3D print material guide
Ultimate Materials Guide - Tips for 3D Printing with PLA
Overview
Polylactic Acid, commonly known as PLA, is one of the most popular materials used in desktop 3D printing. It is the default filament of choice for most extrusion-based 3D printers because it can be printed at a low temperature and does not require a heated bed. PLA is a great first material to use as you are learning about 3D printing because it is easy to print, very inexpensive, and creates parts that can be used for a wide variety of applications. It is also one of the most environmentally friendly filaments on the market today. Derived from crops such as corn and sugarcane, PLA is renewable and most importantly biodegradable. As a bonus, this also allows the plastic to give off a sweet aroma during printing.
- Low Cost
- Stiff and good strength
- Good dimensional accuracy
- Good shelf life
- Low heat resistance
- Can ooze and may need cooling fans
- Filament can get brittle and break
- Not suitable for outdoors (sunlight exposure)
Hardware Requirements
Before 3D printing with PLA make sure your 3D Printer meets the hardware requirements listed below to ensure the best print quality.
Bed
Temperature: 45-60 °C
Heated Bed Optional
Enclosure not required
Build Surface
Painter’s tape
PEI
Glass plate
Glue stick
Extruder
Temperature: 190-220 °C
No special hot-end required
Cooling
Part Cooling Fan Required
Fan Speed: 100%
Best Practices
These tips will help you reduce the chances of common 3D printing issues associated with PLA such as stringing, oozing, or under-extrusion.
Fine Tune the Retractions to Prevent Oozing
One of the most common problems with PLA is oozing. Since the filament flows relatively easily when compared to the other materials, it has a tendency to continue flowing during travel movements at the end of a segment. This creates strings or hairs on your part, and dialing in your retraction settings is the best way to combat this behavior! Different brands of PLA and different printers may need slightly different retraction settings, so you may need to experiment to find the best value for your printer. Simplify3D added a very useful feature in Version 4.0 that can help with this, by allowing you to quickly try dozens of different settings, and then look at the final part to determine which one worked the best on your specific setup. For example, you could setup two vertical pillars which are printed side-by-side to evaluate stringing when moving back-and-forth between each pillar. Then go to Tools > Variable Settings Wizard and choose how you want to adjust your settings during the print. For example, you could try a different retraction distance for each 20mm section of the print and then pick the value that works best in the end. For more tips on how to reduce stringing and oozing, be sure to check out our Print Quality Guide which contains an entire section dedicated to this issue: How to Reduce Stringing and Oozing.
Optimize Your Cooling Settings
Cooling is one of the most important aspects of printing with PLA. Having a dedicated part cooling fan makes a huge difference in the quality of the printed parts. The freshly extruded plastic needs to cool down below the glass transition temperature as quickly as possible. This will prevent the plastic from stringing and producing other artifacts. We recommend setting the fan to 100% throughout the print, except for the first 1-2 layers where you want to form a strong bond with the print bed. Simplify3D also includes a useful option on the Cooling tab of your process settings that can automatically reduce the print speed for small parts, ensuring that the layers have sufficient time to cool. This can greatly improve the print quality by allowing the layer to solidify before printing the next layer on top of it. This setting can be found on the Speeds tab of your process settings.
Choose the Correct Extruder Temperature
This is a great tip for any filament, but is especially useful for PLA which often contains different combinations of additives depending on the manufacturer. These different additives can lead to variations in printing temperature between 190-230 degrees Celsius. If you are not printing at the right temperature this can lead to several print quality issues including oozing, stringing, and under-extrusion. PLA can also be combined with different fills like metal, wood, and fiber that give it different characteristics than a standard homogeneous PLA. These may require different settings or even different hardware. Be sure to check with the manufacturer of your filament to verify the optimal temperature to use for your specific filament. If you have trouble with stringing, try reducing this temperature by 5-10 degrees, which will help prevent the excess oozing. If you’re struggling with under-extrusion, try increasing the temperature by 10 degrees so that the material flows more easily through the nozzle.
Pro-Tips
- Using a fan that cools the 3D printed part from all directions is highly recommended. Many popular 3D printers have community-designed attachments that can be printed and retrofitted onto your machine to improve the cooling airflow.
- Increasing the number of perimeter outlines for your PLA prints will create a strong bond between each layer, creating stronger parts that are less prone to breaking.
Get Started with PLA
Now that you are ready to start printing with PLA, here’s a bit more information to help you get started. Start thinking of project ideas by reviewing our common applications, try out one of the provided sample projects, or find a new filament to try from our list of popular material brands.
