3D printed finger cast
Mallet Finger Lattice Casts Using 3D Printing
On this page
AbstractIntroductionMaterials and MethodsResults and DiscussionConclusionsData AvailabilityConflicts of InterestSupplementary MaterialsReferencesCopyrightRelated Articles
Currently, research based on the technology and applications of 3D printing is being actively pursued. 3D printing technology, also called additive manufacturing, is widely and increasingly used in the medical field. This study produced custom casts for the treatment of mallet finger using plaster of Paris, which was traditionally used in clinical practice, and 3D printing technology, and evaluated their advantages and disadvantages for patients by conducting a wearability assessment. Mallet finger casts produced using plaster of Paris, when incorrectly made, can result in skin necrosis and other problems for patients. These problems can be mitigated, however, by creating casts using 3D printing technology. Additionally, plaster casts or ready-made alternatives can be inconvenient with respect to rapid treatment of patients. In contrast, 3D-printed casts appear to provide patients with appropriate treatment and increase their satisfaction because they are small in size, custom-made for each patient, and can be quickly made and immediately applied in clinical practice.
1. Introduction
Mallet finger refers to a deformity in which the finger cannot be extended due to severing of the extensor tendon at the distal phalanx or fracture of the bone to which it attaches. Mallet finger can be classified as tendinous, in which only the tendon is ruptured, or bony, in which it is accompanied by a broken phalanx. Surgical intervention is required in the case of bony mallet finger. However, tendinous mallet finger is treated conservatively, primarily by using a splint to extend the finger so that the tendon reattaches naturally. Traditional conservative treatments include fixation of plaster of Paris or metal casts, whereas surgical interventions include bone fragment fixation using steel wire, fixation with lag screws, tension band wire fixation, fixation using figure-eight tension band wire, intramedullary wire fixation, and dorsal suture.
Three-dimensional (3D) printing technology is widely used in industry, biology, and medicine [1]. Major applications of the technology include prosthetic fingers made using 3D scanners and printers [2], wrist protection devices [3], and synthetic bone implants made of calcium phosphate scaffolding using low-temperature 3D printing technology [4]. Custom-made orthopaedic wrist casts can be created using techniques such as fused deposition modelling with rapid prototyping (FDM-RP) and 3D printing [5–8]. 3D printing technology offers significant advantages in biomedical instrumentation and tissue engineering because of its ability to produce small quantities or single parts when needed based on patient-specific requirements [9] owing to its ability to produce recognizable 3D objects applied to surgery planning, orthoses, and related application programs [10], as well as the capability to produce single or small quantities of parts according to patient-specific needs.
Medical applications of 3D printing are rapidly expanding, and revolutions in medical services are expected [11]. The present study attempts to use a 3D printer to produce lattice casts that provide good ventilation, hygienic treatment, and clear X-ray images for treatment of mallet finger.
2. Materials and Methods
2.1. Subjects
Subjects of the study were selected randomly. Casts were designed for subjects’ index fingers using either the traditional plaster of Paris method or MediACE 3D software (based on 3D scanning to measure the finger’s dimensions).
2.2. Production of Plaster of Paris Casts
Plaster of Paris casts, which are traditionally used in clinical practice to treat mallet finger, were created as shown in Figure 1(a). Figure 1(b) shows a removed plaster of Paris cast.
2.3. Production of 3D-Printed Casts
First, the index finger was scanned repeatedly while maintaining posture of the extensor tendon (Figure 2) using a 3D scanner (3D Systems Sense scanner) to generate a stereolithography (STL) file of the finger. STL files, the end result of the 3D modelling process, are typically generated by computer-aided design (CAD) programs, which use this file type to store information about 3D models. The STL file shows the surface shape of a 3D object without representation of colour, texture, or other general characteristics of the model. Accordingly, STL files are widely used for rapid prototyping, 3D printing, and computer-aided manufacturing.
A 3D model of the mallet finger cast was then created based on the STL file (Figure 3) using the MediACE 3D software (Figure 4), and the final lattice design of the 3D-printed cast was completed (Figure 5).
The MediACE 3D software is expected to create beneficial business value in the medical industry and to contribute to implementation, distribution, and diffusion of customised medical services using 3D printing, the foundation of the 4th Industrial Revolution. It has been verified through clinical application and evaluation.
A mallet finger cast for 3D printing was designed using the mallet finger STL file and MediACE 3D and then converted into G-code. The cast, shown in Figure 6(a), was produced using polylactide (PLA) resin on a 3D Edison printer. For comparison, a plaster of Paris cast is shown in Figure 6(b).
