3D printer pcb
A New Way To Produce PCBs With Your 3D Printer
- by: Tom Nardi
With the low-cost PCB fabrication services available to hackers and makers these days, we’ll admit that making your own boards at home doesn’t hold quite the appeal that it did in the past. But even if getting your boards professionally made is cheaper and easier than it ever has been before, at-home production still can’t be beat when you absolutely must have a usable board before the end of the day.
If you find yourself in such a situation, this new method of DIY PCB production detailed by [Adalbert] might be just what you need. This unique approach uses a desktop fused deposition modeling (FDM) 3D printer throughout all of its phases, from creating a stencil based on the exported board design, to warming the UV soldermask to accelerate the curing process. It may not be an ideal choice for densely packed boards with fine-pitch components, but could definitely see it being useful for many prototypes.
[Adalbert] has done an excellent job of documenting the process through a step-by-step guide posted on Hackaday.io, and has also put together a video you can see after the break.
But if you’re looking for the short version, the process involves taking a 2D DXF from your PCB design software, converting it into three dimensions, and printing it out. This is then placed over a copper clad board that has been coated with soldermask, and a UV light source is used to expose it. Afterwards, isopropyl alcohol can be used to wash away the unexposed mask, leaving behind your PCB design.
You’ll still need to chemically etch the board, and if you’re using through-hole components, manually drill your holes. But compared to some of the old school methods of making your own boards, it’s relatively straightforward. This technique looks like it could also hold promise for small scale production, as the stencil can be reused indefinitely.
If your 3D printer is of the resin variety, don’t worry, you can make PCBs with those as well. We’ve also seen impressive boards produced with cheap laser engravers, as well as budget CNC routers.
3D-printed circuit boards: How they're made and why they matter
Once confined mainly to home-brew tinkering, circuit boards created via 3D printing are now practical for some manufactured products.
J.F. Brandon, BotFactory Inc.
In the past ten years, 3D Printing has gone from a niche prototyping tool to a process acceptable for mass production. Most of the recent hubbub has been about monolithic plastic and metals. But new materials and processes have appeared to help create 3D-printed PCBs that meet long-standing engineering problems.
If the history of electronics manufacturing could be summarized in one phase, it would be, “Shrinking everything to nothing to squeeze out something faster.” The push towards miniaturization has been driven by the inviolable laws of nature – faster devices that consume less power require shorter electrical paths.
However, the printed circuit board is an outlier in the electronics world. PCBs still use basic drilling and plating processes perfected 50 years ago. That is not to say that PCB manufacturing is trivial or antiquated. But the investment in new PCB manufacturing methods is a pittance compared to the hundreds of billions put into chip fabs by IC makers such as TMSC and AMD.
It is worth looking at the details of PCBs and their construction. The word ‘printed’ in printed-circuit board only describes half of the process – the silkscreen masks are the only part that is printed. A PCB is originally copper foil on a rigid fiberglass laminate which is selectively etched, drilled, and plated using a set of silkscreens and chemical baths to produce the final product.
Examples of inkjet-printed circuitry made with a BotFactory SV2 PCB printer.The sole purpose of the PCB is to reliably connect passive and active components and provide a reliable platform for integration or interactions with the rest of a product. For example, the PCB in the average computer keyboard connects electronic elements together, but it also must manage human interactions and provide a sound mechanical connection to the body of the product. In addition, PCBs must be designed so they can easily be stenciled with reflow solder paste and integrated into industrial surface-mount pick-and-place lines. Optical inspection and flying-probe systems require PCBs that can be easily analyzed and binned for repair or discard automatically. All in all, modern PCBs can play a variety of roles within the end products in which they are found. So it is worth considering new manufacturing processes that can expand the capabilities of PCBs.
PCBs have thermal, electrical, geometric and mechanical requirements that go beyond what most materials for 3D printing can offer. For example, the average $500 3D printer that uses Fused Deposition Modeling (FDM) uses PLA, ABS and PETG which melt under the harsh gaze of any standard soldering station. Metal 3D printing techniques are designed to handle one material at one time. Yet PCBs require, at a bare minimum, a dense and conductive metal for conductors.
Three technical paths have appeared for PCB printing: inkjets, extrusion, and additive manufacturing (AM)-electroless plating. First consider ink-jetting. New nanoparticle and particle-free inks have allowed inkjet printing to go beyond CMYK inks and graphics. Inkjets can now lay down metal (overwhelmingly silver) inks in fine patterns on flexible materials. In combination with a polymer ink, it is possible to create PCBs with complex multilayer circuitry (blind and buried vias are trivial items) in only a few steps on a single machine.
The inherent advantage of creating PCBs layer-by-layer this way is that each layer can be tested and validated. The minimal level of processing simplifies the dispensing solder paste, part assembly, and testing for every layer. The disadvantages are that material dispensing via inkjet printing is slow relative to all other additive manufacturing processes– deposition speeds can be in the millimeters-per-hour range. It’s possible to create precise traces with inkjet printing (metal traces with 100-micron widths are commonly attainable). But the smaller droplets limit deposition speeds.
