3D printed limb
Scientists create fully-automated 3D printed prosthetic production line
0Shares
Scientists from the Israel Institute of Technology have developed an automated production line for 3D printing low-cost customized prosthetic limbs.
Within the team’s streamlined design process, amputees’ unaffected hands are scanned, tailored using CAD software and converted straight into an STL file ready to print. The resulting parts can then easily be assembled into lifelike extremities with advanced object-gripping capabilities, that provide patients with an enhanced quality of life, at the click of a single button.
The scientists’ custom scanning setup (pictured) cost them less than $40. Image via the Israel Institute of Technology.Advancing accessible prosthetics
Losing a hand can drastically affect someone’s quality of life by increasing their level of dependency on others, but prosthetics can cost anywhere from $3,000 – $100,000. As a result, many amputees are priced out of customized devices, especially given that they often require an expensive manual fitting from trained specialists to achieve optimal performance.
Cost aside, prosthetics also suffer from several other issues that lead to sky-high rejection rates, including their appearance, weight, grasping force and lack of sensory feedback. Such patient rejection can also have serious consequences, causing joint and muscle degeneration, painful inflammation and a myriad of other potentially serious complications.
Using 3D printing, meanwhile, it’s now possible to reduce the number of assembly steps required to build prosthetics while creating more intricate designs, and a number of recent projects have done so successfully. However, developing low-cost artificial limbs with consistent properties and at a rapid enough pace to meet demand, has continued to remain problematic.
In an attempt to ramp up production and reduce reliance on trained specialists, the Israeli scientists have therefore developed a digital design pipeline, in which affordable prosthetics can be churned out with minimal manual intervention.
The team’s 3D printed hands feature embedded force sensors (pictured) to give them sensing functionalities.
Creating an artificial limb factory
The researchers’ production line essentially consists of four steps: scanning, modelling, 3D printing and assembly. During the initial design phases, the artificial limb’s appearance can be tailored to match user preferences, and patients can pick between body-powered hands and more advanced EMG-controlled devices.
Once the prosthetic has been perfected, it’s automatically converted into an STL file and sent for printing. Although the scientists’ workflow still requires the resulting parts to be assembled manually, they found that previous steps can be optimized to shorten the process, making construction simple, quick and accessible for users.
To make their setup as attainable as possible, the Israeli team even created a low-cost custom scanner based on an Intel RealSense camera, which came to around $40. The resulting prosthetics weren’t found to be low-quality either, as they proved capable of pouring liquids and holding household items for over 50,000 cycles.
In other tests, the additive extremities demonstrated the ability to adapt their level of grip to either ultra-soft or rigid objects, with their motors stopping at different times depending on levels of resistance. While the prosthetics haven’t yet been rolled-out to prospective users, when shown to amputees, they’ve complimented the devices’ weight and realistic appearance, suggesting that patient rejection is likely to be minimized.
Ultimately, the scientists concluded that by removing the necessity for an expensive manual fitting, their 3D printing production line could dramatically reduce the cost of artificial limbs for those in need. Although the team didn’t put an overall price on their production pipeline, they concluded that the overall concept could “provide a much-needed leap in the field.”
Optimized prosthetic production
While it has been possible to 3D print prosthetics for several years, the industry’s focus has recently shifted towards making them more accessible to amputees.
Prosthetics manufacturer Partial Hand Solutions, for instance, has adopted Formlabs’ new Form 1 3D printer within its production process, enabling it to create 80 artificial fingers per day. Using the machine has also allowed the company to fabricate limbs that are both cheaper and better tailored to patient needs.
Similarly, researchers from the University of Lincoln have developed a 3D printed sensor-operated prosthetic arm that’s specifically designed for use by two-year-olds. Given that many children don’t get additive limbs due to their continuous growth, the device has been built as a more accessible affordable alternative.