2.4. Comparative Evaluation of Products
Application of the plaster of Paris and 3D-printed casts is shown in Figure 7. To evaluate the performance of and patients’ satisfaction with each type of cast, a satisfaction evaluation (Quebec User Evaluation of Satisfaction; QUEST) [12] and a wearability evaluation (Product Performance Program; PPP) were conducted. The items of both measures were rated on a 5-point Likert scale from 1 (negative end of scale) to 5 (positive end of scale).
3. Results and Discussion
3D-printed lattice casts for treatment of mallet finger were produced based on STL files obtained through 3D scanning, the MediACE 3D software, and 3D printing technology. The advantages and disadvantages of the 3D-printed casts were then compared with those of plaster of Paris casts traditionally used in clinical practice.
The 3D-printed lattice casts showed results similar to those of the traditional plaster of Paris casts in the QUEST evaluation (Table 1). However, overall, subjects indicated that they were “very satisfied” or “satisfied” with the 3D-printed casts’ dimensions, weight, adjustment, ease of use, and comfort. Subjects were more satisfied with the weight and ease of use of the 3D-printed casts than the plaster of Paris casts (Table 1). Overall, the 3D-printed casts received a rating of “very satisfied” in the PPP wearability assessment (Table 2). In contrast, the plaster of Paris casts received many negative or “not applicable” ratings because they must be applied by medical staff.
The lattice design of the 3D-printed casts and their customised application can prevent necrosis or infection, offer a thickness and elasticity that guards against slipping off, and resolve other shortcomings of traditional plaster of Paris casts, including oedema, discoloration, hinderance of function and circulation, pain, pulselessness, dysesthesia, and burning from pressure. In future, 3D-printed lattice casts should be used instead of plaster casts to treat mallet finger, based on their many benefits, such as providing patients with the most appropriate, customised treatment.
4. Conclusions
This study produced 3D-printed lattice casts for treatment of tendinous mallet finger based on STL models of the index fingers of randomly selected subjects, obtained using a 3D Systems Sense scanner. The casts were constructed from PLA resin using a 3D Edison Printer.
The advantages of traditional plaster of Paris casts are the difficulty of taking it off by patients once it is worn and short application time. Disadvantages include possible pain, skin oedema, discoloration, burning, infection, and necrosis; the complications of splint treatments are mainly skin-related.
Complications occurring in 123 cases of mallet finger treated both surgically and nonsurgically were reviewed. The 84 cases of splint treatment had a complication ratio of 45%; these complications were almost always temporary. Among the 45 cases of surgical treatment, 53% experienced complications and 76% of complications developed during the average monitoring period of 38 months. Six cases that involved surgical treatment after splinting (for a minimum of six weeks) were counted in both groups. Major complications experienced by surgically treated patients were deep infection (4%), total joint incongruity (18%), and nail deformity (18%). Seven patients (16%) required reoperation, and all had unsatisfactory results [13] except for one whose result was unknown.
The 3D-printed lattice cases were compared with plaster of Paris casts in treatment of patients with mallet finger. The results of PPP evaluation indicated that 3D-printed lattice casts allow for accurate, rapid production of customised orthoses, improving upon existing production methods. The 3D-printed casts can additionally resolve problems associated with plaster of Paris casts, namely, hyperextension and skin problems, because production is customised to the patient using 3D scanning. The size is very appropriate for 3D printer output, and it uses less material than a plaster of Paris cast and requires little output time. The ability of 3D-printed casts to overcome the disadvantages of traditional plaster of Paris casts makes them beneficial for clinical application.
Development of 3D-printed lattice casts is meaningful because they have the potential to help many patients if produced in clinical practice using 3D printers. Improvements in body scanning technology and product design software are expected to bring benefits to clinical practice. Future research should investigate the production of orthoses with various structures using the processes developed in this study. The investigators hope that the present study may serve as a reference for research on the production methods of finger orthoses based on various diseases and their treatment in clinical practice, such as the various types of 3D-printed finger casts in Figure S1.
Data Availability
The data used for evaluation purposes are uploaded and made publicly available.
Conflicts of Interest
The authors declare that there are no conflicts of interest regarding the publication of this paper.
Supplementary Materials
Figure S1: various types of 3D-printed finger casts. (Supplementary Materials)
References
B. Ripley, T. Kelil, M. K. Cheezum et al., “3D printing based on cardiac CT assists anatomic visualization prior to transcatheter aortic valve replacement,” Journal of Cardiovascular Computed Tomography, vol. 10, no. 1, pp. 28–36, 2016.