And there are problems with metal inks: Applying too much can cause bleeding and cracking during drying, thus limiting PCB fabrication speeds. Solderability is a particular blind spot – silver can wilt under standard pastes like SAC305, suffering from tin ‘scavenging’ silver during reflow. In addition, inkjet polymers melt at temperatures that standard PCBs easily manage. Fortunately, industry-accepted low-temperature tin-bismuth and indium-based solder pastes are compatible with inkjet-printed PCBs.
Today there are two PCB printers that use ink jetting – the BotFactory SV2 and the Nano Dimension DragonFly. Each printer uses the same process to create multilayer circuitry, although the BotFactory SV2 utilizes inexpensive thermal inkjet heads instead of the piezo heads found in the DragonFly. Nano Dimension has focused on printing for production, whereas BotFactory has emphasized integration of pasting and PCB assembly into a small unit, working on projects with the USAF to automate the entire process. In this regard, BotFactory is unique in the electronics industry and is the only commercial product below $20,000.
Single nozzle jetting
Inkjetting isn’t the only way that nanoparticles can be deposited to create circuitry. An alternative method extrudes lines onto flat surfaces and uses fused-deposition modeling to provide a polymer structure for the traces to inhabit. Pastes are notoriously difficult to control when creating fine traces and spaces, requiring precise control and extremely close contact with the substrate surface.
Here the target surface must be covered twice – first for mapping, then for pasting. The two-step procedure handicaps the scalability of the process for production. Pastes must be devoid of air pockets lest each bubble act as a kind of ‘spring’ and impede the extrusion process. The flip side of using viscous pastes is that metal-loading is higher and it’s possible to deposit metal in thicker layers, boosting conductivity and solderability right off the bat. However, at this time, silver is the overwhelming favorite material and thus suffers from the same constraints as inkjet-printed PCBs in regards to silver scavenging.
The first example of 3D printed electronics was demonstrated by Voxel8 in 2015. The printer used FDM and paste extrusion to create basic circuit traces. After delivering early beta systems, Voxel8 switched to industrial-scale fabrication with a broader focus on multi-material printing rather than just electronics. nScrypt has taken a similar tack, creating a more general tool that includes pasting as well as polymer extrusion to create three-dimensional objects with traces within the object.
AM + electroless plating (also abbreviated as AMEP, or 3D-Print-and-Plate) is a completely new category of AM that combines existing additive manufacturing processes and well-understood electroless plating techniques. An object is printed via stereolithography (SLA) or fused-deposition modeling (FDM) using a distinct metal-loaded material that can be electroless-plated afterward. AMEP continues to be a topic of academic research. Last year, researchers at UCLA published results on using SLA to create multi-material prints that could be selectively plated. Using two vats of pure and metal-loaded polymers, the process enhances the existing premise of AM with no extra constraint on fabrication speed.
Palladium, a metal that is traditionally extremely expensive, normally serves as a seed material in this process. But on the other side of the world, UK researchers devised a way of printing less expensive metal on a new polyimide material. Polyimide (also known as Kapton) is highly prized by electrical engineers in flexible and printed electronics for its low thermal expansion and dielectric constant. UK researchers found UV energy can be used to chemically bond silver particles and the polymer chains, providing seeds for plating afterward.
The technology described above has not been commercialized, but the overall concept has been utilized for creating unique antennae at firms like Swissto12. There a high-resolution SLA print is made, coated, and then electro-plated (not electroless plated). Electroplating requires a current to initiate and control the plating process, whereas a PCB often has unconnected traces and vias that require plating.
Overall, the greatest challenge to AMEP is that it cannot create conductors within an object unless there are exposed holes or the PCB undergoes multiple dips into the plating baths. As it stands, the technology has the ability to meet all the technical requirements for high-performance PCBs, including ease-of-solderability and high-thermal tolerances.
What it’s not
There is some confusion about what is and isn’t ‘AM electronics,’ and certain lines have been drawn. In the AM industry overall, any process that uses subtractive processes is not additive manufacturing. So it is fair to argue that any process that builds circuitry on pre-existing substrates or augments AM with subtractive processes is not 3D-printed electronics. Consider the traditional PCB: UV-curable polymers mask copper foils, utilizing a process and materials seen in AM technologies like inkjet printing and stereolithography. By conveniently ignoring the drilling process for vias and shaping, one could argue that PCBs are made with AM when they clearly are not.
When an entire model is fabricated using AM, it typically has characteristics and form factors that go beyond what would be possible if subtractive fabrication is included. In other words, use of subtractive processes detracts from the entire point of adopting AM.
An example of a semi-additive process that is commonly cited as 3D-printed electronics is Laser Directed Structuring, a technique developed by LPKF. Essentially, an object consists of an injection-molded plastic that has been filled or coated by an organometallic compound. When a laser applies a circuit pattern to the surface, metallic seeds form and create an electroless nickel or copper plating. The technology is limited by the reach of the laser, inhibiting the possibility of allowing conductors to pass thru the object. Thus LDS parts are not true 3D PCBs by any means.
