3D print recycled plastic
Eco-friendly 3D filament guide - what are the possibilities and innovations
What is eco-friendly 3D filament?
Eco-friendly 3D filament is a new alternative to the classic plastic filament. 3D printing requires a lot of energy and often uses non-biodegradable materials. For example, ABS is made from petroleum. It is one of the most common 3D printing materials when it comes to filament extrusion.
However, innovations now offer the opportunity to 3D print ecologically and responsibly at a lower cost. Many biodegradable filaments, made from recycled materials, have been developed to be environmentally friendly and have become alternatives to plastic filaments.
By incorporating a biodegradable plastic base (in the form of fibers or powders), it is possible to create filaments that include a high percentage of organic material.
3D printing from recycled plastics
How to make 3D printing materials from plastic waste
Thanks to Tyler McNaney’s Filabot, or MIT’s Recyclebot, it is possible to create ecological filament at home by recycling plastic waste. These machines turn waste into a 3D filament that a 3D printer can use.
A bottle of milk recycled by the Filabot converts into 2.5 meters of 3D filament.
First, the machine crushes recyclable plastic waste (bottles, boxes, etc.) to transform it into plastic pellets (or granules). The recycling machine then heats and extrudes these pellets into the shape of filament. The filament is then wrapped around a spool so that it can be reused again by a 3D printer.
Reuse 3D printed objects and plastic print waste
3D printing requires patience and involves a lot of testing to perfectly configure a 3D printer and produce quality 3D models. Many of these tests result in print fails, extra material, supports, or simply old pieces that are no longer useful.
Plastic waste extruders such as the Filabot or ProtoCycler can recycle this plastic waste. This innovation, with its ecological aspect, also represents a big cost saving for the users who can reduce their 3D filament expenses.
Buy 3D filament made from recycled materials
The Dutch startup Refil sells 3D filament made from two recycled plastics, ABS and PET. These two plastics mainly come from plastic bottles and car dashboards. This award-winning innovation is called Refilament.
According to Refil’s co-founder Casper van der Meer, the recycled filament (free of toxic additives), boasts the same features as ordinary filament and is available at a price between 30 and 40 dollars a spool.
Black ABS 3D filament produced by Refil from old car dashboards.3D printing with biodegradable 3D filament
PLA, a cornstarch-based 3D printing material
With ABS, PLA is the most commonly used 3D printing material when it comes to filament deposition.
PLA is made from cornstarch. It is compatible with most 3D printers using extrusion 3D printing technology.
Unlike ABS, PLA is a biodegradable material. Thanks to its non-toxicity, PLA can also be used to 3D print objects that will be in contact with food.
The main weakness of PLA is its high sensitivity to moisture and its tendency to break rather than bend. It makes it more difficult to handle than ABS.
Green and blue frogs 3D printed from PLA.Sustainable 3D printing: paper, an alternative to plastic
Mcor Technologies (now CleanGreen 3D) is a 3D printer manufacturer that has successfully made 3D printing material from paper. Their Laminar 3D printing technology successively cuts sheets of paper and glues them onto each other to 3D print an object.
Paper is not as environmentally friendly as PLA, but it is a serious alternative to more toxic materials. It also costs much less: a ton of paper costs around €1,300 while a ton of PLA costs between €5,000 and €10,000.
Plant-based 3D printing materials
Many plant-based filaments have been developed, such as the soy-based FilaSoy or SeaWeed, a material made from seaweed. The Algix from 3DFuel is also available and is made from nuisance algae.
Wood is also a material that is used to make natural 3D filaments. For example, Laywood is made up of 40% of wood, which gives it a touch and appearance similar to wood.
ColorFabb has even developed two 100% organic filaments: the WoodFill made up of 70% PLA and 30% wood fiber, and the BambooFill, half bamboo, and half PLA.
Finally, oysters and coconuts have also been experimentally used to create new 3D filaments.
A small 3D printed elephant made with ColorFabb’s Woodfill material.3D printing with recycled building materials
3D printed houses made from recycled concrete
The Chinese company WinSun Decoration Design Engineering received attention in 2014 by 3D printing ten houses in less than 24 hours. These were 3D printed from a mix of cement, industrial waste, and recycled fiberglass. In 2015, they did it again, this time with a four-story building, and also succeeded in less than 24 hours.
In January 2018, the same company 3D printed bus stops at Fengjing Town in Shanghai.
In Amsterdam, a canal house was also 3D printed by DUS Architects in 2016. This house, designed in partnership with Henkel, is 3D printed with bioplastics. It consists of 80% ecological materials.
Examples: two innovative projects to recycle plastic waste
An eco-friendly 3D printer launched by Coca-Cola, 3D Systems, and will.i.am
will.i.am, who was previously creative director of the 3D printer manufacturer 3D Systems, had teamed up with Coca-Cola to create Ekocycle. The Ekocycle is a 3D printer that uses a 3D filament, of which 25% is made from recycled plastic bottles.
“Ekocycle’s goal is to collaborate with the world’s most influential brands and use technology, art, and fashion to change an entire culture. It’s the beginning of a more sustainable lifestyle through 3D printing. Waste is waste only if we waste it.”
will.i.am
Ekocycle will be able to 3D print objects with a build volume of one hundred cubic centimeters, with a minimum layer thickness of 70 microns.
Three 500ml Coca-Cola bottles are needed to make one Ekocycle cartridge. The available colors Coca-Cola’s emblematic colors: red, black, and white.
will.i.am, a founding member of the Black Eyed Peas and 3D Systems’ previous artistic director, presenting the Ekocycle eco-friendly 3D printer.Clean beaches and 3D printed souvenirs of the sea
In 2014, two Swiss entrepreneurs, Jennifer Gadient and Fabian Wyss, launched the Seafood Project. This project aimed to clean the beaches of France, Spain, and Morocco by recycling all plastic waste into 3D printed objects.
The couple left France in October 2014 and drove down to Morocco in their van, in which they had all the necessary equipment for 3D printing.
On the beaches, they recovered plugs, bottles, and other plastic waste. With the help of an extruder and a shredder, they transformed this waste into 3D filament. They then 3D printed objects with an Ultimaker 3D printer and sold them on their website.
Picture of Jennifer Gadient and Fabian Wyss in front of their van, equipped with a 3D printer to recycle plastic waste from beaches.LA Startup Is Using Recycled Plastic to 3D Print Prefab Homes
Photos: LA Startup Is Using Recycled Plastic to 3D Print Prefab Homes Search iconA magnifying glass. It indicates, "Click to perform a search". Insider logoThe word "Insider".US Markets Loading. .. H M S In the news
Download the app
Azure Printed Homes- Los Angeles-based startup Azure is using recycled plastic to 3D print prefab homes.
- The startup is now selling several models ranging from a backyard studio to a two-bedroom ADU.
- Azure says it can build homes 70% faster and 30% cheaper than "traditional home construction methods."
