3D print your own car
3D Print Your Car - Etsy.de
Etsy is no longer supporting older versions of your web browser in order to ensure that user data remains secure. Please update to the latest version.
Take full advantage of our site features by enabling JavaScript.
-
Loading
Click to zoom
Star Seller
Star Sellers have an outstanding track record for providing a great customer experience—they consistently earned 5-star reviews, shipped orders on time, and replied quickly to any messages they received.
| 191 sales |
5 out of 5 starsIn 15 carts
Price: from €196.11
Original Price: from €245.14
(20% Off)
Loading
Local taxes included (where applicable), plus shipping
Size
Select a size 4 inches (€196.11) 6 inches (€215.72) 8 inches (€294.17)
Please select a size
Please provide Make/Model of Car!
If you would like an inscription on the model, please write it here. ..
256
Star Seller. This seller consistently earned 5-star reviews, shipped on time, and replied quickly to any messages they received.
Listed on Jan 7, 2023
391 favorites
Report this item to Etsy
Choose a reason…There’s a problem with my orderIt uses my intellectual property without permissionI don’t think it meets Etsy’s policiesChoose a reason…
The first thing you should do is contact the seller directly.
If you’ve already done that, your item hasn’t arrived, or it’s not as described, you can report that to Etsy by opening a case.
Report a problem with an order
We take intellectual property concerns very seriously, but many of these problems can be resolved directly by the parties involved. We suggest contacting the seller directly to respectfully share your concerns.
If you’d like to file an allegation of infringement, you’ll need to follow the process described in our Copyright and Intellectual Property Policy.
Review how we define handmade, vintage and supplies
See a list of prohibited items and materials
Read our mature content policy
The item for sale is…not handmade
not vintage (20+ years)
not craft supplies
prohibited or that use prohibited materials
not properly labeled as mature content
Please choose a reason
Tell us more about how this item violates our policies.Tell us more about how this item violates our policies.
Here’s How to Get Started 3D Printing Your Own Car Accessories
3D printing is a big deal. It enables the average person to quickly whip up a fix for something around the house, a cool toy, some functional equipment for hobbies, or even rapidly prototype a new product for a business. You can see why it could easily become the next big appliance for homes and garages.
One area it’s bound to have a huge impact on is the car world. Over the past few weeks, my coworker Rob and I have been experimenting with 3D-printed accessories for the new Ford Maverick pickup with good results. I printed a heated/cooled cupholder. My partner Rob printed a dash cubby-mounted phone charger. (You all liked the charger most of all.) The implications of the stuff we designed go further than the parts themselves, though.
The point of our whole print-off wasn’t just so we could print some fun accessories. It was to explore the automotive potential of this now-commonplace technology in a vehicle built for makers. After having lived the life for roughly two weeks, we can confidently offer some tips for beginners looking to get into the hobby.
Starters
Before you embark on purchasing a 3D printer of any kind, even a very cheap one, you should really try to think about what you want to do with it. There are different types of printers, filaments, and resins beyond your wildest dreams—it can be overwhelming. When I started printing in high school, I didn’t have nearly as many options as hobbyists do today, and even trying to keep track of all the advancements today has been a lot for me.
Another thing is that, while the hobby doesn’t technically require computer-aided design skills, such proficiency is really necessary to design parts for your own use. When I got my first printer, I had no CAD skills. But I figured out pretty quickly that if I wanted to make stuff that would be useful to me personally, I needed to learn.
Luckily, there are a lot of options in terms of programs to use in order to design your own parts. Fusion360 is free for hobbyists and probably the most popular, but there is even web-based CAD software like TinkerCAD or OnShape that can provide the sorts of tools necessary to make custom odds and ends. I personally use Solidworks, which you either have to pay for or find some other way of obtaining. Keep in mind most CAD programs have free periods or student editions, so you can play around until you find one you like.
Be wary that many of these tools have rather steep learning curves. While TinkerCAD might be an easy way to jumpstart your 3D-printing journey, you’ll quickly find its limitations and end up venturing into Fusion360 or another piece of software. Don’t get overwhelmed, though, because plenty of great resources exist to learn 3D-modeling basics on YouTube, in Facebook groups, and elsewhere.