The same limitation also applies to aerosol jetting, a concept commercialized by Optomec. Here a carrier gas (nitrogen typically) jets out of a fine nozzle at high speed and carries a fine suspension of materials such as nanoparticle metal inks. The wide variety of viscosity, metal-loading and material choice makes aerosol jetting a candidate for creating sensors on objects, overcoming the limited choice of materials for LDS. As both processes utilize non-AM elements, they arguably do not create 3D-printed electronic devices.
Credible advances in materials, metals and polymers have made it possible to 3D-print PCBs that are useful in many applications today. However, the 3D-printed circuit board made in a few hours which is a perfect replica of a traditional PCB is the Mount Everest of AM. The most mature technique is inkjet printing; it comes closest to reaching the necessary geometric and electric properties, with materials advancing quickly to meet the thermal and mechanical needs. Extrusion is well-understood but hard to scale, and its fundamental capabilities are uneven. AM-EP is the dark horse in the race, combining old and new techniques to provide another path to the 3D PCB.
Example of how AM and Plating can be combined, courtesy of University of Leeds and Heriot-Watt University.
Ultimately, all technologies can be viable paths to reducing PCB size and shortening traces, yielding lighter devices in forms that would have been unthinkable just ten years ago.
BotFactory Inc.
www.botfactory.co/
Printed circuit boards using a photopolymer 3D printer / Sudo Null IT News And in the last year or two, thanks to a strong reduction in cost, their photopolymer subspecies is also flourishing. Now such a printer is already available to almost everyone, and the number of their models on the market is multiplying every month.
Even when I just learned about the appearance of a new type of photopolymer printers a few years ago - in which the image of the layer for illumination is formed by an LCD, the thought flashed through me already then: "Hmm, what if we substitute a photoresist on a textolite?". But then it was a purely theoretical question - the prices for them were considerable, and the resolution and display area left much to be desired. However, today these printers can already boast of a decent resolution - from 30 microns per pixel, and a completely normal display area.
And as it turned out, with the help of an inexpensive modern photopolymer printer, it is quite possible to make boards with tracks / gaps from 0.15 mm.
I apologize in advance for such a voluminous graphomaniac, I myself did not expect that the note would get so fat...
I foresee the question "But why? In China, they will make normal boards with a mask and silk-screen printing for a penny!" I answer: now, most likely, there will be several iterations of finishing the board to a satisfactory state. I made a board - tested it - made corrections. And so several times. Waiting every time for 2-3 weeks from China is not an option :) But when the final design of the board is determined - then, of course, normal production in China or on Rezonit.
Now let's get down to business.
Who does not know - here is a brief principle of operation of such a printer The main part of such a printer is an LCD display. Below this display is a 405 nm UV source. Above the display is a bath of photopolymer, which has a thin transparent FEP film as a bottom. A platform is lowered into the bath, on which the model is “grown”. At the beginning of printing, the platform lowers to the height of one layer from the film, the image of the first layer is displayed on the display, and UV illumination is turned on for a specified time. Illumination, getting through the "open" pixels of the display and the film onto the photopolymer, hardens it, so a hardened layer is obtained. The first layer sticks to the platform. Then the illumination is turned off, the platform rises to the height of the next layer, the image of this layer is displayed on the display, and the illumination is turned on. The second layer is cured by welding with the previous layer. And this is repeated over and over until the entire model is printed.
The idea to try to make a printed circuit board using such a printer came to me again about three years ago, when I bought myself an Anycubic Photon S printer. , then I just forgot about this idea, because and there was no need to make boards. But the other day, the need arose for the manufacture of several small boards, and with a high probability that as tests are made, changes will be made to these boards and it will be necessary to go through several iterations of "manufactured-checked-changed" in a short time. And the idea resurfaced.
To be honest, I thought that by now the Internet would be filled with the results of such experiments, the idea lies on the surface :) But to my surprise I found that the Internet is almost completely silent on this issue. There are separate notes, but there is no integrity and completeness in them. That's why I decided to publish this post - maybe it will help someone go all the way faster than me, and with less rakes :)
Well, the most important thing is that you don't need film and you don't have to struggle with increasing the contrast of the template. You also do not need a separate UV source with a place for its installation. And, of course, it is stylish, fashionable, youthful.
There are also disadvantages - the resolution of most modern 3D printers still does not cause much enthusiasm yet - the pixel size of all fluctuates around 0.05 mm. But this is already enough for confident manufacturing of boards with tracks from 0.2 mm and rather high chances of success with tracks from 0.15 mm. Due to the raster nature of such a template output, the position and size of elements on it can vary + -1 pixel, so I think it’s not even worth counting on tracks of 0.1 mm or less.
Let's go in order.
Task
It is necessary to make a printed circuit board at home using photoresist. Instead of templates and illumination lamps, use a photopolymer 3D printer that will serve both at the same time.
Let's divide the problem into separate steps-solutions for each moment.
-
Board development
-
Outputting layers in a printer-friendly format
-
Preparation of textolite with photoresist
-
Printer flare
-
Photoresist development, board etching
1.
