3D printing service nashville
3D Printing Service for Nashville, Tennessee
CapabilitiesCustom Online 3D Printing ServiceTennesseeNashville
High Quality Nashville, Tennessee 3D Printing | 60+ Materials Available
Endless Options
Choose from millions of possible combinations of materials, finishes, tolerances, markings, and certifications for your order.
Easy to Use
Get your parts delivered right to your door without the hassle of sourcing, project management, logistics, or shipping.
Quality Assurance
Our number one job at Xometry is making your custom parts to your specifications.
Your Nashville, Tennessee 3D Printing Service: 3D Prototypes and Production Parts
A Global Leader in Industrial-Grade 3D Printing
Xometry is an industry-leading 3D printing service. Whether you need prototypes or production parts, we can make them for you in as fast as a day. We are your one-stop-shop for accurate, precise custom 3D printed parts at a low cost. Upload your 3D CAD file to get a quote and lead time within seconds. We use the latest additive manufacturing processes to build affordable functional prototypes & end-use parts in over 60 metals and plastics.
We offer eight high-quality 3D printing processes including selective laser sintering, fused deposition modeling, stereolithography, direct metal laser sintering, polyjet, Carbon DLS, binder jet metal, and HP Multi Jet Fusion. We use commercial and industrial-grade printers such as Stratasys Fortus 900mc and Fortus 450 FDM, EOS Polymer Laser Sintering (SLS) and DMLS, Concept Laser, SLM Solutions, 3D Systems, ExOne, and more.
Xometry's High Quality 3D Printing Services
Selective Laser Sintering (SLS)
Selective Laser Sintering (SLS) is a powerful 3D printing technology that produces highly accurate and durable parts that are capable of being used directly in end-use, low-volume production, or for rapid prototyping.
An additive manufacturing layer technology, SLS involves the use of a high power laser (for example, a carbon dioxide laser) to fuse small particles of plastic powders into a mass that has a desired three-dimensional shape. The laser selectively fuses powdered material by scanning cross-sections generated from a 3-D digital description of the part (for example from a CAD file or scan data) on the surface of a powder bed. After each cross-section is scanned, the powder bed is lowered by one layer thickness, a new layer of material is applied on top, and the process is repeated until the part is completed.
Download the SLS Design Guide.
Stereolithography (SLA)
Stereolithography (SLA) is a robust 3D printing technology that produces extremely accurate and high-resolution parts that are capable of being used directly in end-use, low-volume production, or for rapid prototyping.
SLA is an additive manufacturing process that focuses an ultraviolet (UV) light on a vat of photopolymer resin. It offers higher resolution printing than many other 3D printing technologies, allowing customers to print parts with fine details and surface finishes. SLA 3D printing is a highly-versatile platform for making custom parts in prototype and production settings; often acting as a stand-in for injection-molded plastic parts.
Xometry offers both standard and high-resolution options for fine detail parts, and can also print larger sized parts and products, with some materials offering up to a 58" inch build area. In addition, Xometry's manufacturing partner network allows us to offer a larger variety of materials than other 3D printing companies - we offer a wide range of both Accura and Somos brand materials.
Download the SLA Design Guide.
Fused Deposition Modeling (FDM)
Fused Deposition Modeling (FDM) is a 3D printing technology widely known for its speed, accuracy, and competitive cost. A machine precisely extrudes melted plastic filament to create a part. Parts are very rigid, especially compared to Selective Laser Sintering (SLS), which makes them a great fit for projects with a rigidity requirement. Xometry's FDM solution offers large build volumes up to 24″ x 36″ x 36″, a variety of colors, and a diverse selection of production-grade thermoplastics — from ABS to Polycarbonate to Ultem.
Download the FDM Design Guide.
HP Multi Jet Fusion (HP MJF)
HP Multi Jet Fusion is a new 3D printing technology that produces highly accurate and durable parts that are capable of being used directly in end-use, low-volume production, or for rapid prototyping. Since the process uses well-established 2D printing ink-jetting, it has remarkably fast layer times compared to other powder bed fusion technologies.
Download the HP Multi Jet Fusion Design Guide.
PolyJet 3D (PJ3D)
PolyJet 3D is a 3D printing technology known for its customizable material properties and excellent surface finish. It works by jetting UV curable resin onto a build tray in a process that is somewhat similar to inkjet printing. PolyJet 3D printing offers one of the most advanced industrial 3D printing solutions available, producing parts with incredible precision and speed. It also supports a wide variety of build materials including rigid and rubber-like plastics. Xometry's PolyJet solution has a maximum build envelope of 19. 3 × 15.4 × 7.9 in. (490 × 390 × 200 mm) in a variety of colors and materials.
Download the PolyJet 3D Design Guide.
Direct Metal Laser Sintering (DMLS)
Direct Metal Laser Sintering (DMLS) is an 3D metal printing technology that builds prototype and production metal parts from a CAD file using a laser to selectively fuse a fine metal powder in either stainless steel or aluminum materials. A DMLS machine is capable of producing highly complex features and all-in-one assemblies using metal materials that would be difficult to achieve with subtractive manufacturing techniques.
Our DMLS metal 3D printing service typically offers build volumes up to 250 x 250 x 325 mm, but we may be able to accommodate larger part volumes upon request in the quote. (See our Manufacturing Standards for more details) A good first step is to find out the cost of the parts you need using DMLS and compare them to other 3D printing processes and CNC machining.
Download the DMLS Design Guide.
Carbon DLS™
Carbon DLS™ uses digital light projection, oxygen-permeable optics, and programmable liquid resins to produce products with end-use durability, resolution and surface finish. This 3D printing technology is called Digital Light Synthesis™, or DLS for short. Another legacy term for the process is Continuous Liquid Interface Production (CLIP). Along with Carbon’s custom liquid resins, DLS unlocks new business opportunities and product designs previously impossible, including mass customization and on-demand inventory of end-use products.
Carbon bridges, and sometimes substitutes, for processes like Urethane Casting and Injection Molding service production, because the materials are urethane-based or epoxy-based, giving excellent mechanical properties. There are even elastomer and silicone resins that outperform most additive manufactured rubber-like materials.
The typical build area is 7.4” x 4.6” x 12.8”. Parts with dimensions exceeding 4” x 4” x 6” will require manual review.
Download the Carbon DLS Design Guide.
Metal Binder Jetting
With binder jetting, an inkjet print head quickly deposits a bonding agent onto a thin layer of powdered particles -- either metal, sand, ceramics or composites. This process is repeated, layer-by-layer, using a map from a digital design file, until the object is complete. Binder jetting is offered through our Digital RFQ Marketplace through Xometry's partnership with ExOne.
Download the Binder Jetting Design Guide.
