3D printers demonstration
3D printing gets bigger, faster and stronger
As a metal platform rises from a vat of liquid resin, it pulls an intricate white shape from the liquid — like a waxy creature emerging from a lagoon. This machine is the world’s fastest resin-based 3D printer and it can create a plastic structure as large as a person in a few hours, says Chad Mirkin, a chemist at Northwestern University in Evanston, Illinois. The machine, which Mirkin and his colleagues reported last October1, is one of a slew of research advances in 3D printing that are broadening the prospects of a technology once viewed as useful mainly for making small, low-quality prototype parts. Not only is 3D printing becoming faster and producing larger products, but scientists are coming up with innovative ways to print and are creating stronger materials, sometimes mixing multiple materials in the same product.
Sportswear firms, aviation and aerospace manufacturers and medical-device companies are eager to take advantage. “You’re not going to be sitting in your home, printing out exactly what you want to repair your car any time soon, but major manufacturing companies are really adopting this technology,” says Jennifer Lewis, a materials scientist at Harvard University in Cambridge, Massachusetts.
The latest techniques could be lucrative for researchers, many of whom — Lewis and Mirkin among them — are already commercializing their work. They’re also fundamentally exciting, says Iain Todd, a metallurgist at the University of Sheffield, UK. “We can get performance out of these materials that we didn’t think we could get. That’s what’s really exciting to a materials scientist. This is getting people used to the new weird.”
From trinkets to productsThe 3D printing technique is also referred to as ‘additive manufacturing’, because instead of chopping or milling a shape out of a larger block, or casting molten material in a mould, it involves building objects from the bottom up. Its advantages include less waste and an ability to print custom designs, such as intricate lattice structures, that are otherwise hard to create. Low-cost hobbyist machines print by squeezing out thin plastic filaments from heated nozzles, building up a structure layer by layer — a method known as fused deposition modelling (FDM). But the term 3D printing encompasses a much wider range of techniques. One of the oldest uses an ultraviolet laser to scan across and solidify (or ‘cure’) light-sensitive resin, layer by layer. That concept was described as far back as 1984, in a patent filed by Charles Hull2, the founder of a company called 3D Systems in Rock Hill, South Carolina.
The latest techniques — including Mirkin’s — still use light-sensitive resin, but are faster and larger-scale, following improvements reported in 2015 by a team led by Joseph DeSimone, a chemist and materials scientist at the University of North Carolina at Chapel Hill3. Early printers were slow, small-scale and prone to producing layered, imperfect and weak structures. These found a niche in rapid prototyping, making plastic model parts as mock-ups for later production by conventional methods. As an area of research, this kind of printing wasn’t thrilling, says Timothy Scott, a polymer scientist at Monash University in Melbourne, Australia: “Basically making trinkets and knick-knacks. For a polymer chemist, it was pretty dull.”
In 2015, Joseph DeSimone at the University of North Carolina at Chapel Hill unveiled a technique to speed up 3D printing.Credit: Carbon 3D Inc.
Then DeSimone unveiled a way to print light-sensitive resin up to 100 times faster than conventional printers3. It uses a stage submerged in a vat of resin. A digital projector shines a pre-programmed image up at the stage through a transparent window in the floor of the vat. The light cures an entire resin layer at once. DeSimone’s advance was to make the window permeable to oxygen. This kills the curing reaction and creates a thin buffer layer, or ‘dead zone’, just above the window’s surface so that the resin doesn’t stick to the bottom of the vat each time a layer is printed. The stage rises continually, pulling the completed part up through the liquid as new layers are added at the bottom.
Other labs were working on similar concepts at the time, says Lewis. But perhaps most impressive about DeSimone’s resins was that they could undergo a second reaction in a post-print heat treatment to strengthen the finished product. “It opens up a much broader array of materials,” says Lewis.
Forget everything you know about 3D printing — the ‘replicator’ is here
Many research groups and firms have since built on the work. Mirkin’s printer pumps a layer of clear oil across the bottom of the vat to inhibit the polymer’s reactions. This also acts as a coolant, removing heat that can deform a printed part — and it means that the equipment is not limited to printing with resins that are inhibited by oxygen. He says the printer produces material ten times faster than DeSimone’s. And last January, Scott and his colleague Mark Burns at the University of Michigan in Ann Arbor reported a printer that inhibits the reactions by mixing into the resin a chemical that can be activated by a second lamp emitting a different wavelength of light4. By varying the ratio of the strength of the two light sources, the researchers can control the thickness of the photo-inhibited zone, allowing the creation of more complicated patterns, such as surfaces embossed with seals or logos.