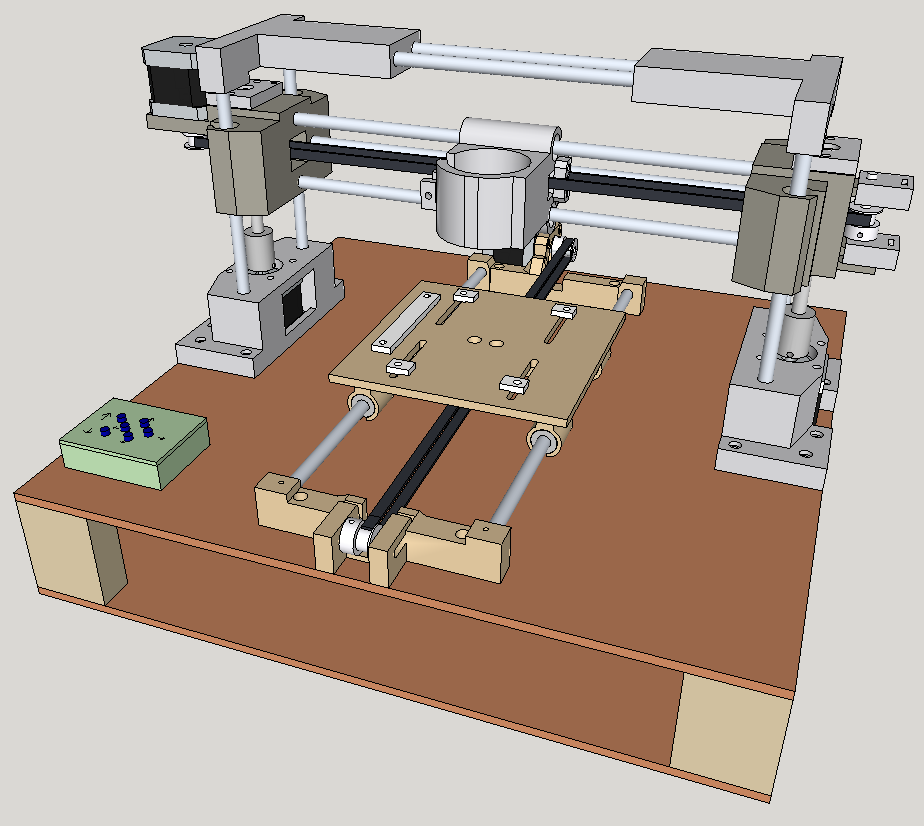
Well, there are no questions. Whoever prefers to work in what program - in that one makes boards. The main thing is that the program should be able to display the result in some commonly used form. The easiest way I've come up with is outputting board layers to gerber files that can be fed to an online service. But you can also output to PDF or images.
2. Converting the CAD output to a printer friendly
This is where the trouble begins. If almost all CADs can output to generally accepted formats - gerberas, DXF, printing to PDF, then 3D printer manufacturers so far categorically refuse to accept any file standard. Everyone is perverted as they can. The situation is largely saved by the fact that many manufacturers use motherboards from one Chinese company, Chitu Systems, in their printers. Thanks to this, many printers on such boards are able to understand one of the basic formats developed by the same company. And even often, if a file has some unique extension, then in fact it has the same basic format, just with a different extension. But it may differ in some details.
In any case, there is a free UVtools utility known among photopolymerists that can open files in one format and convert them to another format. It understands almost all formats on the market :)
I have tried two ways of preparing files with layers for the printer and I will describe both.
2.1 Gerber output and conversion to .photon
The .photon file format is understood by the old Anycubic printers - Photon and Photon S. This is exactly the case when the printer manufacturer took the format from Chitu and changed its extension. In the original, this is the Chituvian .cbddlp format, so you can safely change the extensions of these types of files among themselves and the printers will devour them like native ones.
Since I have a printer that understands this format, this method suited me perfectly. The limitations of this method are that the printer must understand .photon or .cbddlp files and have a standard display for most non-monochrome printers with a resolution of 2560x1440 and a diagonal of 5. 5". manuals on how to do this for any CAD that can, in principle, mirror layers or not - it makes no difference, they can be mirrored in the utility during the conversion process.0003
Now open the online utility for converting gerber files - https://pcbprint.online/ and load the gerberas into it. By the way, this is a utility from a Russian developer who lives here.
It is easy to understand, although it does not contain any information or help. But here is a short guide:
For a single-sided boardUpload your gerbera in the main window with the "Upload file" button:
We made sure that everything is fine and the image meets expectations, if necessary, make a negative or mirror the image with the buttons in the top center, and press the button " Render layout":
Now press "Lauout" at the top right and get into another screen:
Here you first need to go to the settings (gear button at the top right) and there select the format of the output file "photon":
The time in "Exposition" can be left at default and change it to the desired one directly in the printer. But you can immediately put the right one if its value is already known :)
Close the settings and return to the previous screen. Here the output image is on a black space showing the working field of the printer. The image can be moved, aligned. When everything suits, we first press "Render", and when the "Download result" button next to it becomes active, we also press it. And save the proposed .photon file to a convenient location on your computer :)
For double-sided boards, things are a little more complicated due to the need to match them. Therefore, it is necessary to know very exactly the position of the image displayed on the printer's display in order to place the board on the display very accurately in accordance with it.
