3D printed esc cover
3D Printed Parts - 3D Printing
Skip to ContentFilter By:
Black (63) Blue (8) Caramel (1) Fluorescent Yellow (1) Gold (4) Gray (1) Green (11) Orange (5) Pink (1) Purple (2) Red (13) Titanium (4) White (6) Yellow (6)
Manufacturer
AstroX (1) BETAFPV (2) Brain3D (86) Diatone (8) Ethix (1) Flywoo (9) GetFPV Affiliate (1) Great 3D (1) Happymodel (5) HOM FPV (1) iFlight (10) ImmersionRC (1) Lumenier (10) Madcase (1) PIRAT (1) RunCam (1) Shen Drones (3) SpeedyBee (4) StanFPV (2) Team BlackSheep (1) XHover (6)
Receiver Protocol
Analog (1) DJI (11)
Antenna Connector / Length
SMA (1)
Voltage / Cell Count
14. 8 Volt (4 Cell) (153)
Sort Featured Mounting Pattern New Best Sellers Most Viewed Biggest Saving Price: low to high Price: high to low Reviews Count
View as Grid List
Page
- You're currently reading page 1
- Page 2
- Page 3
- Page 4
- Page 5
- Page
Show
20 40 60 100
per page
of 155
Loyalty Program
Earn 'Crash Cash' loyalty rewards to redeem towards your next purchase!
Create An Account
Discounts & Coupons
Check out our landing hub for all GetFPV promotions, discounts, and coupons!
Learn More
Stay Connected
Enter your e-mail to get exclusive deals and stand a chance to win monthly FREE products!
Email Address
Live Chat
Check Order Status
Same Day Shipping
Customer Support
Mon - Fri: 9:00am - 6:00pm ESTsupport@getfpv.
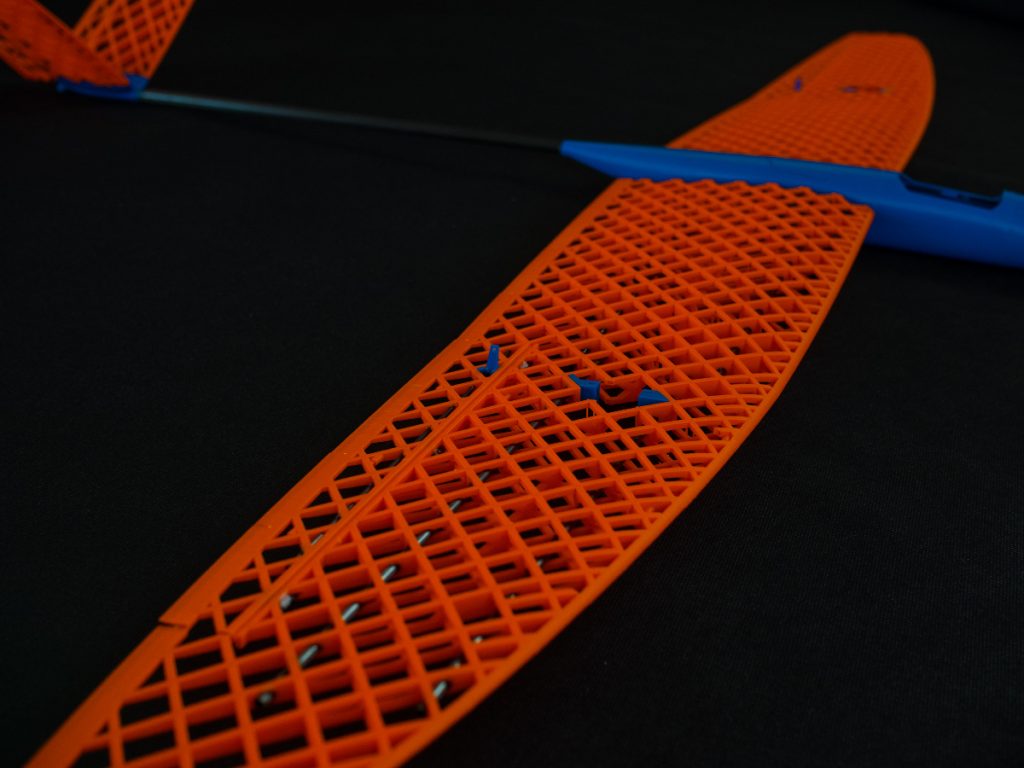
Need Help?