Inventions in 3D printing often have rapid commercial potential: some researchers start forming companies before they publish their advances. On the same day DeSimone’s paper was published, for instance, he showcased it at a TED talk in Vancouver, Canada, and officially launched his start-up firm Carbon 3D in Redwood City, California, although he had quietly registered the company two years earlier. The firm is now one of the biggest start-ups in 3D printing; it has already raised US$680 million in publicly disclosed funding rounds, and is reportedly valued at $2.4 billion. It has high-profile contracts with Adidas to make rubber-like midsoles for athletic shoes, and with sports-gear firm Riddell to manufacture customized helmet padding for American-football players.
Carbon 3D’s technology is used to print Adidas shoes (left) and padding for American football helmets (right).Credit: Carbon 3D Inc.
Mirkin and his colleagues James Hedrick and David Walker have also launched a start-up, Azul 3D in Evanston, Illinois, to commercialize their technique, which they have dubbed HARP (high-area rapid printing). And Scott and Burns are preparing a commercial prototype printer with their Ann Arbor-based start-up Diplodocal, a name derived from the Greek for ‘double beam’.
New resin-printing techniques are still emerging. One begins with a small spinning glass holding liquid resin. As the glass rotates, a projector shines a loop of video onto it that corresponds to 2D slices of the desired object. Within seconds, the final object solidifies inside the liquid resin — no layers necessary5. The method is inspired by X-rays and computed-tomography scans, which image a cross-section of a solid object. This is the inverse: back-projecting cross-sections to form a 3D object.
A projector shines a video loop onto liquid resin, causing an entire object to be created at once, rather than layer by layer.Credit: UC Berkeley
Even in this fast-moving field, the technique turned heads for what Lewis calls “the gee-whiz factor”. It has significant limitations: the resin used must be transparent, and the printed object must be small enough for light to pass through it to cure it. But it also has a potential advantage: it can handle highly viscous resins, which other resin-based printers struggle to suck through the narrow dead zone. That means it could make stronger materials and more accurate prints.
The approach has garnered substantial interest from industry, says Christopher Spadaccini, a materials and manufacturing engineer at Lawrence Livermore National Laboratory (LLNL) in California. Spadaccini was a member of the team that published the work last January5. A group at the Swiss Federal Institute of Technology in Lausanne (EPFL) independently developed the same concept, and has also reported a demonstration of it6. Spadaccini thinks the technology has tremendous commercial potential because it has modest hardware requirements. “In the end, really, what you need is a halfway-decent projector and a rotating stage,” he says.
While chemists work on smarter ways to 3D-print intricate resins, engineers are pushing boundaries in 3D printing of concrete — using computers and robots to precisely automate the pouring process.
A 3D-printed concrete pedestrian bridge developed by Tsinghua University.Credit: Imaginechina/Shutterstock
The world’s first 3D-printed concrete pedestrian bridge was made by researchers at the Institute for Advanced Architecture of Catalonia in Barcelona, Spain, and installed in a park in Alcobendas, near Madrid, in 2016. Twelve metres long, the bridge features a lattice structure designed with algorithms that maximize strength and reduce the amount of material needed. Other teams have made similar structures, including a 26-metre-long bridge in Shanghai, China, produced by engineers at Tsinghua University in Beijing. And teams and companies in China and the Netherlands have 3D printed demonstration houses.
Those structures aren’t constructed in one print job, however: separate segments are printed and then connected. By producing bridges and houses more cheaply and efficiently, 3D printing could reduce concrete’s carbon footprint — but it could also just encourage engineers to build more.
It’s not just concrete that is going big: Amsterdam firm MX3D has printed a bridge from stainless steel. First displayed publicly in 2018, the bridge is now being tested and having sensors installed ahead of a planned installation over an Amsterdam canal.
A view of MX3D’s printer during the process of printing a metal bridge.Credit: Olivier de Gruijter/MX3D
And California start-up firm Relativity Space in Los Angeles says it is constructing a nearly fully 3D-printed rocket. The rocket is designed to lift 1,250 kilograms into low Earth orbit, and its first test launch is slated for 2021. Printed metal doesn’t always have the same heat-dissipating performance as non-printed metal, says Relativity Space’s chief executive, Tim Ellis, but the printing process can add cooling channels in geometries that can’t usually be manufactured. Because rockets are used only once or perhaps a few times, they don’t have to be as strong in the long term as do alloys in aeroplane parts, which must resist failure over tens of thousands of pressure cycles, Ellis says.
A metal printer at start-up firm Relativity Space, which aims to test a mostly 3D-printed rocket in 2021.Credit: Relativity Space
These large-scale metal-printed projects are built with robot arms that feed a thin metal wire to a laser that welds the material into place. Other established ways to print metal use a laser or a beam of electrons to melt or fuse a bed of powder into layers of finished product. Another technique binds a bed of powder with liquid glue, then sinters the structure in a furnace. And printers designed in the past few years extrude molten metals through nozzles, in much the same way as in FDM.
Aviation firms such as Boeing, Rolls Royce and Pratt & Whitney are using 3D printing to make metal parts, mainly for jet engines. It can be cheaper than milling metal blocks, and the intricate components often weigh less than their conventionally made counterparts.