I had several options for solving this issue, but in the end I decided on the simplest of them, which did not require any mechanical conductors. To do this, I still in CAD in a separate layer (it is possible in the border layer or in any other "unnecessary" layer) I draw a frame around the board with a line of 0. 15 mm and indented from the edges of the board by 0.25 mm. As a result, I get three gerberas - the top layer, the bottom layer and a separate empty frame.
I upload all three gerberas to the above site and then in a few steps I get three files for the printer.
Double-sided board in pcbprint.online/So, all three gerberas have been loaded. All of them are mixed together, but it's not scary:
Now hide the top and bottom layers, leaving only the frame (by clicking on the eyes in the names of the gerberas).
Click "Render layout" and go to the "Layout" screen with the button in the upper right corner. We see an empty frame, drag it to the desired position on the black field of the display, click "Render" and "Download". The first file for the printer is ready.
Switch back to the gerber screen with the "PCB comose" button. Redisplay the first layer (the frame layer still remains visible), mirror if necessary, and click "Render layout" again. Again we go to the output screen and now there are two pictures hanging on the display field - a separate frame and the first layer with a frame. The frame remained in the same place where we pulled it last time. And now our task is to exactly combine the frame of the first layer and the empty frame:
Click "Increase" and combine in one of the corners. In this case, in no case should you move the empty frame that we set in the last step!
Combined, click "Render" and "Download", and we have a second file for the printer. Before returning to the gerbera screen, we delete the render layer with the frame, we should again have an empty frame. And now we return to the gerberas, hide the first layer and display the second one, look at the need to mirror, click "Render layout" and go to this screen again. In the same way, we combine the layer frame with an empty frame (which cannot be moved!), then "Render" and "Download".
Everything, all three necessary files for the printer are ready.
All this hemorrhoids allows you to generate for the printer files of an empty frame and layers with a frame in the same place on the printer display with high accuracy. The empty frame serves to aim the board, more on that below.
If necessary, the resulting .photon files can be converted to the desired format using UVtools :)
2.2 Output layers to PDF or images
The second method is perhaps more confusing, but its great advantage is versatility, it is suitable for any printers, whose formats are supported by UVtools. I will describe it only in general terms, because. There are quite a lot of tools and specific ways to implement it, and everyone can choose them according to their preferences.
So, the goal of the first step is to get a picture with a size equal to the resolution of the printer's display, preferably in a lossless compression format. In this case, the image of the layer in the picture must correspond to the real size in the scale of the display.
If CAD allows you to output directly to the picture - great, output to it. If the resolution of the output image is configurable - specify the resolution of the printer display. It is elementary to calculate it - we divide the number of pixels across the width of the display by the width of the working area in mm and multiply the result by 25.4, we get the resolution in pixels per inch. If the resolution is not set, then set the image size as large as possible so that there are at least 15-20 pixels per 1 mm of the board.
If output to image in CAD is not available, then output to PDF. This PDF will need to be opened in another program and converted to an image. Photoshop, Corel, maybe other programs can do this... The requirements for image resolution are the same. For example, in Photoshop, when importing a PDF, you can immediately specify with what resolution to convert to an image. For example, for common displays with a resolution of 2560x1440 and a diagonal of 5.5 "the resolution is approximately 537.566 PPI (pixel size - 0.04725 mm).
The resulting image will need to be changed in some image editor, bringing its size to the resolution of the printer's display. In this case, the layer image must be scaled to the real one (taking into account the pixel size of the printer display) or saved without scaling if the PPI of the display was specified when importing the image.
UPD: in the comments @0x3f00 gave a link to his converter of PNG images to files for the .photon printer - https://github.com/0x3f00/PhotonCpp/releases/tag/v1.0.0 . There is also an instruction for using it just for the purpose of manufacturing boards - https://github.com/borelg/PhotonPCB.
2.3 There is another way, but it is very resource-intensive
You can output layers to PDF, then open this PDF in Corel, convert it, save it in DXF, extract a three-dimensional object from this DXF, which you can push into the printer's slicer.
Necessary transformations in the vector editor:
-
Connect all curves.
-
Convert outlines to objects.
-
Merge intersecting objects.
You can extract a three-dimensional object from DXF, for example, SolidWorks. Fusion360 also seems to be able to. Who else is capable of this - I honestly don't know, but in theory any CAD that can import DXF as a sketch.
Thus, for example, I made a model for determining the exposure time of the photoresist.
3. Preparation of textolite with photoresist
The Internet is simply littered with articles on this topic, but for the sake of integrity and for the sake of some specific points, I will also describe such well-known stages as the preparation and etching of textolite.
My first experience with such a fabrication was a couple of days ago with a domestic photoresist PF-VShch. Taking into account the last yesterday's experience, I categorically advise not to waste time on this photoresist, but immediately take a decent one - Ordyl Alpha 350(330) :) They say that Kolon is also decent, but I have not tried it. With Ordyl photoresist, the results are much more stable and accurate, it is easier to develop and adheres much better to the foil. And he can forgive those mistakes that will be critical for the PF-VSC. And what is important - it is sold in a bunch of places quite inexpensively.