- Technical Support
- Order Support
- Check Order Status
- FAQ
- Contact Us
Store & Shipping
- Loyalty Program
- Drone Brands
- Discounts and Coupons
- Reseller Catalog
- FREE SHIPPING on most orders $99+
- Local Curbside Pickup
- Shipping Tips
- Return Policy
Shop Top Categories
- Drone Bundles
- FPV Equipment
- Drone Frames
- Electronics
- Motors
- Batteries / Chargers
- Radios
- Propellers
More GetFPV
- GetFPV Learn
- GetFPV Benefits
- GetFPV Distribution
- FPV Crate
- FPV Clearance
- Career Opportunities
Connect
- Newsletter Sign-Up
- Text Message Sign-Up
- YouTube
- AUVSI
- Clubs, TSA, STEMS
© 2022 GetFPV LLC. All Rights Reserved. | Terms & Conditions | Privacy Policy | Site Map
▷ esc case 3d models 【 STLFinder 】
ESC Case
thingiverse
Esc enclosure based on Boosted model from emancarrilo
Multicopter ESC case
thingiverse
Multicopter ESC case
electric skateboard esc case
thingiverse
electric skateboard esc case
ESK8 ESC case
thingiverse
ESC case for FSESC 4. 12
Castle Creations ESC case
thingiverse
Castle Creations Phoenix Ice80HV ESC case
PennyBoard Dual ESC Case
thingiverse
This is a Dual ESC Case for weird looking square esc's. ...fits max: 165x75x65mm
YGE 90HV ESC case
thingiverse
YGE 90HV ESC case. included step file for remix and fixing. ...
Plush 40a ESC Case
thingiverse
This is my standalone 40a Plush ESC case. This will not only provide an easy way to mount your ESC, but also adds a good amount of protection. There are 2 versions of the standalone case, with and without a heatsink. There is also one that mounts...
FocBox ESC case V2
thingiverse
ESC case for FocBox Unity you can fit a StormCore but mounting will depend and be very tight i used 35mm round 3M stand offs pressed in gasket and Test spacer should be printed with TPU i have 3 versions of the top plate one for xt90 loop key and...
Diatone 302X ESC Case
thingiverse
This case cradles the ESC like a glove and provides shielding between the ESC and inductive CF unlike most ESC covers which are simply hollowed out and require double sided tape. The interior cavity is designed for the 302X without heatshrink. The...
APD 120a ESC Case
thingiverse
Case for APD 120a ESC. ... -ESC clips into print (no double sided tape needed) -Top plate covers power leads -Holes through sides for Zip-ties
ESC case skateboard
thingiverse
... button. The connection holes in the top have to be drilled At first I put the electronicsboard in the box (photo open case) but then the cooling plate is at the wrong side. ...Later I put the electronicsboard to the top plate (photo closed case).
Crawlmaster ESC Case
thingiverse
This little box clips together, and houses your Holmes Hobbies Crawlmaster ESC. ...There's enough room in there for a Castle BEC as well, provided you shrinkwrap the two together.
Multicopter ESC case Free 3D print model
cgtrader
Multicopter ESC case
ESC case for skywalker 20A V2.0
thingiverse
ESC case for skywalker 20A. ...With the wires coming from the side.
ESC-case for Amax freestyle 10 frame
thingiverse
I´ve created an ESC-case for the 8mm arms of the Amax freestyle 10 frame and the Furhling32 32Bit 35A ESC. ...Some other ESC´s will fit too if they ar not bigger.
Super Race Bee 30A ESC Case
thingiverse
ESC case for the Super Racer Bee 30A ESC. Simply split open to install ESC and secure case with single zip tie. No double sided tape required. The case has been designed to fit the ESC without heatshrink. Print Settings Printer Brand: ...
BLHeli ESC Case with Clips
thingiverse
Protection case for BLHeli ESCs with clips. ...This case is made for the ZMR frame.
ESC Case for Afro 12A
thingiverse
I removed the wires from my ESC's (I wouldn't recommend this, bullet connectors were hard to align) With this case you may also be able to add a small heat sink pad (one of those squishy ones) to the MOSFETs The fit may be a little tight, so some. ..
