3D printed motherboard tray
▷ atx motherboard tray 3d models 【 STLFinder 】
Atx Motherboard tray
grabcad
This is a Motherboard tray for ATX motherboards. All the measurements taken from the ATX v2.2 specs. ...If you find any errors, please let me know.
Micro ATX Motherboard Tray Remixed
thingiverse
Just remixed the mATX Motherboard Tray from skywurz https://www.thingiverse.com/thing:158233 to have the correct dimensions. ...His file was only ~9mm wide in Cura.
Micro ATX Motherboard Tray
thingiverse
I printed this on my MM2 with full support
Micro ATX Motherboard Tray (for small printers)
thingiverse
I noticed that thingiverse did not have any micro atx mobo tray that could be printed on a smaller printer. This will print on an Ender 3! it takes nearly 9 hours to print. The tray itself is 4mm thick to ensure a strong part. Refer to the render I...
ATX, Mini-ATX, µATX and ITX/Mini-ITX Motherboard Tray Version 12.26.2021 - 3D Printable and CNC Machinable
thingiverse
ATX, Mini-ATX, µATX and ITX/Mini-ITX Motherboard Tray - 3D Printable and CNC Machinable. Intended to be the basis of something bigger and better. Developed by "The R.A.T." Customizations MAY be available upon request. This work is licensed under a...
ATX Motherboard
grabcad
Computer motherboard ATX size
motherboard atx
thingiverse
motherboard model atx
ATX motherboard dimensions
grabcad
ATX motherboard dimensions (cm)
ATX Motherboard Hole Template
thingiverse
A mounting hole template for a standard ATX motherboard 12"x9. 6".
Model - ATX Motherboard
thingiverse
Model - ATX Motherboard (Dimension & Holes) Dimension - 12" x 9.6" For Modeling purposes, not for printing!
Intel Mini ATX Motherboard
grabcad
Intel Mini ATX Motherboard. 170mm x 170mm. 85% populated against original design. Used for a client we were desiging a secure server housing. ...Image rendered using PV360
Atx motherboard specification
grabcad
Atx motherboard with exact geometry. Includes IO panel cut out / PCI and GPU cut outs and fixationsMotherboard PCB Geometry based on following specification : http://www.formfactors.org/developer%5Cspecs%5Catx2_2.PDF
ATX/mATX motherboard standoffs
thingiverse
simple standoff of any motheboard size - ATX, mATX, etc. ...just to lift the motherboard from the ground and avoid any shortage :) used with #6-32 UNC screws (typical larger PC screws) modeled into standoff. ...
ATX Motherboard Standoff
thingiverse
Just a simple ATX motherboard standoff. It raises motherboard about 2.3cm.
Print it with the infill at 25%, and at the top section make it 100%. I recommend using Brim.
...
If you have any suggestions please write them in the comments.
ATX Motherboard Plate
thingiverse
My full size ATX motherboard mounting plate. It strictly follows official ATX specifications and fits nicely with my I/O shield. My preferred version houses 5mm brass bolts that accept screws rather than the version that takes standoffs. The...
ATX Motherboard Mount Backplate
thingiverse
I needed an ATX motherboard mount for a 2020 aluminum extrusion open-air build Printed in PETG on an Ender XL 400 (400x400x500 build plate) The print area is 248mm x 302 so you'll need a larger sized bed Mounting holes are for M4*8 Hex Socket cap. ..
Motherboard ATX 1.0
thingiverse
Motherboard mATX 1.0
Micro ATX Motherboard Template
grabcad
Based on a design by case.io, but the Micro ATX file was missing. ... Quick and dirty edit from the full ATX version.
Asus P6T SE MotherBoard. ATX
grabcad
Motherboard ATX
Motherboard Tray
grabcad
Accurate hole placement to standard will fit ATX spec. ...Please ask my permission to use :).
Screwdriver for ATX Motherboard standoffs
thingiverse
A teeny tiny screwdriver for teeny tiny ATX motherboard standoffs. ...M3 x 0.5mm
ATX-ITX Motherboard foot Print
grabcad
Accurate representation of ATX and ITX motherboard footprints. All of our custom PC cases use this extremely meticulous ITX- ATX template. ...CaseMaker cases:Model 16: CaseMaker Model 16Model 86: Casemaker Model 86Model 87: Casemaker Model 87Enjoy!
PCIe Bracket for ATX Motherboard
thingiverse
This was created to support a PCIe x4 splitter for an ATX motherboard with seven slots. I've also included a four slot bracket. ... These work well with https://www.thingiverse.com/thing:4789196 due to the 4mm thickness of the bracket.
