3D printer fiber reinforced
What You Need to Know
A Brief Composites Fiber Lesson
As we covered in Physics of 3D Printing, imagine the fiber is like raw spaghetti. If you try to bend it, it snaps. If you try to compress it lengthwise by trying to push the two endpoints closer together, it also snaps. However, if you load it in tension by pulling on it, it can hold a decent load. Like the spaghetti, continuous fibers are strongest when loaded in tension. The key is understanding where the fibers are loaded in tension, and how a given load can distribute amongst the local fibers.
Continuous fibers act strongest in tension, just like raw spaghetti.
Types of Fiber Fill
Eiger, the Markforged 3D printing software platform, provides a few options for reinforcing your parts with continuous strands of composite fibers. Each reinforcement strategy can be applied to a layer or group of layers in a part. The different reinforcement options allow you to strategically place fiber so that you can optimize the reinforcement method for your part's loading conditions.
Different fiber fill options will reinforce a given layer with a different reinforcement strategy.
Concentric Fill
Concentric Fill lays fiber around the perimeter of a wall. This fill type mainly helps resist bending about the Z axis and strengthens the walls against deformation. You can specify how many fiber shells you want by changing the number of concentric fiber rings. You can edit the start point of the fiber by changing the "Start Rotation Percent" setting when viewing a 2D layer slice or group in Internal View.
All walls: This type lays down fiber to reinforce both the outer shell and the inner holes, providing the reinforcement properties of both.
Outer shell only: This type only reinforces the outer walls of a part. This can be used to reinforce the part for bending or impact loads applied to the sides of the part.
Inner holes only: This type only reinforces the inside walls of a part. This can be used to strengthen bolt holes or cavities to improve load distribution when compressive or out-of axis torsional forces are applied to inner holes.
Isotropic fill
Isotropic fill routes fiber back and forth in a zig-zag pattern to simulate the individual unidirectional layers of a traditional laminated composite. By default, subsequent isotropic fiber layers rotate the fibers by 45 degrees to achieve unidirectional strength within a fiber group, but the fiber angle (the orientation of the zig-zag pattern of the fibers) can be changed if needed. Layers of isotropic fill fiber resist bending in the XY plane. In addition to the isotropic fill pattern, this option by default traces concentric rings around all walls to improve wall strength.
Types of Fiber
Your choice of fiber impacts the behavior of your part. It can affect strength, stiffness, failure condition, and even heat resistance. Selecting the best fiber for your application is an important factor in your part's performance. Watch our webinar on selecting a fiber fit for your application, or check out or material data sheet for more.
Carbon Fiber
Carbon fiber has incredible strength to weight properties. It is a very stiff material that remains close to rigid until failure, in which case it often fractures or splinters. It's best used in constant loading conditions when you want to match the strength of metal at a fraction of the weight, since it behaves like 6061 aluminum.
Carbon fiber can match the strength of 6061 aluminum - in this test, both beams are loaded with a 27.5 lb weight.
Fiberglass
Fiberglass is a robust reinforcement option that has a bit more flex and energy return to it than carbon fiber. It's best used in intermittent loading conditions, and bends until eventual fracture. Fiberglass is a great general-use fiber for when you need sturdy parts, and it is the most cost-effective reinforcement option.
Fiberglass is s good starting point fiber, already 2-3 times stronger than traditional 3D printing plastics. Each of these was tested with a 7.5 lb weight.
Kevlar
Kevlar is a very shock-resistant material ideal for impact loading or similar use cases. It is very tough, and will fail by bending until it eventually permanently deforms.
Kevlar is ideal for impact or shock loading cases. Here we test a PLA, ABS, and Kevlar reinforced puck for toughness.
High Strength High Temperature (HSHT) Fiberglass
HSHT Fiberglass is a heat-resistant fiber reinforcement material. It has a higher heat-deflection point than the other fibers, meaning it can hold its strength at high temperatures. It is similar to fiberglass in that it has high energy return and will bend until it fractures.