Common Applications
- Test and calibration items
- Dimensionally accurate assemblies
- Decorative Parts
- Cosplay Props
Sample Projects
- LA Spring Motor, Rolling Chassis
- G – Clamp
- Storm Trooper Helmet
Popular Brands
- Polymaker PLA, PolyMax, PolyPlus
- ColorFabb PLA/PHA
- Hatchbox PLA
- eSun PLA
- Filamentum PLA
Ultimate Materials Guide - Tips for 3D Printing with PETG
Overview
PETG is a Glycol Modified version of Polyethylene Terephthalate (PET), which is commonly used to manufacture water bottles. It is a semi-rigid material with good impact resistance, but it has a slightly softer surface which makes it prone to wear. The material also benefits from great thermal characteristics, allowing the plastic to cool efficiently with almost negligible warpage. There are several variations of this material in the market including PETG, PETE, and PETT. The tips in this article will apply to all of these PET-based filaments.
- Glossy and smooth surface finish
- Adheres well to the bed with negligible warping
- Mostly odorless while printing
- Poor bridging characteristics
- Can produce thin hairs on the surface from stringing
Hardware Requirements
Before 3D printing with PET / PETG make sure your 3D printer meets the hardware requirements listed below to ensure the best print quality.
Bed
Temperature: 75-90 °C
Heated Bed Recommended
Enclosure Not Required
Build Surface
Glue Stick
Painter’s tape
Extruder
Temperature: 230-250 °C
No special hot-end required
Cooling
Part Cooling Fan Required
Best Practices
These tips will help you reduce the chances of common 3D printing issues associated with PET / PETG such as stringing, oozing, and poor bed adhesion.
Invest In a Good Build Surface
Some 3D printers come with a glass bed or blue painter’s tape installed on the bed. Although these surfaces might work fine for PETG, we recommend using a heated build platform for best results. The heated bed can significantly improve the first layer adhesion, making things much easier for future prints. Many of these heated beds come with a glass surface, allowing you to print directly on the bed without needing to apply any additional layers of tape or glue.
Calibrate Retraction Settings to Reduce Stringing
One of the few common issues that we see with PETG is stringing. These strings are thin hairs, similar to a spider web, that run between the different surface of your 3D print. Preventing these strings requires precisely calibrated retraction settings, so make sure to adjust your retraction distance and speed for the best results. Simplify3D also includes several useful features that can further reduce stringing. The first is called Coasting, which works by reducing the pressure in the nozzle right before the end of a segment. This way, when moving to the next segment, there is less pressure in the nozzle, so you are less likely to see stringing and oozing during that move. Another great option can be found on the Advanced tab of your Simplify3D process settings. By enabling the “avoid crossing outline for travel movements” option, the software will automatically adjust the travel movements of your print to stay on top of the interior of your model as much as possible. This means that the strings stay inside of your part where no one can see them, instead of being on the outside of your model. If you are looking for more tips to reduce stringing, we have an entire section dedicated to this issue on our Print Quality Guide: How to Reduce Stringing and Oozing.
Optimize Extruder Settings to Prevent Blobs and Zits
When 3D printing at higher temperatures associated with PETG, you may notice small blobs or zits on the surface of your model. These print defects typically occur at the beginning or end of each segment, where the extruder has to suddenly start or stop extruding plastic. There are several ways to eliminate these print defects such as enabling “Extra Restart Distance” or “Coasting” options located in the Extruder tab. Simplify3D also includes an option to perform a dynamic retraction, where the filament is retracted while the extruder is still moving. This completely eliminates blobs that are typically formed from a stationary retraction. To learn more about these features and other tips for reducing blobs on the surface of your print, please refer to our Print Quality Guide.
Pro-Tips
- The glossy surface of PETG is especially useful when using rafts. The part separates easily from the raft and maintains a clean surface finish.
- Try disabling your part cooling fan for the first few layers of the print to prevent warping. This trick especially works well for larger prints.
Get Started with PET / PETG
Now that you are ready to start printing with PET / PETG, here are a few ideas to help you get started – from common applications to popular filament brands.
Common Applications
- Water proof applications
- Snap fit components
- Planter Pot
Sample Projects
- Self-watering Planter
- Water Bottle
- Snap Fit Parts
Popular Brands
- ColorFabb PETG
- eSun PETG
- E3D Spoolworks Edge
- Hatchbox PETG
- HobbyKing PETG
types, applications and features
3D printing enables rapid and cost-effective prototyping and production of models for a wide range of applications. But choosing the right 3D printing technology is only one side of the coin. Ultimately, the ability to create models with the required mechanical properties, functional characteristics or appearance will depend on the materials.