Locations near Nashville, Tennessee
Bowling Green
KentuckyHuntsville
AlabamaOwensboro
KentuckyChattanooga
TennesseePaducah
KentuckyEvansville
IndianaLouisville
KentuckyKnoxville
TennesseeLexington
KentuckyBirmingham
AlabamaMemphis
TennesseeBloomington
IndianaTuscaloosa
AlabamaAtlanta
GeorgiaTerre Haute
IndianaCincinnati
OhioAsheville
North CarolinaAthens
GeorgiaIndianapolis
IndianaSaint Louis
Missouri
Ready to start making custom 3D printed parts?
3D Printing Service Nashville, TN | Instant Quotes Online
Our 3D printing capabilities
We have over 90 3D printing shops in our network and are well known for manufacturing high-quality parts at competitive prices, from rapid prototyping with Fused Deposition Modeling (FDM) to functional end parts made with Selective Laser Sintering (SLS) or Multi Jet Fusion (MJF).
Gallery of 3D printed parts manufactured by Hubs
With over 65,000 customers from every industry, including aerospace, defense, robotics, medical, machinery, automotive and electronics, we have extensive experience meeting a diverse range of 3D printing requirements, from prototyping to production: Visual aids, concept models, injection-molding prototypes, form-fit & function prototypes, tooling and casting patterns, jigs, grips and fixtures, and durable end parts.
HP PA 12 - Dyed Black
Customer | True North Design |
Purpose | Structural and vacuum EOAT components |
Process | SLS / MJF |
Unit price | $69.23 / $34.33 |
Industry | Automotive |
Prototyping PLA
Customer | Allision Conner |
Purpose | End caps and cable strain relief for sheet metal enclosure |
Process | FDM |
Unit price | $7.![]() |
Industry | Industrial Automation |
HP PA 12
Customer | US Hammer |
Description | A part for gasoline engine powered jackhammers |
Process | MJF |
Unit price | $22.18 |
Industry | Construction |
Markforged Onyx - Black
Customer | Autocom Manufacturing |
Purpose | A production part for 3D printed lathe gantry gripper fingers |
Process | FDM |
Unit price | $48.86 |
Industry | Automotive |
PC Stratasys - white
Customer | Terumo medical corporation |
Purpose | Prototyping parts used for a disposable electrical device |
Process | FDM |
Unit price | $55.![]() |
Industry | Medical |
Formlabs Clear Resin
Customer | Aversan Inc |
Purpose | A prototyping part of an injection molded component for an automated door mechanism |
Process | SLA |
Unit price | $29.83 |
Industry | Aerospace |
HP PA 12 - Dyed Black
Customer | True North Design |
Purpose | Structural and vacuum EOAT components |
Process | SLS / MJF |
Unit price | $69.23 / $34.33 |
Industry | Automotive |
Prototyping PLA
Customer | Allision Conner |
Purpose | End caps and cable strain relief for sheet metal enclosure |
Process | FDM |
Unit price | $7.![]() |
Industry | Industrial Automation |
HP PA 12
Customer | US Hammer |
Description | A part for gasoline engine powered jackhammers |
Process | MJF |
Unit price | $22.18 |
Industry | Construction |
Markforged Onyx - Black
Customer | Autocom Manufacturing |
Purpose | A production part for 3D printed lathe gantry gripper fingers |
Process | FDM |
Unit price | $48.86 |
Industry | Automotive |
PC Stratasys - white
Customer | Terumo medical corporation |
Purpose | Prototyping parts used for a disposable electrical device |
Process | FDM |
Unit price | $55.![]() |
Industry | Medical |
Formlabs Clear Resin
Customer | Aversan Inc |
Purpose | A prototyping part of an injection molded component for an automated door mechanism |
Process | SLA |
Unit price | $29.83 |
Industry | Aerospace |
HP PA 12 - Dyed Black
Customer | True North Design |
Purpose | Structural and vacuum EOAT components |
Process | SLS / MJF |
Unit price | $69.23 / $34.33 |
Industry | Automotive |
Prototyping PLA
Customer | Allision Conner |
Purpose | End caps and cable strain relief for sheet metal enclosure |
Process | FDM |
Unit price | $7.![]() |
Industry | Industrial Automation |
HP PA 12
Customer | US Hammer |
Description | A part for gasoline engine powered jackhammers |
Process | MJF |
Unit price | $22.18 |
Industry | Construction |
Markforged Onyx - Black
Customer | Autocom Manufacturing |
Purpose | A production part for 3D printed lathe gantry gripper fingers |
Process | FDM |
Unit price | $48.86 |
Industry | Automotive |
PC Stratasys - white
Customer | Terumo medical corporation |
Purpose | Prototyping parts used for a disposable electrical device |
Process | FDM |
Unit price | $55.![]() |
Industry | Medical |
Formlabs Clear Resin
Customer | Aversan Inc |
Purpose | A prototyping part of an injection molded component for an automated door mechanism |
Process | SLA |
Unit price | $29.83 |
Industry | Aerospace |
HP PA 12 - Dyed Black
Customer | True North Design |
Purpose | Structural and vacuum EOAT components |
Process | SLS / MJF |
Unit price | $69.23 / $34.33 |
Industry | Automotive |
Prototyping PLA
Customer | Allision Conner |
Purpose | End caps and cable strain relief for sheet metal enclosure |
Process | FDM |
Unit price | $7.![]() |
Industry | Industrial Automation |
HP PA 12
Customer | US Hammer |
Description | A part for gasoline engine powered jackhammers |
Process | MJF |
Unit price | $22.18 |
Industry | Construction |
Markforged Onyx - Black
Customer | Autocom Manufacturing |
Purpose | A production part for 3D printed lathe gantry gripper fingers |
Process | FDM |
Unit price | $48.86 |
Industry | Automotive |
PC Stratasys - white
Customer | Terumo medical corporation |
Purpose | Prototyping parts used for a disposable electrical device |
Process | FDM |
Unit price | $55.![]() |
Industry | Medical |
Formlabs Clear Resin
Customer | Aversan Inc |
Purpose | A prototyping part of an injection molded component for an automated door mechanism |
Process | SLA |
Unit price | $29.83 |
Industry | Aerospace |
HP PA 12 - Dyed Black
Customer | True North Design |
Purpose | Structural and vacuum EOAT components |
Process | SLS / MJF |
Unit price | $69.23 / $34.33 |
Industry | Automotive |
Prototyping PLA
Customer | Allision Conner |
Purpose | End caps and cable strain relief for sheet metal enclosure |
Process | FDM |
Unit price | $7.![]() |
Industry | Industrial Automation |
HP PA 12
Customer | US Hammer |
Description | A part for gasoline engine powered jackhammers |
Process | MJF |
Unit price | $22.18 |
Industry | Construction |
Markforged Onyx - Black
Customer | Autocom Manufacturing |
Purpose | A production part for 3D printed lathe gantry gripper fingers |