Why "reduce, reuse, recycle" when you can just turn your plastic waste into homes?
A worker stands in front of a pile of plastic waste as machinery processes it at a facility in Japan. Makiko Tanigawa/Getty ImagesThis may sound like a far-fetched idea, but that's exactly what one 3D printing home construction startup in Los Angeles is trying to do.
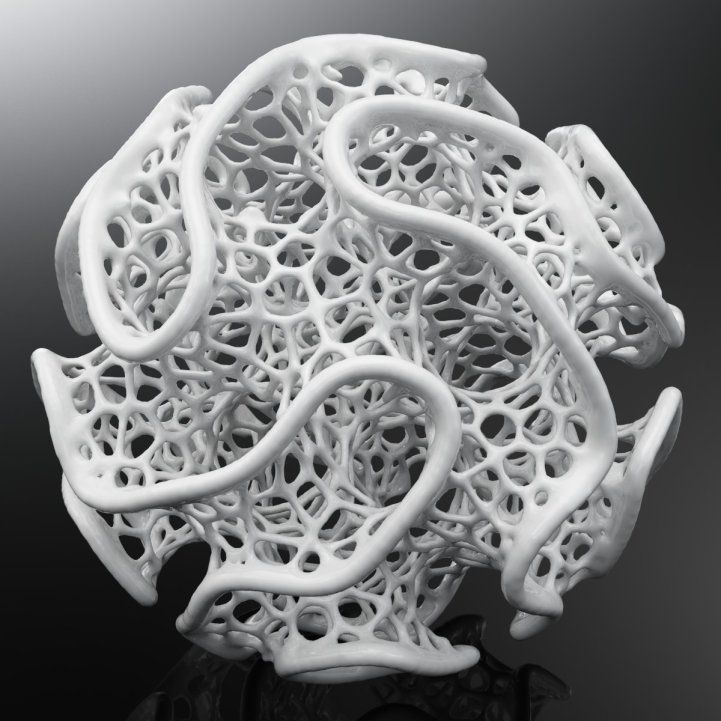
In April, Azure unveiled what it called the world's first 3D printed "backyard studio" made with recycled plastic materials.
Azure Printed HomesSource: Azure
And its plastic-printed studios and accessory dwelling units (ADUs) are now available for preorder as the startup prepares to ramp up its production line in the Culver City neighborhood of Los Angeles.
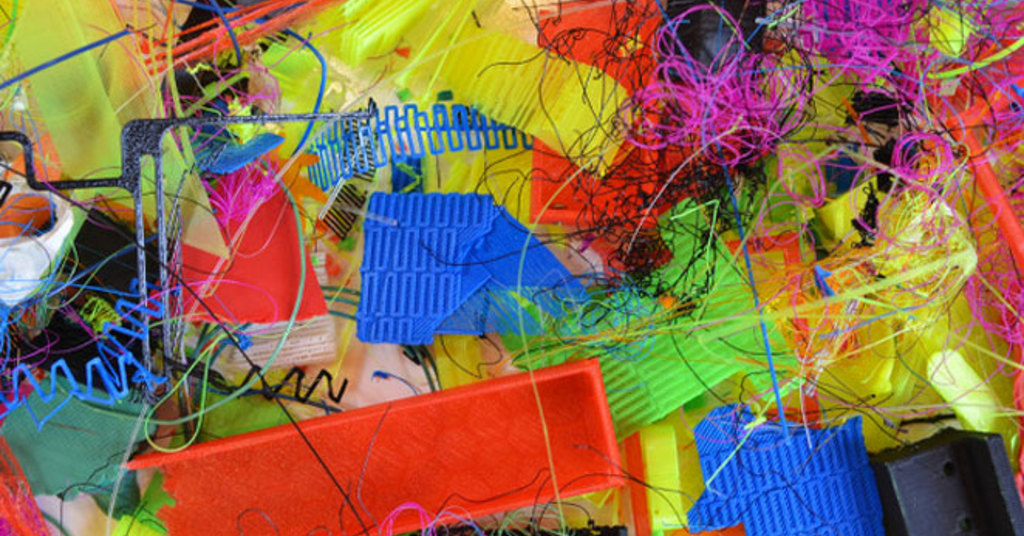
Most 3D printing home builders currently use a form of concrete to create their homes, whether it be a proprietary mix or pure concrete.
3DCP GroupSource: Insider, Insider
But Azure is saying goodbye to this drab grey look by taking a more sustainable approach …
Azure Printed Homes… giving a second life to plastic once destined for landfills or incineration.
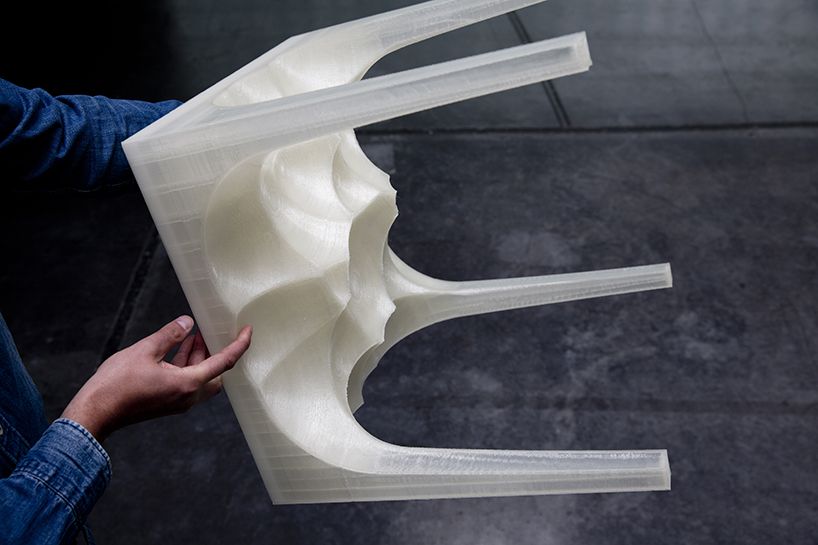
Over 60% of Azure's printing material will use the inherently waterproof plastic polymer often found in plastic bottles and packaging for food, according to the startup.
Azure Printed HomesSource: Azure
It's currently working with three suppliers to source "post-industrial plastic" for its printing mix, Ross Maguire, who cofounded Azure to make construction more efficient and sustainable, told Insider.
