Polycarbonate 3d printers
The Guide to Polycarbonate 3D Printing
What is Polycarbonate?
Polycarbonate is a thermoplastic that is most prominently known for its incredible strength and impact resistance. The basis of bulletproof glass, polycarbonate is lightweight and exhibits a translucency that is superior to other Fused Filament Fabrication (FFF) 3D printing materials. Polycarbonate also boasts heat resistance, is flame-retardant, and insulates electricity, making it essential to use in electrical components and hardware.
Polycarbonate is extremely durable and highly effective for a wide range of professional-level applications:
- Widely used in the construction, transportation, and automotive industries
- Electrical and telecommunications hardware
- Data storage, such as CDs, DVDs, and Blu-Ray Discs
- Consumer products like sunglasses, phone and computer cases, water bottles, and food containers
Polycarbonate: The Strongest 3D-Printing Material
When it comes to strength, polycarbonate truly is the “king” of 3D printer filament, dramatically out-performing other materials in strength tests. In an informal material strength test, Airwolf 3D printed a series of hooks using a variety of 3D printing materials: ABS, PLA, Nylon 910, and polycarbonate. Each material was then tested by loading the hook with weight until it fractured. Polycarbonate won by a landslide.
PLA has a tensile strength of 7,250 psi and was able to lift 285 pounds. In comparison, ABS has a tensile strength of 4,700 psi and snapped instantly under 285 pounds of weight. Polycarbonate, on the other hand, has a tensile strength of 9,800 psi and lifted a whopping 685 pounds — far more than any of the other materials that were tested.
Using 3D-Printed Polycarbonate for Production Parts
Historically, there has been a great deal of hesitance when it comes to making fully functional, end-use parts out of 3D-printed materials. For example, most parts made from commonly used 3D printing materials simply are not strong enough for safety-critical automotive components. The advent of 3D printing in polycarbonate, however, has initiated a paradigm shift.
With the incredible strength of polycarbonate as described above, along with significant developments in 3D printing technology, such as a better understanding and employment of thermal management and innovations in bed adhesion, users are now empowered to create extremely strong functional parts for end-use applications.
The ability to 3D print polycarbonate also has revolutionized the rapid prototyping process as prototypes for polycarbonate parts can now be created in the same material as the end-use part. Even if a production part’s final iteration will be injection-molded, 3D printing in polycarbonate allows quick design changes, a more efficient method of testing,and an easier, money-saving way to create a new prototype virtually immediately.
Click here to download.
Download Guide
HOW TO 3D PRINT WITH POLYCARBONATE
With all of the material’s superior qualities, why doesn’t everyone print everything in polycarbonate? To put it simply, polycarbonate is not an easy material with which to work. Successfully printing the material starts with high-quality polycarbonate filament and requires both a high-performance desktop 3D printer capable of printing and managing high-temperature materials and an effective method of bed adhesion to prevent warpage.
Choose High-Quality Polycarbonate Filament
As with any other material, it is critical that you choose a high-quality filament when printing with polycarbonate. While a spool of filament might look flawless on the outside and carry a budget-friendly price tag, beware of cheap materials. Manufacturers of low-quality filament are able to keep their prices down by producing their filament with additives and fillers, the addition of which negatively affects the 3D printing experience and the quality of the final part. Inferior product is also less expensive because it often has air pockets or debris embedded in it — a problem that could clog or jam nozzles and ruin a print.
Furthermore, manufacturers who cut corners to save time or are careless with their production methods tend to make filament that is extruded at lighter tolerances. As a result, inconsistent diameters will cause over- or under-extrusion, creating blobs and imperfections in the final print.
When choosing an engineering-grade polycarbonate filament, make sure to buy from a trusted source. Know where the manufacturing facility is located and inquire about their quality control process. Is the filament pure or does it contain additives? If possible, try to procure a sample or at the very least study photos of sample prints to try to assess the filament’s quality. The ideal polycarbonate filament will deliver easy printability, structural integrity, and a beautiful finish.
Choose the right 3D printer
When it comes to 3D printing in polycarbonate, you must choose a 3D printer that adeptly handles high temperatures. In addition to having a high temperature hot end and heated bed, a 3D printer with an enclosed build chamber is essential for printing polycarbonate plastic.
Airwolf 3D developed the first commercial desktop 3D printer to print in polycarbonate and later fully optimized the process with the AXIOM Series of 3D printers.One of the greatest barriers to entry when 3D printing in polycarbonate is simply having a 3D printer that effectively reaches high enough temperatures for extruding the high-temperature material. There are not a lot of machines under $50,000 that effectively achieve this.
Successfully printing in polycarbonate requires a hot end that reaches temperatures of 290 to 315 degrees Celsius. Your print bed temperature must be able to reach 140 to 145 degrees Celsius.
Enclosed Build Chamber
When it comes to 3D printing in Polycarbonate, you not only need a printer that reaches the requisite high extruder and bed temperatures, but also an enclosed print chamber to manage the heat and prevent imperfections in the printed part, such as cracking and deformation.
Having a closed print environment becomes even more critical when you are printing large parts. The bigger your print, the less you are able to rely simply on the bed’s heat to maintain a stable ambient printer temperature. To keep the entire part warm and prevent the cracking that comes with premature cooling, you must achieve proper thermal management by employing a high-performance enclosure like the signature patented build chamber of any AXIOM series printer.
Bed Adhesion
In addition to heat management, the other critical factor when printing in polycarbonate is proper bed adhesion. In the 3D printing world, bed adhesion for polycarbonate is the number one challenge that most users face when attempting to print in the high-performance material. Polycarbonate is among the most finicky 3D printing materials because it has a high tendency to shrink and warp, making strong bed adhesion essential for successfully printing in the material.
Hobbyists have done some experimentation with bed adhesion, but with little success. Solutions range from household items like gluesticks and hairspray to toxic slurries and even super glue — an only moderately effective option that is practically guaranteed to break your glass. In the end, almost every solution was messy, dangerous, or destructive and a waste of money.
Seeing the need for a safe, highly effective way to get polycarbonate to stick to a glass print bed, Airwolf 3D formulated Wolfbite Mega. A liquid bed adhesion solution, Wolfbite Mega creates a heat-activated film on your glass plate. While printing, the solution strongly bonds the polycarbonate print to the glass. Once the print is complete and cooled, the bed adhesion solution automatically deactivates, allowing the part to simply release from the bed — no pulling, scraping, or cutting required.
To use Wolfbite Mega, simply apply a coat of the solution on your glass print bed before starting your polycarbonate print. Like all Wolfbite formulas, Wolfbite Mega is non-toxic and environmentally safe to wash down the drain.
The easiest, most effective way to 3D print polycarbonate
As outlined above, the essential factors for printing in polycarbonate are:
- A high-temperature hot end and heated print bed
- Enclosed build chamber
- Effective bed adhesion
As innovators of the first commercial desktop 3d printer to print in polycarbonate, Airwolf 3D largely has built its reputation on the fact that we build the only 3D printers in their price range to print polycarbonate and other “difficult” materials successfully.
The AXIOM All-in-One System is the easiest solution to getting started printing in polycarbonate as quickly and easily as possible. Complete with an AXIOM Dual 3D printer, Airwolf 3D’s signature high-performance polycarbonate filament, Wolfbite Mega, and a host of other 3D printing filament and accessories for professional use, The AXIOM All-in-One System has everything you need to implement 3D printing into your workflow.
For more information, including a solution customized for your organization, please contact us at (949)478-2933 or [email protected].
Download our Guide "The Key to 3D Printing Large Polycarbonate Parts"This guide is intended to shed light on many of the methods we have used since 2014 to master polycarbonate printing on the desktop. In particular, we will pay close attention to temperature requirements, bed adhesion, printer configurations, and best settings practices.
Reading time: 15 minutes
5 Best Polycarbonate 3D Printers Reviewed (Fall 2022)
5 Best Polycarbonate 3D Printers Reviewed (Fall 2022)For 3D Print is reader-supported. We may earn a commission through products purchased using links on this page. Learn more about our process here
Polycarbonate filament is a must-use material for many 3D materials, thanks to its durability and heat resistance. According to a study by Harvard, it can even be used to manufacture 3D printed material for aeronautic applications. However, if you don’t find the right 3D printer, your polycarbonate projects will fail before you’ve even started. To save you from wasting time and money, we reviewed the best polycarbonate 3D printers on the market and ranked them on our list of favorites.
When choosing our top picks, we considered specific factors like material quality, software, features, and cost to determine which polycarbonate 3D printers can provide you with the most value. Whether you are new to the world of 3D printing or you’re a professional printer looking to incorporate polycarbonate fiber into your projects, there’s something for everyone here.
