act as a heat sink, removing heat from the model.
Parts are often oriented at an angle. However, this will increase the amount of support required, the printing time, and ultimately the overall cost.
Deformation can also be minimized with laser sintering templates. This strategy prevents the accumulation of residual stresses in any particular direction and adds a characteristic surface texture to the part.
Since the cost of metal printing is very high, software simulations are often used to predict how a part will behave during processing. These topology optimization algorithms are otherwise used not only to increase mechanical performance and create lightweight parts, but also to minimize the need for supports and the likelihood of part distortion.
Hollow sections and lightweight structures.
An example of printing on a BLT 3D printer
Unlike polymer powder melt processes such as SLS, large hollow sections are not typically used in metal printing as the support would be very difficult to remove, if at all possible.
For internal channels larger than Ø 8 mm, it is recommended to use diamond or teardrop cross-sections instead of round ones, as they do not require the construction of supports. More detailed recommendations on the design of SLM and DMLS can be found in other articles on this topic.
As an alternative to hollow sections, parts can be made with sheath and cores, which in turn are machined using different laser power and pass rates, resulting in different material properties. The use of sheath and cores is very useful when making parts with a large solid section, as it greatly reduces printing time and reduces the chance of warping.
The use of a lattice structure is a common strategy in metal 3D printing to reduce the weight of a part. Topology optimization algorithms can also help design organic lightweight shapes.
Consumables for 3D metal printing.
SLM and DMLS technologies can produce parts from a wide range of metals and metal alloys, including aluminum, stainless steel, titanium, cobalt, chromium and inconel. These materials meet the needs of most industrial applications, from aerospace to medical applications. Precious metals such as gold, platinum, palladium and silver can also be processed, but their use is of a minor nature and is mainly limited to jewelry making.
The cost of metal powder is very high. For example, a kilogram of 316 stainless steel powder costs approximately $350-$450. For this reason, minimizing part volume and the need for supports is key to maintaining optimal manufacturing cost.
The main advantage of metal 3D printing is its compatibility with high-strength materials such as nickel or cobalt-chromium superalloys, which are very difficult to process with traditional methods. Significant cost and time savings can be achieved by using metal 3D printing to create a near-clean shape part. Subsequently, such a part can be processed to a very high surface quality.
Metal post-processing.
Various post methods. treatments are used to improve the mechanical properties, accuracy and appearance of metal printed products.
Mandatory post-processing steps include the removal of loose powder and support structures, while heat treatment (heat annealing) is typically used to relieve residual stresses and improve the mechanical properties of the part.
CNC machining can be used for critical features (such as holes or threads). Sandblasting, plating, polishing, and micro-machining can improve the surface quality and fatigue strength of a metal printed part.
Advantages and disadvantages of metal 3D printing.
Pros:
1. Metal 3D printing can be used to make complex custom parts, with geometries that traditional manufacturing methods cannot provide.
2. Metal 3D printed parts can be optimized to increase their performance with minimal weight.
3. Metal 3D printed parts have excellent physical properties, metal 3D printers can print a wide range of metals and alloys. Includes difficult-to-machine materials and metal superalloys.
Cons:
1. Manufacturing costs associated with metal 3D printing are high. The cost of consumables is from $ 500 per 1 kg.
2. The size of the working area in metal 3D printers is limited.
Conclusions.
• Metal 3D printing is most suitable for complex, one-piece parts that are difficult or very expensive to manufacture using traditional methods, such as CNC.
• Reduced need for building supports, greatly reducing the cost of printing with metal.
• 3D printed metal parts have excellent mechanical properties and can be made from a wide range of engineering materials, including superalloys.
And that's all we have! We hope the article was useful to you.
Catalog of 3D printers for metal BLT
You can purchase metal 3d printers, as well as any other 3d printers and CNC machines, by contacting us:
• By email: Sales@3dtool.