Process | FDM |
Unit price | $48.86 |
Industry | Automotive |
PC Stratasys - white
Customer | Terumo medical corporation |
Purpose | Prototyping parts used for a disposable electrical device |
Process | FDM |
Unit price | $55.![]() |
Industry | Medical |
Formlabs Clear Resin
Customer | Aversan Inc |
Purpose | A prototyping part of an injection molded component for an automated door mechanism |
Process | SLA |
Unit price | $29.83 |
Industry | Aerospace |
HP PA 12 - Dyed Black
Customer | True North Design |
Purpose | Structural and vacuum EOAT components |
Process | SLS / MJF |
Unit price | $69.23 / $34.33 |
Industry | Automotive |
Prototyping PLA
Customer | Allision Conner |
Purpose | End caps and cable strain relief for sheet metal enclosure |
Process | FDM |
Unit price | $7.![]() |
Industry | Industrial Automation |
HP PA 12
Customer | US Hammer |
Description | A part for gasoline engine powered jackhammers |
Process | MJF |
Unit price | $22.18 |
Industry | Construction |
Markforged Onyx - Black
Customer | Autocom Manufacturing |
Purpose | A production part for 3D printed lathe gantry gripper fingers |
Process | FDM |
Unit price | $48.86 |
Industry | Automotive |
PC Stratasys - white
Customer | Terumo medical corporation |
Purpose | Prototyping parts used for a disposable electrical device |
Process | FDM |
Unit price | $55.![]() |
Industry | Medical |
Formlabs Clear Resin
Customer | Aversan Inc |
Purpose | A prototyping part of an injection molded component for an automated door mechanism |
Process | SLA |
Unit price | $29.83 |
Industry | Aerospace |
HP PA 12 - Dyed Black
Customer | True North Design |
Purpose | Structural and vacuum EOAT components |
Process | SLS / MJF |
Unit price | $69.23 / $34.33 |
Industry | Automotive |
Prototyping PLA
Customer | Allision Conner |
Purpose | End caps and cable strain relief for sheet metal enclosure |
Process | FDM |
Unit price | $7.![]() |
Industry | Industrial Automation |
HP PA 12
Customer | US Hammer |
Description | A part for gasoline engine powered jackhammers |
Process | MJF |
Unit price | $22.18 |
Industry | Construction |
Markforged Onyx - Black
Customer | Autocom Manufacturing |
Purpose | A production part for 3D printed lathe gantry gripper fingers |
Process | FDM |
Unit price | $48.86 |
Industry | Automotive |
PC Stratasys - white
Customer | Terumo medical corporation |
Purpose | Prototyping parts used for a disposable electrical device |
Process | FDM |
Unit price | $55.![]() |
Industry | Medical |
Formlabs Clear Resin
Customer | Aversan Inc |
Purpose | A prototyping part of an injection molded component for an automated door mechanism |
Process | SLA |
Unit price | $29.83 |
Industry | Aerospace |
HP PA 12 - Dyed Black
Customer | True North Design |
Purpose | Structural and vacuum EOAT components |
Process | SLS / MJF |
Unit price | $69.23 / $34.33 |
Industry | Automotive |
Prototyping PLA
Customer | Allision Conner |
Purpose | End caps and cable strain relief for sheet metal enclosure |
Process | FDM |
Unit price | $7.![]() |
Industry | Industrial Automation |
HP PA 12
Customer | US Hammer |
Description | A part for gasoline engine powered jackhammers |
Process | MJF |
Unit price | $22.18 |
Industry | Construction |
Markforged Onyx - Black
Customer | Autocom Manufacturing |
Purpose | A production part for 3D printed lathe gantry gripper fingers |
Process | FDM |
Unit price | $48.86 |
Industry | Automotive |
PC Stratasys - white
Customer | Terumo medical corporation |
Purpose | Prototyping parts used for a disposable electrical device |
Process | FDM |
Unit price | $55.![]() |
Industry | Medical |
Formlabs Clear Resin
Customer | Aversan Inc |
Purpose | A prototyping part of an injection molded component for an automated door mechanism |
Process | SLA |
Unit price | $29.83 |
Industry | Aerospace |
HP PA 12 - Dyed Black
Customer | True North Design |
Purpose | Structural and vacuum EOAT components |
Process | SLS / MJF |
Unit price | $69.23 / $34.33 |
Industry | Automotive |
Prototyping PLA
Customer | Allision Conner |
Purpose | End caps and cable strain relief for sheet metal enclosure |
Process | FDM |
Unit price | $7.![]() |
Industry | Industrial Automation |
HP PA 12
Customer | US Hammer |
Description | A part for gasoline engine powered jackhammers |
Process | MJF |
Unit price | $22.18 |
Industry | Construction |
Markforged Onyx - Black
Customer | Autocom Manufacturing |
Purpose | A production part for 3D printed lathe gantry gripper fingers |
Process | FDM |
Unit price | $48.86 |
Industry | Automotive |
PC Stratasys - white
Customer | Terumo medical corporation |
Purpose | Prototyping parts used for a disposable electrical device |
Process | FDM |
Unit price | $55.![]() |
Industry | Medical |
Formlabs Clear Resin
Customer | Aversan Inc |
Purpose | A prototyping part of an injection molded component for an automated door mechanism |
Process | SLA |
Unit price | $29.83 |
Industry | Aerospace |
HP PA 12 - Dyed Black
Customer | True North Design |
Purpose | Structural and vacuum EOAT components |
Process | SLS / MJF |
Unit price | $69.23 / $34.33 |
Industry | Automotive |
Prototyping PLA
Customer | Allision Conner |
Purpose | End caps and cable strain relief for sheet metal enclosure |
Process | FDM |
Unit price | $7.![]() |
Industry | Industrial Automation |
HP PA 12
Customer | US Hammer |
Description | A part for gasoline engine powered jackhammers |
Process | MJF |
Unit price | $22.18 |
Industry | Construction |
Markforged Onyx - Black
Customer | Autocom Manufacturing |
Purpose | A production part for 3D printed lathe gantry gripper fingers |
Process | FDM |
Unit price | $48.86 |
Industry | Automotive |
PC Stratasys - white
Customer | Terumo medical corporation |
Purpose | Prototyping parts used for a disposable electrical device |
Process | FDM |
Unit price | $55.![]() |
Industry | Medical |
Formlabs Clear Resin
Customer | Aversan Inc |
Purpose | A prototyping part of an injection molded component for an automated door mechanism |
Process | SLA |
Unit price | $29.83 |
Industry | Aerospace |
Instant, online 3D printing quotes
-
Upload a CAD to start (STEP, STP, IGES, IGS, SLDPRT, 3DM, SAT, STL, OBJ or X_T)
-
Price updates in real-time as you change materials, lead time, etc..
-
No hidden costs. Our instant quotes are not just indications, but the actual price, and include shipping and customs up front.