HP Z600 motherboard ATX build
thingiverse
This post contains 3d design for lga1366 adapter bracket., io back plate and atx psu adapter connection diagram. 1. Z600 Memory connector. This motherboard requires power supply for memory module. This connector can be made from molex connector...
Basic Motherboard Stand - ATX Compatible
thingiverse
... at once, but it may be easier to fit them 1 at a time at an angle depending on you print bed size.
Print the "Complete" version OR: - 2 Longs & 1 Short The holes are not threaded but are made small enough to "thread" normal motherboard screws into.
Micro ATX Motherboard Standoff Plate
thingiverse
The hole alight perfectly with the motherboard. YouTube Channel https://www.youtube.com/channel/UCZ8WG-kqF1kmL2s0xIMfIIg If you found this video helpful or would like help fund future experiments.please donate below. ... Patreon ...
Motherboard tray components
grabcad
.stl files of my motherboard tray components.
Stand for ATX motherboard to assemble
prusaprinters
Stand for ATX motherboard to assemble with 4 M3 screws and nuts. The model has been cut to be printable on MK2 and MK3.Then the stand can be fixed with wood screws to a board. ...Be careful, the screws must not touch the motherboard. 4x M3x10 or...
NES PC Motherboard Tray
thingiverse
This is a motherboard tray I made to fit in an NES so that a mini itx board could fit inside. I also allowed for there to be spacing around the already existing vents so that Airflow would not be as Impeded. ... ...
Mini-ITX Motherboard Tray
thingiverse
I glued it on the motherboard tray with super glue, but I'm sure there's better ways of doing it. .. .https://www.mcmaster.com/#93365a130/=166kvd3 Print Settings Printer Brand: MakerBot ...
3D Printed SFF PC case that fits MATX Motherboard and ATX PSU : sffpc
Link to Grabcad: https://grabcad.com/library/sub-20l-matx-case-1
https://imgur.com/71krPNw
Hello everyone!
A couple months back I got interested in SFF PCs; However, I only have standard size components. After some research, the only SFF PC case I could find in the US (At the time) that fit my components was the Cerberus, which was out of my budget. I decided as a fun project that I would design and 3D print a pc case for myself and anyone else who wants to build a SFF PC but is limited by their large parts. The goals I set were as followed
The case is under 20L
It can fit MATX motherboard and a ATX PSU
It can fit a reasonably powerful GPU
It is cheap to reproduce (Granted you have a 3D Printer)
Bear In mind this is a first draft and I may update it at a later time. The Printer I used was an Ender 3 Pro.
The end result was a PC case that could fit all the previously mentioned components. It is 18L that fits a 2 slot GPU of max length 280mm, and a tower cooler of max height of roughly 145-150mm. It has room for 2 120mm fans and 1 92 mm fan. The components used were as followed:
2 spools of TECBEARS PETG 3D Printer Filament (20 dollars each)
https://www.amazon.com/dp/B0817ZWLJ4?psc=1&ref=ppx_yo2_dt_b_product_details
Various assembly screws (Including some I Found around the house)
https://www.amazon.com/dp/B0831CP2C4?psc=1&ref=ppx_yo2_dt_b_product_details (8 dollars)
https://www.amazon.com/dp/B08Z75M47H?psc=1&ref=ppx_yo2_dt_b_product_details
(17 dollars)
A Power button
https://www.amazon.com/dp/B07PPDHKDT?psc=1&ref=ppx_yo2_dt_b_product_details
(10 dollars)
In total, this case cost me around 75 dollars.
This is my first case I’ve designed but I want to share the files with you so others who are stuck with regular size PC parts can go SFF.
However, before you print this, I highly recommend purchasing the SAMA IMO1. It is extremely similar to my case; however, it is slightly bigger but can fit a much bigger GPU and has some built in IO. It just recently came back in stock.
newegg.com/p/N82E16811197012?Description=SAMA%20IM01&cm_re=SAMA_IM01-_-11-197-012-_-Product&quicklink=true
Notes when assembling this case:
The tools I used were an allen wrench and pliers. The pliers hold the nut in place while the allen wrench tightens it. I recommend assembling the front and back panels together first, as It will be harder to reach those bolts later on. The GPU Must be inserted into the motherboard when the motherboard is installed. Then Put in the Rear ATX plate and Rear IO plate in that order. The last couple screws cannot be tightened due to the fact you are closing a box and no longer have access to the nut. For these last ½ dozen holes, just get a slightly bigger screw that will bite into the plastic to hold it in. To make the handle foldable like mine, buy something called an eye screw. Thread a bolt through the handle and eye screw to make it hinge on the eye screw.
This was a Fun project and I hope you guys can make use of it or improve it! Take care.