Elsewhere, customized prosthetics have been developed to address the needs of patients with various other injuries, and scientists have even gone to the trouble of 3D printing testicles. Korean men reportedly have to pay over $715 for artificial gonads, and the additive balls are designed to provide a low-cost substitute.
The researchers’ findings are detailed in their paper titled “Scan-Driven Fully-Automated Pipeline for Personalized, 3D Printed Low-Cost Prosthetic Hand. ” The study was co-authored by Yair Herbst, Shunit Polinsky, Anath Fischer, Yoav Medan, Ronit Schneor, Joshua Kahn and Alon Wolf.
To stay up to date with the latest 3D printing news, don’t forget to subscribe to the 3D Printing Industry newsletter or follow us on Twitter or liking our page on Facebook.
Are you looking for a job in the additive manufacturing industry? Visit 3D Printing Jobs for a selection of roles in the industry.
Featured image shows a schematic of one of the researchers’ 3D printed prosthetic hands. Image via the Israel Institute of Technology.
Tags Formlabs Intel Israel Institute of Technology Partial Hand Solutions University of Lincoln
Paul Hanaphy
Paul is a history and journalism graduate with a passion for finding the latest scoop in technology news.
3D-printed prosthetic limbs: the next revolution in medicine | 3D printing
John Nhial was barely a teenager when he was grabbed by a Sudanese guerrilla army and forced to become a child soldier. He spent four years fighting, blasting away on guns almost too heavy to hold, until one day the inevitable happened: he was seriously injured, treading on a landmine while he was on morning patrol.
“I stepped on it and it exploded,” he recalled. “It threw me up and down again – and then I tried to look for my leg and found that there was no foot.”
His comrades carried him back to base camp, but there was hardly any medical care available. It took 25 days before he received proper treatment, during which time he developed tetanus down one side of his body. Finally, Nhial (not his real name) was put on a flight to the Kenyan border, his life only saved when he was handed over to a Red Cross team.
Now, a decade later, he lives in a Juba refugee camp, having suffered further troubles in the conflict that has engulfed the struggling new nation of South Sudan. He plays wheelchair basketball for his country, although he relies on a prosthetic lower leg to struggle around the muddy, sprawling camp. Reaching the most basic services often entails long walks and it can be difficult to get to training. But at least his hands are free to carry things such as food and water, unlike those on crutches.
Such stories of lives devastated by conflict or disease are all too common in developing countries. Lack of an arm or leg can be tough anywhere, but for people in poorer parts of the world it is especially challenging. Some are victims of conflict, while others may have been born with congenital conditions. Many more are injured on roads, with the casualty toll soaring in poorer nations. In Kenya, half the patients on surgical wards have road injuries. The World Health Organization estimates there are about 30 million people like Nhial who require prosthetic limbs, braces or other mobility devices, yet less than 20% have them.
Prosthetics can involve a lot of work and expertise to produce and fit and the WHO says there is currently a shortage of 40,000 trained prosthetists in poorer countries. There is also the time and financial cost to patients, who may have to travel long distances for treatment that can take five days – to assess their need, produce a prosthesis and fit it to the residual limb. The result is that braces and artificial limbs are among the most desperately needed medical devices. However, technology may be hurtling to the rescue – in the shape of 3D printing.
Slowly but surely, 3D printing, also known as additive manufacturing, has been revolutionising aspects of medicine since the start of the century, just as it has had an impact on so many other industries, from cars to clothing. Perhaps this is not surprising, given that its key benefit is to enable the rapid and cost-efficient creation of bespoke products. There are few commercial products that need to suit a wider variety of shapes and sizes than medical devices made for human beings.
Experts have developed 3D-printed skin for burn victims, airway splints for infants, facial reconstruction parts for cancer patients, orthopaedic implants for pensioners. The fast-developing technology has churned out more than 60m customised hearing-aid shells and ear moulds, while it is daily producing thousands of dental crowns and bridges from digital scans of teeth, replacing the traditional wax modelling methods used for centuries.
