3D printed prosthetics arm
Teenagers develop 3D-printed bionic arm 30 times cheaper than existing prosthetics
Article
Seeking to create affordable solutions for people with disabilities, Global GenU winning team eBionics developed a 3D-printed bionic arm which allows anyone to print and assemble it themselves.
Lisar Morina
UNICEF North Macedonia
28 January 2021
Skopje, North Macedonia – Somewhere in downtown Skopje, amid the purring of engines and honking of sirens, 17-year-old Boris meanders the many streets and alleys of the city to make his way into an inconspicuous building not far from the plaza. He steps into a small makeshift workshop lined with shelves full of odd machines, wrenches, screwdrivers, crates and canisters with labels of all kinds. Joining three other teenagers, he sits in front of a 3D printer. It is printing a prosthetic arm.
One glance suffices to realise that Boris and his friends are not just high-school students. They are also remarkable innovators with a zeal and fervor about their work that is contagious.
“People look differently at young innovators like us—they don’t believe that we are capable of creating impactful innovations that help people at large,” says Boris. “But we like to think differently.”
Driven by a deep desire to create affordable solutions for people with disabilities, 17-year-old Boris Nocheski, 17-year-old Anamaria Ilieva, 16-year-old Teo Kitanovski, and 17-year-old Orhan Bahashov are using 3D printing technology to create a user-friendly bionic arm that is 1/30th of the price of existing prosthetics. And it can “grow” with children!
Globally, millions of people suffer from upper limb deficiencies, which can affect physical and mental health and inhibit people from leading productive lives. Prosthetic arms and artificial limbs can vastly improve the ability of people living with upper limb disabilities to be independent and engage in daily activities. But prosthetic limbs are expensive, need to be routinely replaced because of wear and tear, and are therefore out of reach for millions of people across the globe.
“Currently-available bionic arms are inaccessible—they cost thousands of dollars, can only be bought in a few developed countries, and must be continuously changed if you’re a young person, as your body is constantly growing,” says Boris, who is the co-founder of eBionics. “We believe that these problems can be solved by approaching the [bionic arm] technology differently.”
The eBionics ‘VenusArm’ is 30 times cheaper than the second cheapest bionic arm in the market. This is because Boris and his team do not charge for shipping or labor, or pay profits to suppliers. The VenusArm, Boris explains passionately, allows anyone with access to a 3D printer to print the bionic arm themselves within just a short hour, using the instructions made available on the eBionics website. The team have also provided options to purchase the individual parts from third-party sellers to assemble the arm themselves.
“Our VenusArm is entirely 3D printed and uses muscle sensors to allow for flexible movement that helps the user in everyday life,” says Boris, explaining that they also used an impression mold to create a universal socket, which means it will fit anyone, even growing children. “We want to make sure that people can get a fully functional bionic arm that is both affordable and available for everyone, regardless of where you are from.”
Bionic arms pick up signals from the user around the same muscles (typically below the elbow) used to move a biological hand. Specially designed sensors pick up electric signals and use these to create hand movement relative to the electrical signal.
In a video, trying the bionic arm for the first time, a young woman from North Macedonia said, “Even on the first day, after only thirty minutes of wearing it, I started feeling it as part of my body.” The young woman is shown using the bionic arm to operate a sewing machine and even to drive a car, stating that she feels like she is in “complete control, now that she has the arm”.
The youngsters behind ‘eBionics’ developed the blueprint of the bionic arm—dubbed VenusArm—at the global Generation Unlimited Youth Challenge which took place in 36 countries, encouraging young people to design entrepreneurial solutions to social challenges.
The Youth Challenge is a true example of a multi-sector partnership initiative—engaging the private sector in mentorship, youth-led organizations in grass-roots outreach, young people in co-creating solutions, and governments in the judging process.
