3D printed comforters
3d Bedding Set - Etsy.de
Etsy is no longer supporting older versions of your web browser in order to ensure that user data remains secure. Please update to the latest version.
Take full advantage of our site features by enabling JavaScript.
Find something memorable, join a community doing good.
(1,000+ relevant results)
Print Comforter Set – HIGBEDDING
Save $20
Quick view
HIG 3 Piece Bohemian Floral Print Comforter Set for Queen King Bed, Pastoral Style Lightweight Duvet Set for Bedroom Decor
Regular price $59. 99 Sale price $39.99
Save $30
Quick view
HIG Romantic Love Heart Print Comforter Set, 3 Piece Quilted Down Alternative Comforter with 2 Shams
Regular price $59.99 Sale price $29.99
Save $30
Quick view
HIG Geometric Print Comforter Set, Grid / Stars Pattern, 3 PCS Lightweight Quilted Comforter with Two Shams
Regular price $59.99 Sale price $29.99
Save $30
Quick view
HIG Animal Themed Print Comforter Set, Cow Pattern, 3 PCS Lightweight Quilted Comforter with Two Shams
Regular price $59.99 Sale price $29.99
Save $30
Quick view
HIG Botanical Themed Monstera Print Comforter Set, 3 PCS Lightweight Quilted Comforter with Two Shams
Regular price $59.99 Sale price $29. 99
Save $10
Quick view
3D Print Ball and Bat All Season Comforter Set-S27
Regular price $39.99 Sale price from $29.99
Save $10
Quick view
3D Print Basketball Fire All Season Comforter Set-S28
Regular price $39.99 Sale price from $29.99
Save $10
Quick view
3D Print Sunflower All Season Comforter Set-S29
Regular price $39.99 Sale price from $29.99
Save $24
Quick view
Puppy Print Down Alternative Lightweight All Season Comforter Set
Regular price $49.99 Sale price from $25.99
Save $24
Quick view
3D Reactive Print Starfish All Season Comforter Set Twin -S11
Regular price $49.99 Sale price $25. 99
Save $24
Quick view
3D Reactive Print Skull Flower All Season Comforter Set Twin -S9
Regular price $49.99 Sale price $25.99
Save $24
Quick view
3D Reactive Print Skull All Season Comforter Set Twin-S8
Regular price $49.99 Sale price $25.99
Save $24
Quick view
3D Reactive Print Owl All Season Comforter Set Twin -S7
Regular price $49.99 Sale price $25.99
Save $24
Quick view
3D Reactive Print Kitten All Season Comforter Set Twin -S5
Regular price $49.99 Sale price $25.99
Sold Out
Quick view
3D Print Galaxy All Season Comforter Set Twin Queen Size-S3
Regular price $49.99 Sale price from $39. 99
Save $24
Quick view
3D Reactive Print Elephant All Season Comforter Set Twin -S2
Regular price $49.99 Sale price $25.99
Save $24
Quick view
3D Reactive Print Sea Dolphin All Season Comforter Set Twin Queen Size-S1
Regular price $49.99 Sale price from $25.99
Save $24
Quick view
3D Reactive Print White Tiger All Season Comforter Set Twin - S14
Regular price $49.99 Sale price $25.99
Save $24
Quick view
3D Reactive Print Lion Head All Season Comforter Set Twin -P27
Regular price $49.99 Sale price $25.99
Galvanic coating of 3D printed models / Sudo Null IT News
Picture Jason Welsh youtube channel
With the spread of 3D printing, many fans have received unique opportunities, which, however, are limited by the properties of the material itself - the plastic base. In one of the previous articles, we talked about an interesting way to make metal castings from 3D printed models using metal melting in a conventional home microwave.
However, it is not always necessary to manufacture ultra-solid metal parts in complex ways, as there is a much simpler option ...
And this widely known method is electroplating! That is, a coating with metals dissolved in the form of salts in an electrolyte, when an electric current is passed through it.
The method is quite interesting, because with proper organization it allows you to deposit metals even on hard-to-reach parts of surfaces, and the do-it-yourselfer has at his disposal a relatively easy way to create any objects that look like metal.
This is especially true with the advent and widespread use of inexpensive photopolymer 3D printers, the print resolution of which makes it possible to create quite interesting “metal” figurines that an unknowing person can hardly distinguish. Especially if the figurines have voids to fill them with some kind of weighting agent, for example, hunting lead shot mixed with epoxy or other binder. nine0005
Caution: electroforming involves working with electricity and chemicals, which can be quite dangerous. All subsequent information is given for general development. The author does not call for anything and is not responsible for the result of any experiments, if you want to conduct them.