Printed circuit boards using a photopolymer 3D printer / Sudo Null IT News And in the last year or two, thanks to a strong reduction in cost, their photopolymer subspecies is also flourishing. Now such a printer is already available to almost everyone, and the number of their models on the market is multiplying every month.
Even when I just learned about the appearance of a new type of photopolymer printers a few years ago - in which the image of the layer for illumination is formed by an LCD, the thought flashed through me already then: "Hmm, what if we substitute a photoresist on a textolite?". But then it was a purely theoretical question - the prices for them were considerable, and the resolution and display area left much to be desired. However, today these printers can already boast of a decent resolution - from 30 microns per pixel, and a completely normal display area.
And as it turned out, with the help of an inexpensive modern photopolymer printer, it is quite possible to make boards with tracks / gaps from 0.15 mm.
I apologize in advance for such a voluminous graphomaniac, I myself did not expect that the note would get so fat...
I foresee the question "But why? In China, they will make normal boards with a mask and silk-screen printing for a penny!" I answer: now, most likely, there will be several iterations of finishing the board to a satisfactory state. I made a board - tested it - made corrections. And so several times. Waiting every time for 2-3 weeks from China is not an option :) But when the final design of the board is determined - then, of course, normal production in China or on Rezonit.
Now let's get down to business.
Who does not know - here is a brief principle of operation of such a printer The main part of such a printer is an LCD display. Below this display is a 405 nm UV source. Above the display is a bath of photopolymer, which has a thin transparent FEP film as a bottom. A platform is lowered into the bath, on which the model is “grown”. At the beginning of printing, the platform lowers to the height of one layer from the film, the image of the first layer is displayed on the display, and UV illumination is turned on for a specified time. Illumination, getting through the "open" pixels of the display and the film onto the photopolymer, hardens it, so a hardened layer is obtained. The first layer sticks to the platform. Then the illumination is turned off, the platform rises to the height of the next layer, the image of this layer is displayed on the display, and the illumination is turned on. The second layer is cured by welding with the previous layer. And this is repeated over and over until the entire model is printed.
The idea to try to make a printed circuit board using such a printer came to me again about three years ago, when I bought myself an Anycubic Photon S printer. , then I just forgot about this idea, because and there was no need to make boards. But the other day, the need arose for the manufacture of several small boards, and with a high probability that as tests are made, changes will be made to these boards and it will be necessary to go through several iterations of "manufactured-checked-changed" in a short time. And the idea resurfaced.
To be honest, I thought that by now the Internet would be filled with the results of such experiments, the idea lies on the surface :) But to my surprise I found that the Internet is almost completely silent on this issue. There are separate notes, but there is no integrity and completeness in them. That's why I decided to publish this post - maybe it will help someone go all the way faster than me, and with less rakes :)
Well, the most important thing is that you don't need film and you don't have to struggle with increasing the contrast of the template. You also do not need a separate UV source with a place for its installation. And, of course, it is stylish, fashionable, youthful.
There are also disadvantages - the resolution of most modern 3D printers still does not cause much enthusiasm yet - the pixel size of all fluctuates around 0.05 mm. But this is already enough for confident manufacturing of boards with tracks from 0.2 mm and rather high chances of success with tracks from 0.15 mm. Due to the raster nature of such a template output, the position and size of elements on it can vary + -1 pixel, so I think it’s not even worth counting on tracks of 0.1 mm or less.
Let's go in order.
Task
It is necessary to make a printed circuit board at home using photoresist. Instead of templates and illumination lamps, use a photopolymer 3D printer that will serve both at the same time.
Let's divide the problem into separate steps-solutions for each moment.
-
Board development
-
Outputting layers in a printer-friendly format
-
Preparation of textolite with photoresist
-
Printer flare
-
Photoresist development, board etching
1.