ESC Case Plug
grabcad
3D printed TPU plug for empty powert button socket
littebee esc case v1
thingiverse
real basic nothing fancy if you have a problem with the design let me know what happened and where it failed and i'll try fix
S800 ESC 80A case kit
thingiverse
S800 esc case kit ABS 100% infill
beerotor 210 ESC protect case
thingiverse
beerotor 210 ESC protect case
DYS Aria esc protector case
thingiverse
DYS Aria esc protector. Case. TPU recomended. ...Esc link: https://goo.gl/wdFFGi
Quickrun 1080 ESC Case Mount Holder
thingiverse
This a mount for the quickrun ESC
Electric Skateboard ESC Case - 5" x 4"
thingiverse
ESC enclosure for electric longboard. ... Dimensions- 4" x 5"
PennyBoard Dual LiPo&ESC Case v3.0
thingiverse
Made for dual lipo 22.2v 22ah batteries + escs
Esc/WiiCeiver Case/Cover
thingiverse
Esc/Wiiceiver Cover/Case to house a FVT 120A esc and a wiiceiver. Bit of a basic design but it works and looks alright. Added the .dwg of it and a .stl feel free to customize. Print Settings Printer Brand: Up! ... ...
esc skateboard case 2021
thingiverse
I reccomend screwing the esc on the board itself, rather than sticking it on the bottom of the case. Printing: I reccomend atleast 2 walls with a thickness of 0.8mm, but more would be a bit stronger (using pla). INFILL USE ATLEAST 40%, less and...
DDW RC MG995 Servo ESC Switch Case
thingiverse
DarkDragonWing Website ○ YouTube ○ Facebook ○ Online Store ○ Product Recommendations Description Software: Cura Layer Height: 0. 2mm Infill Density: 75% Materials: PLA Wall Thickness: 4mm Top/Bottom Thickness: Same as Wall Thickness Filter Out Tiny...
Free 3D file 3d printer power supply cover 120mm version・3D printer model to download・Cults
anycubic photon mono 4k stock mount
Free
handle cz 97b
Free
Futaba steering wheel adapter
Free
Clock Wall Mount
Free
Yokomo YD-2 Rear Mount ESC
Free
junction box for square tube table
Free
Delta Bed Clamp
Free
Wall mount for wire basket
Free
The best files for 3D printers in the Tools category
Compliant Clip
Free
Downward Blower Duct for Replicator 2
Free
Beer Bottle Lid
Free
Cyclone dust separator
Free
Case for whiteboard markers - sharpie pen box
1. 39 €
Liquid propellant rocket engine, 1st supersonic level flight, X-1, 1947 year
10.18 €
drip valve
Free
Bestsellers in the Tools category
Ender 3 Briss fang Gen2, red lizard, spider, nf crazy, dragonfly, etc.
€1.87
UNIVERSAL BED LEVELING INDICATOR FOR PRACTICALLY ALL PRINTERS
3,19 €
Printer boxes for Ikea Lack Table
1.99 €
Armadillo - flexible wire conduit
€1.78 -thirty% 1.25 €
Tool holder for 3D printer V3.0
1.12 €
Rapid loader for magazine SIG Sauer P365/XL and P226 9 mm
2.04 €
Filament shielding
2. 95 €
Housing FLSUN SR
8,50 €
Filamentmeter
2,80 €
Fire hydrant storage container
2.04 €
Quick print paint bottle holder (6 sizes)
2.88 €
well designed: Hemera 9 fan duct0004
2.50 €
Ender 3, 3 V2, 3 pro, 3 max, dual 40mm axial fan hot end duct / fang. CR-10, Micro Swiss direct drive and bowden compatible. No support required for printing
1.68 €
AIR DUCT 5015 ENDER 3 S1/PRO V3
2.46 €
GEAR AND DRIVE
3.56 €
Business Card Embossing System
3 €
Do you want to support Cults?
Do you like Cults and want to help us continue our journey on our own ? Please note that we are a small team of 3 people, so supporting us in maintaining activities and creating future developments is very easy. Here are 4 solutions available to everyone:
-
AD: Disable your AdBlock banner blocker and click on our banner ads.
-
AFFILIATION: Shop online with our affiliate links here Amazon.
-
DONATIONS: If you want, you can donate via PayPal here.
-
* INVITE FRIENDS: * Invite your friends, discover the platform and great 3D files shared by the community!
Problems, defects, 3D printing errors and solutions
Often during the operation of a 3D printer, problems may arise due to which defects appear on the finished model. Or instead of a neat product, plastic noodles suddenly appear on the table.
In fact, the causes of defects can be conditionally divided into 2 types - these are physical and software.
Physical ones are those that arise due to problems with the mechanics or any other causes that can be eliminated physically. These include problems with printer mechanisms (belt tension, backlash), clogged or deformed nozzle, incorrect table geometry, etc.
