3D print a house in 24 hours
3D Homes That Take 24 Hours and Less Than $4,000 to Print
3D Homes That Take 24 Hours and Less Than $4,000 to Print Search iconA magnifying glass. It indicates, "Click to perform a search". Insider logoThe word "Insider".US Markets Loading... H M S In the news
Chevron iconIt indicates an expandable section or menu, or sometimes previous / next navigation options.HOMEPAGEScience
Save Article IconA bookmarkShare iconAn curved arrow pointing right.Download the app
New Story and Icon's first 3D-printed home model.- Last March, the 3D printing company Icon produced a 350-square-foot tiny home that cost $10,000 and took just 48 hours hours to build.
- The company was confident that it could print a larger structure in just 24 hours for even less — around $4,000 — since the printer wasn't running at full speed.
- A year after its prototype was released, Icon is now selling an upgraded version of its 3D printer.
Printable homes represent the latest wave in construction, but they're not always cheap or easy to build.
In March, New Story, a housing nonprofit based in San Francisco, and Icon, a construction-technology company that designs 3D printers, defied these stereotypes by producing a $10,000 tiny home in just 48 hours.
Icon called the structure "the first permitted, 3D-printed home in America."
Read more: A French family just became the first to permanently live in a 3D-printed home
At 350 square feet, the house was far cheaper than the average tiny home, which has a price tag hovering at around $25,000, but can often reach six figures. Before using 3D-printing technology, it took New Story eight months to build 100 homes, each costing about $6,000.
While the prototype was being developed, Icon's printer, known as the Vulcan, was running at only 25% speed. That gave the companies confidence that they could build a 600- to 800-square-foot home in just 24 hours for $4,000 or less.
When it comes to producing an average-sized home — around 2,000 square feet — the savings aren't quite as stark. A year after releasing its $10,000 prototype in Austin, Texas, Icon told the Wall Street Journal that printing a 2,000-square-foot home would cost around $20,000.
More remarkable is the fact that the company's upgraded printer, the Vulcan II, is now available for purchase, and could soon be used to produce affordable homes in places like Austin and Latin America.
Icon's first 3D model offers a glimpse of what the machine could produce in the future. Take a look.
The Vulcan II can produce a home seamlessly onsite, without having to piece together individual units.
New Story/BANDD DesignsThe printer churns out layers of cement, which amass to form the walls of the home. Non-printed fixtures like doors and windows are installed later.
The Vulcan II is capable of producing walls that are up to eight-and-a-half feet tall and up to 28 feet wide.
It's also made to withstand rural weather conditions, meaning it could operate during a power shortage or without access to potable water.
New Story/BANDD DesignsThe home's cement mixture is also able to withstand extreme weather conditions.
The New Story prototype features a living room, a single bedroom and bathroom, and a small office space.
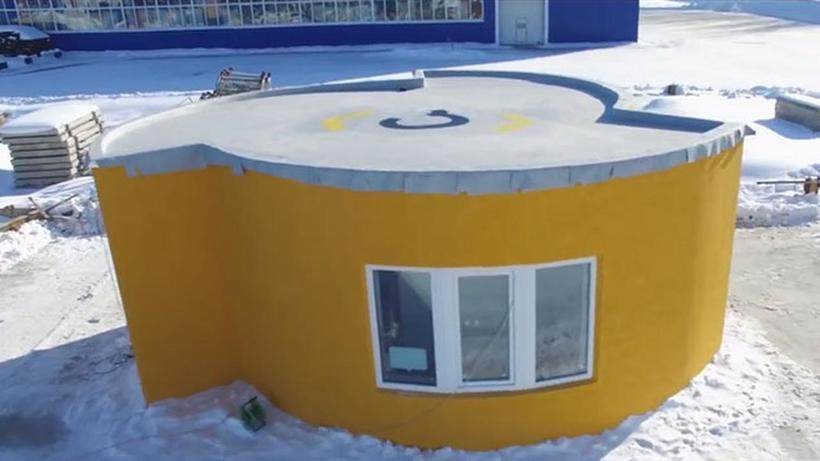
Families in El Salvador could move into the 350-square-foot homes this year, following seismic and safety tests.
New Story/BAAND DesignsIcon and New Story plan to produce more than 100 homes in El Salvador, a country whose rough terrain and frequent floods have made housing construction difficult.
New Story is seeking $1 million to print the homes, CNN reported last year.
From there, they hope to provide safe homes to some of the 1.3 billion people around the world residing in slums.
Icon will begin shipping its upgraded printer in April.
New Story/BANDD DesignsAn Austin-based developer called Cielo Property Group is planning to use the printer to build affordable homes in the area.
The next stop? It could be 3D-printing in space.
