3D print arch
fdm - How to print an overhanging arc
Asked
Modified 6 years, 7 months ago
Viewed 5k times
$\begingroup$
I am designing a part that has to clamp around a 11mm bushing, and due to other design constraints, it has to be printed with a semicircle-shaped overhang:
This is proving very challenging to print. Two copies of this part have to clamp tightly around the bushing in all directions. Support material is rather hard to remove from the very top of the arc (where the overhang angle is the highest) and I often end up removing just too little of the support material (so the part doesn't fit around the bushing) or too much (and the bushing can wobble around).
Is there any way I can modify the design of this part (bearing in mind that it absolutely has to be printed in this orientation) to make it more tolerant of my inaccuracy when removing supports, or is there perhaps some way to manually design supports that are easier to remove (Simplify3D and Cura both don't quite cut it)?
- fdm
- support-material
$\endgroup$
7
$\begingroup$
You could modify it as shown in my picture. I added lines tangent to the 11mm circle and in this example I set them to a 40 degree overhang which should be fine, the top line is also tangent to the circle and in my experience it's easier to bridge a small section rather than do a bunch of small overhangs like an arc would do. You still end up with quite a bit of contact but also easy to print.
I did something similar to this on my printer where the smooth rods enter horizontal holes.
$\endgroup$
$\begingroup$
I think a lot of this depends on the slicing engine you're using as to what options you have. I use MakerWare (now MakerBot Desktop) which has many options for the support scaffolding as well as other useful settings for your situation. As someone else stated, adjusting the distance (even slightly) can make a world of difference in how easy the supports are removed. Also bear in mind that supports can be more difficult to remove with larger layer heights, so try printing in a lower layer height.
Often times, you shouldn't need to use support structures for a feature like this. I might suggest printing without supports at a reduced speed and lowered nozzle temperature. This will help ensure that the material hardens quicker, which becomes helpful higher along the arc.
Related to the suggestion above, you can focus your slicing setting on better bridging. This should give better control on feeds/speeds while "bridging" a gap between overhanging features. Some slicing engines allow you to specify a different layer height for these areas on the print.
So, I would try printing with reduced print speed, nozzle temperature(s), and layer height with supports. My machine has a range of 0.1mm to 0.3, but I've had more success printing between 0.12mm and 0.15mm layer height with scaffolding in mind.
Last suggestion (when absolutely all else fails) purchase some sort of dissolvable filament (ie PVA - water soluble) and set your scaffolding-to-part distance really close and print. Obviously this only works if you have a multi-extruder head or a lot of time on your hands to swap the materials and adjust the nozzle temperature for each layer (please don't do that...)
$\endgroup$
$\begingroup$
If your printer is printing support material that is too strongly attached, you can increase the space between the support and the part in some slicing softwares. On Cura it is located in the "expert settings" menu (you can open it by pressing Ctrl + E), under the "Support" text. Try fiddling with the "Z distance" setting until you find the right setting. You can also change the type of support and support infill amount and see if it have any positive or negative effect.
Edit : I think you should also redesign your part : it seems that it cannot lock the bushing on. The semicircle should be a bit smaller to have a bit of space between your two parts. This way the bushing will be secured firmly by the tightening force of the screws and precision should be less of an issue.
$\endgroup$
1
$\begingroup$
I believe the post by @tbm0115, covers many of the general options. However, I would also consider installing additional fans to improve cooling of the model during printing.
As pointed out by this excellent article, installing a fan can significantly reduce issues the from printing overhangs. Regarding the type of fan to get, they stated that:
It seems that the fan shroud you choose is less important than the fan type. The blower fan was consistently weighted above the stock 40 mm fan regardless of shroud. Using a blower also gives you the best possible airflow through any shroud you decide to use.
In addition - in my experience - adding having two or more fans blowing on the model from different directions will further improve overhang performance. This is because all parts of the print are less likely to experience lack of cooling due to wind shadow - or drag.
$\endgroup$
2
$\begingroup$
Here are all the ways I can think of:
Turn the temperature down just a little, which may reduce sagging
Crank up cooling, like bigger fan(s) aimed at the print, so it solidifies faster
Change orientation when possible (not in this case)
Use soluble support material, and wash it away afterwards (requires 2-head printer)
Pause the print as you go up, and insert support material manually (ick)
Omit support material at the very top
Machine out the support material afterwards with a more precise tool, like a drill or sander the same diameter as the bearing. I'm eagerly waiting for a BoxZY printer that can swap in a milling head in place of the extruder.