3.1 Preparing the textolite
To begin with, the textolite should be smooth, very preferably with a smooth foil without scratches or dents. Otherwise, the chances of success are reduced.
If a double-sided board is being made, then you need to immediately cut the board out of the PCB exactly to size. If there is any CNC router, then you can drill all the holes and cut along the contour in one installation, as I do. If not, then it is better to leave the drilling for later, when the board is etched.
After this, the textolite blank must be very carefully cleaned and degreased. This can be done with a kitchen abrasive sponge (but not used for washing dishes on which fats have already accumulated) and a scouring powder like Pemolux. Very carefully, slowly three every square millimeter of foil, without touching it with your fingers. In general, I categorically do not advise touching the foil with your fingers after the start of cleaning, there should not be the slightest even the faintest greasy spot on it. After cleaning, rinse thoroughly in running water, shake off excess water and allow to dry. I do not advise blotting or wiping with anything, because. grease can be applied, even from a new napkin.
3.2 Application of photoresist
Also a fairly common topic on the Internet, so I'll go over it briefly.
Photoresist usually comes in sheets or rolls. It consists of three layers - two protective films and the photoresist itself between them. A piece is cut off from the photoresist according to the size of the board + 5 mm in length and width, then a matte (polyethylene) protective film is removed from it.
the second, glossy (lavsan) must remain on it until the etching stage.
The easiest way to remove the film is with a piece of tape. It is glued with its edge to the corner of the photoresist and then folded back, pulling the protective film along with it.
After removing the matt film, the photoresist is applied to the edge of the board and smoothed along this edge with a finger. The rest of the photoresist is supported by weight, without tension, but in such a way that as little as possible of its area lies on the foil.
Please note that if the Ordyl photoresist falls on a well-prepared textolite, then it can firmly stick to it, and without bubbles it can no longer be rolled. You have to scrape it off and do it all over again. And PF-VShch can fall as much as you like - it definitely won't stick :)
Now the knurling itself. If you have a laminator, in which the textolite will crawl through the thickness, then it's just wonderful. We make an envelope-type strip of paper folded in half, put a textolite with a sticky edge of the photoresist in it, and serve this sandwich into a laminator heated to 100-110 degrees. At the same time, we continue to hold the photoresist so that it comes into contact with the textolite foil only directly at the inlet of the laminator.
That's all for Ordyl, for PF-VShch it will be harmless to roll a couple more times.
If there is no laminator, then smooth the photoresist to the textolite with your finger from edge to edge, gradually lowering it onto the textolite. The main thing is not to catch the bubbles. After all the photoresist lay on the foil, we take a hair dryer and heat the textolite to 70 degrees, after which we iron the entire photoresist once again.
After knurling, let the textolite with photoresist lie down for 15-20 minutes, or at least until they cool down to room temperature - according to the recommendation of the photoresist manufacturer.
And now everything is ready to highlight the layer pattern :)
4. Printer highlights
I want to warn you right away: looking directly into the glowing display of a photopolymer printer may not be very good for the eyes. Although not true UV (405 nm), the brightness is quite noticeable and can be harmful to the eyes. Therefore, I recommend using colored or tinted goggles. I think even sunscreen will do.
First, you need to remove the bath and platform from the printer, they are completely unnecessary for this business and even interfere. This completes the preparation of the printer :)
Lighting also has different options. If you have a one-sided board and the blank is larger than the size required for the board, then everything is simple - throw the file obtained at the preparation stage into the printer and, knowing the approximate place for displaying the image on the display, put a textolite with photoresist in this place. Then start printing the file and wait until it is completed. Everything, the photoresist is exposed, it is possible to develop.
If the workpiece is equal in size to the board being made and the error with the position of the workpiece on the display is unacceptable, then in this case it is necessary to remove the frame during preparation, as is the case for a double-sided board. Illumination also occurs using a frame, similar to a double-sided board, only without the second side and the second layer.
So, the illumination of the double-sided board. We throw all three files into the printer - with a frame, with the first layer and with the second layer. We put the workpiece next to the printer in quick accessibility. If it is already pre-drilled, it will be useful to make sure that it lies in the correct position so that you can quickly take it and immediately put it on the display. To do this, we run a file with a layer planned for exposure, and compare the layer pattern on the display and the orientation of the board next to the printer.
Printing a file with one frame. As soon as the frame lights up on the printer display, we take the workpiece and put it approximately inside the frame. While the frame is being illuminated, we align the workpiece so that it is exactly in the frame, with the same indentation of the frame from the edges of the workpiece on all sides.
In the photo, I gave an example with a ready-made board, because I did not take pictures during the manufacturing process. Well, reflections interfere quite strongly, alas... But I think it's understandable :)
That's it, the position of the workpiece is verified, printing of the frame file can be interrupted or wait for it to finish. Without moving the workpiece, run the file with the first layer and wait for it to finish. We illuminate the second layer (the second side) in the same way - we launch the frame, place and align the workpiece, without moving it, we launch the second layer. Before this, just in case, you can make sure that the workpiece will lie in the correct orientation, as before the first layer.
