Material 3d printers use
What Materials Are Used in 3D Printing?
Published Date
Author Jeff Yoders- Plastic is still the most popular material used for 3D printing.
- As the 3D-printing market value increases, the list of what materials can be used also grows.
- Raw materials such as metal, graphite, and carbon fiber are commonly used for 3D printing, though at-home use is mostly limited to PLA for now.
Ice cream. Molecules for medicine. Even human skin. The list of what materials are used in 3D printing grows longer—and much more interesting—by the day. And expanding it is a multibillion-dollar material arms race right now.
A recently released 3D-printing market study found that the worldwide market for 3D-printing products was valued at $12. 6 billion in 2020 and was expected to grow to $37.2 billion by 2036. That means a huge increase in the materials those machines use.
What Is The Most Common Material Used for 3D Printing?
Plastic still reigns supreme in the 3D printing. According to a Grand View Research report, the market size for 3D printing plastics globally was valued at $638.7 million in 2020 and was expected to grow to $2.83 billion by 2027.
This material isn’t just your “everyday” plastic. Two types of plastic are most commonly used in 3D printing:
- PLA: Poly Lactic Acid (PLA) is the most popular 3D-printing material. It’s a biodegradable plastic made from renewables such as cornstarch. Its low melting point makes it easy to use at home.
- ABS: Acrylonitrile butadiene styrene (ABS) is best suited for parts that require strength and flexibility, like car components or household appliances. It’s also known for its low cost.
But it doesn’t stop there in the 3D-printing materials world.
1. Metal
Used for: Ready-to-install parts, finished products, prototypes
If there is a runner-up to plastic, it would be metal. Direct metal laser sintering (DMLS) is the technique and, unlike printing plastics, it can be used to make either a finished industrial product or a prototype. The aviation industry is already an early proponent and consumer of DMLS printing to streamline operations and manufacture ready-to-install parts. There are even already mass-market DMLS printers for creating 3D-printed jewelry.
The growth and popularity of 3D printing metals holds the potential to manufacture and create more effective machine parts that currently cannot be mass-produced onsite. This could lead to better conductors, tensile strength, and other attributes of laboratory metals than “mined-and-refined” metals such as steel and copper.
In the aerospace industry, the materials question is largely answered, and creating volume of parts is the Holy Grail. GE Aviation began printing fuel nozzles for its LEAP jet engine in 2016, ramping up to 30,000 parts in less than three years and printing its 100,000th nozzle in 2021. The LEAP’s successor, the RISE, will also incorporate 3D-printed parts.
Used for: Electronics, lighting
Australian-listed graphite and nickel miner Kibaran Resources has partnered with 3D-printing company 3D Group to share development costs on a research-and-development venture called 3D Graphtech Industries.
The partnership is pursuing patents to investigate 3D printing graphite and graphene, a pure form of carbon first created in a laboratory in 2004. Graphene conducts electricity better and is stronger, easier to insulate, and lighter than other conductors on the market today. It outperforms even the best conductors several times over. Because it must be created in a lab, it is a good case study for just what kind of mass production of metals additive manufacturing can accomplish.
Materials for research and development are sourced from Kibaran’s Tanzanian mines, where graphite with high crystallinity and a purity of 99.9% carbon has been found. This is incredibly well-suited to the production of graphene.
The semiconductor industry is interested in producing large quantities of graphene, as well. For example, IBM found a way to use it for LED lighting in 2014. The ability to 3D print sheets of material for use in LEDs could seriously cut lighting production costs.
3. Carbon FiberUsed for: Bearings, parts, electrical cable installation
Related to graphite, carbon fiber (which undergoes an oxidation process that stretches the polymer) can be added to the more traditional plastic to create a composite that can be as strong as steel but less intensive to use than aluminum, says Markforged. The company’s large-format 3D printers are designed to print stronger parts more quickly and at significantly lower costs.
Meanwhile, startup Impossible Objects has also been exploring carbon fiber, as well as glass, Kevlar, and fiberglass. The company’s printer can also work with PEEK (polyether ether ketone) thermoplastic polymers, which are typically used for bearings, piston parts, and electrical cable installation.
New 3D Printing Materials
The 3D-printing industry is experimenting with a wide variety of innovative, novel approaches such a bio-based resins made from corn and soybean oil, powders, nitinol, and even paper.