Jaw surgery and knee replacement operations are also routinely carried out using surgical guides printed on the machines. So it is no surprise that the technology has begun to stir interest in the field of prosthetics, even if sometimes by accident. Ivan Owen is an American artist who likes to make “weird, nerdy gadgets” for use in puppetry and budget horror movies. In 2011, he created a simple metal mechanical hand for a steampunk convention, the spiky fingers operated by loops pulled through his own.
He posted a video that was seen by a carpenter in South Africa who had just lost four fingers in a circular-saw accident. They began discussing plans for a prototype prosthetic hand and that came to the attention of the mother of a five-year-old boy, called Liam, who had been born without fingers on his right hand.
She wanted a tiny version of their hand, but Owen realised the child would rapidly grow out of anything they made, so he looked at the idea of using 3D printing. “If we could develop a design that was printable, it would be possible to rescale and reprint the design as Liam grew, essentially making it possible for his device to grow with him,” he said.
So the artist persuaded a printer manufacturer to donate two machines and developed what has been claimed to be the first 3D-printed mechanical hand. Crucially, rather than patent this work, Owen published the files as open source for anybody to access, allowing others to collaborate on, use and improve the designs.
This has grown into Enabling the Future, a network with 7,000 members in dozens of countries and access to 2,000 printers, who help make arms and hands for those in need. One school student in California even printed a new hand for a local teacher.
Often they are aimed at children, since many dislike the weight, look and hassle of modern prosthetics, which can involve inserting the arm into a silicone sleeve and using straps across the back to hold the device in place.
These body-powered hands cost thousands of pounds, yet must be replaced every couple of years as a child grows. The 3D-printed versions cost about £40, come in any colour and look like a cheery toy, so are often more appealing despite being less sophisticated.
Jorge Zuniga, a research scientist in the biomechanics research department at the University of Nebraska in Omaha, heard about this project on his car radio. He was only half-listening, but on arriving home he started playing baseball with his four-year-old son and observed how important the grabbing of an object was to his child’s development.
A Cyborg Beast prosthetic hand.He spent the next month carefully building a prosthetic model that mimicked the human hand, only for his work to be dismissed instantly by his son. “He told me children wanted a hand that looked like a robot.”
From this conversation and the open-source designs emerged Cyborg Beast, a project heavily backed by Zuniga’s department to develop futuristic-looking, low-cost prosthetic hands. “You can do anything with 3D printing,” said Zuniga, who now leads a seven-strong team. “We believe it will revolutionise the prosthetics field. It will lower the costs worldwide and gives engineers, patients and doctors the chance to modify prosthetic hands as they want. And they can be any colour.”
When I told Zuniga, slightly hesitantly, that his design looked like a toy, he was delighted. “That’s great – we want children to see it as a toy,” he said. “This is a transitional device. Many children do not like prosthetics, however good they are these days, because they might have a hook for a hand and they need help to put the harness on, which children dislike. So this is to bridge the gap, helping them get used to the idea as they grow up.”
“We have even had a child missing a shoulder. So we developed a device that weighs the same as the missing arm. This meant he not only got a new arm that helped daily life but it also improved his posture and balance, therefore was much better for his spine. This sort of thing can be done much easier with 3D technology.”
It is remarkable that people who do not even own a printer can obtain a functional child’s hand for the price of a theatre ticket within 24 hours. Zuniga says at least 500 Cyborg Beasts are in use worldwide and the design has been downloaded more than 48,000 times. He has taken it to his native Chile, where he runs a paediatric orthopaedic 3D-printing laboratory, and has had recent requests for the plans from Nigeria.
“My concern at this stage is that some of the materials can melt in higher temperatures. It is not working well there yet, but this sort of prosthetic has huge potential to be used with better materials in the developing world. We are still in the infancy stage at this moment.”