Remove support material as now, but if you remove too much, fill the gap after installing the bearing to prevent wobbling -- epoxy, hot-melt glue, melted PLA, etc.
might work, depending on how the part will end up being used.
Add a set-screw to secure the bearing
Of course, these all have tradeoffs; but I hope at least one of them might help.
Steve
$\endgroup$
$\begingroup$
if I printed it in a different orientation it would delaminate too easily
If you flip it around, the orientation of the layers would be the same, except that you would print from top to bottom instead of bottom to top.
With the arch opening to the top, there would be no overhang. Without overhang, you don't need support structures (red). The holes for screw heads have flat roofs (green) that the printer should be able to gap by moving over them quickly.
Here's an image that shows the original orientation at the top and my proposed flipped orientation at the bottom. The blue lien is the print bed.
$\endgroup$
$\begingroup$
I had to design something rather like this, but I made the part that wraps around the pipe (pipe in my case - bushing in yours) into a separate piece that slotted into the main arch.
That way, the main arch could be printed with poor precision on the overhang, and the sleeve was printed on its side. It took a little work to make the slotting system fit well, but it was fine. The two arches screwed together to grip two sleeve sections. It also meant I could print the big parts quickly because their precision was less critical.
If - as you suggest - you absolutely have to print it this way, then how about pulling the top of the arch up a little; make it a bit "gothic" if you see what I mean. This is a variation on tjb1's idea above, but rather than have a flat at the top, organize it so there's a gentle point. That way, the printer isn't trying to draw a critical fitting over empty space, and the area that prints poorly is away from the bushing. You might have the slack to put supports back in.
$\endgroup$
3 D Printing | Tag
NASA and AI Space Factory Develop a 3D Printed Lunar Structure