Do I Need a New 3D Printer for These Materials?As the list of materials grows, what does this mean for the actual hardware? Right now, on the consumer level, plastic is about as good as it gets. For example, the $1,399 Dremel 3D40 Flex is limited to PLA.
Today, several printers are focused entirely on DMLS, including the 3DSystems DMP Flex 350 and several models from Stratasys, but these currently cost upward of $100,000 each because DMLS printers burn much hotter than their plastic counterparts, as the powders and metals they create have higher melting points. Stronger housings and more powerful industrial smelting tools increase their costs significantly.
Although many 3D-printer manufacturers are offering metal 3D-printing services, it will be some time before the economies of scale that helped bring down the cost of plastic 3D printing affect the DMLS market. And 3D-printing systems with graphite/carbon fiber are just now starting to gain traction in the marketplace.
The diversity of applications that industries are exploring for 3D printing makes for an exciting but tumultuous time. From jet parts to lighting to rapid prototyping, the new (and “old”) 3D printing materials will deliver even more opportunities for how and what industries print.
This article has been updated. It was originally published in November 2014.
About the Author
Jeff Yoders has covered IT, CAD, and BIM for Building Design + Construction, Structural Engineer, and CE News magazines. He has won six American Society of Business Publications Editors awards and was part of the reporting team for the 2012 Jesse H. Neal Award for best subject-related series of stories.
Follow on Twitter More Content by Jeff Yoders
What Materials Are Used in the 3D Printing Process?
The materials used for 3D printing are as diverse as the products that result from the process. As such, 3D printing is flexible enough to allow manufacturers to determine the shape, texture and strength of a product. Best of all, these qualities can be achieved with far fewer steps than what is typically required in traditional means of production. Moreover, these products can be made with various types of 3D printing materials.
In order for a 3D print to be realized in the form of a finished product, a detailed image of the design in question must first be submitted to the printer. The details are rendered in standard triangle language (STL), which conveys the intricacies and dimensions of a given design and allows a computerized 3D printer to see a design from all sides and angles.
Basically, an STL design is the equivalent of multiple flat designs in one computerized file.
The industry for 3D printing is expected to surpass the 10-figure mark in the near future and plastic is set to be the main material to drive this market. As concluded recently in a SmarTech Markets Publishing study, the market for 3D printing is likely to exceed $1.4 billion before 2020. With an ongoing market expansion, the industry has sought new ways to yield plastics, including the use of organic ingredients like soybean oil and corn. Consequently, plastics are set to become the most environmentally friendly option in 3D printing.
Plastic
Out of all the raw materials for 3D printing in use today, plastic is the most common. Plastic is one of the most diverse materials for 3D-printed toys and household fixtures. Products made with this technique include desk utensils, vases and action figures. Available in transparent form as well as bright colors — of which red and lime green are particularly popular — plastic filaments are sold on spools and can have either a matte or shiny texture.
With its firmness, flexibility, smoothness and bright range of color options, the appeal of plastic is easy to understand. As a relatively affordable option, plastic is generally light on the pocketbooks of creators and consumers alike.
Plastic products are generally made with FDM printers, in which thermoplastic filaments are melted and molded into shape, layer by layer. The types of plastic used in this process are usually made from one of the following materials:
- Polyastic acid (PLA): One of the eco-friendliest options for 3D printers, polyastic acid is sourced from natural products like sugar cane and corn starch and is therefore biodegradable. Available in soft and hard forms, plastics made from polyastic acid are expected to dominate the 3D printing industry in the coming years. Hard PLA is the stronger and therefore more ideal material for a broader range of products.
- Acrylonitrile butadiene styrene (ABS): Valued for its strength and safety, ABS is a popular option for home-based 3D printers.
Alternately referred to as “LEGO plastic,” the material consists of pasta-like filaments that give ABS its firmness and flexibility. ABS is available in various colors that make the material suitable for products like stickers and toys. Increasingly popular among craftspeople, ABC is also used to make jewelry and vases.
- Polyvinyl Alcohol Plastic (PVA): Used in low-end home printers, PVA is a suitable plastic for support materials of the dissolvable variety. Though not suitable for products that require high strength, PVA can be a low-cost option for temporary-use items.