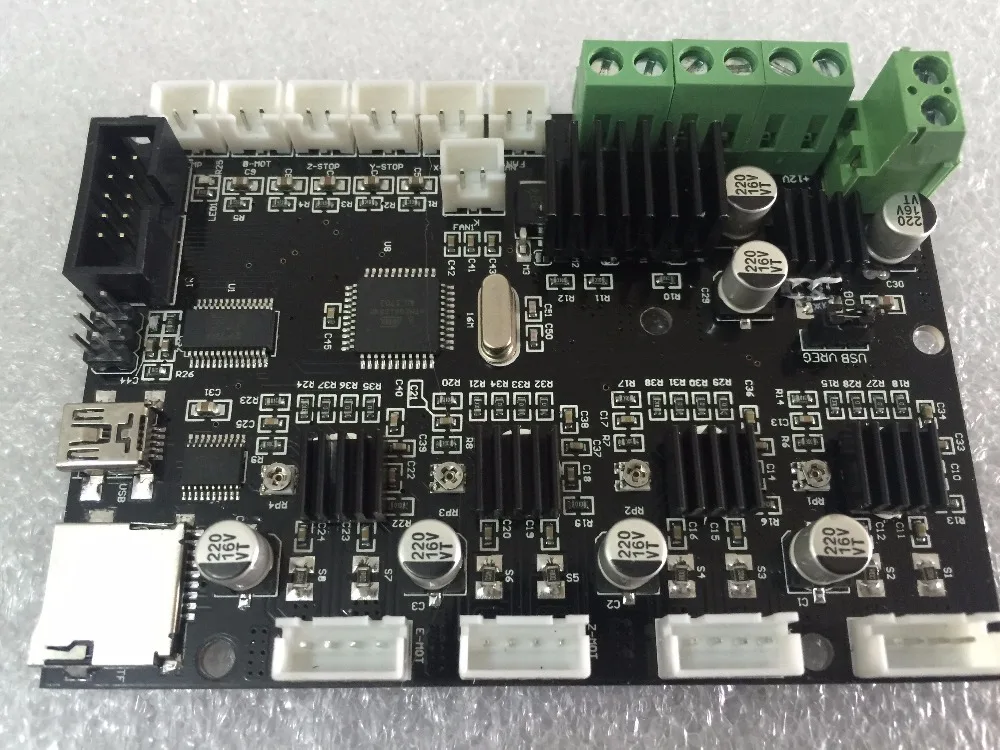
Well, there are no questions. Whoever prefers to work in what program - in that one makes boards. The main thing is that the program should be able to display the result in some commonly used form. The easiest way I've come up with is outputting board layers to gerber files that can be fed to an online service. But you can also output to PDF or images.
2. Converting the CAD output to a printer friendly
This is where the trouble begins. If almost all CADs can output to generally accepted formats - gerberas, DXF, printing to PDF, then 3D printer manufacturers so far categorically refuse to accept any file standard. Everyone is perverted as they can. The situation is largely saved by the fact that many manufacturers use motherboards from one Chinese company, Chitu Systems, in their printers. Thanks to this, many printers on such boards are able to understand one of the basic formats developed by the same company. And even often, if a file has some unique extension, then in fact it has the same basic format, just with a different extension. But it may differ in some details.
In any case, there is a free UVtools utility known among photopolymerists that can open files in one format and convert them to another format. It understands almost all formats on the market :)
I have tried two ways of preparing files with layers for the printer and I will describe both.
2.1 Gerber output and conversion to .photon
The .photon file format is understood by the old Anycubic printers - Photon and Photon S. This is exactly the case when the printer manufacturer took the format from Chitu and changed its extension. In the original, this is the Chituvian .cbddlp format, so you can safely change the extensions of these file types among themselves and the printers will devour them like native ones.
Since I have a printer that understands this format, this method suited me perfectly. The limitations of this method are that the printer must understand .photon or .cbddlp files and have a standard display for most non-monochrome printers with a resolution of 2560x1440 and a diagonal of 5. 5". manuals on how to do this for any CAD that can, in principle, mirror layers or not - it makes no difference, they can be mirrored in the utility during the conversion process.0003
Now open the online utility for converting gerber files - https://pcbprint.online/ and load the gerberas into it. By the way, this is a utility from a Russian developer who lives here.
It is easy to understand, although it does not contain any information or help. But here is a short guide:
For a single-sided boardUpload your gerbera in the main window with the "Upload file" button:
We made sure that everything is fine and the image meets expectations, if necessary, make a negative or mirror the image with the buttons in the top center, and press the button " Render layout":
Now press "Lauout" at the top right and get into another screen:
Here you first need to go to the settings (gear button at the top right) and there select the format of the output file "photon":
The time in "Exposition" can be left at default and change it to the desired one directly in the printer. But you can immediately put the right one if its value is already known :)
Close the settings and return to the previous screen. Here the output image is on a black space showing the working field of the printer. The image can be moved, aligned. When everything suits, we first press "Render", and when the "Download result" button next to it becomes active, we also press it. And save the proposed .photon file to a convenient location on your computer :)
For double-sided boards, things are a little more complicated due to the need to match them. Therefore, it is necessary to know very exactly the position of the image displayed on the printer's display in order to place the board on the display very accurately in accordance with it.
I had several options for solving this issue, but in the end I decided on the simplest of them, which did not require any mechanical conductors. To do this, I still in CAD in a separate layer (it is possible in the border layer or in any other "unnecessary" layer) I draw a frame around the board with a line of 0. 15 mm and indented from the edges of the board by 0.25 mm. As a result, I get three gerberas - the top layer, the bottom layer and a separate empty frame.
I upload all three gerberas to the above site and then in a few steps I get three files for the printer.