Top 5 Polycarbonate 3D Printers Reviewed in 2022
?
Consumer Engagement
Chosen by 4457 people in the past 30 days
9.9
Customer Feedback
Customer Feedback
9.5
Brand Reputation
Based onweb analytics
9. 8
Features & Benefits
Product Review
9.6
9.9
If you’re looking for a polycarbonate 3D printer that offers useful features and impressive versatility for a mid-range price, the Qidi X-Plus is the right choice for you. Designed with quality and affordability in mind, this machine successfully strikes a balance between the two by offering features like a double-sided print bed, two interchangeable extruders, an intuitive interface, and high precision printing for less than $1000.
Qidi is one of the leads in 3D printer manufacturing, and its X-Series of printers offer users a wide range of options. The X-Plus is one of their larger printers, boasting a 4.3” color touchscreen as well as the original creation of the AB extrusion system and removable magnetic platform sticker.
What makes it stand out?
- As our Editor’s Choice, it shouldn’t come as a surprise that there were many things we liked about this printer. The design is sleek and professional, while the large, enclosed build area is the perfect space for bigger projects.
The updated slicer software has been redesigned with the user in mind and provides a beautiful, easy-to-use UI along with higher print quality.
Which disadvantages must you keep in mind?
- There aren’t many things we didn’t like about the X-Plus. Earlier Qidi printers lacked several useful software features and often confused inexperienced users, but these are no longer issues thanks to Qidi’s latest software update. One minor complaint some may face is having to switch between two filaments, but it isn’t too much of a hassle. Additionally, while the print quality is great, it isn’t as smooth or precise as some of its competitors.
?
Consumer Engagement
Chosen by 8498 people in the past 30 days
9.5
Customer Feedback
Customer Feedback
9.1
Brand Reputation
Based onweb analytics
9.0
Features & Benefits
Product Review
9.4
9.5
The DigiLab 3D45 is an incredibly reliable machine built for heavy usage and high-quality results. Featuring a direct drive, metal extruder for smooth 3D prints, filament run-out detection that resumes printing where you left off, and a built-in automatic leveling sensor, we consider this premium printer to be the best choice for those who can afford the hefty price.
While many 3D printer manufacturers are scrappy startups, Dremel is an exception. The company has made a name for itself by producing quality power tools over the past 85+ years, and they clearly put the same care into crafting their flagship DigiLab 3D printer. The DigiLab 3D45 is a good fit for engineers, professional product developers, and tech-savvy hobby printers alike, thanks to Dremel’s top-tier design.
What do we love it for?
- We like the stellar print quality and consistent performance that the DigiLab 3D45 offers, with no misprints or stringing occurring in any of our test projects. The included DigiLab 3D Slicer software uses the Cura platform that can be found in many other 3D printers, so it is easy for beginners to use and familiar for advanced users.
We also like the convenience of the Dremel Print Cloud, which allows you to slice files, launch projects, and monitor your prints in real-time using the built-in HD camera.
What were we disappointed with?
- The DigiLab 3D45 undoubtedly lives up to the Dremel legacy, but there are a few things we didn’t like. Although the machine can handle a wide range of materials, loading third-party filament spools proved to be a challenge at times. The machine itself is also quite bulky, weighing 47 pounds and taking up a larger footprint than other printers in its class, so some aesthetic improvements would go a long way in matching the quality of the work it produces.
?
Consumer Engagement
Chosen by 8767 people in the past 30 days
8.9
Customer Feedback
Customer Feedback
8.7
Brand Reputation
Based onweb analytics
8.8
Features & Benefits
Product Review
8.5
8.9
The Gantry Pro is worth exploring if you’re looking for an affordable printer that doesn’t skimp on features. With its large print area, lattice glass platform, and resume print technology, this machine offers premium features that aren’t typically found on other printers in this price range.
Recent upgrades have made the Gantry Pro unbeatable when it comes to providing users the best value for a low cost. Gantry made notable improvements, such as the addition of dual z-axis motors and dual y-axis tracks for more accurate printing, extended filament compatibility for a greater range of projects, and a Titan Direct extruder for smoother, more convenient extrusion.
What are our favorite features?
- We like how feature-rich the Gantry Pro is, especially considering its extremely affordable price of sub-$400. This printer is not only easy to assemble and use right away but also boasts high-quality printing capabilities comparable to machines with much higher price tags. We also like that Gantry gives users the option to upgrade this printer even further by adding an auto-leveling feature, Wi-Fi connectivity, and an upgraded touchscreen for a low extra cost.
What could be better?
- Even though the Gantry Pro offers better quality than what you might expect from other printers in its price range, it is still an entry-level polycarbonate 3D printer with room for improvement. We didn’t like the open frame, which leaves the bed unprotected. Even the slightest bump to the machine can ruin a project, resulting in wasted time and money. The exposed frame also poses a safety hazard, especially around small children who could burn themselves on the hot moving parts.
?
Consumer Engagement
Chosen by 2218 people in the past 30 days
8.7
Customer Feedback
Customer Feedback
8.4
Brand Reputation
Based onweb analytics
8.5
Features & Benefits
Product Review
8. 2
8.7
With its larger build volume, remote print management capabilities, and swappable nozzle design, the Adventurer 4 aims to please a wide variety of users. Casual hobbyists, professional designers, and educational institutions alike have chosen this machine for its dazzling array of features, making it our top choice for a versatile polycarbonate 3D printer.
The Adventurer 4 is the latest printer from FlashForge USA and offers several much-needed feature upgrades from its predecessor. Like the Adventurer 3, this printer features a fully enclosed build chamber and rugged polymer casing, but its build volume is noticeably larger. The modular extruder setup of the Adventurer 3 is also included, but now you can expect higher nozzle temperatures with a greater range of material compatibility.
What makes it special?
- In addition to its sturdy, reliable build, we liked the large 4.3” touchscreen, clean UI, and intuitive user interface. The built-in HD camera and Wi-Fi connectivity are helpful as well, offering remote build control that can be easily monitored for precision.
Overall, we like how this system built on the success of its predecessor, keeping the best features of the Adventurer 3 while improving on its shortcomings. With its premium features and affordable price tag, this printer offers something for everyone.
What cons did we find?
- However, while we can’t deny the Adventurer 4 is a well-built printer, it falls flat when it comes to its proprietary FlashPrint software. With only one standard profile for slicer support, beginners are left to try and build additional profiles from scratch. The included filament spool leaves something to be desired as well, producing an unimpressive first print with a rough surface finish that could result in a major hang-up for less experienced users.
?
Consumer Engagement
Chosen by 2231 people in the past 30 days
8.5
Customer Feedback
Customer Feedback
8.3
Brand Reputation
Based onweb analytics
8.1
Features & Benefits
Product Review
8. 2
8.5
The Bibo 2 Touch surfaced on Amazon around 2016 and has since gained massive popularity, with over 500 positive reviews and regular placements on bestseller lists. Bibo is a lesser-known 3D printing manufacturer based in China, so you may be tempted to pass this printer up in favor of a more expensive option from a big-name printing company. But with features such as dual extruders, filament detection, add-on laser engraving module, and full-color touch screen, the Bibo 2 Touch definitely lives up to the hype.
This machine’s many powerful features make it a solid choice for beginners. Assembly typically takes less than an hour since it comes 95% assembled. And with larger z- and x-axis guide rods than many printers on the market and a demountable glass bed for easy removal, beginners can learn 3D printing with less trial and error.
What stands out?
- We liked the quick assembly, intuitive touchscreen interface, and straightforward, reliable features.
Plus, with the dual extruders perfectly leveled right out of the box and an all-metal frame to increase precision and stability, we’ve found that the printing quality is consistently on-par with most other highly reviewed printers at higher price points. Overall, the Bibo 2 Touch seems to come with everything a beginner could want in their first polycarbonate 3D printer.
What cons did we manage to find?
- While it is an excellent choice for beginners looking for an easy-to-use, affordable option, there are a couple of things about the Bibo 2 Touch that we would like to see improved. Auto-bed leveling features are sorely missed here, and the laser engraver continuously proves to be weaker than most others on the market. Additionally, while the software setup is simple enough, the clunky, convoluted process for setting up wireless file transfer is bound to be a point of frustration.
Things to Consider
Polycarbonate filament is strong, durable, and incredibly tough. As a naturally transparent thermoplastic, it is unique in its high-impact and heat resistance, but it is more prone to warping than most other transparent materials. While it is an ideal material for countless projects, not every 3D printer can successfully print with polycarbonate filament.