Types of Machines
Once you have some proficiency in a CAD program, you can get down to choosing a printer. There are a lot of variables here at play, but for automotive applications, it gets narrowed down a bit. There are two main types of printers you’ll encounter: Stereolithography (SLA) types and Fused Deposition Modeling (FDM) machines.
SLA machines use photosensitive resin to create parts that require some post-processing. SLAs are quickly coming into their own with growing print surfaces and a rapidly dropping cost of entry, but an FDM is typically where most people start.
A Prusa MK3S printer (FDM) vs a Prusa SL1S (SLA). Prusa ResearchFDM Printers
FDM printers melt a plastic filament and extrude it layer by layer in order to create a component—making things with the telltale layer lines you probably associate with 3D-printed parts at this point. They are cheap, extremely versatile, and work pretty well for automotive applications, depending on the filament and use case. Before we get into filaments, though, there are two main types of FDM machines to consider: open and enclosed.
Open printers have no enclosure around them, which limits them in terms of the sorts of filaments you can use. The reason why they’re popular is that they typically have larger build areas (which means larger possible prints) and are usually less expensive than their enclosed counterparts. If you want to get into printing as cheaply as possible, buy an open machine and work from there.
Prusa MK3S open printer. Prusa ResearchEnclosed machines are more capable in a few ways but also have their limitations. They are almost always more expensive, have smaller build areas for a given printer size, and can be heavy. They are, however, capable of printing a wider variety of filaments. If you’re worried about noise, an enclosed machine might also be a bit quieter.
That being said, you can often enclose an open printer using—you guessed it—3D-printed parts. In fact, a pair of cheap IKEA Lack tables and some acrylic can enclose most open printers for under $30.
Flashforge enclosed printer. Screengrab via YouTube | FlashforgeI use an enclosed FDM machine because I don't usually have a need to print large parts. I also use filaments that would warp in an open-air printer. Also, my printer is in my office, so noise is a concern. It really depends on what you want to do with your machine, though.
FDM printers also come in various “flavors” that control how their controls lay down plastic, the most popular of which are Cartesian and CoreXY. Cartesian printers, as the name might suggest, use Cartesian coordinates (X, Y, and Z) to move the hotend around the print bed in a linear fashion. They are cheap and easy to set up but aren't exactly fast to spit out a job. CoreXY, on the other hand, can crank up the speed without a reduction in print quality. They are often costlier and can often be cumbersome to set up, so these are often an “upgrade” for people who have already been in the 3D-printing world for some time.
The biggest challenge for most new printers choosing to go the FDM route is getting the first layer of molten plastic to stick to the print surface. It’s a problem not everyone faces, though, so keep that in mind. If you have this issue, you have to spend some time calibrating the bed. And in the case of a warped print surface, a correction device like Prusa’s SuperPINDA or a BLTouch can be used to offset small surface variations. And to further improve adhesion, some makers will choose to use borosilicate glass, while others will use a spring steel sheet with either a Polyetherimide (PEI) sticker on top or PEI-based powder coating.
Common Filaments
After picking up your first FDM printer, it’s time to choose the filament that you print with. There are going to be a lot of abbreviations here but stay with me, because there’s no need to get deeper into the weeds by spelling out the scientific names.
When it comes to automotive purposes, I would really stick to either ABS, PETG, ASA, or other temperature-resistant filaments. It’s most important you do not use PLA. PLA is a plant-based plastic that begins to soften at around 120 degrees Fahrenheit. Car interiors and underhood areas can regularly reach these temperatures. If you use it, do so knowing your parts will very likely deform over time because of this. PLA is also not an especially strong plastic. There are filaments known as PLA+ that claim to have greater capability, however, I’ve never used them and can’t speak to their quality.
ABS is a great material for a few reasons, but it tends to warp if the build area isn’t enclosed or if the bed isn’t kept around 110 degrees Celsius (230 degrees Fahrenheit). It’s important to make sure that you have a well-ventilated work area when printing ABS, as printing at high temperatures can give off Volatile Organic Compounds (VOCs).
Parts will also gradually degrade in direct sunlight. That being said, I use ABS parts for hydroponic projects, which receive a lot of direct sun as well as exposure to grow lamps, and I’ve never had that issue. Those are the primary reasons why people don’t like it. Otherwise, ABS parts have reasonably high-temperature resistance, chemical resistance, and, as a plus, they are easy to sand, cut, tap, whatever. They will also accept paint/primer with no problem.
