Sandstone 3d printer filament
All About Sandstone 3D Printing Filament: Materials, Properties, Definition
Resources3D Printing DesignAll About Sandstone 3D Printing Filament: Materials, Properties, Definition
Learn about sandstone 3D printing filament and all of its different properties.
By Team Xometry
September 19, 2022
8 min read
RECENT STORIES
Polypropylene vs. Nylon: Material Differences and Comparisons
January 6, 2023
7 min read
Silicone vs. Neoprene: Material Differences and Comparisons
January 6, 2023
7 min read
Polypropylene vs. Polystyrene: Material Differences and Comparisons
January 6, 2023
9 min read
Sandstone 3D printing filaments are artistically and visually pleasing when used to build 3D models. 3D printing enthusiasts and hobbyists alike have been fascinated by the variety of colorful designs that can be created with these filament materials, especially in the embellishment of action figures or figurines. Sandstone filament also benefits the architectural and construction industry, for which it aids considerably in the crafting of very realistic designs of architectural and landscape models.
The 3D printing filament is called sandstone because it possesses the rock-like features of a sandstone. Sandstone printing filament is composed of PLA (Polylactic Acid) and ceramic or limestone powder. Among its properties, it: can be inked easily, is not water resistant, and melts at a temperature of 165–210°C. Sandstone filament does not need a heated bed and does not warp or shrink during the printing process. Also, the sandstone binder allows for stronger binding between the layers of the extruded material.
This article will further discuss what sandstone is, its composition, properties, printer settings, and how it compares with other filaments.
What Is Sandstone 3D Printing?
Sandstone 3D printing is the use of 3D printing technology – particularly color jet printing – to build sandstone-like models. Sandstone is a great option for multicolor printing. It transcends many filament types when it comes to the 3D printing of decorative models. Some of the applications of sandstone 3D printing include figurines, medical models, and architectural models. Sandstone is among the most popular 3D printing filaments because it prints with different surface textures when printed at different temperatures. For example, a lower temperature of 165 °C will produce a model with a smoother finish, while a higher temperature of 210 °C will produce a rougher finish. A single model can be created with different surface textures by altering the print temperature. For more information, see our guide on how 3D printing works.
What Is the Composition of Sandstone Filament?
Sandstone filament is generated by fusing PLA (Polylactic Acid) with limestone or ceramic particles. Sandstone-printed parts look a lot like ceramic or sandstone. Most 3D models go through post-processing to achieve a smooth surface finish. However, the rock-like finish of sandstone filament is a positive attribute that benefits several design types, such as architectural models.
What Are the Properties of Sandstone Filament?
Sandstone filament is a very interesting material with several physical properties including:
- The surface finish of the model is rock-like.
- It is relatively lightweight.
- When it comes to high-strength applications, sandstone is certainly not the choice. It is known for its rigidity and brittleness.
Comparison of Sandstone Filament Properties
Table 1 below highlights a side-by-side comparison of the properties of sandstone with other filament materials:
Table 1: Comparison of Sandstone vs. PETG vs. ABS vs. TPU
Properties | Sandstone | PETG | ABS | TPU |
---|---|---|---|---|
Properties Melting or printing temperature | Sandstone 165–210 °C | PETG 230–250 °C | ABS 240–270 °C | TPU 220–250 °C |
Properties Heated bed temperature (not necessary) | Sandstone 45–70 °C | PETG 70–80 °C | ABS 95–110 °C | TPU 30–60 °C |
Properties Impact resistance | Sandstone Poor | PETG Good | ABS Good | TPU Good |
Properties Rock-like finish | Sandstone Yes | PETG No | ABS No | TPU No |
What Are the Limitations of 3D Printing With Sandstone?
3D printing with sandstone, though very useful, comes with a disadvantage. Layers of construction are difficult if not impossible to smooth out; as a result, this sandstone-like material has a haptic feel to it. The surface is also quite porous, not waterproof, and has low impact resistance. Some of its advantages are that the material is resilient and flexible, and compared to other filaments it seldom warps.
Why Is Sandstone Used in 3D Printing?
Sandstone is used in 3D printing for many reasons. Prototypes can be 3D printed according to a prescribed set of colors. There are a myriad of colors to choose from, which enables one to create visually and artistically pleasing models. The material allows for ink coloring and can be structurally fused with definite precision. 3D-printed sandstone is not ideal for creating functional parts because of the brittle nature of the material. In other words, it breaks easily under intense stress. This property is why it is used essentially for decorative pieces.
How To Use Sandstone in 3D Printing?
Getting everything right at the outset ensures that 3D printer sandstone comes out in the best texture, form, and shape possible. Here are some tips and tricks for 3D printing with sandstone:
- Limestone or gypsum-based powder should be used. This powder goes along with a binder which facilitates the fusion. The binder is a glue-like solvent that has been mixed with CMY or CMYK colors.