A few months after winning the local competition, eBionics was crowned a global Generation Unlimited Winner—just one of 8 teams across the world to receive further funding of up to $15,000, along with a tailored global incubation programme which is coordinated globally by UNICEF’s Office of Innovation, working with GenU partners and Country Offices.
“Step by step, we are getting closer to our goal—creating value for all people around the world, especially those who need it most” says Boris. “Every idea can bе accomplished if you work hard on it, with the right people around you. Steve Jobs once said that the people who are crazy enough to think they can change the world are the ones who do. Throughout our whole experience, we were motivated by this quote and we believe that other talented young people also should!”
“We feel that our story won’t be complete without thanking UNICEF and Foundation Telekom for Macedonia, the supporters of the Generation Unlimited Youth Challenge in North Macedonia, as well as SmartUp - Social Innovation Lab, the implementers of the challenge. Without their help it would've been much harder to succeed,” says Boris.
EBionics’ vision is to create a user-generated sustainable and altruistic social enterprise with a worldwide community of makers, contributors and supporters, third-party partners, and most importantly, a business that provides affordable and reliable 3D printed bionic arms.
The
Generation Unlimited Youth Challenge 2019/20 is co-hosted globally by four Generation Unlimited partners – UNICEF, UNDP, Plan International and the World Organization of the Scout Movement, with support from Irish Aid
3D-printed prosthetic limbs: the next revolution in medicine | 3D printing
John Nhial was barely a teenager when he was grabbed by a Sudanese guerrilla army and forced to become a child soldier. He spent four years fighting, blasting away on guns almost too heavy to hold, until one day the inevitable happened: he was seriously injured, treading on a landmine while he was on morning patrol.
“I stepped on it and it exploded,” he recalled. “It threw me up and down again – and then I tried to look for my leg and found that there was no foot.”
His comrades carried him back to base camp, but there was hardly any medical care available. It took 25 days before he received proper treatment, during which time he developed tetanus down one side of his body. Finally, Nhial (not his real name) was put on a flight to the Kenyan border, his life only saved when he was handed over to a Red Cross team.
Now, a decade later, he lives in a Juba refugee camp, having suffered further troubles in the conflict that has engulfed the struggling new nation of South Sudan. He plays wheelchair basketball for his country, although he relies on a prosthetic lower leg to struggle around the muddy, sprawling camp. Reaching the most basic services often entails long walks and it can be difficult to get to training. But at least his hands are free to carry things such as food and water, unlike those on crutches.
Such stories of lives devastated by conflict or disease are all too common in developing countries. Lack of an arm or leg can be tough anywhere, but for people in poorer parts of the world it is especially challenging. Some are victims of conflict, while others may have been born with congenital conditions. Many more are injured on roads, with the casualty toll soaring in poorer nations. In Kenya, half the patients on surgical wards have road injuries. The World Health Organization estimates there are about 30 million people like Nhial who require prosthetic limbs, braces or other mobility devices, yet less than 20% have them.
Prosthetics can involve a lot of work and expertise to produce and fit and the WHO says there is currently a shortage of 40,000 trained prosthetists in poorer countries. There is also the time and financial cost to patients, who may have to travel long distances for treatment that can take five days – to assess their need, produce a prosthesis and fit it to the residual limb. The result is that braces and artificial limbs are among the most desperately needed medical devices. However, technology may be hurtling to the rescue – in the shape of 3D printing.
Slowly but surely, 3D printing, also known as additive manufacturing, has been revolutionising aspects of medicine since the start of the century, just as it has had an impact on so many other industries, from cars to clothing. Perhaps this is not surprising, given that its key benefit is to enable the rapid and cost-efficient creation of bespoke products. There are few commercial products that need to suit a wider variety of shapes and sizes than medical devices made for human beings.
Experts have developed 3D-printed skin for burn victims, airway splints for infants, facial reconstruction parts for cancer patients, orthopaedic implants for pensioners. The fast-developing technology has churned out more than 60m customised hearing-aid shells and ear moulds, while it is daily producing thousands of dental crowns and bridges from digital scans of teeth, replacing the traditional wax modelling methods used for centuries.