Learn about how our quoting algorithm works
Our ordering process
Receive instant quote
Upload your CAD to our online quoting platform
Confirm specs
Configure your part specifications and select a lead time that suits your schedule
Production
We select the best manufacturer for your order, and production begins immediately
Quality control
We take full responsibility for making sure your parts are manufactured according to our standards
Delivery
Our 3D printing service has been rated 4.9/5
Over 266 customers are satisfied with our 3D printing service.
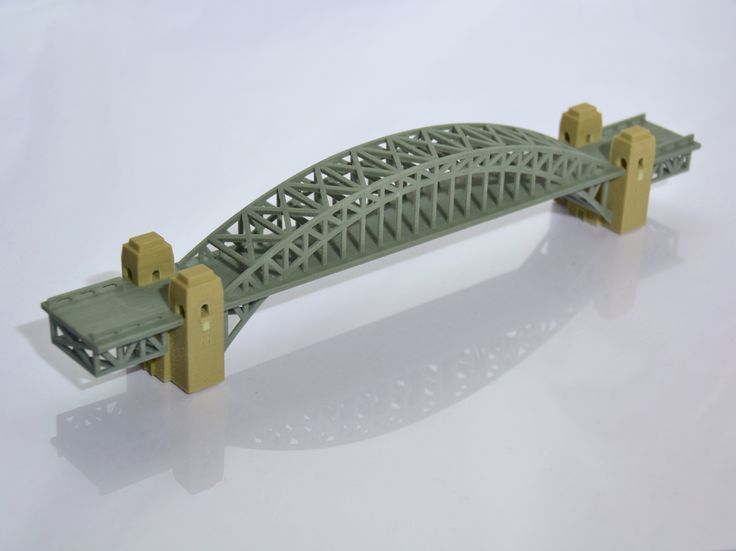
“Very fast response to all inquires. Parts arrived on time and in good condition. Thanks!”
“9 hour turn around from placing my order to picking up locally! ”
“Perfect quality and quick turn around-- once again! ”
“He was great! Offered advice and made suggestions based on the specific design and use of the object I needed to print and communicated very quickly and professionally!”
“The part arived exactly as modeled with a fine surface finish. I can't ask for more.”
“Excellent quality and communication, I was really blown away by the entire process. Thank you so much!”
“Amazing work. Thank you so much. We will be in touch for more. ”
“Great communication. Print quality was good and deliverey was fast! Highly recommended!”
“I had a great experience with this hub and would definitely recommend. My order was processed quickly, the hub was communicative, and parts turned out great!”
“Communication was excellent, turnaround was very quick. ”
“Super quick, knowledgeable, and helpful. ”
“5 stars across the board. Thank you so much!”
“I sent them a big order and they responded like troopers! This wasn't the first time that I'd ordered from them and it definitely won't be the last. They do a stellar job and communicate very well. I knew exactly what to expect and was asked for feedback on production decisions. ”
“Highly recommended! Extremely quick turnaround, great prints, and instantly responded to a custom request that wasn't charged extra for.”
“This is the guy I'll order from next time. Great communication and quality.”
“Offered good recommendations and printed on time with excellent quality paying special attention to the smaller detailed pieces.”
“Excellent service! Ordered on May 31 and delivered via mail just a couple days later. Party looks good and material looks sturdy. This was my first time ordering a print and if given the opportunity I would use this printer again”
“great service, and communication! thank you”
“Great communication and very fast work! An absolute pleasure to work with. I would give 10 stars if I could! ”
“First time using the service, went very smoothly. Thanks!”
“This was my first 3d printed object to order, so I didn't know what to expect. The parts I received were what I needed, albeit with some sanding and polishing - but I understand that is normal. Very happy - no complaints.”
“As always, we are very happy with the build quality of this part.”
“Everything about this experience was great! The quality of the print was perfect and the time was right on the money. ”
“Great service and assistance for my first 3D print.”
“Excellent! Clear communication with photos along the way. 100% recommended.”
Show more reviews
Show less reviews
Teams build better parts
Create your Hubs team and start collaborating
Read more
The Hubs Standard - consistent quality, every time
Hubs takes the stress out of manufacturing by guaranteeing the quality and consistency of every part. Each order is dimensionally and visually inspected to make sure it meets the Hubs Standard.
3D printing materials
We can generate instant 3D printing quotes for 25+ plastics. For metal 3D-printed parts, you can request a quote from our parent company, Protolabs.
Available materials
SLS
PA 12 Glass filled PA 12
Desktop FDM
Prototyping PETG Prototyping ASA Prototyping TPU Prototyping ABS Prototyping PLA
Desktop SLA
Formlabs Standard Resin Formlabs Clear Resin Formlabs Tough Resin 2000 Formlabs Rigid Resin 4000 Formlabs Grey Pro Resin Formlabs Flexible Resin 80A Formlabs High Temp Resin Formlabs Durable Resin
MJF
HP PA 12 Glass filled HP PA 12
Industrial FDM
Markforged Onyx ABSplus Stratasys ULTEM 9085 Stratasys Stratasys ASA ABS M30 Stratasys ULTEM 1010 Stratasys
Industrial SLA
Accura 25 (PP-like) Accura ClearVue Accura Xtreme White 200 (ABS-like)
3D printing locations near Nashville, TN
Franklin, TN Nashville, TN Hendersonville, TN
Murfreesboro, TN Clarksville, TN Bowling Green, KY
Florence, AL Huntsville, AL Decatur, AL
Owensboro, KY
The 3D Printing Handbook
No one understands 3D printing like us - our founders literally wrote the book. Click here to download the sample chapters.
Buy the book from Amazon
FAQ's
How much does your 3D printing service cost?
The cost of your 3D printed parts depends on factors such as part volume, part complexity, choice of material, which 3D printing technology is used, and if any post processing is required. For more details on these cost factors, see our article on the cost of 3d printing. To check the cost of your 3D printed part, simply upload a CAD (.STL) file and select your material and 3D printing technology to receive a quote within seconds.
How do you guarantee the quality of my prints?
Your parts are made by experienced 3D printing shops within our network. All facilities are regularly audited to ensure they consistently meet the Hubs quality standard. We include a standardized inspection report with every order and offer a First Article Inspection service on orders of 100+ units.
We have partners in our network with the following certifications, available on request: ISO9001, ISO13485 and AS9100.
Follow this link to read more about our quality assurance measures.
How do I select the right 3D printing process for my prints?
You can select the right 3D printing process by examining which materials suit your need and what your use case is.
By material: if you already know which material you would like to use, selecting a 3D printing process is relatively easy, as many materials are technology specific.
By use case: once you know whether you need a functional or visual part, choosing a process is easy.
For more help, read our guide to selecting the right 3D printing process. Find out more about Fused Deposition Modeling (FDM), Selective Laser Sintering (SLS), Multi Jet Fusion (MJF) and Stereolithography (SLA).
How can I reduce the cost of my 3D prints?
In order to reduce the cost of your 3D prints you need to understand the impact certain factors have on cost. The main cost influencing factors are the material type, individual part volume, printing technology and post-processing requirements.