- Sandstone 3D printing filament can do without a heated bed. However, if a heated bed is used, let it fall between 40–70 °C.
- The model should be handled with care and should not come in contact with water. If that happens, it will cause the model to lose its lustrous color.
To get a really good finish, print in the temperature range 165–210 °C
What Are the Best Configuration Settings for Sandstone 3D Printing?
The best configuration settings for sandstone 3D printing depend on the brand used. It is recommended to check the manufacturer’s recommended settings to get optimal results. Table 2 below shows the recommended printer settings for sandstone filament:
Table 2: Sandstone Filament 3D Printer Settings
Printer Settings | Value |
---|---|
Printer Settings Extruder temperature or nozzle temperature or print temperature | Value 165-210 °C |
Printer Settings Bed temperature | Value 45-70 °C |
Printer Settings Print speed | Value 50-60 mm/s |
Printer Settings Extruder fan speed | Value 0-10% |
Printer Settings Retraction speed | Value 20-45 mm/s |
Printer Settings Retraction distance (direct) | Value 2-3 mm |
Printer Settings Retraction distance (Bowden) | Value 4-6 mm |
Printer Settings Flow rate | Value 95-105% |
Printer Settings Bed material | Value Glue Stick, PET Sheet, Kapton Tape, and Glass Plate |
What Is the Best Sandstone 3D Print Speed?
The best sandstone 3D print speed ranges from 50–60 mm/s. The speed should stay within this limit. However, an individual can start with a low speed and work up until an unusual level of strings begins to form on the print. When this formation of strings happens, reduce speed a little and observe the results.
What Is the Melting Temperature of Sandstone Filament?
The melting temperature of sandstone 3D printing filament is between 165–210 °C. The printing temperature depends on certain factors, namely, the type or brand of filament used, the type of printer, and the part requirement. The temperature has a direct impact on the model's surface texture. Adjust the temperature setting until the preferred texture is reached. To print a model with varying surface texture, alternate between the specified melting temperatures.
Is a Heated Printing Bed Required When Printing With Sandstone?
No, sandstone 3D printing filament does not require a heated printer bed. The reason is that sandstone filament does not warp during 3D printing. However, if a heated bed is used, set it at a temperature that falls in the range of 40–70 °C.
What Is a Good Wall Thickness for 3D Printing Sandstone?
A good wall thickness for 3D printing sandstone is 2 mm for supporting walls – connected to at least two sides of the 3D model. However, if it is an unsupported wall – connected to only one side of the 3D model – a value of 3 mm should be used.
What Is a Good Wall Density for 3D Printing Sandstone?
Generally, the infill density used for most filaments falls between 15-50% – and sandstone 3D printing filament is not an exception. Infill density describes how much thermoplastic material or filament the inside of a 3D print is made of. It is usually measured or defined as a percentage in slicer software programs.
Slicers are calibrated to read an infill density ranging from the very least (0%) to the highest (100%). 0% means the part is hollow and 100% implies that the part is completely solid and strong. The decision on which infill density to use is highly dependent on the application. For functional and end-use parts, an infill density above 50% is recommended. For prints that do not need to be super strong, an infill density of 15-50% is okay.
Is Sandstone Filament Water Soluble?
There is no available information on sandstone filament’s water solubility. It is recommended to refer to the manufacturer’s material data sheet.
What Is the Difference Between Sandstone and PLA in 3D Printing
PLA is created from organic materials such as sugarcane and corn (also included in the composition are additives). Sandstone, on the other hand, is made by combining PLA with calcium or ceramic powdered particles. PLA use cases include medical implants, medical suturing, and food packaging purposes. While sandstone is used for artistically pleasing applications such as architectural models, figurines, and landscape design models.
Summary
This article presented sandstone 3D printing filament, explained what it is, and discussed how it can be used for 3D printed parts. To learn more about sandstone 3D printing filament, contact a Xometry representative.
Xometry provides a wide range of manufacturing capabilities, including 3D printing and other value-added services for all of your prototyping and production needs. Visit our website to learn more or to request a free, no-obligation quote.
Disclaimer
The content appearing on this webpage is for informational purposes only. Xometry makes no representation or warranty of any kind, be it expressed or implied, as to the accuracy, completeness, or validity of the information. Any performance parameters, geometric tolerances, specific design features, quality and types of materials, or processes should not be inferred to represent what will be delivered by third-party suppliers or manufacturers through Xometry’s network. Buyers seeking quotes for parts are responsible for defining the specific requirements for those parts. Please refer to our terms and conditions for more information.
Team Xometry
This article was written by various Xometry contributors. Xometry is a leading resource on manufacturing with CNC machining, sheet metal fabrication, 3D printing, injection molding, urethane casting, and more.