New Story and Icon's first 3D-printed home model.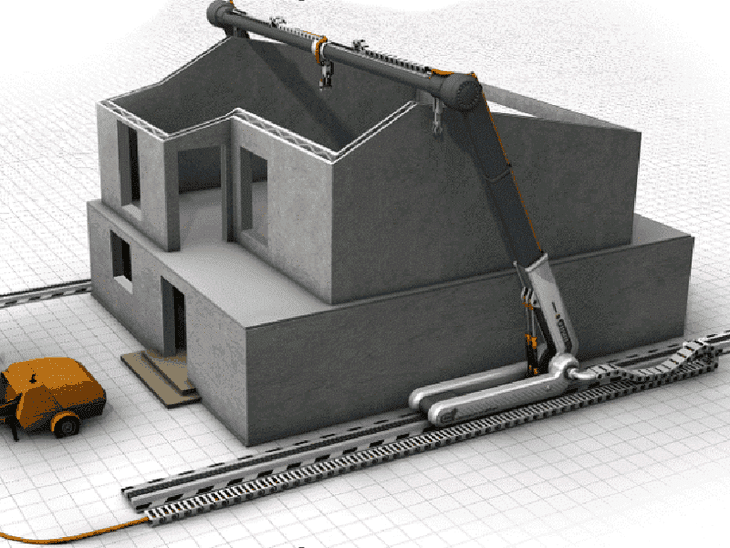
Icon is researching how its printing technology might be used to build space habitats. As the company put it: "It sounds crazy, but it would be a lot crazier to fly sheet rock and 2x4's to Mars."
Read next
LoadingSomething is loading.Thanks for signing up!
Access your favorite topics in a personalized feed while you're on the go.
More...
3D Printed House Was Built in Just 24 Hours, and We Want to Live in It
3D Printing Has Made Incredible Feats, but Can It Also Answer the Housing Crisis?
What if you could build a house in just 24 hours? Actually, you don’t have to. This 3D printing machine can do that for you.
3D printing has inspired some remarkable designs over the last decade. From engineers to fashion designers, anyone has used 3D printing to bring their ideas to life, meanwhile saving time and money. Innovators are also harnessing the power of 3D printing to solve worldwide problems ― think 3D printed organs and recyclable cars.
But what about using 3D printing to solve another problem: housing?
The first 3D-printed, on-site house
Apis Cor wanted to prove that not only could they print a house using a 3D printing machine but that they could do it in less than 24 hours. Together with PIK companies, they printed the first on-site house in Stupino, Russia. Unlike other 3D printed houses, the machine printed the house as a whole rather than component parts.
The yellow, three-pronged, tycoon-shaped house is just 38 m2 and one story tall. The unusual shape of the house was purposeful. Apis Cor wanted to show the machine’s flexibility and diversity in formats available.
Inside, there’s a hall, bathroom, living room and compact functional kitchen complete with modern Samsung appliances. It also has a washing machine that lets you add forgotten laundry and detergent to a running load without starting over (score!). If that’s not cool enough, you can also control it remotely via your smartphone.
Extreme conditions, meet smart solutions
The team used concrete as the printing “ink” to construct the house, which presented a challenge. The build took place in 2016 during the coldest time of the year, where temperatures average 17-26°F. Although the machine can operate at temperatures below -31°F, the concrete mixture only works above 41°F.
Apis Cor solved this problem by pitching a large tent around the machine to control the temperature. With new materials like geopolymers, companies can soon print houses any time of the year.
After the walls were printed, the team applied insulation and a roof to withstand the snowy winter. They touched-up the house with eco-friendly, weather-resistant paint and climate-control windows.
What are the saving – if any – of 3D printing houses?
In total, the build cost $10,134 equal to approximately $275 per m2. A square printed house using more standard materials would have cost just $233 per m2. Additionally, 3D printing houses erases the risk of human error during construction.
Typical construction cost for anything from houses to hotels can range from $810 to $2,650 per m2, according to Mortgage House. And that’s on the low end of construction costs. Furthermore, building a standard cottage house can take up to 2 months to complete.
Apis Cor believes this house in Stupino is a big leap to a new evolutionary stage. Going forward, they hope that this build can convince others worldwide that 3D printing is a reality in the construction market.
An answer to the housing crisis?
We’ve seen 3D printed human organs, musical instruments and cars that function equally to their non-3D-printed counterparts. Now, companies can create unique 3D printed houses in less than 24 hours no matter the weather.
For the housing crisis worldwide, this offers an innovative and achievable solution for lack of housing. As 3D printing advances and becomes more popular, countries can use this technology to meet the demands for more affordable housing in any climate. And, they can build the houses faster than ever before.
3D printing technology for residential buildings becomes a reality in 24 hours
From space exploration to robotics and medicine, 3D printing has huge potential in all areas, but especially it is starting to make a real impact in the world of affordable housing. The latest example of this is a slightly augmented project for the homeless in Texas, USA, which began with the construction of a stylish new 3D-printed administrative block in just one day.