Double-sided board in pcbprint.online/So, all three gerberas have been loaded. All of them are mixed together, but it's not scary:
Now hide the top and bottom layers, leaving only the frame (by clicking on the eyes in the names of the gerberas).
Click "Render layout" and go to the "Layout" screen with the button in the upper right corner. We see an empty frame, drag it to the desired position on the black field of the display, click "Render" and "Download". The first file for the printer is ready.
Switch back to the gerber screen with the "PCB comose" button. Redisplay the first layer (the frame layer still remains visible), mirror if necessary, and click "Render layout" again. Again we go to the output screen and now there are two pictures hanging on the display field - a separate frame and the first layer with a frame. The frame remained in the same place where we pulled it last time. And now our task is to exactly combine the frame of the first layer and the empty frame:
Click "Increase" and combine in one of the corners. In this case, in no case should you move the empty frame that we set in the last step!
Combined, click "Render" and "Download", and we have a second file for the printer. Before returning to the gerbera screen, we delete the render layer with the frame, we should again have an empty frame. And now we return to the gerberas, hide the first layer and display the second one, look at the need to mirror, click "Render layout" and go to this screen again. In the same way, we combine the layer frame with an empty frame (which cannot be moved!), then "Render" and "Download".
Everything, all three necessary files for the printer are ready.
All this hemorrhoids allows you to generate for the printer files of an empty frame and layers with a frame in the same place on the printer display with high accuracy. The empty frame serves to aim the board, more on that below.
If necessary, the resulting .photon files can be converted to the desired format using UVtools :)
2.2 Output layers to PDF or images
The second method is perhaps more confusing, but its great advantage is versatility, it is suitable for any printers, whose formats are supported by UVtools. I will describe it only in general terms, because. There are quite a lot of tools and specific ways to implement it, and everyone can choose them according to their preferences.
So, the goal of the first step is to get a picture with a size equal to the resolution of the printer's display, preferably in a lossless compression format. In this case, the image of the layer in the picture must correspond to the real size in the scale of the display.
If CAD allows you to output directly to the picture - great, output to it. If the resolution of the output image is configurable - specify the resolution of the printer display. It is elementary to calculate it - we divide the number of pixels across the width of the display by the width of the working area in mm and multiply the result by 25.4, we get the resolution in pixels per inch. If the resolution is not set, then set the image size as large as possible so that there are at least 15-20 pixels per 1 mm of the board.
If output to image in CAD is not available, then output to PDF. This PDF will need to be opened in another program and converted to an image. Photoshop, Corel, maybe other programs can do this... The requirements for image resolution are the same. For example, in Photoshop, when importing a PDF, you can immediately specify with what resolution to convert to an image. For example, for common displays with a resolution of 2560x1440 and a diagonal of 5.5 "the resolution is approximately 537.566 PPI (pixel size - 0.04725 mm).
The resulting image will need to be changed in some image editor, bringing its size to the resolution of the printer's display. In this case, the layer image must be scaled to the real one (taking into account the pixel size of the printer display) or saved without scaling if the PPI of the display was specified when importing the image.
UPD: in the comments @0x3f00 gave a link to his converter of PNG images to files for the .photon printer - https://github.com/0x3f00/PhotonCpp/releases/tag/v1.0.0 . There is also an instruction for using it just for the purpose of manufacturing boards - https://github.com/borelg/PhotonPCB.
2.3 There is another way, but it is very resource-intensive
You can output layers to PDF, then open this PDF in Corel, convert it, save it in DXF, extract a three-dimensional object from this DXF, which you can push into the printer's slicer.
Necessary transformations in the vector editor:
-
Connect all curves.
-
Convert outlines to objects.
-
Merge intersecting objects.
You can extract a three-dimensional object from DXF, for example, SolidWorks. Fusion360 also seems to be able to. Who else is capable of this - I honestly don't know, but in theory any CAD that can import DXF as a sketch.
Thus, for example, I made a model for determining the exposure time of the photoresist.
3. Preparation of textolite with photoresist
The Internet is simply littered with articles on this topic, but for the sake of integrity and for the sake of some specific points, I will also describe such well-known stages as the preparation and etching of textolite.
My first experience with such a fabrication was a couple of days ago with a domestic photoresist PF-VShch. Taking into account the last yesterday's experience, I categorically advise not to waste time on this photoresist, but immediately take a decent one - Ordyl Alpha 350 (330) :) They say that Kolon is also decent, but I have not tried it. With Ordyl photoresist, the results are much more stable and accurate, it is easier to develop and adheres much better to the foil. And he can forgive those mistakes that will be critical for the PF-VSC. And what is important - it is sold in a bunch of places quite inexpensively.