Sandstone Filament: Properties, How to Use Them, and Best Brands
3D Insider is ad supported and earns money from clicks, commissions from sales, and other ways.
If you have read our previous articles on composite filaments, you should be familiar with all the unique prints you can make with materials such as carbon fiber, stainless steel, and wood. Sandstone filaments are yet another one of these exotic materials. What can you do with sandstone filaments and how do you use them? In this article, we tell you just what you need to know to get started with these nifty sandstone filaments.
What are sandstone filaments?
Similar to other composite filaments, sandstone filaments are made by infusing PLA with a very fine powdered solid. In this case, this powdered solid is in the form of very fine milled chalk. Prints made from sandstone filaments simulate the look of sandstone or ceramic, depending on how they are printed and finished.
Although technically the term ‘sandstone’ can refer to a broad group of rocks composed of sand-sized particles, it is used in this context to refer to the overall finish or look of the final prints made from the specialty filament. Chalk, also known as limestone or calcium carbonate, technically is not a sandstone but is a practical material for this application. It is a lightweight and sturdy material that is quite resistant to weathering and can be ground down to a powder-like consistency.
Sandstone filaments can be used to make prints with a rock-like finish, a nice deviation from the polished look of prints made from other composite materials. The gritty finish of sandstone prints is perfect for interesting design pieces and architectural models. You probably won’t be the next Michelangelo, but at least you will not have to hammer and chisel your work of art.
How do you use sandstone filaments?
Sandstone filaments have the unique characteristic of being able to make prints with different surfaces depending on the printing temperature. According to the guidelines for the LAYBRICK brand of sandstone filaments, printing at around 165 °C results in a smoother finish while printing at around 210 °C results in a much rougher surface. This is a very interesting property, and we are quite curious about trying to print between these two temperatures to get just the right finish for a particular job.
There are no recommended printing speeds for sandstone filaments, but we have been able to get good results at a 60 mm/s setting. We recommend an initial setting of 50 mm/s, from which you may try working your way up until you observe an unpleasant degree of stringing.
A heated bed is not a necessity when printing using sandstone filaments, although you may set a temperature of about 50 °C should you be using one. Standard blue painters’ tape works really well for adhesion in a non-heated bed. Since the filament is PLA-based, any method of bed adhesion commonly used for PLA should work well enough with sandstone filaments.
The composite material is relatively heavier because of the powdered solids fused into the plastic, so we recommend speeding up the cooling process to strengthen the print as soon as possible. You may use a cooling fan at maximum setting when printing with sandstone filaments and ensure that the print bed is not enclosed to any degree.
Prints made from sandstone filaments can be finished in several creative ways. Like real stone carvings, sandstone prints can be sanded to achieve a smooth and consistent finish. Sanding also makes subsequent treatment compounds, such as paint, easier to adhere.
What are the benefits and limitations of sandstone filaments?
The main benefit of sandstone filaments is that they are a niche product: there is no other filament product in the market right now that can be used to make prints with a stone-like finish. If this is the type of finish you are going for in your 3D print, then you literally have no option but to use sandstone filaments. That being said, the aesthetics of sandstone prints is quite excellent.
The unique capability of sandstone filaments to create different finishes in the print based on the printing temperature definitely opens up avenues in creativity that other filaments cannot provide. Printing at low temperatures results in a finish that is very smooth, almost like ceramic. At higher temperatures, prints come out with a more layered and uneven finish, which also has character and may be desirable for some applications.
As with other composite filaments, sandstone filaments have very low tendency to warp or shrink. This makes it a very easy material to work with, as you need not worry about the effects of rapid cooling or fast extrusion.
Much has been written about the abrasiveness of composite filaments, which makes it necessary to upgrade to a hardened nozzle or to use a nozzle with a wider diameter. Sandstone filaments are much less abrasive compared to stainless steel or carbon fiber, primarily due to the soft nature of chalk and the finer chalk particles present in the filament. However, the mere presence of powdered solids in the filament will accelerate the wear and tear on a standard brass nozzle. We still recommend using a nozzle with a diameter of 0.5 to 0.6 mm. This will serve not only to decrease the effect of abrasion to the nozzle, but will also lessen the chances of clogging,
Probably the biggest challenge you will encounter when working with sandstone filaments is ensuring that the filament does not snap in the middle of the print. The filament itself is quite brittle and can be broken off with minimal effort. It is crucial to ensure that the path that the filament takes from the spool to the extruder is free of sharp turns which the brittle filament cannot negotiate without breaking.
Another drawback you will likely encounter with sandstone filaments is the fact that they can be quite expensive. They are not very hard to work with, so hopefully you will not end up wasting the filament.
What are the best brands of sandstone filaments available today?