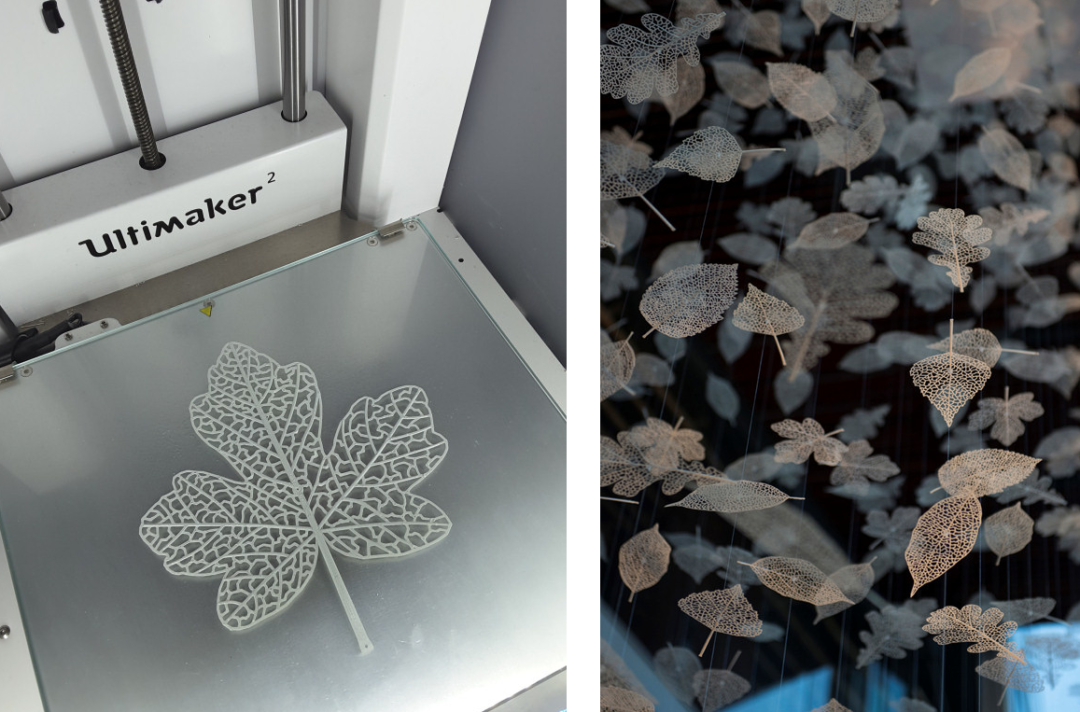
But in the future, the goal is to use post-consumer plastic: "Our supply chain should never be short in our lifetime," he said.
A volunteer with Dominion Tabernacle Ministries prepares cold water bottles to hand out in Dallas, Texas on June 12, 2022. Shelby Tauber/ReutersEven without the use of recycled plastic, the nascent 3D printing homebuilding industry has already been heralded as a more sustainable and efficient construction method.
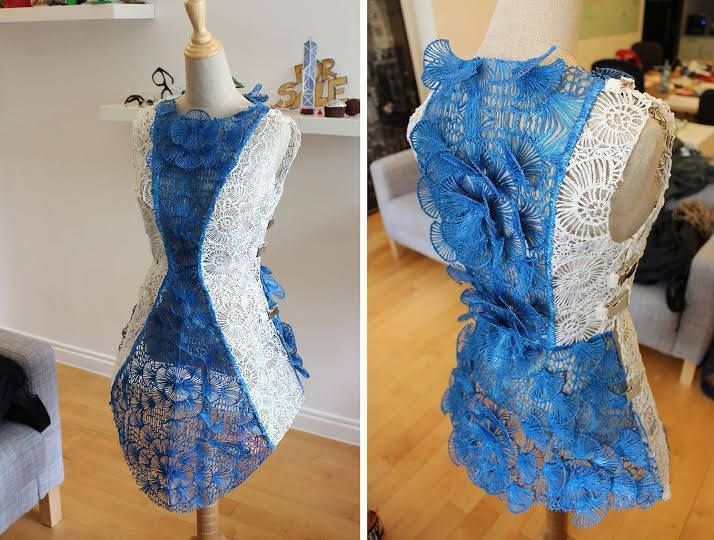
According to its biggest proponents, by using printers instead of people, homes can be built more efficiently using less waste, materials, and time.
Mense-KorteSource: Insider
And Azure will be no different: The startup says it can build homes 70% faster and 30% cheaper than "traditional home construction methods" by 3D printing the floor, roof, and walls of its models inside its factory.
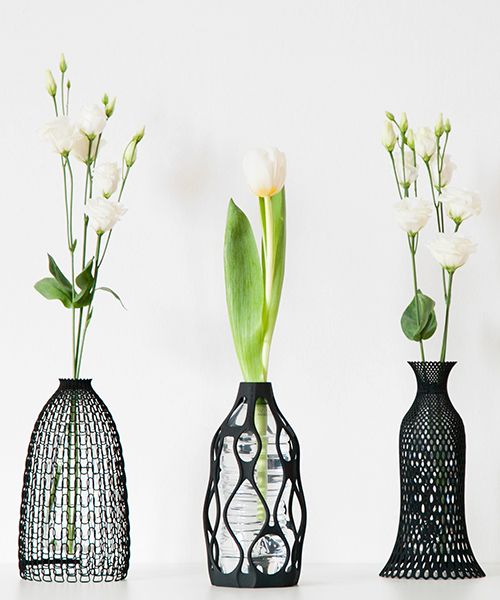
Source: Azure
And with the help of prefabrication, before a unit leaves Azure's 10,000-square-foot factory in Los Angeles, 99% of its finishes will be complete, Maguire said.
Azure Printed HomesSo when it arrives on site via a flatbed truck, the only necessary on-site work will be to connect the home to its foundation and utilities.
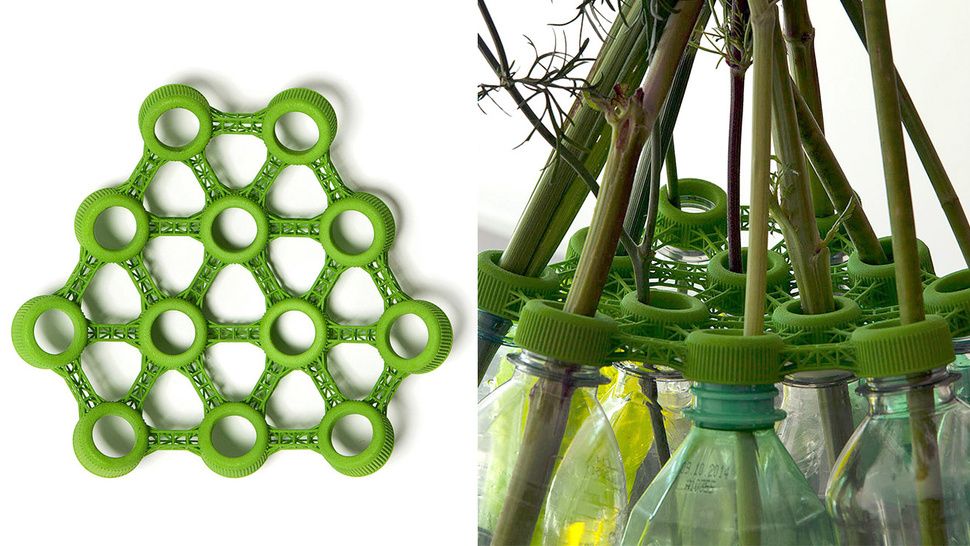
Azure currently has several customizable models ranging from small studios to 900-square-foot two-bedroom ADUs.