This comprehensive guide provides information on the most popular plastic and metal 3D printing materials available, compares their properties and applications, and provides guidance on how to select the most suitable material for your project.
Interactive Material
Need help choosing your 3D printing material? Our new interactive materials wizard will help you select the right material from our growing range of polymers, based on your intended application and the properties that matter most to you.
Get material recommendations
Dozens of plastic materials are available for 3D printing. Each of them has unique properties suitable for specific applications. To make it easier to find the best material for a particular model or product, let's first look at the main types of plastics and the various 3D printing processes.
There are two main types of plastics:
-
thermoplastics are the most common type of plastics. The main feature that distinguishes them from thermosetting plastics is their ability to withstand multiple melting and solidification cycles. Thermoplastics can be heated and shaped into desired shapes.
This process is reversible because no chemical bond is formed. As a result, they can be recycled or melted down and reused. Thermoplastics can be compared to butter: it melts and hardens many times. With each melting cycle, the properties of thermoplastics change slightly.
-
thermoset plastics (also called thermosets) remain permanently solid after polymerization. The polymers in thermosetting plastics are crosslinked during the polymerization process, which is induced by heat, light, or appropriate radiation. Thermoset plastics decompose when heated, rather than melt. In addition, they do not change their shape when cooled. It is not possible to recycle thermosetting plastics or restore the material to its original state. Thermosetting is like pie dough: once baked, the pie cannot be melted back into dough.
The three most common plastic 3D printing processes today are:
-
Fused Deposition Modeling (FDM) 3D printers melt and extrude thermoplastic filaments, which the printer's nozzle deposits layer by layer on the work area.
-
The Stereolithography (SLA) 3D Printer uses a laser to photopolymerize thermoset liquid polymers into a hardened plastic.
-
The Selective Laser Sintering (SLS) 3D Printer is equipped with a high power laser to sinter fine particles of thermoplastic powder.
How-to video
Can't find the 3D printing technology that best suits your needs? In this video tutorial, we compare Fused Deposition Modeling (FDM), Stereolithography (SLA), and Selective Laser Sintering (SLS) technologies in terms of the top factors to consider when purchasing.
Watch video
Fused fusion modeling (FDM), also known as fused filament manufacturing (FFF), is the most common form of consumer grade 3D printing, fueled by the rise of hobbyist 3D printers.
This method is well suited for making basic experimental models, as well as for quickly and inexpensively prototyping simple products, such as parts that are usually machined.
Consumer grade FDM has the lowest resolution and accuracy of any other plastic 3D printing process, making it unsuitable for printing complex designs or models with intricate features. It is possible to improve the surface quality of models printed using this technology using chemical and mechanical polishing processes. FDM-based industrial 3D printers, which offer a wider range of engineering thermoplastics, can solve these problems, but are also much more expensive.
Each layer is formed with a thermoplastic thread. Sometimes, if the layers are not completely adjacent to each other, there may be voids between them. As a result, anisotropic models are obtained, which is important to consider when designing products that must withstand load and be resistant to tension.
FDM 3D printing materials are available in a variety of colors. There are also various experimental mixtures of thermoplastic threads designed to create models with a surface that mimics wood or metal.
The most common materials for 3D printing in FDM technology are ABS (acrylonitrile butadiene styrene), PLA (polylactic acid) and various mixtures of these polymers. More advanced FDM printers can also print on other materials with different properties, such as increased temperature and chemical resistance, impact resistance, and rigidity.
Material | Features | Methods of use | |||||
---|---|---|---|---|---|---|---|
ABS (acrylonitril-butadien-styrol) | Strong and durable Thermal and impact-resistant need for a heated printing platform | Easiest media to print with FDM technology Strong, tough but brittle Less resistant to temperature and chemicals The biodegradable does not have a smell of | Conceptual models Realistic prototypes | ||||
PETG (polyethylenertalatlatglycol) | is compatible with low printing temperatures . ![]() | Waterproof application Clip-on components | |||||
nylon | Hard, durable and light Strong and partially flexible heat -resistant and shockproof Complex for printing using FDM | Functional Prototypes Basement models | TPU (thermal polyurate) | 9008 9008 9008 9008 9008 9008 9008 9008 Excellent vibration dampingFlexible Prototypes | |||
PVA (polyvinyl alcohol) | Soluble support structure material The material for supporting structures | ||||||
impact -resistant polystyrene | The material for creating soluble supporting structures, the most commonly used with ABS | Material for supporting structures | |||||
Composit materials (carbon, composite composite materials are dissolved in water. Kevlar, fiber optic) | Strong, tough and incredibly hard Only compatible with some expensive industrial 3D printers based on FDM technology | Functional prototypes Clamping fixtures, fixtures, tooling |
Invented in the 1980s, stereolithography is the world's first 3D printing technology and is still one of the most popular among professionals today.