▍ General description
The process of electroforming is the movement of metal salt ions, since when they are dissolved in an electrolyte, they undergo electrolytic dissociation, that is, they turn into a set of ions with positive and negative charges. nine0005
For this process, it is necessary to lower two contacts (negative and positive) into the bath with salts dissolved in the electrolyte and connect them to the corresponding terminals of the power source:
Odnoralov
When an electric current appears on the contacts, the ions in the electrolyte begin to move: with a positive charge they move to the negative contact, with a negative charge - to the positive one. Coating occurs when applying voltages in the range from 1 to 5-6 volts. nine0005
In this case, pure metal is deposited on the negative contact, and an acid residue is released on the positive contact. The amount of metal deposited on the negative electrode is directly proportional to the amount of current that was used to deposit it. That is, to put it simply, many amperes deposit more metal in less time, and fewer amperes deposit less metal in more time.
But this is to say in very general terms, since you also need to take into account the surface area of \u200b\u200bthe part on which you want to deposit metal, since a large current for a small surface will damage the coating. There is a good table for this, which allows you to calculate the amount of deposited metal:
Picture from the book "Entertaining electroplating", N.V. Odnoralov
To calculate the amount of metal that will precipitate in a certain time, you need to take the value from the last column of the table and multiply it by the current strength and the electrolysis time.
For example, in the literature cited at the end of the article there is the following calculation:
1.186 x 8 x 3 = 28.464 g.
the following calculation is required: the amount obtained is divided by the density of the metal ( 8.9g/cu. see for copper) electrolytically deposited, as well as on the surface area. For example, if the surface area is 100 sq. cm (1 sq. dm), the resulting thickness of the metal film will be 0.31 mm. This is information from the literature and this approach can even be improved nowadays if your slicer, CAD or other 3D editor can calculate the surface area of a 3D model.
▍ Electrolyte and bath
As an electrolytic bath, it is best to use plastic, glass or ceramic containers. nine0005
The model for coating (cathode) and the second electrode (anode) are suspended in baths on hooks made of conductive wire in such a way that this suspension does not get into the electrolyte and does not corrode it.
Use a plate of the same metal as the second electrode to cover the 3D model.
In the process of galvanization, it is necessary that the parts to be coated with metal be turned to the metal plate (anode) with the largest side. However, this is not always possible, therefore, various tricks are used: more than one plate is used, hanging them from both sides of the part (a - surrounding plates, b - coated part):
Picture from the book "300 Practical Tips", V. G. Bastanov
Or, in general, they use a round container with curved plates (with - bent anode plates):
Picture from the book "300 Practical Tips", V G. Bastanov
In order for all the elements of the product to be coated to be properly connected to the electric current, additional electrodes are brought into recesses and other deep places.
One of the simplest and most affordable metals for coatings is copper. Therefore, it is necessary to purchase copper sulphate (looks like plastic bags with bright blue crystals), which can be bought in almost any department of stores working in the "Garden and vegetable garden" theme:
Picture markik.ru
Electrolyte is produced by dissolving copper sulphate in water, and for this it is desirable to use hot or warm water.
Then the resulting solution must be cooled, after which sulfuric acid is slowly poured into it in a thin stream to increase the electrical conductivity. In this case, the solution will be very hot, so you need to do it very slowly so that splashing does not occur, which can cause severe burns. As sulfuric acid, it is quite possible to use a regular battery electrolyte from an auto shop. In the process of mixing water and sulfuric acid, personal protective equipment must be used. nine0005
The required amount of copper sulphate is calculated from the ratio of 200-250 g of copper sulphate per liter of water. As water, it is desirable to use distilled water for automotive electrolytes (also sold in bottles in car dealerships). When selecting the amount of sulfuric acid in the electrolyte, one should be guided by an approximate ratio of 30-35 g of acid per liter of water.
To improve the quality of the resulting copper film, you can add alcohol at the rate of 8-10 g per liter, which will lead to precipitation of copper in a finer crystalline form, as well as an increase in its hardness and elasticity. nine0005
In general, exceeding the indicated values both in terms of acid content and alcohol content will lead to a deterioration in the quality of copper and an increase in its friability.
Electrolysis is usually carried out at a temperature of about 18-20 degrees, which, however, may increase when heated during the passage of current.
Over time, sludge will form at the bottom of the electrolytic bath, which must be periodically filtered, otherwise it will float in the electrolyte and be included in the metal structure, degrading its quality. nine0005
In the process of electrolysis, it is necessary to control the ongoing process, for which you can focus on the classic table of indicators: Odnoralov
And there is an interesting point here, which is that the result will be a copper matte finish.
