Palette 3d print
Multi-material 3D printing at its best – Mosaic Manufacturing
Enabling multi-material 3D printing has been Mosaic’s mission since our early days in 2014. Since then, we’ve sold tens of thousands of Palette units to customers in over 70 countries. Introducing the latest generation of Palette:
Palette 3 + Palette 3 Pro
Design ApproachTwo of the most important aspects that Palette 3 improves on are user experience, and reliability.
Additionally, Palette 3 Pro allows for the printing of up to 8 materials on a single extruder 3D printer. This is double the 4 inputs on every other Palette to date, and more available materials than any other approach on the market.
Simple Multi-Material 3D Printing
Palette 3’s new user interface, and approach to connectivity means that you’re able to get an incredibly simple experience. One of the biggest changes when compared to Palette 2 is the integrated Canvas Hub S. This means that you’re able to connect Palette 3 (Pro) to your printer, and access easier loading, connected calibration, and a simpler printing workflow.
Alongside this, Mosaic has developed our own version of printer control and communication in Canvas, which allows you to send files directly to your Palette 3, with no USB drives or SD cards. Through this interface, you’re able to heat up your printer, start prints, and monitor your print job.
Including Canvas Hub S functionality meant the Mosaic team had more flexibility to add in additional workflows, tutorials, and walkthroughs on Palette itself. This means Palette is better able to guide you through setup and printing.
These three aspects combine to ensure your Palette printing experience will be straightforward and simpler than ever before.
Increased ReliabilityWith product feedback on thousands of Palette 2 units, the Mosaic team was able to isolate the most common failure modes and design Palette 3 to ensure these were no longer present for users.
There were two main wear points that were focused on - splice tubes and limit switches.
Re-Engineered Splicing
Each Palette Splice Core consists of a few main components, one of the important ones being the PTFE tube. This PTFE tube is where the filament is actually spliced, and re-formed to a tight tolerance in order to allow the spliced filament to feed into your 3D printer. These tubes are made through an incredibly precise manufacturing process. Based on our team’s data collection and endurance testing, we found that the typical Palette 2 splice tube would wear out between 5,000 and 10,000 splices.
This wear is very dependent on the quality of the filament used, which leads to the range seen above. Increasing the average time for a splice tube to wear is one of the primary reasons we launched Mosaic PLA last year. With tolerances of +/- .02mm, Mosaic PLA guarantees a higher average life of your PTFE tube, especially when compared to +/- .05mm filaments.
Palette 3 was designed to splice in a different way, and due to the Palette Engineering teams’ ability to modify hardware and splicing algorithms - Palette 3 splice tubes average life now ranges from 10,000 splices, up to 25,000 splices.
What that means for you is that you’ll experience a more reliable printing experience.
Filament Sensor Re-Design
One of the requirements of Palette is that it understands where filament is in the system at any given time. In order to accomplish this, Palette has a number of ‘filament sensors’ inside in order to understand if filament is present in that area of Palette (or not present).
The filament sensors on Palette 2 used an off the shelf mechanical switch that was directly in contact with the filament. Sometimes the filament would apply excessive load to the switches requiring them to be replaced leading to a less than optimal user experience.
When working through the initial designs of Palette 3, the Palette engineering team knew that these switches needed to be redesigned and optimized for longer term operation. The team took an entirely new approach to switch design, and the results came in illustrating a new lifetime of over 2,000,000 splices. The new switch features a hardened steel, bi-directiional spring loaded switch tab that activates an optical sensor when the filament displaces the tab. The filament no longer engages with the switch allowing for drastic performance and durability improvements. These switches were run for millions of cycles without fail, and have gone from one of the weaker links in the Palette system to one of the strongest.
Pushing the boundaries of 3D printing
CamDrive Design and 8 Material 3D Printing
One of the biggest challenges Mosaic’s engineering team faced was how to scale the number of materials Palette could print, without scaling the size and cost of the product accordingly. The Palette Engineering team came up with a cam system that would still allow for 4 inputs on Palette 3 while also enabling up to 8 inputs for Palette 3 Pro.
Building on the backbones of Mosaic’s patent pending sliding selection drive system from a 2014 application, this new rotary CAM system embodies the key benefits of 2 motors to drive any number of filament. Unlike other simpler rotary feeder systems on the market, Palette 3’s CAM is a first of it’s kind workhorse with unrivaled drive strength and consistency between all inputs.