But 3D-printed metals are prone to defects that can weaken the final products. Spadaccini and others are trying to use arrays of sensors and high-speed cameras to watch for irregularities such as hotspots of heat or strain — and then make adjustments in real time, he says.
Five innovative ways to use 3D printing in the laboratory
Many scientists are also hoping to improve the intrinsic strength of printed metals, sometimes by controlling the microstructures of the materials. For instance, in October 2017, a US team reported that the intense heat and rapid cooling used in 3D-printing stainless steel could alter the metal’s microstructure such that the product is stronger than those cast conventionally7. And two months ago, researchers in Australia and the United States reported a titanium–copper alloy with similar strength advantages8. As they solidified, previous 3D-printed titanium alloys tended to form grains that grew in column-like structures. The copper helps to speed up the solidification process, which results in grains that are smaller and sprout in all directions, strengthening the overall structure.
Mark Easton, a materials engineer at RMIT University in Melbourne and one of the leaders of the alloy work, has already had conversations with aerospace companies interested in exploring uses for the material. He says it could also be used in medical implants such as joint replacements.
Many of the printing techniques that work for metals can also be applied to ceramics, with potential applications that include making dental crowns or orthopaedic implants. Moulds for these objects are already made by 3D printing, with the material cast in the conventional way. But 3D-printing the entire object could save time at the dentist or surgeon’s office.
However, it is harder to control the microstructure of 3D-printed ceramics, says Eduardo Saiz, a materials scientist and ceramicist at Imperial College London. And nearly all practical ceramic printing techniques involve extensive post-print sintering that can warp or deform the part. “In my opinion, ceramics is way behind polymers and metals in terms of practical applications,” he says.
The field’s future could also lie in ‘4D printing’ — 3D-printed objects that also have the ability to perform some mechanical action, akin to artificial muscles. Often, these incorporate shape-memory polymers, materials that can react to changes in their environment such as heat or moisture.
In May 2018, researchers at the Swiss Federal Institute of Technology (ETH) in Zurich and the California Institute of Technology in Pasadena reported printing a submarine that propels itself forward using paddles that snap backwards when placed in warm water9. The work could lead to microrobots that can explore the oceans autonomously. But for the moment, the paddles must be reset after each stroke. Such devices could use battery power to reset themselves, but that makes the machine less efficient than one made conventionally, says Geoff Spinks, a materials engineer at the University of Wollongong in Australia. “There are still some big challenges with 4D printing,” he says.
Another approach to 4D-printed devices involves triggering the action with a changing external magnetic field. US researchers have 3D-printed lattice structures filled with a liquid that changes stiffness in response to a magnetic field10 — which could perhaps be used to help car seats stiffen on impact.
A fluid that stiffens in response to a magnetic field is injected into the hollow struts and beams of a 3D-printed lattice. The material can be made stiff or flexible.Credit: Julie Mancini/LLNL
Other, more passive potential 4D printing applications include stents, which could be compressed to be implanted then expanded on reaching the desired site in a blood vessel to prop it open. Last July, researchers in Switzerland and Italy described a 4D-printed stent that is just 50 micrometres wide11, much smaller than conventional ones. The devices are so small, the team says, they could one day be used to treat complications in fetuses, such as strictures in the urinary tract, which can sometimes be fatal.
Perhaps the most ambitious example of 4D printing is matter that not only moves, but is alive. Currently, techniques for such bioprinting can print tissue, such as human skin, that is suitable for lab research, as well as patches of tissue for livers and other organs that have been successfully implanted in rats. But such techniques are still far from ready to integrate into a human body. Researchers dream of printing fully functioning organs that could alleviate long wait lists for organ donors. “I personally feel we’re a decade-plus away from that, at least, if ever,” says Lewis.
All together nowMany inventive ideas about printing matter that moves or changes rely on printing multiple materials together. “That’s absolutely where the field is heading,” says Scott.
Last November, Lewis and her lab described a printer that can rapidly switch between different polymer inks or mix them as it prints a single object12. This means objects can be printed with both flexible and rigid parts. Lewis has spun off previous work on multi-material printers into a firm called Voxel8, a start-up in Somerville, Massachusetts. Her multi-material printer could help with the athletics wear that Voxel8 is developing, says Lewis. Wearable devices need to be flexible around joints while also having rigid parts to house electronics. Saiz calls the printer “beautiful work”, adding wistfully: “There’s nothing like that for ceramics or metal.”
And in March 2018, a team led by Jerry Qi, a materials engineer at Georgia Institute of Technology in Atlanta, unveiled a four-in-one printer. This combines a nozzle that extrudes molten polymer with one that prints light-sensitive resin, ready to be cured by ultraviolet lamps or lasers, and two that print wires and circuitry from tiny dots of metal13. The print heads work together to make integrated devices with circuits embedded on a rigid board or inside a flexible polymer enclosure. Qi says his group is now collaborating with electronics companies interested in printing circuit-board prototypes faster than conventional methods.
