3D print gold jewelry
Shapeways: Gold 3D Printing
14K and 18K Gold
Wax Casting
Upload a model
Loading contents...
Show menu
14K and 18K Gold
Wax Casting
Upload a model
Material info
About Gold 3D Printing
Gold 3D printing is perfect for creating everyday wear, and timeless pieces too. Available in yellow, white, and rose, as well as 14K and 18K, Gold is one of the highest quality materials Shapeways offers. Capable of showcasing intricate details, Gold offers a professional, finished look and feel.
Color & Finishes
Yellow
Available in 14k and 18k
Rose
Only available in 14k
White
Only available in 14k
Technology
- Wax Casting
Description
Material Highlights
High quality, shiny finishing, skin-friendly, 14K and 18K gold. 3D printed Gold is capable of showing intricate details.
Handling and Care
Skin-friendly, 3D printed Gold offers high electrical conductivity and is heatproof to 800°C/1472°F.
Design Guidelines
Bounding Box
Bounding Box Max
89 × 89 × 100 mm
Bounding Box Min
2.4 × 2.4 × 0.6 mm
The bounding box is a 3D imaginary outline of a box that encloses the smallest area occupied by your model. Your model must be within the minimum and maximum bounding box sizes. If the size of the model is close to the maximum bounding box, then the printing orientation will be restricted.
Supported Wall Thickness Min
0.8 mm
Unsupported Wall Thickness Min
0.8 mm
A supported wall is connected at least on two sides of the wall, while an unsupported wall is connected only on one side of the wall. Walls that do not meet the minimum requirements may not survive printing and cleaning processes. Additionally, models may still be rejected based on the wall geometry of the model. Please consider the size of your model and reinforce the walls or add support structures as needed as minimum guidelines will not always be adequate for large models.
Supported Wires Min
0.8 mm
Unsupported Wires Min
1.0 mm
A wire is a circular, rectangular or even triangular feature that is thinner in its unconnected directions than its length. A supported wire is connected at least on two sides of the model, while an unsupported wire is connected on one side of the model. Wires that do not meet the minimum requirements may not survive printing and cleaning processes. Additionally, models may still be rejected based on the wire geometry of the model. Please consider the size of your model and reinforce the wires or add support structures as needed as minimum guidelines will not always be adequate for large models.
Details
Details Min Embossed
0.4 mm high & wide
Details Min Engraved
0.35 mm high & wide
For text, the ratio between width and depth, should be 1:1 and sans-serif fonts are preferred for line weight consistency.
Escape Holes
Single Escape Hole Diameter (Min)
4.0 mm
Multiple Escape Hole Diameter (Min)
2.0 mm
Escape holes are necessary to empty the support material of a hollow model. Two escape holes at the opposite ends of the model is optimal for the support removal process. Please consider the size of your model and make the escape holes bigger or add more escape holes as needed as minimum guidelines will not always be adequate for large models.
A single escape hole at the end of a cavity will not allow material in the corners near the escape hole to fully escape. So we recommend multiple escape holes at both ends of the cavity.
Clearance
Min
0.3 mm
Clearance is the space between two individual parts in a model. If the space among the individual parts do not meet the minimum clearance, then parts can fuse together or can be difficult to clean. This is important for movable pieces like hinges, gears, etc.
Interlocking & Enclosed Parts
Interlocking
No
Enclosed
No
Parts in File
Max
Upload as many as two identical parts, like earrings or cufflinks, in the same model file for the Gold 3D printer. Multiple, unique, non-interlocking parts cannot be ordered in the same model files; therefore, separate files are required for unique parts.
Accuracy
Accuracy Your Gold 3D printing model may shrink about 0.25 mm plus 2.5% after casting and finishing. For rings the inner diameter is accurate within +/- 0.1 to 0.15 mm. On average, the Gold 3D printing model shrinks about 2.5% after casting and finishing. We do our best to polish the internal diameter to match your model file.
For example: A product with dimensions of 50 x 50 x 100 mm can be 0.25 mm + 0.025*100 mm = 0.5 mm smaller in any direction.