The construction company behind the new 3D printed homes goes by the name ICON. The company presented its first prototype during the Texas media conference SXSW 2018, and after that it set about building an entire village - the world's first 3D-printed neighborhood, in a poor area of South America. Its Vulcan II 3D printer is designed to build simple boxes of houses, while the installation of roofs, doors and window openings is carried out by builders. The company is able to build housing much cheaper and more efficiently, and its concept shown at SXSW took just 48 hours to complete and cost just $10,000.
The Village of 3D Printed Homes aims to instill hope for a secure future for low-income people whose income does not exceed $200 a month, while promoting this concept of affordable housing solutions around the world.
Participation in a new project in Austin, Texas called Community First! Village was the next step for ICON. The project is led by local non-profit organization Mobile Loaves & Fishes for the homeless and will include more than 500 homes on 20 hectares when completed. In this social settlement of more than five hundred houses, additional addresses will appear - six objects made using the 3D construction method. Designed by Texas-based Logan Architecture, Icon will print three houses at once for the first time to showcase their build efficiency and focus on cost reduction. According to the company, all six houses will be rented out before the end of the year, but construction of the 46 sq. m. welcome center building is already completed at this stage. m for the future village, which was printed in just 27 hours. These 3D houses are among the affordable ones and will be ready to move in in just a few weeks.
How does it work?
The façade of the building is erected on the Vulcan printer developed by the company. The device prints walls with a mortar of concrete that retains its shape as it cures. Such technology allows them not to collapse. After erecting the facade, the builders install the necessary infrastructure, a wooden roof and windows. It takes a little more than 24 hours to fully build a finished house, depending on the building area, the maximum figures of which are about 75 square meters. The company installed the first such house in the American city of Austin.
This development has a number of advantages, such as relative cheapness, construction time, and the ability to build houses in conditions with limited resources and harsh climatic conditions. In addition, the walls of the building have an air gap that retains heat in cold weather. The estimated cost of building a dwelling is $4,000.
The second generation of this printer, the Vulcan II, is designed specifically for the production of reliable one-story buildings - quickly, inexpensively and with great variability. The printing area has been increased to 186 square meters. m, the width of the walls is adjustable for different sizes of panels. You can transport the printer in a special trailer; no assembly is required before starting work.
As ICON assures, anyone who has been instructed will be able to operate this printer. All functions are intuitive and displayed on the tablet screen. The printer itself is 3.5 meters high and 10 meters wide. It prints walls up to 2.5 meters high on a foundation up to 8.5 meters wide. It prints a part 0.3 high and 0.6 m wide at a speed of 1.5 - 2 meters per second.
Especially for the operation of the machine, the company has developed and patented a recipe for concrete-lime material Lavacrete. It has passed all strength tests and is recognized as safe for residential construction.
This is not the first attempt at 3D printing living spaces. Recall that in the spring of 2017, researchers from the Massachusetts Institute of Technology presented a similar construction technology.
Not only American startups are going to solve the problem of affordable housing with printing. A similar project is planned in India. Tvasta promised the first printed houses this year. Indian technology takes more time: the startup plans to print the components of a 30-square-meter house in about three days, and assemble it “under the roof” within a week.
Source: New Atlas
3D printer will build a house in 24 hours
Researchers have announced the creation of a giant 3D printer that "prints" concrete and should revolutionize the construction industry. This printer is able to build a house with a total area of 230 sq. m. in just 24 hours.
The author of the printer, Professor Berok Khoshnevis from the University of Southern California (USA), said that his brainchild can build a full-fledged house layer by layer, in a single day.
According to MSN News, the giant robot will replace a crew of construction workers with wet concrete ejected from a special nozzle to form the walls of the house according to a pre-designed computer scheme.
This is “virtually commonplace 3D printing, only at the scale of a building,” Khoshnevis said.
"Contour construction" is a technology in which buildings are built in layers, has great potential for maximum automation of the process of creating architectural structures.
With this technology, it is possible to create both single buildings and whole series of buildings with different designs at a time, and each building will immediately be equipped with air conditioning, built-in electrical and plumbing systems.
This technology can be used in all kinds of emergencies, for the construction of cheap housing, etc.
In addition, compared to traditional construction, "contour construction" saves on electricity and causes much less harm to the environment.
A giant 3D printer presented by engineers at the University of Southern California, USA, is capable of creating a full-fledged residential building in a day.
During the specified time period, the device "prints out" a separate house with an area of 250 square meters. m. The invention was presented by a scientist, professor Berok Khoshnevis . His system of express "building" housing was called Contour Crafting.
In fact, the printer is a giant robot with a nozzle mounted on a frame, through which the concrete mixture passes and is applied layer by layer, according to a plan pre-designed by a computer,
All that is required of the workers is to install the rails along the contour of the future house and attach the 3D printer structure to them. The computer does the rest.