Can you 3d print electronics
3D printing electronics: Transforming the electronic industry
3D Learning Hub
See all categories
Contents:
- Introduction
- What are the advantages of 3D printing for electronics?
- 3D printing with electrostatic discharging properties
- Conductive 3D printing offering new opportunities
- 3D printed electronics: What is possible?
- What about the future of 3D printing in the electronics industry?
Introduction
What are the advantages of 3D printing for electronics?
3D print the perfect prototype
3D printing helps you get from the idea to the product in a matter of days.Launch your first series
Moreover, the electronics industry can truly benefit from additive manufacturing. No stock, no minimum number of units and short turnaround are the key upsides of using Sculpteo’s 3D printing service for your electronic devices, regardless of where they are in product life cycle management. Electronic production is made easy thanks to our 3D printing technology and will improve and simplify your whole supply chain management! 3D printing and electronics are strongly linked. Online 3D printing allows you to create a new kind of relationship with your clients.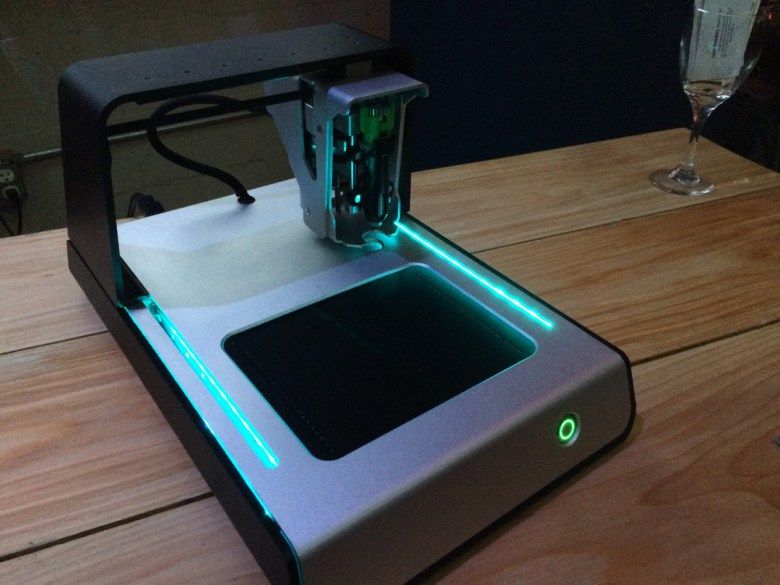
Design freedom
Electronic components production can now be thought in terms of 3D design and not only 2D, with new ways of stacking the circuits. It opens new possibilities to design for electronics, that are new to explore! Customization is becoming a big asset while using additive manufacturing for the creation of your products: you can create parts perfectly adapted to a circuit board or any electronic device. 3D printing can be used to create personalized electronic enclosures, USB stick cases, and keyboards, for example. Using additive manufacturing also offers you flexibility in the creation of your design. More than a perfectly adapted device, you can also elaborate complex geometries impossible to make with other traditional manufacturing techniques.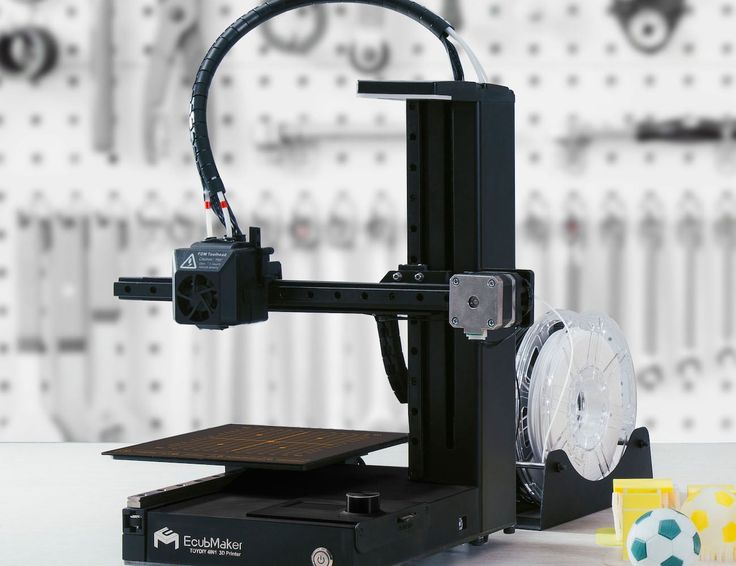
3D printing with electrostatic discharging properties
What is an electrostatic discharge?