Because of its fickle nature, 3D printing with polycarbonate filament requires a very high ambient temperature along with a high-performance nozzle if the printer cannot achieve a high enough temperature, the polycarbonate filament with separate or begin to crack between the printed layers.
Important Features
While advanced features will depend on the amount you’re willing to pay for the machine, the most important factors to consider when searching for the best polycarbonate 3D printer Trusted Source Polycarbonate based multifunctional self-sensing 2D and 3D printed structures for aeronautic applications - NASA/ADS Different polycarbonate materials have been reinforced with carbon nanotubes to tune electrical conductivity and to induce piezoresistive self-sensing capabilities. Further, the composites were processed by solvent casting and fused deposition modelling (filament for 3D printing) methods. An electrical conductivity percolation threshold of ≍0.3 wt.% has been found for solvent casted films, whereas samples processed by 3D printing show higher thresholds, ≍2 wt.%, presenting all samples a similar maximum electrical conductivity, thermal and chemical properties. ui.adsabs.harvard.edu are always going to be the same. For our recommendations, we looked for specific selection criteria such as quality software, compatible printing materials, a large build volume, a removal printing plate, adjustable nozzles to account for layer thickness, and a valuable warranty.
Technology
Many printers come pre-packaged with proprietary software, but not all technology can effectively handle an advanced material like polycarbonate filament.
Some printer software simply doesn’t offer options for working with polycarbonate filament, which can be a challenge for inexperienced users. Look for polycarbonate 3D printers that offer robust, feature-rich software like the Dremel DigiLab 3D Printer, whose DigiLab 3D Slicer software includes built-in profiles for working specifically with polycarbonate filament. As a bonus, their user-friendly interface can save you a lot of frustration when it comes to adding additional printing profiles.
Compatible materials
As we mentioned above, polycarbonate filament is a very strong material and therefore takes a lot of heat to print with. If the 3D printer’s casing is flimsy or low-quality, it is a guarantee that it won’t be able to hold up to the high temperatures needed for a successful polycarbonate project.
To successfully print using polycarbonate filament, your 3D printer requires a nozzle that can reach temperatures between 500- and 590-degrees Fahrenheit, as well as a heated printing plate that can reach up to 300-degrees Fahrenheit. Not every printer can achieve these high specifications, which can be the biggest barrier when it comes to using polycarbonate filament in your 3D printing projects.
In addition to reaching the required high extruder and plate temperatures, an enclosed print chamber can help manage the heat and prevent any deformation to the polycarbonate filament during printing.
Proper thermal management must be maintained to keep the entire project warm during printing, and the bigger your project is, the less likely you’ll be able to rely on the heat from the plate alone.
Printers with robust, reliable hardware, such as the FlashForge Adventurer 4 3D Printer or the Dremel DigiLab 3D Printer, are ideal here. They both feature an enclosed build chamber along with a sturdy metal casing and high-temperature extruders, so they can stand up to the heat and produce consistently great results.
Build volume
The build volume of a 3D printer is exactly what it sounds like: the maximum size of any object you can print. This might go without saying, but the larger the build volume of a printer is, the more variety you have when it comes to projects.
If you’re a casual hobbyist, you may be tempted to buy a 3D printer with a small build volume so that it may fit on a personal desk easier. However, consider the fact that many projects involving polycarbonate filament tend to be on the larger side. A small build volume will greatly limit the size of the projects you can make.
For beginners searching for the best polycarbonate 3D printer, aim to find a machine with a larger build volume that doesn’t come with a massively high price tag. Printers like the ADIMLab Gantry Pro 3D Printer and the R QIDI TECHNOLOGY 3D Printer give you the ability to create polycarbonate projects without compromising on size.
Printing plate
There are many different types of printing plates, but not all of them are convenient to use with polycarbonate filament. In addition to proper heat management, another crucial factor for polycarbonate printing is plate adhesion.
Polycarbonate filament is one of the more difficult high-performance materials to print with due to its tendency to warp and shrink, so strong plate adhesion is a must.
Look for a 3D printer that features a removable printing plate that provides easy adherence, such as the R QIDI TECHNOLOGY 3D Printer’s magnetic plate sticker, the ADIMLab Gantry Pro 3D Printer’s lattice glass plate, or the BIBO 3D Printer’s demountable glass platform. These printing plates are well-suited to the high temperature needed to print with polycarbonate filament, provide an effective surface for the project to adhere to, and can be easily removed for more convenient project separation.
Layer thickness
Printing with polycarbonate filament requires specific measurements when it comes to layer thickness, so finding a 3D printer with adjustable nozzles is important.
The ideal space left between the nozzle and plate should be 0.1mm, while the recommended wall thickness of the polycarbonate itself is a minimum of 1.2mm. Since it is critically important to adjust the nozzle height to compensate for the added thickness of the plate surface, a modular extruder setup like the one found in the FlashForge Adventurer 4 3D Printer is ideal. The nozzle can be detached and reattached quickly for easy repositioning.
Warranty
While a high-quality printer can provide months of use without issue, a warranty can go a long way in terms of security. Look out for printers that include a warranty of 12 months or longer, like those found with the BIBO 3D Printer or R QIDI TECHNOLOGY 3D Printer.
Some polycarbonate 3D printer manufacturers even allow resellers to offer warranty support, which can be helpful for quick, convenient repairs. However, other manufacturers do not, so it is important to consider which option would provide you with the highest value.
Which project do you need to use polycarbonate for?
Polycarbonate is a lightweight yet highly durable thermoplastic ideal for use in several projects that require high-performance material. With its high tensile strength and ability to withstand very hot temperatures, polycarbonate filament is one of the most versatile materials available for 3D printing and can be used in a wide range of projects.
It has been used by professional 3D printers in a variety of industries, such as for skylights and security lights in buildings, room dividers for office spaces, and siding for agricultural greenhouses. A team of engineers even used polycarbonate filament to build an entire house Trusted Source 3D printed house: Builders say the method will reduce new home construction costs - CNN The company can set up its Autonomous Robotic Construction System at a build site in six to eight hours. It then lays concrete layer by layer, creating footing, the foundation of a house and the interior and exterior walls of the structure. www.cnn.com , according to CNN.
Since it is a relatively cheap and easy to form material, if you have the right printer, it can be used in many everyday applications as well. Simple projects that utilize polycarbonate filament may include phone cases, digital data storage devices like DVDs and CDs, baby bottles, and food containers. However, due to its strength, heat resistance, and flexibility, it can also be found in more advanced projects such as medical devices, bulletproof glass, telecommunication hardware, automotive parts, or electrical components.
How to clean a 3D printer after use?
Cleaning your polycarbonate 3D printer is essential for keeping it in proper working condition and achieving perfect printing results. Always make sure to follow the instructions provided by your printer’s manufacturer to ensure you’re maintaining it properly, and remember to exercise caution so that you don’t damage your printer.
As a general guideline, always clean the printing plate once it has cooled using an IPA concentration or specialized cleaning solution. Soak a paper towel, microfiber cloth, or cotton ball with the IPA concentration and clean the surface of the printing plate in a circular motion. Repeat until the plate is free of any oils, fingerprints, or leftover printing filaments that can lead to imperfections during your next printing project.
If your printer has a glass base, you may need to use a scraper to remove any additional residue as well. If you have a demountable printing plate, we recommend removing it before cleaning since this can help you avoid damage.
Clear out the extruder by removing any remaining filament that has leaked through the nozzle to prevent clogging in the future. Some people find that using a nylon cleaning filament when switching filaments also helps to clear out any remaining filament that refuses to be dislodged. You should also clear debris from the nozzle’s exterior by using a wet cloth or alcohol wipe while the nozzle is still hot. If this doesn’t work, use a small wire brush or blade to scrape off the remaining debris.
What’s the best way to organize a 3D printer working station?
Your 3D printing station will depend on how large your printer is, but there are a few things to keep in mind when organizing your workspace. First, ensure your workspace is level, near an outlet, and located in an area with good ventilation. Fumes are always present when 3D printing, even when you can’t smell them. Whenever your 3D printing projects are warm or melting, volatile organic compounds (also known as VOCs) are being released into the air around your printer. Placing your workstation near a window, opening doors between rooms, using fans, or simply placing your printer in a room with less foot traffic are easy ways to reduce your exposure to VOCs.
Leave plenty of room beside the 3D printer for the wash and cure systems, as well as an area to store your parts. Some essential 3D printing parts, such as filaments, can be rendered unusable if they aren’t properly stored, so make sure to keep them in a moisture-free, air-tight container such as a dry box, dehumidifier, or vacuum bag.