Models printed with stereolithography printers have the highest resolution and accuracy, the sharpest detail and the smoothest surface of any other plastic 3D printing technology. Resin 3D printing is a great option for producing highly detailed prototypes that require tight tolerances and smooth surfaces such as molds, templates, and functional models. Models printed using SLA technology can be easily polished and/or painted after printing, resulting in highly detailed finished products.
Models printed on SLA 3D printers are generally isotropic: their strength is more or less constant and independent of orientation, since chemical bonds occur between each layer. This results in models with predictable mechanical characteristics critical for applications such as fasteners, fixtures, finished products, and functional prototypes.
Stereolithography supports a wide range of plastic 3D printing materials.
SLA 3D printing is versatile and provides a wide range of optical, mechanical and thermal properties that match those of standard, engineering and industrial thermoplastics.
Materials of FORMLABS | Characteristics | Methods of use | |
---|---|---|---|
Standard polymers | High resolution Smote, matte surface | Conceptual models 958 Conceptual models | Conceptual Models Realistic prototypes |
Clear Resin | The only truly transparent material for 3D printing from plastics can be polished to almost complete optical transparency | models, which should be optically transparent | |
DRAFT REDI | One of the fastest 3D printing materials Prints 4x faster than standard resins and 10x faster than FDM | Initial prototypes Rapid iterations | |
Tough Resin and Durable Resin | Materials that are tough, strong, functional and dynamic Able to withstand compression, tension, bending and impact without breaking Various materials with properties similar to ABS | Enclosures and Enclosures Clamps and Mounting Devices Connectors Wear Prototypes | |
Rigid Resins | Highly filled, stiff and strong material, resistant to bending Resistant to temperature and chemicals Maintains dimension under load | Clamping and clamping fixtures, tooling Turbines and fan blades Fluid/air components Electrical enclosures and enclosures used in the automotive industry | |
High Temp Resin | High temperature resistant High Precision | Hot Air, Gas, and Liquid Components Heat Resistant Fasteners, Housings, and Fixtures Molds and Inserts | |
Flexible Resin and Elastic Resin | Flexibility of Rubber, TPU, or Silicone compression Withstand many successive cycles without wear | Consumer product prototypes Foldable structures for robotics Medical devices and anatomy models Props and models for special effects | |
Medical and dental resins | A wide range of biocompatible resins for the manufacture of medical and dental products | Dental and medical products, including surgical templates, dentures and prosthetic limbs | |
Lost Wax and Vulcanized Rubber Casting Materials Easy to cast, allows for intricate designs and retains shape well | Products for trying on Models for reusable press forms Jewelry to order | ||
Ceramic Resin | Surface System, similar to the Firing Personal Product, the possibility of firing for creating a real ceramic product | Technical survival Unique articles 908 |
Sample
Experience Formlabs print quality for yourself. We will send a free print sample directly to your office.
Request a free sample
Selective laser sintering (SLS) 3D printing is a technology trusted by engineers and manufacturers across industries to create durable and functional models. With its low model cost, high performance, and use of common materials, this technology is well suited for a wide range of applications, from rapid prototyping to low-volume production, limited trial runs, or custom-made products.
The green powder supports the model during printing and eliminates the need for special support structures. As a result, SLS is ideal for complex geometries, including internal features, undercuts, thin walls, and negative draft features.
Like stereolithography, SLS produces more isotropic models than FDM models. Models created with SLS technology have a slightly rough surface due to powder particles, but have almost no visible layer lines.
SLS 3D printing materials are ideal for a range of functional applications, from consumer product design to manufacturing and healthcare applications.
Compared to FDM and SLA technologies, SLS technology allows the use of a limited number of materials. However, the available materials have excellent mechanical properties. They have strength comparable to die-cast models. The most common selective laser sintering material is nylon, a popular engineering thermoplastic with excellent mechanical properties. Nylon is light, strong and flexible, resistant to impact, heat, chemicals, UV radiation, water and dirt.