It wasn’t as simple as bolting four different printers into one platform: the researchers also needed to develop software that would allow each print head to communicate with the others and keep track of the progress.
The field is still far from delivering on early visions of bringing mass manufacturing into people’s homes. For now, sophisticated printers are too expensive to appeal to non-specialists. But 3D printing has come a long way in the past 20 years. Todd remembers people touring his lab in the early 2000s to see his technique to fuse specks of metal dust together to grow parts. Compared with the conventional milling machines and metal-cutting systems in neighbouring labs, his 3D-printing machines struck visitors as a complete oddity. “It was like we were some sort of a dog playing a piano in a bar,” he recalls. Now, for many firms, that trick is standard practice.
The Best 3D Printing Videos from 2021
Published on January 9, 2022 by Madeleine P.
The year 2021 has come to an end and, like every Sunday, 3Dnatives is taking a look at some of the best videos, though this time it’s from the past 12 months rather than the week. Between building houses, bridges, robots or car parts, the technology has developed greatly over the past year. Other industries, such as medical and aerospace have also been impacted by the advancement of the technology. In addition, the return of physical events, such as Formnext, the world’s largest trade show dedicated to 3D printing, has brought industry players together. Through these 10 3D printing videos, relive some of the most outstanding innovations of 2021!
A 3D printed ocular prosthesis
A few weeks ago we learned about the case of Steve Verze, a London resident who became the first person in the world to receive a 3D printed ocular prosthesis. The prosthesis was developed in a collaboration between several agents in the UK and Europe, in a project led by researchers at UCL and Moorfields Eye Hospital NHS Foundation Trust. In this video, see how 3D printing has enabled Steve to regain his self-confidence thanks to the ultra-realistic appearance of the prosthesis, which is also adapted to the shape of the eye socket.
Large format machines at Formnext 2021
One of the biggest 3D printing events that the industry experienced in 2021 was undoubtedly Formnext. Organized in Frankfurt in mid-November, this event brought together the main players in the industry in one place after several months without the possibility of physical events. And to bring you first-hand all the news of the 2021 event, the 3Dnatives team made a series of videos with the most outstanding machines, applications and innovations of the fair. Specifically, in this video, get to know the 5 large format 3D printers that we saw in Frankfurt, specifically at the CMS, Triton, CEAD, Cubicure and MX3D booths. Discover the features of these five machines below!
The 3D printed Striatus bridge
Among the various 3D printed bridges from this year, we would like to highlight the Striatus Bridge. The project was carried out by a group of architects from ETH Zurich who, together with Zaha Hadid Architects and Incremental3D technology, managed to design this pedestrian bridge. It is a 12 x 16 meter long bridge that was installed by assembling several individual pieces in a park in Venice. Thanks to 3D printing, the concrete was only applied at certain angles which ensured that the bridge did not need any extra reinforcement. We’ll let you discover the rest of the details in the video!
Trying out the Adidas 4DFWD
The combination of 3D printing, footwear and sport is certainly something we have seen throughout 2021. In fact, the so-called Adidas 4DFWD were launched in May this year by the German manufacturer in collaboration with 3D printing company Carbon. What is striking about these sneakers is that the midsole has been created using resin additive manufacturing. According to those behind the project, this design should allow athletes to generate more thrust when exercising thanks to the lattice structure of the midsole. To learn more about these shoes, see them in action in the video below.
The role of additive manufacturing in construction
As additive manufacturing takes center stage in the construction industry, many companies have started 3D printed house projects. What once seemed like science fiction is now a reality. Thus, companies such as WASP, ICON, Mighty Buildings, TAM and many others have taken advantage of 3D printing to bring their innovative projects to life. To learn more about the rise of the technology in construction, we at 3Dnatives wanted to take a look at some of the most popular 3D printed houses in recent months. Will additive manufacturing be the main method to build houses in the future?
Atlas, the Boston Dynamics robots
This is undoubtedly one of the 3D printing videos that went viral in 2021. It is about an obstacle course performed by the so-called Atlas, 3D printed humanoid robots. The development of the robots was carried out by the company Boston Dynamics, who aim to test the limits of what is possible by combining 3D printing and robotics. Specifically, the Atlas prototypes have certain 3D printed components, such as legs or other parts of the final structure. Don’t miss the amazing video where the robots make all kinds of jumps by itself!
3D printing of bones with living cells
Advances in additive manufacturing in medicine are revolutionizing the industry, enabling the development of exciting projects ranging from prosthetics to 3D printed organs. In this case, we will watch a video in which Kris Kilian, a research doctor at the University of New South Wales in Sydney, explains a new initiative using this technology. Specifically, his research team developed an ink that could allow surgeons to create 3D printed bones using real living cells. If you want to learn more about this project and its impact on the medical sector, don’t miss the video below!