What is called “electrostatic discharge” (ESD) is the flow of electricity between two electrically charged parts causes by contact. Static electricity often causes ESD through a process known as tribocharging. This static electricity can arise when surfaces rub together and this results in an excess of electrons on one surface and a deficiency on the other. The ESD occurs when differently-charged objects are brought close together or when the dielectric between them breaks down, often creating a visible spark. Electrostatic Discharges are a real problem and can damage sensitive electronic components. It can also lead to the alteration of magnetic media and set off fires, explosions in flammable environments! ESD is a big concern for the electronic industry, and being able to manufacture ESD-safe part is a real advantage to avoid any problem.
Focus on: Ultrasint PA 11 ESD
At Sculpteo, we are now offering you the possibility to manufacture your ESD-safe parts. If you are prototyping or producing a project where electrostatic discharging safety is critical, our Ultrasint® PA11 ESD material will be a perfect choice. Ultrasint® PA11 ESD is a bio-derived material, appearing to be a perfect choicel for increased process safety in advanced applications. With its interesting mechanical properties, this material offers new possibilities for a wide range of new applications, especially for the electronics sector. Indeed, with its low resistivity, Ultrasint® PA11 ESD is reducing the risk of electrostatically induced damage or failures, the material does not accumulate static electricity and can come in contact with electronic components without running any risk. The surface resistivity of Ultrasint® PA11 ESD is lower than traditional electrostatic dissipating materials. You can now make the most of the advantages of both additive manufacturing and electrostatic discharge properties. For electronic housing, electronic jigs and fixtures, this material is perfectly adapted. PA 11 ESD also as other advantages and interesting mechanical properties such as high tensile strength and elasticity, which could help you create efficient tools. What are you waiting for? With this material, you can create parts combining superior mechanical and thermal characteristics with outstanding electrostatic discharging properties. Get your parts 3D printed with Ultrasint® PA11 ESD by uploading your 3D file on our 3D printing service right now. It will only take a few clicks and you will get an instant quote.
Conductive 3D printing offering new opportunities
3D printing complex electronic components could go even further with conductive 3D printing. The creation of electronic devices with conductive features using 3D printing can particularly be useful to develop IoT (Internet of Things) projects. This innovative technology could allow creating 3D printed devices like LED, or touch sensors. But this ability to 3D print conductive devices could be involved in bigger projects, in soft robotics, 3D electronics, and also for communication devices such as 3D printed Near Field Communication (NFC) antennas.
3D printed electronics: What is possible?
As you will see, this 3D technology can be used for various applications in the electronics industry. Get inspired by these innovative electronic devices made using additive manufacturing!
3D printed circuit board by Nano Dimension and Harris Corp: 3D Printed Circuit Boards
Nano Dimension is known to work actively on 3D printed electronic devices The Nano Dimension’s DragonFly™ system is used to 3D print functional electronics prototypes and complex multi-layer Printed Circuit Boards (PCBs). But that is not all.
Nano Dimension and Harris Corp partnered to develop 3D printed electronic devices to create a radio frequency (RF) amplifier. They now work to go further and create hardware for the International Space Station. Their goal is to optimize the 3D printing process for RF components for flight studies aboard the ISS. Using additive manufacturing is a solution for them to find new ways to create radio frequency and circuit boards to find new innovative techniques.