3.1 Preparing the textolite
To begin with, the textolite should be smooth, very preferably with a smooth foil without scratches or dents. Otherwise, the chances of success are reduced.
If a double-sided board is being made, then you need to immediately cut the board out of the PCB exactly to size. If there is any CNC router, then you can drill all the holes and cut along the contour in one installation, as I do. If not, then it is better to leave the drilling for later, when the board is etched.
After this, the textolite blank must be very carefully cleaned and degreased. This can be done with a kitchen abrasive sponge (but not used for washing dishes on which fats have already accumulated) and a scouring powder like Pemolux. Very carefully, slowly three every square millimeter of foil, without touching it with your fingers. In general, I categorically do not advise touching the foil with your fingers after the start of cleaning, there should not be the slightest even the faintest greasy spot on it. After cleaning, rinse thoroughly in running water, shake off excess water and allow to dry. I do not advise blotting or wiping with anything, because. grease can be applied, even from a new napkin.
3.2 Application of photoresist
Also a fairly well-used topic on the Internet, so I'll go over it briefly.
Photoresist usually comes in sheets or rolls. It consists of three layers - two protective films and the photoresist itself between them. A piece is cut off from the photoresist according to the size of the board +5 mm in length and width, then a matte (polyethylene) protective film is removed from it.
the second, glossy (lavsan) must remain on it until the etching stage.
The easiest way to remove the film is with a piece of tape. It is glued with its edge to the corner of the photoresist and then folded back, pulling the protective film along with it.
After removing the matt film, the photoresist is applied to the edge of the board and smoothed along this edge with a finger. The rest of the photoresist is supported by weight, without tension, but in such a way that as little as possible of its area lies on the foil.
Please note that if the Ordyl photoresist falls on a well-prepared textolite, then it can firmly stick to it, and without bubbles it can no longer be rolled. You have to scrape it off and do it all over again. And PF-VShch can fall as much as you like - it definitely won't stick :)
Now the knurling itself. If you have a laminator, in which the textolite will crawl through the thickness, then it's just wonderful. We make an envelope-type strip of paper folded in half, put a textolite with a sticky edge of the photoresist in it, and serve this sandwich into a laminator heated to 100-110 degrees. At the same time, we continue to hold the photoresist so that it comes into contact with the textolite foil only directly at the inlet of the laminator.
That's all for Ordyl, for PF-VShch it will be harmless to roll a couple more times.
If there is no laminator, then smooth the photoresist to the textolite with your finger from edge to edge, gradually lowering it onto the textolite. The main thing is not to catch the bubbles. After the entire photoresist lay on the foil, we take a hair dryer and warm up the textolite to 70 degrees, after which we iron the entire photoresist once again.
After knurling, let the textolite with photoresist lie down for 15-20 minutes, or at least until they cool down to room temperature - according to the recommendation of the photoresist manufacturer.
And now everything is ready to highlight the layer pattern :)
4. Printer highlights
I want to warn you right away: looking directly into the glowing display of a photopolymer printer may not be very good for the eyes. Although not true UV (405 nm), the brightness is quite noticeable and can be harmful to the eyes. Therefore, I recommend using colored or tinted goggles. I think even sunscreen will do.
First, you need to remove the bath and platform from the printer, they are completely unnecessary for this business and even interfere. This completes the preparation of the printer :)
Lighting also has different options. If you have a one-sided board and the workpiece is larger than the size required for the board, then everything is simple - throw the file obtained at the preparation stage into the printer and, knowing the approximate place for displaying the image on the display, put a textolite with photoresist in this place. Then start printing the file and wait until it is completed. Everything, the photoresist is exposed, it is possible to develop.
If the workpiece is equal in size to the board being made and the error with the position of the workpiece on the display is unacceptable, then in this case it is necessary to remove the frame during preparation, as is the case for a double-sided board. Illumination also occurs using a frame, similar to a double-sided board, only without the second side and the second layer.
So, the illumination of the double-sided board. We throw all three files into the printer - with a frame, with the first layer and with the second layer. We put the workpiece next to the printer in quick accessibility. If it is already pre-drilled, it will be useful to make sure that it lies in the correct position so that you can quickly take it and immediately put it on the display. To do this, we run a file with a layer planned for exposure, and compare the layer pattern on the display and the orientation of the board next to the printer.
Printing a file with one frame. As soon as the frame lights up on the printer display, we take the workpiece and put it approximately inside the frame. While the frame is being illuminated, we align the workpiece so that it is exactly in the frame, with the same indentation of the frame from the edges of the workpiece on all sides.
