Nea 3d printer price
NEA Family of 3D Printers at CES
0Shares
Launched at CES this year is one of the most elegant looking series of desktop 3D printers I’ve seen so far, more than eligible for Shane’s Sexiest 3D Printer award. The NEA family of FFF printers – which includes the NEA PRO Mini, PRO, and PRO+ – boasts a great footprint to print area ratio, a sleek design, and a reasonable price tag.
The NEA family is everything you expect from a Golidlocks fairytale: a baby, momma, and poppa bear. The NEA PRO Mini has a build volume of 6”x6”x6” and a price of $995, while the PRO measures 10”x10”x10” and will cost $1,295 and the PRO+ is 14”x14”x20” and will run at about $1,995. The machines are all capable of layer thicknesses of about 25 microns and are all equipped with some of the latest features, now standard on new generations of 3D prints, including: a self-leveling, heated printbed and wi-fi connectivity.
In addition to these standard features, the NEA printers are modular, so that parts, including the printhead, can be easily removed and replaced. The filament spool fits nicely into the top of the printer, so as to remain inconspicuous and, as the printer maxes out its print volume on the Z-axis, the filament spool is pushed upward for even greater room. And the company is introducing its proprietary Vibration Dampening system, to ensure repeatability and even prints.
CTO and chief inventor of the technology, Stoyan Tadin, said of his invention, “Throughout 2014 we engineered the NEA family of 3D Printers to be able to offer professional quality and specifications with models for home, education and professionals –whether in art, entertainment or medical and professional prototyping and final product.” He adds, “In my 30 years of management and involvement in Research & Development, this has been and is my most exciting endeavor because it is only the beginning of the many innovations we have in the pipeline.”
NEA 3D Inc. CEO, William Chang, contributed, “We’re applying two decades of experience in high end 3D modeling to further enrich peoples understanding of what can be created and how it can be applied to the rapidly growing 3d printing industry and community. We’ve brought together a team of 3D printing experts to design one of the coolest, most innovative 3D printers in the world. Our unique online maker experience puts customer support and education at the forefront, empowering professionals and hobbyists to share their creations and knowledge with everyone.”
Chang is also the CEO of Playfight VFX Inc., a branding and visual effects company that has worked on Respawn’s Titanfall, Freddie Wong’s Video Game High School., and musician Lindsey Stirling. Chung continues, “In our business we understand and need to produce quality, excellence and performance. We simply weren’t satisfied with the 3D Printers we had purchased on crowdfunding platforms. So we embarked on engineering out the flaws we had experienced with those products, the result producing what we believe is not only the most stunning series with superb engineering craftsmanship, but fully featured and calibrated out of the box.” Chang’s background is illustrated clearly in the beautiful promo video below:
After they stint at CES, NEA plans to launch a crowdfunding campaign, including special pricing on all of their products, to launch their NEA family into full production. Along with it, you can expect more details about the printers, as well as more sleek marketing that’s hard to beat.
Michael Molitch-Hou
Michael Molitch-Hou previously served as Editor-in-Chief of 3D Printing Industry, he is now the Editor of Engineering . com's 3D printing section. He has covered additive manufacturing technology day in and day out since 2012 and has hundreds of article to his credit. He is the founder of The Reality Institute.
NEA 3D Printer at Early Bird Prices
0Shares
NEA 3D’s very beautiful family of 3D printers waltzed into CES this year, where they were met with attendees that fawned over, the elegant appearance of the PRO Mini, PRO, and PRO+ FFF machines, as well as their excellent mechanical design, and their reasonable prices. Though not available for purchase in January, the family is now ready for prime time, as it heads to Indiegogo on May 6th. And, today, NEA 3D has opened up its VIP sign-up page, allowing you to get VIP access to the crowd-funding campaign 24 hours in advance. You know what that means! Early bird prices!