Stay up to date on promotions, case studies, and more.
Newsletter Sign up
Stay up to date on promotions, case studies, and more.
Email Address
Online Gold 3D Printing Service
Design Specifications
Minimum Wall Thickness
0. 8 mm
Minimum Details
0.35 mm
Accuracy
±5% (with a lower limit of ±0.35 mm)
Maximum Size
88 x 88 x 125 mm
Clearance
0.3 mm
Enclosed Parts?
No
Interlocking Parts?
No
Pricing Info
The pricing for Gold is based on model volume, which is the volume of your model used to calculate the material cost (mm³).
Additionally, a startup cost is applied to the price of your model. This is a fixed cost independent of the parameters of your model. If you order two or more copies of a model, the price automatically decreases because the preparation of multiple copies can be carried out more efficiently.
Hallmarking
The hallmarking of gold is a way of guaranteeing that you’re getting the correct level of purity in your precious metals. We don’t use an assay office; instead, we have permission from the Royal Mint of Belgium to mark cast models with a master (also called a maker) and purity stamp. The purity mark will indicate the purity of the precious metal. For 14k gold, the mark is a diamond (or rhombus) with the text “au 585”. For 18k gold, the text “au 750” is featured in the same diamond shape.
The master or maker stamp has been registered and approved by the Royal Mint of Belgium. It displays the symbol of a lightbulb with the letters “i.m” inside the outline of a barrel.
Hallmarking is performed to the highest extent possible, either with a laser or by stamping the metal. However, if there is a risk of damaging the final product, the marks may be missing. In every case, you will always receive an invoice as proof of authenticity. Pursuant to the Belgian Law of 11 August 1987 on the warranty of works on precious metals and the Belgian Royal Decree of 18 January 1990 on the warranty of works on precious metals, i. materialise guarantees that the object of the Invoice fulfills the standards of purity for 14K gold at 58.5% purity or 18K gold at 75% purity, whichever is applicable.
For customers outside the EU, hallmarking is not provided.
i.materialise complies with Belgian legislation and the free movement of goods in Europe.
Typical Use
Gold is mostly used for jewelry.
Technology
Wax 3D printing and lost wax casting are used to build your design when using this material. The wax printing process is a type of Stereolithography that uses a wax-like resin. Support structures are printed along with the model to make sure your model doesn’t fall apart. These support structures are automatically generated and manually removed after the printing process. After support structures are removed and your model is cleaned, the model can be prepared for casting.
First, one or more wax sprues will be attached to your model. Next, the sprue and model will be attached to a wax ‘tree’, together with a bunch of other models. The tree is then placed in a flask and covered in fine plaster. When the plaster solidifies, it forms a mold for gold casting. The plaster mold is then put in an oven and heated for several hours to a point where the wax is completely burned out.
Then, molten gold is poured in to fill the cavities left by the wax. Once the gold has cooled and solidified, the plaster mold is broken and the gold models are removed by hand and polished.
Additional Information
- Because pure gold would be too soft for durable jewelry, solid gold is mixed with an alloy (usually with metals like silver, copper or zinc) to harden the material for longer wear
- Due to the nature of the process (lost-wax casting and printing) used in the production of gold, interlocking or enclosed parts are not possible
- In order to comply with European regulations (REACH), we use nickel-free white gold.
Consequently, the color of white gold models may appear slightly yellow
- Please also be aware that we do not use rhodium plating to whiten our white gold because plating eventually wears off. If you really want to whiten your model, you can always turn to your local jeweler to apply rhodium plating. Keep in mind that this plating will need to be reapplied each time it wears off and that the natural, slightly yellow color of white gold will reappear
- 14k yellow gold consists of 58.5% gold, 12.6% silver, 25.4% copper, and 3.5% zinc
- 14k white gold consists of 58.5% gold, 17.43% silver, 9.13% copper, 4.15% zinc, and 10.79% palladium
- 14k red gold consists of 58.5% gold, 39.5% copper, and 2% zinc
- 18k yellow gold consists of 75.2% gold, 12.1% silver, 10.8% copper, and 2.1% zinc
- 18k white gold consists of 75.2% gold, 10.42% silver, 5.45% copper, 2.48% zinc, and 6.45% palladium
- 18k red gold consists of 75.