Jaw surgery and knee replacement operations are also routinely carried out using surgical guides printed on the machines. So it is no surprise that the technology has begun to stir interest in the field of prosthetics, even if sometimes by accident. Ivan Owen is an American artist who likes to make “weird, nerdy gadgets” for use in puppetry and budget horror movies. In 2011, he created a simple metal mechanical hand for a steampunk convention, the spiky fingers operated by loops pulled through his own.
He posted a video that was seen by a carpenter in South Africa who had just lost four fingers in a circular-saw accident. They began discussing plans for a prototype prosthetic hand and that came to the attention of the mother of a five-year-old boy, called Liam, who had been born without fingers on his right hand.
She wanted a tiny version of their hand, but Owen realised the child would rapidly grow out of anything they made, so he looked at the idea of using 3D printing. “If we could develop a design that was printable, it would be possible to rescale and reprint the design as Liam grew, essentially making it possible for his device to grow with him,” he said.
So the artist persuaded a printer manufacturer to donate two machines and developed what has been claimed to be the first 3D-printed mechanical hand. Crucially, rather than patent this work, Owen published the files as open source for anybody to access, allowing others to collaborate on, use and improve the designs.
This has grown into Enabling the Future, a network with 7,000 members in dozens of countries and access to 2,000 printers, who help make arms and hands for those in need. One school student in California even printed a new hand for a local teacher.
Often they are aimed at children, since many dislike the weight, look and hassle of modern prosthetics, which can involve inserting the arm into a silicone sleeve and using straps across the back to hold the device in place.
These body-powered hands cost thousands of pounds, yet must be replaced every couple of years as a child grows. The 3D-printed versions cost about £40, come in any colour and look like a cheery toy, so are often more appealing despite being less sophisticated.
Jorge Zuniga, a research scientist in the biomechanics research department at the University of Nebraska in Omaha, heard about this project on his car radio. He was only half-listening, but on arriving home he started playing baseball with his four-year-old son and observed how important the grabbing of an object was to his child’s development.
He spent the next month carefully building a prosthetic model that mimicked the human hand, only for his work to be dismissed instantly by his son. “He told me children wanted a hand that looked like a robot.”
From this conversation and the open-source designs emerged Cyborg Beast, a project heavily backed by Zuniga’s department to develop futuristic-looking, low-cost prosthetic hands. “You can do anything with 3D printing,” said Zuniga, who now leads a seven-strong team. “We believe it will revolutionise the prosthetics field. It will lower the costs worldwide and gives engineers, patients and doctors the chance to modify prosthetic hands as they want. And they can be any colour.”
When I told Zuniga, slightly hesitantly, that his design looked like a toy, he was delighted. “That’s great – we want children to see it as a toy,” he said. “This is a transitional device. Many children do not like prosthetics, however good they are these days, because they might have a hook for a hand and they need help to put the harness on, which children dislike. So this is to bridge the gap, helping them get used to the idea as they grow up.”
“We have even had a child missing a shoulder. So we developed a device that weighs the same as the missing arm. This meant he not only got a new arm that helped daily life but it also improved his posture and balance, therefore was much better for his spine. This sort of thing can be done much easier with 3D technology.”
It is remarkable that people who do not even own a printer can obtain a functional child’s hand for the price of a theatre ticket within 24 hours. Zuniga says at least 500 Cyborg Beasts are in use worldwide and the design has been downloaded more than 48,000 times. He has taken it to his native Chile, where he runs a paediatric orthopaedic 3D-printing laboratory, and has had recent requests for the plans from Nigeria.
“My concern at this stage is that some of the materials can melt in higher temperatures. It is not working well there yet, but this sort of prosthetic has huge potential to be used with better materials in the developing world. We are still in the infancy stage at this moment.”