Despite the above restrictions on the content of components, there is an interesting recipe on the net, practically tested by its author, where the content of components, in particular, sulfuric acid, is much higher than usual. However, the method allows obtaining copper glossy coatings. To do this, for each liter of water you should take: 200 g of copper sulfate, 180 g of sulfuric acid, 0.07 g of thiourea, 0.07 g of edible salt. nine0005
The process takes place at a current of 10-20 mA per sq. see
When studying the experiments of interested people, the author of the article paid special attention to the fact that do-it-yourselfers, as a rule, miss the use of chemical methods for creating gloss. Instead, at the final stage, they suffer, rubbing the resulting model with a velvet cloth with polishing paste (which, in principle, does not deny a similar approach here).
Often copper is used in electrolysis as a substrate for the deposition of subsequent, "more noble" metal coatings. This is necessary both for preliminary leveling of the surface so that the final coating looks more presentable, and because it is impossible to directly apply the final coating to the original surface due to the impossibility of strong adhesion to it. nine0005
There are many different recipes for creating metal coatings on the net, but half the success in this business is understanding the sequence of processes, as well as understanding the possibility and impossibility of applying certain metals to target surfaces. Therefore, the following formulations can be studied for yourself simply for informational purposes to understand which components are required to apply a particular coating and which you have the opportunity to get.
However, if you are interested in the appropriate coating, you need to study the accompanying technological process in more detail, since this is half the battle. In particular, as far as the author of this article is aware, chromic anhydride (used in chromium plating) is a strong carcinogen, so you should study the coating of interest to you very closely from different angles (in terms of technology) before taking it:
The numbers in the recipes shown above indicate the sequence of preparing the mixture, while mixing each component with 200-300 ml of water, after which the same amount of water and the next component in the list are added, etc., until the total amount of electrolyte reaches 1 l. nine0005
A detailed description of some of the plating technologies is given in the literature available at the end of the article.
▍ Surface degreasing
The classical technology of galvanic coating involves preliminary high-quality surface preparation, which consists in cleaning it from pollutants and degreasing. Usually the surface is cleaned of coarse contaminants using solvents and alcohols. Subsequently, the part is dipped in a hot solution of caustic soda dissolved in water (80-90 degrees), at the rate of 10-15 g per liter, after which the removed part is washed with running water. Such degreasing gives a good subsequent wetting of the parts with water, which is a marker of the absence of grease contamination.
By the way, as far as the author knows (at this point, a comment from chemists is required, not completely sure), ordinary household bathroom products, especially for cleaning heavy blockages, sold in black plastic bottles in the form of loose formulations, are predominantly caustic alkali (sodium or potassium). The chemical purity certainly leaves much to be desired, but at least they are quite affordable and are available in almost any store. nine0005
However, due to the low heat resistance of the photopolymer resin (of course, if you do not use a special, heat-resistant version of it that can withstand temperatures above 200 ⁰С), this method seems difficult to implement. Therefore, the following is most applicable: all operations with the finished printed part are carried out with gloves (removal of supports), after which the part is thoroughly washed in isopropyl alcohol.
Since the part is freshly printed, it must not contain any particular contaminants that may cause subsequent problems. nine0005
▍ Conductive coating
Since we are dealing with a 3D printed plastic part, it is natural that it does not conduct electricity. To give the surface of the part the properties of electrical conductivity, according to classical technology, it is rubbed using soft artistic brushes with finely ground lamellar graphite, which can even be used as a pencil lead.
But this is a classic method, and now there are simpler methods, one of which is the application of an aerosol coating using an airbrush (metal mixtures, in particular copper):
Or spray-on using Graphite 33 mix:
It is also possible to use pure graphite powder mixed with some binder, eg paint. The example below illustrates this well and also shows how presentable a simple copper plating can be:
some interesting thoughts about creating conductive surfaces. nine0005
Why did this idea come to mind: I remembered my childhood and the experience of smoking various surfaces with a candle or matches (not always socially approved :-)).
The author began to study this topic for realism in the field of "smoking 3D models", since, in theory, soot, which is carbon, should conduct electricity well!