Depending on the projects you’ll be printing, you may wish to set up a finishing station near your printer to store projects that require gluing, polishing, or painting. No matter what, always make sure that your 3D printer has plenty of space surrounding it and is clear of any dangling items that might touch it while it is printing.
Our Verdict
Whether you’re just entering the world of 3D printing or you’re a professional who wants to incorporate polycarbonate filament into your 3D printing projects, scouring the internet for the best polycarbonate 3D printers can be intimidating. Knowing what to look for can take a lot of frustration out of the process, though, so with our top picks, you can breathe a sigh of relief.
For the most bang for your buck, the ADIMLab Gantry Pro 3D Printer holds the title of our Best Value 3D printer for projects using polycarbonate filament. With a score of 8.9, the Gantry Pro delivers high-quality features not typically found in other affordable printers in the price range.
With a score of 9.5, the Dremel DigiLab 3D Printer affords you premium quality printing, an intuitive interface, and a reliable machine for any type of user.
R QIDI TECHNOLOGY 3D Printer simply can’t be beaten. Boasting high-quality features, updated slicer software, and a 4.3” color touchscreen, this robust 3D printer deserves its spot as the best polycarbonate 3D printer with a score of 9.9.
References
1.
Polycarbonate based multifunctional self-sensing 2D and 3D printed structures for aeronautic applications - NASA/ADS
Different polycarbonate materials have been reinforced with carbon nanotubes to tune electrical conductivity and to induce piezoresistive self-sensing capabilities. Further, the composites were processed by solvent casting and fused deposition modelling (filament for 3D printing) methods. An electrical conductivity percolation threshold of ≍0.3 wt.% has been found for solvent casted films, whereas samples processed by 3D printing show higher thresholds, ≍2 wt.%, presenting all samples a similar maximum electrical conductivity, thermal and chemical properties.
ui.adsabs.harvard.edu
2.
3D printed house: Builders say the method will reduce new home construction costs - CNN
The company can set up its Autonomous Robotic Construction System at a build site in six to eight hours. It then lays concrete layer by layer, creating footing, the foundation of a house and the interior and exterior walls of the structure.
www.cnn.com
Overview of high-temperature FDM plastics for industrial 3D printing / Sudo Null IT News materials in stock. To understand what materials are needed to obtain a strong and lightweight part, we are moving from personal printing to industrial printing.
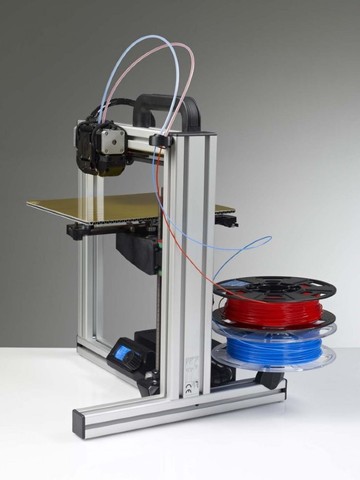
Where are superplastics needed?
Plastics with outstanding properties are very useful in space. No, it’s not yet possible to print a rocket engine out of plastic, the heat resistance is not even close to the same, but it is ideal for various parts around. An example is Stratasys and the "climate control" of Atlas V rockets. 16 printed parts instead of 140 metal parts - faster, lighter, cheaper. And this is not a theoretical project, it has already flown into space.
Another example is aviation. The flight altitude is lower, but the application is more massive. Here, too, there is a reason to reduce the mass of parts, switch to plastic where possible. It is used in the aircraft industry and direct metal printing, when it comes to engine components or fuselage frame parts, but less loaded structural elements, such as cabin ventilation and interior elements, are best made from plastic. This direction is being developed, for example, by Airbus.
We descend from heaven to earth: here the mass is no longer so critical, other properties of engineering plastics are of interest. Resistance to aggressive chemicals and elevated temperatures, the ability to create structures inaccessible to classical methods. At the same time - a lower price, in comparison with metal printing. Printed products are used in medicine, oil and gas industry, chemical industry. As an example, a mixing block with a complex channel structure, made for illustration in a section.
Difference from conventional plastics
Why not launch PLA into space and make air vent grilles from ABS? A number of requirements are applied to engineering plastics related to resistance to high and low temperatures, fire resistance, mechanical strength. Usually all at once. So, it is undesirable to launch PLA “floating” when interacting with the environment or perfectly burning ABS into the sky.
Now - to what, in fact, plastics are used in industrial printing using FDM / FFF technology.
Polycarbonate filaments
Polycarbonate is a common industrial plastic with high impact resistance and transparency, also produced for the needs of FDM printing. The material holds temperature better than ABS, is resistant to acids, but is sensitive to UV radiation and is destroyed by oil products.
Clear polycarbonate, PC
The maximum operating temperature for polycarbonate products is 130 °C. Polycarbonate is biologically inert, products made from it can withstand sterilization, which makes it possible to print packaging and auxiliary equipment for medicine.
- Stratasys PC, PC-ISO for Fortus printers. The first is general purpose, the second is certified for biocompatibility, for medical use.
- Intamsys PC;
- Esun ePC;
- SEM PC;
- PrintProduct PC;
ABS/PC
Polycarbonate/ABS alloy combines the sanding and painting capabilities of ABS with higher impact resistance and operating temperature. Retains strength at low temperatures down to -50 °C. Unlike pure PC, it is better applicable in cases where it is necessary to eliminate the layered structure of the part by grinding or sandblasting. Application: production of housings and elements of controls for piece and small-scale production, replacement of mass-produced plastic parts in equipment, parts for which have ceased to be produced.
- Stratasys PC/ABS;
- Roboze PC-ABS;
- SEM ABS/PC;
- BestFilament ABS/PC.
Polyamide based filaments
Polyamides are used in the production of synthetic fibers, a popular material for printing by selective laser sintering (SLS). For printing using FDM / FFF technology, polyamide-6 (kapron), polyamide-66 (nylon) and polyamide-12 are mainly used. Common features of polyamide-based filaments include chemical inertness and anti-friction properties. Polyamide-12 is more flexible and resilient than PA6 and PA66. Operating temperature approx. 100 °C, some modifications up to 120.
First of all, gears are printed from polyamide. The best material for this purpose, which can be worked with on a regular 3D printer with a closed chamber. Abrasion resistance allows you to make rods, cams, sliding bushings. In the line of many manufacturers there are composite filaments based on polyamide, with even greater mechanical strength.
- Stratasys Nylon 6, Nylon 12, Nylon 12CF. The latter is filled with carbon fiber.
- Intamsys Nylon, PA6.
- Taulman Nylon 618, Nylon 645 based on PA66 and PA6 respectively. Nylon 680 is approved for use in the food industry. Alloy 910 is a low shrinkage polyamide alloy.
- PrintProduct Nylon, Nylon Mod, Nylon Strong;
- REC Friction;
- BestFilament BFNylon.
Moving on to the fun part
You can work with polycarbonate or polyamide on a regular 3D printer. With the filaments described below, it is more difficult, they require other extruders and maintaining the temperature in the working chamber, that is, you need special equipment for printing with high-temperature plastics. There are exceptions - for example, NASA, for the sake of experiment, upgraded the Lulzbot TAZ popular in the USA to work with high-temperature filaments.
Polyetheretherketone, PEEK
The operating temperature of PEEK products reaches 250 ° C, short-term heating up to 300 is possible - indicators for reinforced filaments. PEEK has two disadvantages: high price and moderate impact resistance. The rest is pluses. The plastic is self-extinguishing, heat-resistant, chemically inert. Medical equipment and implants are produced from PEEK, abrasion resistance makes it possible to print parts of mechanisms from it.
- Intamsys PEEK;
- Apium PEEK;
- Roboze PEEK, Carbon PEEK. The second is reinforced with carbon fiber.
Polyetherimide, PEI
He is Ultem. A family of plastics developed by SABIC. The characteristics of PEI are more modest than those of PEEK, but the cost is noticeably lower. Ultem 1010 and 9085 are Stratasys' primary materials for printing functional parts. PEI is in demand in the aerospace industry - the mass is much less compared to aluminum alloys. Operating temperatures of products, depending on the modification of the material, reach 217 ° C according to the manufacturer and 213 - according to the results of tests by Stratasys.
The advantages of PEI are the same as those of PEEK - chemical and temperature resistance, mechanical strength. It is this material that Stratasys is promoting as a partial replacement for metal in the aerospace industry, for drones, the manufacture of tooling for molding, the rapid printing of functional parts in pilot production.
