3D printed house interior
See Inside This 3D-Printed House With an Ultra-Modern Interior
US Markets Loading... H M S In the news
Chevron iconIt indicates an expandable section or menu, or sometimes previous / next navigation options. HOMEPAGEReal Estate
2022-08-03T13:16:54Z
Save Article IconA bookmarkShare iconAn curved arrow pointing right. Read in app The 3D-printed house is in Beckum, in western Germany. PERI- Architecture firm Mense-Korte constructed Germany's first 3D-printed house.
- The firm built the house in Beckum, near Münster, in western Germany.
- See inside the 1,722-square-foot award-winning home.
Thanks for signing up!
Access your favorite topics in a personalized feed while you're on the go.
This is an edited, translated version of an article that originally appeared on July 23, 2022.
The architecture firm Mense-Korte completed Germany's first 3D-printed house in Beckum, North Rhine-Westphalia, in western Germany, in August 2021. The printing process took eight months.
The company worked with Peri, a formwork and scaffolding manufacturer and supplier, and HeidelbergCement, a multinational building-materials company.
The two-story house has 1,722 square feet of living space and a modern interior with smart technology. The project has won several awards, including a 2021 German Innovation Award.
Take a look inside.
The foundation of the 3D-printed house
Mense-KorteThe 3D-printing process
Mense-KorteThe house during construction
Mense-KorteAnother view of the house during construction
Mense-Korte/EPA-EFE/FRIEDEMANN VOGELThe living room, with the kitchen to the left
PERIAnother view of the living room
PERIThe kitchen
PERIThe bathroom
PERIThe fireplace
PERIThe stairs
PERIThe balcony
PERI Read the original article on Business Insider Deutschland.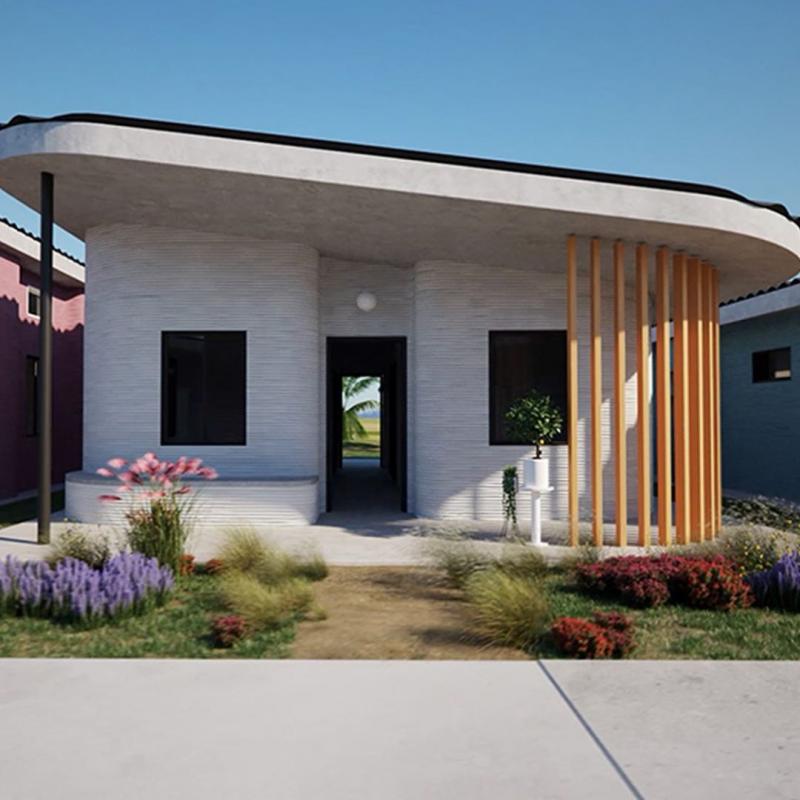
This post originally appeared on Business Insider Deutschland and has been translated from German.