If you head over to the NEA 3D website, you’ll be able to register to purchase any one of the three models of NEA 3D printers before the rest of the public. The first 100 customers backing each model will all get early-bird pricing on the the PRO Mini, PRO, and PRO+ 3D printers. And, for each printer, this cuts the price down by 50%. That’s $495 for the Mini, $845 for the PRO, and $1,095 for the PRO+, all of which have suggested retail prices of nearly twice those figures. And, the best part is, for every NEA PRO and PRO PLUS sold during the campaign, NEA 3D will donate $25 and $30, respectively, E-nable, to get more 3D printed prosthetics to even more people!
All of the machines are billed with self-leveling and wi-fi connectivity, as well as layer thicknesses of 25 microns. The Pro and Pro+ will come standard with a heated bed, while this will be offered as an upgrade for the Mini. The build volumes of the Mini, PRO, and PRO+ are 6 x 6 x 7″ (15 x 15 x 17cm), 10 x 10 x 11″ (25.5 x 25.5 x 28cm), and 14 x 14 x 15″ (35.5 x 35.5 x 38cm), respectively. All of the parts are modular, for easy removal and replacement, which also means that all of the printers will be upgradable. As CEO William Chang puts it, “Any printer can have any feature in the future.” Uniquely, the filament spool is hidden in the top of the printer, where the spool is pushed upward as the Z-axis is maxed out while printing. Finally, the machines also feature the company’s proprietary Vibration Dampening system, for greater repeatability. It was all of these features that impressed onlookers at CES, apart from the printers’ keen aesthetic.
NEA 3D has firm ties with video FX firm, Playfight VFX Inc, through CEO, William Chang. Not only does this yield some really polished marketing for NEA, but it immerses NEA 3D in the world of video gaming and video production, opening the company up to a number of opportunities for connecting with production companies in a number of industries. I envision licensed, 3D printable content from one of Playfight’s many partners, such as the variety of companies behind Titanfall.
So far, NEA has one happy customer, Freddie Wong, of Video Game High School, and I’m sure there will be plenty more, if the company can deliver on all of these specs. We’ll find out when the first batch of printers are delivered in the third quarter of this year. Until then, there will be more opportunities to learn more about the company.
For instance, this summer, NEA 3D plans to roll out their online community beta site, where their galleries, resources, and learning tools will be located. And, this June, from the 22nd to the 26th, NEA will be attending the Consumer Electronics Show in NYC. So, if you’re in the area, you might get to see one of their gorgeous machines up close and in action. For now, sign up for VIP access to the campaign or stay tuned for the Indiegogo launch on May 6th.
Update 5/6/2015: With the launch of their Indiegogo campaign just twenty minutes ago, NEA 3D has already reached their $75k crowdfunding goal. And, as every model is still available at early bird prices, it’s likely that the campaign will only continue to grow.
The campaign also reveals a lot of new details about NEA 3D, their printers, and their software. For instance, the company plans to launch their online 3D model community, NEATSTUFF, just before the first printers are shipped fall of this year. With the company’s CEO also acting as the CEO of Playfight VFX, NEA will also provide free tutorials to help users learn their NEA Repetier software.
Other details revealed with the campaign include the fact that NEA will likely release additional extruders in the future, meant to be easily added or switched out due to the printers’ modular designs. The campaign also features a number of prints demonstrating the quality of their printers and the following video, showcasing all of the printers’ features, the printers in action, and more.
If you’re interested in contributing to the campaign, head over to Indiegogo to learn more.
Michael Molitch-Hou
Michael Molitch-Hou previously served as Editor-in-Chief of 3D Printing Industry, he is now the Editor of Engineering . com's 3D printing section. He has covered additive manufacturing technology day in and day out since 2012 and has hundreds of article to his credit. He is the founder of The Reality Institute.
The cheapest, fastest and most innovative devices — Look At Me
Text
Margarita Popova
3D printers are gradually becoming commonplace, thanks to the many ways to quickly and cheaply print your object or projects like The Buccaneer, which reduce the price of devices several times.