Material | Description | Methods of use |
---|---|---|
Nylon 12 Powder | Strong, hard and durable Siberian, Solp. water | Functional prototypes End use products Medical devices |
Nylon 11 Powder | Similar properties to Nylon 12 Powder. Possesses greater elasticity, elongation at break and impact resistance, but less rigidity | Functional prototypes Products for the final use of Medical devices |
TPU | Flexible, elastic, elastic resistant to deformation High resistance to ultraviolet Excellent damping capacity | .![]() Medical devices |
Nylon composites | Nylon materials reinforced with glass, aluminum or fiberglass for greater strength and rigidity | Functional Prototypes Structural End-Use Products |
Sample
Experience Formlabs SLS print quality for yourself. We will send a free print sample directly to your office.
Request a free sample
Different 3D printing materials and processes have their own advantages and disadvantages that make them suitable for different scenarios. The following table provides a brief overview of some of the main features and factors to consider.
Poor detail
Limited conformance to design design
High cost of industrial devices if precision and high performance materials are required
Basic experimental models
Production of special end-use products using professional industrial devices and materials
Templates, molds and tooling
Dental products
Prototypes and molds for casting jewelry
Props and models
Small-scale production, production of limited trial runs, creation of products to order
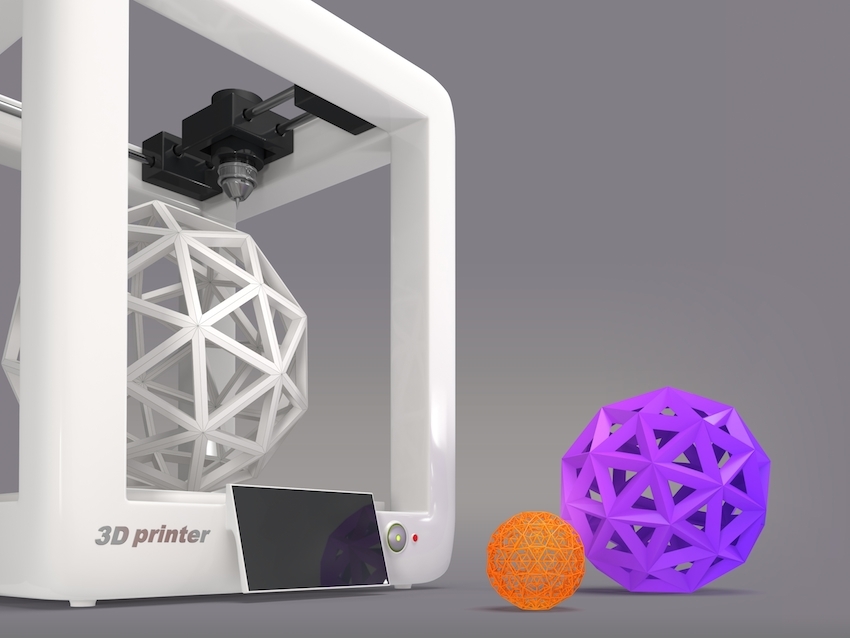
There are several 3D printing processes not only from plastics, but also from metals.
Metal FDM printers are similar in design to traditional FDM printers, but use extruded metal rods held in place by a resin binder. The finished models are in an intermediate state and then sintered in an oven to remove the binder.
SLM and DMLS printers are similar to SLS printers, but instead of polymer powders, they fuse metal powder particles layer by layer using a laser. 3D printers based on SLM and DMLS technologies can create strong, precise and complex metal products, making this process ideal for the aerospace, automotive and medical industries.
-
Titanium is a light metal with excellent mechanical properties. It is strong, hard and highly resistant to heat, oxidation and acids.
-
stainless steel has high strength, ductility and corrosion resistance.
-
aluminum is a lightweight, durable, strong metal with good thermal properties.
-
Tool Steel is a hard, scratch-resistant material that can be used to print end-use tools and other high-strength products.
- nickel alloys have high tensile, creep and tensile strength, as well as heat and corrosion resistance.
Compared to plastic 3D printing technologies, metal 3D printing is much more expensive and difficult, and therefore beyond the reach of most companies.
As an alternative to casting workflows that produce metal models cheaper and faster than traditional methods and provide greater design freedom, SLA 3D printing is well suited.
Another alternative is galvanization of SLA printed models. It involves applying a layer of metal to plastic using electrolysis. This combines some of the best qualities of metal (strength, electrical conductivity, corrosion and abrasion resistance) with the special properties of the base (usually plastic) material.