Once these have been decided, an easy way to further cut costs is to reduce the amount of material used. This can be done by decreasing the size of your model, hollowing it out, and eliminating the need for support structures.
To learn more, read our full guide on how to reduce the cost of 3D printing.
Where can I learn more about 3D printing?
Our knowledge base is full of in-depth design guidelines, explanations on process and surface finishes, and information on how to create and use CAD files. Our 3D printing content has been written by an expert team of engineers and technicians over the years.
See our complete engineering guide to 3D printing for a full breakdown of the different 3D printing technologies and materials. If you want even more 3D printing, then check out our acclaimed 3D printing handbook here.
We have an extensive range of online resources developed to help engineers improve their capabilities.
Introductory guides
Design guides
Material guides
Applications
CAD & file preparation
Post processing & finishing
Our other manufacturing capabilities
CNC machining
CNC machining
Milling (3-, 4- & full 5-axis), turning and post-processing
-
50+ metals and plastics & 10 surface finishes
-
Tolerances down to ±.0008” (0.020 mm)
-
Lead times from 5 business days
See our CNC machining services
Put your 3D printed parts into production today
Get an instant 3D printing quote
Branch Technology erected a huge 3D printed pavilion in Nashville
News
As Branch Technology prepares to build the first 3D printed residential building in the United States, the branch demonstrated the capabilities of its own 3D printer by printing the OneCity pavilion in Nashville, Tennessee.
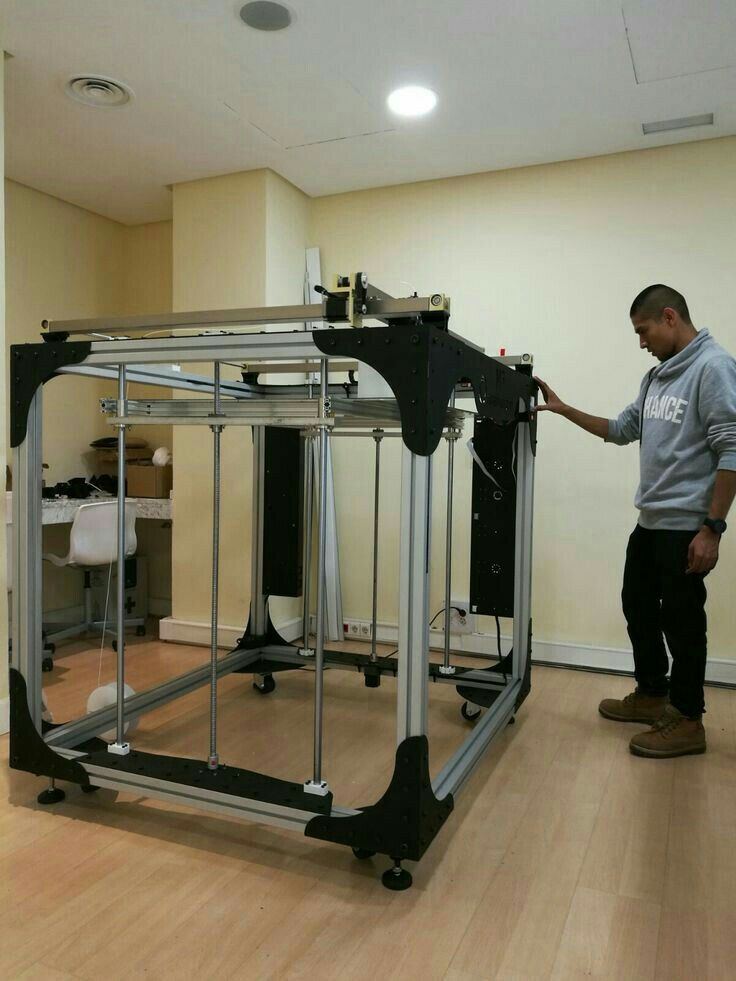
Branch Technology has been trying for years to push through bureaucratic barriers a 3D printed residential building project, the first of its kind in the United States. Initially, the house was planned to be built two years ago, but the company received a building permit only at the beginning of this year.
While final preparations are being made, namely the preparation of design documentation and testing of prototype 3D printed structures, the team decided to spend their free time on another demonstration of the possibilities.
Massive $400 million housing and beautification project OneCity is underway near downtown Nashville. The development company Cambridge Holdings is building eight residential and commercial buildings with a total area of 1.2 million square meters. Branch Technology joined the project, decorating the area with a 3D printed pavilion designed in the same spirit as the future 3D printed residential building.
C-Fab's proprietary technology combines Kuka industrial robotic arms with 3D printed thermoplastics reinforced with carbon fiber if required. After the erection of the frame, it is planned to fill the cavities with insulation and building mixtures, although in the case of the pavilion, the builders did not become wiser and left the structure in its original form.
According to the company, this is the largest 3D printed structure in the world. The statement is very, very controversial, but let's not quibble, especially since the size is really impressive - six meters high and thirteen meters wide. The structure is assembled from 36 3D printed blocks, one of which is five and a half meters long, and the heaviest block, thanks to the openwork design, weighs only 130 kg.
Another very interesting C-Fab project we featured last spring was when architect Keith Caseman of the University of Tennessee at Knoxville hired the company to 3D print a drone landing pad ( in the illustration above ). The site was fixed on the wall of the university as a demonstrator of architectural designs of the future, adapted for the mass operation of commercial drones.
Do you have any interesting news? Share your developments with us, and we will tell the whole world about them! We are waiting for your ideas at [email protected].
Follow author
Follow
Don't want
5
More interesting articles
7
Subscribe to the author
Subscribe
Don't want
0003
Read more
5
Subscribe to the author
Subscribe to the author
Don't want to
Stamping is widely used in a wide variety of industries - from the production of consumer goods and auto . ..
Read more
82
Subscribe to the author
Subscribe
Don't want
Collaboration 3D
We are pleased to present you our joint development with Speci...
Read more
Military 3D printers - big overview
Overview: Military 3D printers.
Source: https://all3dp.com/
The military industry has always been at the forefront of progress: many inventions either began their life as military or dual-use products, or, in the very first years after their appearance, were involved in this area . In this age of digital technology, this fate has not escaped 3D printing.
3D printers are actively used by military contractors and direct employees of all branches of the military.
In this article, we will talk about the use of 3D printing in the military-industrial complex around the world: from providing military equipment with spare parts, to operational printing of drones and buildings at any location.
In Russia,
JSC "Federal Research and Production Center "Titan-Barricades", which develops missile systems and military vehicles, bought and uses a kit based on the XJRP SPS450B 3D printer for prototyping. The kit consists of two devices: directly a 3D printer with a large print area, working on SLA technology, and a polymer curing chamber.