Another scheme experimenting with this technology is Project Daniel in the Nuba mountains of Sudan, where in the middle of the ongoing civil war an American physician, Tom Catena, has been working as the only permanent doctor for half-a-million people around his Mother of Mercy hospital. Fuelled by his religious faith, for almost a decade this brave medic has ignored bombings, a lack of electricity and water shortages to do everything from delivering babies to amputating limbs.
“It’s demoralising for us to amputate an arm knowing that there is no good solution,” Catena told me by email. “We have many arm amputees – both above and below the elbow as a result of the war here and general lack of medical care. This in an agricultural society, where nearly everyone is a subsistence farmer. If one is missing an arm, he is not very functional in this society.They become totally dependent on the family and have a difficult time getting married [which is also very important in this society]. ”
The idea of using 3D printing to help arose when Mick Ebeling, an American film producer and philanthropist, learned about the Mother of Mercy hospital at the same time as he was hearing about the emerging work on low-cost prosthetic hands. Searching for information on Catena, Ebeling read about one of his patients: Daniel Omar, a 12-year-old boy who had wrapped his arms around a tree to protect himself during an aerial attack. His face and body were protected when a bomb exploded nearby, but both the boy’s arms were blown off.
You can’t just smash in these new technologies, but if we get this right the growth could be exponentialMatt Ratto, Nia Technologies
Ebeling travelled out to the Nuba mountains with 3D printers and, working with hospital staff, fitted about a dozen people with new arms. “Unfortunately, as time went on, none of the amputees was using the prostheses as they felt they were too cumbersome,” said Catena. The doctor concluded: “The 3D model was good, fairly easy to make and inexpensive… although it hasn’t worked out so well here. Perhaps with some tweaking, the 3D printers can be of great use for arm amputees.”
Yet for all the agonies and difficulties associated with arm loss, the bigger problem in poorer countries is when lower limb disability leads to a loss of mobility. Wheelchairs are expensive and can be difficult to use when roads are potholed, streets are muddy and pavements are nonexistent. Without a prosthetic limb, people struggle to fetch water, prepare food and, above all, to work. This throws them back on their families and communities, intensifying any hardship and poverty.
One group that has spent almost three decades trying to tackle these issues is Exceed, a British charity set up by diplomats and academics at the request of Cambodia’s government to help thousands of landmine survivors. It works in five Asian countries, training people at schools of prosthetics and orthotics. In Cambodia, there are almost 9,000 landmine survivors in need of artificial limbs, although these days traffic accidents are a more likely cause of disability, while children also need braces for a range of common conditions such as spina bifida, cerebral palsy and polio.
“If you wear a prosthesis, you are disabled for about 10 minutes in the morning while you have a shower, then you put your leg on and go to work. If you do not have one, then your hands are out of use with crutches so you can’t even take drinks to the table,” said Carson Harte, a prosthetist and the chief executive of Exceed. “Without a prosthesis, there are no expectations. You just go back and rely on the goodwill of your family.”
It is not really a lack of money that denies people these devices, since simplified forms cost little and generic Chinese models are improving fast. The components can cost just £30. The big hurdle is the lack of trained technicians to fit the artificial limbs. In the Philippines, there are estimated to be 2 million people needing prosthetics or orthotics. However, there are only nine fully trained experts, each able to treat 400 patients a year, at most, although more are being trained on a new four-year course.