If you buy an open machine, PETG is a good choice. I don’t use PETG, but I had friends in college who swore by it. It’s similar to ABS but a bit more flexible and easier to scratch. If you wanna make cheap parts, an open machine with PETG is the best option. That being said, PETG is also a difficult filament to dial in, as first layer adhesion can be a bit difficult and require more “squish” than other filaments. It also tends to stick to printer hotends easily, so a silicone sock is recommended to protect the printer’s delicate electronics.
Other Filaments
The holy grail of automotive filaments is probably nylon impregnated with very short strands of carbon fiber, commonly known as carbon fiber nylon. I’ve never printed it. You need a very hot nozzle, typically made out of tool steel, to extrude it for a long period of time for good results. You also need an enclosed build area. It will produce very strong and impressive-looking parts, but unless you find your ABS or PETG parts just aren’t up to the task in a constrained environment, you don’t have to get into it. Most machines require modifications to run, which is why I say this.
The other unique filament I will mention is TPU and others like it. These are basically flexible plastics that can be used to create things like gaskets, something I’ve done in the past for hydroponic setups. They aren’t perfect and typically require a lot of fine-tuning to print correctly, but the results are impressive once everything is all set up just right. I could imagine them being used for stuff like intake manifold gaskets that don’t get too hot, but definitely not stuff that touches an engine block directly. You may also want to select a printer that has a direct-drive extruder rather than a Bowden-equipped model if you plan to print a lot of TPU. Bowden extruders work by pushing filament through a long tube, which is a problem when the filament is flexible.
SLA Printers
Stereolithography machines use photosensitive resin to create parts. It’s a bit tougher to explain how they work. Basically, a vat full of resin with a transparent bottom sits on top of a high-intensity LCD screen. The LCD turns on and displays an image in black and white. This is the specific layer of the 3D model that it's printing. Similar to how an FDM printer prints one layer at a time, an SLA printer exposes a single layer to light before passing to the next.
Sitting above the transparent bottom of the resin vat is the build plate, which can move up or down. After keeping the screen on for anywhere from a few seconds to a few minutes, the resin in the areas where the image is displayed will harden, and the build plate lifts a fraction of a millimeter to provide space for another layer. This process is repeated dozens of times until an entire part has materialized. Once the parts are done, the excess resin needs to be washed off—typically in alcohol—and the parts have to be cured under a source of UV light for a period of time in order to get the resin to its full hardness.
SLA machines have a lot of advantages. They can print much thinner layers as compared to FDM machines and, if you adjust your settings correctly, they can make parts much faster, too. In fact, because a single exposure can fill the entire build plate, it takes the same amount of time to print, say, 25 parts as it does one part, so as long as they are arranged side-by-side. The downside is that, currently, SLA machines have relatively small build areas, the resin is reasonably expensive, and the post-processing is a lot for some people. Plus, the resin usually smells and makes a mess. I’m also curious about the impact the resin itself has on human health, as it doesn’t appear to be an area that’s been widely explored.
If you want to print primarily small interior trim pieces, these machines have a lot of potential. The sheer variety of resins out there is dizzying. There are water-washable resins, tough resins, flexible resins, clear resins, and all sorts of stuff.
Choosing a Machine, and Other Things to Get
I have both an SLA and an FDM printer. If you’re curious about which ones specifically, the FDM is a Flashforge Creator Pro 2 and the SLA is an Elegoo Saturn S. The former was around $650 and the latter was closer to $500. Rob has a Prusa MK3S, which runs $799 for a DIY kit, or $1,099 assembled. He also has an Elegoo Mars ($250) and a large-format Prusa XL on pre-order.
The bottom line is that you’ll get more bang for your buck with an FDM and the build areas will be consistently larger. If you need parts with only a basic level of detail and don’t want to deal with any post-processing, an FDM is your best bet.
SLA machines are better for smaller stuff that require a higher level of finish, like miniature figures. You can definitely do bigger parts, but you need more expensive machines and it takes a fair amount of trial and error. There is also post-processing involved and the resin is more expensive, but a lot of people see those things as acceptable tradeoffs. In the end, printers are cheap enough at this point that you can buy and experiment with both if you want. Good quality examples of either type can be had for around $400 each. Lower quality sorts that might take a bit of fiddling or have limited capabilities can be bought for around $200.