Cam system works with one motor ‘selecting’ which material is to be driven via rotating a cylinder with a number of idler bearings. Depending on the position of the cam, a certain input’s idler bearing will be opposite the drive gear. This idler bearing pushes the filament into the gear, and the filament is driven when the gear rotates. The other 3 (or 7) materials are not pressed up against the gear so these materials do not move forward when the drive gear rotates.
Cam systems have an incredible amount of nuance to them and must be designed, tested and manufactured in a specific way in order to operate reliably. The cam system in Palette 3 has gone through torture testing of over 100,000 material changes.
Designed with a combination of metal and solid polymer components, the system is strong and rigid enough to last through the most rigorous printing processes.
Constrained Buffer System
The Palette engineering team re-imagined the buffer system inside Palette 3 in order to allow for higher print speeds, and a more constrained material path. This updated buffer system has the material staying inside of a PTFEtube, constraining the material through the buffer.
Unlike Palette 2, The lower limit buffer switch has been moved out to allow for additional movement once this switch has been triggered. In the past, if this switch was triggered it meant that there was no buffer remaining, and if the printer was pulling filament, this could lead to skips in extrusion and small gaps in your part.
With the lower limit switch moved out, there is an additional buffer below this switch, which means Palette 3 will have more time to move filament out into the buffer and continue feeding material to your printer. We also added a buffer maximum switch to further optimize buffer performance.
The constrained buffer system allows for easier automated loading and system clearing.
Additional Cooling Systems
Airflow and cooling is an understated aspect of the Palette system that most operators don’t think about. Cooling splices, and ventilating the electronics systems are incredibly important to reliable operation over longer periods of time.
With the help of some new thermal imaging equipment, we were able to collect data over tens of thousands of splices and use this data to ensure efficient cooling and airflow when Palette 3 is being run over extended periods of time.
3D Printing, Evolved.Palette 3 and Palette 3 Pro are the simplest, most reliable way to achieve multi-material 3D printing on your 3D printer. This generation of Palette is the culmination of 7 years of expertise in multi-material 3D printing, all created to allow you to get the most flexibility out of your machine.
Palette 3 and Palette 3 Pro will begin arriving as early as July 2021, check out the Palette 3 and Palette 3 Pro product page here.
Simple multi-material 3D printing Palette 3 Pro by Mosaic
Item #: 90117
850226000847Mosaic
List Price $899.00
Super Buy Price! $799.00
Quantity discounts available
List Price $899.00
Super Buy Price! $799.00
Item (2)
IncomeAccount
TaxCode Mapping
UPC Code
Pick Up
Tax Amount
- Details
Mosaics Palette 3 Pro works with your printer to provide a seamless multi-material printing experience with up to 8 inputs and built-in Canvas Hub functionality connecting to your printer has never been easier. Manufacturer Warranty: 24 months or 50,000 splices. Check out the full printer Compatibility List to see which 3D printers Palette 3 Pro is compatible with.
See MoreSee Less
Transform your 3D printing experience with our best 3D printing solution yet!
With a simple plug-and-play setup, Palette 3 enables your printer to print multiple colors in one print, combine flexible and rigid materials together, and achieve high quality complex prints with soluble supports.
- Communicate your ideas and bring your prints to life with Palette 3’s 8 color printing capabilities
- Unlock multi-material printing by combining flexible and rigid materials
- Experience Palette’s 3rd generation splice core for fast and reliable splicing
- Automated filament management system allows you to run your longer prints without interruption
- Custom designed brand new switch mechanism to make sure it performs for a long period of time
- Integrated Canvas Hub to streamline communication between all your devices for an easier user experience
- Manage all prints on the cloud with our seamless software integration of Canvas
Accessories included:
- Power Supply
- Stand
- Extruder Clip
- Filament Holder (for 8 spools)
- USB Drive (8GB)
- USB-A to UBS-B Cable
- UBS-A to USB-Micro Cable
- Screwdriver
- Outgoing Tubes (2 small, 1 medium, 1 long)
- Spare Splice Core Tubes (4x)
Filament Compatibility: 1. 75 ±0.03mm PLA, PETG, TPU, ABS, PVA, HIPS Shore hardness of 95A or harder
- 1. Inputs - Palette 3 Pro comes with 8 inputs to provide you with flexibility to use 8 different colours and/or materials for your prints.
- 2. Drives - Palette 3 Pro’s all-metal drive systems, inspired by those on industrial FDM machines, accurately control filament to ensure the right lengths are driven from each input.
- 3. Cut - A rotary cutter system slices filament to ensure a clean, low-resistance cut, time after time
- 4. Splice Core - Palette 3 Pro’s updated and optimized Splice Core splices filaments together in an improved and efficient manner, with an additional fan to cool down the filament as it exits the splice core, speeding up the process drastically.
