Reach 3d printer
Reach 3D Printer – Just Add Filament
Looking Back
Reach 3D Printer kit production reached summer’s end some time ago and is now passing into the dead of winter. The Reach 3D Printer began as a Kickstarter back in March 2015, a time when consumer printers were evolving rapidly and the cost of printers seemed to be rising as Makerbot was bought up and left the open source kit market, a market they had pioneered only a few years prior. A simple low cost open source RAMPS based kit that could print, mill, and laser engrave was the Reach vision and unlike most printer Kickstarters of the era, Reach kits were fully delivered to over 500 awesome backers. Some of those backers are just now finding the time to assemble their kits and so we are keeping the documentation alive here at our new project site. A few Reach kits and sub components may still be hanging out on a shelf in Nate’s garage so if you are feeling like a 5 hour build for old time’s sake, feel free to contact us through Just Add Filament with your request. However, as of this writing (Aug 2020) the Ender 3 is one of the best low cost printers that target what was once the Reach market and it is selling for nearly $200 shipped right now. Thank you Reach backers for all your support!
Original Kickstarter Video
Legacy Reach 3D Printer Support Links
Documentation:- Dropbox Folder
- User Manual
- Firmware
- CAD Models
- STL Printable Parts
- Youtube Channel
- Assembly Demonstration
- Setup Overview
- Software Tutorials
- Troubleshooting Tips
- Milling and Laser Demonstration
- Facebook Group
- Replaced Google+ which Google shut down April 2019
- Google Groups Forum
- Initially the place to collaborate but Google+ quickly took over
- Pierre’s BL touch Sensor holder with LED light ring
- Ashaman’s Reach stability enhancing Feet
- Benson Chan’s precision Proximity Mount
- Upgrades and Mods
- Greg Huber compiled a master list that can still be found here
- Thingiverse
- Printer definition is mirrored here with a few mods (e.
g. LCD Screen, frame mounts)
- STL files for printing backup parts
- Printer definition is mirrored here with a few mods (e.
- Kickstarter
- Campaign that started it all
Reach Kit Specs:
Original Kit:- 200 x 200 x 200 mm aluminum build plate
- LCD screen / SD card Reader for stand alone printing
- All Metal Plate construction
- 4x NEMA 17, 4000g.cm stepper motors
- 3 axis V-slot aluminum and Delrin wheels
- Inductive Proximity Sensor for Autoleveling
- Ramps 1.4, Arduino mega, 6A power supply
- Bowden fed, fan cooled, J head hot end
- Able to print multiple materials
- 15A industrial power supply
- MK2B heated bed, 100k thermistor, and original aluminum bed
- Laser cutter and CNC Dremel engraver enabled, with very little modification
- An $80 2.
8 watt laser will cut up to 5 mm plywood.
- A $25 500 mw laser will only engrave images or cut thin material like paper
- Kit does NOT include the laser or Dremel Flex tool, but each modification can be purchased and installed for $20-$25
- Dremel style flex tool can be purchased on Amazon as a “WEN rotary tool with flex shaft”
- YouTube videos show you how to install, and operate the free software needed to operate the laser and CNC engraver/mill
Reasons Why 3D Printing is Reaching Mainstream
Cutting-edge technology developments, evolving value chains and market innovations are pushing 3D printing into the mainstream arena according to the latest exclusive research from Smithers
According to the new Smithers report The Future of Global 3D Printing to 2027 this market is set for explosive growth over the next decade. It will rise from $5.8 billion in 2016 to $55.8 billion by 2027, an aggressive annual growth rate of 23.0%. The 3D printing market is beginning to transition into a maturing business environment and has earnt an important position as a design and prototyping tool, and in the production of complex tooling and moulds.
The market continues to experience substantial success among hobbyists and home users, dominating the number of 3D printers delivered in 2016 (233,000 printers versus 63,000 units in industrial/commercial applications), and in the total number of 3D printers installed. However, the combined value of the industrial/commercial sectors is overwhelmingly larger ($5.4 billion versus $0.4 billion in 2016), due to the much higher cost of industrial/commercial 3D print hardware, higher raw materials costs and larger spending on services.
Evolution of printer and materials technologies
The most common 3D printing raw materials are the commodity thermoplastic polymers:
- Acrylonitrile butadiene styrene (ABS)
- Polylactic acid (PLA)
- Polyethylene terephthalate glycol-modified (PETG).
These materials, made in huge quantities by the global chemicals and plastics industry, are readily available, relatively inexpensive, and easy to handle and process in fused filament fabrication (FFF) 3D printing equipment.
Currently, the most readily available metallic raw materials are aluminium and bronze powders, selected grades of maraging steel and of stainless steels, a few aluminium alloys, cobalt-chromium compounds and a limited number of titanium alloys. Private industry and independent research agencies are investing substantial R&D resources to expand the envelope of metals for 3D printing.