© NASA/Frank MichauxNASA and AI Space Factory developed LINA (Lunar Infrastructure Asset), an in-situ 3D-printed outpost to protect astronauts and critical missions on the Moon. The project is part of the Relevant Environment Additive Construction Technology (REACT), a multi-year collaboration to develop technologies for lunar surface constructions within the timeframe of the Artemis Mission: humankind’s return to the Moon. LINA is a step in the effort to expand civilization to Earth’s natural satellite and explore it in a sustainable way that minimizes human disturbance.
+ 12
https://www.archdaily.com/989713/nasa-and-ai-space-factory-develop-a-3d-printed-lunar-structurePaula Cano
Nature and Technology: Walls That Can Grow Plants
Cortesia de E.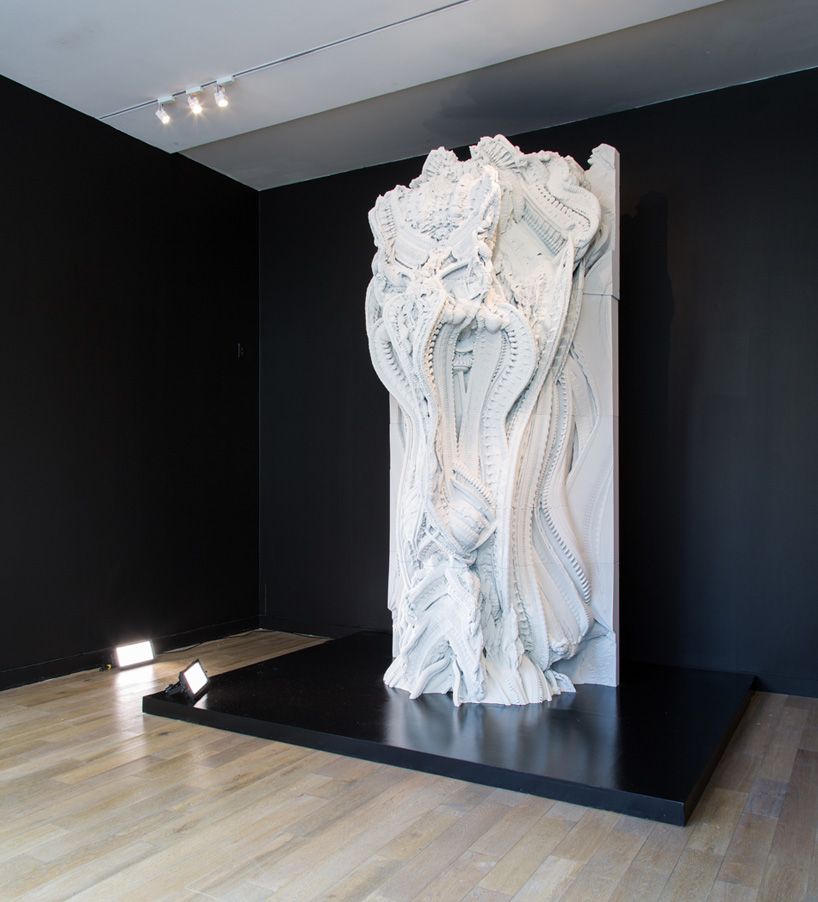
The relationship between architecture and nature is complex. If, on the one hand, we enjoy framing nature as art in our homes; on the other hand, we try at all costs to avoid the presence of obstructive "real" nature in our walls and structures, which can be damaged by roots and leaves. At the same time, we use green roofs, vertical gardens and flower boxes to bring cities closer to nature and improve people's wellbeing; but we also construct buildings with materials that are completely dissociated from fauna and flora. Although the advancement of biomaterials and new technologies is gradually changing this, we should nevertheless ask ourselves whether the structures and buildings we occupy need to be separated from the nature that surrounds them. This was the question that led researchers at the University of Virginia (UVA) to develop geometrically complex 3D-printed soil structures on which plants could grow freely.
https://www.archdaily.com/989216/nature-and-technology-walls-that-can-grow-plantsEduardo Souza
Environmentally Friendly Materials: 8 New Products To Reduce Carbon Emission
luffa fibres.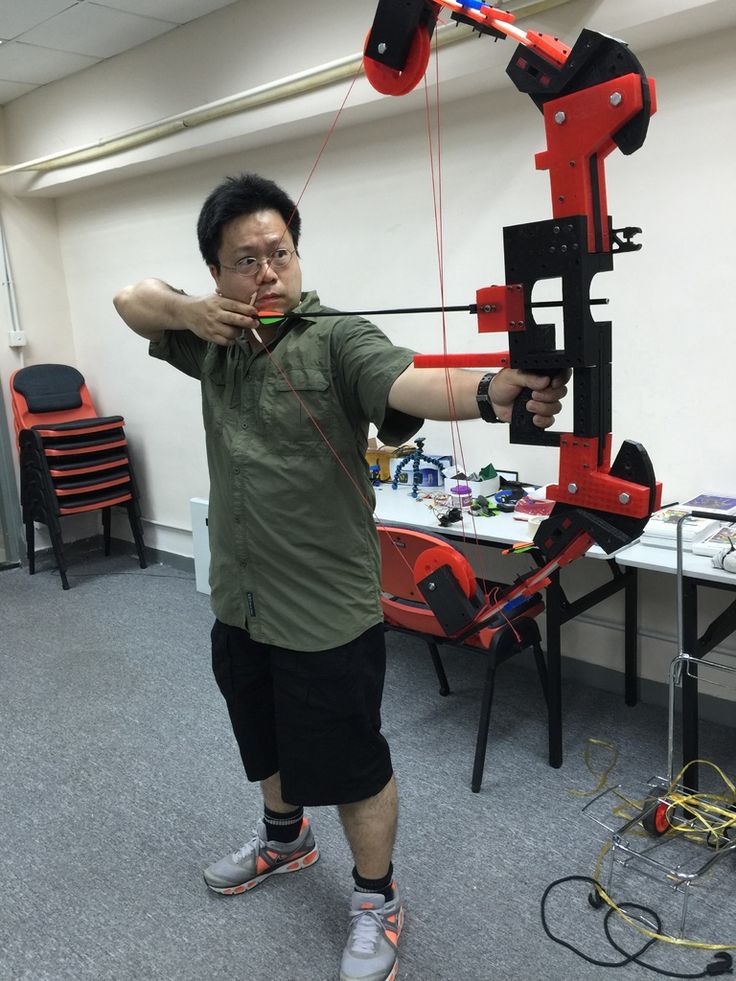
The construction industry's future will undoubtedly include "carbon reduction" as a mandatory task. Aside from locally sourced, virgin materials, an increasing number of new materials are becoming available. New materials can be developed in several ways, including low-carbon substitution, recycling, performance enhancement, and 3D printing. New materials will not only be more environmentally friendly and enable new construction methods, but they will also influence the starting point and direction of design concepts, resulting in new buildings with new perceptions and spaces.