There really is only one brand of sandstone filament that has achieved any degree of popularity. The LAYBRICK brand has pretty much cornered the market on sandstone filaments and has received very good feedback from 3D printing enthusiasts with different levels of experience. The LAYBRICK sandstone filament is a very easy material to work with since it has a wide range of printing temperatures and has almost zero warp. The filaments are available in both 1.75 mm and 2.85 mm diameters, and are only sold in 0.25 kg spools.
The final word
Material | Sandstone filament |
Properties | – Rigid and brittle – Lightweight – Results in a rock-like or ceramic-like finish |
Applications | – Architectural models – Design and display items |
Recommended printing temperature | 165 to 210 °C, depending on desired finish |
Recommended bed temperature | Heated bed is not required, but a temperature of 50 °C can be set if the bed is heated |
Bed adhesion | Standard blue painters’ tape |
Printing speed | 50 mm/s to 60 mm/s |
Cooling | Cooling fan at maximum setting is recommended |
We have to admit that sandstone filaments probably are not for everybody. They fulfill very specific needs and are a little too expensive for casual use. However, it is a fun and unique material to work with. Unlike other composite materials, working with sandstone filaments is quite easy since it is less abrasive, does not warp, and performs well over a broad range of printing temperatures. Should you have the inclination, you can make some very interesting projects with this niche filament.
Warning; 3D printers should never be left unattended. They can pose a firesafety hazard.
Laybrick 3mm: Kai P.
3D printer suppliesfrom Kai P.
Starting price 3 000 ₽
Starting price 3 000 ₽ - starting price 3 000 ₽
Starting price 3 000 ₽
Current price 2 500 ₽
2 500 ₽ - 2 500 ₽
Current price 2 500 ₽
| / nine0003
Saving 500 ₽ Saving 500 ₽
In stock
Laybrick is a material for 3D printing that allows, depending on the temperature, to obtain a different surface quality: from very smooth to rough, similar in feel and appearance to sandstone.
Polymer properties | nine0034 |
Material type | FDM |
Plastic diameter | 3 mm |
Material | Laybrick |
Laybrick
One of the advantages of FDM printing is the ability to create composites that mimic all kinds of materials, including wood, metals, and stone. Laybrick is the brainchild of renowned inventor Kai Party, creator of the popular Laywoo-D3 wood composite. This time, Kai set his sights on creating a sandstone simulant. As with Laywoo-D3, the material is very low maintenance, requiring no high extrusion temperature or platform heating.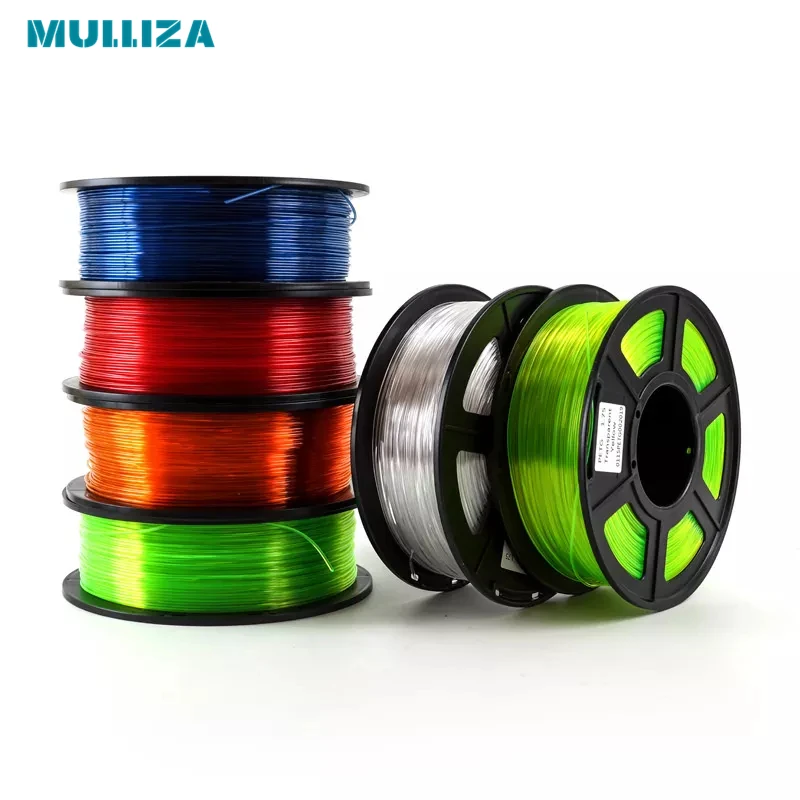
Recommended products
- Saving 1 000 ₽ Savings 0 ₽
Plastic PETG monofilament for 3D printing with LPD deposition filament, made of ethylene polymers (ethylene terephthal polymer...