Atlas V rocket cooling system components and Airbus plastic parts shown as an example at the beginning of the review are made of Ultem 9085.
- Stratasys Ultem 1010 and 9085, for Fortus 450mc and 900mc printers.
- Intamsys Ultem 1010 and 9085;
- Roboze Ultem AM9085F;
- Apium PEI 9085.
Polyphenylsulfone, PPSF/PPSU
Another material that combines in its properties temperature resistance, mechanical strength and resistance to chemical attack. Stratasys PPSF is certified for aerospace and medical applications. Positioned as a raw material for the production of auxiliary medical devices, it can be sterilized in steam autoclaves. It is used in the production of parts for laboratory installations in the chemical industry.
- Stratasys PPSF;
- 3DXTech Firewire PPSU.
Polysulfone, PSU
Less common than PPSU, similar physical characteristics, chemically inert, self-extinguishing. 175°C operating temperature, up to 33% cheaper than PPSU.
- 3DXTech Firewire PSU
Comparison of filament characteristics
* calcination for 2 hours at 140 °C.
** Apium PEEK 450 natural, impact test results not available with similar methods. Temperature resistance is specified for unfilled PEEK.
Data shown for Stratasys filaments, excluding PEEK. If a range of values is indicated, then the tests were carried out along and across the layers of the part.
About composite filaments
Most FDM printing materials have composite versions. If we talk about PLA, then metal or wood powders are added to it to change the aesthetic properties. Engineering filaments are reinforced with carbon fiber to increase the rigidity of the part. The influence of such additives on the properties of plastic depends not only on their quantity, but also on the size of the fibers. If a fine powder can be considered a decorative additive, then the fibers already significantly change the characteristics of the plastic. By itself, the word Carbon in the name of the material does not yet mean outstanding properties, you need to look at the test results. For example: Stratasys Nylon12CF has almost twice the tensile strength, when tested along the layers, than Nylon12.
Exotic variant - implementation of continuous reinforcement from Markforged. The company offers a reinforcing filament for co-FDM printing with other plastics.
Other specific properties
Engineering plastics are not only resistance to high temperatures and mechanical strength. For housings or boxes for storing electronic devices, and in environments where flammable volatile liquids are used, materials with antistatic properties are required. In the Stratasys line, this is, for example, ABS-ESD7.
- Stratasys ABS-ESD7;
- Roboze ABS-ESD
Conventional ABS does not have UV resistance, which limits its outdoor use without a protective coating. As an alternative, ASA is offered, which has characteristics similar to ABS, except for the UV resistance.
- REC Eternal;
- SEM ASA;
- BestFilament A.S.A.
Original alternative
Plastic can replace metal in many areas, as it is superior in lightness, thermal and electrical insulation, resistance to reagents. But printouts from the best FDM filaments do not reach the physical indicators of metal products.
Chemical giant BASF offers the Ultrafuse 316LX FDM filament, with a stainless steel content of 80%. The part is printed on an FDM printer and then placed in an oven where the binder plastic is burned off and the metal is sintered. The part obtained in this way is much cheaper than the one made by direct metal printing. With an FDM printer and a suitable oven, no new equipment is needed at all.
Note that a similar solution is offered by the Virtual Foundry company - its Filamet, with bronze or copper powder, is baked in a similar way. The choice of metal hints at decorative rather than engineering applications.
AIM3D has its own implementation of this principle - the ExAM 255 printer does not work with filament, but with granules. This allows the use of raw materials for FDM printing, which are usually used in MIM installations, Metal Injection Molding. For sintering the part, the company offers an ExSO 9 furnace0. It is also possible to print with plastic granules, which is usually cheaper than using traditional filament.
Special machinery for engineering plastics
To recap. In a nutshell: the considered consumables differ from the usual materials in high printing temperature, which requires the use of special equipment, and serious heat resistance and mechanical strength of the manufactured parts. To work with such filaments, 3D printers with an extruder operating temperature of 350 °C and a heat-stabilized working chamber are required. Top 3D Shop specialists will help you with the selection of an industrial 3D printer and plastics for solving the most interesting tasks.
Want more exciting news from the world of 3D technology?
Follow us on social. networks:
Polycarbonate for 3d printer characteristics
Updated: 10/05/2022
Polycarbonate. Properties of polycarbonate and application in the field of 3D printing.
Follow the author if you like his publications. Then you will be notified of his new posts.
You can always unsubscribe from notifications in the author's profile.
Article applies to printers:
[IMG WIDTH=501 HEIGHT=139]
Polycarbonates belong to a special group of thermoplastic polymers.
Polycarbonate (PC) is a very strong material that also has the property of high impact resistance. The characteristics of polycarbonate are similar to those of acrylic (PMMA), but polycarbonate is stronger and suitable for use over a wide temperature range.
Unlike most thermoplastics, polycarbonate can undergo large plastic deformations without cracking or breaking, which is an advantage for polycarbonate applications in 3D printing.
Polycarbonate is valuable in the field of prototyping where electrically non-conductive parts are required that cannot be made from sheet metal.
Low water absorption, high temperature resistance, thermal stability and good electrical properties, as well as very high impact strength, are among the many useful properties that polycarbonate has.
Due to the properties of polycarbonate, it can be used in many ways.
Polycarbonate as an electronic component - is a good electrical insulator and has heat and flame retardant properties, it is used in a variety of products related to electrical and telecommunications equipment. It is used as a dielectric with high stability.
[IMG WIDTH=490 HEIGHT=321]
Capacitors with polycarbonate dielectric.
[IMG WIDTH=302 HEIGHT=302]
Polycarbonate is used in industrial areas of automotive and aviation engineering, as a material for prototyping, and also for the manufacture of working parts.
The fact that polycarbonate has an exceptionally high impact strength suggests its use as a material for working parts of equipment.
Cage parts are made of high impact polycarbonate.
Most often, polycarbonate is used as a material for the well-known “cellular polycarbonate”, which is later used to manufacture all kinds of structures and structures.
[IMG WIDTH=424 HEIGHT=322]
Polycarbonate is widely used for dental prototyping. This is because PC is an environmentally friendly material.
Polycarbonate is a plastic that, unlike polyethylene and aluminum, is non-toxic and does not enter into chemical reactions with water and is therefore absolutely safe for health.
Another well-known use of polycarbonate is in the manufacture of optical discs. Of course, for CDs and DVDs, polycarbonate with certain optical properties, the so-called optical polycarbonate, is used. In addition to all the properties described above, optical polycarbonate has properties that allow the laser to read any digital information from the carrier without changing it.
[IMG WIDTH=484 HEIGHT=315]
Due to and despite its properties, polycarbonate is gradually being used in 3D printing. Thanks to the properties of plasticity and in spite of the high temperature resistance.
Unfortunately, not all 3D printers can use polycarbonate material, since the melting point of the most common material for ABS 3D printers is + 220C, at this temperature most 3D printers work. To melt polycarbonate, a temperature of + 282 C is required. In addition to the complexity associated with the melting temperature, there are others, for example, how to achieve uniform solidification of plastic, preventing spreading of the already printed part of the part. Unfortunately, this cannot be achieved on most 3D printers.
But progress does not stand still and some developers of 3D printers have managed to create 3D equipment with the ability to use high-tech polycarbonate.
One such printer is the FORTUS series.
Combining the properties of polycarbonate and the professionalism of the FORTUS series printer, it is possible to print high-precision and high-strength parts that can even be used as a working part of industrial equipment.
[IMG WIDTH=490 HEIGHT=366] [IMG WIDTH=490 HEIGHT=366]
I hope this article will be useful for you.
P.S. Our company will be glad to provide everyone with a polycarbonate printing service on the FORTUS 400mc printer.
Follow the author
Follow the author if you like his publications. Then you will be notified of his new posts.
Polycarbonate for 3D Printing
Polycarbonate is a thermoplastic in honeycomb form widely used as a durable replacement for conventional glass. In addition, polycarbonate has found use as a material for the manufacture of CDs, contact lenses, protective equipment (for example, bicycle helmets or glasses). The combination of transparency of polycarbonate and high strength (about 250 times higher than ordinary glass) makes it possible to produce even bulletproof glass.
Another advantage of polycarbonate is its high resistance to high and low temperatures - from -40 to 120°C. In addition, polycarbonate is prone to attenuation when exposed to open flame, contributing to fire safety, and resistant to acids.
Among the disadvantages of polycarbonate, one can single out a rather high hygroscopicity. Thread spools are recommended to be stored in dry places, and preferably vacuum-packed. In addition, polycarbonate is somewhat vulnerable to ultraviolet light, which leads to loss of strength over time, and is vulnerable to attack by petroleum products and organic solvents.
