3D print factory
Factory best 3D printer models・Cults
TWO HEADED DRAGON FLEXI
€2.28 -50% €1.14
Industrial roller slide
€8.95
FLEXI PRINT-IN-PLACE LOCHNESS MONSTER ARTICULATED
€2.10
Finn - Adventure Time
€2.40 -50% €1.20
Adult Blue - The Sea Beast (Flexi)
€2.32
FLEXIBLE CHRISTMAS SNOWMAN
€2.60
Shark Ray (Bowmouth Guitarfish) Flexi
€1.80
Sawfish Flexi
€1. 80
Dragon ball sugar cane sugar cane
€2.91
Barrel
Free
Pilot Whale Flexi
€1.80
tower ladder
€3.50
CUTE MICE COUPLE❤️
€5.88
fireman's cradle 1/43 special lights
€10
HOGWEED FIREFIGHTER UAR 1/43
€10
PRINT-IN-PLACE HAND
€1.59
FLEXI PRINT-IN-PLACE ZOMBIE CRAWLER ARTICULATED
€2.93
Factory Floor PBR Texture
€11.63
KAIEI3D repair bot 01
€5
LAZY SPACE MARINE - Articulated FLEXI MODEL
€3. 50
FLEXI PRINT-IN-PLACE WITCH ARTICULATED
€3.04 -50% €1.52
G29 Quick Release To Factory Wheel Adapter
Free
G29 Factory wheel quick release
Free
Transformers Lugnut (Iron Factory Style)
€17.46
YCF - PSB sprocket protection
€3
Cobalt Pillar
Free
Cuvier's Beaked Whale Flexi
€1.80
Mario Bross Vintage Factory art
€0.50
BASE para la figura de Samus Other M de Max Factory
€19. 21
Space Dwarf Barrier
Free
DEADPOOL MATE SET - SUGAR BOWL AND YERBA MATE SET
€1.16
Kaiei factory set 01
€3
PRINT-IN-PLACE- BAT ARTICULATED- FLEXIBLE- EASY TO PRINT WITH NO SUPPORTS
€3.77 -50% €1.89
Flying Bison (inspired by Appa) Flexi
€2.32
Complete matte set ! imperial/ Traditional, for 3 different polymers.
€6.98
Flexi Print-in-Place Brachiosaurus Dinosaur
€2.83
FLEXI PRINT-IN-PLACE PUMPKIN SPIDER ARTICULATED
€2.93
Amazon River Dolphin Flexi
€1. 80
MICKEY MOUSE MATE SET - SUGAR AND YERBA MATE -DISNEY
€1.74
Ankylosaur Flexi
€2.32
Oompa Loompa Head
€20.35
BOCA MATE SET - YERBERA AND SUGAR BOWL - BOMBONERA
€2.04 -10% €1.83
ARTICULATING FLEXI Baby RHINO
€1.99
Destroyed factory - 28mm
€9.99
Flexi Print-in-Place Skeleton Hand
€1.91
FLEXI PRINT-IN-PLACE SCARE CROW ARTICULATED
€2.93
Gravity Falls "duck" Mate Kit
€2. 40
Platypus Flexi
€2.32
The Largest 3D Printing Factory Is Coming « Fabbaloo
Concept diagram of “Print Farm Beta” [Source: Slant 3D]The idea of parallel 3D printing is incredibly powerful.
The rap against 3D printers has long been that they are monumentally slower than traditional manufacturing equipment to produce finished units, even though they are able to make objects of any design on the next print job.
This slowness has sometimes been the reason for not considering 3D printing as a manufacturing option, along with the unavailability of desired materials. However, in recent years the breadth of material selection has widened considerably, and now includes many popular engineering materials.
It’s now possible to make many types of end-use parts on 3D printers, but they are still slow.
But that constraint can be overcome with parallelism. If a single device takes two hours to produce a part, then 100 devices can produce 50 parts per hour. Slant 3D’s Gabe Bentz explains this well in his 2018 TEDxBoise talk:
I spoke with Bentz recently to find out more about this concept and specifically what is being done at Slant 3D.
Bentz explained that his company, Slant 3D, is attempting to produce a large-scale manufacturing operation based solely on 3D printing technology. He says they now operate the “largest 3D print farm in North America”, with a “couple hundred machines” all capable of operating in parallel to produce thousands of parts on demand.