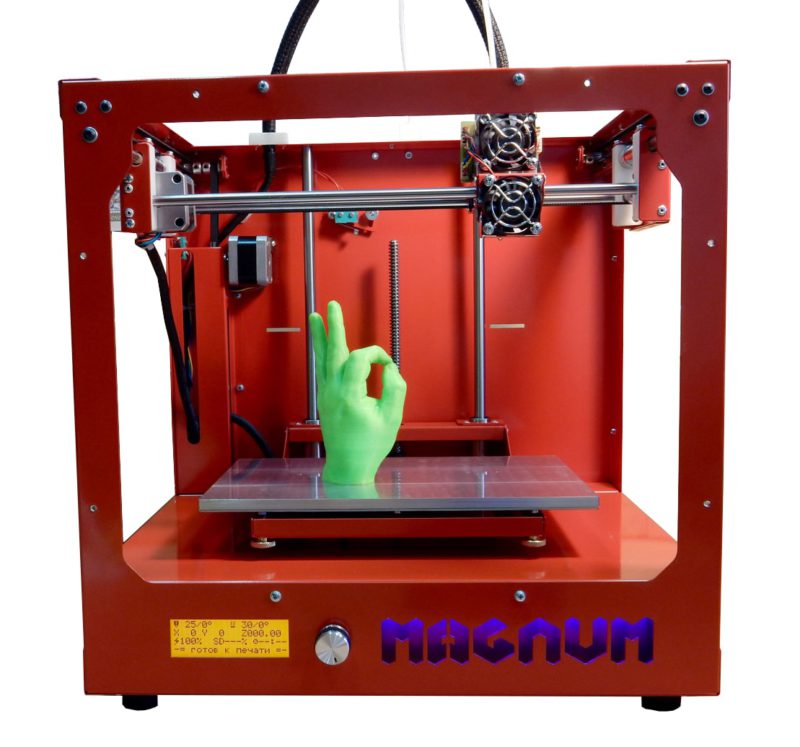
Ease in use
Makerbot Replicator 2
$ 2199
, unlike those market representatives who prefer to supply parts for parts, Makerbot Replicator 2 does not require assembly and ready to use immediately after as the buyer pulls it out of the box. However, it is not only this that makes it one of the easiest printers to use, but also an active user community that takes on any problems with the device with great enthusiasm, and a number of related products - from materials to 3D scanners. In this, MakerBot is close to the idea of its close competitors - Cubify, however, the latter also sell print results.
Ralf van Bemmel
co-founder of MakerWise
Cubify is aimed at the consumer, while MakerBot 2 positions itself as a slightly more professional product.
Cubify is cheaper, but the materials (cartridges) for it are more expensive. MakerBot is bigger and stronger on the technical side. However, there are other 3D printers on the market that differ in price, quality, size, appearance, materials, software, and so on. If you have not yet compared these two printers with others, it makes sense to start with this.
Price
Solidoodle
$ 499
It was logical that increased attention to 3D-printing should sooner or later reduce price reduction of both devices and materials for materials — which is what happens: projects like The Buccaneer raise astronomical amounts on Kickstarter and promise not to set a price higher than $397. Unfortunately, we'll have to wait until production and sales start, but if you need a cheap 3D printer right now, you should pay attention to Solidoodle, which promises decent quality for only $49.0008
Wil Chang
co-founder of Cubehero
The speed of a 3D printer depends on how fast the layers are created (print speed) and how fast the components move (travel speed).
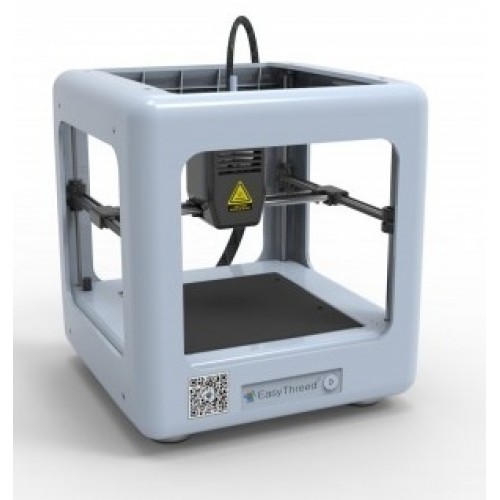
The best print quality
TYPE A SERIES 1
$ 1695
, according to Type a Series 1 manufacturers, accessible to their printers, twice the average in the market. Printer resolution starts at 50 microns (0.05 mm) and minimum layer thickness from 100. This is made possible by the use of more precise components. Considering the printer's speed and ease of use, the Type A Series 1 is well suited for perfectionists.
