3D printed rocket engine
Careers
Scroll
CAREERS
CAREERS
View Open Positions
Relativity team members at our hangar at Launch Complex 16 in Cape Canaveral, FL
Celebrating World Creativity and Innovation Day 2022, Long Beach, CA Headquarters
Propulsion Test Technician working on our engine at our test facility in Stennis, MS
GO/NOGO polling from the control room at Cape Canaveral, FL
2022 Aerospace Games in Long Beach, CA
You're a multihyphenate human who thrives where engineering meets creativity. And we at Relativity defy labels, exceed expectations, and push through boundaries. From day one, you'll get to work on cutting-edge technology and solve complex problems in creative ways that haven't been done before. By creating the world's largest metal 3D printers, Relativity is taking 3D printing to new heights, starting first by creating orbital rockets, Terran 1, the world's first 3D printed rocket and Terran R, the first fully reusable, 3D printed rocket. With the ultimate goal of building humanity's multiplanetary future, Relativity is expanding the possibilities of the human experience by upgrading humanity's industrial base on both Earth and Mars. Want to create new worlds while protecting our own? Join our team and help create the future of manufacturing.
As a partner of NASA’s Stennis Space Center and the U.S. Air Force, Relativity operates multiple production, test, and launch sites across the country. Whether you want to work at our headquarters in California, our testing facilities in Mississippi, or our launch complex in Florida, Relativity has a spot for you.
AUDACITY
Challenge convention in pursuit of an expansive future.
RELENTLESSNESS
Focus on achieving intentionally meaningful results.
WONDER
Approach the world with awe and a deep desire to create.
Humanity
Expand possibilities for the human experience in this world – and beyond.
We are committed to our team member’s health, well-being, and growth.
COMPREHENSIVE BENEFIT PACKAGEWe offer high-quality care plans for health, dental, and vision, and provide an additional stipend for employee wellness.
COMPETITIVE COMPENSATIONIn addition to receiving a competitive salary and 401(k), team members are eligible to receive equity.
WORK / LIFE INTEGRATIONWe observe 11 company holidays and have a generous PTO policy.
Our team connects and recharges with monthly lunches, game nights, holiday celebrations, and offsite events.
Parental Leave and Family Building
We offer generous parental leave and provide a $10,000 stipend for fertility, adoption, and other family-building benefits.
LEARNING AND DEVELOPMENT
Our $2,000 annual learning stipend allows you to develop your professional skills and accelerate your career. We also have constant training opportunities, company Lunch and Learns, and access to industry conferences.
We look forward to welcoming you and building a multi-planetary future – for everyone!
We believe empowering people from different backgrounds, identities, and perspectives will advance our mission and enable us to build the highest-performing team possible. Diversity, equity, and inclusion are integrated into Relativity’s DNA, and we continuously take steps to advance our culture of belonging internally and externally.
Through our Inclusion Champion Program and Inclusion 30 Conversations, our team members advocate for DEI and consistently drive our mission forward. By partnering with organizations like the Los Angeles’ Racial Equity & Newly Empowered Workplaces (RENEW) Task Force, Aerospace 2030, and the City of Long Beach’s Space Beach Mentorship Program, we seek to inspire and build a more inclusive future for aerospace.
Relativity team. Pride celebration at Long Beach, CA Headquarters
Full-time positions are listed below.
Relativity Space
Scroll
FACTORY OF
THE FUTURE
ROCKETS BUILT AND FLOWN IN DAYS
Relativity's proprietary Factory of the Future centers on Stargate, the world’s largest metal 3D printers, that create Terran 1, the world’s first 3D printed rocket, and the first fully reusable, entirely 3D printed rocket, Terran R, from raw material to flight in 60 days. Relativity’s Stargate printers’ patented technology enables an entirely new value chain and innovative structural designs that make Terran 1 and Terran R possible. By developing its Factory of the Future and rockets together, Relativity accelerates its ability to improve design, production, quality, and speed.