Plastic 3D printing is well suited for creating templates that can be cast to produce metal models.
With so many materials and options available for 3D printing, making the right choice can be difficult.
We provide a 3-step process for selecting the right material for 3D printing.
Plastics used for 3D printing have different chemical, optical, mechanical and thermal characteristics that affect the properties of 3D printed models. As you move from the intended use case to the actual operating environment, the performance requirements increase accordingly.
Requirement | Description | Recommendations |
---|---|---|
Low Efficiency | Example: Prototype mold for a ladle for ergonomic testing. | FDM PLA SLA: Standard Resins, Clear Resin (transparency), Draft Resin (fast) |
Medium Efficiency | For validation or pre-production use, printed models should have properties as close as possible to those of final production models , for functional testing, but do not meet stringent requirements regarding service life. Example: housing for electronic components to protect against sudden impacts. Functional characteristics include the ability to absorb impact energy. In addition, the body must snap into place and retain its shape. | FDM ABS SLA: Engineering Resins SLS: Nylon 11 Powder, Nylon 12 Powder, TPU |
High Efficiency | Final 3D printed models need to be highly stable to achieve end use products to wear and tear over a certain period of time, whether it be a day, a week or several years.![]() Example: shoe soles. Functional features include rigorous cycling and unloading life testing, color fastness over many years, and tear resistance, among other things. | FDM Composites SLA: Engineering, Medical, Dental or Jewelry Resins SLS: Nylon 11 Powder, Nylon 12 Powder, TPU, Nylon Composites |
material requirements: material properties that will satisfy these requirements. These indicators are usually given in the technical specifications of the material.
Requirement | Description | Recommendation | |
---|---|---|---|
Tensile strength | Resistance of material to fracture under tension. High tensile strength is important for structural, load-bearing, mechanical or static models. | FDM PLA SLA: Clear Resin, Rigid Resin SLS: Nylon 12 Powder, Nylon Composites | |
Flex Modulus | Material resistance to bending under load.![]() | FDM PLA (high), ABS (medium) SLA: Rigid Resin (high), Tough Resin and Durable Resin (medium), Flexible Resin and Elastic Resin (low) SLS: Nylon composite materials (high value), Nylon 12 Powder (medium value) | |
Elongation | Material resistance to tensile failure. Allows you to compare the degree of stretching of flexible materials. It also indicates whether the material is stretched or immediately destroyed. | FDM ABS (medium), TPU (high) SLA: Tough Resin and Durable Resin (medium), Flexible Resin and Elastic Resin (high) SLS: Nylon 12 Powder (medium), Nylon 11 Powder (medium), TPU (high) | |
Impact strength | The ability of a material to absorb impact and its energy without breaking. Shows toughness and durability. Allows you to determine how easily the material breaks when it falls to the ground or collides with another object.![]() | FDM ABS, Nylon SLA: Tough 2000 Resin, Tough 1500 Resin, Gray Pro Resin, Durable Resin SLS: Nylon 12 Powder, Nylon 11 Powder a certain load. Indicates whether the material is suitable for high temperature applications. | SLA: High Temp Resin, Rigid Resin SLS: Nylon 12 Powder, Nylon composites |
Hardness (durometer) | Material resistance to surface deformation. Allows you to determine the right degree of plasticity for soft plastics such as rubber and elastomers for a particular application. | FDM TPU SLA: Flexible Resin, Elastic Resin SLS: TPU | |
Tear resistance | Material resistance to notching under tension. This indicator is important for evaluating the durability and wear resistance of soft plastics and flexible materials such as rubber. | FDM TPU SLA: Flexible Resin, Elastic Resin, Durable Resin SLS: Nylon 11 Powder, TPU | |
Creep | Creep is the tendency of a material to permanently deform under the influence of constant stress: tension or bending, compression, shear .![]() | FDM ABS SLA: Rigid Resin SLS: Nylon 12 Powder, Nylon 9 composites0092 | |
Compression set | Irreversible deformation after material compression. An important indicator for soft plastics and applications where elasticity is needed. Indicates whether the material will restore its original shape after the load is removed. | FDM TPU SLA: Flexible Resin, Elastic Resin SLS: TPU |
For more information on material properties, see our guide to the most common mechanical and thermal properties.
By converting performance characteristics into material requirements, you can most likely find out which material, or small group of materials, is right for your application.
If several materials meet your basic requirements, a broader range of desired characteristics, as well as the advantages and disadvantages of these materials and processes, can be considered for the final selection.