There are extra associated costs with both. It will take a while to find a good filament/resin that performs how you want it to. You should also get a wash/cure station if you buy a resin printer, which makes the whole process much easier. Some FDM filaments like ABS also have mildly toxic fumes when printing, so ventilation is necessary. In fact, I recommend using a vent for both machines. A simple duct booster and some drier hose is the easiest way to accomplish solid ventilation out a window.
For FDM machines, goods things to have are a wide selection of sandpaper to get a precise fit and finish on your final parts, several types of pliers to remove support material or pick off imperfections, a deburring tool, and a few metal spatulas/paint scrapers.
SLA machines are a different ballgame. Rubber gloves are a minimum. I also recommend a steady supply of paper towels, hand sanitizer, and a flexible build plate. The latter isn’t standard on most SLA machines but makes a big difference. Finally, get a set of digital calipers. If you want to design your own parts you need to be able to measure things.
The Rest Is Up to You
One thing we didn't touch on is workflow. Mostly, this is because it varies so much from vehicle to vehicle and even accessory to accessory.
For example, you wouldn't go about designing a mockup manifold the same way you would a chicken nugget holder. The best bit of advice to give any newcomer to 3D printing is to grab your calipers and get measuring. Look for problems to solve while you begin your 3D-printing journey, and if you're not proficient at modeling in CAD software, use the small problems you find to dig deep into that rabbit hole.
All in all, it's a very fun thing to get into, and hopefully, more manufacturers will follow in Ford's steps and open up their cars to makers.
Got a tip? Send us a note: [email protected]
5 ways 3D printing is changing the automotive industry / Sudo Null IT News
You can't buy a fully 3D printed car in a car dealership yet, but additive technologies have been used in car design for many years. Every year, especially in recent years, 3D printing is taking an increasingly important place at all stages of production. This is evidenced by the rapid growth of 3D printing market share in automotive manufacturing, which is projected to reach $2.5 billion by 2023. nine0005
For example, luxury car companies including Bentley, Porsche, BMW and Ferrari are using 3D printing to create custom car interior parts. GM, Volvo, Ford are using 3D printing to produce tooling to save money, improve designs and reduce delivery times. 3dprinting.com If the first 3D printers cost about $20,000, now you can find 3D equipment for $100. Now companies can, with the help of additive technologies, produce the necessary components directly at their own enterprises and not depend on suppliers. nine0005
With new materials, 3D printers can print high-precision, functional end parts. Additive technologies facilitate the production of custom products and increase productivity.
But this is only the beginning of the journey. Here are five key ways 3D printing is driving innovation in the automotive industry, from car design to production. Plus one bonus.
1. Changing the prototyping process
It was with the manufacture of prototypes that the use of 3D printers in the automotive industry began. 3D printed prototypes took much less time than traditional methods required.
Using Raise3D 3D printers and ideaMaker software, Crazy Grandpa Garage was able to automate the process of creating custom car parts. Production costs have been reduced by 50%, design reliability has improved significantly, and lead time has been reduced by 83%. The parts now come out very well fitted to the car. nine0005
Source: facebook.com
Using 3D printing, car designers can quickly prototype individual parts or assemblies, from interior detail to dashboard, or even full-size car models. Thanks to 3D prototyping, the initial idea quickly turns into a physical embodiment of the concept - a conceptual model. The concept can then be developed into full-featured, high-fidelity prototypes, and after several validation steps, mass production begins. For the automotive industry, getting through these steps quickly is vital, and the entire downtime of an automobile production line in just an hour is very costly for the company. nine0005
For example, the assembly plant of the US car manufacturer General Motors claims to have saved more than $300,000 by purchasing a 3D printer in 2016.
Ringbrothers designers and engineers are not dependent on third parties to implement laser stereolithography (SLA) in their facility. The cost is reduced, the development time is reduced. Source: formlabs.com
Hose for Eventuri BMW M4, Source: ultimaker.com
Traditional prototyping was time-consuming and costly, in part because the product went through more iterations. With 3D printing, you can create high-quality prototypes in one day and at a much lower cost. More examples.
The Ford Fiesta ST with 3D printed parts, ext. SEMA 2016, ultimaker.com
For example, General Motors has partnered with Autodesk to produce low cost, lightweight automotive parts using 3D printers. Tools, fixtures and fittings can now be produced at a fraction of the cost, according to Autodesk. For example, a 3D printed tool used to align engine and transmission ID numbers costs less than $3 at General Motors. A traditionally produced instrument will cost $3,000. In addition, downtime due to faulty tools can be significantly reduced as new tools are produced in-house. nine0005
2.