If the workpiece is not completely flat and does not fit the entire area of the display, then you can press it down from above with some heavy flat piece of iron. You just need to make sure that this piece of iron does not interfere with the platform lever, which will go down with the start of printing - the printer thinks that this is a normal photopolymer print and you need to lower the platform to the bottom of the bath :)
Illumination time can be different from printer to printer . It depends on the power of the emitter, and on the optical illumination system, and on what type of display is worth - monochrome or RGB. Here already it is necessary to select each individually. For orientation, I can say that I got the best result with the Ordyl photoresist at an exposure time of about 90-110 seconds. With photoresist PF-VShch - about 10-13 minutes. Printer with paraled, illumination power slightly less than 50 watts.
After exposure, the workpiece should be allowed to rest for 15 minutes - this is according to the recommendation of the photoresist manufacturer. Ordyl changes the color of the highlights quite noticeably, so it's pretty easy to control the highlights. Unfortunately, the photo did not convey it well, it can be seen better with the eyes.
5. Development, etching
Everything here is according to the recommendation of the photoresist manufacturer and according to the classics of the Internet.
All necessary chemicals were purchased inexpensively from Auchan. Even hydrogen peroxide 6% - this was a surprise for me, I had never seen it in hypermarkets before, and even in liter bottles.
For one session you need:
-
Soda ash - 1.5 grams
-
Hydrogen peroxide - 150 ml for 3% (or 75 ml for 6% + 75 ml of water)
- citric acid
-
Salt - 7.5 grams
-
Alkali (caustic soda, sodium hydroxide) 5-7% - 100 ml
With the cheapness and ease of buying all the components around the corner, I am in favor of preparing a new solution for each board. Although the etching solution, as they say, is not stored anyway. A solution of soda ash noticeably "poorer" in the process of development. Unless caustic soda can be reused, but is it worth it to keep another bottle ...
Both Ordyl and PF-VSH appear in a weak solution of soda ash. For PF-VShch - 1-2%, for Ordyl - 0.8-1.2%. For Ordyl, we take 150 ml of water and dilute 1.5 grams of soda in it. The solution can be heated up to 30 degrees, this will speed up the development, but it is important not to overdo it, otherwise the illuminated areas may begin to be damaged.
Ordyl appears rather quickly. Already after 10-15 seconds, the illuminated pattern begins to become more and more contrasty, the unexposed areas gradually dissolve, become thinner and become paler.
To speed up the process, it is recommended to shake the bath so that the reaction products are washed off the surface of the workpiece. For this I adapted my old 3D printer, its table and shook and heated the bath with the solution during development and etching :) Two minutes passed before there were at least some signs that development had begun. In addition, if Ordyl does dissolve, then PF-VShch first swelled like gelatin and discolored, and only then began to slowly dissolve.
At the end of development, you can go over the boards with a hard paintbrush (or soft toothbrush) several times in different directions to help flush out any remaining photoresist from tight spots. Ordyl holds on tight, this procedure should not disrupt it, but with PF-VShch you need to be very gentle, even without a brush it strives to exfoliate on thin paths.
After etching, the workpiece must be rinsed in cold water so that the soda residues do not continue to attack the photoresist and so as not to clog the etching solution with them.
The result should be something like this, maybe even better :)
More detailsScale of the grid square - 0.2 mm:
The scale is the same. Here you can see the raster component of the illumination, the pixels stick out:
Etching was also done according to the traditional recipe, popular on the net:
It is better to heat the solution to 40-50 degrees, then the etching goes much faster. This is my first experience with this solution. I used to poison with ammonium perchlorate, and even earlier - with classic ferric chloride. To be honest, I can't really express how I feel about this solution. On the one hand, it poisons rather quickly, is transparent, does not get dirty, and is relatively safe. On the other hand, it seemed to me that it was easing quite a lot ... But maybe it just seemed, I haven’t been making boards for 10 years and I forgot how it all worked when the trees were big :)
After etching, the exposed photoresist must be removed from the workpiece, and this is done in caustic soda.
On my bottle of cleaner it says "at least 5% but not more than 15%" and it takes 5-8% to remove the photoresist. I diluted the product 1:1 with water and this solution did the job perfectly. The photoresist does not dissolve in it, it simply peels off the foil after 2-3 minutes and begins to float in tatters in the solution.
After that, the board is thoroughly rinsed under the tap and... The board is ready!
Summary of my experience
Overall I am satisfied. I did not expect to get tracks / gaps of 0.1 mm and I did not get them. Here, the capabilities of the printer are severely limited (pixel size), and in general, good experience is needed for such results. But I was hoping to get at least 0.2 mm, and if I'm lucky, then 0.15 mm - and I got it. 0.2 mm confidently, 0.15 mm - well, so-so... If you try, you can achieve :)
There were some flaws - it was not pickled in some areas, and imperfect alignment of layers and holes. But neither is critical. As for the non-mordant - I think that I just hurried to take it out of the developer, I was afraid after PF-VShch that thin paths would begin to peel off.
Although in the reviews people write that it is quite difficult to re-develop this Ordyl, you need to try for this. Imperfect alignment of layers and holes is to be expected. From such a simple method of alignment, I expected an error of 0.1-0.2 mm, which I got, but it suits me.
Thank you for reading.