Maxim Lobovsky
co-founder of
Form Labs
To minimize the size of The Form 1, we used the latest developments in laser technology.
What's more, we didn't just want to downsize huge stereolithography machines, but we designed our printer from the very beginning. So we came up with ideas that were more suitable for our task - to create a stereolithographic 3D printer that would fit on the desktop.
How much does a 3D printer cost?
3D printing is a one-stop solution for a wide range of applications, from high-resolution model production to rapid prototyping, rapid tooling for traditional manufacturing processes, production of aids and end-use models.
However, when you consider investing in a 3D printer, the viability of a solution usually boils down to a simple question: Is it cost-effective for your business? How much does a 3D printer cost and how much time and money can it save your business?
3D printer prices range from $200 to $500,000 depending on the printing process, materials, and complexity of the solution.
In this guide, we'll break down 3D printing costs by technology, compare outsourcing versus in-house manufacturing, list factors to consider when calculating the cost of each model, and look at what else to look for when comparing different solutions. for 3D printing and other production methods.
Interactive
This interactive ROI tool will help you find out how much time and money you can save by 3D printing with a Formlabs 3D printer.
Calculate your costs
Three of the most well-known plastic 3D printing technologies today are Fused Deposition Modeling (FDM), Stereolithography (SLA), and Selective Laser Sintering (SLS).
Each technology has its advantages and disadvantages - take a look at the infographic:
Download this high resolution infographic here. Interested in learning more about FDM, SLA and SLS 3D printing technologies? Check out our detailed guide.
Prices for 3D printers have dropped significantly in recent years, and today all three technologies are available in compact, low cost systems.
FDM generally produces models at a lower cost if you only print relatively simple prototypes in limited quantities. SLA technology offers higher resolution and quality, as well as a wide choice of 3D printing materials at a slightly higher price. But this difference is quickly offset when you print complex designs or larger batches due to the less labor-intensive post-processing process. Finally, SLS technology is the most cost effective for medium to high volume production of high quality functional models.
Comparing the total cost of different 3D printers by price alone will not give you a complete picture of how the cost of a 3D printer and a printed model will compare. The cost of 3D printing materials and labor significantly affects the cost of a model, depending on the application and your production needs.
Let's look at the different factors and costs for each process.
FDM, also known as Fused Filament Manufacturing (FFF), is a printing method where the parts of a model are made by melting and extruding a thermoplastic filament that the printer's nozzle applies layer by layer onto the model being made.
FDM is the most popular form of consumer grade 3D printing, fueled by the rise of hobbyist 3D printers. However, professional and industrial FDM printers are also popular among professionals.
The cheapest 3D printers are FDM printers. DIY kits for FDM 3D printers start at $200. However, most of these models are more like toys or DIY projects that require a significant amount of time to build, set up and calibrate. The quality of the print largely depends on the success of these operations. In addition, machines require repairs and regular maintenance to keep them working, so they are more suitable for people with a higher engineering education who have a lot of time and patience.
Hobbyist FDM 3D printers cost between $500 and $1,500, come pre-assembled or unassembled, require less setup, but have the same disadvantages as the cheapest 3D printers. More expensive models are capable of large print volumes and work with a wide variety of materials besides low temperature ones such as PLA.
Professional 3D FDM printers start at $2,500 and large format professional FDM printers are available from $4,000. The cost of the most modern industrial FDM printers can exceed 10,000 US dollars. Most of these printers come pre-assembled and calibrated in the box, or they can be automatically calibrated. Printers in this category offer better print quality, a wider range of media, higher print volumes, improved reliability, and ease of use and maintenance. In addition, professional 3D printer manufacturers offer customer support services for troubleshooting.