Bentz says they currently are focused on jobs ranging from 10-20,000 pieces, and even take on jobs requiring 100,000 parts.
This is all part of a larger plan, according to Bentz, who is approaching this in stages. “Print Farm Alpha”, which is now complete, was the stage where they developed their farm system technology.
Mason 3D Printer
The Mason 3D Printer [Source: Slant 3D]This includes a custom-made 3D printer, the Mason 3D Printer, which has an ability to eject completed parts all by itself.
I asked Bentz to reveal the secrets behind this ejection mechanism, but he wouldn’t say much, as it’s a key strategic advantage. I was able to determine that it has to do with a sophisticated bed adhesion system that allows the part to be released under some form of control. Ejected parts can land on a conveyor belt for collection.
Slant 3D has created a custom software solution that manages all the farm devices at once. They’ve been able to develop an automated process that allows an incredible 150 live 3D printers to be managed by a single operator.
Print Farm Beta
A portion of the hundreds of Mason 3D Printers at Print Farm Beta [Source: Slant 3D]Currently Slant 3D is in the midst of building “Print Farm Beta”, which is a vastly scaled-up version of the equipment and process they developed during Print Farm Alpha. The goal here is to have an incredible 800 3D printers simultaneously in 24/7 operation. By Bentz’s arithmetic, this suggests they’d need only half a dozen people to manage such a site.
When complete, Print Farm Beta might well be the largest 3D print facility in the world, possibly exceeding Prusa Research’s 500 machines. A concept diagram appears at top. Bentz says:
“Over the next year we will be completing Print Farm Beta. Which will give us a break even with injection molding of nearly 100,000 parts on average.”
3D Printing vs Injection Molding
This is an intriguing result, as Slant 3D would then be able to take on a massive order immediately, since competing injection molding operations would have to wait for molds to be designed, tested and produced. Meanwhile, arrays of 3D printers need only be sent the next job to execute.
I asked Bentz whether they sell the Mason 3D Printer, and the answer is basically no. However, they will sell individual units to customers so they can test prints to simulate what they’d receive from Print Farm Beta.
Bentz says the array configuration will solve the speed problem, but now the industry still faces the design problem. Before committing to such massive amounts of 3D printing, parts will have to be properly designed for production on 3D printers, and that’s a skill that’s still pretty rare these days. Bentz says:
“If you’re designing for 3D printing you want to minimize surface area and don’t worry about part volume; that’s just the opposite of what you’d do with injection molding!”
FFF For Array 3D Printing
1000 mass produced 3D printed phone stands [Source: Slant 3D]I asked Bentz why focus on FFF-style 3D printing when there are other 3D printing processes available that can supposedly achieve high throughput. He believes that “FFF is the only 3D printing technology that can achieve production scale at a good cost.”
Print Farm Gamma
I asked Bentz what’s next for the company, and he explained a rather dramatic leap for the next stage of company development:
“We will be building Print Farm Gamma to serve as a full digital warehouse and distribution center.
That will be able to print and ship individual parts at the same cost as if they had been made with traditional manufacturing by the millions. This will mean that anyone in the world can design a product and have it manufactured and delivered to potentially millions of people for basically the cost of hosting a website.”
Many years ago I wrote about a futuristic concept I called the “Anything Factory”, where a static factory can run 24/7 making literally anything requested.
It may be that Slant 3D is building one.
Via Slant 3D
3D printing factory in Odessa, contract with General Electric and $2 million investment — Stories on vc.ru
The story of Kwambio startup founder Vladimir Usov — why 3D technologies are not yet in every home and when it will be possible to replace bones with printed implants.
6485 views
Vladimir Usov.
MC Today journalist Tatyana Gonchenko told the story of Ukrainian entrepreneur Vladimir Usov - about the first failures in business, the development of a 3D printer for printing ceramics and entering the American market.
Forwarder failures
Like many who graduated from the Odessa National Maritime University, after graduation, Vladimir Usov got a job in the port as a freight forwarder and agent. The work was hard and the pay was low. A year later, Usov realized that something had to change.
He discussed the idea that he had to start earning money somehow with the same young guys who worked with him in the port. We got together and decided - we need to do business. The port constantly needs spare parts for port loaders and cranes, which means they need to be taken somewhere, the guys thought. The decision seemed obvious - it is necessary to supply spare parts to the port.