HSHT has a high heat deflection temperature. Each of these beams was heated to 300 degrees Fahrenheit before being tested with a 5lb load.
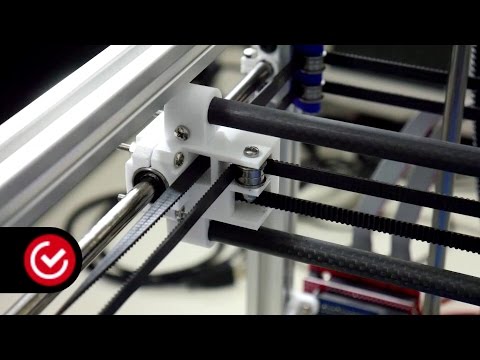
Reinforcing For Different Loading Conditions
Tension
Align your fibers with your tensile force.
Fibers are strongest in tension, so a part loaded in tension should consist of fibers running up and down the length of the part, being “stretched” by the force. You can align fibers with your tensile forces with concentric rings along ribs or with isotropic fiber by setting the fiber angle parallel to the force.
Bending
Place fiber planes on the extreme faces experiencing bending.
Beam Bending Theory shows that when a beam is bent, the inside face of the bend is loaded in compression, while the outside face of the bend is loaded in tension. By putting rigid materials on the extremes of a beam you reinforce it most effectively. This is why traditional composite layups consist of fiber panels on each face with a softer material on the inside, forming what is called a sandwich panel. To reinforce a part in bending, build a sandwich panel with isotropic fiber panels if the neutral plane is in XY, or concentric fiber when bending around the Z axis.
Compression
Build a scaffold of fiber to reinforce against compressive forces.
The key to dealing with compressive forces is in the force distribution. The fiber should serve as a scaffold beneath the load, able to distribute the load along the fiber’s path. Side loads can be reinforced from compression with concentric reinforcement. Vertical loads can be reinforced from compression using isotropic reinforcement on the upper and lower faces, and concentric reinforcement between the two Isotropic panels to further support the load. This is especially helpful for supporting clamping forces from bolts.
Fiber Anisotropy
Think critically about how your part is oriented when reinforced with fiber, because anisotropy is still at play.
Markforged 3D printers print composite parts that are effectively transverse isotropic. While isotropic materials have uniform material properties in all directions, transverse isotropic materials have one set of properties along an axis, and a different set on planes normal to that axis. This translates to 3D printed parts, in which the part strength on XY planes is stronger than the part strength along the Z axis, especially with continuous fibers. This is why it’s important to consider print orientation during the design process.
Fiber™ | Desktop Metal
_Fiber™ applications
Fiber™ applications span a variety of industries including manufacturing, tooling, automotive, consumer, electronics, and marine.
-
Brake Duct
PEEK + CFFound on a BMW hill climb car, this duct reroutes air from the front of the car to cool its brakes.
Brake Duct
-
Size (mm) 130 x 63 x 97
Cost ($) 54.
92
Weight (g) 65
Print time (hr) 11
-
Printing on Fiber enables optimization for the most efficient air flow, leading to better cooling. Brakes get extremely hot during competition, PEKK + CF provides heat resistance and is lighter than an aluminum alternative.
-
Ski Binding
PA6 + CFThe ski binding heel track attaches to the base plate on a ski, allowing the heel binding to be adjusted.
Ski Binding
-
Size (mm) 143 x 57 x 10
Cost ($) 6.
24
Weight (g) 25
Print time (hr) 5
-
Ski bindings need to be extremely stiff to withstand the forces experienced by the ski as it turns, making composites an ideal choice.
Using Fiber™, manufacturers can prototype this part before it is mass produced via injection molding.
-
Rocket Tail Cone
PEEK + CFThis part sits at the end of a rocket, redirecting air for optimal aerodynamics
Rocket Tail Cone
-
Size (mm) 155 x 155 x 157
Cost ($) 297.