XJRP SPS450B 3D Prototyping Kit. |
Source: http://pechat3d.ru/ |
The 3D printer is planned to be used to create miniatures of future parts, cases or mechanism assemblies. The first product made on this 3D printer was a prototype wheel with a tread.
Ilyushin specialists plan to produce some simple parts for the Il-112V military transport aircraft using 3D printing.
Model of the Il-112V transport aircraft. |
Source: © ITAR-TASS |
Together with specialists from the Voronezh Aircraft Plant (VASO), PJSC Il specialists use 3D-printed parts as test samples, which will be replaced with originals made by the classical method before departure. But in the future, it is planned to master the printing of simple components that will be installed on mass-produced aircraft.
Pavel Chernikov, First Deputy General Director of PJSC Il, said: “The IL-112V is being created from scratch, and many parts and components need to be improved during installation on the aircraft. We started using a 3D printer to see how right or wrong our calculations were. Such technologies make it possible not to interrupt the finalization of finished products, which, in turn, significantly reduces the installation time of equipment and reduces the cost of the production process.”
Research and Production Corporation "Uralvagonzavod" named after F. E. Dzerzhinsky purchased a 3D printer S-Max manufactured by ExOne.
ExOne S-Max 3D printer. |
Source: http://3dtoday.ru/ |
This printer is designed for making sand molds. Molds are used for casting metal blanks. As the deputy chief metallurgist of NPK Uralvagonzavod said: “We will no longer have to manufacture expensive foundry equipment for experimental, new products and complex castings of small series. It will be enough for a designer to develop a 3D model of the required casting, according to which, also in 3D, the mold is made. The finished cores will go to the foundry. In addition, they can be transported to solve the problems of the corporation over any distance."
A sand mold produced by the S-Max 3D printer, used for casting metal blanks. |
Source: http://3dtoday.ru/ |
This is not the first professional 3D printing system that Uralvagonzavod uses. In 2015, the company purchased a Fortus 400mc 3D printer manufactured by Stratasys Corporation. This printer is used in the production of parts for the T-14 "Armata" tank and other vehicles manufactured by Uralvagonzavod.
Tank T-14 ("Object 148") on the platform "Armata". |
Source: OAO NPK Uralvagonzavod |
Representatives of the enterprise note that the introduction of 3D printing saves time and production resources. It is not required to spend forces on turning metal samples. If a part doesn't fit, it's easier to reprint it than remake it.
Russian Helicopters Holding, according to its CEO Andrey Boginsky, plans to 3D print about a hundred parts for rotorcraft by 2020.
Andrey Boginsky. |
Source: © Yuri Smityuk/TASS |
In 2018-2019, it is planned to conduct a series of bench tests in order to obtain all the necessary certificates for printed parts by mid-2020. In total, it is planned to test about a hundred parts and assemblies.
Compared to traditional parts, 3D-printed parts are lighter and their production will be deployed at the Kazan Helicopter Plant. As a result of the use of parts obtained by 3D printing, the holding plans to reduce the cost of products.
In the world
The road of army 3D printing is not paved with roses. When we hear about cool 3D printed military projects, we have to consider some of the challenges that come with doing them.
Soldiers get acquainted with FORTUS. |
Source: https://all3dp.com/ |
Quality certification problem. Many things that the army is supposed to produce using 3D printing are designed for harsh operating conditions, they are subject to high requirements for compliance with dimensions, geometry and quality, and an unsuccessfully printed part can lead not only to monetary losses, but also to the death of soldiers . This issue will most likely be resolved by certification of the 3D printers themselves.
Insufficient printing speed for the army. Even the most expensive 3D printer is not fast enough. There are also issues of privacy/security, copyright, and many other little things that are not obvious at first glance.
While these issues are being addressed, the US Department of the Navy has decided to host a 3D printing hackathon. 12 organizations were invited to participate, which showed their developments in the field of 3D printing for the Navy. According to the participants, fully or partially printed inventions: “Allow to improve the ability to maintain combat readiness.”
One of the new and memorable developments was the four-legged transporter robot (MeRlin). It turned out to be quite compact and can run, jump and walk up and down stairs. Three-dimensional printing made it possible to create, right in the supporting frame of the robot, a hydraulic manifold that serves to transfer energy to the robot drives. Those interested in robotics will find Merlin similar to the transport robots of Boston Dynamics.
The device of the robot MERLIN (Merlin). |
Source: https://all3dp.com/ |
Aviation
A 3D-printed drone was launched from one of the British Royal Navy ships at sea, HMS Mersey. The device was created in collaboration with the University of Southampton.
Launch of a 3D printed drone. |
Source: https://all3dp.com/ |
Body made of nylon, laser sintered. With a wingspan of one and a half meters, the drone weighs only three kilograms. The main task of this project was to create a small drone for exploring the surroundings, which can be quickly printed on board the ship.
The drone, named SULSA, was equipped with a small video camera. Management was carried out by researchers from Southampton using video cameras. The flight, with a range of 500 meters, lasted only a few minutes, but proved that 3D printed drones could be launched from the sea.
The route of the SULSA drone during a test flight. |
Source: https://www.southampton.ac.uk/ |
3D printing will solve the problem of limited ship capacity by allowing equipment to be printed at sea as needed. The only thing you need to have on board to print a drone is a 3D printer and a supply of nylon, which is disproportionately cheaper than a case made using traditional technologies, and takes up much less space.
The only drawback is the print speed, but it is expected to improve in the near future. Engineers from the American Army Research Laboratory (ARL) are trying to fight this shortcoming. They are developing drones that can be made within a day. Engineers are building drones that can be used to assist soldiers in communication, delivery, and aerial surveillance.
Eric Sopero demonstrates his drone to US military personnel.![]() |
Source: https://all3dp.com/ |
Drones are made using off-the-shelf motors and propellers, but their body is almost entirely 3D printed. The maximum speed of the drone is 55 miles per hour. Drones can either be controlled by the operator from the remote control or operate in a completely autonomous mode. Work continues to reduce noise and increase flight range, maneuverability and payload.
The US Army is partnering with the Marine Corps to develop an unmanned vehicle parts catalog that can be downloaded to an employee's tablet. The software of this catalog allows you to order or 3D print a product directly from it.
American soldier with a drone. |
Source: https://all3dp.com/ |
In addition to experiments with drones, 3D printing is also used in “big” aviation.
For example, the US Air Force has announced that it will 3D print toilet seats for military transport aircraft. The announcement comes after a scandal erupted when it was reported that each toilet seat cost the Air Force $10,000 to replace.
Airplane seat for $10,000. |
Source: https://all3dp.com/ |
The public, which already believed that the government did not always save on military spending, was extremely outraged. After an investigation initiated by one of the senators, the military department announced that it would print toilet seats on 3D printers.
Why is the toilet lid so expensive? These covers were mass-produced by Lockheed Martin, and in 2001 this giant of the military industry stopped their production. In addition, the military department explained that the C-5 toilet seat is not only a cover, but also part of the lavatory wall, which is designed to protect the body of the aircraft from corrosion that can be caused by urine.