3% gold and 24.7% copper
Choice of technology and 3D printer for jewelry making, pros and cons
Currently, there are many new technologies that are designed to simplify production in various industries. Progress does not stand still and, despite some opponents, 3D printing has its own niche in the production of jewelry.
3D printing can speed up and reduce the cost of jewelry production due to the low cost of consumables. With 3D printers, jewelers have the ability to quickly change the design of a product and make prototypes at least several times a day. For many jewelry industries, 3D printing is becoming a good alternative or addition to milling machines and other equipment.
Until now, some believe that handmade is a sign of craftsmanship, especially when it comes to creative work, and models made using 3D modeling and printing are amateurish. But many people forget that behind the computer is the same person who not only mechanically presses the buttons, but also puts his soul into his creation.
![]()
Benefits of 3D printing
In order to understand how justified the use of a 3D printer is, you need to know how jewelry is made. This is very painstaking work. No wonder the expression "jewelry work" appeared, denoting a very delicate and complex work.
Any decoration begins with a sketch. Usually several sketches are made in order to accurately determine the design and location of the inserts. Not only stones are used as decor, it can be elements made of wood, bone, precious metals, it all depends on the designer's imagination.
At the next stage, the product is drawn in a 3D editor. This allows not only to visualize the future product, but also to correct some errors and inaccuracies made at the design stage.
Ring model
Some craftsmen still carve "stencils" by hand. Such work requires certain skills and perseverance. Usually this is how products are made that will be cast in a single copy.![]()
A finished 3D model can have several ways to be implemented in a physical version - this is milling or 3D printing.
Stencil milling
Currently, 3D printing is not much inferior in accuracy to a milling machine and often has a significant advantage in speed, despite the fact that after printing it is still necessary to separate the supports and clean up the points of contact with the model. Once a physical model has been obtained, it can be cast immediately if the material used is wax or a burnable polymer.
If it is necessary to cast a large batch of products, then a mold is made from the master model made with the help of special rubber for subsequent wax casting. There are many types of rubber that vary in hardness and curing temperature. Rubber is selected depending on the material from which the master model is made.
For pouring molds, a special machine is usually used - an injector. In some models, you can not only heat the wax, but also vacuum it or leave it under pressure. This helps to reduce the number and size of air bubbles for better pouring of the rubber mold.
In home workshops, silicone is used instead of special rubber. After all, a special machine is needed to vulcanize rubber. But rubber molds are too soft and short-lived for making a large batch of stencils.
After making the required number of stencils, they are collected in "Christmas trees". "Elks" are waxes soldered to a wax rod. To save space, the distance between them is very small and they resemble fluffy Christmas trees, hence the name. The finished Christmas tree is weighed to calculate the required amount of metal. In some places, stones are immediately inserted into the stencils, unless another mounting option is provided.
Stencil Christmas trees
Ready "Christmas trees" are placed in a special cylindrical "cassette" without a bottom, which is called a flask, and filled with a gypsum-based molding mass. The flask with uncured gypsum must be evacuated to get rid of unnecessary air bubbles that can lead to defects on the surface of the finished casting.
After hardening, the gypsum flask is sent to a muffle furnace to melt the wax.
The calcination mode is selected depending on the material of the wax. For wax or burnout polymer, different modes are needed in order for the material to be completely removed from the gypsum!!!!!!
When all the wax is melted, cavities are formed inside the gypsum, repeating the contours of the wax. Metal is poured into these voids. After casting, the flask is cooled and the gypsum mold mass is washed out under the pressure of water. The result is a metal Christmas tree.
Herringbone after casting
Finished castings are cut from the Christmas tree and washed, polished, if necessary, blackened by the master until the desired appearance is achieved.
3D printers for jewelers
There are several 3D printing technologies that may be suitable for the needs of jewelers. Each has its pros and cons. Some 3D printers are ideal for a large workshop, and some are ideal for a small workshop.