Orthopaedic technician Moses Kaweesa assembles a 3D-printed artificial leg at CoRSU hospital in Uganda.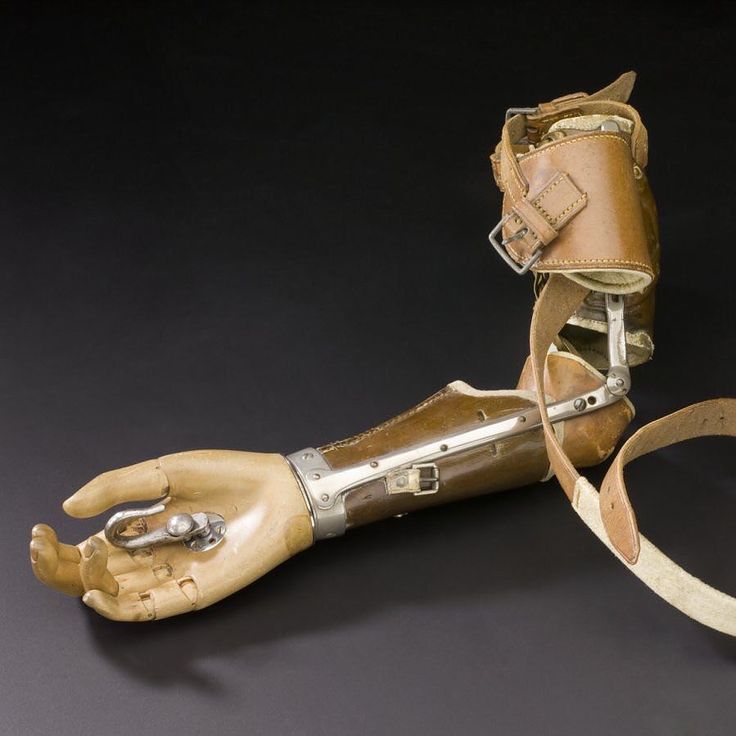
Traditionally, a prosthetist would wrap a stump with plaster of Paris bandages to make a reverse mould and let it dry, then fill it with more plaster that must harden. From this, a socket can be forged that fits, with more modifications for precision, to the bone on the stump. Great care must be taken to avoid nerves and tender areas that are not tolerant of pressure.
The key for the technician is to understand the pathology of a stump, which differs for each person. This is a cumbersome process that can take a week, especially with physical therapy for new patients that lasts three days. It can also be messy work, mixing up and moulding the plaster, while a prosthetist visiting a rural area must transport 20-kilo packs of plaster. With a 3D scanner, a digital image can be made in half an hour and sent by email.
Exceed has begun a seven-month trial of 3D-printed devices in Cambodia with Nia Technologies, an innovative Canadian not-for-profit organisation. “This technology has the potential to increase the productivity of every technician,” said Harte. “It is not about printing off legs, nor does it replace the skills of a well-trained professional, but it has potential to produce a better, faster, more easily repeatable way of doing one key part of the chain. There are no magic bullets, but this may be an important incremental change.”
Nia is also trialling its 3D PrintAbility technology in Tanzania and Uganda, where there are only 12 prosthetists to serve a population of about 40 million people; at the time of writing, all six state clinics have run out of materials. Doctors there often deal with children who have lost limbs after falling into open cooking fires, while other youngsters need braces after suffering post-injection paralysis caused by badly administered jabs that damage nerves.
In Uganda, its team is working with CoRSU hospital in Kisubi, a specialist rehabilitation centre for children with disabilities. Orthopaedic technician Moses Kaweesa said they found the technology lighter and faster to use, as well as easier for people in remote rural areas. “It used to take five days to have a limb manufactured, with lots of hanging around for the patient. Now, it is barely two days, so they spend much less time in the hospital. There is also less waste of material, so for a country like ours this can help so much by cutting down the costs.”
The first person to test out a 3D-printed mobility device at the hospital was a four-year-old girl who until then had dragged herself across floors and had to be carried around by her family. “When she was born, her right leg was missing the foot,” said her older brother. “It was very difficult for her to walk, to play with other children. She can be lonely. But when she was given a leg she was able to run with others, play with others.”
Matt Ratto, Nia’s chief science officer, who led the project’s development, admitted that it was only when he saw the serious-looking child in her red dress start to walk that he realised his technology actually worked. But, like Harte, he urges caution. “We are surrounded by the hype of 3D printing with crazy, ridiculous claims being made,” he said. “We must be cautious. A lot of these technologies fail not for engineering reasons but because they are not designed for the developing world. You can’t just smash in these new technologies.”