- Polycarbonate (PC): Less frequently used than the aforementioned plastic types, polycarbonate only works in 3D printers that feature nozzle designs and that operate at high temperatures. Among other things, polycarbonate is used to make low-cost plastic fasteners and molding trays.
Plastic items made in 3D printers come in a variety of shapes and consistencies, from flat and round to grooved and meshed. A quick search of Google images will show a novel range of 3D-printed plastic products such as mesh bracelets, cog wheels and Incredible Hulk action figures. For the home craftsperson, polycarbonate spools can now be purchased in bright colors at most supply stores.
Powders
Today’s more state-of-the-art 3D printers use powdered materials to construct products. Inside the printer, the powder is melted and distributed in layers until the desired thickness, texture and patterns are made. The powders can come from various sources and materials, but the most common are:
- Polyamide (Nylon): With its strength and flexibility, polyamide allows for high levels of detail on a 3D-printed product. The material is especially suited for joining pieces and interlocking parts in a 3D-printed model. Polyamide is used to print everything from fasteners and handles to toy cars and figures.
- Alumide: Comprised of a mix of polyamide and gray aluminum, alumide powder makes for some of the strongest 3D-printed models.
Recognized by its grainy and sandy appearance, the powder is reliable for industrial models and prototypes.
In powder form, materials like steel, copper and other types of metal are easier to transport and mold into desired shapes. As with the various types of plastic used in 3D printing, metal powder must be heated to the point where it can be distributed layer-by-layer to form a completed shape.
Resins
One of the more limiting and therefore less-used materials in 3D printing is resin. Compared to other 3D-applicable materials, resin offers limited flexibility and strength. Made of liquid polymer, resin reaches its end state with exposure to UV light. Resin is generally found in black, white and transparent varieties, but certain printed items have also been produced in orange, red, blue and green.
The material comes in the following three categories:
- High-detail resins: Generally used for small models that require intricate detail.
For example, four-inch figurines with complex wardrobe and facial details are often printed with this grade of resin.
- Paintable resin: Sometimes used in smooth-surface 3D prints, resins in this class are noted for their aesthetic appeal. Figurines with rendered facial details, such as fairies, are often made of paintable resin.
- Transparent resin: This is the strongest class of resin and therefore the most suitable for a range of 3D-printed products. Often used for models that must be smother to the touch and transparent in appearance.
Transparent resins of clear and colored varieties are used to make figurines, chess pieces, rings and small household accessories and fixtures.
Metal
The second-most-popular material in the industry of 3D printing is metal, which is used through a process known as direct metal laser sintering or DMLS. This technique has already been embraced by manufacturers of air-travel equipment who have used metal 3D printing to speed up and simplify the construction of component parts.
DMLS printers have also caught on with makers of jewelry products, which can be produced much faster and in larger quantities — all without the long hours of painstakingly detailed work — with 3D printing.
Metal can produce a stronger and arguably more diverse array of everyday items. Jewelers have used steel and copper to produce engraved bracelets on 3D printers. One of the main advantages of this process is that the engraving work is handled by the printer. As such, bracelets can be finished by the box-load in just a few mechanically programmed steps that do not involve the hands-on labor that engraving work once required.
The technology for metal-based 3D printing is also opening doors for machine manufacturers to ultimately use DMLS to produce at speeds and volumes that would be impossible with current assembly equipment. Supporters of these developments believe 3D printing would allow machine-makers to produce metal parts with strength superior to conventional parts that consist of refined metals.
In the meantime, the use of 3D parts is taking flight in the aerospace industry. In what has been the most ambitious push of its kind, GE Aviation plans to print engine injectors at an annual rate of 35,000 units by 2020.
The range of metals that are applicable to the DMLS technique is just as diverse as the various 3D printer plastic types:
- Stainless-steel: Ideal for printing out utensils, cookware and other items that could ultimately come into contact with water.
- Bronze: Can be used to make vases and other fixtures.
- Gold: Ideal for printed rings, earrings, bracelets and necklaces.
- Nickel: Suitable for the printing of coins.
- Aluminum: Ideal for thin metal objects.
- Titanium: The preferred choice for strong, solid fixtures.
In the printing process, metal is utilized in dust form. The metal dust is fired to attain its hardness. This allows printers to bypass casting and make direct use of metal dust in the formation of metal parts. Once the printing has completed, these parts can then be electro-polished and released to the market.