3D printed rockets for space exploration
As time goes on, more and more projects using additive manufacturing are emerging in the aerospace sector, whether for the creation of parts and tooling or large-scale structures. The growing implementation of 3D printed rockets in the industry is enabling companies to reduce the weight of final parts as well as production times. To learn more about the advantages of this technology in space exploration, we have taken a look at the main projects to date. Discover the activity of major companies such as Relativity Space, Hyperganic, SpaceX or SPEE3D!
The TECLA project uses sustainable resources
Although we have seen several videos from 2021 that use 3D printing in the construction sector, we could not leave out the TECLA project, one of those that has most marked the year 2021. Carried out by the Italian company WASP, these structures have been created with natural and sustainable materials, using their proprietary construction 3D printer. The innovative habitat model created by WASP aims to implement a new circular model of housing created entirely with reusable and recyclable materials, from local soil, carbon neutral and adaptable to any climate and context.
3D scanning of difficult surfaces
Another video that caught our attention during 2021 was offered by HandsOnMetrology. The company published this short video in which it aims to solve a big question that many users in the industry ask themselves on a daily basis: how can you 3D scan the most difficult areas of a part or model? To do so, it shows the case of the IndyCar RLL racing team, who needed to scan the windshield of a racing car, which was complicated because the laser went through the surface. For this, they used a 3D scanning mattifying spray that allowed them to coat the surface, obtaining a much cleaner and higher quality final result.
Ford and BigRep additive manufacturing
Another video highlight of 2021 comes from Ford Motor Company. In this case, the famous automaker used BigRep’s large-format additive manufacturing to optimize tooling production at the factory. With more than 30 years of experience in additive manufacturing, Ford expanded its Cologne prototyping facility with two BigRep solutions. This integration of 3D technology enabled Ford to reduce lead time by 94%, as well as final costs. All these investments in additive manufacturing machinery highlight the growing popularity of the technology in many areas, particularly in the automotive industry.
What do you think of our choices for the best 3D printing videos from 2021? Let us know in a comment below or on our Linkedin, Facebook, and Twitter pages! And don’t forget to sign up for our free weekly Newsletter here, the latest 3D printing news straight to your inbox! You can also find all our videos on our YouTube channel.
Feature Demo
As part of the 3D Print Expo exhibition, which was held in Moscow in Sokolniki Exhibition and Convention Center in October, the editors asked what new and interesting things in the field of 3D printing and 3D scanning are offered to the consumer on the Russian market. What did the visitors see?
3D printers
When asked about the most interesting, most of the exhibitors readily demonstrated the equipment and materials presented at the stands, including novelties from the domestic manufacturer.
Vortex from Surgut showed 3D printers of its own design and production: DUAL and GIANT models ( fig. 1 ). The presence of two printheads makes it possible to produce two-color parts or parts with complex supports on them, when the supports are printed with a water-soluble material, and the product is the main one. The small DUAL has a diameter of 320 mm and a print height of up to 55 cm, the large GIANT has a diameter of 55 cm and a print height of up to 95 cm. As innovative components for delta printers were identified: a fairly light head, head height switching system and a fully automated calibration system .
Fig. 1.
3D printers also with two extruders: Pro2 and Pro+2 by the well-known Chinese developer RAISE3D — were demonstrated at the booth of Tsvetnoy Mir LLC (construction area, respectively, 305 × 305 × 300 mm and 305 × 305 × 605 mm, resolution printing - 0.01 mm). The printers are distinguished by high productivity, as well as a wide range of materials used, which is achieved due to the special design of the extruder and its heating up to 300°C.
The capabilities of the Her-cules STRONG DUO printer with a new dual-extruder printhead manufactured by IMPRINTA demonstrated a unique motorcycle from Vizuit lab (a motorcycle customization company). Vizui Lab uses printing for two purposes: prototyping and testing parts before final production from metal and for printing parts that are not under load: electronics cases, decorative covers, overlays, etc. As for this printer model, it has new systems automatic calibration from nozzle height position to table plane calibration, increased positioning accuracy, plastic control system in the coil.
The Dragon 3D printer, a new product from Cyber, was taken as a benchmark for speed and quality. Printing is implemented by two independent extruders on the same X-axis. In addition to the fast switching of materials, this gave an additional function of parallel printing - two parts in the time of printing one. The closed case with a space frame provides good rigidity and allows printing with structural materials with shrinkage.
Two new models were presented at the Maestro booth. The goal of the little Honey printer was to make it affordable for the home, but like the base Maestro Classic, it has a filament motion sensor and table adjustment. The future flagship with two printheads was also presented. In addition to the technologies mentioned, the model provides a power backup system, a new control controller, a color screen, USB support, and a built-in Wi-Fi module. In the process of developing a remote monitoring and control system via the Internet, it is planned to install a camera to receive slides from a printed table.