SLA
SLA or stereolithography is based on the principle of layer-by-layer solidification of a photopolymer resin under the action of a UV beam. The UV beam is focused by means of mirrors on the surface of the resin and illuminates the model in layers.
How the SLA Printer Works
SLA 3D printers were the first to be noticed by jewelers. SLA devices are compact, while they have high printing accuracy.
Pros and cons
pros
Minuses
Print examples
From prototype to finished product
Cast and printed ring
Rating of printers.
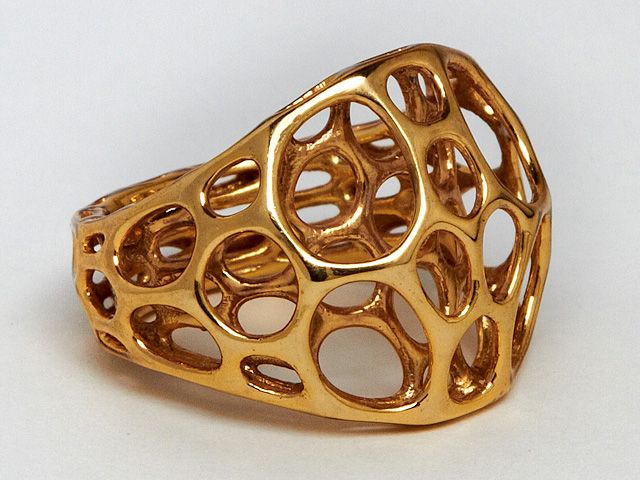
Leadership among the production of SLA 3D printers is held by Formlabs.
Formlabs Form 3
Formlabs Form 3
Specifications:
XY resolution: 25 µm
Laser spot size: 85 µm
Laser power: One 250mW laser
Working area size: 14.5×14.5×18.5cm
Layer thickness: 25 – 300 µm
A professional 3D printer that is popular with professional jewelers and dentists.
Formlabs Form 3L
Formlabs Form 3L
Specifications:
XY resolution: 25 µm
Laser spot size: 85 µm
Laser power: One 250mW laser
Working area size: 33.5×20×30cm
Layer thickness: 25 – 300 µm
Form 3L differs from younger models in its large print area, which allows you to produce truly large products without losing quality and accuracy.
DLP/LCD
DLP is very similar to SLA, only as a source of UV radiation, to illuminate the photopolymer resin, not a directed beam of light is used, but a DLP projector. DLP printers illuminate the entire work area at once, so they greatly outperform SLA in print speed.
How a DLP Printer Works
Today it is one of the most affordable photopolymer 3D printing technologies. In terms of cost, LCD printers have caught up with the price level of amateur FDM. DLP printers are much more expensive due to the use of an expensive projector as a UV source.
The projector is of course more expensive, but more durable, on the other hand, the LCD display is not so expensive and can be easily seen, unlike the projector. What to choose each user decides for himself.
Pros and cons.
pros
Minuses
Print examples
Comparison between 3D printed master model and molded part
Burnout resin model and finished product
Demonstration of products cast with burnout resin
Rating of printers.
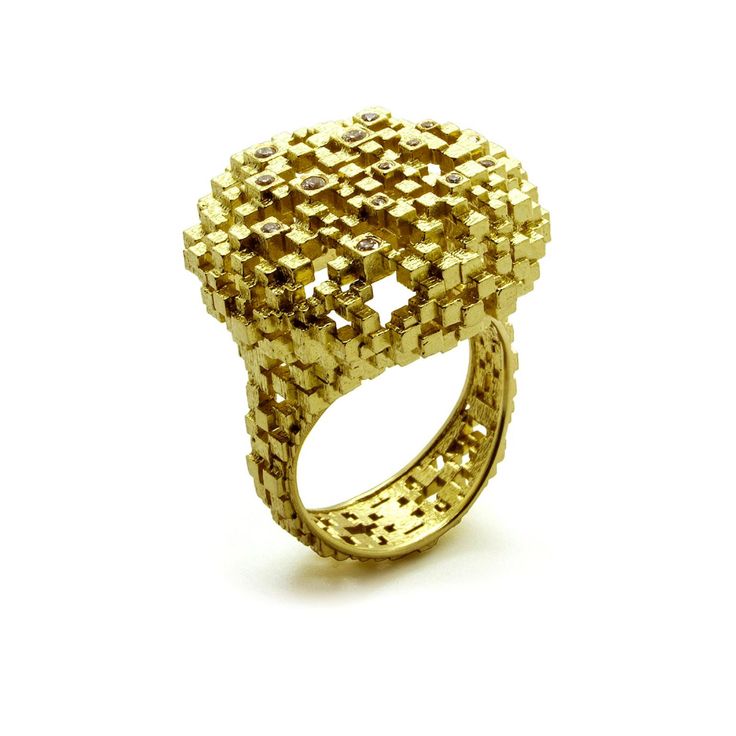
The print accuracy of LCD printers depends on the pixel size, so you should pay attention to this parameter when choosing a printer.