08
Weight (g) 350
Print time (hr) 31
-
This part has to withstand the extreme heat of a rocket engine, so it must be fabricated using a high temperature material like PEEK. With the design freedom of Fiber, engineers were also able to add complex features to improve aerodynamics.
-
Curling Whip
PA6 + FGUsed in wheelchair curling, this part allows athletes to push curling stones from a seated position.
Curling Whip
-
Size (mm) 129 x 46 x 33
Cost ($) 11.
24
Weight (g) 37
Print time (hr) 7
-
The shape and weight of the whip are critical to the athlete’s performance. Plastic alternatives often break during competition and machined aluminum requires long CNC milling lead times and labor.
Fiber enables the rapid production of custom whip geometry, while continuous fiberglass reinforcement provides a lighter and stiffer alternative to aluminum.
-
Mirror Mount
PA6 + CFThis part attaches a rear-view mirror to the roll cage on a BMW race car.
Mirror Mount
-
Size (mm) 75 x 97 x 37
Cost ($) 6.
47
Weight (g) 65
Print time (hr) 10
-
Printing this mount on Fiber delivers a part 4X lighter than the original aluminum design, while maintaining strength and durability. In racing, weight is everything, and reducing weight leads to faster times.
-
Surfboard Fin
PA6 + FGA hydrofoil mounted on the underside of a surfboard, the fin enables foot-steering and improves stability.
Surfboard Fin
-
Size (mm) 143 x 120 x 6.
8 mm
Cost ($) 11.05
Weight (g) 31
Print time (hr) 5
-
Printing on Fiber enables rapid functional prototyping of the many variables that affect surfboard performance - the fin’s rake, cant, base length, height - and greatly speeds the process when compared to traditional hand layup.
Composites are ideal for this part due to their high strength. In this case, the part is made from PA6 nylon with fiberglass reinforcement to keep costs low and to resist corrosion.
-
GRIT Lever Connectors
PA6 + FGA pair of these level connectors are used in custom, all-terrain wheelchairs.
GRIT Lever Connectors
-
Size (mm) 86 x 89 x 47
Cost ($) 12.67
Weight (g) 78
Print time (hr) 12
-
All-terrain wheelchairs manufactured by Grit are powered entirely by the user - making weight reduction, strength, and stiffness critical to performance. Traditionally machined out of aluminum in custom low quantities, these level connectors typically require a multiple week lead time.
Printing on Fiber in fiberglass-reinforced PA6 enables shorter lead times, reduced weight and greater customization - all while increasing part strength and stiffness.
-
Balance Shaft Gears
PEKK + CFThis part is a balance shaft gear used in an automotive turbocharger to reduce vibration.
Balance Shaft Gears
-
Size (mm) 117 x 117 x 15
Cost ($) 53.37
Weight (g) 63
Print time (hr) 11
-
Printing in PEEK delivers a lighter part compared to metal counterparts, while still meeting the strength and heat requirements.
With the ability to print industrial-grade composites like PEEK with continuous carbon fiber reinforcement, Fiber™ allows engineers to print parts that can stand up to high temperatures and have unrivaled part strength - without spending tens of thousands of dollars.
-
Press Brake Tooling
PA6 + CFThese press brake tools are used to bend aluminum sheet metal.
Press Brake Tooling
-
Size (mm) 95 x 127 x 80, 91 x 64 x 51
Cost ($) 162.
6, 46.73
Weight (g) 364, 105
Print time (hr) 33, 11
-
Many sheet metal applications require custom press brake tooling, but machining this custom tooling out of metal for short runs can be prohibitively expensive.
For low tonnage applications, printing on Fiber eliminates the need for machining costly metal tooling, greatly reducing manufacturing lead time and cost.
-
Bike Pedal Crank
PA6 + FGConnecting arm responsible for attaching a pedal to the rear wheel crankset of a bike.
Bike Pedal Crank
-
Size (mm) 205 x 46 x 24
Cost ($) 22.