New from Picasso — the VC Picasso machine has a large print area of 360×360×610 mm, automatic table level, an automated profile system, like all X-series printers. So far, printing is carried out with one material, but a two-nozzle version is being prepared.
The new Magnum Creative 2 printer ( fig. 2 ) has improved and simplified the process of printing with two nozzles, the switching time between which is no more than 0.5 s. For ease of use, semi-automatic calibration of the height and distance between the nozzles has been added. The updated software gives you faster speed and better print quality than the PRO model. The size of the construction area is 245×170×170 mm.
Fig. 2 .
The key feature of the new PrintBox3D White 3D printer is the fully enclosed forced draft chamber. Thus, the best temperature balance is created in the 3D printer chamber for printing with high-temperature plastics. For this model, a new extruder was developed, which has become much lighter than its predecessor. Easier cleaning process. There is a filament sensor. Working chamber size: 220×210×230 mm.
Elektroprivod presented the SkyOne 3D printer based on the Koskar mechanics ( fig. 3 ). To date, no one in the world produces such printers. What is the main advantage? The printer turned out to be quite compact with standard print settings. Removing the table, you can achieve a minimum dimension for storage. The printer has no components subject to temporary deformation.
Fig. 3 .
A new product on the market - a 3D printer that prints with clay, was presented by the company "Robokinetics". The company also offers Delta 3D printers with a Mixing extruder, which allows you to mix two or three filaments of the same material of different base colors in the required proportions during the printing process. Thus, shades of these colors and new colors can be obtained in the product.
At the booth of AM-KOR LLC, the official representative of XYZprinting (Taiwan), they showed the world's first affordable 3D printer with the ability to print in full color daVinci Color ( fig. 4 ), combining inkjet and 3D printing processes based on technology FFF (Fused Filament Fabrication). The principle of operation is as follows: an inkjet printhead applies CMYK ink to a special CPLA absorbent filament, allowing you to create products with millions of colors. The print area of this model has dimensions of 200 × 200 × 150 mm, positioning accuracy along the Z axis is 0.4 μm, along the X and Y axes is 12.5 μm, the layer thickness is 100–400 μm, which allows you to create quite voluminous and accurate full-color 3D models.
Fig. 4 .
Industrial 3D printers using FDM technology were presented by two companies Nissa Digispace — a dealer of Stratasys (the Srtatasys F370 model with a working area of 356 × 254 × 355 mm was demonstrated at the booth) and a Russian manufacturer, Total Z (the model was demonstrated at the booth). ANYFORM 450 PRO with working area 450×450 mm - fig. 5 ). In addition, Maker Bot FDM printers, the Replicatior+ and Replicator 9 models, were shown at the Nissa Digispace booth.0003 Mini+ with working areas 295×195×165 mm and 101×126×126 mm, respectively.
Fig. 5.
The only SLM metal-printing printer at the exhibition was demonstrated by the domestic company Exclusive Solutions LLC (3DSLA.RU). According to the manufacturer, the platform of its own design allows you to quickly manufacture printers with any reasonable build zones (up to 900 × 900 × 1000 mm), install laser sources of different powers and create solutions with several synchronously operating scanners. These machines work not only with spherical powders, but also with non-spherical ones, which are 2-4 times cheaper. Triangulatica's own software allows you to prepare printing tables, arrange support structures in automatic mode, create printing strategies for various materials, etc.
The ISL group of companies, together with the Moscow State University of Food Production, is developing innovative 3D food printers. Various materials, modes of their supply, temperature parameters are investigated. A concept model was demonstrated at the exhibition, the first 3D printer is expected to be released within a year. Among the materials used: chocolate, icing, dough, puree.
And at the stand of the 3D ARTEL online store, one could already see the results of printing on coffee foam, cocktails and desserts.
And of course, there were other exhibits and exhibitors, including online stores offering Chinese equipment.
Scanners
Range 3D Vision Scanners manufactured in Russia. The user is offered two models: Spectrum and Pro. The flexible equipment is accurate and detailed and allows you to scan both miniature (less than 3 cm) and large (from 1 m) objects.
Terem3D booth demonstrated the capabilities of THOR 3D scanners ( Fig. 6 ). According to the company, this is the first handheld 3D scanner that can digitize almost everything from a coin to a tractor. All you need to do is choose the right lens - one of the three. Patented hardware and software ensure the best results even when scanning complex objects with sharp edges or shiny, thin walls. Mini model accuracy up to 40 µm, Midi up to 70 µm, Maxi up to 150 µm.
Fig. 6 .
In the art gallery area, Texel presented a new version of the 3D scanner, thanks to which you can make a three-dimensional model of a person in 30 seconds. Two models were shown: the compact Texel Portal MX and the full-size Texel Portal BX.
Materials
At the booth of the REC manufacturing company, attention was drawn to promising flexible materials for 3D printing: elastic Flex, similar in properties to the flexible rubber Rubber, as well as the most elastic and wear-resistant in the Sealant line, which also features high chemical resistance to oils, gasolines, alkalis and some acids.