3D printing application
Polycarbonate printing example
Polycarbonate is rare in FDM printing due to certain technological difficulties, but is rapidly gaining popularity as technology improves.
Polycarbonate requires a fairly high extrusion temperature in excess of 300°C when printing at high speed.
Due to its high hygroscopicity, it may be necessary to dry the consumable immediately before printing.
Otherwise, water vapor may be released during extrusion, clouding of the material and increased shrinkage, which increases the risk of deformation.
Even dry polycarbonate will require the use of a heated worktable up to 90°C-120°C.
It is recommended to use a polyimide film (Kapton) for better adhesion of the first layer to the worktable surface.
Printing examples with dry and slightly damp polycarbonate
Finding the right balance of extrusion temperature and print speed is essential to maintain transparency and avoid nozzle clogging and cracking.
Printing at 30mm/s will require heating up to approximately 265˚C, 285˚C at 60mm/s, 300˚C at 80mm/s and over 305˚C at 120mm/s. The glass transition temperature of polycarbonate is about 150˚C.
Polycarbonate threads are available in standard diameters of 1.75mm and 3mm.
Polycarbonate Safety
Polycarbonate itself is safe, but the material typically uses BPA as the main raw material. Bisphenol A, in turn, is very toxic even in small volumes, up to the excitation of oncological diseases. Unfortunately, polycarbonates often contain residual Bisphenol A (albeit in extremely small amounts), which is released when heated. Accordingly, the use of polycarbonate products for storing hot food or drinks is not recommended. Limited bans on the use of polycarbonate in food packaging have already been introduced in Canada and the EU, and are being considered in the US. We recommend that you print in a well-ventilated area.
Properties of polycarbonate for 3d printing. Test results
Subscribe to the author if you like his publications. Then you will be notified of his new posts.
You can always unsubscribe from notifications in the author's profile.
The article applies to printers:
PRODUCTION THERMOPLASTIC FOR 3D OBJECT MANUFACTURING SYSTEMS
The previous post was about polycarbonate and its applications in various fields. Today we will consider the use of polycarbonate for 3D printing, using the example of polycarbonate from Stratasys.
The tables below may be useful for owners of printers that print on polycarbonate material, as well as for those who want to print parts from polycarbonate material, but do not know about its properties and applications.
Industrial thermoplastic PC (polycarbonate) is widely used in automotive, aerospace, medical and many other fields.
PC provides precision, strength and stability. The created parts are durable and withstand functional testing. PC parts made on the FORTUS 3D industrial machine are 5 to 60 percent stronger than parts made on previous FDM systems. It also has the improved mechanical properties of ABS and the properties of a number of other thermoplastics. The PC printed parts on the industrial FORTUS 3D printer have sufficient strength for conceptual modeling, functional prototyping, tool making and working parts of equipment.
POLYCARBONATE STRENGTH CHART
POLYCARBONATE STRENGTH CHART Explanation:
psi - Pound per square inch - unit of pressure.
MPa – megapascal. Value 10 (to the 6th degree) Pa.
In practice, approximate values are used: 1 atm = 0.1 MPa and 1 MPa = 10 atm. 1 mm of water column is approximately equal to 10 Pa, 1 mm of mercury is approximately equal to 133 Pa.
ASTM D 638 - Standard Test Method for Tensile Properties of Plastics.
ASTM D790 - Flexural properties of non-reinforced and reinforced plastics and electrical insulating materials.
ASTM D256: Izod impact strength of composites made from carbon fibers and EPS.
ASTM D695 Compression testing of rigid plastics.
THERMOPHYSICAL PROPERTIES OF POLYCARBONATE
Explanation of the table THERMOPHYSICAL PROPERTIES OF POLYCARBONATE:
ASTM D648 Test method for polymeric materials.
ASTM D1525 Vicat softening point determination for plastics.
Based on advanced FDM technology
FORTUS systems are based on FDM technology (Fusion Deposition Technology). FOPRUS systems use a wide range of thermoplastics with enhanced mechanical properties so that parts can withstand high temperatures, harsh chemicals, and have increased wear resistance.
Which parts can be produced with FORTUS 3D printer and PC material.
Small parts. Details with a smooth surface. High precision parts. Details with high strength.
ELECTRICAL PROPERTIES OF POLYCARBONATE
Explanation of the table ELECTRICAL PROPERTIES OF POLYCARBONATE:
ASTM D257 - test method for polymeric materials.
C ASTM D150 Standard Test Methods for AC Loss Characteristics and Dielectric Constant (Dielectric Constant) of Solid Electrical Insulation.
ASTM D149-09. Standard Test Method for Dielectric. Breakdown voltage and electrical strength of solid electrical insulating materials at industrial frequencies.
ADDITIONAL PROPERTIES OF POLYCARBONATE
Explanation of table ADDITIONAL PROPERTIES OF POLYCARBONATE:
ASTM D792 - 13. Standard Method for Determining Density and Specific Gravity (Relative Density) of Plastics by Volume of Liquid Displaced.
UL94 - Flammability standard for polymeric materials.
ASTM E831 - Thermal expansion standard for polymeric materials.
ASTM D785 - Standard. Rockwell hardness. Rockwell hardness is determined by the total depth of the impression left by the indenter after the load has increased from the minimum to the maximum value and then returned to the minimum level.
POLYCARBONATE PRINTABLE ON FORTUS INDUSTRIAL 3D SYSTEM
Follow the author
Follow the author if you like his publications. Then you will be notified of his new posts.
Plastic for a 3d printer - types, characteristics
We choose plastic for a 3d printer by type and characteristics.
You have purchased a 3D printer and started printing. Now you need to know what material you want to work with. For example, different materials have different characteristics and are suitable for certain parts. Therefore, it is important that you are aware of the plastics used in 3D printing.
Hide article content
Plastic for 3d printer types and characteristics:
Plastics are the most common material for 3D printing. And this article will explain the difference between each of these plastics. And also what materials are used with each 3D printing technology. For example, such as FDM, SLA and SLS, and much more.
So, plastic for 3d printer types and characteristics
ABS — Plastic for 3d printer
ABS 3D printer plastic is the most commonly used 3D printing plastic. In particular, it is used in car bodies, household appliances and mobile phone cases. It is a thermoplastic and contains a backbone of polybutadiene based elastomers. Which makes it more flexible and impact resistant.
ABS is used in 3D printing when heated to temperatures between 230°C and 260°C. It is a durable material that can easily withstand temperatures from -20ºC to 80ºC. In addition to its high strength, it is a reusable material. It can be welded using chemical processes.
However, ABS is not biodegradable and shrinks when exposed to air. Therefore, the print platform must be heated to prevent warping. But, in addition, it is recommended to use a 3D printer with a closed chamber. To limit particle emissions when printing with ABS.
ABS is mainly used in hardfacing modeling technologies. This is the most affordable 3D printing technology. However, there is also a liquid form of ABS. It is sometimes used in stereolithography and PolyJet processes.
FLEX (Flexible filaments), TPE, TPC — 3D printing with flexible filament
A new type of filament and one of the most successful is FLEX (Flexible filaments), TPE, TPC. They look like PLA 3d printer plastic. But usually made of TPE or TPU. What is the benefit of using these 3D printing filaments? For example, in that they allow you to create deformable objects that are widely used in the fashion industry. For example, in the Danit Peleg collection.
These flexible filaments generally have the same print characteristics as PLA. Although they come in different ranges depending on their stiffness. It's worth figuring out what type of extruder is best for the material to avoid jams when 3D printing.
PC or polycarbonate - Plastic for 3d printer
Polycarbonate (PC) is a high strength material designed for technical applications. The material has good heat resistance. As a result, it is able to withstand any physical deformation up to a temperature of around 150ºC.
However, PC is susceptible to absorbing moisture from the air. Which can affect performance and print stability. Therefore, polycarbonate must be stored in airtight containers.
Plastic for 3d printer using PC requires very high temperatures. If this is not done properly, individual layers may be visible. Due to low temperature or excessive cooling. For example, there are polycarbonate threads on the market. They contain additives that allow filaments to be printed at lower temperatures.
PET - 3d printer plastic
3d printer plastic PET or polyethylene terephthalate, commonly seen in disposable plastic bottles. PET is the ideal thread for any item intended to come into contact with food.
But, in addition, the material is quite rigid and has good chemical resistance. For best results when printing with PET, print at 75-90ºC.
PET is usually sold as a translucent thread. Variants such as PETG, PETE and PETT are also sold. The advantages of PET are that the material does not emit any odors when printed. And it is 100% recyclable.