A great idea was quickly shattered by harsh reality. There were many who wanted to supply spare parts and these people did not like competition. And the volume of corruption in this area just went through the roof. Six months later, Usov went bankrupt.
But his desire to earn money did not disappear. Later, he tried himself in the advertising business - he tried to print billboards, but again went bankrupt. Having no experience in entrepreneurship, Usov could not cope with the accounting and hardly got out of this venture without debts.
And only on the third attempt, the entrepreneur's business was successful.
First successful project
Usov's first successful startup was Gutenbergz, a digital publishing house that created interactive e-books for the iPad. The entrepreneur bought his first iPad in 2010. He thought it would be nice to create a book for him with live pictures, music and interactive elements.
The first book, Sherlock Holmes, took a year and a half to develop. Things went well - the book hit the top 10 sales in thirty countries around the world. Gutenbergz has been successfully working so far - creating electronic textbooks. But Usov's second passion was 3D printers.
Thinking about where to go, Usov thought that many Americans and Europeans already have desktop 3D printers at home. But in order to print any object on them, you need to have a source file, that is, roughly speaking, a drawn model of the future product. The entrepreneur decided that it was possible to create a platform that would bring designers together with end users.
It should have worked like this: a person wants to print, for example, a cup, chooses from the models offered on the site, or orders the designer what he needs, pays for the file and immediately prints the result. As a result, a person would receive his product without any shipments. It seemed like a great idea.
Usov and his friend Dmitry Krivoshey painted their idea on a piece of paper. This is how Kwambio was born.
I got excited about this idea and we immediately began to implement it. We created a very complex project in terms of technology - a platform solution for personal printers. Spent a lot of time, effort and money. At that time, it was exclusively my vision, which was not supported by any demand on the market
Vladimir Usov
The team won the startup competition at IDCEE, the largest IT conference in Central and Eastern Europe, and received half a million dollars. Then she raised another $650,000 from TechStars to develop her startup.
When the project was finally launched, it turned out that not many people even in America had home 3D printers. In addition, simple desktop printers can only print from plastic, and mostly non-functional things - a plastic ring, bracelet or Yoda head figurines.
Problems appeared already a month after the launch of the platform. There were many designers and products on the site, but few printed products.
The mistake was that we delayed the launch, trying to fix the slightest flaws and immediately launch 100% of the functionality. And it was necessary to launch a simple version and start testing it. After launch, I quickly realized that this concept was way ahead of its time. Even now she is ahead of him - at least ten years.
Vladimir Usov
We couldn't buy a printer so we designed it ourselves
Realizing that the idea failed, Kwambio decided to rebuild the system. Instead of printing on home 3D printers, they planned to work with a service bureau. The process is similar: a person selects what he needs to print on the site, the order is sent to one of the companies that makes 3D printing on industrial printers, and then the product is sent to the buyer's address.
But this model did not work well either. Service bureaus - only three or four in the world, the print quality was low, the prices were cosmic, the delivery times were uncontrollable. It was hard to establish a normal stable operation of such a service.
Vladimir Usov
The only way out was to open their own factory and print products on it. Production was opened in Odessa. The first orders started coming in pretty quickly. Clients needed to print products made of plastic, metal and ceramics - dishes, vases, various spare parts, interior items, decorations.
There were many orders for ceramics.
We began to look for where to buy a printer that would print high-quality ceramic products. But no one in the world could sell us such a printer - it simply did not exist.
Vladimir Usov
Then Kwambio decided to develop such a printer in-house. It took two years. As a result, they developed not only a printer, but also their own 3D printing technology based on ceramic powders. Now this is the main activity of the company.
Ceramic replaces metal
Soon the American media began to write about Kwambio. The support of Techstars, a well-known startup accelerator, also helped. As a result, more than 13 thousand products were sold at the factory in Odessa in a little over a year. The main buyers from the US are New York and Boston, so Kwambio has a second office in America. Goods are sent to them using UPS, an American express delivery company.
Printer designed by Kwambio costs $25,000. It prints ceramic products of any complexity in a matter of hours. At the beginning of the year, the company presented it at the world exhibition and received 13 pre-orders. Now Usov is working on the second model of the printer - they plan to present it next year.
Another development the team is working on is the first desktop ceramic printer. It will be more affordable than industrial ones - about $4,000. With its help, designers and people who are interested in ceramics will be able to produce their own ceramic products in the office or at home.