Follow Business Insider Deutschland on Twitter.Read next
Translation Team Nathan Rennolds Business Insider DeutschlandMore...
Would You Buy a 3D-Printed House? Take a Peek Inside the First of Its Kind to Hit the Real Estate Market
Photo: zillow.com
Three-dimensional printing isn’t just for little things—SQ4D, pronounced “S-squared,” a New York construction company, uses patent-pending 3D technology, known as Autonomous Robotic Construction System (ARCS), to print houses on-site. Now, the company’s first full-size spec house is on the market, and it looks a lot like a traditional house. Check out their 3-bedroom, 2-bath house in Riverhead, New York, and keep reading to find out more about this new type of construction.
How It Works
The basics behind printing 3D homes are nearly identical to those 3D printers use to create other items. Through the use of computer numerical control (CNC), a large concrete extrusion machine carefully follows paths designated for interior and exterior walls, depositing uniform layers of semi-solid concrete that cure to form a structurally sound frame. Each house is meticulously engineered to meet building codes. The company inputs a home’s architectural plans into its computer and then manually mixes and feeds concrete into the extrusion machine. The home in Riverhead took just 48 hours of concrete extrusion over eight days to complete the frame.
RELATED: The 12 Biggest Downsides to Buying New Construction
What’s Included
A 3D-printed house is comparable to other types of concrete-frame homes, including those built from precast concrete blocks and those where the exterior walls are formed and poured with wet concrete. But the finished home is not entirely 3D printed. The concrete extrusion machine creates the interior and exterior walls, and in some cases it may also form a foundation. For a close-up look at how the process works, check out this video from Apis Cor, a Utah-based 3D contractor.
Once the walls are complete, traditional framing takes over to build a truss or rafter roof system, add doors and windows, shingles, wiring, plumbing, and HVAC runs, and then complete the interior finish (cabinets, wallcovering, flooring, and fixtures) that make a house a home.
Advertisement
Photo: zillow.com
RELATED: 5 Things to Know Before Buying a New Construction Home
Cost Factor
Although it’s one of the most robust building materials around, concrete is also one of the least expensive, so the materials necessary to build a concrete house will be cheaper. The most significant savings, however, comes in reduced labor charges. For a traditional house, labor costs can range from 30 to 50 percent of the house’s overall cost.
According to Zillow, the SQ4D house in Riverhead is listed at $213 per square foot, which is about $60 to $70 cheaper than the per-square-foot price of comparable homes in the Riverhead community. Keep in mind that a lot of factors go into pricing a new home, such as the value of the lot it sits on, so the best way to understand a new home’s actual value is to chat with a local real estate agent who is knowledgeable about the houses in the community.
Photo: zillow.com
Environmental Impact
Framing a house in traditional style is a noisy, dusty endeavor that requires cutting down trees to harvest the wood necessary to frame the walls, floors, and roof. Right off the bat, a 3D-printed house is a more eco-friendly option because it saves trees. New concrete does off-gas as it cures; however, complete curing of concrete is 28 days. Once the concrete cures, the risk of off-gassing is minimal.
Photo: zillow.com
RELATED: Wannabe Homeowners, Listen Up! Find Out Why 2021 Might Be the Best Year to Buy Your First House
The Future of 3D-Printed Housing
As technology improves, it’s almost certain that 3D-printed structures will become more common. Currently, 3D printing is making it possible to create affordable homes for the homeless. According to The Architect’s Newspaper, an entire community of low-income housing, known as the Community First Village, has recently been developed in Austin, Texas, built by ICON, a robotics company. These homes offer something residents may not have had before—a safe place to call home. Three-dimensional printing won’t replace traditional construction anytime soon, but it offers an affordable and environmentally sound alternative.
Advertisement
decor on a 3D printer - a geek toy or a trend?