Azure Printed HomesAnd these builds are now available for pre-order to be delivered as soon as early November.
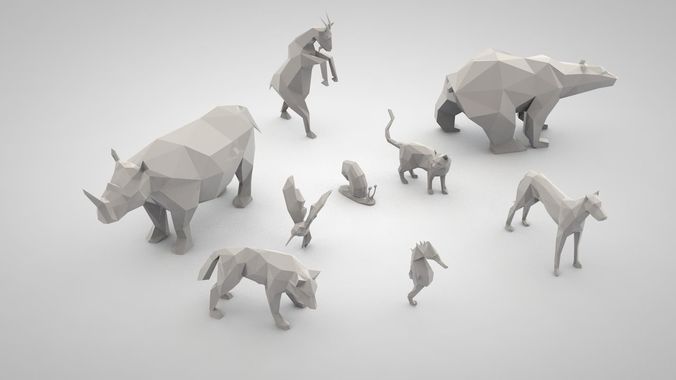
But no matter the model or size, these units will all be prefabricated and built using connectable modules that can each be printed in under 24 hours.
Azure Printed HomesThe floor and ceiling are connected by a flowing wall with curved corners, a trademark of 3D printers.
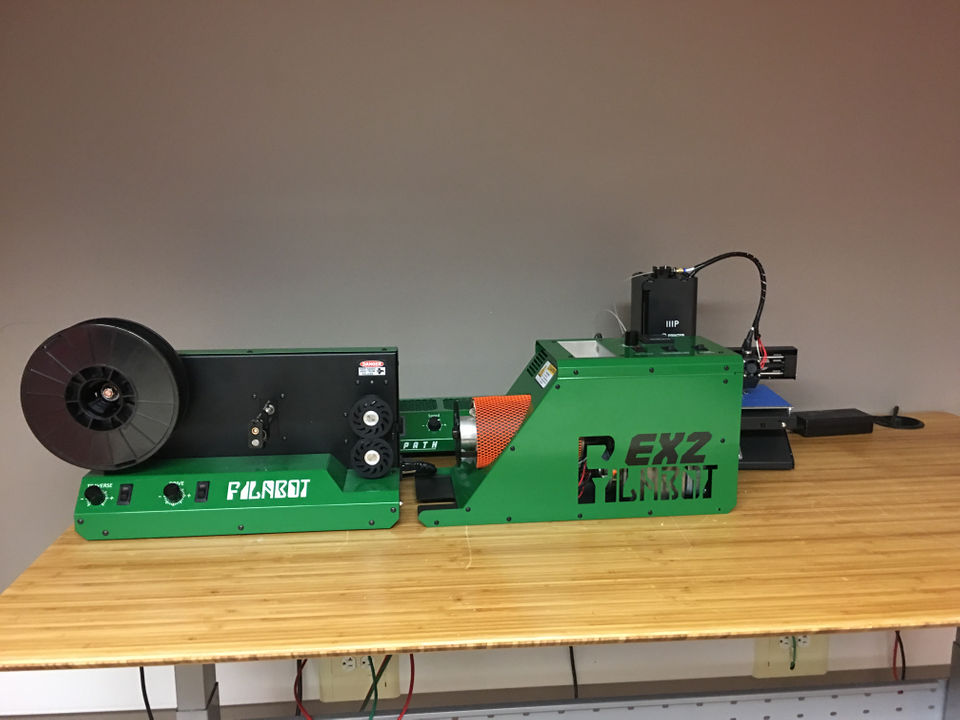
Given its smaller size, these studios can be printed within day one, wired by day two, insulated by day three, and then delivered on-site in two weeks, Maguire told Insider.
Azure Printed HomesBut if you're looking for something more substantial, Azure also prints ADUs, which skyrocketed in popularity in 2020.

ADUs extend the square footage of the main home by serving as a backyard guest home or Airbnb.
Azure Printed HomesAnd Azure's comes in multiple sizes: a studio, one-bedroom, or two-bedroom.
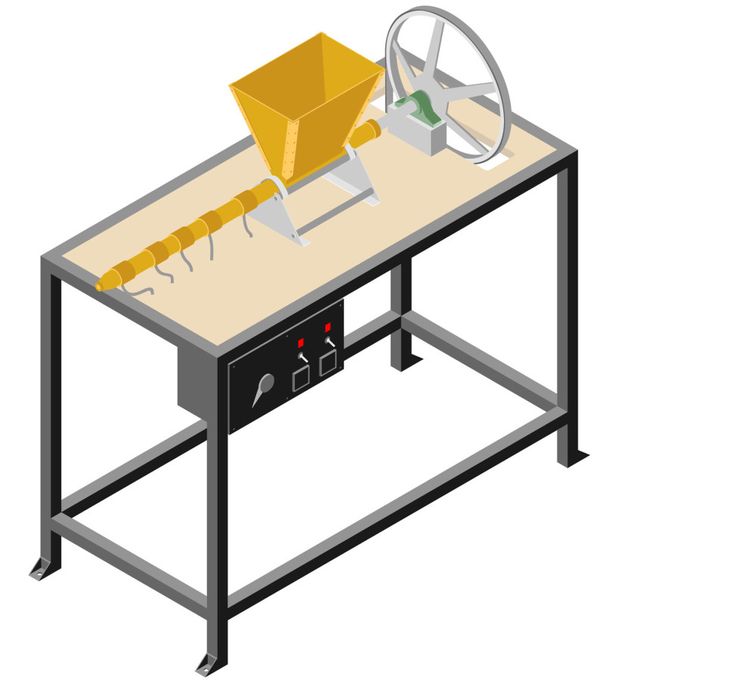
These units range from 180 square feet to 900 square feet…
Azure Printed Homes… although the smallest $39,900 option already has a three-month waitlist, according to local news reports.