According to the manufacturer, its high cost is due to the need to suspend the production of other goods. In the case of independent production of the Air Force, the spare part will cost only $300.
The manufacturer now claims that the US Air Force does not own the copyright to this cap. It is not known how this lawsuit will end, but the Air Force says that they will no longer buy this spare part, because they can make it themselves much cheaper.
As stated by the department: “The use of 3D printing allows us to create parts that are no longer being produced, resulting in significant cost savings.”
C-5 transport aircraft. |
Source: https://all3dp.com/ |
Another example of 3D printing was demonstrated by the Maryland Marines. Using 3D modeling and 3D printing, they made a $70,000 F-35 fighter jet part for just 9 cents. The Marines were assisted by Sam Pratt, a mechanical engineer in the design office of the Carderock Additive Technology Factory.
Sam revealed that he was with a support platoon in South Korea teaching CLB-31 Marines how to design 3D models and how to use 3D printing. His main task was to test the performance of 3D printers on marine vessels. He also taught employees how to use Solidworks CAD.
Sam Pratt talks to the Marines about 3D printing. |
Source: https://all3dp.com/ |
When there was a problem printing a part needed to repair an F-35, a Marine officer offered to team up to work together. It turned out that the employees had already developed this part, but could not find the right dimensions. The fact is that they used a hobby-grade 3D printer and the free 3D editor Blender - Blender is ideal for implementing art projects, but it is difficult to create engineering products in it.
American Marine at the 3D printer. |
Source: https://all3dp.com/ |
Pratt helped with modeling and printing issues, the part was printed in PET-G.
Currently there are about 90 parts for ground vehicles that are approved for 3D printing in the military, you can download one of these parts and print it.
Large manufacturers are also moving forward and mastering 3D printing technologies. Thus, the giant of the aviation and military industry Lockheed Martin is actively investing in 3D printing.
Lockheed Martin uses 3D printing in its manufacturing processes, with over a hundred 3D printers in its arsenal for prototyping, tooling and printing finished products.
There are several reasons why Lockheed Martin uses 3D printing:
- Reducing the time of production of products - up to 80%;
- Reducing the weight of parts - up to 40%;
- Proven reliability of parts in difficult conditions;
- The most important thing is the possibility of an additional increase in production in the near future.
For example, it takes 18 to 20 months to manufacture fuel tanks for spacecraft using traditional technologies. The production of such a tank by 3D printing takes two weeks. In this case, a better uniformity of the structure of the tank elements is achieved. The tanks are manufactured using a Sciaky printer using EBAM (Electron Beam Direct Manufacturing) technology, in which a bar of metal material is heated by an electron beam.
Lockheed Martin uses 3D printing in its manufacturing processes. |
Source: https://all3dp.com/ |
Lockheed Martin's 3D printed products have already passed the lab testing stage and are in active use. Some of them travel around our solar system: the Jupiter-exploring Juno satellite has eight 3D-printed brackets, and the Orion spacecraft uses printed high-pressure valves.
Fleet
In South Korea, loudspeaker grilles for aircraft carriers are printed on 3D printers. Shipping these gratings from Europe took up to seven months and cost $612 each. The printed part is made in 4-5 hours and costs about $35. Printing parts reduces their cost and production time, and localization of production reduces dependence on foreign supplies, which may be delayed or become unavailable for various reasons.
General Electric has contracted with the US Navy to develop software for rapid 3D printing of spare parts for ships, aircraft and other critical military installations. The contract, worth nine billion dollars, is designed for four years and provides for the creation of technology "digital duplicates" - a complex of software, base models and hardware. This technology will be used both for those spare parts that are no longer manufactured, and for new parts of ships and aircraft.
Concept Laser M2 3D printer printing with metal powder. |
Source: https://all3dp.com/ |
The project is being implemented in two stages: at the first stage, software and hardware parts will be developed, at the second they will be combined into a complex capable of quickly creating the necessary products using laser metal melting technology (DMLM).
Ammunition and small arms
The US Army has designed and 3D printed a fully functional grenade launcher called "R.A.M.B.O". The development of the grenade launcher took about six months. He shoots 3D printed grenades
R.A.M.B.O. grenade launcher |
Source: https://all3dp.com/ |
The grenade launcher consists of 50 parts, all of which, with the exception of springs and hardware, are 3D printed.
3D printed parts of the R.A.M.B.O. |
Source: https://all3dp.com/ |
R.A.M.B.O. demonstrated characteristics similar to the M203 underbarrel grenade launcher made in the traditional way.
A US Marine team is 3D printing and testing small explosive containers that can be used on the battlefield.
3D printed container for explosives.![]() |
Source: https://all3dp.com/ |
The development of small arms began in the private sector, with the most primitive pistols. On the Internet, you can find drawings of products such as the sensational Liberator. The first 3D printed pistol was printed on a professional Stratasys Dimension SST printer. The gun is chambered for 9 caliber rounds.mm and is charged during assembly.
A gun whose main components are made of plastic and printed using a 3D printer. Frame: YouTube. |
Source: YouTube |
The very possibility of obtaining weapons using 3D printing so excited the public that the drawings of the "Liberator" were removed from the public domain, and the United States introduced a ban on 3D-printed weapons.
Solid Concepts has created a replica of the .45 Browning M1911 pistol, the Solid Concepts 1911 DMLS, using selective metal laser sintering. The first sample withstood 50 shots, later ones are capable of firing 600 shots without visible damage.
A working replica of a .45 Browning pistol M1911 - Solid Concepts 1911 DMLS, made by selective metal laser sintering. |
Source: Solid Concepts Inc |
Recently, the ban on the distribution of 3D printed weapons was lifted by a court decision. So, it is now possible to print weapons in the USA, with some restrictions: they can be no more than 50 mm in caliber and models cannot be freely available. This ban was easily circumvented by Defense Distributed, which posted models of their rifle for sale on one of the online services.
M4 rifle from Defense Distributed. |
Source: https://depositphotos.com/ |
“Our models are not in the public domain because customers pay money for them,” a company spokesman said.
Uniforms and protection
The Vatican decided to use 3D printing technology for the production of traditional Swiss Guard headdresses.
Swiss Guard. |
Source: https://all3dp.com/ |
The Swiss Guard is the personal bodyguard of the Pope. From time immemorial, their form was made of metal, but now they have decided to keep up with the times. A 3D printed helmet will be significantly cheaper and, more importantly, lighter.
3D printed helmet prototype. |
Source: https://all3dp.com/ |
The helmets are made of PVC and bear the coat of arms of Pope Julius II, who founded the Swiss Guard in 1506.
The US military turned to the creators of the Iron Man costume, a movie character, for help in creating uniforms for the soldier of the future. The military commissioned Legacy Effects to develop and print the prototype components for the TALOS Special Outfit Kit.