Ratto’s aim is to use the technology to fit 8,000 people with 3D-printed mobility devices within five years, across some 20 sites in poorer countries. “If we get this right the growth could be exponential. If we iron out the kinks, and work out the best way to help clinicians, I think we will see something of a hockey stick curve on the graph. But we must not get it wrong, move too fast nor over-hype the potential.”
This article first appeared on Mosaic and is republished here under a Creative Commons licence
3D printed bionic prostheses from Unlimited Tomorrow
You are here
Home
The American company Unlimited Tomorrow brought to the market 3D printed bionic prosthetic hands with a custom design. Artificial hands with six grips are created from individual 3D scans of patients and are offered for eight thousand dollars.
Unlimited Tomorrow is the brainchild of a young entrepreneur named Easton LaChapelle, who built his first remote-controlled robotic arm at the age of fourteen. Three years later, the now high school student was invited to the traditional school science fair at the White House after winning a competition at the Intel International Science and Technology Fair, and another year later, Easton joined forces with British designer and almost namesake Christopher Chappelle and launched his own startup, collecting the initial funding on the Kickstarter crowdfunding site.
Easton is now twenty-four years old and leads a company that offers a ready-made commercial product - functional 3D printed prostheses. The idea of a startup was born back in his school years, when during one of the fairs, his attention was attracted by a girl who was carefully studying his booth with a robot. The girl was missing her right arm, and a rather simple electromechanical prosthesis with one grip replaced the limb. As it turned out, this miracle of technology cost parents eighty thousand dollars.
TrueLimb prostheses can hardly be called cheap either, but they are much more affordable in terms of affordability: Unlimited Tomorrow offers its products for $7,995 or in installments with monthly payments of $259, working directly with patients, without intermediaries, while the closest analogues cost about twenty thousand even with good health insurance. In addition, these hands are much more functional, being able to perform six different grips with individual finger control, and much more attractive to look at than many of the analogues.
The hand size, color and detailing is chosen by the future user, who only needs to go through the 3D scanning procedure. Scanning can be performed at home: the company sends the necessary equipment and instructions to selected candidates. Then the company's engineers bring the 3D scans up to standard and use the resulting digital models to print components on a color 3D printer from Hewlett Packard using Multi Jet Fusion technology. The minimum age of a candidate for prosthetics is seven years.
For now, the company is focusing on prosthetic arms, but is considering making artificial lower limbs and even exoskeletons. The most well-known Russian manufacturer of custom prostheses using 3D printing technologies is the Moscow company Motorika, which offers low-cost mechanical traction prostheses "Kibi", myoelectric prostheses "Indy" with one grip, and also working on bionic artificial hands "Manifesto" with fourteen grips. . Customers can count on compensation through the Social Security Fund. This summer, Motorika received the CE marking for all its products and announced its intention to enter the European market.
CNET edition of the Unlimited Tomorrow project:
Source
Tags:
TrueLimb prostheses, 3D printed bionic prostheses from Unlimited Tomorrow, Multitard 3D printed technology Jet Fusion, 3D scanning, 3D printing technologies, Motorika
Other materials:
- 3D Scanning FAQ Part 2
- Digital artisans. Where will our children work?
- Food from a printer: who uses 3D printing in cooking and why
- The scope of Werth tomographs and their capabilities
- Computer simulation of metal 3D printing processes based on MSC Software solutions
Attention!