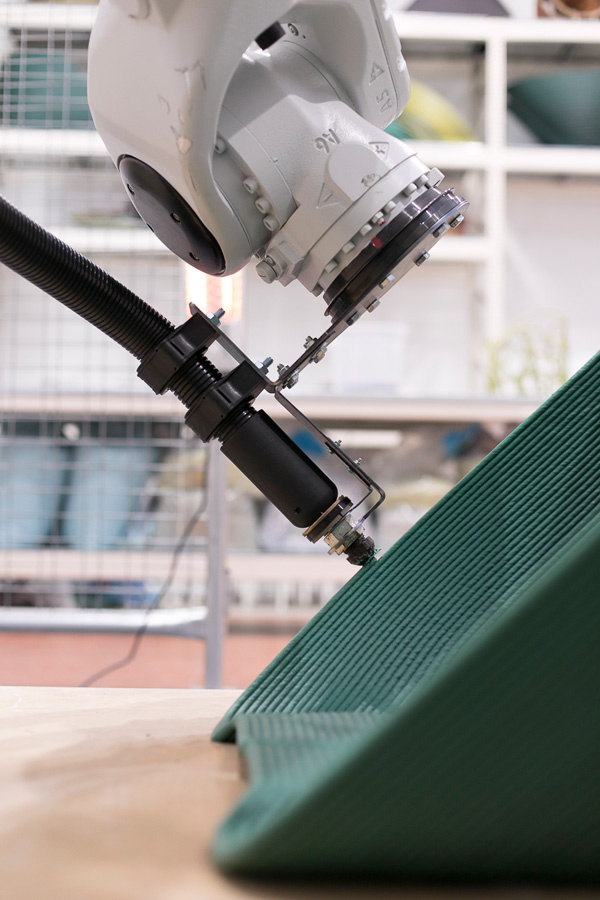
Source: Spectrum News 1
Inside, there are spaces like a bedroom, living room, bathroom, and even a laundry room in the larger builds.
Azure Printed HomesThe smaller ADU has a more traditional appearance with a pointed roof (shown below), while the size up features the same futuristic aesthetic as the backyard studio.
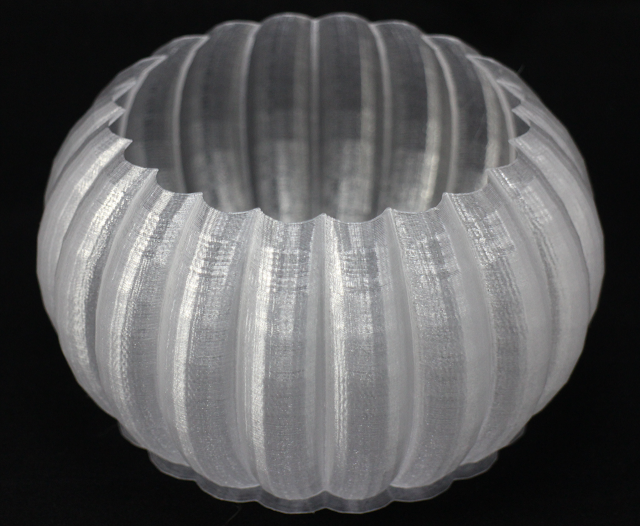
When the startup debuted the former look, it saw a "big rush of preorders," Maguire told Insider.
Azure Printed HomesAnd moving forward, he believes the company will sell more of this traditional-passing ADU.
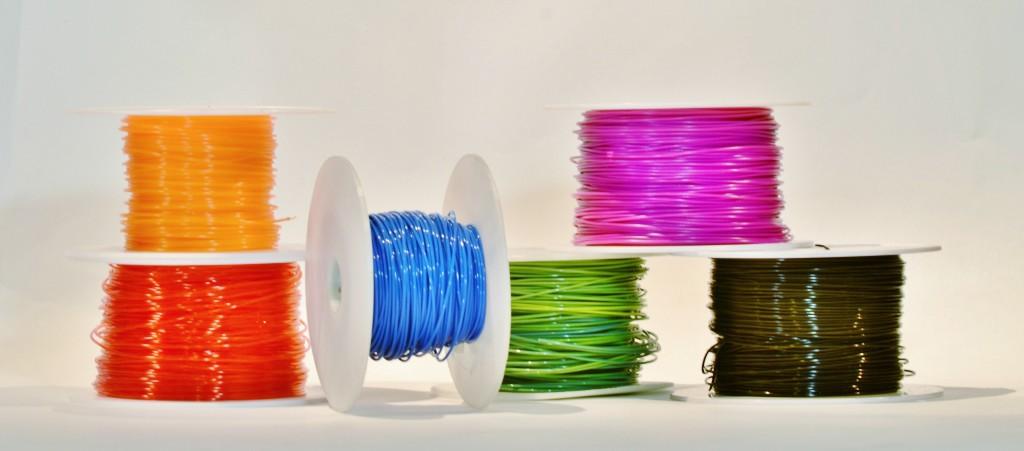
Azure has only printed one model so far, although it does have another in the works.
Azure Printed HomesBut next month, the startup will receive the last bits of equipment it needs to begin rolling out the production line .

... which should help address its "big backlog of orders" that has already been overloading its one printer, Maguire said.
Azure Printed HomesAnd in 2024, the startup will begin rolling out larger homes.
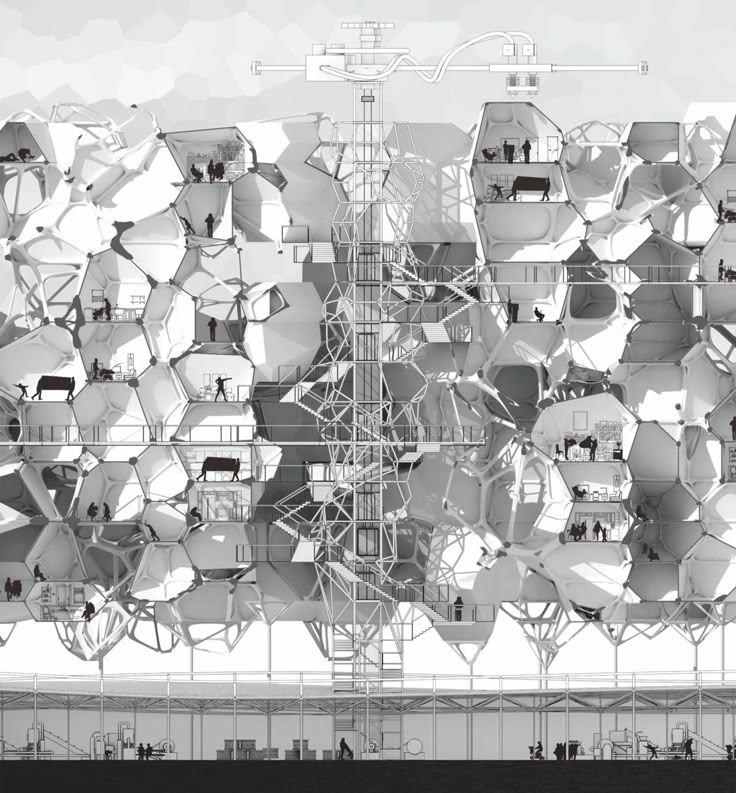
Further down the line, Azure may also explore printing housing for the unhoused or for overseas clients …
Azure Printed Homes… and in the future, if the company decides to expand, you could find a pop-up-like Azure production line near you.
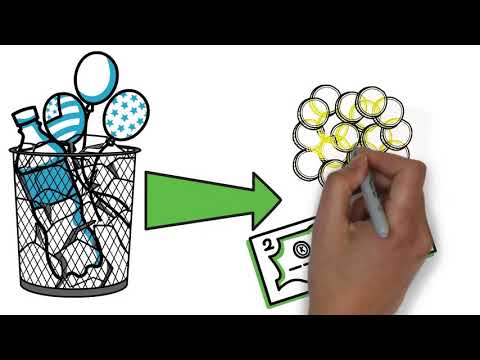
"3D printing is a more efficient way of building and it should only get better as we develop the processes, technology, and materials further," Maguire said. "I can only see it becoming more and more prominent in [construction] as we move forward."