Software - these are defects that occur due to incorrect slicer settings or, less often, errors in the printer firmware. For example, incorrectly selected print speed, retract settings, incorrectly selected temperature for plastic, etc.
Very rarely, the problem may lie in the wrong or “flying” printer firmware (although usually the printer simply will not start then), overheating of some boards during printing, etc. These are rather special cases, so we will not consider them.
Model peels off or does not stick to platen
This is the most common 3D printing problem. Every 3D printer has had a case when the first layer treacherously rolls, clinging to the extruder, or the most offensive - when it tears off a partially printed model from the table. The first layer must stick tightly otherwise nothing will be printed.
Gap between table and nozzle 9 too large0200
This is the most common reason. You just need to set the correct gap between the table and the nozzle.
Modern printers often use an auto-calibration (auto-leveling) table system or an auxiliary table leveling program. To calibrate such printers, use the instructions. If there is no manual, it can be downloaded from the manufacturer's website.
If you have a simple printer without auto-calibration, a self-assembly or KIT kit, use a probe or a piece of paper folded in half to calibrate. The probe should be slightly pressed against the table by the nozzle. Before calibration, the table and extruder must be heated. Align the table surface over each adjustment screw (there may be 3 or 4) in turn, and only then check the center point.
If you're having trouble getting your table surface perfectly level, try raft printing. Raft is a thick substrate in several layers that is printed under the model.
It will help smooth out the slight curvature of the table.
A small cheat sheet to determine the correct gap on the first layer
Plastic with poor adhesion
Some types of plastic, due to various reasons, such as large shrinkage, do not adhere well to the surface of the printing platform. In this case, try using stickers or special 3D adhesives to improve adhesion between the table and the first layer of plastic.
In the early days of 3D printing, there were experiments with different homemade 3D adhesive recipes. ABS diluted in acetone, BF glue, sugar syrup and even beer. Some experiments have been successful. Until now, some enthusiasts use some types of hairspray or glue sticks as 3D glue. But still they are inferior in their properties to industrial 3D adhesives.
Some types of high temperature plastics with a high percentage of shrinkage (ABS, Nylon, etc.) may peel off the table during printing. This is due to uneven cooling and “compression” of the model (the lower layers have already cooled down, but the upper ones have not yet). For such plastics, it is imperative to use a 3D printer with a heated table and a closed case.
Plastic temperature too low
The hotter the plastic is when it exits the nozzle, the better it will adhere to the print bed. It is better to print the first 5-10 layers at a higher temperature (+ 5-10 degrees) and turn off the blower fan.
Wrong first layer settings (speed and thickness)
A thicker layer sticks easier, so the standard first layer is 0.3mm thick. With an increase in print speed, the heating block may simply not have time to heat the plastic to the desired temperature and it will stick to the table worse. Before printing, check the speed and thickness settings of the first layer in the slicer.
A lot depends on how the 3D printer prints the first layer.
Try to control the printing of the first layer and only then leave the printer to work alone.
Plastic does not choke out of the nozzle
The printer has already begun to print, but the print table remains empty. Or part of the model did not print.
Clogged nozzle
In 3D printing, a nozzle is a consumable. The nozzles are clogged or worn out (frequency depends on the type of plastic). The simplest thing is to replace the nozzle. But if there was no spare at hand, you can try to clean the old one. To do this, there is a whole set of thin needles. Or you can heat a clogged nozzle above the melting point of the plastic and “burn out” the blockage. But later it is still better to replace the nozzle.
Low temperature nozzle
You need to increase the temperature of the extruder in the slicer settings or check the thermistor and heating block. Sometimes the thermistor may not read the temperature correctly due to a malfunction or incorrect 3D printer firmware settings.
If the problem occurs after replacing the thermistor - contact the manufacturer or read articles about PID tuning.
Empty extruder
As the extruder heats up, plastic begins to ooze out of the nozzle. Because of this, the extruder may start printing half empty. Because of this, part of the first layer is not printed. You can push the plastic manually by simply pushing the bar into the nozzle. Or solve this problem programmatically - in the slicer, add a contour print around the model (one line).
Some manufacturers and 3D enthusiasts add a line print on the edge of the table at the beginning of each GCode. This is done so that there is plastic in the nozzle by the time the model is printed.
Feed mechanism does not push through plastic
The plastic pushes the feed mechanism to the extruder - a motor with a special pulley put on the shaft. If for some reason the plastic is not pushed through (nozzle clogged, extruder temperature low, etc. ), then the pulley “gnaws” through the bar. You need to push the plastic bar with your hands or cut off the damaged piece.