Metal dust is most often used to print prototypes of metal instruments, but it has also been used to produce finished, marketable products such as jewelry. Powderized metal has even been used to make medical devices.
When metal dust is used for 3D printing, the process allows for a reduced number of parts in the finished product. For example, 3D printers have produced rocket injectors that consist of just two parts, whereas a similar device welded in the traditional manner will typically consist of more than 100 individual pieces.
Carbon Fiber
Composites such as carbon fiber are used in 3D printers as a top-coat over plastic materials. The purpose is to make the plastic stronger. The combination of carbon fiber over plastic has been used in the 3D printing industry as a fast, convenient alternative to metal. In the future, 3D carbon fiber printing is expected to replace the much slower process of carbon-fiber layup.
With the use of conductive carbomorph, manufacturers can reduce the number of steps required to assemble electromechanical devices.
Graphite and Graphene
Graphene has become a popular choice for 3D printing because of its strength and conductivity. The material is ideal for device parts that need to be flexible, such as touchscreens. Graphene is also used for solar panels and building parts. Proponents of the graphene option claim it is one of the most flexible of 3D-applicable materials.
The use of graphene in printing received its largest boost through a partnership between the 3D Group and Kibaran Resources, an Australian mining company. The pure carbon, which was first discovered in 2004, has proven to be the most electrically conductive material in laboratory tests. Graphene is light yet strong, which makes it the suitable material for a range of products.
Nitinol
As a common material in medical implants, nitinol is valued in the 3D printing world for its super-elasticity. Made from a mixture of nickel and titanium, nitinol can bend to considerable degrees without breaking. Even if folded in half, the material can be restored to its original shape. As such, nitinol is one of the strongest materials with flexible qualities. For the production of medical products, nitinol allows printers to accomplish things that would otherwise be impossible.
Paper
Designs can be printed on paper with 3D technology to achieve a far more realistic prototype than a flat illustration. When a design is presented for approval, the 3D-printed model allows the presenter to convey the essence of the design with greater detail and accuracy. This makes the presentation far more compelling, as it gives a more vivid sense of the engineering realities should the design be taken to fruition.
Get 3D Plating From Sharretts Plating Company
For more than 90 years, Sharretts Plating Company has offered prompt, affordable, high-quality plating services. Operating from our 70,000-square-foot Pennsylvania production facility, we offer services to customers across North America and abroad. As one of the most globally recognized names in the plating industry, our customizers know they can trust us for plating, metal finishing and other solutions.
With each passing decade, SPC has remained at the forefront of innovation in the world of plating. Now, with 3D printing technology approaching maturity, we are determined to meet the demands of this exciting and revolutionary new form of product creation.
At SPC, our extensive background with plating applications has allowed us to apply these capabilities to 3D-printed parts. In recent years, we have applied surface finishing to 3D parts manufactured by electronics and automotive companies as well as in numerous other industries. Regardless of your industry, we can customize a process that will suit your products.
Ultimately, companies that master this technology are bound to have an edge over their competition. Browse our 3D-print plating page to learn more about the options and contact us today for a free quote.
3D Printing Materials | A wide variety of materials
Materials for 3D printing! To date, the main materials for printing on a 3D printer are PLA and ABS plastic. Both materials have long established themselves on the market and are used for printing on a 3D printer using layer-by-layer material build-up technology.
ABS (ABS) plastic is a plastic formed during the polymerization of substances such as acrylonitrile (A) with butadiene (B) and styrene (S).
PLA plastic, or biodegradable plastic as it is also called, is an aliphatic polyester with a monomer in the form of lactic acid. The materials for the production of such plastic are rapidly renewable resources - corn or sugar cane, that is, starch or cellulose.
PVA plastic. The well-known PVA glue is transferred from a dry state to a liquid of the desired consistency, then melted using special equipment and formed into PVA threads or special granules that are used for 3D printing.
An even newer material, Nylon, is resistant to a wide range of chemicals and solvents. The materials discussed above are known to everyone who is associated with the 3D technology market.