Azure Printed HomesRead next
Features9 Projects 3D Printing From Plastic Waste
Plastic waste, which not so long ago went straight to landfill, is increasingly being recycled, not least 3D printers.
By using post-consumer plastic as a raw material for 3D printing, corporations, small businesses and even individuals can create new products with real value while removing plastic waste from the environment. Let's figure out what is created from plastic waste using a 3D printer and who does it. nine0003
How to prepare material for 3D printing from plastic waste
The process of making useful products from local plastic waste using 3D printing is quite simple. Known as distributed recycling and additive manufacturing, or DRAM for short, it involves the following steps:
• Plastic waste collection.
• Waste sorting and cleaning.
• Shredding waste into plastic pieces.
• Extruding 3D printing filament from plastic shred with an extruder. nine0003
• Product printing.
Video: thenewraw. org
Thread made in this way retains almost all the same qualities as pure plastic, but is much cheaper. According to a study by Aubrey L. Verne (et al.) of Michigan Technological University, a 3D printer can print objects at a cost 1,000 times less than if commercial polymer fibers were used.
There are different types of shredders, extruders and 3D printers on the market today, both in terms of cost and complexity of the tasks performed. nine0003
For example, for home use, manufacturers have long used a simple blender or grinder to grind up 3D print stock and failed prints, but this is not a long-term or high-volume solution.
More and more 3D printers can print with raw shredded plastic or bulky plastic pellets instead of filament. This simplifies the process and reduces energy consumption. The cost of a simple 3D printer can be $2,000, and a complex industrial one can cost more than $150,000. nine0003
Introducing 9 successful projects that prove that 3D printing from household plastic waste is a viable solution for removing plastic from the environment, while also making a difference.
Plastic Bottle Olympic Podiums
Unbeknownst to everyone, recycled plastic has taken center stage at the Tokyo 2020 Olympic Games. Each of the 98 podiums where medals were presented to Olympic winners was 3D printed from waste plastic. nine0003
Catwalk material has been collected by Japanese citizens over the past two years through a program sponsored by consumer goods giant Proctor & Gamble. More than 2,000 boxes have been set up across the country to collect empty drink bottles, shampoo containers and other plastic waste. Plastic waste has also been fished out of the seas surrounding Japan.
After the games, some of the podium plastic will be used to educate the public about sustainability, and much of it will be recycled back into packaging for P&G products. nine0003
Waste bins made from plastic waste
Screenshot: Waste bin 3D printed by Justina Zdanovichute in collaboration with R3direct.
(Source: Justina Zdanovichute/CC BY-NC-ND 4.0)
How about collecting plastic waste in trash cans made from the same waste? Italian design company R3direct makes them and more using 3D printing. The company has one stated goal: to design and 3D print products from plastic waste. R3direct's list of products grows longer every year, from artwork made from local plastic waste to practical urban furniture. nine0003
R3direct states that their printing technology can use plastic pellets immediately after grinding, skipping the filament extrusion step. This allows them to further reduce their energy consumption and CO2 emissions with 3D printed furniture made from waste plastic.
Trendy Fishnet Seats
Photo: facebook/@bluecycle use of marine plastic waste from shipping and fishing. nine0003 New Raw has also teamed up with The Coca-Cola Company for the Zero Waste Future program in Thessaloniki, Greece. Consumers will bring their plastic waste to the Zero Waste Lab, which has a plastic recycling facility and a robotic arm, to create custom-made modern furniture. One of the partnership's furniture series is called Elements and includes a solarium, walk-in closet and walkway made from recycled marine plastic waste. There's no better way to showcase the potential of recycling plastic waste than to let people enjoy a clean beach while lying on a lounge chair made from what used to pollute the water. nine0003 New Raw is launching a Print Your City program in several neighborhoods that allows local residents to recycle their plastic waste through a robotic 3D printing process that can turn sorted plastic into outdoor furniture. Photo: instagram/@yuma.labs.circular closed loop models. nine0003 Yuma Labs uses both powder pad 3D printing and injection molding to make their sunglasses. The raw materials are recycled soda bottles and bio-based nylon. In the future, the frames of sunglasses can be completely recycled. Yuma Labs partners with companies, cities and events such as the Tomorrowland Music Festival to collect the plastic waste generated at the event. Yuma Labs also organizes and participates in community events to raise awareness about recycling. For example, in 2019 they organized an event at the Stormkop playground in Antwerp where children had to pull plastic trash from a nearby river. The company then 3D-printed it into children's sunglasses. As Yuma Labs says, it's not just the production of sunglasses or the recycling of plastic that matters. They hope to inspire others with their example for a broader transition to a circular economy. nine0003 Utility Vehicle (ZUV) is an electric trike with a 3D printed frame made from recycled polypropylene plastic. Developed by Austrian design firm EOOS and Dutch 3D printing company The New Raw, ZUV aims to do more than reduce plastic waste. According to the developer's plans, consumers can 3D print the ZUV's polypropylene frame using a 3D printing service such as Craft Cloud and then take it to a bike shop to have the motor, wheels, lights and handlebars installed. The square ZUV has a rear wheel drive and a spacious trunk. It can be ridden by two adults. EOOS hopes to raise awareness of the environmental impact of urban transport and offer an alternative mode of transportation based on a circular economy. nineThe 0003 ZUV is currently only in the prototype stage and its blocky look may not be to everyone's liking. However, the concept is promising, and the car has every chance of becoming an ordinary city landmark. Photo: lofbergs-com.mynewsdesk.com Swedish coffee group Löfbergs is partnering with 3D printing company Sculptur to turn coffee waste into new coffee stations. The coffee stations are 3D printed from a by-product of the coffee roasting process and polypropylene. Further development will allow the use of polypropylene from recycled coffee big bags, making coffee stations almost 100% renewable. “Our new coffee station is a prime example of a closed loop—recycling leftovers from our own primary raw material, coffee, to create an entirely new and associated sustainable product.” , says Lars Aen Tegersen, Director of Innovation and Circular Transformation at Löfbergs. Photo: instagram/@architechcompany interiors. Modular circular workspace printed from recycled PET (supplied by the Port of Rotterdam) using a CFAM printer and reinforced with fiberglass. Photo: instagram/@therogerie Canadian company The Rogerie is working to remove waste from the environment, with the help of small suppliers who remove it from landfills and oceans, and create from this waste beautiful, useful items. The Rogerie's 3D printed product catalog includes mugs, bathroom accessories, teapots and a wide selection of flower pots, among others. Customers love these products - by purchasing them they are contributing to the removal of plastic waste from the environment. nine0003 The company's founders say they are constantly looking for new waste streams and also have their own recycling program. They are willing to use anything from old TVs to food packaging and car parts. Photo: instagram/@utilizestudios The Utilize project turned used coffee stirrers into chandeliers, soft plastic items into wicker baskets, and fishing tackle into chairs. And all this with the help of an oven and a desktop 3D printer from Ultimaker. nine0003 Utilize is more than a design studio, it specializes in helping companies transition to a circular economy and build sustainable products. They aim to help businesses reduce, reuse and recycle waste through 3D printing. “The biggest surprise was how many types of waste we can use – soft plastics, organics, polypropylenes and polyethylenes – we kind of asked, why isn’t everyone doing this?” , said Utilize Project founder Matthew O'Hagan in an interview with Stuff magazine. - nine0023 "Why isn't this being done?" Material based on: all3dp.com