Zero fixed tooling and radical part count reduction
LEARN ABOUT TERRAN
POWERING THE STARGATE PRINTER
METALLURGY
Relativity developed multiple proprietary alloys custom designed for 3D printing to meet mission-critical performance.
UNIFORMITY
Parts are inspected during and after printing to ensure they meet the highest standards of uniformity and quality.
THE FUTURE IS 3D PRINTEDFor 60 years, aerospace manufacturing has relied on large factories, fixed tooling, complex supply chains, and extensive manual labor to build costly rockets comprised of 100,000+ parts in 2 years or longer.
To accelerate innovation in the industry, Relativity built its Factory of the Future, the first aerospace platform to automate rocket manufacturing, vertically integrating intelligent robotics, software, and data-driven 3D printing technology. Incorporating Stargate, the world’s largest metal 3D printer with AI-driven controls, our Factory of the Future continuously optimizes production, resulting in greatly compounded quality and time improvements, lower costs, and product designs previously not possible.
Relativity is an application-layer 3D printing company that is starting with rockets, and will extend its Factory of the Future to all of aerospace.
Rigid Factories, Fixed
tooling & HIGH Labor Costs
100,000+ Part Count
24 Month Build Time
48 Month Iteration Time
Complex Supply Chain
High Physical Complexity
ADAPTABLE, SCALABLE
AUTONOMOUS ROBOTICS
<1,000 Part Count
2 Month Build Time
6 Month Iteration Time
Simple Supply Chain
Software Defined Factory
CHANGING THE WAY ROCKETS ARE BUILT AND FLOWN
Custom designed
for printing
- High strength alloys specially designed for Stargate printers
- Physical properties designed to meet mission-critical structural requirements
- In-house material characterization lab for quickly iterating on new alloy development
- Relativity developed multiple proprietary alloys custom designed for 3D printing to meet mission-critical performance
- Parts are inspected during and after printing to ensure they meet the highest standards of uniformity and quality.
UNIFORMITY
REAL-TIME QUALITY CONTROL
AND PART INSPECTION
- Intelligent data-driven manufacturing
- Machine learning control algorithms
- Collaborative additive and subtractive process enables complex geometry
Collaborative robotics
and path planning
- Verification and validation data captured during manufacturing
- Flexible and highly scalable system architecture
- Cloud-based manufacturing simulation and training
3D printing of a large rocket engine using the SLM800 printer
Aerospace industry
Implementation stories
Author: Aleksey Chekhovich
Author: Aleksey Chekhovich
SLM Solutions, a manufacturer of metal additives, has produced what it claims to be the world's largest 3D printed rocket engine for British aerospace company Orbex.
The Prime commercial orbital launcher engine has been 3D printed as an all-metal product and will be used to deliver small satellites into orbit. The Prime rocket was recently officially unveiled during the opening ceremony of the new Orbex headquarters in Forres, Scotland, created with the support of the European Commission's Horizon 2020 Fund, the UK Space Agency (UKSA) and other private and public organizations.
At the ceremony, Graeme Turnock, Chief Executive of UKSA, said: “The new Orbex project complex is another step for the UK towards independent commercial rocket launches. This is the strengthening of its leadership position in Europe in the eyes of those who are looking to the Earth's orbit and beyond in search of new opportunities."
UK Space Agency Executive Director Graham Turnock speaks at the official presentation of the Prime rocket. Photo: Orbex
From an obscure startup to a $40 million investment
Orbex was founded in 2015 with the goal of launching commercial cubesats, small satellites with a mass of several kilograms, into earth orbit. The company operated "in stealth mode" until July 2018, when it announced it had raised £30 million ($40 million) in private and public funding. At the same time, information was officially confirmed that the UKSA would provide Orbex with the opportunity to launch from the Sutherland cosmodrome, using it in conjunction with an American competitor, Rocket Lab.