82
Weight (g) 66
Print time (hr) 9
-
Shedding weight is critical for performance bikes. Composites are an ideal choice for bike components like this due to their high specific strength and stiffness.
Printing on Fiber in fiberglass-reinforced PA6 allows for the manufacture of a corrosion resistant, low cost, functional prototype without the typical labor-intensive process of hand layup.
-
Assembly Fixture
PA6 + CFThis fixture is used to hold a sheet metal housing while fasteners and electronics are installed.
Assembly Fixture
-
Size (mm) 80 x 61 x 14.3
Cost ($) 2.24
Weight (g) 15
Print time (hr) 3
-
Assembly fixtures improve consistency and speed operator assembly by holding the work piece in the same location for each unit.
By printing the part on Fiber, the fixture can be manufactured extremely quickly and affordably while still conforming to the exact dimensions of the housing being assembled.
-
Skydiving Camera Mount
PA6 + GFThis mount attaches a camera to the helmet of a skydiver.
Skydiving Camera Mount
-
Size (mm) 64 x 84 x 14
Cost ($) 3.89
Weight (g) 16
Print time (hr) 3
-
Glass fiber reinforced PA6 allows for high specific stiffness to withstand those forces at a low cost. This part has to support the weight of the camera while being hit with 100mph+ winds during free fall.
-
BattleBots Bot Motor Housing
PEEK + CFCreated for a BattleBots, this motor housing was custom-designed to hold an electric motor.
BattleBots Bot Motor Housing
-
Size (mm) 108 x 128 x 24.3
Cost ($) 63.68
Weight (g) 75
Print time (hr) 10
-
This part holds a motor in place on a combat robot used in the Discovery Channel program, BattleBots. During competition, the bots are subjected to competitors weapons, including saws, axes, and flamethrowers. To withstand the significant stresses and heat, PEEK with Carbon Fiber reinforcement was selected.
On the show, BattleBots teams have very limited time to design and manufacture their bot, so utilizing 3DP is essential. By printing this motor housing, the team was able to get the part in their hands in just a few hours. This allowed them to quickly iterate on the part.
-
UHF Housing
PEKK + CFUltra high frequency radio housing for use in a cubesat.
UHF Housing
-
Size (mm) 95 x 67 x 36
Cost ($) 60.51
Weight (g) 54
Print time (hr) 20.
6
-
Due to the extreme temperatures this part will face in space, this part was printed using PEKK.
Printing this part allowed the cubesat team to quickly iterate on the design in its intended material, and producing multiple variations in a matter of days. The complex geometry and small features of this part make it ideal for printing.
-
Shroud Holder
PA6 + CFThis fixture is used to hold metal injection molded shrouds for secondary machining operations.
Shroud Holder
-
Size (mm) 143 x 30 x 22
Cost ($) 6.
71
Weight (g) 45
Print time (hr) 7
-
Designed to hold metal injection molded shrouds in place as an articulated robot picks them up and places them in a CNC fixture. This part features customized geometry that conforms to the shrouds’ shape.
Due to their stiffness and wear resistance, composites are ideal for this part.
-
Heat Shield
PEEK + CFThis heat shield protects the surrounding area of the car from hot exhaust.
Heat Shield
-
Size (mm) 187 x 142 x 83
Cost ($) 18.
72
Weight (g) 22
Print time (hr) 5.25
-
This heat shield can be produced in just a few hours, drastically reducing manufacturing lead time.
The original aluminum heat shield became hot enough to char CF components under the car. PEEK + CF is far less conductive than aluminum, solving this problem and saving weight at the same time.
-
Machining Fixture
PEEK + CFThis fixture holds lock barrels in place during a secondary reaming operation.
Machining Fixture
-
Size (mm) 212 x 72 x 26
Cost ($) 62.
31
Weight (g) 145
Print time (hr) 18
-
To achieve desired tolerances, metal injection molded (MIM) parts, such as lock barrels, often require secondary machining operations. The fixtures for these operations must be very stiff to hold lock barrels steady while experiencing the forces and vibration of the reamer.