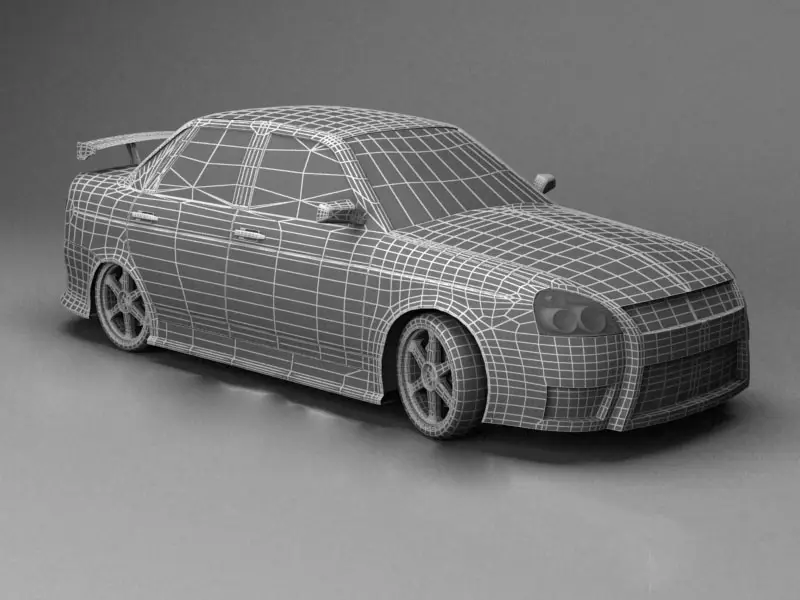
Daihatsu, Japan's oldest car manufacturer, launched a project in 2016 to customize its Copen model.
Source: 3dprint.com
In partnership with Stratasys, Daihatsu customers can design and order custom 3D printed panels for their front and rear bumpers with a choice of over 15 basic patterns in 10 different colors. nine0005
Source: 3dprint.com
In Europe, the BMW MINI brand also uses 3D printing to create personalized car parts. Since the beginning of 2018, MINI customers have been able to personalize various trim elements such as the instrument panel, LED treadplates and illuminated bumpers, as well as choose from different colors and textures. These parts are then 3D printed using a range of technologies from DLS Carbon to SLS.
Source: formlabs.com
Volkswagen Motorsport's I.D. R Pikes Peak is designed with over 2000 3D printed test parts.
Source amfg.ai
The use of 3D printers makes it possible to experiment in the development of non-standard designs, reduces the cost of their production. Long production processes for custom-made products are becoming much shorter.
Ringbrothers uses 3D printing to create customized end pieces such as ventilation grilles. Source: formlabs.com
Large companies are merging 3D printing technologies with traditional manufacturing methods. Volkswagen has recreated its iconic 1962 Microbus by replacing the petrol engine with a 120 hp electric one. The Type 20 concept electric minivan has received many improvements using 3D printed parts. These improvements include cast aluminum wheels. Even the wheel hubcaps, while looking like stamped steel, are actually printed on a Formlabs SLA 3D printer, then electroplated and polished. nine0005
Source: formlabs.com
Formlabs Form 2 SLA 3D printer specifications
Bentley has used cutting-edge metal 3D printer technology to produce a grille, side vents, door handles and exhaust pipes much more complex than those used on current production models.
Bentley used metal 3D printing to create intricate micron precision parts. Source: formlabs.com
Source: youtube.com
3D printing has also made it possible to create parts that could not be made in any other way.
Bugatti's monobloc brake caliper is a prime example. For some components, Bugatti would have preferred titanium due to its high performance, but processing this metal with traditional methods is expensive and difficult. 3D printing has allowed Bugatti to produce a titanium alloy brake caliper. Due to the thin walls, the caliper turned out to be very light - almost two times lighter than forged aluminum. At the same time, the strength of the 3D-printed monoblock is superior to that of aluminum. The 3D printed titanium monoblock has a tensile strength of 1250 N/mm2. This means that a force of just over 125 kg will be applied per square millimeter of this titanium alloy without tearing the material. The new titanium caliper is 41 cm long, 21 cm wide and 13.6 cm high and weighs only 2.9kg compared to currently used aluminum, which weighs 4.9 kg.