Thanks to 3D printing, Prime is 30% lighter and 20% more efficient than any other launch vehicle in its category
The Orbex Prime Lightweight Booster is powered by liquid oxygen and propane, a gas that is a non-toxic and cheaper alternative to hydrogen. Like many modern rockets, the Prime upper stage is designed to be reusable, reducing the amount of waste generated during the launch process.
With a height of 19 m and a diameter of 1.3 m, the Prime rocket is capable of delivering a payload of 150 kg to an altitude of up to 500 km. In this regard, it is comparable to Rocket Lab's Electron rocket, which has a payload of 150 to 225 kg, but it should be noted that the two rockets use different types of fuel.
Prime Rocket Engine 3D Printed
The Prime rocket engine was printed by SLM Solutions on the SLM 800 large format 3D printer. The SLM 800 build chamber is 260x500mm and can print parts up to 800mm high, which is what the Orbex engine needs.
A close-up of the Prime rocket engine printed as one piece. Photo: Orbex
The motor was made from a nickel alloy, and the additive manufacturing method allowed Orbex to spend 90% less time and cut costs by more than 50% compared to traditional CNC machining. In addition, according to experts, this way of manufacturing the engine made it possible to make the Prime rocket “30% lighter and 20% more efficient than any other launch vehicle in this category.” During the concept phase, Orbex's strategic investor, Elecnor Deimos Space, demonstrated that the Prime rocket weighed only 18 tons.
One of the key factors in the production process of the engine is 3D metal printing in the form of a single piece, which significantly increases its overall reliability due to the absence of any joints and seams. Speaking about the process of building the engine, Lukas Pankiewicz, 3D Printing Applications Specialist at SLM Solutions, says: “We aimed to meet the Orbex team's quality expectations and make the engine suitable for additive manufacturing without compromising its functionality. In preparing the data, each support structure was individually tuned to ensure the best quality in each section of the engine, considering, among other things, the post-processing process.”
Looking forward to launching in 2021!
In the private space launch industry, there are more and more competitors who are rushing to take the place of the leader in the commercial market. In an effort to reduce costs and develop new, lightweight designs, many manufacturers in this field are turning to the use of 3D printers for the production of engines. For example, 3D printing has been used to create Space X's Superdraco engine, Aerojet Rocketdyne's AR1 engine, Rocket Lab's Rutherford engine, and Blue Origin's BE series engine parts.
The first launch of the Orbex Prime rocket with a 3D printed engine is scheduled for 2021, which will be the output of an experimental payload for Surrey Satellite Technology, a leader in 3D printing applications.
Speaking at the launch of the Prime rocket, Chris Larmor, CEO of Orbex, said: “Today, Orbex took some big steps forward by creating something unique in Europe - a well-funded private microsatellite launch project, backed by excellent manufacturing capabilities, close cooperation with industrial enterprises and the rapid growth in the number of commercial customers.
Translation from English. The original of this material on the site 3dprintingindustry.com
Article published on 04/05/2019, updated on 03/04/2022
A 3D-printed prototype of a landing pad for the Moon was tested / Sudo Null IT News
It is almost impossible to imagine space exploration without the use of local resources. Lunar base projects were buried under the surface, sprinkled with soil or surrounded by printed walls. But less attention was paid to the buildings of the lunar cosmodrome - at best, flat areas are drawn in the illustrations. They will have a minus - the engine exhaust will corrode the surface and raise dust. To address these potential challenges, a team of students from ten U.S. universities and colleges, with support from NASA and 3D printing company ICON, designed, built, and successfully tested a large-scale prototype of the Lunar PAD airstrip.
In the summer of 2019, a team of students from the NASA L'SPACE Virtual Academy won a round of the 12-week NASA NPWEE Technology Concept Proposal course and received funding to develop their concept for protecting lunar landers from dust using robotic construction. The goals of both L'SPACE and NPWEE are to expand the pool of high-quality proposals of new concepts and technologies that can then be useful to NASA. In 2020, the team submitted a revised concept to an online technology readiness review and received funds to build and test a scale model. After spending hundreds of working hours consulting with NASA experts, the students went from idea to implementation of a model of the potentially important task of creating a safe reusable landing site for the Moon. In autumn, a scale model was built at Camp Swift, Texas, and successfully tested by a geophysical rocket engine in early March.