As it turned out in the process of diving into the topic, alternative ways to create conductive surfaces are a kind of "Holy Grail" in the field of chemistry and there are quite active discussions on this issue in the relevant chemical forums. nine0005
If we try to summarize the results of these discussions, the most promising, from the point of view of chemists, are the following options:

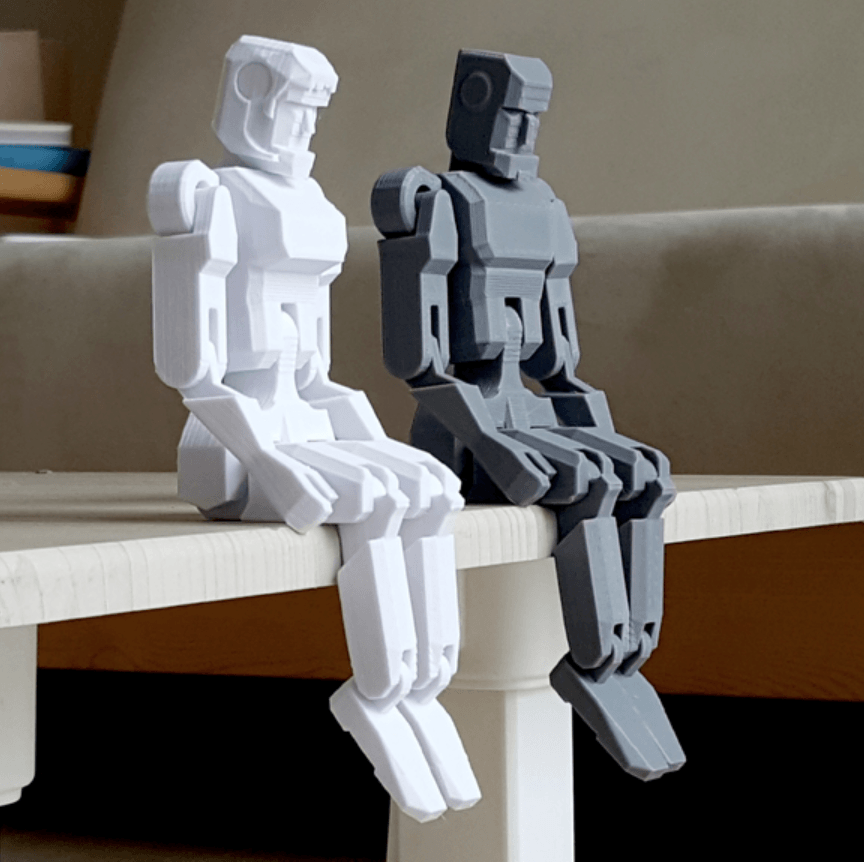
Summarizing all the smoking methods, it should be said that according to the results of a number of tests, everyone noted the highest degree of soot adhesion to the surface, which is explained by high-temperature fusion. All these methods are quite curious and deserve their attention, as they lead, if successful, to obtaining a cheap, fast and high-quality conductive coating.
The high temperature that occurs during the smoking process is not an insurmountable barrier, since it can act for a very short time if the flame is pressed almost close to the model, which will cause the predominantly low-temperature zone of the flame to interact with the model (usually has a blue color and is located in the center of the tongue flame, at its base). A side benefit of this treatment will be some melting of the surface roughness and their smoothing, which will eliminate the need for manual action (for example, using iron wool). nine0005
▍ Prospects?
Oddly enough, there are very few homemade products of this kind in RuNet, since 3D printing enthusiasts usually limit themselves to just coloring a printed 3D model, losing sight of the interesting possibilities that electroplating provides.
The use of electroforming also draws prospects never seen before: literally in May of this year, there was news that the developers from the Moscow Institute of Physics and Technology created an antenna for 5G and 6G using a new technology: the antenna was printed on a 3D printer, after which it was covered with metal using galvanization. This way of producing complex technical things seems quite interesting and allows any do-it-yourselfer to create quickly and easily even very complex designs, which, moreover, will be significantly cheaper than fully printed using 3D metal printers. nine0005
The topic of electroplating is quite large, and it is difficult to state all the subtleties within the framework of one article, so I recommend those who are interested to read the relevant chapters of the books below. They cover many issues in great detail, the approach to which has not lost its relevance, despite the years of publications.
Materials of books were used for writing the article:
1. "Entertaining electroplating", N.V. Odnoralov, Moscow, Enlightenment, 1965
2. "300 Practical Tips", V.G. Bastanov, - Moscow, Moscow Worker, 1986
Telegram channel with utility and cozy chat
3D-printed hydraulics and robberus printing with fiberglass
Subscribe to the author
sign up
I do not want
9000 9000 9000 Researchers at MIT's Information Technology and Artificial Intelligence Laboratory have released a video that demonstrates the operation of finished hydraulic assemblies created by printing multiple materials simultaneously on a 3D printer. The report will be presented at the ICRA 2016 conference. The authors of the work used a Stratasys Objet260 for printing with several nozzles through which materials with different characteristics are fed. With multiple nozzles, the printer can simultaneously print the rigid and elastic body parts of the hydraulic assembly and immediately fill the fluid, eliminating the need for subsequent refilling and pumping. So you can print pumps and pumps immediately assembled. nine0005
Scheme
In particular, the researchers managed to print a gear hydraulic machine. Also, using the printing of finished hydraulics, the authors printed a working six-legged walking robot, which is driven by a single electric motor.
The authors note that their method allows the creation of hydraulic systems that would be impossible to obtain by traditional installation of a separate system. In addition, this production method does not require any additional filling manipulations, since the liquid is placed inside already during the printing process. nine0005
In the published video, the authors demonstrate the performance of previously printed devices. Examples include a gear driven hydraulic machine, a hexapod driven by a single electric motor, and individual hydraulic actuators:
2 .
Learn more