PLA - Plastic for 3d printer
This 3D printer plastic is known as polylactic acid, or PLA. Plastic for 3d printer PLA has advantages. Because, unlike ABS, it is biodegradable. PLA is made using renewable raw materials such as cornstarch.
PLA is one of the easiest materials to print. Although it tends to shrink a little after 3D printing. You don't need a heated bed when printing in PLA, unlike ABS. PLA also prints at a lower temperature than ABS, from 190°C to 230°C.
PLA is more difficult to handle due to its high cooling and solidification rate. It is also important to note that models can deteriorate when in contact with water.
However, the material is uniform, easy to use. And it comes in a wide range of colors. This makes it suitable for FDM 3D printing.
Gypsum - Plastic for 3d printer
Gypsum is rarely used for 3D printing. In 3D printing, gypsum is used in powder form. The technology is called powder bonding. Used with plaster to create 3D prints.
The powder binding technique was invented at MIT in 1993. This is an Additive Manufacturing (AM) method that consists of curing a powder with a binder.
In 1995, the American company Z Corporation received exclusive rights to this technology. And in 2012, it was acquired by 3D systems, which renamed the company to ColorJet Printing.
Polyamide (nylon) - Plastic for 3d printer
How does polyamide (nylon) 3D printing actually work?
Nylon is a polyamide. It is well suited for 3D printing of functional parts with superior tensile strength compared to PLA. Polyamide is one of the most popular 3D printing materials used by professional 3D printing companies.
3D printed polyamide – the benefits are manifold. It is available at a reasonable price. May include interrelated and interchangeable parts. It can be processed in various ways (dyed, smoothed, spray painted, velvet finish). Today we will explain why polyamide is so versatile and how polyamide (nylon) 3D printing works.
Carbon fiber
Threads, including carbon fibers, are becoming increasingly popular in the industry. Especially considering that Markforged 3D printers specialize in them.
There is a reason for its growing popularity. For example, 3D printing using carbon fiber provides very high strength. While maintaining very light manufactured parts.
Carbon fiber fibers are actually small carbon fibers installed inside a base material. And it can be either PLA or PETG, nylon, ABS or polycarbonate. Which makes them more durable.
The print settings are usually the same as their base material. Although a reliable 3D printer is required. This is because carbon fibers can clog the print nozzle.
Hybrid materials
There are many hybrid materials that mix base plastics. Like PLA, with powders to give them a new color or finish. These materials are typically 70% PLA and 30% hybrid material.
In addition, there are wood threads. Which can range from bamboo, cork, wood dust and more. As a result, materials blended with PLA give the hybrid filament a more organic texture.
There are also a number of machines that use FDM technology to print on metal. For example, Desktop Metal 3D printers. However, these printers are not very affordable for most consumers. Therefore, ColorFabb has released its own metallic 3D filament.
Their threads have the same warp as wood threads. Only with wooden parts exchanged for metal powders. This gives the parts a stylish metallic finish. Depending on which thread is used from these options: copper, bronze, silver, etc.
In addition, the category of hybrid materials also includes building materials. Such as are used in homes. These include rock materials such as cement, bricks and sand. As a result, they give a completely different texture to the models they 3D print.
Solubles
Solubles are materials printed with the intent of being dissolved at a future stage in the manufacturing process. For example, the two most common soluble fiber materials are HIPS (high impact polystyrene) and PVA (polyvinyl acetate).
HIPS is related to ABS and can be diluted with lemon. Whereas PVA is bonded to PLA and can be dissolved using only water.
There are also BVOH threads that are becoming more and more popular. Especially in printers with two extruders. This is due to the fact that the material is soluble in water. And, according to experts, it has a higher solubility than PVA.
3D Printer Plastic: Stereolithography
Technologies such as SLA, DLP or even PolyJet use photosensitive liquid resins to produce. They can be divided into two categories: thermoplastics and thermoplastics. These resins allow you to print objects with a matte or glossy finish.
The range of colors that can be used with resins is limited. Usually limited to white, transparent and red. But there are new developments, such as Formlabs. They release a wider range of resins for their Form 2 SLA 3D printer.
But what makes resins different from FDM filaments? This is that it is not possible to mix resins to get different results. So there are no dual extruder SLA printers.
In addition, when using resins in 3D printing, there is also a post-printing process. This includes cleaning the models in isopropyl alcohol to strengthen the print.
There are some resins in resin 3D printing that are considered more technical. For example, flexible resins that provide greater flexibility and deformation when printed. In addition, there are casting resins for 3D printing jewelry. And biocompatible resins dedicated to the dental sector and dentures.
Polyamides
Objects made from polyamides are usually made from a fine white granular powder. However, there are some material options such as nylon. They are also available in filaments used in Fused Deposition Modeling (FDM).
Polyamides can be used to create parts that come into contact with food. As a result of its biocompatibility. In addition to products containing alcohol.
Composing semi-crystalline structures, polyamides have a good balance of chemical and mechanical characteristics. As a result, they provide good stability, rigidity, flexibility and impact resistance.
These advantages mean that the material has many applications in different sectors. And offers a high level of detail. Polyamides are used in the production of gears, parts for the aerospace market, the automotive market, robotics, medical prostheses and injection molds. Thanks to the high quality.
Exotic 3D Printing Materials - Plastics
- Metal Filled filaments (Metal Filled)
- Wood Filled (Wood Filled)
- Carbon Fiber Filled - Carbon Fiber Filled
- Biodegradable Plastics (bioFila)
- Conductive Plastics
- Conductive Plastics
- luminescent resins
- magnetic resins
- color changing resins
- 3d printer filament - Glow-in-the-Dark
- ceramic resins
Professional 3D printing materials
ASA
FPE
HIPS
PMMA (Acrylic)
POM (Polyacetal)
PP (Polypropylene, Polypropylene)
PVA
Nozzle cleaning filaments (3D printer cleaning thread)
Carbon fiber filament AB/PC/9003
Carbon fiber plastic
Carbon fiber plastic
from wax
PC (polycarbonate) - a group of thermoplastics. These are polyesters of carbonic acid and dihydric alcohols of the general formula (-O-R-O-CO-) n. PC (polycarbonate) belongs to a group of plastics that are known for their strength, toughness and heat resistance.
Used in many applications. Including technical details, DVDs and "bulletproof glass". As a nice bonus, it's also optically clear!
Polycarbonate is an extremely durable but difficult material to 3d print due to its unique properties. As a result, polycarbonate 3d printing has gained some popularity over the years.
Even if it's a little difficult. Let's take a closer look at this fascinating material!
Hide article content
PC (Polycarbonate) - 3D Printing
Printing Issues
Printing at low temperatures causes jamming as shown here.
Polycarbonate has certain properties that make it difficult to work with. As we explore in more detail below. Do you want successful prints? You need to be prepared for the following three challenges:
- Requires high temperatures to properly extrude.
- subject to deformation and shrinkage.
- polycarbonate absorbs moisture.
Polycarbonate Benefits
Polycarbonate printing differs from PLA and other filaments in a number of ways. This affects not only the properties of prints. But also on what you need to do to succeed.
PC is more durable and flexible than PLA, but less than nylon. It is heavier than ABS, PLA or PMMA. However, it is lighter and less dense than ABS.
Its ability to withstand torsional loads is superior to other thermoplastics. And it's flexible enough to be bent at room temperature.
PC has the specifications:
- heat resistant up to 135°C (for reference, PLA can start to deform at around 60°C)
PC - print recommendations
Ambient temperature difficult. But this is if proper precautions are not taken. The material is subject to deformation and shrinkage. Therefore, it is necessary to maintain a constant temperature.
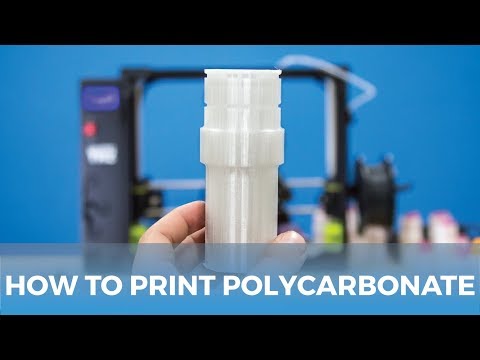
This makes a heated bed essential. The bed should ideally be between 135 and 150°C. There are also third party adhesives. Which you can use to maintain adhesion to the bed.
Sometimes the layers may not stick, separate or crack. As the material cools and deforms. But this can be avoided. By maintaining the ambient temperature in a suitable housing.