View at:
Publisher Site | Google Scholar
K. H. Lee, S. J. Kim, Y. H. Cha, J. L. Kim, D. K. Kim, and S. J. Kim, “Three-dimensional printed prosthesis demonstrates functional improvement in a patient with an amputated thumb: a technical note,” Prosthetics and Orthotics International, vol. 42, no. 1, pp. 107–111, 2018.
View at:
Publisher Site | Google Scholar
D. Gu and J. Lee, “Development of a wrist protector using a 3D scanner and a 3D printer,” Journal of the Korean Medical Industry Society, vol.
19, no. 3, pp. 312–319, 2017.
View at:
Google Scholar
D. S. Koo and J. R. Lee, “The development of a wrist brace using 3D scanner and 3D printer,” Fashion & Textile Research Journal, vol. 19, no. 3, pp. 312–319, 2017.
View at:
Publisher Site | Google Scholar
K. Chang, J. H. Chang, M. W. Huang, and L. Y. Lee, “Innovative orthosis for phalanx extension neurofacilitation (iOPEN)—development of a 3D-printed hand orthosis for chronic stroke patient,” in Proceedings of the 2018 IEEE International Conference on Applied System Innovation (ICASI), pp. 13–17, Institute of Electrical and Electronics Engineers, Chiba, Japan, April 2018.
View at:
Google Scholar
D. Palousek, J. Rosicky, D. Koutny, P. Stoklásek, and T. Navrat, “Pilot study of the wrist orthosis design process,” Rapid Prototyping Journal, vol.
20, no. 1, pp. 27–32, 2014.
View at:
Publisher Site | Google Scholar
A. P. Fitzpatrick, M. I. Mohanned, P. K. Collins, and I. Gibson, “Design of a patient specific, 3D printed arm cast,” in Proceedings of the International Conference on Design and Technology, pp. 135–142, Knowledge E, Dubai, United Arab Emirates, December 2017.
View at:
Google Scholar
Y.-H. Seoung, “3-dimensional printing for mesh types of short arm cast by using computed tomography,” Journal of the Korea Contents Association, vol. 15, no. 1, pp. 308–315, 2015.
View at:
Publisher Site | Google Scholar
A. Bandyopadhyay, S. Bose, and S. Das, “3D printing of biomaterials,” MRS Bulletin, vol. 40, no. 2, pp. 108–115, 2015.
View at:
Publisher Site | Google Scholar
F.
Rengier, A. Mehndiratta, H. von Tengg-Kobligk et al., “3D printing based on imaging data: review of medical applications,” International Journal of Computer Assisted Radiology and Surgery, vol. 5, no. 4, pp. 335–341, 2010.
View at:
Publisher Site | Google Scholar
C. L. Ventola, “Medical applications for 3D printing: current and projected uses,” Pharmacy and Therapeutics, vol. 39, no. 10, pp. 704–711, 2014.
View at:
Google Scholar
Y. H. Cha, K. H. Lee, H. J. Ryu et al., “Ankle-foot orthosis made by 3D printing technique and automated design software,” Applied Bionics and Biomechanics, vol. 2017, Article ID 9610468, 6 pages, 2017.
View at:
Publisher Site | Google Scholar
P. J. Stern and J. J. Kastrup, “Complications and prognosis of treatment of mallet finger,” Journal of Hand Surgery, vol.
13, no. 3, pp. 329–334, 1988.
View at:
Publisher Site | Google Scholar
Copyright
Copyright © 2019 Hyeunwoo Choi et al. This is an open access article distributed under the Creative Commons Attribution License, which permits unrestricted use, distribution, and reproduction in any medium, provided the original work is properly cited.
All About 3D-Printed Splints - Bitfab
3D printing is involved in many aspects of medicine. More specifically, it is increasingly common to find 3D-printed splints to treat injuries. Years ago this sector was quite popular, but now there are many companies that market these products.
Do you want to know everything about 3D-printed splints? Then keep reading. Let’s get started!
📖 What do you want to read?
What is a splint?
A splint is basically an external, rigid element that is used to immobilize a part of the body. This is usually used in medicine when, in order to heal a dislocation or fracture, it is necessary to partially or totally restrict the movement of a joint.
As you can see, there are splints to immobilize your wrist, your finger, or even your dog’s paw. They are elements that, generally, are quite widespread and surely you have used one of these before.
What are 3D-printed splints like?