Ultimaker
Starting price 5 500 ₽
Starting price 5 500 ₽ - starting price 5 500 ₽
Starting price 5 500 ₽
Current price 4 500 ₽
4 500 ₽ - 4 500 ₽
Current price 4 500 ₽
nine0080 - Savings 0 ₽ Savings 0 ₽
- Saving 1 600 ₽ Savings 0 ₽ nine0002 Plastic PVA monofilament for fusing 3D printing, from hydrolysis products (vinyl acetate polymer), filament diameter 2.
8...
Ultimaker
Starting price 5 500 ₽
Starting price 5 500 ₽ - starting price 10 500 ₽
Starting price 5 500 ₽
Current price 4 600 ₽
4 600 ₽ - 8 900 ₽
Current price 4 600 ₽
- Saving 7,000 RUB Savings 0 ₽ nine0103 Savings 0 ₽ Savings 0 ₽
FDM/FFF Consumables
FFF technology has many advantages, including the relative simplicity of the design of printers and the affordability of both devices and consumables. Moreover, the range of materials is perhaps the widest among all available technologies. As a rule, thermoplastics are used for printing, but there are exceptions - composite materials containing various additives, but based, again, on thermoplastics. In this section, we will try to talk about the most widely used materials in more detail, starting with the most popular types. nine0003
- 1 Polylactide (PLA, PLA)
- 2 Acrylonitrile butadiene styrene (ABS)
- 3 Polyvinyl alcohol (PVA)
- 4 Nylon
- 5 Polycarbonate (PC)
- 6 High density polyethylene (HDPE)
- 7 Polypropylene (PP, PP)
- 8 Polycaprolactone (PCL)
- 9 Polyphenylsulfone (PPSU)
- 10 Polymethyl methacrylate (Acrylic, plexiglass, acrylic, PMMA)
- 11 Polyethylene terephthalate (PET, PET)
- 12 High impact polystyrene (HIPS)
- 13 Wood Simulators (LAYWOO-D3, BambooFill)
- 14 Sandstone Simulators (Laybrick)
- 15 Metal Simulators (BronzeFill)
Polylactide (PLA, PLA)
Polylactide is one of the most widely used thermoplastics due to several factors. Let's start with the fact that PLA is known for its environmental friendliness. This material is a lactic acid polymer, which makes PLA a completely biodegradable material. The raw materials for the production of polylactide are corn and sugar cane. At the same time, the environmental friendliness of polylactide causes its fragility. Plastic easily absorbs water and is relatively soft. As a rule, PLA models are not intended for functional use, but serve as designer models, souvenirs and toys. Few practical industrial applications include the production of food packaging, drug containers and surgical sutures, as well as use in bearings that do not carry high mechanical loads (for example, in modeling), which is possible due to the material's excellent slip coefficient. nine0003
One of the most important factors for 3D printing applications is the low melting temperature of only 170-180°C, which contributes to relatively low power consumption and the use of inexpensive brass and aluminum nozzles. As a rule, extrusion is carried out at 160-170°C. At the same time, PLA solidifies quite slowly (glass transition temperature is about 50°C), which should be taken into account when choosing a 3D printer. The best option is a device with an open case, a heated work platform (to avoid deformation of large models) and, preferably, additional fans to cool the fresh layers of the model. nine0003
PLA has low shrinkage, i.e. loss of volume on cooling, which helps to prevent warping. However, shrinkage has a cumulative effect as the dimensions of printed models increase. In the latter case, the build platform may need to be heated to evenly cool the printed objects.
The cost of PLA is relatively low, which adds to the popularity of this material.
Acrylonitrile butadiene styrene (ABS)
ABS is perhaps the most popular thermoplastic used in 3D printing, but not the most common. This contradiction is explained by certain technical difficulties that arise when printing ABS. The desire of craftsmen to use ABS is determined by the excellent mechanical properties, durability and low cost of this material. In the industry, ABS plastic is already widely used: the production of car parts, cases of various devices, containers, souvenirs, various household accessories, etc. nine0003
ABS plastic is resistant to moisture, acids and oil, has a fairly high temperature resistance - from 90°C to 110°C. Unfortunately, some types of material are destroyed by direct sunlight, which somewhat limits the application. At the same time, ABS plastic is easy to paint, which allows you to apply protective coatings on non-mechanical elements.
Despite a relatively high glass transition temperature of around 100°C, ABS has a relatively low melting point. Actually, due to the amorphous nature of the material, ABS does not have a melting point, as such, but 180 ° C is considered an acceptable temperature for extrusion, which is on the same level as the above-described PLA. The lower temperature spread between extrusion and glass transition allows ABS to cure faster than PLA. nine0003
The main disadvantage of ABS plastic can be considered a high degree of shrinkage during cooling - the material can lose up to 0.8% of its volume. This effect can lead to significant deformations of the model, twisting of the first layers and cracking. To combat these unpleasant phenomena, two main solutions are used. First, heated work platforms are used to help reduce the temperature gradient between the lower and upper layers of the model. Secondly, ABS 3D printers often use closed housings and control of the background temperature of the working chamber. This makes it possible to maintain the temperature of the applied layers at a level just below the glass transition threshold, reducing the degree of shrinkage. Full cooling is carried out after receiving the finished model. nine0003
The relatively low stickiness of ABS may require additional bonding aids such as adhesive tape, polyimide film, or applying a solution of ABS in acetone to the platform just prior to printing. For more information on how to avoid warping, see How to Avoid Warping 3D Printed Models.