Another scheme experimenting with this technology is Project Daniel in the Nuba mountains of Sudan, where in the middle of the ongoing civil war an American physician, Tom Catena, has been working as the only permanent doctor for half-a-million people around his Mother of Mercy hospital. Fuelled by his religious faith, for almost a decade this brave medic has ignored bombings, a lack of electricity and water shortages to do everything from delivering babies to amputating limbs.
“It’s demoralising for us to amputate an arm knowing that there is no good solution,” Catena told me by email. “We have many arm amputees – both above and below the elbow as a result of the war here and general lack of medical care. This in an agricultural society, where nearly everyone is a subsistence farmer. If one is missing an arm, he is not very functional in this society.They become totally dependent on the family and have a difficult time getting married [which is also very important in this society].”
The idea of using 3D printing to help arose when Mick Ebeling, an American film producer and philanthropist, learned about the Mother of Mercy hospital at the same time as he was hearing about the emerging work on low-cost prosthetic hands. Searching for information on Catena, Ebeling read about one of his patients: Daniel Omar, a 12-year-old boy who had wrapped his arms around a tree to protect himself during an aerial attack. His face and body were protected when a bomb exploded nearby, but both the boy’s arms were blown off.
You can’t just smash in these new technologies, but if we get this right the growth could be exponentialMatt Ratto, Nia Technologies
Ebeling travelled out to the Nuba mountains with 3D printers and, working with hospital staff, fitted about a dozen people with new arms. “Unfortunately, as time went on, none of the amputees was using the prostheses as they felt they were too cumbersome,” said Catena. The doctor concluded: “The 3D model was good, fairly easy to make and inexpensive… although it hasn’t worked out so well here. Perhaps with some tweaking, the 3D printers can be of great use for arm amputees.”
Yet for all the agonies and difficulties associated with arm loss, the bigger problem in poorer countries is when lower limb disability leads to a loss of mobility. Wheelchairs are expensive and can be difficult to use when roads are potholed, streets are muddy and pavements are nonexistent. Without a prosthetic limb, people struggle to fetch water, prepare food and, above all, to work. This throws them back on their families and communities, intensifying any hardship and poverty.
One group that has spent almost three decades trying to tackle these issues is Exceed, a British charity set up by diplomats and academics at the request of Cambodia’s government to help thousands of landmine survivors. It works in five Asian countries, training people at schools of prosthetics and orthotics. In Cambodia, there are almost 9,000 landmine survivors in need of artificial limbs, although these days traffic accidents are a more likely cause of disability, while children also need braces for a range of common conditions such as spina bifida, cerebral palsy and polio.
“If you wear a prosthesis, you are disabled for about 10 minutes in the morning while you have a shower, then you put your leg on and go to work. If you do not have one, then your hands are out of use with crutches so you can’t even take drinks to the table,” said Carson Harte, a prosthetist and the chief executive of Exceed. “Without a prosthesis, there are no expectations. You just go back and rely on the goodwill of your family.”
It is not really a lack of money that denies people these devices, since simplified forms cost little and generic Chinese models are improving fast. The components can cost just £30. The big hurdle is the lack of trained technicians to fit the artificial limbs. In the Philippines, there are estimated to be 2 million people needing prosthetics or orthotics. However, there are only nine fully trained experts, each able to treat 400 patients a year, at most, although more are being trained on a new four-year course.
Orthopaedic technician Moses Kaweesa assembles a 3D-printed artificial leg at CoRSU hospital in Uganda. Photograph: Isaac Kasamani/AFP/Getty ImagesTraditionally, a prosthetist would wrap a stump with plaster of Paris bandages to make a reverse mould and let it dry, then fill it with more plaster that must harden. From this, a socket can be forged that fits, with more modifications for precision, to the bone on the stump. Great care must be taken to avoid nerves and tender areas that are not tolerant of pressure.