3D-printed splints are quite different in appearance and features from traditional ones. When manufactured by 3D printing, quite complex geometries can be created, so these splints usually have some quite refined features in order to save weight, improve strength and be, in general, better designed products.
Photographs from orthopedics aids store La MilagrosaWhat are the advantages of 3D-printed splints?
As you have seen, splints are quite common and have been manufactured for a long time, so why manufacture them using 3D printing?
Well, the advantages are not few. We are going to tell you what we consider to be the most interesting ones: Ergonomics, customization and costs
Ergonomics of 3D-printed splints
Regular splints are not designed individually for each user. They usually consist of a rigid, hard part and a series of fasteners, either bandages, tapes or straps.
A conventional brace is designed to be able to work on anyone, so it will never be as accurate as it should be and will sometimes restrict our movement more or less than necessary.
A 3D-printed splint should not have to work like this, since it does not need to be adapted to any individual. Following the digital manufacturing paradigm, splints are designed to be 3D printed to fit each person. This means that the splint will perfectly wrap around our limb to meet any mobility restrictions prescribed by a physician.
In addition, the splint can be adapted to the patient’s morphology, solving the problem that sometimes very tall or very short people suffer from, whose extremities are not of the average size.
Finally, keep in mind that these splints can be designed with total freedom, because they are almost always designed to be easily put on and taken off for rehabilitation, treatment or cleaning of the injured area.
Customization of 3D-printed splints
Customization always goes hand in hand with 3D printing and digital manufacturing. If each splint is custom designed for the patient, things like materials and aesthetic appearance can also be adapted to his or her taste.
Since each user has different requirements, the splint can be produced to meet any need. By choosing appropriate materials and design patterns, it is possible to design very light splints for people without great mechanical requirements, very resistant for those who are going to put a lot of stress on them, very breathable for those who do not tolerate heat well, etc. Generally, a 3D printed splint will be lighter and more resistant than a traditional one, in addition to other advantages such as being radio-transparent (for X-rays), submersible, etc.
Besides, by varying the rigidity of the material and the geometry of the design, the splint can be made more or less restrictive, allowing it to adapt to different injuries.
On the other hand, the appearance of 3D-printed splints does not have to imitate that of traditional ones. This means that, as long as optimal functional criteria are met, the design can vary to suit our tastes. Therefore, splints can be manufactured to look almost like works of art and can become an aesthetic element. Being injured doesn’t have to stop you from being fashionable.
Cost of 3D-printed splints
Splints, especially those that treat more complex problems such as back problems, are often expensive. In these cases it is often necessary to custom design the splints or adapt the design for each person to treat their injury properly. As you know, custom manufacturing at low cost is one of the great advantages of 3D printing.
By means of accessible technologies it is possible to design and print in 3D splints with very complex geometries and adapted perfectly to our morphology without having to spend a lot of money. If you want to put yourself in the hands of professionals, there are some businesses in Spain such as La Milagrosa Orthopedics that have their own professional 3D splint printing service.
If, on the other hand, you want to manufacture it yourself, the costs will be laughable, since you can design it using free software and domestic FDM printers. In this Instructables article they explain the process using paid software and a 3D scanner, but this same process can be done using photogrammetry and freely available software. If you choose this path, the total cost will be a few euros, whatever the material and the amortization of the machine you use costs.
If you are interested in knowing more about how to make your own 3D printed splints, either for yourself or for your business, do not hesitate to leave us a comment and we will gladly help you. In Bitfab we love to give ideas so that the most pro maker can start new projects.
3D-printed splints in Bitfab
In Bitfab, as you know, we are experts in digital manufacturing. If there is any issue in which digital manufacturing is a good fit, it is in issues such as this, where customization brings enormous value to our part. Making splints printed in 3D is something that, from our point of view, makes a lot of sense, and we think it can be a widespread reality in a few years.
We are already working with this today, so we would love to help you start or develop your digital manufacturing projects for splints and other medical and orthopedic items.
Contact with Bitfab
The first 3D printed ... eye. And he's alive!
3D printer Eye The medicine Prosthesis
The first 3D printed .