Is 3D printing an outdated trend from 2015? Interior designers from all over the world do not agree with this. Everything can be printed on a 3D printer: jewelry, dresses, bus stops, and even houses. But more often technology is used to create interior items. 3D printing has become more accessible in 3 years, and it can be used in interiors of any style.
Furniture
3D printers are able to create real masterpieces of furniture, thanks to the precision and subtlety of printing. The production uses recycled materials, which helps save on raw materials and reduce equipment costs. 3D technology is capable of printing thin frame modular furniture.
Furniture printing is considered an invention of MIT University and Steelcase. The OneShot stool is the first product of its kind designed by designer Patric Join. The chair folds easily and stands out with its unique design.
The latest furniture production technology combines traditional furniture production and printing. The smallest details (hinges, fittings, frames) are printed on the printer, and the surfaces are selected from noble wood, glass, and specialized fabrics. Such production allows to produce more durable and functional furniture and expands its functionality.
Lights and decor
3D printed lampshades and shades come in all shapes and sizes. A distinctive feature of such lighting fixtures is also the presence of the finest decorative elements and non-standard shapes. Most often, designers use thin ligature in print, which allows you to play with light and shadows. These can be interchangeable shades, and transformer lampshades. Printing made it possible to simplify the production of complex design ideas that were previously made individually, manually, and were quite expensive.
Additive decor is also unique and varied. There are all kinds of vases, figurines, planters, sculptures, candlesticks. The largest printed sculpture of a man was created by Jameson Bruton (Jameson Bruton), its height is 3.62 meters. Today, materials for printing decorative elements can be completely different.
Fittings
The invention of metal 3D printing helped put the production of the thinnest door handles, locks and latches of incredible shapes on the conveyor. Once-unique handcrafted designer pieces are now fast to produce and affordable. Exquisite decorative elements also appear on finished pieces of furniture, which allows designers to experiment with interiors and embody bold ideas.
Noise reduction technology.
3D printing in the interior is used not only to create aesthetically beautiful and unique decorative gizmos. There are a number of noise reduction materials that are used to print unique noise reduction panels on walls. This is very convenient when developing acoustics in a residential or specialized room. That is, special preparation of walls and expensive repairs are not required, you can simply install panels printed on a 3D printer.
Metamaterials are a class of additive printing materials characterized by their ability to adapt properties to changing environments. 3D printed acoustic metamaterials use a magnetic field. The technology allows you to block the mechanical vibrations of sound waves. It was this invention that brought the noise reduction system to a new level.
Printing materials.
The first 3D printed products were made of special plastic - all kinds of shades, vases and bedside tables. Now technology has stepped forward, and printed objects can be made from completely different materials.
Glass products
Previously, the finest glass knitting was made by hand to order and cost fabulous money. It was 3D printing that made unique glass decorative products affordable, putting them on the production line.
Glass vases and figurines of the smallest details are not printed with molten glass initially. A 3D printer casts a mold from a heat-resistant material, after which hot glass is poured into it. The form is easily removed after cooling, and the glass product is not inferior to the manual work of professional glassblowers and stained glass artists in terms of sophistication of execution.
Three-dimensional ceramic objects
Author's interior ceramics brings aristocracy and artistry to the apartment. These items are very fragile. The attempt to replace manual work with 3D printing failed to reduce the cost of production, but it was able to increase the impact resistance of products.
Ceramic printing is a labor intensive process. This is due to the need for specific processing of clay: firing and glazing. Tethon 3D has adapted inkjet 3D printing using a press that compacts each freshly applied layer. This technique improves the density of ceramics after firing, but the final cost of the products is as high as handmade.
Marble stamp?
Marble in the interior always looks expensive and rich. Marble figurines and other figures are made by sculptors at the request of designers. Such luxury can only be found in premium class interiors.
This year the Poles Spestrum Filaments presented a unique PLA-based material called Antique Composite. The appearance of the material resembles marble due to small inclusions. Figurines and vases made of this material are suitable for contrast in high-tech or Scandinavian interiors. They will also become an attractive element for neo-baroque or avant-garde interiors.