In the photo, I gave an example with a ready-made board, because I did not take pictures during the manufacturing process. Well, reflections interfere quite strongly, alas... But I think it's understandable :)
That's it, the position of the workpiece is verified, printing of the frame file can be interrupted or wait for it to finish. Without moving the workpiece, run the file with the first layer and wait for it to finish. We illuminate the second layer (the second side) in the same way - we launch the frame, place and align the workpiece, without moving it, we launch the second layer. Before this, just in case, you can make sure that the workpiece will lie in the correct orientation, as before the first layer.
If the workpiece is not completely flat and does not fit the entire area of the display, then you can press it down from above with some heavy flat piece of iron. You just need to make sure that this piece of iron does not interfere with the platform lever, which will go down with the start of printing - the printer thinks that this is a normal photopolymer print and you need to lower the platform to the bottom of the bath :)
Illumination time can be different from printer to printer . It depends on the power of the emitter, and on the optical illumination system, and on what type of display is worth - monochrome or RGB. Here already it is necessary to select each individually. For orientation, I can say that I got the best result with the Ordyl photoresist at an exposure time of about 90-110 seconds. With photoresist PF-VShch - about 10-13 minutes. Printer with paraled, illumination power slightly less than 50 watts.
After exposure, the workpiece should be allowed to rest for 15 minutes - this is according to the recommendation of the photoresist manufacturer. Ordyl changes the color of the highlights quite noticeably, so it's pretty easy to control the highlights. Unfortunately, the photo did not convey it well, it can be seen better with the eyes.
5. Development, etching
Everything here is according to the recommendation of the photoresist manufacturer and according to the classics of the Internet.
All necessary chemicals were purchased inexpensively from Auchan. Even hydrogen peroxide 6% - this was a surprise for me, I had never seen it in hypermarkets before, and even in liter bottles.
For one session you need:
-
Soda ash - 1.5 grams
-
Hydrogen peroxide - 150 ml for 3% (or 75 ml for 6% + 75 ml of water)
- citric acid
-
Salt - 7.5 grams
-
Alkali (caustic soda, sodium hydroxide) 5-7% - 100 ml
With the cheapness and ease of buying all the components around the corner, I am in favor of preparing a new solution for each board. Although the etching solution, as they say, is not stored anyway. A solution of soda ash noticeably "poorer" in the process of development. Unless caustic soda can be reused, but is it worth it to keep another bottle ...
Both Ordyl and PF-VSH appear in a weak solution of soda ash. For PF-VShch - 1-2%, for Ordyl - 0.8-1.2%. For Ordyl, we take 150 ml of water and dilute 1.5 grams of soda in it. The solution can be heated up to 30 degrees, this will speed up the development, but it is important not to overdo it, otherwise the illuminated areas may begin to be damaged.
Ordyl appears rather quickly. Already after 10-15 seconds, the illuminated pattern begins to become more and more contrasty, the unexposed areas gradually dissolve, become thinner and become paler.
To speed up the process, it is recommended to shake the bath so that the reaction products are washed off the surface of the workpiece. For this I adapted my old 3D printer, its table and shook and heated the bath with the solution during development and etching :) Two minutes passed before there were at least some signs that development had begun. In addition, if Ordyl does dissolve, then PF-VShch first swelled like gelatin and discolored, and only then began to slowly dissolve.
At the end of development, you can go over the boards with a hard paintbrush (or soft toothbrush) several times in different directions to help flush out any remaining photoresist from tight spots. Ordyl holds on tight, this procedure should not disrupt it, but with PF-VShch you need to be very gentle, even without a brush it strives to exfoliate on thin paths.
After etching, the workpiece must be rinsed in cold water so that the soda residues do not continue to attack the photoresist and so as not to clog the etching solution with them.
The result should be something like this, maybe even better :)
More detailsScale of the grid square - 0.2 mm:
The scale is the same. Here you can see the raster component of the illumination, the pixels stick out:
Etching was also done according to the traditional recipe, popular on the net:
It is better to heat the solution to 40-50 degrees, then the etching goes much faster. This is my first experience with this solution. I used to poison with ammonium perchlorate, and even earlier - with classic ferric chloride. To be honest, I can't really express how I feel about this solution. On the one hand, it poisons rather quickly, is transparent, does not get dirty, and is relatively safe. On the other hand, it seemed to me that it was easing quite a lot ... But maybe it just seemed, I haven’t been making boards for 10 years and I forgot how it all worked when the trees were big :)
After etching, the exposed photoresist must be removed from the workpiece, and this is done in caustic soda.
On my bottle of cleaner it says "at least 5% but not more than 15%" and it takes 5-8% to remove the photoresist. I diluted the product 1:1 with water and this solution did the job perfectly. The photoresist does not dissolve in it, it simply peels off the foil after 2-3 minutes and begins to float in tatters in the solution.
After that, the board is thoroughly rinsed under the tap and... The board is ready!