We accept news, articles or press releases
with links and images. [email protected]
Printing prostheses on a 3D printer, the use of 3D technologies in prosthetics | project news 3DPulse.Ru
Printing prostheses on a 3D printer, the use of 3D technologies in prosthetics | project news 3DPulse.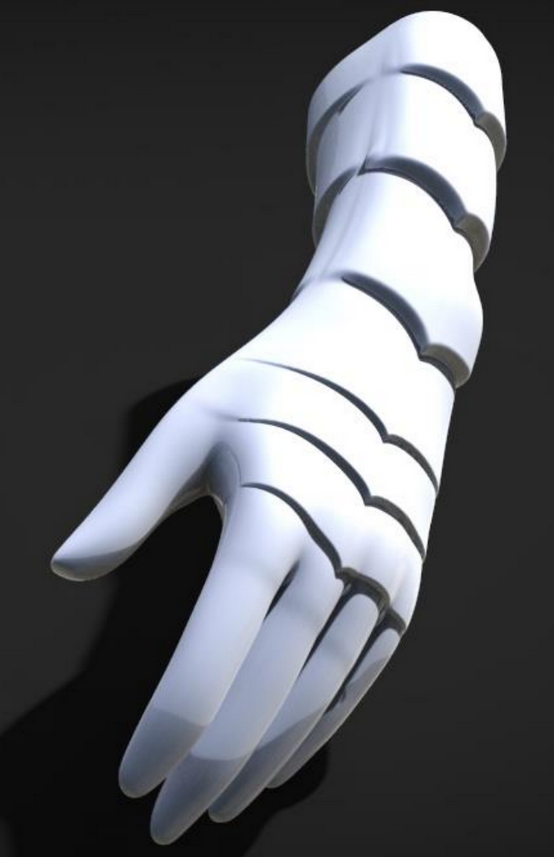
3d pulse.ru
Our new report "Construction 3D printing in Russia" has been published
Our report "Construction 3D printing in Russia" has collected information about domestic companies and start-ups that produce...
Vladimir Viktorovich Molodin (SIBSTRIN): "The idea [of printing with polystyrene concrete] appeared three years ago, and it took 30 years to get there."
Interest in 3D construction printing is growing rapidly around the world, with most of the developed 3D printers working with...
Mass 3D printing of individual houses: reality or utopia? - public study by the Techart group
In its public survey, Techart explores whether 3D printing can bring something really new to the construction...
Victor Mann (RUSAL): "In Russia, additive manufacturing is one of the fastest growing industries"
RUSAL is a leading company in the global aluminum industry and the largest aluminum producer with a low carbon footprint. Her...
"3D Printing in the Oil and Gas Industry: Incentives and Constraints" - Techart Group Public Study
Techart Consulting Group published a study analyzing the current state and development prospects...
Current news
Prostheses
3D printed piano prosthesis
A short story about how 3D printing helped a man realize his dream.
Prostheses
3D-printed middle ear prostheses help treat hearing loss
Hearing in healthy people works by transmitting vibrations from the eardrum to the cochlea through three small auditory...
Prostheses
LimbForge improves 3D-printed prosthetic hand
The LimbForge team, a spin-off from the e-NABLE prosthetic 3D printing community, has developed a 3D-printed prosthetic hand from...
Prostheses
An engineer from Novgorod uses 3D printing to work on a prototype bionic prosthesis.
Novgorod engineer Stanislav Muraviev is working on a new bionic prosthesis. In his work, the developer uses ...
3
Prostheses
3D printed Third Thumb expands human capabilities
Dani Claude, a student at the Royal College of Art in London, has 3D printed an extra large prosthetic...
Prostheses
A software system for the neurocontrol of prostheses is being created in Tomsk
Specialists from the Tomsk University of Control Systems and Radioelectronics (TUSUR) are developing software for...
Prostheses
Samara State Medical University scientists print individual prostheses on a 3D printer
Samara State Medical University scientists have patented a method for manufacturing individual prostheses with...
Prostheses
3D printing makes it possible to create a prosthetic leg for a disabled parrot
Pete, a 34-year-old parrot, lost his leg after being attacked by a fox - thanks to veterinarian Jonathan Wood from.