Brass
Golden brushed brass inserts, shades and fittings are now at the height of fashion. This metal perfectly imitates golden sheen at an affordable price. The printing of brass decorative elements or even coffee tables and chairs found its fans very quickly. Brass is an alloy of zinc and copper that is great for additive printing. Metal decorative products with amazing accuracy of small details will ideally fit into Art Deco and modern interiors.
Concrete
Printing building machines 50 times the size of a printer, a mixture of fast hardening concrete is used instead of a plastic reel. At the moment, there are not many printed buildings in the world, not counting bus stops and playgrounds.
- Cheap housing
American company ICON has partnered with New Story, a non-profit organization, to use printing to build affordable homes. The houses are designed for the resettlement of victims of natural disasters or other cataclysms. The process of building such a house takes only 24 hours. To date, the construction cost is approximately $10,000, but the company is trying to reduce the budget to $4,000.
- Hotel rooms
Philippine Lewis Grand Hotel boasts printed rooms. Hotel owner Lewis Yakic and 3D printing specialist Andrey Rudenko have developed a unique design for a suite consisting of two bedrooms, a living room and a jacuzzi, all of which are made using printing.
- Office building in Dubai
One of the first printed buildings - a futuristic office center with a cafe and an exhibition area. The project quickly attracted fans of modern technologies, and now it actively hosts exhibitions and seminars. The author of the project was able to halve the material and time costs in comparison with traditional construction. The construction took no more than three months.
- Residential buildings in the Netherlands
The architecture firm, together with the Eindhoven University of Technology, has begun construction of a residential complex that plans to be printed by early 2019. Project Milestone will be the first ever 3D printed commercial housing.
Concrete 3D printing is used not only for houses, but also for interior items. Furniture is also printed from concrete, this non-standard material is beginning to become relevant. This year's Milan Interior Design Week featured Philippe Aduaz' exhibit and incremental3d, a chaise longue made from 3D printed concrete.
But if concrete furniture is still an outlandish exhibit, then plastic 3D printing is already being used in interiors everywhere. Interior designers create unique decorative items using printers. Units for three-dimensional printing have helped in the development of more than one creative project. A 3D printer is an indispensable tool for the affordable creation of individual concepts, embodying bold design ideas. Additive technologies serve not only for the benefit of aesthetics, but also help to reduce time, materials and energy costs.
Construction 3D printing is waiting for a breakthrough / Sudo Null IT News
3D printing technology originated in the 80s of the 20th century, but construction 3D printing appeared much later. The first construction projects using this technology appeared only in 2014. We are talking, first of all, about the so-called small architectural forms (benches, flower beds, fences). They never even dreamed about building houses. But already in 2015, the Russian startup Apis Cor made a splash - it printed a whole house in the Moscow region. Since then, news about new 3D printed houses has periodically appeared. However, despite the fact that the technology proved to be very promising in terms of the speed of construction of housing and the reduction in the cost of construction, no mass implementation followed.
Construction is the world's number one market. And, if many technological innovations are being introduced in the field of high-rise construction, then little has changed in the field of low-rise construction over the past decades. The last 30 years have seen the availability of the Internet, mobile phones, mobile internet, robotics taken to a new level, etc., but when you get to a house construction site, you are unlikely to find many technological innovations. Automation is practically non-existent, and manual labor prevails. 2020 was a test of strength for the whole world, and also led to the highest level of inflation, which, first of all, hit the construction market, there was a dramatic change in prices for metals, cement, wood and much more.
This Internet meme shows what happened to the cost of building materials in just a year. And the process is still going on. At the same time, there is a serious rise in the cost of labor, and there is an acute shortage of it. All this leads to a sharp rise in the cost of building houses. No matter how strange it may sound, statistics show that the growth of automation does not occur when everything is fine, but precisely in crisis situations, during increased competition, reduced demand and the need to urgently look for new technologies to increase production efficiency. So it happened this time, and after some stagnation, construction 3D printing received a new impetus for development.