The pace of raw materials development for 3D printing will accelerate dramatically over the coming years. Raw materials for 3D printing will become more uniform and of a higher, more reliable quality. These materials will be generally more accessible and affordable, and improvements in materials formulations and processing techniques will make them more user friendly.
Developing value chainWith the advancing technology and sophistication of the 3D printing marketplace, value chains are evolving to meet the growing and diverging needs of the rapidly developing markets. Currently, most industrial/commercial 3D printing installations function as a stand-alone unit operation, not intimately integrated into the overall manufacturing environment and workflow. For many companies, 3D printing remains something of a lab curiosity, still far from achieving its potential to transform product design and manufacturing processes or, ultimately, the structure of value chains and the marketplace.
Companies with a deep experience of incorporating 3D printing principles into their design and manufacturing workflow – companies like Airbus, Lockheed Martin, and Boeing – are now developing integrated manufacturing systems that seamlessly incorporate 3D printing into the factory environment and workflow.
The industry will likely devise constructive solutions to potential business transformations. While traditional second tier part suppliers and logistics companies may see their business diminish over time, these changes will open up significant opportunities, particularly for contract manufacturing providers.
Leadership in the global 3D printing marketplace will continue to reside in North America and Western Europe. Asian companies will manufacture an increasingly large share of 3D printing machines, especially the low-cost, lower capability machines favoured by the hobbyist/DIY segments, and by casual school and commercial users.
Widespread innovation is expected across the forecast period, both in terms of 3D printing technologies and equipment, and in terms of raw materials and end uses. Widespread adoption of 3D printing processes will enable the dramatic transformation of value chains and supplier–customer relationships.
Many of these innovations will address the natural evolutionary pressures that affect any new technology: increases in production speeds, process efficiency and reliability, reductions in machinery and systems costs, and improvements in product quality and uniformity.
Smithers exlusive research reveals the industry can expect:
- 3D printer and process innovations to focus upon progressive improvements and refinements to existing processes, and less upon radical new technologies
- A broadening of the range of commercially important metals and plastics to be made available in forms suitable as 3D printers
- Companies in the industrial and commercial sectors will increasingly view 3D printing as a toolbox of technologies and production techniques to be commercially exploited and integrated.
These changes in the scope and direction of 3D printing innovation will create substantial opportunities for the industry in terms of 3D printing materials and processes, applications and end user development; and in terms of the value chains and relationships across the 3D printing business environment.
The full impact of these technology changes, innovations and evolving supply chains are analysed in-depth in Smithers report The Future of 3D Printing to 2027.
3D printing process
3DPrintStory     3D printing process
As the nozzle of the FDM printer moves across an open space to get to the next point, it can sometimes ooze molten plastic that...
Read completely nine0008 10692
One of the key programs you will need for 3D printing is a slicer. Although 3D printing was invented three decades ago, desktop 3D printers have become popular...
Read completely 11904
Quite often, 3D printing is used to produce parts that can be easily made using another manufacturing technology. However, although finite... nine0004
Read completely 8995
Hi all. Some time ago I became the owner of a magnetic table. I wanted to try it for a long time, but upon the arrival of the parcel, there was not enough time to install it, and it was too late.
Read completely nine0008 10784
Hi all. In this article, we will consider 3d printing of a model with different infill density in its individual sections. This technique can be very useful...
Read completely 7308
A 3d printer, like any other piece of equipment, needs maintenance. And if you haven’t done it until today, it’s better to start right after reading this ... nine0004
Read completely 6059
Hi all. In this article, I will look at the Cura - Ironing slicer function, which means Smoothing in English. The reasons for the roughness of the top layer With each new ...
Read completely nine0008 10883
Polyethylene terephthalate glycol, aka PETG. Let's talk about this plastic. I resisted printing with this plastic for a long time in favor of PLA and ABS, which generally satisfied all my needs.
Read completely 7768
Hi all. In this article, as part of useful guides for setting up a 3d printer, we will talk about such a basic process as extruder calibration. A lot of people neglect it... nine0004
Read completely 9719
Subscribe to our Telegram channel 3DPrintStory and stay up to date with the most interesting posts and news in the world of 3D printing!
JoysMaker R2 Black - a 3D printer for the inexperienced / Sudo Null IT News I got the Joysmaker R2 Black FDM printer in an acrylic case, I liked it first of all with characteristics comparable to more expensive competitors.