Elephant foot
The first layers of the model are wider and protrude beyond the boundaries of the model. This is due to the fact that the upper layers put pressure on the first ones that have not yet cooled down and flatten them.
High table temperature
Due to the too high temperature of the table, the lower layers remain soft for a long time. Try lowering the table temperature. It is better to reduce gradually (in increments of 5 degrees). You can try to turn on the blower when printing the first layers.
Small gap between nozzle and platen
If, when printing the first layer, the nozzle is too close to the table, then excess plastic will be forced out. After a few coats, this will not be as noticeable, but can lead to the effect of an “elephant's foot”.
Plastic re-extrusion
When too much material is squeezed out of the nozzle, the walls of the model are not smooth, but bumpy, with sagging.
The solution is software - in the settings of the slicer, you need to set the material feed rate (fluidity) to a lower value. The average value is 95-98%.
It is worth checking the diameter of the rod. If its size is greater than 1.75, then the plastic will be squeezed out more than necessary.
Plastic underextrusion
The plastic is squeezed out too little, because of this, gaps may appear between the layer. The finished model will be fragile and fragile.
Wrong thread diameter
Check the filament diameter in the slicer settings. Sometimes, instead of the popular 1.75, the default is 2.85.
Incorrect feed rate settings
Check the fluidity settings in the slicer. The average should be 95-98%.
Clogged nozzle
Something could get into the nozzle and partially block the exit of the plastic. Visually, the plastic will choke from the nozzle, but in a smaller amount than necessary for printing.
Hairiness or cobwebs on finished model
Thin threads of plastic protrude from the outer wall of the model (most often on one side). The defect appears due to the flow of plastic from the nozzle during idle movement.
Insufficient retract
A retract is a slight pull of a plastic filament from an extruder. Due to the retract when the extruder is idle (from layer to layer or from model to model), heated plastic does not drip from the nozzle. For some flowable plastics (eg PETG) the speed and amount of retraction must be increased.
"Hairiness" can be easily removed by grinding or cutting off the threads with a sharp scalpel.
High temperature extruder
The higher the extruder temperature, the more fluid the plastic becomes. It is important to find a balance so that the plastic is not too liquid and sticks well in layers.
In the selection of the optimal extruder temperature, a test model - a tower - helps a lot. It clearly shows how plastic behaves when printed at different temperatures.
.
Temperature test
Top "perforated" or uneven
The top of the model is bumpy or with holes. The problem may arise if the top of the model is flat. For example, like a cube.
Insufficient airflow
When printing the top plane (cover), the plastic does not have time to cool down and remains too liquid. Because of this, the threads are torn and holes are formed. Increase the fan speed on the last layers.
Few top layers
The top of the print may be too thin and deform as a result. Check slicer settings. The number of upper layers is not recommended to be set less than 6.
Low percentage of filling
If the infill percentage is too low, then the top layer will simply have nothing to rely on. Increase the fill percentage in the slicer settings.
Model deformation
Some parts of the model seem to have melted in some places or on one side. The problem most often occurs when printing with PLA plastic. The defect appears due to the fact that the plastic does not have time to cool and deforms.
Insufficient airflow model
Turn the fans on to maximum. If their power is not enough (in some printers, the fan is located only on one side), you can put a regular desktop fan and direct it to the 3D printer table.
Small model
Small models are difficult to blow well. Try to print small items alongside larger ones, or place several identical models in different corners of the table. So the plastic will have more time to cool.
Layer offset
Layers shift along the x or y axis during printing.
Print head jam
Turn off the printer and try to move the extruder along the x and y axes with your hands. The extruder must move freely. If there are jams, check the mechanics of the printer. Bearing wear or the curvature of the shafts may be to blame.
Electronics overheating
Sometimes electronics problems can be to blame for misaligned layers. The most common cause is overheating of the drivers or too low current exposed to them.
Table top is loose
This is most often seen in 3D printers with glass. During printing, the nozzle may hit the model and move the glass slightly. Before printing, check if the glass or other printing surface is well fixed on the heating table.
Skip layers
Small holes are visible on the print, or the shell of the model is not continuous.
Teflon tube deformed
There are 2 types of thermal barriers - all-metal and with a Teflon tube. If overheated, the Teflon tube may deform. Plastic will pass through it, but in a smaller amount.
Low extruder temperature or high print speed
If the extruder is not heated enough, then the plastic will not be liquid enough and simply will not have time to be forced through the nozzle. The higher the print speed, the higher the extruder temperature should be.