Preparing to write an article, I turned to the founder of Arkon - Boris Kozlov y. Arkon was established in 2020 and is engaged in the production of construction 3D printers, both a workshop type for creating prefabs (prefabricated houses) and a portal one capable of printing a two-story house. I asked Boris the key, in my opinion, question:
- Construction 3D printing appeared in 2014, but no mass introduction of this technology followed in 7-8 years. Why do you think this happened, and why is there a surge of new projects right now?
- It seems to me that the reason is the snowball effect. The technology had to mature, grow from a hypothesis to a pilot implementation, and finally to commercialization and scaling (what is happening now). In addition, it should be borne in mind that construction is one of the most conservative industries, where, unlike even aviation and the automotive industry, there is still an extremely low introduction of digital solutions and automation in the field of the production process itself - the construction itself.
The issue of regulation and certification also plays an important role - this process is long and creates an additional lag.
In 2014-2016 the first samples of building 3D printers and prototypes of printed buildings appeared. The concepts of various form factors of construction 3D printers and types of printing materials were tested.
In 2017-2018 in the world, the first notable investments were made in a number of construction 3D printing start-ups. Further, by 2020, these investments "rolled" in the form of reaching a certain level of technology maturity - the first commercial products (3D printers and houses) appeared.
Finally, in 2020-2022 it became clear that the hypotheses of the effectiveness of construction 3D printing were justified (cheaper, faster, more environmentally friendly), and large investments began in the industry. A striking example is the investment of GE (the French division of General Electric) in the Danish COBOD or the achievement of a capitalization of $ 2 billion by the American company ICON.
![]()
In 2022-2023 over 1,000 buildings will be printed worldwide already, scaling from single buildings/pilot projects to entire villages and major infrastructure/reinforced concrete implementations. In addition, in a number of countries, by now, a regulatory framework has been created or is being actively created for the introduction of additive technologies in the construction industry.
Thus, I think that the specified time period is a fairly natural cycle of technology development, which is likely to experience exponential growth in the next decade.
According to ResearchAndMarket report, the global construction 3D printing market is valued at USD 354.3 million in 2022 and is projected to reach USD 11068.1 million by 2027, an increase of 99.04%.
Various market processes affect the prices and behavior of participants in the global 3D construction printing market. They create price signals that are the result of changes in the demand and supply curves for a product or service. They can be associated with both macroeconomic and microeconomic factors. Even human emotions can also drive decisions, influence the market, and create price signals.
Now let's take a quick look at what is the construction 3D printer. Without delving too deeply into the technology, we can say that construction 3D printers are very similar to classic FDM/FFF printers that print with plastic, but instead of plastic, the material here is a cement mixture, which is fed directly into the nozzle and forms an object by layer-by-layer overlay. Printers are also portal, on the basis of a flying boom, with a robotic arm.
Pictured left is a construction printer based on a boom. The figure on the right is a gantry construction 3D printer
In the figure above, a construction 3D printer in the form of a robot arm installed on a mobile platform.
Everything changed completely when, in the summer of 2021, the American company ICON, which was trying to introduce 3D printing into the construction of various auxiliary facilities, signed a contract with one of the largest American developers, Lennar, to build a village of 100 houses in Texas and immediately became a unicorn , having received 200 million dollars of investments from several investment funds.
At the same time, the Danish company COBOD, created by the world's largest construction formwork company PERRI, began selling its gantry 3D construction printers and participating in construction projects around the world. In the photo below, a modern two-story house built in Germany and a school building in Malawi, built in record time with a minimal budget.
Few things unite developed, developing and poor countries, everywhere their problems and tasks, but The lack of affordable housing is a global agenda . If in poor countries there is an acute problem with the increase in the number of homeless people due to a lack of housing, as such, then in developing countries it is necessary to dramatically accelerate the number of new housing being built to meet the needs of a growing population. In developed countries, the problem is primarily in the cost of housing, which has risen in price to such an extent that it has become practically inaccessible to young people. And with the simultaneous increase in life expectancy in these countries, this problem is only getting worse.