General Electric already wants to cooperate with Kwambio - they ordered several printers from Odessa. Under the contract, Kwambio will print parts that were previously made in metal for the American manufacturer of equipment.
According to many characteristics, they are more satisfied with ceramics - it is lighter, it has higher conductivity and higher elasticity. Today, the ceramics that we produce from our powders can, in some cases, replace metal. Including for the production of complex industrial parts.
![]()
Vladimir Usov
In the near future the company will open a branch in London to cover the European market.
Plans to “print” bone implants
Now Kwambio is working on a project that looks fantastic even for America. The company wants to print bone implants. According to Usov's idea, a person will be able to receive a finished implant literally in a couple of hours after the order - no matter in what part of the world he is.
We found that human bones are very similar in composition to ceramics. If we print ceramics, then why not print implants from biopowders? We have already begun testing biopowders based on calcium salt, a substance that makes up 70% of any bone tissue. Now the tests are being carried out in two European laboratories.
Vladimir Usov
Certification of these implants in the US is a lengthy process that can take up to ten years. In Europe, it passes faster, about two years. Therefore, Kwambio is now working more actively with laboratories and universities in Europe - they are testing their biopowder there.
The Kwambio team wants to go beyond printing bone implants, to create an online service where anyone can upload their bone scans and create an atlas of their skeleton based on MRI or other scans. After that, the client will have access to his personal cloud account.
If such a person breaks his arm, he can go to a certified hospital, the doctor will log into the patient's account, open the desired area of the bone, order an implant, they will print it right in the clinic and insert it into the arm. Now Kwambio is discussing the possibility of creating an electronic service that will help establish a system for working with American and European clinics. But this process is at an early stage.
I agree that it sounds fantastic, but I think that in 2-3 years we will bring it to life.
Now we are conducting tests to understand how the human body will perceive such an implant. But I am sure that everything will be fine, because the material from which it will be made is very similar in composition to bones. As soon as the tests are completed, we plan to obtain all the necessary permits, certificates, test it in action and find a partner in America. It will be some kind of large healthcare company.
Vladimir Usov
The company cannot yet predict the cost of such implants. But given that their production will take much less time than conventional implants, and fewer people will be involved, the developers suggest that the price will be much lower.
A 3D printer in every home will not appear soon
Now 3D printing technologies are beginning to be actively used in business in industries, both large and medium. For example, most technology companies in the US and Europe are already using 3D printing to some extent in their production chains.
If 4 years ago it was about 5-10%, then today about 30% of the entire production chain uses additive technology. I think that over the next 10 years, more than half of the industries will use 3D printing as the main production model
Vladimir Usov
As for home 3D printers, according to Vladimir Usov's forecasts, in the next five years they are unlikely to appear en masse in the homes of not only Ukrainians, but also Americans. To do this, a breakthrough technology must appear that will allow the use of a 3D printer for various purposes, and not just for printing plastic souvenirs, as it is now.
Make mistakes quickly and cheaply
Kwambio's Odessa office employs 25 people.
Most of the people who work with us with the technology of 3D printing and 3D printers did not understand this at all before coming to us. There is no such qualification in Ukraine, so we teach everyone to work from scratch.
![]()
Vladimir Usov
The entrepreneur is sure that Ukraine today occupies a very high place in the world in terms of the development of the production base and high-tech production.
But Kwambio still has few orders from Ukraine. Usov explains this by the high price for his services for Ukrainian manufacturers.
From his failures with the first versions of Kwambio, Usov learned the main rule - one should make mistakes quickly and cheaply.
I would advise against doing something complicated right away before checking if someone needs your product. The first version of the product needs to be created with minimal resources as quickly as possible. After that, look at the demand, and immediately correct mistakes if they were made. Long-term and expensive mistakes can win you over, because the next projects may not have the resource and inspiration left.
Vladimir Usov
Moscow 3D printing factory will produce spare parts for locomotives
News
The Russian company 2050.