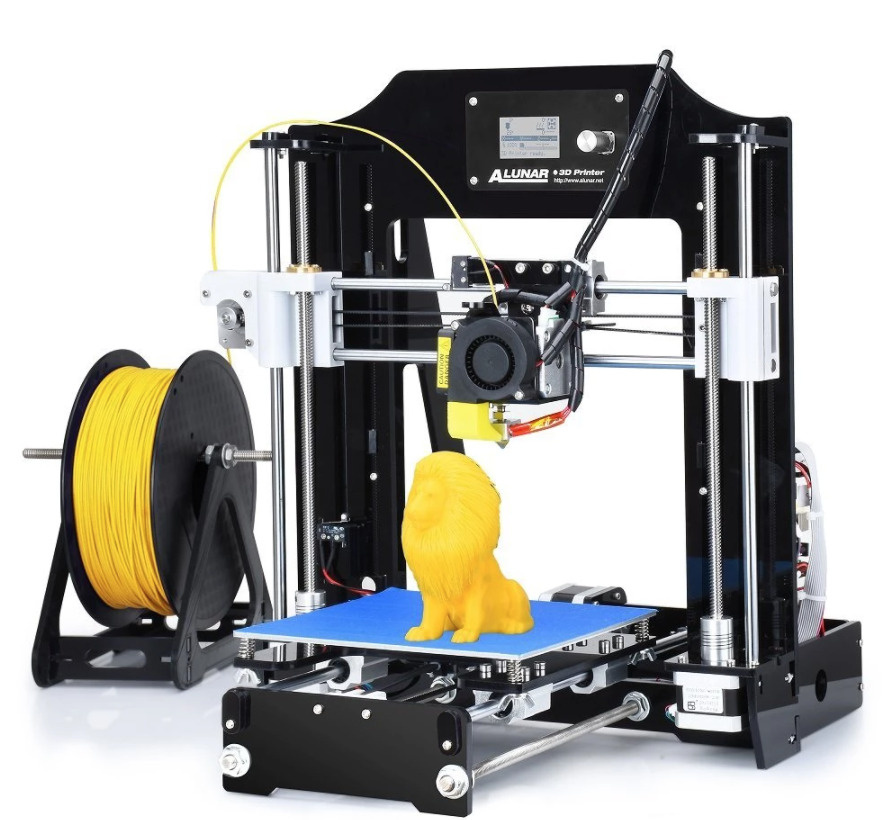
Having calculated the cost of shipping from China and remembering my adventures with customs a couple of years ago, I decided to order it in Moscow in an online store, besides, it was in stock there. I did not order an assembly kit, but immediately took the assembled version, all that remained was to charge the plastic coil and calibrate it.
The first thing I naturally rushed to closely examine this device, I must say that the quality of workmanship exceeded my expectations. The body made of black acrylic no longer looks as handicraft as plywood. There was a booklet with a brief instruction that prompted the happy owner the first steps of communication with a 3D printer. nine0004
I can't say that the printer is heavy, but not light either. In total, its weight is about 13 kg. A couple of photos of the filling itself will help you see the details below:
Dimensions of the printer working area: 21x22x22 cm. It should be noted that the Joysmaker R2 Black model itself has the ability to use both PLA plastic and ABS plastic.
An important indicator when ordering this model is the number of extruders. My model had one extruder, but if you wish, you can order a complete set with two extruders. The thing turned out to be cunning and without the help of the hall calling a friend, I could not put a plastic thread into it and get to the base of the print head, which in turn would heat this very thread.
Briefly describe the process of this operation below.
1. Pull up on the lever, which will allow the lower extruder assembly to be lowered all the way down. nine0051 2. Insert the plastic thread as far as it will go. You should see it already at the other end of the transparent tube and feel the base of the nozzle.
3. Pull up the lower structure of the extruder, returning the white lever to its initial position, finally fixing it with the transverse lever.
A short video of how we did it is attached below.
After preparing the printer, all that remains is to install the software. Joysmaker uses the same software as Ultimaker, namely the Cura program. What can I say, China produces analogues that are not inferior to the original, while maintaining compatibility with the software. nine0004
Finally, with the printer calibrated, we were ready to print. Many ready-made models can be downloaded on the Internet, but it is much more interesting to create a model yourself. For simple models, Trimble SketchUp Pro (Pro, because there is export to obj) is quite suitable. The printer itself willingly “eats” files with the .stl extension and works much faster with them when they are copied to the memory card itself.
Well, we only had to wait 30 seconds, after which the nozzle of the 3D printer heated up to 220 degrees and started the process. A narrowly focused mini-fan is also mounted to the print head of the printer, which prevents the part from melting in the layer of hot air between the heated platform and the extruder. The cooler works very quietly and imperceptibly. It was also quite convenient to track all the processes through the built-in display, which optionally appeared in the R2 models, which allows you to track many parameters. Of the languages, only English is available. nine0004
The accuracy of positioning and the final product that the JoysMaker R2 produces is often lame, however, the correct calibration of the printer decides a lot. For small items, it takes a lot of time, the smallest robot was printed in 11 minutes with a layer thickness of 0.5 mm.
The main characteristics according to the manufacturer for JoysMaker R2 Black are as follows:
Print technology: FDM
Materials used: ABS, PLA
Number of extruders: 1 (installation of 1 more is possible)
Heated platform: yes
Working area: 210x210x220 mm
Print speed: 50-300mm/s
Declared layer thickness: ≥0.05 mm
Claimed accuracy: 0.0125 mm
Part cooling: yes
Nozzle diameter: 0.