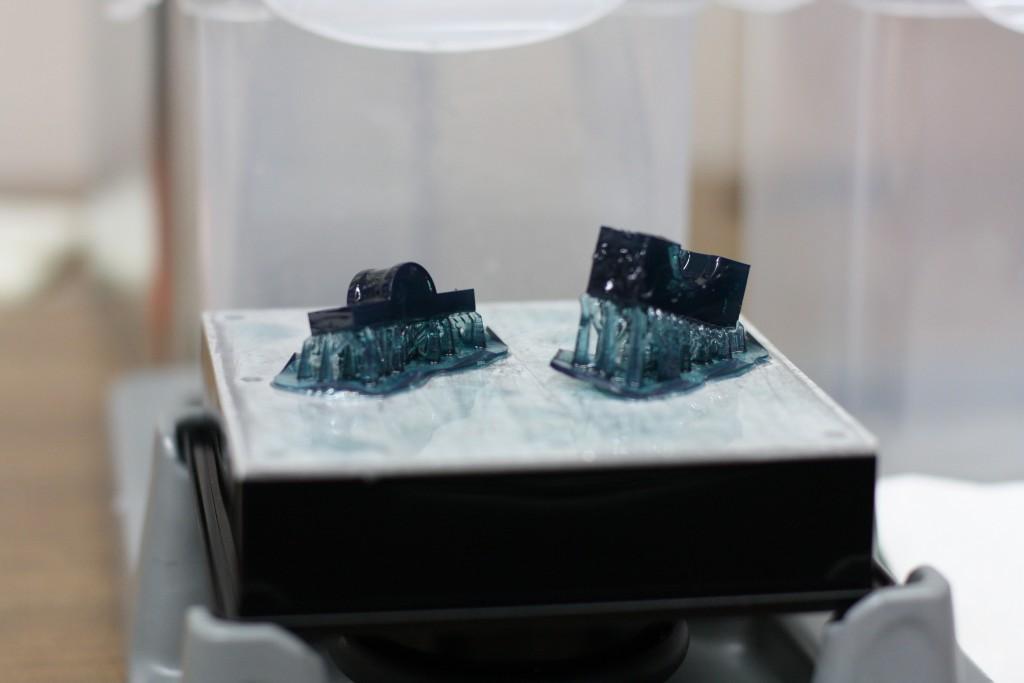
Oleg Voronin —
In the UK, for the first time created a prosthetic eyeball using a 3D printer. This was reported in the foreign edition of Neowin.
According to the source, the artificial eye was created for a patient at Moorfields Eye Hospital in the UK, who was funded by the NHS Foundation Trust. He became the first person in the world to have a prosthesis created using a 3D printer.
Steve Verz, a patient at the Moorfields Clinic, first “tried out” a printed eye on November 11, 2021, and returned home on November 25 to a full life without any restrictions. He says:
“I have been wearing an eye prosthesis since I was 20 and have always been embarrassed about it. When I left the house and looked in the mirror, I really did not like what I saw there.
This new eye looks fantastic!
The fact is that a 3D printed artificial eye is much better than a classic acrylic prosthesis. Eye experts from the same hospital cite several advantages of this method:
- First, it is much easier to create a prosthesis with a 3D printer, since this device only requires a non-contact eye scan; the creation of a conventional acrylic prosthesis is accompanied by rather painful examinations of the patient's face and the creation of an invasive cast - for children, before this procedure, even general anesthesia had to be applied;
- Secondly, a 3D printer creates a prosthesis within 2.5 hours after scanning, after which an optometrist finishes it within 1-2 weeks - and a regular acrylic prosthesis is signed by hand, and this takes up to six weeks;
- Thirdly, the printed eye looks much more realistic, it is almost indistinguishable from the real one; however, the acrylic prosthesis is often very noticeable.
- Fourthly, the eye from a 3D printer is much more convenient in terms of domestic "use" - a full-fledged biomimic digital system is introduced into it with a clear image resolution and a real pupil depth; in other words, a person can focus on objects in the same way as he does with a healthy eye.
Professor Mandig Magu, an ophthalmologist at Moorfields Hospital, has high hopes for this experiment and is looking forward to seeing the new technology go into mainstream use, improve patients' quality of life and shorten waiting lists.
iGuides in Yandex.Zen — zen.yandex.ru/iguides.ru
iGuides on Telegram — t.me/igmedia
Source:
Neowin
Buy advertising
Recommendations
- AliExpress brazenly overcharged all prices.
Don't rush shopping
- How to turn off SMS notifications that have risen in price in Sberbank and VTB
- In Russia, the price of the MacBook Air with the M1 chip has collapsed. Grab while available!
- AliExpress has decided on the rate at which prices are calculated
Recommendations
AliExpress brazenly overcharged all prices. Don't rush shopping
How to turn off SMS notifications that have risen in price in Sberbank and VTB
In Russia, the price of the MacBook Air with the M1 chip has collapsed. Grab while available!