Music festival waste sunglasses frames
And the sale of sunglasses, then printed on a 3D printer from this garbage, covers the cost of collecting plastic. nine0003
Plastic Waste Urban Lightweight Vehicle
Its creators hope it can become the new type of zero-emission vehicle for cities around the world. nine0003
Coffee station made from coffee waste
The collaboration is part of Circular Coffee Community's commitment and the group's goal of zero coffee waste by 2030. The world's first 3D printed waste-based coffee station is already up and running and others are underway. nine0003
Cozy office space made from plastic bottles
The convenient and strong workplace easily disassembles and moves. The round shape ensures pleasant acoustics of the workspace, it is equipped with ventilation, heating, electricity and LED lighting. nine0003
Beautiful objects made from garbage
Coffee stirrer chandeliers
PET plastic recycling and how 3D printing can change the lives of each of us for a convenient reference, I will indicate the name of the topics in a LARGE FONT)
WHERE IT ALL STARTED:
How can 3D printing change not only the lives of those around you, but also yours? Stupid question, but for me it is rather ironic. nine0003
It all started many years ago, when I became interested in tank modeling, while playing one game known to everyone, I accidentally stumbled upon the news about paper modeling, they offered to make a simple MC1 tank out of paper, I immediately liked the idea, because I liked to do it from childhood something with your own hands.
I won't go into details, but I can say that with time the quality of the work increased, the paper hobby ousted everything superfluous from my life, including computer games.
This hobby greatly developed thinking, ingenuity and fine motor skills, because it was necessary to create durable paper structures, to carry out fine work with small details, and this is not quite the same as buying a ready-made assembly kit. (Assembling Bismarck out of paper was a big challenge)
Everything about it was perfect, except for one BUT! This time, for 1 tank model, it took from 5 to 9 months, over the years, time became less and less, work, study, family . . And I really wanted to do what I loved. nine0003
I found out about 3D printing by accident and immediately the idea appeared that many components and assemblies of tanks can simply be printed, while eliminating the routine, especially for tracks and rollers, making them out of paper is still a pleasure.
An obsessive idea firmly settled in my soul and did not give me rest, but the high cost of the printer cooled my hot ardor. And yet, with confidence, I continued to monitor prices and the situation in general.
After a couple of years, the decisive moment has arrived! I decided to buy, spending all the accumulated money! at that time, 22 thousand was a rather large amount for me and many others around me, so when I spent it on such a toy, many condemned me. nine0003
This miracle was printer Pryusha ah 4, at that time the top model, but now, of course, it's not the best option.
Printing did not work right away, it took a lot of time to set up, understand the operation of the printer, slicer, and upgrade it. He printed all sorts of little things that were not quite necessary, and then he completely cooled off.
A year later I was asked an important question - You bought a printer for a hobby, but you print anything, but not the target product, Why?
I answered that there are no ready-made models, and to create your own, you need knowledge of 3D modeling. nine0003
My opponent said that everything can be learned if you are busy doing what you like and made me promise to make at least one model.
More than one year has passed since then, a lot of effort has been invested, a lot of trial and error, experience has given an understanding of what and how to model, what and how to print better, here are a few examples of printing
There was one caveat, it's plastic. At some point it was expensive, after that I found a place to buy a cheap one. nine0003
But walking along the street and seeing bottles everywhere, thoughts involuntarily began to appear that all the material was underfoot.
In addition, the environmental situation with plastic in our cities, and throughout the world, is quite terrible, which, accordingly, also influenced my idea.
There were attempts to create an extruder for plastic recycling, but the ideas were in vain, the implementation failed.
However, the idea of recycling PEK bottles seemed to me very simple and feasible in practice. As a result, it turned out that I was very mistaken about this. nine0003
RECYCLING PET BOTTLES (5L POTs)
I will try to briefly and concisely describe the essence of the work process, there are a lot of articles on this topic, but there is one BUT !!! In my implementation, they unfortunately almost did not help!
The bottom line is that everyone in the examples of videos and articles printed well, but all my attempts failed ...
There were many reasons for printing failure: cork formation, nozzle clogging, under-extrusion - the printer simply could not push PET the thread, or simply the feed gear, slid along the bar. nine0003
In addition, the length of the rod is always limited, it is necessary to constantly change the filament, but this problem was also solved.
Let's not pull the printer by the bar and start in order:
PREPARATION OF THE BOTTLE
It is very difficult to find an ideally even bottle, and it is not necessary.
First of all, we need:
Plastic plug - we make a hole for the valve in it, the valve is sold at any tire shop or can be ordered on Aliexpress
http://alli.pub/5s0hyt
we get the following:
We wind it on a bottle or flask with a descending cork. Do not forget to add a couple of drops of water to the bottle, then pump it up. You need to pump up quite a bit, without fanaticism, a bicycle pump can do just fine.
Next is the most dangerous and important moment
Our goal is to level the bottle and not to blow it up, there is no need for a lot of pressure!
We heat the bottle on a gas burner or with a building hair dryer (there are a lot of videos on YouTube on this topic, I advise you to read it), do not forget to scroll it, water drops will give steam, which will further expand the walls. nine0003
Do not forget about safety, goggles are required!! Breaking a bottle can burn, cotton itself is not very dangerous, but you can get scared from surprise (remove women, children, old people and a mentally unhealthy cat from the house).
I repeat!!!! our goal is to align, to align the bottle a little, and not to explode, so without fanaticism!
Let's skip the irony and get down to business. Here is a good example:
And now it’s already dangerous, the bottom of the bottle began to fall out, an early sign of a rupture, but this is not a 100% danger indicator, do not forget about the cork, it may also not withstand, especially for bottles, the walls of the cork are very thin there , strength is low! nine0003
After heating, immediately release the pressure, carefully press the valve, for example with a screwdriver, I warn you, a little steam will come out from there, take care of your eyes. And only after that we remove the cork.
Do not leave an inflated and heated bottle, after cooling it will collapse and lose its shape.