The representative of the Print Product company first of all singled out Flex hard (resistant to ultraviolet, solvents and at the same time machined), ADS V-0 - flame retardant ABS, PC polycarbonate for printing durable products.
Filamentarno demonstrated a new wax printing material. Products made from it without changing the technology can be used for any casting process, providing maximum cost reduction in the manufacture of small-scale and single products.
Other interesting materials were also shown here.
TOTAL CF‑5 carbon-filled polyurethane is a material with very low shrinkage, high temperature resistance and high wear resistance, designed for printing final products: gears, parts of mechanism cases. PROFLEX material is specially made for printing art products (such as life-size puppets presented at the exhibition). It is available in two colors and, unlike most FLEX materials, undergoes chemical post-processing. For printing lightweight structures, AEROTEX‑2 carbon-filled composite is suitable, which foams during the printing process. The density of the material after printing is about 0.8 g/cm3. In the process, it is possible to adjust the density and hardness of the structure.
Interesting Applications
The company's clients were invited to work at the booth of the Russian manufacturer of materials Print Product, who illustrated various areas of 3D printing. Thus, the My3DSHoes company demonstrated the work of a factory for the production of individual shoes. In addition to printing individual insoles and other parts of shoes, the company has developed original technologies for gluing various materials to printed parts to ensure comfort.
Fig. 7.
Representatives of the construction industry - the companies 3DSHOP and "DUST NO" at first used additive technologies for their own needs, producing products that were difficult to purchase on the market: a casing for angle grinders for connecting to a vacuum cleaner, separators for grinders, etc. - prefabricated and collapsible products of various form and functionality. Later, a separate direction grew out of this, including an online store and the production of its own large-sized printers. An interesting development of the company was a new composite (printed mesh, covered with a thermally insulating layer such as foamed polyethylene). A sheet of this composite when heated by boiling water or dry exposure to 90 degrees can be molded. Due to the thermally insulated layer, the heated material does not burn (the temperature of the outer layer is 30–35 degrees), heat is stored inside. Moreover, the material remains plastic not for 10–15 seconds, but for a minute and a half. This is sufficient time to, for example, mold it for use in traumatology instead of the usual gypsum or expensive foreign materials.
The highlight of the exhibition, of course, were the unusual exhibits of the art gallery: the Onyx dolls, the Reptiloid doll, a dinosaur with a movable jaw, a four-meter statue of a Girl with an oar.
Winners
As part of the exhibition, the list of winners of the 3D Print Expo Awards, the most influential companies of the year in the field of additive technologies, was traditionally announced. The organizers of this event are Smile Expo and SIU System.
This year the following companies were awarded nominations:
3DSYSTEMS. PRO - brand of the year;
MZTO - the best domestic manufacturer of 3D printers;
VORTEX - the best innovative company of the year;
CYBERON - the best development of the year;
TEREM 3D is the most demanded manufacturer of consumables;
RANGEVISION - Best 3D Scanning Company;
TOP3DSHOP is the best integrator of 3D equipment for additive technologies and digital manufacturing;
MAESTRO Rookie of the Year.
As part of the business program
, the exposition of the exhibition was traditionally supplemented by a rich business program, where one could not only get information, but also acquire new skills. In the lecture area, which was held with the support of RENA SOLUTIONS, they discussed novelties, changes, innovations in the field of additive technologies (Fig. 7). Among the topics of speeches are: intellectual property rights in 3D, integration of additive technologies in production, the use of 3D printing of sand
molds and models for investment casting, modeling of 3D printing processes, 3D printing with composites, etc. Round tables were held on the following topics: “Training for the industry of additive technologies”; "Best practices for the introduction of additive technologies in 2018". During the pitch session, the exhibiting companies made short presentations of their products, presented their brands and talked about the latest developments in the industry. Those who wish could take part in a master class from 3Dmaker and draw a figurine from ABS plastic using a 3D pen. Master classes were also held by PICASO 3D, during which visitors mastered the skills of 3D modeling, 3D printing and 3D scanning.
Interest in additive technologies and their new applications in various industries is constantly growing. And the 3D Print Expo exhibition is one of the leading platforms that reflect new trends and trends in this direction. And the statistics confirm this - this year it was visited by 3,000 guests. ■
Author: Tatyana Karpova
, 3D printers, Vortex Firm, RAISE3D, Dragon 3D printer, VC Picasso machine, PrintBox3D White 3D printer, Elektroprivod Company, SkyOne 3D printer, AM-KOR LLC, 3D scanners, 3D models
90,000 demonstration of the work of 3D printer and 3D scannersSupplier of 3D equipment since 2010
+7 495 646-15-338 800 333-12-82
3D scanners3D-printer-service providing services for the company clients of clients.