The key for the technician is to understand the pathology of a stump, which differs for each person. This is a cumbersome process that can take a week, especially with physical therapy for new patients that lasts three days. It can also be messy work, mixing up and moulding the plaster, while a prosthetist visiting a rural area must transport 20-kilo packs of plaster. With a 3D scanner, a digital image can be made in half an hour and sent by email.
Exceed has begun a seven-month trial of 3D-printed devices in Cambodia with Nia Technologies, an innovative Canadian not-for-profit organisation. “This technology has the potential to increase the productivity of every technician,” said Harte. “It is not about printing off legs, nor does it replace the skills of a well-trained professional, but it has potential to produce a better, faster, more easily repeatable way of doing one key part of the chain. There are no magic bullets, but this may be an important incremental change.”
Nia is also trialling its 3D PrintAbility technology in Tanzania and Uganda, where there are only 12 prosthetists to serve a population of about 40 million people; at the time of writing, all six state clinics have run out of materials. Doctors there often deal with children who have lost limbs after falling into open cooking fires, while other youngsters need braces after suffering post-injection paralysis caused by badly administered jabs that damage nerves.
In Uganda, its team is working with CoRSU hospital in Kisubi, a specialist rehabilitation centre for children with disabilities. Orthopaedic technician Moses Kaweesa said they found the technology lighter and faster to use, as well as easier for people in remote rural areas. “It used to take five days to have a limb manufactured, with lots of hanging around for the patient. Now, it is barely two days, so they spend much less time in the hospital. There is also less waste of material, so for a country like ours this can help so much by cutting down the costs.”
The first person to test out a 3D-printed mobility device at the hospital was a four-year-old girl who until then had dragged herself across floors and had to be carried around by her family. “When she was born, her right leg was missing the foot,” said her older brother. “It was very difficult for her to walk, to play with other children. She can be lonely. But when she was given a leg she was able to run with others, play with others.”
Matt Ratto, Nia’s chief science officer, who led the project’s development, admitted that it was only when he saw the serious-looking child in her red dress start to walk that he realised his technology actually worked. But, like Harte, he urges caution. “We are surrounded by the hype of 3D printing with crazy, ridiculous claims being made,” he said. “We must be cautious. A lot of these technologies fail not for engineering reasons but because they are not designed for the developing world. You can’t just smash in these new technologies.”
Ratto’s aim is to use the technology to fit 8,000 people with 3D-printed mobility devices within five years, across some 20 sites in poorer countries. “If we get this right the growth could be exponential. If we iron out the kinks, and work out the best way to help clinicians, I think we will see something of a hockey stick curve on the graph. But we must not get it wrong, move too fast nor over-hype the potential.”
This article first appeared on Mosaic and is republished here under a Creative Commons licence
A 3D printed leg costs $100. The prosthesis is always individual, it must take into account the personal characteristics and needs of the consumer, be durable, serving the owner for a number of years, and at the same time relatively light and comfortable. All these requirements are not easy to meet, and the manufacture of a prosthesis is delayed for weeks, or even months, and is quite expensive even in the developed countries of the world.
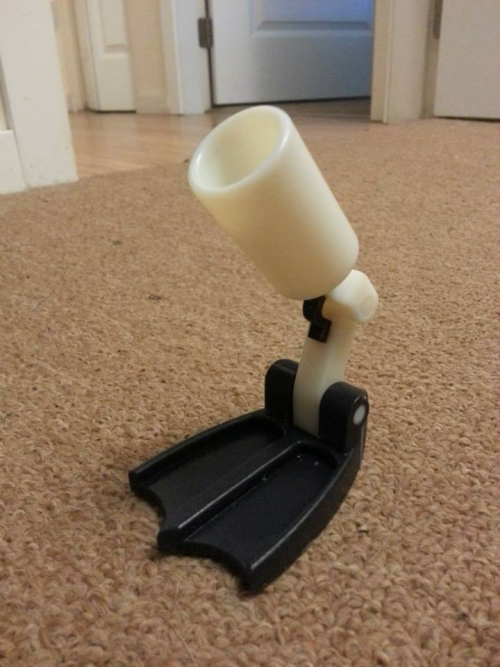
The situation is more complicated for children: firstly, they grow up, and secondly, they break things more often than adults, which means that dentures have to be replaced regularly, and this becomes a difficult financial burden for the family or insurance authorities if the replacement of the denture is covered insurance.