The project, originally called the Dust Devil ("dust whirl"), is eventually called the Lunar Plume Alleviation Device ("Lunar device to soften the exhaust") or, for short, Lunar PAD (playing on what that in English "pad" also means "a platform for launch / landing"). Structurally, the Lunar PAD consists of two levels: the upper one is a flat platform with small slots for exhaust gases to drain.
Ready site with test rocket engine installed, photo ICON The lower level combines load-bearing structures and flues for exhaust gases to the sides. A feature of the project is the use of 3D printing. First, a 3D construction printer forms a frame, which, as is often the case in additive manufacturing, uses complex surfaces and looks aesthetically pleasing.
The printed frame is then filled with filler. The test mock-up used a cement-based material, but for lunar conditions, it would be logical to produce a hardening or sintering regolith building material in situ. The structure built is strong enough to withstand the takeoff and landing of the lunar modules, and produces less dust by diverting engine exhaust into the gas ducts.
Even at the construction stage, sensors were installed in the model to determine temperatures, loads and gas flow. In early March, a geophysical rocket team from Texas A&M University delivered a solid rocket motor to a test site. It was installed above the site, launched and looked at the information recorded by the sensors. The tests were successful - the Lunar PAD pad successfully withstood the takeoff / landing simulation, the data obtained do not contradict the calculated ones.
Inspection of the site after testing.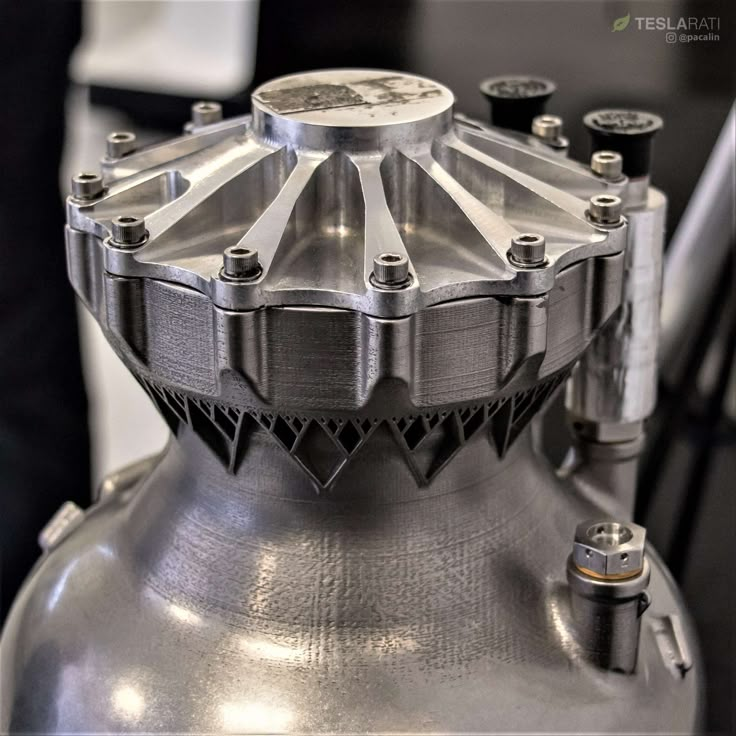
The project has already received its first scientific publication in the AIAA SciTech Forum materials, and a very diverse group of college and university students scattered throughout the United States can take part in a full-fledged and successful scientific and technical project, potentially in demand in future projects moon bases.
It is also interesting to note that ICON, which provided the gantry 3D printer for the project, is also 3D printing houses and other structures. The company also received a contract from NASA last fall to research and develop a construction system that could be used on the moon. Under this contract and, potentially, other space projects, a special division of the company was created. The project was named "Olympus". And it's time to redo the freshly drawn renders - thanks to the efforts of the students who created the Lunar PAD, the depicted landing pads already look outdated.