The Simusolar project
At Sculpteo, some of our customers are working on solar energy using 3D printing. On the blog, we already told you about Simusolar, a company created in 2014 and looking to bring solar energy to the rural population of Tanzania. They develop and implement small-scale sustainable solutions to help local people in their everyday life.
They decided to use 3D printing because they needed a lot of custom made parts, for a low price. Their clients are farmers, fishers, or rural residents looking for various equipment powered by solar energy.
Optomec developing the Aerosol Jet Technology
Optomec announced that their Aerosol Jet Technology will be printing embedded electronics at the micron scale. The innovative process relies on both local deposition and local curing. This way, electronics parts are more affordable and require less waste of materials, and all of this with a superior resolution.
Start 3D printing enclosures!
3D printing enclosures are one of the most common uses of 3D printing for the electronic industry. Solidity, quality, customization, and accuracy, this is what you will make the most of while 3D printing your electronics enclosures.
If you are interested in 3D printing your own enclosure, you can follow our 3D printed enclosure design guide!
What about the future of 3D printing in the electronics industry?
What if in a few years, we could be able to create fully-functional smartphones or multi-material products using additive manufacturing? If these ideas are still dreams today, the innovations related to conductive 3D printing and electronic devices are now showing new opportunities. It might be time to rethink the way we conceive enclosures, circuit boards, and electronic components. From your prototyping process to the production and the management of your supply-chain, additive manufacturing could help you go through new challenges.
As you can see additive manufacturing has a lot to offer for electronics. It could become quite common to 3D print electrical elements. If you have an electronic project, but you don’t know what software you could use to start it: here is our selection of the best CAD software for electronics. Then, don’t hesitate to try out our online 3D printing service. You will just have to upload your 3D file, we will take care of it and send you your 3D printed objects in a few days.
Related Topics
- Return to Top
Get the latest 3D printing news delivered right to your inbox
Subscribe to our weekly newsletter to hear about the latest 3D printing technologies, applications, materials, and software.
What are 3D Printed Electronics? Let us tell you.
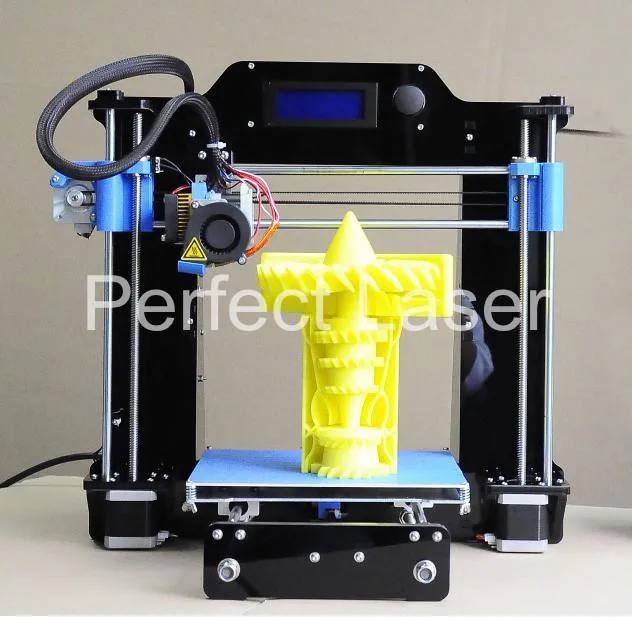
Design
The complexity of electronics combined with the capabilities of 3D printing. Heard of 3D printed electronics but want to know more?The ability to 3D print electronics is making waves in an industry plagued by long stints of R&D and a never ending cycle of prototypes and new releases.
But what exactly does this process entail? And how, as a designer, architect, or artist, can it help you? Is it sustainable? What are the dangers? And what should you know about it?