AliExpress has decided on the rate at which prices are calculated
Buy advertising
See also
Samsung iPhone Apple
iOS will have more ads. Even developers might not like it
Apple iOS
How to listen to music on Vkontakte without ads and the Internet. Telling
VKontakte VK VK Music
how to reduce risks to patients' health / Sudo Null IT News
In the 21st century, many scientific ideas that once seemed fantastic were realized in medicine, for example, robotic surgery or bionic limbs. Considerable merit in the recent successes of medicine belongs to additive technologies. Today, 3D printers are used to make models of body parts and prostheses, and in the foreseeable future, 3D printing of artificial organs and medicines will become common practice.
According to the Wohlers Report 2018, healthcare accounts for 11.3% of the global AM market. According to Market Research Future (MRFR), the cumulative annual growth rate of the global medical device 3D printing market in 2018-2023 is estimated at 18%.
One of the key factors in medicine is accuracy, because the slightest mistake in the calculations can have fatal consequences. And here 3D printing fits perfectly, because the main advantages of this technology are the freedom of design and high precision in the creation of final products. Compared to traditional methods, the ability to print unique one-offs or short runs with complex geometries paves the way for faster, more cost-effective production.
Photo: MaterializeAdvantages of additive technologies for medicine
3D technologies have indisputable advantages:
-
High accuracy, allowing to take into account the individual characteristics of a person.
-
Ability to create structures of any complexity.
-
Lightening the weight of printed products.
-
Reducing the production time (including due to the lack of equipment), and as a result - the acceleration of medical care.
-
Saving labor and material resources.
-
Reducing the cost of products.
-
Large selection of innovative materials.
Thanks to these features, the equipment can be used both in specialized clinics and in ordinary government institutions.
« It is possible to make an individual prosthesis for each individual patient , - says Pavel Vopilovsky, director of the Scientific and Technical Complex "Machine-building Technologies" of Peter the Great SPbPU, - is the most significant factor in the use of this particular technology (3D printing - ed.) for medicine. No two people are the same, and even if you take the hip joint, right and left, they will be different bones .
What can be printed on a 3D printer to increase the effectiveness of treatment
Printing of the following products is practiced:
-
models of organs, tissues and bones when planning operations;
-
prostheses, implants, surgical templates in surgery and dentistry;
-
orthopedic insoles, corsets and other orthoses;
-
hearing aids;
-
master models for medical devices;
-
prototype housings for medical devices;
-
medical cosmetology products.
Such an extensive list allows you to speed up and simplify the process of making life-saving things for patients.
3D scanning and medical software
Medical software Materialize Mimics allows you to create anatomically accurate 3D models / Photo: Materialize Using a 3D scanner, you can get an accurate three-dimensional model of the desired object (bone, dental impression, etc. ) in minutes, then process the obtained data in a special software and print a model or a finished product on a 3D printer, or make it in a traditional way. This eliminates the need to store casts and samples - all 3D models are stored in a digital archive. If necessary, they can be quickly corrected and sent via the Internet to colleagues anywhere in the world.
Plan successful surgery with accurate mock-ups
Create accurate 3D models of bones, body parts, tissues or organs to visualize pathologies at a 1:1 scale. The doctor can accurately assess the size of the pathology and the location of adjacent tissues before starting the operation. In the case of transplantation, 3D models help to develop detailed and individual plans for operations and select exactly the right organs.
A typical example of 3D printing in medicine: a preoperative model made of photopolymer, made in our demo room on a ProtoFab printer / Photo: iQB Technologies The detailed 3D printed model and its anatomically optimal position assist the surgeon in reconciliation at all key stages of the operation. Accurate positioning of pathology and blood vessels in real time makes it possible to increase the efficiency of the operation and reduce risks.
Changing the printed anatomical models according to the actual state of the organs is one of the most important methods of using 3D technologies. This possibility not only saves valuable time for surgeons, but also improves the accuracy of disease prediction.
Printing mock-ups, models and prototypes from plastics
Create custom insoles with the Sharebot Q 3D printer, which helped achieve great results with difficult-to-use flexible elastomers A productive and cost-effective solution for creating pre-operative mock-ups and models of medical devices - 3D printing from plastics. There are several plastic printing technologies, including Fused Deposition Modeling (FDM), Laser Stereolithography (SLA), Selective Laser Sintering (SLS). The first of them uses a thermoplastic thread or granules as a consumable, the second uses a photopolymer resin, the third uses polyamide or modified powders.
An FDM, SLA or SLS printer will be a cost-effective solution for medical device manufacturers: rapid prototyping of device cases using additive technologies speeds up the product development process by several times.