Summary of my experience
Overall I am satisfied. I did not expect to get tracks / gaps of 0.1 mm and I did not get them. Here, the capabilities of the printer are severely limited (pixel size), and in general, good experience is needed for such results. But I was hoping to get at least 0.2 mm, and if I'm lucky, then 0.15 mm - and I got it. 0.2 mm confidently, 0.15 mm - well, so-so... If you try, you can achieve :)
There were some flaws - it was not pickled in some areas, and imperfect alignment of layers and holes. But neither is critical. As for the non-mordant - I think that I just hurried to take it out of the developer, I was afraid after PF-VShch that thin paths would begin to peel off.
Although in the reviews people write that it is quite difficult to re-develop this Ordyl, you need to try for this. Imperfect alignment of layers and holes is to be expected. From such a simple method of alignment, I expected an error of 0.1-0.2 mm, which I got, but it suits me.
Thank you for reading.
And finally, a few photos of my results. Exposure time test, from 1 to 2 minutes. You can see the pads displaced relative to the holes. printer?・CultsThe plate is one of the most important parts of a 3D printer. For optimal printer performance, it must be properly cleaned after each print session. Traces of the thread are deposited on it over time. While cleaning a 3D printer plate is not a difficult task, it can quickly become one if you don't have an effective method or the right cleaner. How to clean this important part of the 3D printer? We invite you to identify the most effective methods.
Do you have a 3D printer? So how do I properly maintain my 3D printer is probably a question you often ask yourself, the first element of which lies, in fact, in the quality of the material you are using.
As far as the print plate is concerned, when using the correct cleaning tools, the various parts of your 3D printer will have good adhesion of .
To clean the plate of your 3D printer, you will need the following tools: sandpaper, scraper, sponge, paper, cotton or microfiber towels and cleaners such as acetone or propanone, isopropyl alcohol (IPA) with a minimum concentration of 70%, soap for dishes... Ideal for effective cleaning of your 3D printer .
Cleaning your 3D printer's plate depends mainly on the plate material, as well as the product used for printing. Most often the plate is made of glass, polyesterimide (EPI) or is covered with adhesive tape . The printing plate of the printer can also be made of plastic, garolite, ceramics, granite, aluminum, but this is much less common. When cleaning the 3D printer plate, you must also consider the use of surface treatments that promote adhesion of parts to the plate.
Cleaning the glass 3D printing plate
Glass is a common material used for 3D printing. It has a much longer lifespan than PEI. In addition, the glass plate makes it easier to use the adhesive and varnish in the 3D printing process. This is because its surface does not react with any material. It is also relatively easy to clean. The 3D printer's glass printing plate is commonly used with adhesives such as glue stick and hair sprays. They increase the adhesion of the surface for the first print layer, which is necessary to ensure the stability of the rest of the model.
The glass plate can be heated to remove material residue. Heat makes it easier to scrape off these materials. However, care must be taken when scraping, as the glass is easily scratched by sharp objects. It is best to use aligned items such as a metal spatula or plastic ruler. If you choose to use metal, we recommend applying only as much pressure as is necessary to avoid scratching the glass plate.
A metal scraper or spatula is also very useful for cleaning the print tray if you are using ABS, PLA, or nylon filament.
Alternatively, you can use the scraper blade to clean the glass plate of your 3D printer. This tool is very sharp. To do this, press down with one hand while holding the edge of the print tray with the other. This will allow you to effectively remove the remaining material from the 3D printer's print tray. Then make sure you clean the part of the plate that is in contact with your hands. It very often leaves residues of oil and dirt.
Plate cleaning PEI
PEI sheets are also used as printing plates for 3D printers. Their resistance to wear under extreme temperatures and radiation levels is well rated. Regular maintenance of the PEI printing plate allows the to maintain its quality. Over time, the adhesion of PEI sheets weakens under the influence of temperature, printing radiation or inks. Traces of dirt, oil, glue, etc.
eventually settle on the surface of your 3D printer's PEI plate. However, physical cleaning procedures such as scraping and scraping are not the most effective and may even damage the print plate.
The best solution for cleaning the EPI print tray is to use a cleaner such as 70% strength unflavored IPA . In the case of a plate surface that is more exposed to dirt and oil, purer IPA can be used. However, before you start cleaning, wait for your 3D printer's PEI plate to cool down. For your protection, make sure you use this cleaner in a well ventilated area.
You can also use acetone to remove ink and plastic residue stuck to your 3D printer's PEI plate. This cleaner should not be poured directly onto the plate. Although PEI does not dissolve in acetone, acetone can damage PEI if you pour a large amount of it onto a plate. To do this, it is recommended to pour acetone on the fabric, and then wipe the print tray in a circular motion.