By printing the part on Fiber, the fixture can be manufactured overnight, with similar material properties to aluminum saving both time and money
-
Rocket Fin
PEEK + CFCustom rocket fin used for an experimental testing rocket.
Rocket Fin
-
Size (mm) 129 x 48 x 6
Cost ($) 22.47
Weight (g) 14
Print time (hr) 2.5
-
Fins are critical to keep a rocket stable in flight, but must be custom designed for each rocket to ensure optimal flight. Rather than solely relying on simulations to determine how fins will perform, 3D printing enables designers to create functional prototypes and iterate on geometry based on testing.
With its high specific strength and temperature resistance, carbon fiber reinforced PEKK is an ideal choice of material.
Carbon Fiber Reinforced Nylon - An Ideal Metal Substitute
Nylon is a tough polymer material for 3D printing, but when mixed with carbon fiber, you can combine the benefits of both. 3D printed nylon carbon fiber parts have good mechanical properties. The strength and hardness are much higher than those of non-reinforced nylon, and the wear resistance, creep resistance and thermal stability are greatly improved. In addition, carbon fiber reinforced nylon has excellent wet properties in 3D printing and has better performance than glass fiber reinforced nylon. nine0003
Benefits of carbon fiber reinforced nylon
When developing tools for industrial applications, traditional technologies used aluminum or alternative metal alloys because the metal parts perform better and meet the requirements of the tool. In many cases, thermoplastics can meet the strength requirements of such tools, but cannot meet the mechanical requirements. nine0003
Data sheet for Eplus3D PA11 Black CF
This is where composites come in. The addition of reinforcing elements to the base polymer can significantly change the properties of the original material, allowing plastic parts to replace metal parts. At present, commonly used reinforcing materials include carbon fiber and glass fiber, which can be used to reinforce ABS, nylon (PA), polypropylene (PP), polyetheretherketone (PEEK) and other materials. nine0003
3D printed carbon fiber and nylon watch mount
Carbon fiber reinforced nylon is an ideal substitute for metal. By combining the lightness of nylon and the mechanical strength and thermal properties of carbon fiber, the strength and hardness of the carbon fiber composite nylon material has been greatly improved, and its mechanical strength is even higher than that of 3D printed PEEK and PEKK. In the automotive industry, metal parts can be exchanged from internal and external parts such as automotive mounting frame and instrument to engine housing. As we all know, carbon fiber is widely used in automotive industry due to its strong thermal and mechanical properties. As a substitute for metal parts, carbon fiber-reinforced nylon has broad application prospects in the automotive industry, allowing for weight reduction and design optimization, as well as environmental and economic benefits. nine0003
E Plus3D EP -P420 SLS 3D Printer
Eplus P420 SLS 3D Printer is high -class equipment for industrial production and scientific research. We offer advanced printing technologies and various resin materials, including PA12, PA12GF, PA11, PA11CF, TPU, etc., with high mechanical properties for functional testing and final products.
Large Format Raise3D RMF500 for 3D Printing with Carbon Fiber Reinforced Materials
Last fall, a well-known Chinese manufacturer of 3D printers, Raise3D, announced a new 3D printer for small-scale production in the industrial sector - RMF500 . The unique feature of the novelty is the combination of the ability to print with carbon fiber reinforced material (colloquially carbon fiber), wide format and affordability .
We all know that high technology is becoming more accessible every day, and the RMF500 is a prime example of this. There have been systems on the 3D printing market for several years that print carbon fiber composites of similar quality, but, unfortunately, they are not available to all companies due to the very high cost and supply problems. For example, such professional 3D printers are produced by the American company Stratasys - Fortus 450mc, but they are equipped with less technological features and are much more expensive. nine0003
Let's take a closer look at what the RMF500 is and how it differs from other 3D printers.