These are the most commonly used materials. But manufacturers have stepped far ahead, and are already using a wide variety of materials for printing on a 3D printer, for example, clay, resin, seaweed, and more. others
Here is a list of the most unexpected and creative 3D printing materials:
White Resin from Formlabs:
3D printing materials
3D printing equipment manufacturer Formlabs introduces a new material - White Resin ("White Resin"). The company has recently launched two new 3D printing materials, Clear Resin and Gray Resin. The main feature of the White Resin material is the striking white and opaque color of the material, as well as the exceptional smoothness of the surface of the printed object. In addition, this material is ideal for subsequent staining.
Titanium Powder for 3D Printing of Auto Parts:
British metalworking company Metalysis has released a new low cost titanium powder that is suitable for 3D printing of auto parts and parts. Until now, the most popular materials for 3D printing have been plastics, due to the high cost of producing titanium powders. But recently, Metalysis has found a new, low-cost way to produce titanium powder, which could be the most sought after in the manufacture of equipment and machinery in the aerospace, defense and automotive industries.
For the production of titanium powder, Metalysis uses rutile, which is electrolyzed directly into titanium powder. This method of obtaining a powder makes it possible to change, if necessary, the size of the powder granules, its purity, morphology and the proportion of the content of alloying elements in the composition.
Metal plastic for ColorFabb 3D printer:
Materials for 3D printing
BronzeFill and CopperFill are two new filaments from the premium Dutch manufacturer colorFabb. Their key feature is the addition of bronze and copper powder to the plastic, which gives the filament additional rigidity, as well as a pleasant metallic sheen and smoothness. To the touch, the model obtained as a result of printing will very much resemble a metal one.
Bronzefill and CopperFill can be polished to a beautiful metallic sheen just like any other hard bronze and copper items. After polishing, the visible streaks that remain after printing disappear, and the bronze or copper item begins to shine.
Bronze and copper plastic for 3d printing is ideal for metal prototyping and very durable models in industry, architecture, design and other fields.
One of the most amazing materials is graphene:
3D Printing Materials
A 3D printable material with incredible potential for applications in various fields (molecular programming, solar energy, etc.), it can change the lives of many people. In this regard, the Canadian research company Lomiko Metals Inc. announced the opening of a new special laboratory Graphene 3D Labs Inc., which will focus on the development of high-performance materials based on graphene. Information about the material: graphite or graphene is entirely composed of carbon atoms, but 1 mm of graphite contains about 3 million layers of graphene. Graphite has a three-dimensional crystal structure, while graphene is a two-dimensional crystal 1 atom thick.
3D Printer Wood Filament:
3D Printing Materials
Dutch 3D printing material company colorFabb has launched WoodFill wood filament. Wooden threads WoodFill are available in two types - Fine (Delicate) and Coarse (Rough). The main difference between these threads is the quality of processing of wood fibers. WoodFill Fine uses finely ground wood particles, WoodFill Coarse threads are thicker - based on coarsely ground wood particles. Wooden threads allow you to print beautiful and original vases, decorative elements and interior items. Finished objects are highly durable and produced in a short time. WoodFill filaments are made up of 30% pine wood fibers and 70% PLA plastic.
Seaweed 3D Printer Filament:
3D Printing Materials
Le Fabshop is the first company in the world to introduce SWF filaments - "green" filaments based on seaweed.
New materials from Proto-Pasta:
Recently, scientist Aaron Crum and mechanical engineer Dustin Crum launched the Proto-Pasta project, which developed three new materials for use in a desktop 3D printer: Carbon Fiber Reinforced PLA ( PLA reinforced with carbon fiber), High Temperature PLA (high temperature PLA) and Polycarbonate-ABS (ABS with polycarbonate alloy). Compared to all known types of plastic - ABS and PLA, the presented materials have improved performance characteristics and are affordable. Carbon Fiber Reinforced PLA is more resistant to high temperatures than regular PLA. Polycarbonate-ABS (PC-ABS) is characterized by high elasticity and bending strength.
Rubber material for stereolithography:
Materials for 3D printing
This is a rubber based material ideal for stereolithography printing, the new material has a wide color gamut, allows you to print objects in high resolution, odorless, easy to peel, available from price.
3D printing material based on silk:
3D printing materials
Another 3D printing material was created from raw silk. The raw silk has been sourced from sustainable sources and treated with epoxy. The silk-based material is flexible and highly durable, thin and light, ideal for 3D printing applications.