- 5. Limit Switches - Newly designed limit switches made of hardened steel monitor filament throughout the device.
- 6. Enclosed Buffer - The newly spliced filament is passed to the updated, enclosed buffer system to cool and ensure that it keeps tight dimensions before being passed to your printer.
- 7. Screen - Higher resolution screen, with increased controls and settings allows you to customize your prints directly from the Palette 3 Pro screen.
Note: This item ships direct from Canada.
Customer Reviews of This Item
No reviews available
Be the first to Write a Review
3DNews Technologies and IT market. News at the cutting edge of science Stratasys has updated the bending color palette... The most interesting in the reviews 06/13/2014 [10:38], Dmitry Prikhodko Stratasys, the largest manufacturer of 3D printing devices, has announced the release of a new consumable kit for its Objet500 Connex3 Color Multi-material printers. And although full color 3D printing in the direct sense of this meaning is still inaccessible due to the limitation on the number of colors used, thanks to the new palette set, the quality of printed multi-colored models will be taken to a whole new level. The first “consumable” presented was a material that was quite rigid in its physical properties and is intended for creating plastic toys, small copies of various designs, parts and layouts. The second type of material from the point of view of practical application seems to be much more interesting. They have become more elastic material in various colors. It can be used when printing flexible products, the full-fledged prototype for which, if such exists in nature, is made of rubber or a similar material. news.softpedia.com Six new sets of elastic consumables further expand the color gamut by more than 200 shades with different gradations. Three sets of palettes with 72 colors were obtained by mixing the flexible rubber-like "consumables" of the TangoPlus series and combined materials such as VeroYellow, VeroCyan, VeroMagenta and the like. The next three kits, totaling 68 different colors, were obtained by Stratasys by combining a soft black material, marketed as TangoBlackPlus, along with multi-coloured Vero standard hard plastic consumables. Another additional palette of 45 colors was the result of adjusting the transparency of the existing shades. Also the gray color was not left without attention, which was replenished with a palette that combines 135 color solutions for hard material. This number of shades of gray was achieved by combining and supplementing VeroWhite and VeroBlack solid consumables with new color components to achieve different gray levels. The Objet500 Connex3 3D printer from Stratasys remains the only 3D printer of this size that can combine both color printing technology and simultaneous printing using different materials in a single form factor. All this makes it possible to combine rigid, flexible, transparent and opaque parts of any shape and color in one manufactured object, creating bright high-quality objects with an individual design. Source: If you notice an error, select it with the mouse and press CTRL+ENTER. Related materials Permanent URL: https://3dnews.ru/821900 Headings: News Hardware, cutting edge science, 3D technology, Tags: 3d printer, 3d printing, 3d technology, stratasys, printing, color, materials, hardware ← В past To the future → |
3D printing FLEX plastic in Sprint 3D
FLEX (Flexible PolyEster) – is a plastic used for 3D printing complex shapes containing flexible elements. The material is rubber-like, so you can easily print a flexible part or a separate component for the finished product. The emergence of flexible elements in 3D printing is a new step in its development, opening up even more possibilities. 3D printing FLEX with plastic in Sprint 3D means high quality with fast order execution.
FLEX plastic for 3D printer allows you to create rubber parts for machinery and equipment, soft toys, plastic shoes and much more. High elasticity, resistance to tearing, resistance to moisture and other negative factors - all this makes FLEX simply indispensable in modern 3D printing.
Material specifications
Among the main features we highlight the following:
- High melting point. The table heats up from 80 to 110 degrees, and the nozzle - from 220 to 240 degrees Celsius.
- Resistant to mechanical stress and even to rather aggressive solvents.
- No reaction with any of the essential oils.
- Large selection of material colors.
- Relatively difficult machining.
3D printing FLEX plastic allows you to create complex three-dimensional models, the individual elements of which are connected using a soldering gun or synthetic rubbers. The sophisticated FLEX print of allows the production of prosthetics, military models and other items where maximum wear resistance is required.
The nature of FLEX plastic for 3D printer is quite similar to PLA plastic, also being a product of natural origin. The main production material is corn. This not only ensures safety and environmental friendliness, but also guarantees complete biodegradability. Unlike a number of other plastics, the use of FLEX is more efficient and safer.
3D printing FLEX plastic in SPRINT 3D
3D 3D-printing on its own industrial 3D printers
The largest working area is 500x500x800 mm 9000
Delivery throughout Russia and CIS countries
If the product does not meet the technical specifications, we return the money
3D printing FLEX - basic rules
Flexible plastics are specific materials that require a clear understanding of how to work with them.