Use our interactive material wizard. It will help you select the right materials from our growing range of polymers for your application and the properties that matter most to you. Do you have specific questions about 3D printing materials? Contact our experts.
Get Material Recommendations
Carbon Fiber 3D Printing Guide: Printers & Materials
Bicycles, racing cars, drones and tennis rackets all have a variety of applications and require high strength and durability without added weight. This combination of properties is typical of carbon fiber composites, which are used in everything from Formula 1 racing car chassis to lightweight road bike frames.
Since many 3D printers usually use polymer-based materials, including various composites, many people ask the question: "Can a 3D printer print carbon fiber?".
Indeed, there are two methods by which 3D printing can be used to create carbon fiber parts: supporting traditional fabrication methods with 3D printed molds, or direct 3D printing of carbon fiber composites. In this article, we'll look at traditional fabrication methods as well as new workflows for 3D printed carbon fiber molds and direct 3D printed carbon fiber composite parts.
Combining traditional carbon fiber parts with 3D printing
Carbon fiber is a composite material traditionally made by weaving long strands of carbon fibers together and then bonding them with a polymer. The yarns can be woven strategically so that the strength is directed along one specific vector, or so that the final product has multiple strengths in all directions. The resulting material is then molded into the desired end product using one of three processes: wet laid, pre-laminated, or resin transfer molding (RTM).
Wet Laid
Wet laid carbon fiber sheets are cut and pressed in a mould, then dyed with a liquid resin that cures to bind the sheets into the desired final shape. This method requires the least equipment and is the easiest to master for a beginner. Because most of the work can be done by hand, this is one of the cheapest methods, but the trade-off is that the resulting parts are less accurate to the master mold than parts made by other methods.
Prepreg lamination
In this method, the carbon fiber is already impregnated with resin and then placed in a mold that uses pressure and heat to form the final shape. This method is the most expensive due to the need for specialized equipment to store and process the pre-impregnated sheets, as well as a heated and pressurized forming machine. These factors also make it the most repeatable and consistent, and thus the most suitable for serial production of carbon fiber parts.
Resin transfer molding (RTM)
In RTM molding, the dry fiber is inserted into a two-part mold. The mold is clamped, after which high-pressure resin is injected into the cavity. This method is usually automated and is used to produce large volumes of products.
3D printed carbon fiber parts
For each of the previous three methods, 3D printing can be used to reduce costs and improve production times. All three traditional manufacturing methods require the use of a mold or multiple molds, which are traditionally created through labour-intensive subtractive processes such as wood, foam, metal, plastic or wax. 3D printing offers an alternative way to make molds. 3D printed molds are customizable and are more efficient and cost effective for small batch or custom production.
For applications requiring live prototypes, such as the automotive and aerospace industries, the iterative process can require hundreds of different shapes. Producing such iterations with traditional manufacturing methods can be costly and time consuming, so 3D printing provides an efficient way to produce small batches. Although 3D printed molds are not as suitable for high-volume production as metal molds, they can be created in-house, reducing costs, speeding up product development and validation, and short-term production.
Carbon fiber molds can be made in a variety of ways, but the smooth surface and wide choice of materials for SLA 3D printers make them a common choice for mold making in the factory. SLA-created parts have virtually no layer lines or porosity, so carbon fiber sheets can be pressed tightly into the mold without the fear of creating a textured surface.
Panoz, a manufacturer of racing and sports cars, needed a custom race car cabin duct to bleed the air out of the cabin and cool the temperature inside. In collaboration with DeltaWing Manufacturing, they used a Formlabs SLA 3D printer to print a high temperature resin part and then manually molded that printed part using high temperature epoxy for tooling. By using 3D printing, DeltaWing avoided outsourcing the costly metal mold for this custom carbon fiber part, reducing overall costs and delivery times.
Carbon fiber wing duct next to two piece mold printed with High Temp Resin made by DeltaWing Manufacturing.
Direct Carbon Fiber 3D Printing
Looking for the best carbon fiber 3D printer? There is a strong demand for workflows that combine the strength, durability and wear resistance of traditional carbon fiber parts with the maneuverability, geometric capabilities and cycling of 3D printing. Therefore, it is not surprising that there are many companies offering 3D printing using carbon fiber, with two methods currently available: printing using chopped or continuous fibers.
Chopped Carbon Fiber 3D Printing
Chopped Fiber refers to 3D printing composite plastic materials that are impregnated with small pieces of carbon fibers. These crushed fibers add strength to the composite, which can be carbon fiber filament for FDM modeling or nylon powder for SLS 3D printing.