+ 20
https://www.archdaily.com/988054/how-will-carbon-reduction-be-achieved-in-the-future-in-terms-of-material-selectionXiaohang Hou
The Future of Architecture: Imagining a World Where Buildings are Constructed from Living Materials
To Grow a Building / Jerusalem Design Week 2022.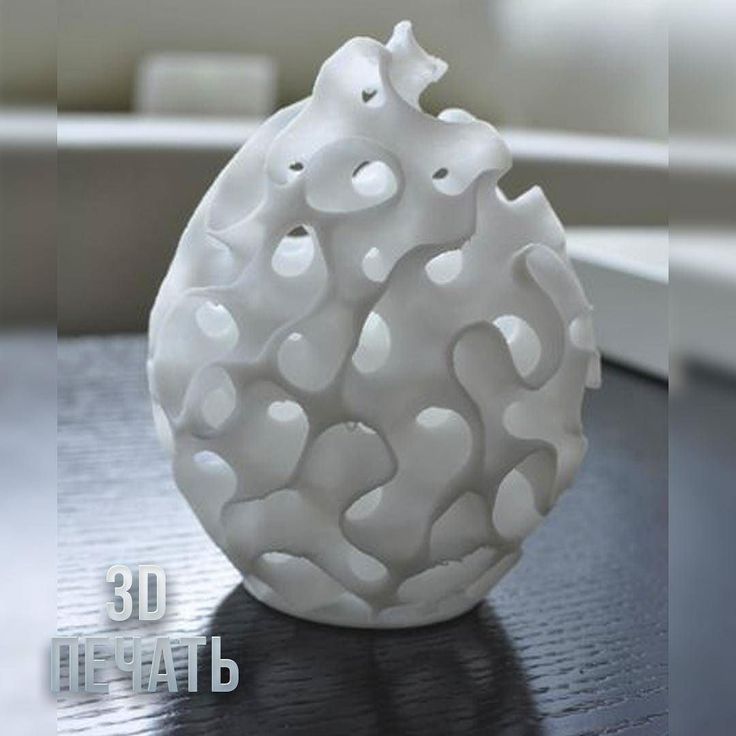
Can you imagine a world in which the built environment around us is 3D printed from living materials? That buildings will germinate, bloom, wither, produce new kinds of material, and eventually return back to the soil? To Grow a Building is a performative lab space that 3D prints - in real time - a live structure. The project presents a new approach to integrating flora into the design process, by developing a novel material for 3D printing, through which seeding is an inseparable part of the fabrication process. To Grow a Building is a gate into a future world in which there are people who build buildings, and there are people who grow them.
+ 85
https://www.archdaily.com/987459/the-future-of-architecture-imagining-a-world-where-buildings-are-constructed-from-living-materialsJullia Joson
3D-Printed Masonry Wall: The Introduction of Digital Craftsmanship
© Fred HunsbergerSince the 1980’s, 3D-printing has offered new ways of developing architecture, engineering, and objects of daily use. When it comes to digitizing analogue processes, it is vital for users to become familiar with current tech innovations and their benefits. HIVE Project reshapes the art and craft of building in clay by combining traditional ceramics, smart geometry, and robotic precision to construct a masonry wall composed of one hundred seventy-five unique 3D-printed clay bricks.
https://www.archdaily.com/985574/3d-printed-masonry-wall-the-introduction-of-digital-craftsmanshipCamila Prieto
A Coastal Intervention with 3D Terracotta Printing: Stools and Shelters for Aquatic Fauna
© Christian J. LangeAs humanity becomes aware of its impact on the environment, it has also sought ways to reverse some of the harm caused to fauna and flora, especially in cities. Our way of living, consumption and construction has caused severe damage to nature. In fact, according to a study from the Weizmann Institute of Science, we are at a point of inflection where the mass of all man-made materials is equal to the planet's biomass, and it should double by 2040. But not necessarily everything we build should have a negative impact. "The Tidal Stool" project is an example of this - part of a comprehensive revitalization project in Kuk Po Village in Shau Tau Kok in Hong Kong, which brings together two different ecologies, the anthropocentric and natural environment.