Source: youtube.com
The Bugatti brake monoblock is the industry's largest functional 3D printed titanium component for a car. Source: formlabs.com
3. Tool making
Various devices help to facilitate and speed up the production and assembly processes, improve the safety of workers. Automotive factories and component suppliers use a large number of non-standard tooling that is specifically designed and optimized for end use. As a result, a lot of non-standard equipment and tools are made, which increases production costs. nine0005
This 3D protective wheel disc was purchased for 800 euros but can now be printed for just 21 euros. Tool development time has been reduced from 56 to 10 days.
Source: ultimaker. com
Delegating custom tooling and fixtures to service providers who machine parts from solid metal or plastic stock can delay production by weeks.
For example, the development and prototype of a commutator motor using traditional manufacturing methods can take up to four months and cost about half a million dollars. Thanks to 3D printing, Ford was able to develop several variants in just 4 days and 99.4% cheaper - only $3,000.
Source: youtube.com
Additive technologies allow you to complete the task in a few hours and significantly reduce costs compared to ordering from a third-party enterprise. Since increasing the complexity of a 3D printed model does not incur additional costs, products can be better optimized for their application. New elastic materials for 3D printing in many cases allow you to print plastic parts instead of metal or create prototypes on a 3D printer to test the tool before using it in production
Gradually, the production of 3D printed accessories and tools is becoming one of the largest applications of additive technologies.
Pankl Racing Systems uses 3D printed fixtures to fasten workpieces to a conveyor belt. Source: formlabs.com
For example, Pankl Racing Systems uses a stack of multiple Formlabs SLA 3D printers to make critical manufacturing tools. The multi-stage production of parts for transmissions on automatic lathes requires a series of fixtures and tools designed for each specific part. nine0005
With the help of 3D printing, Pankl's engineers have reduced the production time for the aids by 90%, from 2-3 weeks to around 20 hours. Costs were also reduced by 80-90%, saving $150,000.
The transition to 3D printing has enabled Volkswagen Autoeuropa to cut tooling development costs by 91% and cut tooling times by 95%.
4. Troubleshooting spare parts
Spare parts have always been a problem for the automotive industry. The demand for them is either there or not, so the production of spare parts is not economically viable, and the storage of pre-fabricated replacement components is also costly. But if there are no repair parts available, difficulties arise and the main product becomes less valuable. nine0005
3D printing could solve the problem of parts in the automotive industry in many ways. The main factors are printed materials, which can match the characteristics of traditional materials used in parts and be cost-effective. There are prerequisites for this.
Using computer-aided design, drawings of all parts can be stored digitally, so there is no need to store the parts themselves. The parts needed by the client can be printed on a 3D printer right in the workshop. nine0005
Even obsolete parts whose blueprints have not survived can in principle be recreated by making a 3D scan of existing parts of this type and applying reverse engineering (reverse engineering). You can read more about this on our blog. Old projects can take on new life. There are many lovers of vintage cars, with the help of 3D printing it would be possible to create parts for them.
Ringbrother 3D printed the Cadillac emblem for a custom built old car. Source: formlabs.com
5. Production of standard parts
As 3D printers and materials for 3D printing become more affordable, a gradual transition to the production of mass-produced automotive parts using additive technologies is possible.
3D printing makes it possible to combine components into a single whole. Let's say there is a mechanism assembled from six or seven car parts that can be combined into one printed part. It will save time and assembly costs. With 3D printing, it is also possible to reduce the weight of the combined assembly, as a result, the car will use fuel more efficiently. nine0005
3D Systems has designed an advanced exhaust pipe for a sport bike. In the image below, you will see 20 sheet metal and hydroformed parts needed to assemble the original exhaust pipe. On the right is a monolithic exhaust pipe that does not require assembly, made using metal 3D printing.
Source designnews. com
The 3D printed tube was produced using Grade23 titanium in just 23 hours, compared to three weeks for traditional production. Design development time reduced from 6 weeks to 6 days. Additive manufacturing also eliminates the need for tooling, fixtures, multiple welding and multiple inspections. nine0005
Geometry optimization has reduced the amount of material needed for maximum productivity. All elements of the original exhaust pipe are incorporated into the new design and, when printed with a typical wall thickness of 0.5mm, the 3D printed exhaust pipe is about 25% lighter than the original one.