Polished and Raw Brass as 3D Printing Material:
3D Printing Materials
Shapeways has introduced two new materials to the world at once - Polished Brass and Raw Brass. Polished Brass is a material with a smooth, glossy bright yellow surface. Products printed with its help, then covered with 22 carat gold, are almost indistinguishable from real gold jewelry. Raw Brass is ideal for 3D printing antique or antique-style objects, and is also useful for jewelry prototyping and functional parts.
Shapeways Soft Plastic:
3D Printing Materials
Shapeways has developed a new soft plastic, Elasto Plastics, for use in the production of summer footwear. Elasto Plastics has a milky white color, the material is very flexible, has an uneven grainy surface and is quite strong.
In our online store ac5ffgxkeg.lceqo.ccwc.finefive.ru there is an excellent analogue of Elasto Plastics - this is a unique flexible plastic from a Ukrainian manufacturer - PLASTAN 9 plastic0003
The second analogue - FlexibelPolyEster (FPE) - is a rubber-like elastic plastic thread designed specifically for printing on a 3D printer
Transparent resin for a 3D printer:
3D printing materials stereolithography, according to the technology of layering transparent resin and strengthening the layers with a special laser. This resin is used to make detailed and fairly complex models.
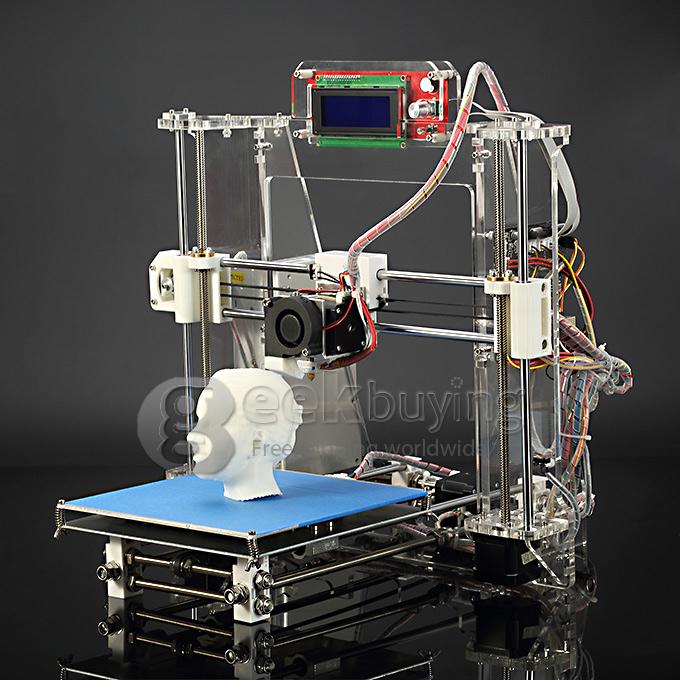
3D Printing Clay:
3D Printing Materials
Design students Tina Zidancek, Danika Rzenicnik, Urška Skáza and Maja Petek from Slovenia have developed the PrintGREEN 3D printer, which can easily print objects of any shape on a substrate, covered with chia grass. "Clay" for 3D printing was obtained by mixing - water, soil and seeds.
Back to home page
Everything you need to know about 3D printing materials
Here is a guide to help you learn about the materials used in modern industrial and home 3D printing.
When it comes to 3D printing, there is (almost) nothing impossible when it comes to materials, and researchers are constantly creating new ones.
There are certain "master" materials. The most common of these are plastics, ranging from industrial grade plastics like PEEK to very easy-to-handle plastics like PLA. Another common material is polymers, which are used in SLA printers. Composites are another category, and, as the name suggests, they are created (as if composed by a composer) by combining several materials, and the best is taken from each. The next large group of materials are metals. They are printed only by industrial machines.
In this guide, we will only consider commercially available 3D printing materials. This means that we have excluded those that cannot be bought in the store, such as biological ones.
So, it's time to start talking about what materials you can work with in 3D printing, about their applications, properties and technologies.
Which material should I choose?
Sorry, but it depends on a lot of circumstances. For example, if you need to print a food container, you will need a 3D printing material that is also food compatible, like PETG. If you want to see in advance and on a smaller scale what will then be made as a result of injection molding, then it is not necessary to immediately use expensive materials when thermoplastics such as nylon are available.