Apparently, the future is not far away when many of these difficulties will be left behind.
Bioengineers from the Japanese company SHC Design have developed a system for 3D printing medical leg prostheses at home. One of the first patients to receive such a prosthesis was 41-year-old Fuminori Ando, who lost his leg below the knee shortly after birth.
Photo courtesy of wsj.com
He received an artificial leg made of soft and light polymer material, outwardly almost exactly copying the real one, reproducing the natural curve of the heel, and even the distance between the toes. This is important for Ando: he has long dreamed of wearing sandals to match his Japanese-style summer suit.
And one more important advantage: now a man can go to the pool and swim with a beautiful and comfortable artificial leg.
Once he gave up swimming because of the weight and unaesthetic appearance of the old prosthesis.
A high-quality, custom-made prosthesis costs about $4,200 in Japan. SHC Design senior Yutaka Tokushima predicts the price of a new prosthesis printed on their company's 3D printer to be around $100.
Photo courtesy of wsj.com
This was made possible not only by their development, but also by the creation of a new material - elastic polymer - rubber manufacturer JSR, who joined forces with SHC Design.
So, first, the patient's healthy leg is scanned, then, using a computer program, a template of a symmetrical prosthesis is created that takes into account the parameters of the shoe at the request of the patient, the feeder supplies the material for printing, and after a while, a soft but strong prosthesis is ready. Its low cost will allow the patient to have several spare prostheses for different shoes and different activities.
However, SHC Design is not only going to meet the needs of patients who care about greater comfort and aesthetics. In a poor country like the Philippines, where their 3D printer is currently being tested, nearly 350,000 people need a prosthetic leg and 90% cannot get it because of the high price and lack of specialists.
“I would like to deliver my product to those who are really in need,” says SHC Design CEO Tsuneo Masuda, who founded the company after 26 years of medical device manufacturing experience. The company received subsidies from the Japanese government to develop a system for printing prostheses.
Senior developer Yutaka Tokushima believes that the company will start selling its 3D printers bundled with software in Japan and the Philippines as early as April next year. They will cost $ 2,000, but the scanner will need to be purchased separately from another provider.
Major prosthesis manufacturers are also interested in 3D printing. Its elements are used by the German company Ottobock, which prints coatings for prostheses that make it possible to hide its mechanical parts from the eye. The Icelandic company Ossur uses 3D printing to create prototypes and some parts of the microprocessor-controlled knee.
Photo from dailycaller.com
The use of a 3D printer is productive not only for printing lower extremities. The Massachusetts Institute of Technology has developed a computer-aided design for a prosthetic hand that can be printed for as little as $50 for the Enable Foundation.
Bioengineers predict the rapid development of prosthetics using 3D printing. Over time, printing artificial limbs will become as commonplace as printing a document today.
Even a child can print a hand for special needs, such as an extendable one, to effortlessly reach the floor and pick up a dropped object.
The development of new technologies for scanning and modeling body parts, created by companies such as Body Labs (New York), is of great importance in this matter.
And when 3D printing combines with propulsion systems, integrated sensors and sophisticated algorithms to easily control the prosthesis, artificial limbs will look little different from real ones.
Resources :
3-D Printing Startup Seeks Niche in Low-Cost Prosthetic Legs
The future of 3D-printed prosthetics
Can the end product (device) be 3D printed?