Contacts
Globatek experts are ready to demonstrate 3D equipment for you: in our demo hall, at an enterprise in your city or region, using an online broadcast. You will be able to try out 3D printers and 3D scanners, see print samples from different materials, and ask technical experts questions.
01
Own demo hall in Moscow with equipment and samples
02
Organization of visits to Russian enterprises using 3D technologies
03
Visiting plants of 3D equipment manufacturers in Russia and abroad
04
Exit demonstrations of 3D scanners, Test 3D 1,
Demosal in Moscow
In the demosal of Globatek, you can ask issues of equipment for equipping enterprises 3D equipment, see popular models of 3D printers and 3D scanners in action
Demonstration of 3D printers
In the Globatek demo hall you can see how professional 3D printers work, compare the features of different additive technologies
Over 500 3D printed samples in various technologies
Explore the properties of 3D printed samples from different materials, compare details, surface quality - so you can understand which material is right for your applications
PhotopolymersMetal powdersWaxPlastic
Test 3D scan your samples
Globatek engineers will explain how 3D scanners work and run a demonstration scan of your samples, show you the results
EPiCRangeVisionGOMScantech
Expert advice on 3D technology implementation
Globatek experts will study your tasks, select a set of equipment according to the budget and terms of delivery, answer all questions about the introduction of 3D equipment into production and research processes
Examples of 3D printing samples located in the Globatek demo
Examples of 3D printing samples located in the Globatek demo
Road demos
1.
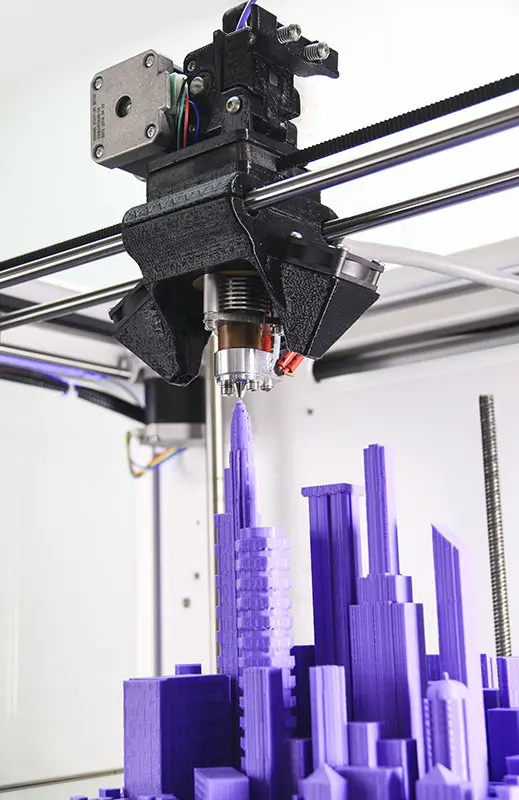
3D scanners
-
We will conduct 3D scanning your samples, show the results
-
We will talk about the role of 3D changing and quality engineering and quality control
-
We will show successful cases of application in your industry
9000 9000 Answer questions
3D printers
-
Let’s talk about the types of equipment and 3D printing technologies
-
Bring samples of 3D printing from the right materials
-
We will show successful application cases in your industry
-
We answer questions
2. Meeting at the enterprise using 3D equipment
at the meeting you can see
-
to see 3D -equipment, 3D -equipment, built -in in real workflows
-
View samples of 3D printing and 3D scanning
-
Get feedback from employees using 3D technologies at work
Geography
-
more than 300 clients
-
79 cities in 40 regions of Russia
-
5 countries of the near-Civil Code
-
4
of science, science, science, science, science, science, science, science, science, science, science, science, science, science, science, science, science, science, science, science 3D equipment manufacturer's plant
When implementing large-scale projects to equip an enterprise with 3D equipment, as well as in the production of additive systems according to individual parameters, it may be necessary to visit manufacturing plants.
Globatek specialists are ready to organize such a trip and act as technical consultants and intermediaries.
We will organize a meeting with manufacturers in Russia, Europe, USA, China, South Korea
We will make a trip plan, select convenient tickets, transfer, accommodation options
We will attend the meeting, we will help to negotiate
When implementing large-scale projects to equip an enterprise with 3D equipment, as well as in the production of additive systems according to individual parameters, it may be necessary to visit manufacturing plants. Globatek specialists are ready to organize such a trip and act as technical consultants and intermediaries.
We will organize a meeting with manufacturers in Russia, Europe, USA, China, South Korea
We will make a trip plan, select convenient tickets, transfer, accommodation options
We will attend the meeting, we will help to negotiate
Sign up for a demo
Leave a request - we will call you back and answer all your questions
Call 8 800 333‑12‑82
to get advice from Globatech engineers on choosing 3D equipment
Come to our demo hall
to see the best 3D printing and 3D scanning systems in action
I confirm the accuracy of the information I entered and agree to the processing of my personal data in accordance with the privacy policy and user agreement.