Well, we have passed the most dangerous section, let's move on! BOTTLE CUTTER
I must say right away that the bearing bottle cutter is by. Too confused, too complicated and incomprehensible, but the choice is yours. nine0003
Printing on a printer is also not an option! The PET tape will cut it like a knife through butter.
Our choice - only metal
or something similar to this
http://alli.pub/5s0i24
It's very easy to make, in a fastener store, buy a corner, M4 screws, nuts and washers for it. Well, do not forget about the clerical blade.
here is the result:
The number of washers adjusts the width of the PET strip, and the nuts clamp the knife blade. At the bottle, we cut off exactly the bottom, align it with scissors and make a small incision. nine0003
Pull and cut slowly, holding the bottle at an angle, keeping the width of the tape constant.
its width should be approximately 0.9 mm, but in the process of work you select individually.
The first time you most likely will not be able to cut as needed, be patient and bottles, everything will come with experience.
Here is the result:
AUTOMATIC FILAMING EXTRUDER
I will say right away that the engine, driver and generator are not the most important, I pulled the bar by hand, it is rather a moment of convenience and for the future. (links to relevant parts are below) nine0003
Most important node
example
https://youtu.be/BsdvdI-L3Vo
I think you recognized it, this is a fuser from a printer. We fix it on the corners, insert the heater.
http://alli.pub/5s0igw
I think they also recognized the nozzle, but it needs to be prepared.
At the exit we drill through a hole with a 1.7-2 mm drill (this will give about 1.7 bar at the exit)0003
And a little more, but to a shallower depth of 3 mm.
And at the very entrance 4-5 mm, to a depth even less
As a result, we will get a hole in the form of a cone, this is necessary so that the PET tape rolls into a rod better and easier, at the entrance it is wide, but moving along the nozzle it begins to roll up due to the heat shrink and the conical shape of the nozzle.
If you have a drill, then I advise you to slightly smooth out all the irregularities based on what we have drilled with a cone-shaped cutter. nine0003
The power supply regulates the heating temperature. (blocks are just a super indispensable thing in the household, I advise you to take 2, 1-1 to adjust the heating of the nozzle, the 2nd will go to power the broach motor) strong due to shrinkage, cut with scissors and pull the bar at the exit with tweezers.
We pull manually or with the help of electronics, I’ll say right away that skill is needed here, it won’t work the first time nine0003
and here is the result
If you want to automate the work, then here are the necessary details:
Generator
http://alli.pub/5s0esv
TB6600 stepper motor driver
http://alli.pub/5s0i7k
EXTRUDER
What can I say, I tried the standard version, I tried the titanium extruder - and all in vain ... this does not mean that you will not succeed, it means that I very tired of dealing with the problem for 1 year and found the ideal. nine0003
Meet the perfect extruder that eliminated most of my problems! http://alli.pub/5s0i9w
Its advantage is that 2 gears rotate simultaneously and have notches, even a smooth and hard bar will not stand a chance. The same extruder is needed for pulling the filament, at the exit the rod will turn out with notches, which will be well displayed during printing
FILEMENT TUBE
http://alli.pub/5s0f6v
The inner diameter must be as large as possible !! nine0003
In my case, the inner diameter is 3mm, the outer diameter is 4mm, otherwise the filament will get stuck, due to expansion and variable size
much more, as a result of which, when cooling, a cork forms in the fuser - as a result, a print failure
THERMAL BARRIER (THROAT)
must be taken as in example 1, with a through hole, for the reason described above, nine0003
Option 2 will not work - there will be a jam
RADIATOR
Here I advise you to take something larger, here is an example
http://alli. pub/5s0g80
If the heat sink is too small, there is a risk that there will be a filament crease as a result of overheating
COOLING
In my case with a large heatsink, cooling is not needed!
Let me explain:
The hot radiator dries the bar as it travels to the nozzle, and the bar is already warm and easier to melt. nine0003
For the experiment, I decided to install a cooler and here clicks of the extruder began, the printer did not have time to melt the bar, as a result - the bar was crumpled and printing failed.
In general - if you decide on cooling - take care of the possibility of its regulation!
NOZZLE
This is no less important moment!!!
We use any, but it needs to be drilled, as I described earlier, but you can immediately use a 3mm drill, not naturally through. nine0003
The bottom line is that the plastic will melt, as it were, in the nozzle chamber that you drill, and not in the thermal block, as it was provided for by the design, and there will be no plug during retraction, the molten mass will remain in the nozzle chamber.
PRINT SPEED AND PLASTIC FEED
Change the bar size from 1.7 to 1.4 or 1.5 in the slicer settings. This is due to the fact that the homemade bar inside will not be hollow, so its feed should be greater! Otherwise, the walls of the part will be thin. nine0003
The print speed, on the contrary, must be reduced, in addition, the print speed of the supports, and the fill must be equal to the print speed of the walls.
print example
https://youtu.be/jIWRY24LOf8
ALLOYING THE ROD INTO A SINGLE WHOLE
Experience and skill are needed here! Be patient !
Tried a lot of things, all without success. I give you a working method right away
https://www.youtube.com/watch?v=4-nrcfdk44Y
We set it on fire and melt it until it burns, carefully, I got a serious burn! nine0003
We extinguish, connect, blow (or better with some water).
I cut off the excess with wire cutters and clean it with sandpaper to the ideal.
Gently twist into a coil, the connection is not perfect and is destroyed when pressed hard, but in general it keeps its shape.
Total
I consider this processing method to be one of the best. Yes, it is not perfect, it is a little confused, there are flaws, not the whole bottle is recycled. But still, as an initial start, this method can and should be applied, just imagine how you can reduce the amount of plastic in the environment if every second person who has a printer uses a similar approach. nine0003
Here is an example of printing and here is a preview of the 3D model that I prepared for printing, so to speak - expectation and reality.
As you can see, I am still in the printing stage, I will print all the knots with a bottle as much as possible, I will finish off all the little things that the pryusha cannot handle with a photopolymer printer, and after priming and painting, everything will look no worse than a sketch.
You can see more photos, follow the complete assembly and my work at the link
https://vk.com/public_model_hends
It will also be important to say that parts made of such plastic are practically indestructible, it is difficult and sometimes impossible to break by hand.
It can be used to print durable parts or children's toys, which is in the plans.
Or collectible toys
You don't want to throw away such a thing, you can also give a toy to another child as you don't need it. (Nemesis does not count, not every child wants this, although I would be very happy about this as a child) nine0003
A lot of time has passed since I collected the first paper model and a lot of effort has been spent, since then I have mastered 3D modeling, painting, 3D printing.
Small hobby - gave direction and understanding to what I want to do in life and how to earn a living.
Mastering 3D modeling has opened up the prospects for developing models for Game Dev / but even here 3D printing does not stand apart, because I use the Hipoly model for printing, so to speak - waste-free production in everything. nine0003
Here is an example of a model I created for printing, which was ordered by a modeler from Rome
and here is the same model, but already Low Poly and for Game dev.