This year, using a 3D printer in an apartment, I designed a device (mechanism) for attaching a cable to a cable by wrapping it with wire. This device is necessary for laying cables through large spans "by air". You can learn more about this mechanism in a series of videos:
SteelWorm (Part 1 - Business Case)
SteelWorm (Part 2 - Design and Features)
SteelWorm (Part 3 - Usage Example)
This article, as you understand from the title, is not about that. Here I want to try to break the stereotype that 3D printed products cannot be reliable and usable by the end user. I will start with common questions that I get asked about my mechanism:
1. Plastic housing? It is fragile, the mechanism will quickly break.
Of course, on average, plastic is inferior in strength to metal. Although it is immediately worth noting here that there are a lot of types of plastics and metals! If, for example, we compare ABS plastic and steel grade Ct. 3, then steel will be about 5 times stronger, but 8 times heavier, so the simplest answer to this question is a counter-question:
Do you have an electric screwdriver, grinder or drill? What material is their body made of?
Of course it's plastic! No major manufacturer of tools and household appliances can do without plastic products. I remind you that there are a lot of types of plastics! Each has its own physical and chemical properties, so for each specific case, the manufacturer chooses his own.
As a rule, 90% of the inhabitants are eliminated after this question, but more knowledgeable ones make the following argument:
2. 3D printed plastic is less durable than injection molded plastic used by most manufacturers!
Indeed, products printed on an FDM 3D printer without additional processing are less durable in one of the directions, unlike injection molded plastic.
I won’t write about 3D printing using the SLS method now, because it is not so common, and practically devoid of this drawback.
The diagram above shows the breaking strength of 3D printed hooks depending on the direction of the layers and the thickness of the printed layers. Test results taken from the CNC Kitchen channel (full video available at: https://youtu.be/fbSQvJJjw2Q)
It can be seen from the diagram that plastic can withstand 3 times less load across the layers. In scientific terms, a product printed on a 3D printer is an anisotropic material, but this is not a reason to give up on it.
Wood is also an anisotropic material, but to this day houses are built from it, moreover, as part of the elements of load-bearing structures. Therefore, a design engineer who develops a mechanism must perform strength calculations and make sure that there is a sufficient margin of safety in all nodes. You also need to study the features of the material in advance and arrange the layers so that the loads act along them. If this is not possible, then it is necessary to use additional reinforcement with fiberglass or, as in my case, metal tubes.
It is important to note that at temperatures above 50℃, most plastics begin to lose their strength properties drastically; in the sun, black elements can easily heat up to this temperature, the calculations must be rechecked. Thin body elements first of all begin to deform from the effects of temperature, therefore it is better not to make walls thinner than 1.6 mm, or it is necessary to strengthen them with stiffeners. If the device is used outdoors, attention should be paid to UV resistance and hygroscopicity so that the case does not become brittle under the influence of the sun and the shape of the product does not lead to humidity. In my project, I used PETG plastic, which is devoid of these shortcomings and can be used in the temperature range from -40 to +70℃.
As a result, if all the strength conditions are met and tests are carried out, then nothing prevents the use of products printed on a 3D printer in the final device.
3. If the parts on a 3D printer are strong enough and stable, why do large manufacturers still use casting or stamping?
Economic viability! It all depends on the circulation of products. If you need more than 100 cases, then it will be more profitable to make a mold and quickly cast a batch, and if less, then you already need to calculate the economy. Moreover, each product (detail) separately, because The cost of 3D printing, mold making and casting can vary greatly depending on the size and geometry of the part, as well as surface requirements and manufacturing precision.
I won't go into details of economic analysis now, and sometimes Customers don't need it. It is enough to request a quotation for the manufacture of parts in various organizations involved in casting or 3D printing. Good specialists will quickly estimate the cost of the product according to your 3D model and its circulation, all that remains is to choose the most profitable option.
4. Plastic gears wear out quickly and become unusable.
Another stereotype that leads to confusion. As I noted above, any node of the mechanism is subject to calculation: both strength and work resource. In household appliances, you can often find both plastic gears and metal gears, and even a combination of them. For example, in the figure below, the plastic gear of the Bosch MFM-45020 meat grinder.