The main advantages of chopped carbon fiber reinforced materials over other types based on polymers are that they are strong, light, heat resistant and less prone to deformation. Compared to traditionally molded carbon fiber parts, chopped fiber 3D printing provides increased geometric flexibility in part design, especially in SLS 3D printing, potentially eliminating the labor involved with traditional molding or opening up innovative new opportunities for users to incorporate this material into the working process.
The Formlabs Fuse 1+ 30W SLS 3D Printer enables this type of carbon fiber 3D printing with Nylon 11 CF Powder, the strongest material in the Formlabs SLS material library. Fuse 1+ 30W is the most affordable high performance SLS printing option for shredded carbon fibers. Although traditional industrial SLS machines also offer some carbon fiber materials, the initial implementation costs negate much of the added value of 3D printing carbon fiber parts over RTM or prepreg lamination methods.
Formlabs Nylon 11 CF Powder is strong, lightweight and heat resistant making it ideal for the automotive, aerospace and manufacturing industries .
Many FDM 3D printers can handle carbon fiber filaments, but these materials are more difficult to print than standard ABS or PLA filaments, resulting in more clogs and more maintenance as the brass nozzles wear out. FDM 3D printers specifically designed to grind carbon fiber filaments are also available but are more expensive.
The main limitation of chopped-fiber printed parts using both SLS and FDM technologies is that they should be considered as more durable 3D printed parts, rather than a true alternative to traditional woven and continuous carbon fiber parts. fibers. They also provide the greatest increase in strength by positioning them in the X-plane direction for SLS printing, and in the XY-plane direction for FDM printing. Traditional methods of creating carbon fiber parts provide multidirectional strength through careful planning and placement of different carbon fiber sheets in a preform.
Carbon Fiber Continuous 3D Printing
Carbon Fiber Continuous 3D Printing is available on some dedicated FDM 3D printers, and the resulting parts are close in strength to traditional carbon fiber parts, but similar to chopped fiber printers FDM, only in the XY plane. In such printers, continuous filaments of carbon fiber are mixed with a thermoplastic and the filaments can be applied strategically to selectively pressurize certain planes or axes. This method can use either a dual extruder nozzle to lay down a combination of carbon fiber and polymer filaments, or a 2-in-1 in which one nozzle lays down the carbon fiber filaments and the other heats and extrudes the filament.
Continuous carbon fiber 3D printing offers an alternative comparable to traditional molded carbon fiber parts, albeit with limited design freedom. While these parts are incredibly strong, strength only appears in the XY planes and the models must be oriented so that their strength matches the direction of the applied force. In designs where possible, this method can be used to replace aluminum parts, as well as to create durable manufacturing aids or end-use parts.
Applications for 3D printed carbon fiber parts
The high strength, light weight, and impact, heat and chemical resistance of carbon fiber printed parts make them ideal for a variety of applications where 3D printing has never been before. was not considered. Now, these plastic and carbon fiber composite parts can withstand the heat generated by automotive or aerospace engine components, be used as a replacement for machined aluminum parts and manufacturing fixtures, and produce durable and impact-resistant equipment.
3D printed carbon fiber parts are ideal for rapid prototyping, the production of wear-resistant and durable production fixtures such as tooling and fixtures, and for low-volume production of durable end-use parts with complex geometries.
3D printing technology has opened up new possibilities in design and manufacturing, and 3D printing of carbon fiber composites has further expanded these possibilities, allowing users in the automotive, aerospace, defense, and manufacturing industries to quickly and efficiently produce high-strength, heat-resistant, geometrically flexibility. By bypassing traditional machining or molding processes, these users can more easily create custom parts, replacement parts and functional prototypes. Although carbon fiber printed parts are not a complete replacement for traditional technologies due to the single plane of added strength, they are still stronger than almost all other plastics, making them exceptionally useful in many applications.
The right process for producing carbon fiber parts by molding or directly by 3D printing depends largely on the specific application and factors such as part design, production volume, and more. SLS 3D printing with shredded fibers offers the best option for those who want to produce parts that are strong, but not necessarily to the same degree as traditional molded carbon fiber parts.
Formlabs Fuse 1+ 30W with Nylon 11 CF Powder enables low-funding, fast-paced businesses to quickly iterate and produce end-parts with strength and better mechanical properties than traditional plastics. They can also functionally test their parts and then redesign with only minor CAD changes, improving their product performance and getting to market faster.