A wide range of 3D printing materials is starting to meet the requirements of various vehicle components. Since additive methods reduce costs compared to traditional methods (such as molding and injection molding), it makes a lot of sense from a production and financial point of view to further introduce 3D printing into the production of basic parts. nine0005
Volkswagen, one of the world's largest and most innovative car manufacturers, is using an HP Metal Jet 3D printer to produce high-performance functional parts with special design requirements, such as shift knobs and mirror mounts. Volkswagen's long-term plans to work with HP include accelerating the production of mass-customized parts such as key rings and exterior nameplates.
Source: youtube.com
+1. 3D printed cars
While 3D-printed cars have yet to hit the market, there are some interesting designs and concepts that can suggest a possible direction for the automotive industry.
Light Cocoon . German engineering firm EDAG was clearly inspired by nature to create the 3D printed supporting structure of the Light Cocoon concept car. The frame resembles the veins of a tree leaf or its branch. Despite the fact that the design of the EDAG took less material than a conventional frame, all the strength requirements for structurally significant components are met. Outside, the case is covered with a lightweight and durable waterproof fabric. nine0005
The cover protects the EDAG Light Cocoon from bad weather and gives the car a unique personality. Source: formlabs.com
Blade . Blade ("Blade") announced as "the world's first 3D-printed supercar." It meets supercar standards but is made from inexpensive materials: carbon fiber tubes and aluminum rods, combined with 3D printed metal parts. Blade turned out to be very light and does not take long to assemble. nine0005
The world's first 3D printed Blade supercar. Source: formlabs.com
Strati . The American company Local Motors 3D printed and assembled the Strati electric car right at the exhibition stand, in just 44 hours. Most of the components were printed - the body, seats, interior parts. A car is made up of less than 50 assemblies, far fewer than the thousands of parts that go into a traditional car. The company intends to reduce the print time to 10 hours. nine0005
The Strati from Local Motors consists of less than 50 individual parts*. Source: formlabs.com
LSEV. Developed by the Italian company XEV, the LSEV could be the first in the 3D printed electric vehicle market when it goes on sale. The 3D printed chassis, seats, windshield and all visible parts of the LSEV. Thanks to the active use of 3D printing, the number of components was reduced from 2000 to just 57, resulting in a very lightweight design. The electric car weighs only 450 kg. nine0005
The LSEV is the first 3D printed electric vehicle to hit the market in 2020. Source: formlabs.com
While most of these and many other 3D printed car projects remain at the concept stage, the extent to which 3D printing has penetrated various areas of the automotive industry is striking. In some cases, additive technologies provide new opportunities for design and production, in others they reduce production costs and save time. nine0005
See also:
3D printer and CNC race car manufacturing
3D scanning of cars in tuning and repair
The world's first 3D printed car in action
Archive
Subscribe 029Don't want to
1
There are so many different projects in the world of 3D printing that it's easy for anyone following the industry to overlook something. However, these words hardly refer to the Local Motors project. Based in Phoenix, Arizona, Local Motors plans to print the car at the Manufacturing Technology Show (IMTS) in Chicago September 8-13 this year. Of course, this idea may fail, because representatives of Local Motors will have to meet 6 days. nine0005
That's why everyone at this company works very hard to make sure they're ready for the big day, less than three months away. To make sure they succeeded, Local Motors employees 3D printed a test sample of their planned car.
If anyone had any doubts about the ability of this company to meet the six-day deadline, then after the work they did last week, one can be absolutely sure of the talent of these guys and that they are able to realize their ideas. Just a few days ago, the main 3D printed frame was completed, and the very next day, Local Motors showed their car in action. James Earl, a member of the staff at Local Motors, was the lucky one to test drive the world's first fully 3D printed car. Earl explained that they wanted to print out a test piece to make sure the drive mechanism was working properly. The video below partially shows the test run itself:
Article prepared for 3DToday.ru
Article comments
More interesting articles
7
Subscribe to the author
Subscribe
Don't want
Volgograd schoolboy Mikhail Kozenko joined the ranks of 3D-makers by designing his own 3D-...
Read more
five
Subscribe to the author
Subscribe
Don't want
Alexander Gessler wrote a small handy program to convert 40+ 3D file formats (OBJ, S.