+ 20
https://www.archdaily.com/983377/a-coastal-intervention-with-3d-terracotta-printing-stools-and-shelters-for-aquatic-faunaEduardo Souza
Towards Sustainable and Affordable Housing: Is 3D Printing the Future or the Present?
ICON 3D Printed Homes Community First Village, Austin, TX. Image © Regan Morton PhotographyIn recent years, the construction industry has faced unprecedented challenges. A lack of skilled workers is driving up costs of labor, there is a global housing shortage, and the effects of climate change around the world are clearer than ever. Therefore, questioning traditional construction methods and pushing the limits of innovation has become a top priority, forcing the industry to implement new technologies as they get on board the digital transformation era. There is one innovation, however, that looks particularly promising: 3D construction printing. Although relatively recent, the technology has already been successfully tested in numerous structures, houses and apartment buildings, reshaping residential construction as we know it. Hence, 3D printing could very well be a viable alternative for more efficient, sustainable and cost-effective mass housing solutions in the near future, positively impacting people’s lives and contributing to greener, healthier cities.
https://www.archdaily.com/979103/towards-sustainable-and-affordable-housing-is-3d-printing-the-future-or-the-presentValeria Montjoy
"Form Freedom with Mass Customization": Technical Challenges in 3D Printing
Cortesia de De Huizenprinters consortiumWhen browsing the 3D printing tag on ArchDaily, it is clear that this technology has developed at an incredibly fast pace. If in the early years we observed the concept as a distant possibility for the future or with small-scale examples, in recent years we have observed entire printed buildings and increasingly complex volumes being produced. Developed by reading a computer file, the fabrication is carried out through additive manufacturing with concrete - or other construction materials - and presents numerous difficulties in providing an efficient process that enables the constructive technique to become widespread. The pavilion printed by the Huizenprinters consortium, for example, illustrates this process well.
https://www.archdaily.com/980754/form-freedom-with-mass-customization-technical-challenges-in-3d-printingEduardo Souza
3D Printing with Low-Carbon Concrete: Reducing CO2 Emissions and Material Waste
Courtesy of Hyperion RoboticsAfter water, concrete is the second most-consumed material on the planet and its production is substantially growing, expected to increase from 4.4 billion tons, reaching production up to 5.5 billion tons by 2050. Unfortunately, this comes at a huge environmental cost, accounting for almost eight percent of the global carbon emissions. With this estimated expected growth, stakeholders in the construction industry must work on integrating sustainable building materials and innovative processes.
https://www.archdaily.com/979145/3d-printing-with-low-carbon-concrete-reducing-co2-emissions-and-material-wasteRene Submissions
ICON Completes First House in New Series of Additive Construction Explorations
© Casey DunnConstruction technology company ICON unveiled its newest 3D-printed project, “House Zero”, designed by Texas-based firm Lake|Flato Architects. The project is the first in ICON’s “Exploration Series,” which seeks to highlight the architectural possibilities enabled by additive construction and develop new design languages with the purpose of “shifting the paradigm of homebuilding”. The material honesty of the house combines the expression of robotic construction processes with the natural wood textures creating a timeless design.
+ 5
https://www.archdaily.com/977809/icon-completes-first-house-in-new-series-of-additive-construction-explorationsAndreea Cutieru
Can 3D Printing Reshape Residential Architecture as We Know It?
Courtesy of PERIBy 2025, Dubai plans for a fourth of its buildings to be printed in 3D construction methods, demonstrating the potential of a fast-growing technology capable of redefining and pushing the limits of traditional architecture. As the technique emerges as a viable solution in the construction, engineering, and architecture areas, its popularity is quickly increasing. In fact, just between 2021 and 2028, the global 3D construction market is expected to grow by 91%, according to a July 2021 report by Grand View Research. Why this rapid growth? Besides being a faster alternative and having lower construction costs, it can also provide affordable housing solutions and allow countless design possibilities, among many other benefits. Thus, as architects must adapt to a new technological era, where speed and efficiency have become key factors in design and execution processes, the rise of 3D printing shows enormous promise. It could even help reshape construction as we know it.