Sometimes the outer walls print well, but the infill is “torn”. In this case, slow down the infill print speed in the slicer.
Model bundle
Cracks form on the surface of the printout during or after printing. Cracks can be large or very small. Most often, this problem occurs with plastics with a high percentage of shrinkage - ABS or Nylon.
Sudden temperature difference (if model delaminates during printing)
With a sharp temperature difference (for example, a draft), part of the model cools down faster. This leads to uneven shrinkage and incorrect distribution of internal stress. For plastics with low shrinkage, this is not critical. But if the shrinkage percentage is more than a few percent, the model may burst in layers.
For printing with such plastics, it is recommended to use a printer with a closed housing. If this is not possible, try to avoid drafts and sudden temperature changes in the room where the 3D printer prints as much as possible.
Print temperature
Due to too low printing temperatures, the layers may not “stick” well to each other. Raise the print temperature in the slicer settings.
Hardening (if the model cracks after printing)
Sometimes cracks appear on the model a few days after printing. This is due to uneven distribution of internal stress after cooling. You can try to “harden” the finished product.
For hardening, the model is placed, for example, in an oven, and heated to the softening temperature of the plastic. After that, the heating is turned off and the oven is left to cool slowly with the model inside. Due to this, the stress inside the print is distributed more evenly. But accuracy is very important in this method - if you make a little mistake with the temperature, the finished product can “float”.
Ringing
In places where the extruder changed direction, ripples are visible. Most often it looks like a shadow around the “sharp” protruding elements of the model.
Mechanical problems
Sometimes the problem occurs due to extruder play. Check if the extruder mount to the rails is loose. Be sure to check the tension of all belts.
High print speed or high accelerations
Moving the extruder too fast can cause vibrations that cause ripples on the wall of the model. The lighter the weight of the extruder, the less noticeable the ripples will be. To get rid of ringing, simply reduce the print speed in the slicer settings.
Slots for thin-walled models (not solid shell)
The thin wall of the model is not solid, but consists of two thin walls with a narrow gap between them. This problem is often faced by fans of printing "cutting" for baking.
Left model with wall defect, right without
Wall thickness and nozzle diameter mismatch
If the wall thickness is 1 mm, and the nozzle diameter is 0.4, it turns out that for a solid wall, 2 nozzle passes are few, and 3 are already many. The result will depend on the slicer algorithm, but most often you will get 2 walls with a thin slot in the middle (the slicer cannot change the wall thickness). The solution to the problem may be a slight refinement of the 3D model or the use of a different slicer.
Algorithms for calculating 3D models are constantly being improved and refined, and now this problem is less common.
When modeling, take into account not only the thickness of the nozzle, but also the percentage of “overlapping” of lines on each other. If you have a nozzle with a diameter of 0.4 - make the wall in your model not 0.8, but 0.7 - 0.75.
Wrong model geometry
When instead of a circle you get an oval, and instead of a square you get a semblance of a rhombus.
The main reason is malfunctions in the mechanics of the printer. Be sure to check:
Belts
Check belt tension in x and y. Belts stretch over time and may need to be tightened or replaced. Each 3D printer has its own way of tightening the belt. If the belts are slightly stretched, you can tighten them with the help of a "spring".
Loose pulleys, etc.
Check if all bolts and nuts are tight. Are there backlashes. Pay special attention to tightening the pulleys located on the motors along the x and y axes.
Sagging of some parts of the model
Some parts are not printed, broken, or instead of a neat surface, a swollen plastic snot is obtained.
No support for overhangs
A 3D printer cannot print in the air, so if there are overhanging elements in the model, you need to set supports - supports. The slicer can set the necessary support itself, you need to check the appropriate box in the settings.
When printing with soluble support, you can set the gap between the model and support - 0. This will make the surface smoother. If the support material and the model are the same, you need to add a small gap. Otherwise, it will be difficult to separate the support from the model.
Split model
Sometimes the supports can take more plastic than the model. In this case, to save material and time, it will be more convenient to cut the model. If you have more than one 3D printer, then the model will print several times faster.
When cutting the model, you can leave grooves or mortgages so that the pieces of the model are connected without displacement.
Totals
In this article, we talked about the most popular 3D printing defects and how to solve them. Don't be intimidated by such a long list. Some problems are rare and you are unlikely to encounter them.
There is a list of problems that arise due to the design features of a 3D printer, so try to choose a printer that suits your needs. To do this, you need to understand what products and what material you need.