Anycubic Photon Mono
Anycubic Photon Mono
Specifications:
LCD display resolution: 2560x1620 (2K)
XY Positioning Accuracy: 0.051mm
UV wavelength: 405 nm
Working area size: 130x80x165 mm
Layer thickness: 0.01-0.15mm
The Anycubic Photon Mono is an inexpensive LCD machine ideal for hobby printing. The monochrome display allows you to reduce the exposure time and speed up printing.
Phrozen Sonic 4K
Phrozen Sonic 4K
Specifications:
LCD resolution: 6.1" 4K Mono LCD
XY positioning accuracy: 35 microns
UV wavelength: 405 nm
Working area size: 134x75x200 mm
Layer thickness: 0.01-0.30mm
Phrozen Sonic 4K is specifically designed for use in the dental and jewelry industry. Despite its compact size, the printer is not inferior to professional machines in accuracy, and the exposure time of one layer is only a few seconds.
Phrozen Sonic Mighty 4K
Phrozen Sonic Mighty 4K
Specifications:
LCD resolution: 9.3" 4K Mono LCD
XY positioning accuracy: 52 microns
UV wavelength: 405 nm
Working area size: 200x125x220 mm
Layer thickness: 0.01-0.3mm
Phrozen Sonic Mighty 4K is a professional device with a large print area. This allows you to quickly produce small batches of models.
Phrozen Sonic XL 4K
Phrozen Sonic XL 4K
Specifications:
LCD resolution: 8.9" 4K Mono-LCD
XY positioning accuracy: 50 microns
UV wavelength: 405 nm
Working area size: 190x120x200 mm
Layer thickness: 0.01-0.3mm
The Phrozen Sonic XL 4K is a professional machine with a large print area and a high resolution monochrome LCD display. This allows you to quickly produce batches of products with high accuracy.
Peopoly Phenom XXL
Peopoly Phenom XXL
Specifications:
LCD display resolution: 3840x2160 (23.8", 16:9, UHD 4K)
XY positioning accuracy: 137 µm
UV wavelength: 405 nm
Working area size: 527x296x550 mm
Layer thickness: 0.01-0.3mm
The Peopoly Phenom XXL is a device with a huge build area, which is ideal for serial production of not only jewelry.
Phrozen Sonic MEGA 8K
Phrozen Sonic MEGA 8K
Specifications:
LCD resolution: 15" 8K Mono LCD
XY Positioning Accuracy: 43 µm
UV wavelength: 405 nm
Working area size: 330 x 185 x 400 mm
Layer thickness: 0.01-0.3mm
This is the first LCD printer with 8k monochrome matrix resolution, and a huge working area allows you to produce large batches of products in one print.
MJM/MJP
MJM (or similar PolyJet technology) is a technology for layering photopolymer or wax through many fine nozzles. Typically, the print head is located from 96 to 448, depending on the printer model.
If a photopolymer is used as a material, it is immediately cured by a UV lamp, which is located on the printer's head.
How the MJM printer works
In addition to photopolymer, MJM 3D printers can use wax as a material for printing.