Material costs for FDM 3D printing range from $50 to $150/kg for most standard and engineering filaments, and $100 to $200/kg for auxiliary materials. There are also cheaper alternatives, but they are of lower quality.
In addition, FDM printing can be very labor intensive. Successful printing of complex models requires support structures that must be removed manually or dissolved in water. To obtain a high quality surface and remove layer lines, lengthy manual post-processing of models, such as sanding, is necessary.
SLA 3D printers use the process of photopolymerization, that is, the conversion of liquid polymers into hardened plastic using a laser. SLA is one of the most popular processes among professionals due to its high resolution, accuracy and material versatility.
Models printed on SLA printers have the highest precision, sharpest detail, and smoothest surface possible of any plastic 3D printing technology. But the main advantage of the SLA method is its versatility. SLA polymers have a wide range of optical, mechanical and thermal properties that match those of standard, engineering and industrial thermoplastics.
SLA 3D printers can handle a wide range of resin materials for a wide variety of applications.
SLA used to be used only in large and complex industrial 3D printers costing over $200,000, but the process is now much more affordable. With the Formlabs Form 3+ Printer, businesses can now use industrial quality SLA printing for as little as $3,750. With Form 3L, large format SLA printing starts at just $11,000.
Stereolithographic 3D printers will be shipped in a box assembled and calibrated. These are professional tools that are highly reliable and require virtually no maintenance. Technical support is also always available. It provides troubleshooting in a critical situation (but its probability is extremely small).
Most standard and engineered polymers for SLA technology cost between $149 and $200 per liter.
SLA printers are easy to use and many workflow steps such as rinsing and final curing can be automated to reduce labor costs. Printed models have a high quality surface immediately after printing and require only simple post-processing to remove supporting structures.
Selective Laser Sintering (SLS) 3D printers use a high power laser to sinter fine polymer powder particles. The unsprayed powder supports the model during printing and eliminates the need for special support structures. This makes SLS ideal for complex geometries, including internal features, grooves, thin walls, and negative taper.
Models produced using SLS printing have excellent mechanical characteristics - their strength can be compared with the strength of injection molded parts. As a result, SLS technology is the most popular plastic 3D printing process for industrial applications.
SLS printed nylon models are ideal for a range of functional applications, from consumer product design to healthcare applications.
Like SLA, SLS was previously only available in large format, complex 3D printing systems costing $200,000 or more. With the Formlabs Fuse 1 stereolithography printer, businesses can now solve industrial-scale tasks with SLS technology starting at $18,500. The complete kit, which includes the post-processing and powder recovery system, costs $31,845.
As with SLA printers, stereolithography printers are shipped assembled and calibrated in the box. They are reliable and can operate 24/7. The package includes in-depth training and fast technical support.
SLS nylon print materials cost about US$100/kg. SLS does not require supporting structures and unused powder can be reused, reducing material costs.
SLS is the least labor-intensive plastic 3D printing process in the production environment, because the printed models are of high quality right away, and to remove excess powder, they simply need to be cleaned.
There are several processes for 3D printing not only plastics but also metals.
Metal FDM printers are similar in design to traditional FDM printers, but use extruded metal rods held together by a resin binder. The finished parts of the model are sintered in an oven to remove the binder.
SLM and DMLS printers are similar to SLS printers, but instead of polymer powders, they fuse metal powder particles layer by layer using a laser. 3D printers based on SLM and DMLS technologies can create strong, precise and complex metal products, making this process ideal for the aerospace, automotive and medical industries.
Prices for metal 3D printers have also begun to decline, ranging from $100,000 to $1 million today. However, these systems are still out of reach for most businesses.
SLA 3D printing is available as an alternative to casting workflows that allow metal models to be produced cheaper and faster than traditional methods and provide greater design freedom.
Technical report
Get design guides for 3D printing samples, see the step-by-step direct investment casting process, and study guides for indirect investment casting and sand casting.