This guide is a useful starting point for you to find out…
With 3D printing electronics it is possible to make various types of boards that can be programmed and connected to prototypes – ©iakovenko123/Depositphotos.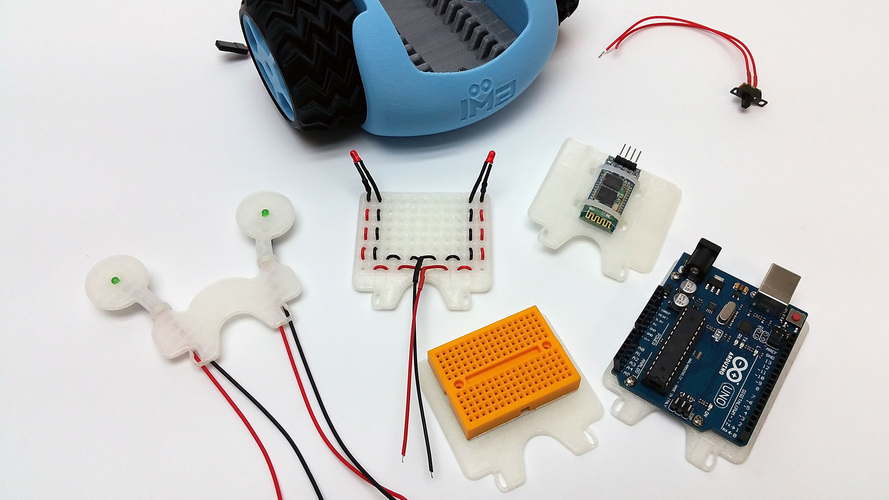
3D Printing objects with electronic functionality is a relatively new concept.
It involves the use of material jetting technology, which is used to jet conductive and insulating inks onto the printing surface.
These inks are applied in lines as thin as a few microns before UV light is used to solidify the inks.
The use of material jetting facilitates multi-material 3D printing, which is particularly useful for the electronics industry.
This means that the different elements necessary in electronics, such as functional circuitry and enclosures, can be manufactured in a single print run.
3D printing electronics involves the use of material jetting technology, which is used to jet conductive and insulating inks onto the printing surface – ©IgorVetushko/Depositphotos.comWhat materials are used when 3D printing electronics?Where systems could typically use just one material in the 3D printing process, recent advancements have enabled the involvement of multiple materials.
This allows manufacturers to merge conductive materials with non-conductive materials.
The thermoplastics used in the 3D printing process are often made with copper, carbon and graphene.
Meanwhile, proprietary conductive and dielectric inks are used simultaneously to build functional circuits and antennas. This expands the range of functions in 3D printed electronics.
Because the process combines multiple materials into the same 3D object it also requires a solvent to ensure their compatibility. The particular solvent used is known as an orthogonal solvent, which is specifically designed not to cause damage to the different components.
The thermoplastics used in the 3D printing process are often made with copper, carbon and graphene – © Julian Pagliaccio, via Wikimedia CommonsWhat can 3D printing electronics produce?With 3D printing electronics, it is possible to make various types of boards that can be programmed and connected to prototypes.
A very wide range of inks can be utilized enabling a full range of printed electronics functionality: conductors, semiconductors, dielectrics, resistors and more.
The process can be used to manufacture electronic components such as resistors, capacitors, antennas, sensors, and thin film transistors.
Using the 3D printing process, it is also possible to rapidly 3D print fully functional electronic circuits that contain electrically-conductive metallic inks and insulating polymeric inks, which could be useful for medical devices, radio frequency shielding surfaces and novel structures for harvesting solar energy.
Today, however, it’s main applications include printing electronics for use in prototypes for upcoming products, prosthetics and more complexly shaped electronic products.
Give me a step-by-stepWhile several methods exist for 3D printing electronic components, they typically mirror the various steps utilised in regular 3D printing. The main difference is the use of a dual-material fused filament process with conductive thermoplastic filaments.
As with all 3D printing, a digital CAD model of the desired part is designed, which serves as the printer’s instruction model.
When the printing process begins, a trace or “fingerprint” is created, and then the requisite materials needed for that specific part are added in layers.
The process flow of the 3D systemWhat machinery is used when 3D printing electronics?Specialised machinery is required which integrates a precise inkjet deposition printer with dedicated nano-inks and software capable of printing electronic circuits such as printed circuit boards (PCBs), antennas, capacitors and sensors.