https://www.archdaily.com/970937/can-3d-printing-reshape-residential-architecture-as-we-know-itValeria Montjoy
Is Fake the New Real? Searching for an Architectural Reality
Marta Minujín, Parthenon of Books, Dokumenta 14, Kassel, Germany, 2017. Image by Anne-Catrin Schultz.. Image Courtesy of Real and Fake in Architecture–Close to the Original, Far from Authenticity?Excerpt from the book: Real and Fake in Architecture–Close to the Original, Far from Authenticity? (Edition Axel Menges)
The term “fake” has been in the media frequently in the early 21st century, referring to headlines and fictional statements that are perceived as real and are influencing public opinion and action. Replacing the historically more common term “propaganda,” fake news aims at misinformation and strives to “damage an agency, entity, or person, and/or gain financially or politically, often using sensationalist, dishonest, or outright fabricated headlines.” Tracing fake news and differentiating “real” information from personal opinions and identifying intentional (or unintentional) deceit can be complicated. It is similarly complex to trace the duality of fake and real in the built world. To explore the larger context of fake statements in architecture and environmental design, a look at the definition of fake and related terms might be necessary.
+ 16
https://www.archdaily.com/977462/is-fake-the-new-real-searching-for-an-architectural-realityAnne-Catrin Schultz
"Robotic Construction Can Help Us Design Better Buildings": An Interview with HANNAH
HANNAH Office is a US-based experimental research and design studio whose work focuses on advancing architecture and contemporary construction practices by examining the possibilities of new digital routines and fabrication technologies. Selected as one of Archdaily's Best New Practices of 2021, HANNAH Office was founded in 2012 by Leslie Lok and Sasa Zivkovic and constitutes a platform for exploring technology and material methods across a variety of scales, from furniture to urbanism in search of new design outcomes.
+ 7
https://www.archdaily.com/976735/robotic-construction-can-help-us-design-better-buildings-an-interview-with-hannahAndreea Cutieru
First Images of Killa Design's Museum of the Future in Dubai Unveiled Ahead of Opening
Courtesy of MoTFNew images of Dubai's Museum of the Future by Killa Design and Buro Happold have been unveiled ahead of its official opening on February 22nd, 2022. The museum promises a one-of-a-kind experience that merges science, technology, and the environment through distinct themes and immersive environments that tap into all five senses. The project aims to "transform the very perception of the future as we know it", showcasing a world that is imaginable 50 years from now.
+ 6
https://www.archdaily.com/976892/first-images-of-killa-designs-museum-of-the-future-in-dubai-unveiled-ahead-of-openingDima Stouhi
"The Same Technology that Will Allow Us to Address Housing Challenges on Earth, Will Allow Us to Venture Off to Space": Interview with Jason Ballard of ICON
Founded in late 2017, named one of the "Most Innovative Companies in the World" in 2020, and selected as ArchDaily's Best New Practices of 2021, ICON is a construction company that pushed the boundaries of technology, developing tools to advance humanity including robotics, software, and building materials. Relatively young, the Texas-based start-up has been delivering 3D-printed homes across the US and Mexico, trying to address global housing challenges while also developing construction systems to support future exploration of the Moon, with partners BIG and NASA.
Featured on Times’ Next 100, as one of the 100 emerging leaders who are shaping the future, Jason Ballard, CEO and Co-Founder of ICON spoke to ArchDaily about the inception of the company, worldwide housing challenges, his ever-evolving 3D printing technology, and process, his partnership with BIG, and the future of the construction field on earth and in space.
+ 13
https://www.archdaily.com/963686/the-same-technology-that-will-allow-us-to-address-housing-challenges-on-earth-will-allow-us-to-venture-off-to-space-interview-with-jason-ballard-of-iconChristele Harrouk
Building Complex Elements in Concrete with 3D Printed Foam Formworks
Courtesy of Patrick Bedarf | dbtWith the aim of generating a significant impact on the responsible and sustainable consumption of resources and energy in the construction industry, ETH Zürich in collaboration with FenX AG is using foam 3D printing (F3DP) to manufacture geometrically complex formwork for the construction of special elements in concrete.