And finally, a few photos of my results. Exposure time test, from 1 to 2 minutes. You can see the sites displaced relative to the holes. printerI'll tell you how you can make a board at home using Delta Design. The order of work is something like this: Delta Design -> DeltaCAM -> FlatCAM -> 3D printer with laser pointer . In my hobby, I periodically need to make prototyping boards to test and / or connect microcircuits with minimal strapping, in this case, an example will be for connecting a MAX5725 DAC.
As a final result, we need to get a gerber file for one layer of copper and, possibly, another layer for a protective solder mask, but why bother with trifles - then also prepare the silkscreen and make a stencil for the paste .
.. but that's for another time.
It all starts with the component library. Footprints for SMD components do not differ much from those for a multilayer board or a single-sided, more precisely, single-layer, except for different soldering modes - manual, paste, wave, or something else. For home use, manual soldering is more often used or on paste, also manual, i.e. not automated. But with DIP components, things are different, because. there is no plating in the holes, and in order for the platform to hold the component well, its size is increased. Thus, for hand soldering and single-layer boards without hole plating, it is reasonable to make a separate library of components. Yes, and the set of rules will have to be corrected in order not to make paths too thin without urgent need, because. the wider the traces and gaps, the easier it is to control the PCB manufacturing process. Further, the process of designing a printed circuit board is no different from the industrial version.
What Delta Design lacks for single layer boards is automatic SMD and/or DIP jumper placement. But even without this, it is possible to design a board, however, it is not very comfortable, if I may say so.
When the library is prepared, we start creating the board. Everything is simple here, the main thing is not to forget to immediately indicate the 3rd class of accuracy - it is quite feasible for home production.
In addition to the rules, you can also choose the format right away, if the scheme is not large, then I choose the A4 format:
Let's move on to creating a circuit and a printed circuit board layout - this is a creative process and everyone does it in their own way. Prepared the circuit and board:
On the DOCUMENTUM layer, I added graphics - text and a circle for later merging on the copper layer along with the PCB layout.
The only thing you need to pay attention to is the choice of grid for the board editor.By default, there is only a millimeter grid, but often you have to make boards with pin connectors like PLS. And then I insert such scarves into the circuit board with holes with a pitch of 2.54 mm or connect them with wires with Dupont connectors. So, in order to put the connectors at the right distance, a multiple of 2.54 mm, it would be convenient to switch the grid to this step and arrange the connectors. The grid setup for the board needs to be done in the standards once:
There's a tricky grid setup relative to the base grid:
Added grid 1.27 and 2.54. The mesh can now be toggled in the PCB editor in the lower left corner.
About once, I lied. Delta Design is frequently updated and needs to be reinstalled frequently. Therefore, if you set it up for yourself once, then you need to export the standards to a DDS file and, after the next update, import the standards before starting work with the new version of CAD.The board is designed, the only thing left is to upload Gerber files to production .
.. But there are also a few points here, which I will dwell on in more detail. For a single-layer board, I usually combine the outline of the board, the copper layer and graphics, for example, put a logo or make inscriptions. In addition, checking the output gerber file in the viewer is also useful.
In Delta Design, export to gerbera is called differently: “Create Production Files”
In the form, select which layers you want to display and indicate that all this should be saved in the project tree. If you need to look at the files in an external viewer, you can choose to save the files to disk.
After creating the production files, a line with the factory icon appears in the project tree:
Open this item and see all the layers that we have selected. This is a DeltaCAM Gerber file viewer and editor already built into Delta Design.
Here you can already transfer the graphics from one layer to another.Select the desired layer with graphics, select all the necessary objects and change the layer for them in the properties:
Thus, we transfer everything to the SIGNAL_TOP layer. The peculiarity of this operation is that during such an operation there is no conversion of graphics and objects in the Gerber file. They are simply transferred without changes.There remains one more necessary operation - this is the addition of holes on the apertures of DIP components for subsequent drilling at home - the hole must be smaller than the diameter of the drill, because. it is only needed to guide the drill while drilling the board. To do this, in the aperture editor, find the necessary apertures and change their hole diameter.
In this example, two apertures are needed for drilling - an oval and a rectangle, DCode 5 and 16, respectively. We make the hole diameter minimal and sufficient for etching at home. This operation also does not change the graphics of the Gerber files, as simply complements the parameters in the description of the aperture according to the Gerber standard.As a result, we immediately see the changes:
The board is now ready for production. We upload the Gerber file of the desired layer and prepare it for making a photomask, a picture for a LUT, or for laser illumination on a home CNC machine, such as a 3D printer. Uploading the edited layer to a file is done through the creation of production files, only not according to the board, but according to the CAM project:
We select one layer, because. we threw everything there and create it as a Gerber file.Further, the ways of manufacturing a printed circuit board may differ. In my example, I will illuminate the photoresist using a UV laser pointer installed on a 3D printer. There is no functionality in DeltaCAM with which you can generate a GCode for execution on a CNC machine, for this stage I use FlatCAM (http://flatcam.org). Details about connecting a laser pointer, GCode preparation described in another article.
I note that FlatCAM does not support holes in apertures, which is written on their website: http://flatcam.Learn more