3D printing process in medicine
The creation of a printed product takes place in several stages:
-
Collecting patient data using various technologies (CT, MRI, ultrasound, PET, 3D scanning).
-
Based on the results of the research, the target area is selected and a 3D model is created in the software.
-
Based on the created 3D model, an exact copy of the object is printed.
-
The printed model simulates a surgical operation.
3D printing of metal prostheses and implants
Various technologies and materials are used to manufacture prostheses and implants, from plastics to metals. Metal 3D printing allows you to create a product with a given complex geometry, ideally suited to a particular patient. Topological optimization solves such important problems for prosthetics as:
-
creation of an all-metal structure of any required shape;
-
lightening the weight of the prosthesis;
-
increasing the strength of products due to microscopic cavities that provide migration of the patient's own bone tissue cells;
-
creation of prostheses with a porous structure that promotes faster implantation.
3D printing from metal alloys (primarily titanium) is used for prosthetics of the bones of the maxillofacial region, intervertebral discs, collarbones, knee joints, shoulder blades, and hip bones. In dentistry, these materials are used for the manufacture of one-piece implants, as well as metal bases for crowns and bridges made of titanium, cobalt-chromium and other alloys.
The most important features of metal 3D printed prostheses are their perfect connection to the body and the absence of rejection. Creating prostheses on a 3D printer is cheaper and takes less time.
Case studies
SLM reconstruction of a zygomatic defect
Reconstruction of a large zygomatic defect is a complex surgical operation that requires the patient's face to be symmetrical, proportionate and anatomically natural. A 43-year-old man presented to the department with a severe defect in the left midface, which he received 6 years earlier as a result of a car accident. The damaged bone was reconstructed with a custom titanium implant printed on an additive machine by SLM Solutions. The computer-designed implant had an ideal geometry, and the operation to install it went exactly as planned. Follow-up of the patient over the next year did not reveal any complications.
Results of 3D technology application:
-
excellent biocompatibility and integration of the bioimplant into tissues;
-
reducing the weight of a titanium product by creating a hollow version of it;
-
accelerated integration by filling the implant with material taken from the patient's ilium;
-
the finished product perfectly fit the damaged area and did not require adjustment during the operation;
-
complete absence of complications and side effects after implant placement.
Obtaining such results gave hope for the successful use of additive installations in surgical operations.
How an accurate model of the spine and trachea was created
Experts from ProtoFab, a manufacturer of a wide range of SLA printers and materials, share their practical experience in using 3D printing in medicine. Peking University Third Hospital asked ProtoFab to create an accurate 3D model of the patient's spine and trachea in preparation for the upcoming surgery. Complications caused by the disease did not allow the surgeon to insert a tube into the trachea to perform the operation. Physicians needed a model with which they could practically evaluate different ways to solve this problem.
Computed tomography and magnetic resonance imaging data were imported into specialized medical software, which allows all these data to be converted into a 3D model. Using this software, ProtoFab specialists were able to see the problematic areas of the patient's trachea.
The next step was to do the 3D printing directly. Such medical projects require the creation of an extremely accurate copy with the utmost level of detail. However, stereolithographic 3D printing can easily handle such complex shapes and structures, and ProtoFab's experienced engineers were able to perfectly reproduce every last detail. The 3D-printed model allowed doctors to analyze an absolutely exact copy of the trachea and the surrounding area before the operation and take preparatory measures that would otherwise be impossible.
3D denture fabrication
A team of researchers from Chabloz Orthopédie (France) has succeeded in creating a unique and truly revolutionary prosthesis. The company worked with Denis Gauthier, who had his forearm amputated. First, the specialists performed a 3D scan of the patient's healthy arm using a peel 3d scanner to obtain its mirror image. This was done so that the designed product ideally repeated the proportions of a healthy limb. The rest of the amputated arm was also scanned to achieve a comfortable and ergonomic fit for the prosthesis.
The team then proceeded to design the CAD model and develop the myoelectric prosthesis. Batteries, sensor cables and an artificial hand were integrated with the fabricated forearm. The prosthesis itself was designed in CAD and printed on a 3D printer. HP Jet Fusion technology was used to print various components of the forearm. After manufacturing, all parts were finished and painted.
The use of 3D scanning and 3D printing guarantees not only the correct fit of the fixture, but also allows complete freedom of movement. A new approach to prosthesis design allows professionals to develop solutions that are lightweight and highly customizable. Did you know that 3D printed parts are 20% lighter than their carbon or fiberglass counterparts? Such products also have the necessary rigidity, hardness and durability.