MJM printers can print multiple materials at the same time. This allows you to print complex models with soluble or investment supports. This makes it possible to produce complex models with a smooth surface quickly and easily.
Pros and cons
pros
-
Ability to print multiple materials at the same time. This means that another, soluble material can be used as a support. This allows you to save a lot of time on removing the support from the finished model and cleaning up the places where the supports come into contact with the print.
Minuses
-
To install the printer, most likely, you will need a separate room. 3D printers based on MJM technology are quite bulky in their dimensions, this is not a device that can simply be placed on a desktop or nightstand.
Print examples
Seal of a lot of stencils
Ring printed with wax
Master models made on MJM printer
Lot of jewelry stencils for further casting
Printer rating
FlashForge WaxJet 410
FlashForge WaxJet 410
Specifications:
Materials: Wax, support material.
Resolution: 1200*1200*1600
Building area size: 289*218*150mm
Layer thickness: 16 microns
Accuracy: ±0. 04mm / 20mm
The FlashForge WaxJet 410 is an industrial machine designed for serial printing of wax models, which will then be cast from metal. Machines of this class can be useful not only in jewelry production, but also in the dental industry, aerospace, mechanical engineering, prototyping, etc.
Totals
Photopolymer 3D printers are no longer inferior in detail to professional milling machines. The main advantage of a 3D printer is the ability to produce models of complex geometry with many internal cavities that are physically impossible to produce on a router.
Large firms will appreciate the flexibility that allows them to quickly adapt to customer requirements, as well as quickly produce large and small batches of products due to the shortening of the production chain.
And for a small workshop, a small photopolymer printer with a can of burn-out resin can be a good help, eliminating the need to purchase some expensive machines.
SLA jewelry printing. 3D printed jewelry
Articles
Stereolithography jewelry making allows you to quickly and inexpensively create jewelry with a unique design.
The use of SLA technology in jewelry
In jewelry, there are two options for using 3D printing:
- Production of products that are immediately ready to wear: that is, a product is printed on the printer, which is then slightly modified, painted - and the jewelry is ready.
- 3D printing blanks for subsequent casting of jewelry parts from real precious metals: 3D modeling technologies and SLA printers are used to create three-dimensional blanks of future jewelry, which are characterized by the highest accuracy, with the ability to detail the smallest elements.
Photopolymers in dentistry
In this case, the common expression "jewelry precision" should be taken literally. Due to this property, the production of products using SLA technology is in demand not only in jewelry, but also in dentistry for creating surgical templates.
With all the advantages of making jewelry using SLA printing technology, there is a minus - the high cost of consumables: photopolymer resin, which looks like epoxy.
A resin blank is used to create a precious detail in the following way: the 3D model is covered with plaster, which, when solidified, repeats all the outlines of the future jewelry. The mold cast in plaster is filled with precious metal - and the exclusive jewel is ready. Due to the peculiarities of production, the finished jewelry practically does not need to be finalized, which greatly saves time and reduces the cost of the jewelry piece.
Benefits of 3D printing for dentists and jewelers
- High accuracy: the production of jewelry models using SLA technology almost completely eliminates the influence of the human factor and errors, the entire process of creating a product is automated as much as possible. The absence of the need for serious refinement can also be attributed to the same point - that is, the detail is obtained as the designer or customer saw it, without “surprises” that looked good in the sketch, but were not provided for in the actual operation of the jewelry.
- Editability: Before a piece of jewelry is printed on a 3D printer (regardless of the technology), a virtual 3D model is created for subsequent printing in a special program. This virtual 3D model can be corrected at any time and the layout with the changes made can be printed - it is much cheaper and faster than “experimenting” with precious metals in the process of creating a precious item.
- Availability: the production of jewelry using SLA technology is developing very quickly, and, given the high demand, in the near future they will only become cheaper until they become available to absolutely everyone. Even now, the cost of 3D printing services is relatively low, especially considering the exclusivity of the result.
- Efficiency: the use of SLA printing technology reduces the production time of jewelry by several times.
Accordingly, productivity increases, the cost of finished jewelry decreases and it becomes possible to significantly increase sales.