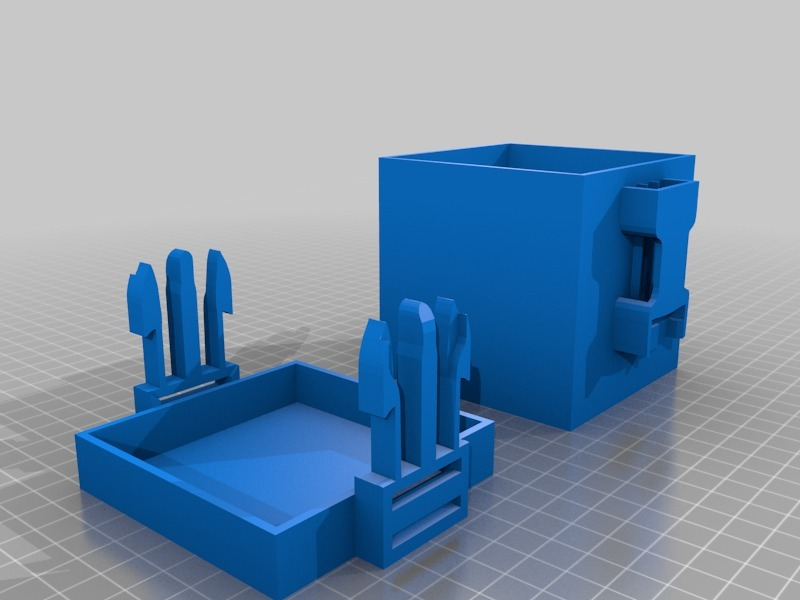
1. Do not put pressure on the filament from above so that it does not bend inside the extruder.
2. Printing should be carried out at low speeds - up to 40 mm. Otherwise, the filament may sometimes bend and slip between the extruder wheel and the presser mechanism.
3. There must be no space between the thermal barrier and the extruder wheel. If there is one, the thread can also bend, as a result of which it will fill the voids.
We at SPRINT3D have been printing using flexible materials for several years now and create unique products of any complexity, shape and purpose. If you are interested in production using flexible plastic FLEX, , please contact us at any time.
5 reasons why FLEX 3D printing is better than analogues
The properties of
FLEX plastic for 3D printer can be compared with other materials: Elastan, Elastan D and Plastan.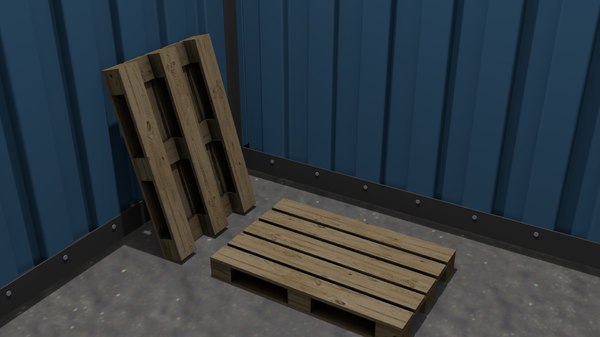
1. It is the most flexible plastic of all.
2. By its properties, it resembles rubber to the maximum, which opens up wide opportunities for the production of original products.
3. The strength and heat resistance is an order of magnitude higher.
4. Better elasticity than the materials in question.
5. Neat appearance of end products due to material properties.
Of course, there are some difficulties with this flexible plastic. Due to its high flexibility, it can be more difficult to load into the printer, parts are sometimes blown off the platform, etc. And this once again confirms that this work should be done by experienced specialists. Otherwise, there is a risk not only to transfer expensive material in vain, but also to damage the printer itself, which will result in expensive repairs.
FLEX print. Process
Loading material into a 3D printer is almost always done manually. Automatic loading is practiced only under the condition of a low thread feed speed. But even in such cases, to guarantee the result, we prefer to load the material manually. New generation clamping mechanisms are used, which greatly simplifies the work and guarantees the absence of defects. Old-style clamping mechanisms are simply not adapted to work with such soft materials.
Use settings close to those for PLA plastics. The differences are small: the temperature of the platform is 80 degrees, the increase in the “Border” parameter and the use of a table substrate, which can be a special glue or ordinary blue tape. We keep the printing speed within 20-40 mm per second, which guarantees the highest printing accuracy and the absence of defects.
Wide color gamut for original results
Like most 3D printing consumables, FLEX is available in a wide range of colors. Including there is a transparent version with good light transmission.