The RMF500 is specifically designed for printing complex parts with high durability. It will enable 3D printing companies to expand their product portfolio with carbon fiber and fiberglass end parts. Both materials specially developed by Raise3D, such as PA12 CF, and materials from other manufacturers approved by Raise3D under the Open Filament Program (OFP) will work. Parts made of carbon and fiberglass are more rigid, durable, resistant to heat and shock than parts made of other plastics. For carbon and fiberglass printing, the RMF500 uses silicon carbide nozzles with a hardness of more than 60 HRC. nine0003
PA12 CF filament is the result of long-term development by Raise3D engineers. This is a carbon fiber reinforced filament with increased stiffness and reduced shrinkage and does not require a thermostatic print chamber. The parts obtained from it are light and extremely durable, sometimes they can even be used instead of metal. In addition, the company has developed the PPA GF glass-filled filament specifically for the RMF500 and plans to release PET-CF, ASA-GF, PPSU-GF and PP plastics for medical use. Raise3D promises that all fiber reinforced plastics will be competitively priced. nine0003
The RMF500 has a huge building area 500x500x500 mm. The size of the build area matters in the production of large parts and small-scale production. For comparison, the print area of the Fortus 450mc is 406x355x406mm.
In the photo: printing a large model with carbon fiber in the RMF500 3D printer from Raise3D.
Repeatability and print speed are very important for low volume production. The maximum print speed of the RMF500, according to the manufacturer, can reach 300 mm/s. Positioning accuracy along the XY axis - 1 micron, along the Z axis - 0.09765 microns.
Synchronous feedback control with 1 µm accuracy reduces speed fluctuations as motor load changes, further improving accuracy. Stability and repeatability of printing has long been a hallmark of Raise3D printers. The FFF technology on which this 3D printer is based allows the production of parts with a high degree of repeatability, high positioning accuracy and uniform extrusion. The RMF500 can quickly print large batches of identical parts. nine0003
Pictured: production of lots from a large number of parts on the RMF500.
The printer has a printing system with two independent IDEX extruders. It allows you to print with one or two extruders at once. The RMF500 can run two jobs at the same time, further increasing productivity and task speed. The extruders are manufactured using high temperature alloys and industrial ceramic composite materials. These characteristics provide stable and high extrusion speed up to 500 g/h. nine0003
The RMF500 has a strong design . The one-piece frame is made of hardened steel. Stainless steel linear guides have a design load of approx. 100 kg. The bearing of the linear guides has minimal backlash and does not require frequent maintenance.
An important detail - Raise3D has developed special support material for printing with reinforced plastic PA12 CF, which can be easily detached.
Pictured: Parts printed on the RMF500 with PA12 CF filament with special proprietary support. nine0073
The RMF500 is equipped with four large compartments for plastic spools. Switching between the main and auxiliary compartments occurs automatically. This feature reduces the amount of time spent threading the filament. The humidity control system keeps the relative humidity in the chamber below 5%, preventing humid air from entering from outside.
What else is there in the RMF500 from nice additional options. The front of the printer has a large 13.3-inch touch screen. Supports connection, management and printing via Wi-Fi and LAN. There is a reliable auto-calibration system from Raise3D. nine0003
Carbon fiber printed parts are strong enough to be used in the automotive and aerospace industries. Of course, they will not replace functional parts that have a special load, but their scope can be very wide. Raise3D has already presented the results of the first RMF500 printing and its application.
Pictured: Functional parts, accessory tools and fixtures, car décor printed on the RMF500. nine0073
Pictured: Functional parts, accessories and aerospace prototype printed on the RMF500.
In the photo: on the left is a prototype of the hinged window mechanism (details are printed with metal filament and carbon fiber), on the right is a carbon fiber fixture. Carbon parts printed on RMF500, metal parts printed on Metalfuse. Printing with fiber-filled plastics does not require a heated chamber, peak power consumption is less than 3 kW. The average power consumption per unit of print area of the RMF500 is 60% lower than the competition. nine0130