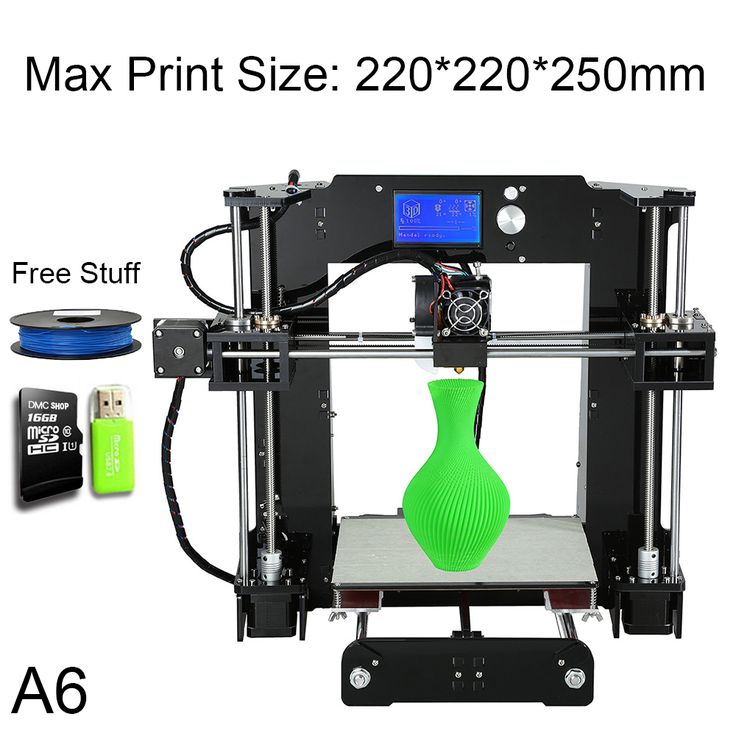
According to the press service of 2050.DIGITAL, the production facilities are located on the territory of the former Moscow Kristall plant. Nine 3D printers have been installed in the refurbished premises, and an area has been created for post-processing and painting 3D printed products. The office area houses jobs for 3D modeling and 3D printing engineers. In the near future, the equipment park is planned to be replenished with twenty more 3D printers, including four large-format additive installations.
The project is being implemented by the 2050.Additive Technologies company, which is part of the 2050.DIGITAL group of companies. The partners are Transmashholding JSC and the LocoTech group of companies. By the middle of the year, the company plans to install 40-50 3D printers using the FFF/FDM technology. From ten to fifteen devices will be able to print products with a size of about 700x700x700 mm. Reverse engineering will use 3D scanning technologies. According to the company's management, these capacities will be enough to completely close the need for 3D printing of products for their own needs and the needs of external partners in test and small-scale 3D printing modes.
“At the end of last year and the beginning of this year, we also selected several parts for the 4ES5K Yermak locomotives, printed these parts and already transferred them to the Bratskoye depot for experimental testing on locomotives as part of the Digital Depot project. Then, at the request of the management of the Tver Carriage Works, together with our partner, Additive Solutions, a domestic manufacturer of industrial printers for metal 3D printing, we printed our first metal part from 316L stainless steel - a galvanic pump housing. For us, this is invaluable experience and moving forward in the development of the production base and competencies,” says Dmitry Kiryanov, CEO of 2050. AT.
As we have already reported, 2050. DIGITAL is developing a digital platform for 3D printing of railway locomotive parts. At the moment, the base consists of several hundred parts in digital form - buttons, handles, holders, bushings, mounts, cabin interior elements, and so on. The company calls this approach "seamless contact": suppliers in the regions will be able to select the necessary spare parts in the catalog and issue a command for additive manufacturing.
“Our company does not aim to become a major manufacturer in the 3D printing market. The key goal of 2050.AT is to create the first domestic digital additive manufacturing platform with its own catalog of 3D models. Similar platforms already exist in Western markets. With the development of the Russian 3D market, the need for it arose in our country as well. The purpose of such a service is to attract professional manufacturers with all kinds of competencies in 3D printing and provide them with work. In turn, the use of this platform should give customers confidence that the part will be manufactured on time and with the required quality,” explains Igor Bevzyuk, CEO of the 2050. DIGITAL group of companies.
Do you have interesting news? Share your developments with us, and we will tell the whole world about them! We are waiting for your ideas at [email protected]
Follow the author
Follow
Don't want
4
More interesting articles
5
Subscribe to the author
Subscribe
Don't want
Specialists of the Institute of Light Materials and Technologies (ILMiT) of the united company RUSAL developed...
Read more
four
Subscribe to the author
Subscribe
Don't want
Scientists of the Arctic Research and Education Center on the basis of the Northern Arctic Federal University...
Read more
82
Follow author
Follow
Don't want
Collaboration 3D
We are pleased to present you our joint development with Speci.