https://www.archdaily.com/973893/generating-complex-elements-in-concrete-with-3d-printed-foam-formworkJosé Tomás Franco
3D Printing, Prefabrication, and Interior Design: Construction Trends for 2022
TECLA, 3D Printed Habitat by WASP and Mario Cucinella Architects.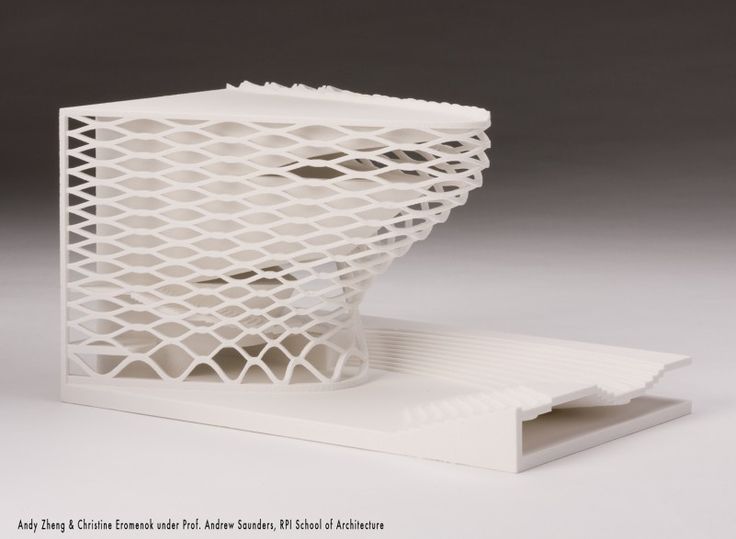
Jorge Drexler sings, in one of his songs, that “we always look at the river, contemplating the other riverbank”. Beyond understanding everything that was done, looking back at the past year can serve to get some clues about the future. This 2021, we published more than 160 articles in the Materials & Products section, covering a wide range of topics. From complex concepts such as 4D printing or very little processed materials such as hempcrete and bamboo, drawing a retrospective of the covered themes and understanding what interested our readers the most is an interesting exercise to foreshadow some trends in the future of the construction field. Looking at our most viewed articles, three large themes are evident: 3D printing, pre-fabrication, and interior renovation. Below, we present a compilation of each topic, reflecting on what we can dare to say about the trends in the construction industry that should consolidate in 2022.
https://www. archdaily.com/973281/3d-printing-prefabrication-and-interior-design-construction-trends-for-2022Materials
15 Architecture Projects for Life in Space
LUNAR HABITATION / Foster + Partners . Image Cortesía de Foster & PartnersThe Apollo 11 Mission, departed Earth on July 16, 1969, and touched down on the moon 4 days later. This moment marked a milestone for humanity and, to this day, makes us reflect on how technological progress is bringing us ever closer to life beyond planet Earth.
With the help of 3D printers, highly developed and fully automated constructive technology, we have compiled a selection of 15 architectural projects that demonstrate that life on the moon and beyond is closer than we've ever imagined.
https://www.archdaily.com/921752/50-years-after-the-moon-landing-15-architecture-projects-for-life-in-spaceBelén Maiztegui
Free STL file Arches National Park Double Arch・3D printing object for download・Cults
Statue of Liberty New York
Free
Ellis Island Litophane Museum New York
Free
Disneyland Castle
Free
Deer in the aspen forest
Free
Minecraft Catan Hexes
20. 46 €
Minecraft Catan Sheep Hex
5.12 €
Minecraft Catan Wheat Hex
5.12 €
Minecraft Catan Wood Hex
5.12 €
Minecraft Catan Brick Hex
5.12 €
Minecraft Catan Ore Hex
5.11 €
Statue of Liberty New York
Free
Disneyland Castle
Free
Best Files for 3D Printers in the Art Category
Celtic Knot #1(fidget toy and desk charm)
2.54 €
Marco Pagot(Porco Rosso)
Free
Cute Flexi Print-in-Place Ant
2 €
Patrick Star (Light printing without support)
0.50 €
Myrtle the Turtle
Free
Captain Okita
Free
Grinder Devil (Moledora Diablo)
Free
Art category bestsellers
Astronaut on flexi printer
3. 02 €
Catacombs Skull of Bones, Creepy Skeleton Skull, Pile of Bones Skull
6.07 €
GIANT CROCODILE HINGED
4.57 €
Leopard gecko articulated toy, imprinted body, snap head, cute flexi
3,48 €
Archaeopteryx nibbler
3 €
Pink Dragon, Valentine's Day, Articulating Animal Flexi Wiggle, Print on the Spot, Fantasy
4.15 €
Cute circus baby elephant with flexi print
3.02 €
BLACK WIDOW SPIDER
3.61 €
Flexi Print-in-Place Foot
2 €
Bearded Dragon toy, body with imprint, head with latch, cute flexi
3,48 €
Cute squirrel with flexi print
2,57 €
CUTE CROCODILE WITH FLEXIBLE PRINT IN PLACE
3. 02 €
Cute frog with flexi print
2 €
Cute sloth with flexi print
3.02 €
Skeleton hand with flexi print
2.04 €
Biting dragon
3 €
Do you want to support Cults?