Can I do it at home?Due to the complexity of the process, it is not possible to replicate it at home unless you have the capability of manufacturing your own 3D printer.
With the relevant machinery, it is possible to 3D print electronics at home.
Find out more about manufacturing processes, don’t miss What is Explosive Forming? Let us tell you…
The benefits of 3D printing electronics range from faster time-to-market, greater freedom of design and customizationWhat are the pros & cons of 3D printed electronics?At the core of every electronic device is a Printed Circuit Board (PCB) which is difficult to produce. Luckily, with the advent of 3D printing, manufacturing these circuit boards is less challenging.
The benefits of 3D printing electronics range from faster time-to-market, greater freedom of design and customisation.
This is because with the advent of 3D printing electronics manufacturers can create prototypes of circuits and circuit birds in-house, reducing procurement expenses and eliminating concerns about IP infringement.
3D printing also opens up opportunities to design complex shapes and components. For example, multilayer circuits can now be 3D printed on non-flat, flexible surfaces, which would not be possible with traditional manufacturing techniques.
Components can also be printed onto 3D surfaces eliminating the need for a separate substrate and reducing the size, thickness and weight of the end product.
However, there are several limitations when it comes to 3D printing electronics, not only because it is limited in the types of parts it can produce.
Whilst the recyclability of 3D printed electronics is an area being explored by various researchers, it remains a con due to what is currently possible.
Another downside to 3D printed electronics, and in fact, all 3D printed products is their structural integrity.
Whilst printed layers adhere together in some cases, and under certain stresses or conditions, they can delaminate.
Another major downside to 3D printing as a whole is its increasing popularity and accessibility. On one hand, it democratises the manufacturing processes but it also makes it easier to fake and counterfeit products.
I want to know if it’s sustainable…Whilst 3D printing electronics can minimise the manufacturing footprint by localising production, the difficulty in recycling the various components means it can’t be considered a sustainable process.
There are several resources that are useful when it comes to building your knowledge around 3D printed electronics.
If you want to learn more check these out:
- A visual demonstration of the 3D printing process used to manufacture electronics.
- An explanation of the various capabilities of 3D printing electronics.
- A paper detailing the evolution of 3D printing electronics.
- A breakdown of the various benefits and current systems employed when 3D printing electronics
- A detailed research into the future of 3D printing electronics and its benefits when used for prototyping.
Fascinated by 3d printing? Don’t miss 3D printing ceramics: Interview with Hilda Nilsson.
3D printers in electronics manufacturing
Manufacturers of consumer electronics and commercial devices are actively using the possibilities of 3D printing to optimize development time and cost.
- What to print
- Advantages 3D
- Case: Microphone for U2
- Select 3D printer
- Printers use common types of plastics (such as ABS) commonly used in instrumentation. Polymer resins are also used to print high-precision prototypes and test samples.
Which products are 3D printed by electronics manufacturers:
- concept models for visual evaluation or market research;
- test prototypes to test functionality, ergonomics, assembly of complex structures;
- ready-to-use articles or individual items;
- master models for casting in silicone.
Many 3D printers use common types of plastics (such as ABS) commonly used in instrumentation.
Polymer resins are also used to print high-precision prototypes and test samples.
Which products are 3D printed by electronics manufacturers:
- concept models for visual evaluation or market research;
- test prototypes to test functionality, ergonomics, assembly of complex structures;
- ready-to-use articles or individual items;
- master models for casting in silicone.
Why use 3D printers in production
- Reduced lead times. It takes only a few hours to create a prototype of a new device using a 3D printer. You no longer have to wait 2-3 weeks for a contractor to make a sample for you.
- Reducing the cost of production. The cost of manufacturing an object on a 3D printer is several times lower than if you create a mold for this.
- Preservation of trade secrets.
3D printer in the office will allow you to save all the details of new developments within the company. You do not need to share information with third-party customers to produce the desired part.