While ABS does not pose a health risk at room temperature, heating plastic releases acrylonitrile fumes, a poisonous compound that can irritate mucous membranes and cause poisoning. Although the amount of Acrylonitrate produced in small scale printing is negligible, it is recommended that you print in a well ventilated area or use an exhaust hood. It is not recommended to use ABS plastic for the production of food containers and utensils (especially for storing hot food or alcoholic beverages) or toys for small children. nine0003
The good solubility of ABS in acetone is very useful, as it allows large models to be produced piece by piece and then glued together, greatly expanding the capabilities of inexpensive desktop printers.
Polyvinyl alcohol (PVA)
Polyvinyl alcohol is a material with unique properties and special applications. The main feature of PVA is its water solubility. 3D printers equipped with dual extruders have the ability to print models with PVA support structures. Upon completion of printing, the supports can be dissolved in water, leaving a finished model that does not require mechanical or chemical roughening. Similarly, PVA can be used to create water-soluble master patterns for molds and molds themselves. nine0003
The mechanical properties of PVA are quite interesting. At low humidity, plastic has high tensile strength. With increasing humidity, strength decreases, but elasticity increases. The extrusion temperature is 160-175°C, which allows the use of PVA in printers designed for printing with ABS and PLA plastics.
Since the material easily absorbs moisture, it is recommended to store PVA plastic in dry packaging and, if necessary, dry before use. Drying can be done in a pottery kiln or an ordinary oven. As a rule, drying of standard coils takes 6-8 hours at a temperature of 60-80°C. Exceeding 220°C will cause the plastic to decompose, which should be taken into account when printing. nine0142
Nylon
Nylon is attractive due to its high wear resistance and low coefficient of friction. Thus, nylon is often used to coat friction parts, which improves their performance and often allows them to function without lubrication. Following the widespread use of nylon in industry, additive manufacturing has also become interested in the material. Attempts to print with nylon have been made almost since the early days of FDM/FFF technology. nine0003
In reality, there are several types of nylon produced by different methods and with slightly different characteristics. The most famous is nylon-66, created by the American company DuPont in 1935. The second most popular option is nylon-6, developed by BASF to circumvent the DuPont patent. These two options are very similar. In terms of 3D printing, the main difference is the melting point: Nylon-6 melts at 220°C, while Nylon-66 melts at 265°C. nine0003
Many hobbyists prefer to use commercially available nylon threads such as trimmer wire. The diameter of such materials often corresponds to the diameter of standard FFF materials, which makes their use tempting. At the same time, these products are usually not pure nylon. In the case of trimmer rods, the material consists of nylon and fiberglass for an optimal combination of flexibility and rigidity.
Fiberglass has a high melting point, and therefore printing with such materials is fraught with high nozzle wear and plugging. nine0003
Recently there have been attempts to commercially develop nylon-based printing materials specifically for FDM/FFF applications, including Nylon-PA6 and Taulman 680. These grades are extrudable at 230-260°C.
Since nylon readily absorbs moisture, store consumables in vacuum packaging or at least in a container with water-absorbent materials. A sign of excessively damp media will be steam escaping from the nozzle during printing, which is not dangerous, but may degrade the quality of the model. nine0003
When printing with nylon, it is not recommended to use a polyimide desktop coating as the two materials fuse together. As a coating, you can use adhesive tape with wax impregnation (masking tape). The use of a heated bed will help reduce the possibility of deformation of the model, similar to printing with ABS plastic. Due to the low coefficient of friction of nylon, extruders with studded feeders should be used.
The nylon layers have excellent adhesion, which minimizes the chance of delamination of models. nine0003
Nylon is difficult to bond, making it difficult to print large multi-piece models. Alternatively, fusion of parts is possible.
Since nylon can release toxic fumes when heated, we recommend that you print in a well-ventilated area or use an exhaust fan.
Polycarbonate (PC)
Polycarbonates are attractive due to their high strength and toughness, as well as resistance to high and low temperatures. nine0003
The potential health risk of printing is worth noting: the toxic and potentially carcinogenic compound bisphenol A is often used as a raw material. .