Later, this innovative prosthesis was combined with the BeBionic hand, one of the most advanced bionic limbs, and a state-of-the-art myoelectric forearm and hand was custom-made. Gauthier's case is a great example of the innovative use of 3D measurement and 3D printing technologies.
Prosthetics of the hip joint
Institute of Traumatology and Orthopedics. R.R. Vreden together with LETI (St. Petersburg) worked on the creation and 3D printing of a titanium hip prosthesis. Based on the CT scan, a plastic model of the bone was created. The next stage is the design of the implant and adjustments for its positioning on the bone. Then, after the doctors planned the operation on a mock-up, the prosthesis was 3D printed. The patient, whose hip joint was almost destroyed as a result of an injury, got to his feet.
Printing the cornea
In 2018, British scientists were able to 3D print the cornea for the first time. Now they can use 3D printing to make the cornea from stromal cells. They also created a special bio-ink, which consists of corneal stroma cells from a living donor. It also contains collagen and alginates. Protein is the basis. By placing the resulting substance in the printer, a healthy cornea was printed in 10 minutes, which was viable for more than a week.
This development is very important for the whole world, as this part of the eye can suffer from a burn, infection or injury at any time. Millions of people around the world are in need of a transplant, and cannot afford it, as there is not enough real donor material.
The technology needs clinical trials, but there is hope for mass printing of the cornea.
3D printed vessel models
Blood vessel and aneurysm models / Photo: ProtoFab The most important role for complete embolization of an intracranial aneurysm is played by the stable position of the microcatheter and its optimal shape. Using a 3D printer, models of a blood vessel and aneurysm can be printed, which will help the surgeon better understand the anatomical structure. Proper molding of a microcatheter for intracranial aneurysms is complex and requires extensive training for clinicians new to this technique. For a visual demonstration of blood vessels and aneurysms, a life-size 3D printed model can be used.
Compared to ABS vascular models, silicone models more closely match human blood vessels. 3D printing allows you to "copy" the complex geometry of the heart of patients with cerebrovascular diseases and instantly transfer information to software.
Printed surgical guide / Photo: ProtoFabAdditive manufacturing of guides
X-rays are traditionally used for osteotomy planning. However, 2D images do not reflect the actual state of the bones. In this regard, 60% of operations do not give a positive result. 3D patterns printed by Materialise will help solve this problem. These templates are inexpensive to produce and are available to all patients.
October 26, 2019 iQB Technologies and our partner TWIZE took part in the medical conference "Live arthroscopic surgery of the hip joint" at the State Clinical Hospital named after V.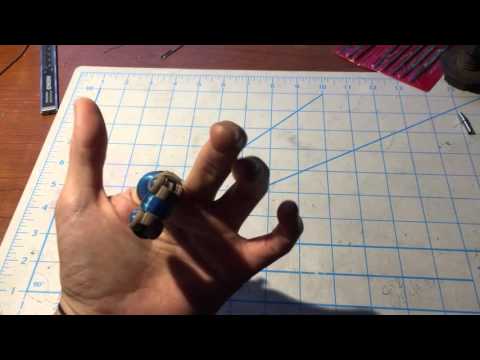
The future of 3D modeling
The innovations described in this article improve the reliability of operations, save time, reduce production costs and the cost of end products, and most importantly, improve and extend the life of patients.
In recent years, there has been a growing focus on 3D printing in the medical field and its benefits of high precision, productivity and customization. Along with the improvement of 3D equipment, active work is underway to create new materials for medicine. Using additive technologies, it will be possible, for example, to directly print ceramic products, as well as to create one-piece dentures, including teeth and gums, from biocompatible materials.
In 2019, Israeli scientists for the first time created a human heart with blood vessels and cells on a 3D printer. It was made in miniature, but the same technology could be used to print a regular-sized heart, the researchers said.
The direction of modern medicine, which is associated with a breakthrough in the treatment of diseases and pathologies in the foreseeable future - 3D printing of tissues, blood vessels and organs, or 3D bioprinting. Leading scientific and medical centers are developing new technologies and conducting clinical research in this area.
Advances in additive and biomedical technologies will contribute to the development of bionic modeling and 3D printing of tissues and organs, which will save the health and save the lives of a huge number of people.
Helping the IT industry during the coronavirus pandemic
Many companies are supporting medical institutions during the COVID-19 pandemic. Suppliers of medical equipment cannot cope with the load, especially when it comes to protective equipment (respirators, masks, screens).