- Extensive testing and development options. You can make as many prototypes as you need quickly and cheaply. Test, make improvements - until you reach the ideal.
Examples of using 3D printing in electronics manufacturing
How Logitech uses 3D printing
A major personal electronics manufacturer uses various types of 3D printers during the design and testing phase of new products.
For example, Logitech creates prototypes of computer mice from a translucent photopolymer in order not only to evaluate the ergonomics and appearance of a new product, but also to analyze the location of components inside the design.
3D printing was also used to assemble test samples of one of the company's headsets.
Comprehensive testing allowed us to release the most convenient, durable and functional product in a very short time.
Why use 3D printers in production
- Reduction of terms. It takes only a few hours to create a prototype of a new device using a 3D printer. You no longer have to wait 2-3 weeks for a contractor to make a sample for you.
- Reducing the cost of production. The cost of manufacturing an object on a 3D printer is several times lower than if you create a mold for this.
- Preservation of trade secrets. 3D printer in the office will allow you to save all the details of new developments within the company. You do not need to share information with third-party customers to produce the desired part.
- Extensive testing and development options. You can make as many prototypes as you need quickly and cheaply.
Test, make improvements - until you reach the ideal.
Examples of using 3D printing in electronics manufacturing
How Logitech uses 3D printing
A major personal electronics manufacturer uses various types of 3D printers during the design and testing phase of new products.
For example, Logitech creates prototypes of computer mice from a translucent photopolymer in order not only to evaluate the ergonomics and appearance of a new product, but also to analyze the location of components inside the design.
3D printing was also used to assemble test samples of one of the company's headsets. Comprehensive testing allowed us to release the most convenient, durable and functional product in a very short time.
Unique microphone for group U2
A specially designed and 3D printed microphone with LED inserts for U2's world tour. Thanks to its complex internal structure, it not only managed to accommodate a large amount of electronics, but also made it strong enough to support the weight of the vocalist.
Unique microphone for U2
A microphone with LED inserts was specially designed and 3D printed for U2's world tour. Thanks to its complex internal structure, it not only managed to accommodate a large amount of electronics, but also made it strong enough to support the weight of the vocalist.
In the field of wearable electronics, there is a concept according to which electronics should be directly integrated with the body: sticking sensors on the skin or, in the long term, implanting electrodes. There are also separate studies in which simple electronic components, for example, stretch or pressure sensors, are offered to be printed directly on the skin using a 3D printer. This is a potentially convenient method, but since printing takes some time, and the person moves during this time, the printing is inaccurate. In 2018, American engineers solved this problem technologically: they supplemented the printer with cameras that track hand movements and compensate for it by moving the print head.
A group of engineers from the Korea Institute of Advanced Technology led by Andrea Bianchi took a different, simpler approach in their new development. They created a compact printer that can be mounted directly above the print site on the body so that the print quality is almost independent of human movements.
The printer has a simple design. It consists of a frame that is placed on the skin and pressed tightly against the body with two straps, and above the frame there is a mechanism that moves the print head in two directions. The print head itself is also simple: it is a syringe with a conductive flexible material, and a linear motor on top that squeezes the substance out of the syringe.
Before printing, the layout of the printed tracks can be changed in the program. Also, before starting the process, the printer calibrates, lowering the head to the level of the skin in different places in order to understand its relief. Immediately before printing, an insulating transparent layer must be smeared onto the skin, after which the printer will draw tracks on it in a few minutes, which can then be connected to electrodes leading to the readout electronics. In addition, while the print substance is still wet, small rigid components, such as an LED, can be inserted into it.
The developers showed several examples of devices that can be printed on leather. One of them is a hand bend sensor in several places, which allows real-time display of the shape of the hand on the computer. Another prototype allows you to control the volume of music by moving your finger along the volume slider. The authors also showed posture, hand touch and walking sensors.
In 2017, American engineers printed a multi-component pressure sensor on a finger model using a printer that can use several materials at once in one printing procedure.
Learn more