TALOS will contain a cooling system to maintain a comfortable temperature in the suit, a tactical display and an integrated exoskeleton.
The concept of the uniform of the future - a set of special uniforms TALOS. |
Source: http://3dprintingindustry.com/ |
The studio team will join the large team already working on the project, which includes bioengineers, combat veterans and technologists.
Building
The US Army Research Engineering Team printed a large building in just 21 hours. The area of the building is 47.5 square meters. The barrack-style building is the result of a three-year US Army Construction Engineering Research (ACES) program with a laboratory in Champagne, Illinois.
3D printed barracks.![]() |
Source: https://all3dp.com/ |
Such a short construction time means that such temporary structures will become more affordable with the development of 3D printing. These buildings can be used as housing for refugees or temporary housing in case of natural disasters.
The process of building a 3D printer. |
Source: https://all3dp.com/ |
The building looks like an ordinary house, but in the future such buildings can be given any look. Such buildings are also more energy efficient than traditional ones - they require less energy for heating and cooling.
ACES cuts the amount of building materials used in half. Reducing the need for labor is 62%, compared with the construction of plywood structures.
Laying concrete mix with a construction 3D printer.![]() |
Source: https://all3dp.com/ |
ACES allows buildings to be printed using local materials.
Self-Sufficiency
A collaboration between the US Army Research Laboratory and the Marine Corps has led to the development of a technology to produce 3D printed PET filament from plastic waste such as water bottles.
According to the military, water bottles and plastic packaging are the most common litter on the battlefield. Both US and allied forces produce large amounts of this waste, and the ability to recycle it will reduce the cost of transporting raw materials. The filament obtained from recycled materials, provided that it is properly cleaned and dried, is completely equivalent in tensile strength to its analogue from primary raw materials.
Joint work of employees of the Research Laboratory of the US Army and the Marine Corps. |
Source: https://all3dp.![]() |
A plant is being developed, housed in a standard shipping container, that will allow the production of filament from waste.
The US Army is also developing food printers. Their advantages are obvious:
- the possibility of reducing the cost of food, compared with the traditional delivery of rations from abroad;
- the possibility of compiling an individual menu, in accordance with the preferences of each soldier;
- the possibility of individual balancing of the diet, depending on the dietary needs of each soldier.
The printer, like classic 3D printers, stacks components in layers.
3D printed food. |
Source: https://all3dp.com/ |
The printer uses the ultrasonic agglomeration method to 3D print small snacks.
Electronics
University of Massachusetts Lowell researchers have developed a new way to 3D print conductive components for radar systems. They have created a new type of ink that allows radars to be made using 3D printing.
Electronic components obtained by 3D printing. |
Source: https://all3dp.com/ |
The development was sponsored by Raytheon, one of the defense industry companies.
According to the developers: “The use of this technology makes it possible to obtain cheaper and more versatile systems than those obtained by classical methods. This technology has obvious advantages in the military sphere, but it can also be used in civilian industry, for example, in the production of weather stations or unmanned vehicles. The main problem was obtaining ink with desired properties, capable of working with high-frequency radiation.”
Applying ink to a plastic plate. |
Source: https://all3dp.com/ |
The 3D printer is equipped with two heads with different operating principles. One applies the ink by spraying, the second fixes them by microvibration. Radar system components such as a voltage controlled capacitor (varicap), phase shifter (for electronic control of phase array radar systems) and frequency filters can be manufactured using this technology.
The ink material is based on nanoparticles that can be injected into molten plastic and then solidify with it, creating conductive structures.
The US Air Force Research Laboratory teamed up with American Semiconductor to create a silicon-polymer memory chip.
Using 3D printing technology, they have developed a new ultra-flexible chip with built-in sensors.
Dan Berrigan holding the new flexible chip. |
Source: https://all3dp.com/ |
According to American Semiconductor, the thickness of the silicon wafer is 2000 angstroms. This tiny chip can measure humidity levels, temperature, muscle fatigue, and so on. This makes it ideal for use in new technologies for monitoring the well-being of wounded soldiers or the elderly.
Flexible electronics technology is being developed not only by research laboratories, but also by industry giants.
Apple, Boeing and the Massachusetts Institute of Technology formed an alliance to collaborate with the US Department of Defense in the field of flexible electronics.
The goal of the alliance is to have high quality flexible electronics by 2020.
The Department of Defense plans to provide a consortium called the FlexTech Alliance with $75 million over 5 years and raise $96 million in additional funding.
Smart clothes. |
Source: https://all3dp.com/ |
The consortium includes 96 companies, 11 specialized laboratories, 42 universities and 14 state and regional organizations. The key partners of the consortium are Apple, Boeing, General Electric, General Motors, Lockheed Martin, Motorola Mobility, Qualcomm and many others. Partner universities include Cornell, Harvard, Stanford, New York University and the Massachusetts Institute of Technology.
Practical applications will be primarily focused on military targets, such as uniforms with vital sign monitors. Pressure sensors can also be installed on vehicles to monitor deformation in key areas.
The civilian application of such microcircuits will help athletes control body function and improve performance, and people suffering from cardiovascular disease, control and prevent seizures. This technology will allow hospitals to monitor their patients en masse.
Concepts or Looking Ahead
British scientists and engineers are working on growing military drones using chemical technology.
Hydroponic chemputter. |
Source: https://all3dp.com/ |
Military developers explore all possible and impossible technologies. In this case, they are working on a "chemcomputer". “Chemputer” is a registered trademark of BAE Systems. The technology is being developed by Professor Lee Cronin of the University of Glasgow and is a 3D printing of biomaterial drones and aircraft.
Unlike classic 3D printers, a chemputter performs chemical reactions at the molecular level, creating everything from electronics to wings.
Drone prototypes. |
Source: https://all3dp.com/ |
While British scientists are inventing new technologies in printing for the military department, simple makers are creating weapons of the future using conventional 3D printers.
So, David Wirth created a hand railgun in his workshop.
David Wirth with his railgun. |
Source: https://all3dp.com/ |
Possibly inspired by the computer game Quake, he created this weapon using CAD, a 3D printer and an Arduino platform. The railgun can use aluminum or graphite bullets as ammunition, firing them at a speed of 250 m/s. The design is based on six huge capacitors, which, with a total weight of about nine kilograms, store more than 1800 joules of energy for each shot. The railgun also consists of batteries, two parallel contact rails and a pneumatic ammunition supply system.
Diagram of a railgun by David Wirth. |
Source: https://all3dp.com/ |
Conclusion
3D printing technology is increasingly used in the military. The main role in its promotion is played by the need to reduce costs. On-site 3D printing of parts helps to solve the problems of logistics and supply, allowing you to save time and money on delivery, which is important for the army and aviation, and even more so for the navy - it is impossible to foresee ashore and take with you everything that you might need, and delivery boarding at sea is expensive.