Do you like Cults and want to help us continue our journey on our own ? Please note that we are a small team of 3 people, so supporting us in maintaining activities and creating future developments is very easy. Here are 4 solutions available to everyone:
-
AD: Disable your AdBlock banner blocker and click on our banner ads.
-
AFFILIATION: Shop online with our affiliate links here Amazon.
-
DONATIONS: If you want, you can donate via PayPal here.
-
* INVITE FRIENDS: * Invite your friends, discover the platform and great 3D files shared by the community!
3D printer light. Variants and implementation
3DPrintStory    Reviews     3D printer backlight. Variants and implementation
Have you ever got up in the middle of the night to check how 3D printing is going and frantically illuminated with a flashlight from your mobile? Or do you want your 3D printer to look cooler in the dark? The backlight can illuminate the entire 3D printer, workspace, or even the printhead, so there's room for your creative choices.
Aside from aesthetics and better visibility, another benefit of proper lighting is webcam accuracy, which is essential for programs like The Spaghetti Detective to track 3D print failures.
In this article, we'll look at a few different lighting options for your 3D printer, print head, or entire desktop. However, before we present these options, let's discuss some of the specifics of your lighting setup.
What to Look for When Choosing a 3D Printer Light
There are several factors to consider when deciding which 3D printer light is best for you.
- Placement and Orientation: If you direct the light towards the center of the 3D printer, it will illuminate the area of the printed model. If you place the backlight outward, then this illumination will be enough not only for your part, but for the entire 3D printer.
- Power: 3D printer backlighting can be implemented through the printer's power supply or take a separate power supply. If your printer uses a motherboard that supports backlighting, such as the SKR Mini E3 V2 or MKS Robin E3D, you can connect a compatible light source (same voltage) directly to the printer.
However, if your motherboard does not have this feature, you can power the lighting from an external source, such as a computer or wall socket.
- Color: If you need different colors, look for RGB (red, green and blue) lights that can produce any color. If you want a plain white light, we recommend that you choose a richer white color (brighter and whiter) for better illumination.
Now let's look at the options! Please note that although some of the suggested options are for the Ender 3, it is not difficult to change them for your specific 3D printer.
Illumination of the extruder zone on a 3D printer from profiles
The first option involves attaching an LED strip to your 3D printer's horizontal portal profile. Many 3D printers use aluminum V-groove profiles as part of the frame and gantry design, making them a great option for mounting LEDs. There are a huge number of options, it all depends on the number of tapes and your desires.
In essence, this lighting option for a 3D printer comes down to mounting an LED strip on a profile with a V-groove. Implementation may vary, there are many mounting options. For example, you can use mounting strips printed on a 3D printer and attach the LED strip to them already. Or mount the tape directly on the profile without using additional parts.
There is an interesting way to illuminate the extrusion zone with a flashlight. The Thingiverse link below will have a fastener that you can print and mount to your frame if you are using an Ender 3 3D printer. to the body, you can do it in other ways. There are many standard fixtures for lighting fixtures, so there are many options. As a general rule, these mounts are fine if you have a closed-case 3D printer.
You can 3D print fasteners yourself. For example, here is a variant of fixtures for LED strips. You can use screws or glue for fastening. The fasteners are pretty versatile.
There are options for more specialized LED strip fixtures for a specific 3D printer. For example, here is a mount for mounting on the body of a Prusa 3D printer. For example, these 3D printable models are designed to fit on the frame of a Prusa 3D printer.
3D Printer Arch Light
Another cool option that will take a bit more effort but will work great for lighting your 3D printer is the arch. After installing this arch with LEDs on your 3D printer table, you will be able to monitor both the 3D printing process and, in principle, use the large illuminated area for soldering and repairing small parts and assemblies. To make an arch, you will need a lot of 3D printed models and a rather large piece of LED strip, but the result is worth it.
3D printer light on print head
If you want to light the 3D print area directly, you can add light on the print head. This performance will help you directly illuminate the area of the current 3D print, as the source itself will move with the print head. Please note that due to the increased weight of the print head, additional noise and vibration may be generated, which may adversely affect the quality of 3D printing.