The extrusion temperature depends on the printing speed to avoid cracking, but the minimum temperature at 30mm/sec can be considered as 265°C. When printing, the use of polyimide film is recommended for better adhesion to the desktop surface. The high susceptibility of polycarbonate to deformation requires the use of a heated platform and, if possible, a closed housing with heating of the working chamber. nine0003
Polycarbonate is highly hygroscopic (easily absorbs moisture), which requires storage in dry conditions to avoid the formation of bubbles in the applied layers. For extended printing in humid climates, even the print spool may need to be stored in a moisture-proof container.
High Density Polyethylene (HDPE)
Arguably the most common plastic in the world, polyethylene is relatively rare among 3D printed materials. The reason for this is the difficulty in layer-by-layer manufacturing of models. nine0003
Polyethylene melts easily (130-145°C) and hardens quickly (100-120°C), as a result of which the applied layers often do not have time to set. In addition, polyethylene is characterized by high shrinkage, which provokes the twisting of the first layers and the deformation of the models as a whole during uneven solidification. Printing with polyethylene requires the use of a heated platform and a working chamber with accurate temperature control to slow down the cooling of the applied layers. In addition, you will need to print at high speed. nine0003
Difficulties in use are more than offset by the cheapness and availability of this material. Recently, several devices have been developed for processing plastic waste from HDPE (bottles, food packaging, etc.) into standard filaments for printing on FDM/FFF printers. Examples are FilaBot and RecycleBot. Due to the simplicity of design, RecycleBot devices are often assembled by 3D craftsmen.
Melting polyethylene releases harmful vapors, so it is recommended to print in well-ventilated areas. nine0142
Polypropylene (PP, PP)
Polypropylene is a widely used plastic used in the manufacture of packaging materials, utensils, syringes, pipes, etc. The material has a low specific gravity, is non-toxic, has good chemical resistance, is resistant to moisture and wear, and cheap enough. Among the disadvantages of polypropylene, one can note the vulnerability to temperatures below -5 ° C and to direct sunlight.
The main difficulty in printing with polypropylene is the high shrinkage of the material during cooling - up to 2.4%. For comparison, the shrinkage of the popular but already problematic ABS plastic reaches 0.8%. Although polypropylene adheres well to cold surfaces, it is recommended to print on a heated platform to avoid deformation of models. The minimum recommended extrusion temperature is 220°C. nine0003
Polypropylene printing filaments are sold by Orbi-Tech, German RepRap, Qingdao TSD Plastic. Stratasys has developed a polypropylene simulant optimized for 3D printing called Endur.
Polycaprolactone (PCL)
Polycaprolactone (aka Hand Moldable Plastic, Mold-Your-Own Grips, InstaMorph, Shapelock, Friendly Plastic, Polymorph, Polymorphus, Ecoformax) is a biodegradable polyester with an extremely low melting point of about 60 ° C . In practice, this property creates certain problems in 3D printing, since not all 3D printers can be configured to work at such low temperatures. Heating polycaprolactone to the usual extrusion temperatures (about 200°C) causes a loss of mechanical properties and may lead to breakage of the extruder. nine0003
Polycaprolactone is non-toxic, making it suitable for use in the medical industry and biodegradable. When ingested, polycaprolactone breaks down, which makes printing with this material safe. Due to the low melting point, there is no danger of burns when touching fresh models. The high plasticity of the material makes it possible to reuse.
Polycaprolactone is not suitable for creating functional mechanical models due to its viscosity (glass transition temperature is -60°C) and low heat resistance (melting point is 60°C). On the other hand, this material is perfect for the production of mock-ups and food containers. nine0003
The material sticks easily to the surface of even a cold working table and is easy to paint.
Polyphenylsulfone (PPSU)
Polyphenylsulfone is a high strength thermoplastic used extensively in the aviation industry. The material has excellent chemical and thermal stability and practically does not burn. Polyphenylsulfone is biologically inert, which makes it possible to use this material for the production of tableware and food containers. Operating temperature range is -50°С - 180°С. Plastic is resistant to solvents and fuels and lubricants. nine0003
For all its merits, polyphenylsulfone is rarely used in 3D printing due to its high melting point, reaching 370°C. Such extrusion temperatures are beyond the power of most desktop printers, although printing is theoretically possible using ceramic nozzles. Currently, the only active user of the material is Stratasys, which offers industrial Fortus installations.
Polymethyl methacrylate (Acrylic, plexiglass, acrylic, PMMA)
Polymethyl methacrylate is a well-known organic glass. The material is durable, moisture resistant, environmentally friendly, easy to glue, plastic enough and resistant to direct sunlight.