At the same time, the trend towards “green agenda ”, CO2 reduction, building with more environmentally friendly materials, etc. is developing. But, unfortunately, so far the construction industry is the absolute leader in CO2 emissions, as well as in the amount of garbage that each construction site leaves behind. This is not to say that construction 3D printing solves all these problems, but at least it is moving in the right direction. Let's look at this with a few illustrative examples.
3D printed walls. Today, when we talk about 3D printing houses, we are talking about printing walls. Everything else (foundation, windows, doors, ceilings and roof) is done in the traditional way. 3D printed walls are built as fixed formwork, which significantly saves the amount of cement used , and this, in turn, reduces the cost of construction and reduces the environmental impact of cement production. In addition, with this method of construction, no additional waste is produced, the strength of the structure does not suffer. It can be reinforced, as shown in the photo on the left, and engineering communications can be immediately laid, as shown in the photo on the right, which also affects the final speed of the construction of the object. At the same time, the total weight of the structure is reduced, the remaining cavities can be filled with lightweight foam concrete, insulation, straw or any other available material. Such a lightweight design can use a lighter foundation. The construction method itself is more economical in terms of material, and therefore environmentally friendly.
Eco-concrete with the addition of polymers is being actively developed, the production of which reduces CO2 emissions from 30% to 100%. The Apis Cor company mentioned at the beginning of the article, which built a house in the suburbs in 2015, is now based in hot Florida, plans to start using this material in its projects.
Another startup from Russia, Mighty Buildings, headquartered in California, initially relied on a polymer with the addition of mineral chips. And while the company doesn't build entire homes, it only makes wall panels, it has won numerous design awards, as well as a $400 million valuation in several investment rounds.
As a result, with a rough calculation, we can say that the total savings on the construction of walls can reach 30%, and the total cost of the house can be reduced by 10%. This is true for houses designed for conventional construction. And if you initially design with 3D printing, you can improve this ratio by optimizing the laying of communications, the ability to immediately print interior walls, bookmark niches for bathrooms, fireplaces, built-in wardrobes and kitchens, as was done in the house built by COBOD in Germany.
"There are spots on the sun." Despite all the advantages of construction 3D printing, has several significant disadvantages of . The main one is layering, which cannot be avoided at the current level of technology development.
The photo above shows the layering of the 3D printed walls.
This task can be worked in several directions:
-
Ribbed walls can be plastered, painted and played with as a design element. That's how ICON does it in the US, for example their latest project House Zero is done that way and has won a number of design awards.
-
Use special "shutters" on the print head that allow smooth layers, as COBOD and other manufacturers do. The photo below shows that this does not ensure the complete absence of layering.
-
Fully sand the surface to get the usual smooth wall for plastering, painting, wallpapering or other finishing. It is possible, but it will require huge labor costs, which can reduce the overall efficiency of using 3D printing.
Pictured above is a 3D printed wall sanded smooth.
The second problem is the required temperature. Ideally, printing should take place at temperatures between +5C° and +30C°. Humidity is also important. Using additives, you can push these boundaries, but not indefinitely. At strong sub-zero temperatures, printing will be possible in the field only if the construction site is covered with a dome and the required temperature is reached inside with the help of heat guns. In conditions of intense heat, it is preferable to print at night. Another solution could be to print the wall panels in the shop and assemble them on site. Of course, each of these decisions will have a negative impact on the economic efficiency of the project.
Building 3D printing can be useful not only for the construction of houses . With its help, you can solve many other problems, and there its disadvantages will not matter. For example, the American concern GE uses COBOD printers to build towers for wind turbines in the shop. Ribbed surface and temperature restrictions in this case do not play any role.