Download white paper
Different plastic and metal 3D printing processes have unique qualities that make them suitable for different applications. Below is a comparison of different printing technologies.
Fused Deposition Modeling (FDM) | Stereolithography (SLA) | Selective Laser Sintering (SLS) | Metal FDM Printing | Selective Laser Melting (SLM) and Metal Direct Laser Sintering (2607) | 2607||||
---|---|---|---|---|---|---|---|---|
Permission | ★ Look | ★ opa | ★cle | ★cle | ★☆★ opa ★ ution | ★ opa | ★cle | ★cle ★ Look |
Surgery | ★ opa ★ opa ☆ | ★cle | ★cle | |||||
Production | ★ opa | ★ Looking ☆ | ★ opa | |||||
Ease of use | ★ opa | ★cle ★ Look | ★cle | ★ opa | ★ | |||
PRESTION | 90 x 300 x 600 mm (Desktop and Workshop 3D printers)Up to ~300 x 335 x 200 mm (Desktop and Workshop 3D printers) | Up to 165 x 165 x 300 mm (3D - workshop printers) | Up to 300 x 200 x 200 mm | Up to 400 x 400 x 400 mm | ||||
Price range | DIY kits for 3D printers start at $200, while hobby printers cost $500-1500.![]() | Professional desktop printers start at $3,750, while high-volume large format desktop printers are available from $11,000. | Workshop industrial printers start at $18,500 and traditional industrial printers start at $100,000. | Metal FDM printers start at $100,000, but complete solutions including an oven are much more expensive. | DMLS/SLM solutions start at around $200,000. These printers require special infrastructure conditions, which can further increase costs. | |||
Cost of materials | US$50-150/kg for most standard and engineering yarns and US$100-200/kg for auxiliary materials. | $50-150/L for most standard and engineering polymers. | US$100/kg for nylon. SLS does not require supporting structures and unused powder can be reused, reducing material costs. | Depends on material and technology.![]() | Depends on material and technology. Significantly higher than plastic. | |||
Labor | Manual removal of support structures (soluble support structures may be used in some cases). Long post-processing is required to obtain a high quality surface. | Washing and final polymerization (both can be automated). Simple post-processing to remove supporting structures. | Easy cleaning to remove excess powder. | Washing and sintering (both can be automated). It is possible to use mechanical processing and other types of surface treatment. | Stress relief, support structure removal, heat treatment, and mechanical and other surface treatments. | |||
Materials | Standard thermoplastics such as ABS, PLA and their various blends. | Various polymers (thermosetting plastics). Standard, engineering (similar to ABS and PP, similar to silicone, flexible, heat resistant, rigid), injection molding, dental and medical (biocompatible).![]() | Engineering thermoplastics - typically nylon and its composites (nylon 12 biocompatible + sterilizable). | Stainless steel, tool steel, inconel, copper, titanium. | Stainless steel, tool steel, titanium, cobalt-chromium, copper, aluminium, nickel alloys. | |||
Applications | Basic experimental models, low cost rapid prototyping of simple parts. | Prototypes with a high level of detail requiring tight tolerances and smooth surfaces: molds, tooling, templates, medical models and functional parts. | Complex geometries, functional prototypes, low volume production or limited trial production. | Strong and durable models, tools and production aids. | Strong and durable models with complex geometries; ideal for the aerospace, automotive and medical industries. |
When calculating the cost of one model, the cost of ownership of equipment, material costs and labor costs are usually taken into account. It is important to understand the factors that affect each of these cost components, as well as the questions to ask in order to evaluate alternative production methods and uncover hidden costs.
Hardware ownership costs are fixed costs: 3D printer price, service contracts, installation and maintenance. These amounts must be paid whether your printer is idle or produces dozens of models per week.
Add up all projected fixed costs over the lifetime of the equipment, then divide by the number of models you plan to make. As a rule, the higher the performance and efficiency of your 3D printer, the lower the cost of ownership of equipment per model.