Naturally, the greater the load on the gear (speed and torque) and the longer the duration of the load, the faster wear will occur. Accordingly, to reduce wear, the gear must be made larger, or rather, the engagement area should be increased, or a more durable material should be used.
The engagement area can be increased by:
- tooth module increase;
- gear width increase;
- helical gear application.
Unfortunately, there are no simplified methods for calculating the resource of plastic gears. In my model, I only performed a static strength analysis. When starting, the maximum force of 2.1 kg acts on the teeth for a short time, but even with this load, the safety margin for PETG plastic is 38 times!
Further, 99% of the operating time occurs with a load 12 times less, solely to overcome the friction force in the bearings, while the maximum rotation speed is 480 rpm. Therefore, we can say with confidence that under such loads, the gear train will last a very long time.
Nylon is considered the best material for plastic gear due to its strength and low surface friction.
From personal experience, if the operating temperature is not more than 50℃, then PLA gears perform well: it also has a low surface friction coefficient and high abrasion resistance. Try to take a file and grind off a part of the PLA part and everything will immediately become clear.
5. Is the 3D printed case waterproof?
There is a standard for protecting the device against water and dust - IP. The case printed on a 3D printer can easily provide the maximum degree of protection of the IP69 standard, i.e. prevent dust from entering the case completely, ensure immersion in water to a depth of more than 1 meter for more than 30 minutes, and also withstand high pressure and high temperature water jets. You can get acquainted with the detailed decoding of the standard at the link: https://ru.wikipedia.org/wiki/IP_(envelope_protection_degree).
In many ways, the result depends on the literacy of the designer. For example, if you print the body of the product in 1 layer, then there can be no talk of any water permeability. And if you print a hollow cube 100x100mm with a 5mm wall thickness of nylon, it will provide IP69, but how do you put useful stuffing inside? Of course, the body must be collapsible! And this is how the parts of the body will be joined and fastened together - the task of the designer, and here I will share my experience:
I usually use screws and bolts to fasten the body parts together. For reliable fixation, I developed the following rules:
1. Bolts and screws are used only with a flat head, i.e. not with a hidden head! Especially if the hole is made along the layers. Otherwise, when you tighten the hardware, the part may simply crack.
2. The holes for the screws must be made smaller than diameter D to engage the thread with the plastic:
If perpendicular to the layers - 0.89*D;
If parallel to the layers - 0.95*D;
If you do less, the screw will be difficult to screw in and the plastic may break.
3. Holes for self-tapping screws must be made smaller than diameter D to engage the thread with plastic:
If perpendicular to layers 0.83*D
If parallel to layers 0.87*D
4. If you need a simple and strong connection of 2 large parts with a tight compression between them, then use the connection on bolts and flanges.
For free play of the bolt, the hole diameter must be increased by 0. 2mm.
5. To ensure that parts fit into each other, I use the following rule:
Fits (gaps) for "Plastic-Plastic" in 3D model:
• Loose (walks easily, dangles) - 0.3 mm;
• Medium (with little effort) - 0.2 mm;
• Thick (forced in) - 0.1 mm.
If the parts are large and the area of their contact is large (>5cm2), then it is desirable to increase the gaps.
"Plastic-metal", the same, just the gaps are 2 times smaller.
Unlike metal, plastic has large tolerances. As can be seen from the diagram above, this is due to the influx of layers. Therefore, in order to achieve the IP65 standard for a prefabricated printed case, it will be necessary to use rubber washers and gaskets, which can also be printed on a 3D printer from elastic filaments.
Conclusion
I hope the article turned out to be equally useful for Contractors and Customers. I tried to dispel the fears of Customers about products printed on a 3D printer, and I also shared my personal experience in designing cases, which means that this article should be useful for beginners in 3D printing.