Unfortunately, acrylic is not suitable for FDM/FFF printing for a number of reasons. Acrylic is poorly stored in the form of spools of thread, as constant mechanical stress leads to the gradual destruction of the material. To avoid bubbles, the print resolution must be high, with a precision almost impossible for home printers. Acrylic's rapid curing requires strict environmental control of the working chamber and high print speeds. Again, the print speeds of FDM/FFF printers are inversely related to print resolution, which exacerbates the problem. nine0003
However, attempts are being made to print with acrylic, and some of them are producing relatively positive results. However, when creating sufficiently strong models, it is not yet possible to avoid the formation of bubbles and achieve the usual transparency of the material. At the moment, the best results with acrylic are shown by another printing technology - multi-jet modeling (MJM) from 3D Systems. In this case, a photopolymer version of acrylic is used. Stratasys has also made significant progress using its own photopolymer acrylic simulant VeroClear on Objet Eden printers. It is hoped that the high demand for acrylic will lead to the emergence of composite materials based on polymethyl methacrylate, designed specifically for FDM/FFF printing. nine0142
Polyethylene terephthalate (PET, PET)
Polyethylene terephthalate - this complex name hides a material used for the production of plastic bottles and other food and medical containers.
The material has a high chemical resistance to acids, alkalis and organic solvents. The physical properties of PET are also impressive with high wear resistance and tolerance to a wide temperature range from -40°C to 75°C. Among other things, the material is easily machined. nine0003
Printing with PET is somewhat problematic due to the relatively high melting point of up to 260°C and significant cooling shrinkage of up to 2%. Using PET as a consumable requires approximately the same conditions as printing with ABS.
Achieving transparency of models requires rapid cooling to pass the glass transition threshold of 70°C - 80°C.
The material has become the focus of attention of 3D craftsmen using used containers as raw materials for home production of 3D printing consumables. Recycling devices such as FilaBot or RecycleBot are used to make threads. nine0142
High impact polystyrene (HIPS)
High impact polystyrene is widely used in industry for the production of various household products, building materials, disposable tableware, toys, medical instruments, etc.
When 3D printed, polystyrene exhibits physical properties very similar to the popular ABS plastic, making it an increasingly popular material among 3D craftsmen. The most attractive feature of polystyrene is the difference from ABS in terms of chemical properties: polystyrene is quite easily amenable to the organic solvent Limonen. Since Limonene has no effect on ABS plastic, it is possible to use polystyrene as a material for building soluble support structures, which is extremely useful when building complex, interlaced models with internal supports. Compared to the convenient, water-soluble polyvinyl alcohol (PVA) plastic, polystyrene compares favorably with relatively low cost and resistance to humid climates that make PVA difficult to work with. nine0003
Be aware that some ABS manufacturers mix slightly cheaper polystyrene into their consumables. Accordingly, models made from such materials can be dissolved in Limonene along with supporting structures.
When polystyrene is heated to extrusion temperature, toxic fumes can be released, so printing in a well-ventilated area is recommended.
Wood simulants (LAYWOO-D3, BambooFill)
LAYWOO-D3 is a recent development for printing wood-like models. The material consists of 40% natural wood chips of microscopic size and 60% binder polymer. The LAYWOO-D3 is very easy to handle, being virtually warp-free and does not require the use of a heated platform. According to the manufacturers, the polymer is non-toxic and completely safe.
The unique material properties allow for different visual results when printing with different nozzle temperatures. The operating temperature range is 180°C-250°C. As the extrusion temperature increases, the shade of the material becomes progressively darker, allowing it to simulate different types of wood or annual rings. nine0003
Finished models are excellent for mechanical processing - grinding, drilling, etc. In addition, the products are easily painted, and unpainted models even have a characteristic woody smell.
Unfortunately, the cost of the material is almost four times higher than the price of popular materials such as PLA and ABS plastics. As popularity is projected to grow, the material should become more accessible.
Alternative materials are currently being developed and tested, such as BambooFill from the Dutch company ColorFabb. nine0142
Sandstone Simulators (Laybrick)
Composite from inventor Kai Parti, responsible for the revolutionary LAYWOO-D3 wood simulant. This time, Kai set his sights on sandstone imitation, using a tried and tested method of mixing a binder with a filler, in this case mineral.
Laybrick allows you to produce objects with different surface textures. At low extrusion temperatures of the order of 165°C-190°C, the finished products have a smooth surface. Increasing the printing temperature makes the material rougher, up to a high degree of resemblance to natural sandstone at extrusion temperatures above 210°C. nine0003
The material is easy to work with no need to heat the work platform, does not show significant deformation when shrinking and does not produce toxic fumes when heated. The only drawback can be considered a rather high cost of the material, which is largely due to limited production.
Metal Simulators (BronzeFill)
Metals have attracted additive manufacturing enthusiasts since the early days of 3D printing technology. Unfortunately, printing with pure metals and alloys causes a lot of difficulties that are insurmountable for most 3D printing methods. Fully functional metal products can only be produced using technologies such as SLS, DLMS or EBM, which require the use of industrial plants that cost hundreds of thousands of dollars. At the same time, metal imitators are successfully used in 3D inkjet printing (3DP), where products are formed from metal powders, the particles of which are held together by an applied binder material.