In recent years, desktop 3D printers have shown excellent results in reducing the cost of ownership of equipment. With a price 10 to 100 times lower than traditional industrial 3D printers and the ability to produce thousands of models over a lifetime, the cost of ownership can be negligible.
Questions:
-
Are there installation, training or additional initial costs other than the cost of the machine itself?
-
Do I need to sign a (mandatory) service contract? What does it include?
-
What accessories and tools are needed to make the final models?
-
What kind of maintenance is required for the machine to function properly? What is the expected annual maintenance cost? Will it change with an increase in production volumes?
The 3D printing raw materials and consumables you need to create models at an affordable price. These costs largely depend on the number of models you produce.
When calculating the cost of materials, determine how much material is required to create one model, and multiply this figure by the cost of the material. Count the amount of waste and any other consumables. As production grows, the cost of ownership of equipment decreases, and the cost of 3D printing materials tends to become more balanced.
Be sure to check what materials you need to create specific models, as the cost of 3D printing consumables can vary greatly. Please note that some 3D printers only work with their proprietary materials and thus limit your ability to use third party materials.
Questions:
-
What is the cost of each type of 3D printing material?
-
How much material is required to create one particular model, including waste?
-
What is the shelf life of the materials?
-
Do I need other consumables to create models?
-
Can the machine work with third-party materials?
While 3D printing can replace complex traditional manufacturing methods and provide significant time savings, depending on the 3D printing technology, it can still be quite labor intensive.
Professional desktop 3D printers are generally optimized for ease of use. DIY kits for 3D printers and hobby printers often require additional effort to adjust settings, while regular maintenance or material changes on traditional industrial machines can involve time-consuming tasks that require the assistance of a skilled operator.
Post-processing workflows vary depending on the 3D printing process, but in most cases include cleaning up models and removing support structures or excess material. However, there are solutions to automate some specific tasks. For example, Formlabs Form Wash and Form Cure simplify the wash and finish process for Formlabs SLA 3D printers, while Fuse Sift offers a turnkey post-processing and powder recovery system for the Fuse 1 SLS printer.
More complex processes such as SLA and SLS do not take long to achieve high quality models, while FDM models require lengthy manual post-processing to improve quality and remove layer lines.
Questions:
-
What is the whole model production workflow? What specific steps are required to set up printing, change materials, and post-process models?
-
How long does it take to post-process one specific model?
-
Are there any tools or devices available to automate some of these tasks?
Outsource production orders to third-party service bureaus or labs when you use 3D printing only occasionally or to produce large models in non-standard materials. Typically, the bureau has several in-house 3D printing processes such as SLA, SLS, FDM, as well as metal 3D printers. They can also provide advice on a variety of materials and offer additional services such as design or improved finishes.
The main disadvantages of outsourcing are the high cost and duration of production. One of the main advantages of 3D printing is its speed compared to traditional production methods. But it is noticeably reduced if the delivery of the model produced by the involved organization takes several days or even weeks. And as demand and capacity grow, the costs of outsourcing are rising rapidly.
Desktop 3D printers are an excellent solution for rapid model production. Depending on the number of parts needed and the volume of prints, the investment in a professional 3D printer can pay for itself in just a few months.
With desktop and workshop printers, you can pay for the capacity that matches your business needs and scale your production by adding more devices as demand grows, without the heavy investment of a large format 3D printer. Using multiple 3D printers also allows you to print models from different materials at the same time. But if there is a need for the production of large parts or the use of non-standard materials, service bureaus can come to the rescue.
Investment, material and labor costs are relatively easy to calculate. But what about indirect costs and hard-to-calculate factors that affect your business? Let's look at some of the main considerations when comparing a desktop 3D printer to outsourcing or other manufacturing methods.
Save time: What if you could get products to market a few months faster? Or reduce the delivery time of your products by a few days or weeks? 3D printing simplifies traditional prototyping and manufacturing workflows, helping you save time and stay ahead of the competition.
Best results: 3D printing allows you to create more iterations, overcome failures faster and produce better end products. Troubleshooting a design early on also helps avoid costly redesign and the use of additional tools.