Which will provide a more stable ambient temperature. And allow the layers to stick properly. If you don't have access to a 3d printer with an enclosure, there are also several DIY enclosure options.
Nozzle temperature
PC requires a really hot end, which should ideally reach 290-300° C. You may be able to avoid high temperatures. If you are walking slowly or using PC Composite Filament.
Temperature too low or speed too high can cause seizure. So before you start 3d printing from a PC, you will need a printer that can reach these temperatures.
Humidity
Remember that polycarbonate absorbs atmospheric moisture. So keep it dry when not in use. For example, in a sealed container.
And buy quality filament to avoid bubbles in the extruder and bad prints. Moisture will not only affect the integrity of the print. But it will also prevent it from becoming optically transparent.
So PC is like PLA. The moisture it contains evaporates during printing, creating bubbles on the printouts. Which can make them less durable and cloudy looking.
Avoid this by storing your floss in sealed containers with desiccant bags. You can even dry the filament before printing.
PC - general applications
Incredibly high PC pollution in the environment. Because polycarbonate is commonly used in many consumer products. But the good news is that 3D printing from a PC opens up the possibility of recycling materials into new products.
Because it is very durable and transparent. A recycled PC can be used to create fully functional prototypes and beautiful designs.
Polycarbonate can also be used to prototype windows and other transparent products. Thanks to its transparency. Which would cost much more if they were made from other materials.
High temperature resistance means it can also be used for functional prototypes. Where even ABS deforms under heat or stress.
License: Text "3d Printing Polycarbonate - Everything You Need to Know" by All3dP is licensed under the Creative Commons Attribution 4.0 International License.
Polycarbonate (PC) 3D Printing: Temperature, Speed, 3D Printer Settings
Polycarbonate is a durable but difficult material to 3D print due to its unique properties.
Polycarbonate (PC ) belongs to a group of plastics known for their strength, toughness and heat resistance. Sold for many years under the brand name "Lexan", the PC is used in many applications including engineering parts, DVDs and "bulletproof glass", it is also optically transparent.
Polycarbonate 3D Printing Issues
Beware Polycarbonate has certain properties that make it difficult to use as a 3D printing material.
- Polycarbonate requires high temperatures for proper extrusion otherwise the filament will get stuck in the extruder
- Polycarbonate is prone to shrinkage and thermal distortion
- Polycarbonate is hygroscopic, absorbs moisture
Benefits of 3D printing with polycarbonate
Polycarbonate is more durable and flexible than PLA and ABS for example, but less so than nylon. It is harder than ABS, PLA or PMMA, but lighter and less dense than ABS. Its ability to withstand torsional loads is superior to other thermoplastics and it is flexible enough to be bent at room temperature.
Thus, polycarbonate is a combination of these properties:
- heat resistance up to 135 ° C (for reference, PLA can begin to deform at 60 ° C)
- impact resistant
- moderately flexible
- transparent
- dielectric
Polycarbonate 3D Printing Guidelines
Ambient Temperature
Polycarbonate 3D printing can be challenging when you're just getting started. The material is prone to strong shrinkage, so it is necessary to maintain a constant ambient temperature. The 3D printer table should ideally be between 135 and 150°C and treated with adhesives.
Sometimes the layers may not stick, separate or crack as the material cools and deforms. This can be avoided by maintaining the ambient temperature in the 3D printer's thermal chamber, which will provide a more stable ambient temperature and allow the layers to bond properly, while also protecting against drafts and other unwanted effects. The thermal chamber allows you to make forced ventilation to remove toxic emissions.
This material requires a 3D printer with a thermal camera, otherwise there is a great risk of the first layer of the model peeling off the 3D printer table.
Extruder temperature
Polycarbonate requires an all-metal hot end, which will ideally be between 290 and 300°C. If you work slowly or use composite filaments, you may be able to get by with lower temperatures. However, using a composite, you will not be able to get all the unique properties of the material.
Humidity
Remember that polycarbonate is good at absorbing moisture from the air, so keep it dry when not in use (in a sealed container) and buy quality filament to avoid blemishes and failed prints. Moisture will not only affect the integrity of the print, but also make it optically opaque.
Polycarbonate is similar to PLA in this respect. The moisture it contains evaporates during printing, creating bubbles in prints that make them less durable and hazy.
Polycarbonate 3D Print Settings
- Nozzle Temperature: 250-310°C (varies)
- Bed temperature: 80-150°C (varies)
- Fan speed: 0%
- Print speed: 20-60 mm/s, selected empirically in increments of 5 mm/s
- Retraction distance: <10 mm
- Adhesives: glue, hairspray, kapton tape, etc.
- Thermal chamber: recommended
- Honend: solid metal
- Shrinkage: high
- Vapors and odors during printing: strong
Polycarbonate's resistance to heat requires equally extreme temperatures. An all-metal hot end and a heated bed are a must, and it is highly recommended to 3D print with a thermal camera. You should also turn off the cooling of the part to ensure good interlayer adhesion. Keep in mind that this material is designed for functional models, not artistic ones, polycarbonate does not have a good surface quality.
Set retraction distances of 10 mm or less to prevent jamming during printing.
When 3D printed, polycarbonate emits strong fumes and odors. Always print with this material in a well ventilated area, ideally an enclosed 3D printer with a thermal chamber and forced ventilation.
Storage of polycarbonate filament
Polycarbonate is extremely hygroscopic, absorbing moisture quickly from the air. Without proper packaging, plastic will lose its properties and it will be almost impossible to get good prints from such plastic. Sealed silica gel containers are the best solution to this problem.
Drying polycarbonate
If the polycarbonate filament has already absorbed moisture, printing performance will be severely reduced. The symptoms may vary, but the material is likely to be brittle, crack when printed, and the model will have imperfections on the surface.
In this case, you will need to dry the thread. This can be done in an oven, food dehydrator, or commercial thread dryer.
Polycarbonate Applications
Polycarbonate is commonly used in many consumer products. Due to its strength and transparency, even recycled polycarbonate can be used to create fully functional prototypes and art models.
In addition, due to its transparency, polycarbonate can be used to prototype transparent models, which would cost much more if they were made from other materials. High temperature resistance means it can also be used for functional prototypes where even ABS will deform when heated or stressed.
Carbon Fiber 3D printing plastic review
Good day. When testing the Wanhao Duplicator 6, we used many exotic plastics. We were especially interested in the nylon-based carbon plastic. We decided to talk about it in more detail.
Now there are many different types of plastics with the addition of carbon, but they all differ in their characteristics.
We used Fiber Force carbon for printing. Carbon Fiber uses nylon as a base.
- Fiber Force was founded in 2013 in Italy. In addition to ABS and PLA, Fiber Force produces several types of specialty plastics. One of them is CARBON FIBER.
The first thing that surprised me was the color — the rod is black, matte.
Looking ahead, I will say that due to the dullness of the rod, the finished “prints” look almost like cast ones.
The bar is slightly rough to the touch. In terms of rigidity, it is very similar to regular ABS, but I didn’t manage to break off a piece with my hands.
After a dozen bends in different directions, the place of the fold was, of course, crumpled, but did not break off. In principle, this is not surprising. No wonder the manufacturer indicates nylon as the basis.
Be sure to check the diameter of the bar. Everything is within the limits declared by the manufacturer of 0.05 mm.
Recommended print settings from the manufacturer - nozzle 240 degrees, table 20 degrees or no heat at all. Although it turned out that the sintering of the layers is very good in the range from 230 to 260 degrees. Of course, as the temperature rises, the material becomes very fluid and overhanging elements begin to sag.
Printed parts are slightly softer than ABS, but much more flexible.
Very little shrinkage. The manufacturer claims only 2%. Cube 25x25mm.
The most interesting feature is the resistance to fire. The material melts, of course, but does not flow and does not light up.
The hardness is somewhere between ABS and PLA. We printed hooks with 100% filling and hung a package with a load on them.
Kilogram spools with plastic were used as weights. One coil weighs an average of 1400 grams.
The weight of one spool all hooks withstood well.
On 2 coils ABS dropped out. PLA and Carbon hold up. But it is clear that Carbon, if tougher than ABS, is not at all much.
On 3 spools Carbon failed. The hook did not break, but straightened out.
The material turned out to be very interesting in terms of its properties. Trouble-free in printing, it will undoubtedly be useful for the manufacture of functional prototypes for which tensile strength, flexibility and wear resistance are important.
For example, while preparing an article, a trifle bushing broke in the car of our employee. The part was quickly modeled and printed from several materials. It was the carbon bushing that showed its best side.
Or let's say Mag Pull was printed for G3 magazines.