There are also additive technologies such as Binder Jetting (jet printing with a binder) or stereolithography, which greatly expanded the range of materials used in 3D printing. Many jobs that have been the domain of manual craftsmen for centuries are now automated and can be done by anyone with even the slightest understanding of 3D printing 3D modeling. Here you can point to the wide possibilities of producing full-color concepts, architectural models and visualization of art projects from paper (SDL), sandstone (Binder Jetting) and polymers (PolyJet). Thus, it can be said that 3D printing materials have led to a kind of democratization of rapid prototyping of design ideas.
Materials for 3D printing with metals have revealed forms and applications that were previously unimaginable. Nowadays, it is no longer surprising that the aerospace industry is creating complex one-piece structures that use less material than before, and are therefore lighter, resulting in lower fuel consumption for aircraft compared to traditional approaches.
PLASTIC
Most consumer goods today are made from thermoplastics, so this guide to 3D printing materials would be incomplete without them. And if we talk about widespread things, then here the plastics come out in all their glory. Designers and engineers prefer to create functional prototypes from 3D printing materials with the same or very similar properties as injection molding materials, the technology that creates the final product.
Most 3D printing thermoplastics can be handled at home in much the same way as professional solutions. The only thing is that some experts began to stare at laser sintering instead of filament fusing (FFF).
ABS
(Source: Wikipedia)
Do you remember the quality of Lego bricks? And this is ABS plastic, which is one of the most common materials for desktop 3D printing today.
It is completely inexpensive, strong and light. ABS filament comes in a variety of colors. There are some complaints about the smell that ABS emits when heated to its melting point, and if you're worried about that, there are alternatives like PLA. Because ABS is printed at temperatures between +220 and +250 °C, it is recommended to use a heated platform and in a closed working space so that the material cools in a controlled manner and does not warp. Also, 3D printing materials like ABS break down when exposed to atmospheric moisture, so you need to store them in airtight bags or containers.
Learn more about ABS: Everything you need to know about ABS filament for 3D printing
- Technologies: FDM, resin inkjet, SLA, PolyJetting
- Characteristics: Rugged, lightweight, high resolution, fairly flexible
- Applications: architectural models, concepts, assembly models, serial production
PLA
Another crowd favorite in our guide to 3D printing materials is PLA, which is made from cornstarch (although sugar cane and tapioca are also available). This is a simple material that exudes a pleasant sweetish aroma when heated, which is why many people prefer it over ABS. In addition, it can print disposable tableware and does not shrink as much when cooled compared to ABS. However, PLA is not as durable as ABS, and is afraid of heat. Therefore, ABS is better for any working structures.
(Source: thingiverse)
Don't Miss: PLA Durability, Biodegradability Experiment
PLA is sold in a variety of colors and is found in many composites that give it the appearance of, for example, wood or metal. Like ABS, PLA filament breaks down when exposed to moisture in the air, so store it in airtight bags or containers.
- Technologies: FDM, SLA, SLS
- Characteristics: easy to print, no toxic smell when printed, food compatible
- Applications: concepts, assembly models, functional models, serial production
Nylon (polyamide)
Due to its flexibility and strength, nylon has become a leader in a wide range of applications, from engineering to artistic. In some places it is simply called "white plastic". Nylon printouts have a rough surface that can be easily polished. Among FDM filaments, nylon has the strongest layer bonding, making it ideal for 3D printing parts that require high tensile strength and mechanical strength. Like other thermoplastics, nylon decomposes when exposed to ambient moisture and is best stored in airtight containers or bags.
- Technologies: FDM, SLS
- Characteristics: strong, smooth surface (after polishing), rather flexible, chemical resistant
- Applications: concepts, functional models, medical applications, instruments, visual arts
PEEK
PEEK is another 3D printing material designed for heavy duty parts. Plastics of this family perfectly tolerate mechanical stresses, temperature fluctuations and chemical influences. And that's not it. PEEK parts can be irradiated with X-rays and gamma rays. And with such reliability, this material is easily processed and produced. But here there is an ambush in the temperature, which in a 3D printer should reach +400 ° C, and it is better to entrust such work to professionals. In addition to high cost, security considerations can also be an argument for abandoning it. PEEK materials with their excellent properties are used in the most demanding applications - automotive, aerospace, chemical and medical industries. In particular, medical instruments and semiconductor components can be mentioned.
- Technologies: FDM, SLS
- Characteristics: biocompatible, very durable, heat resistant, wear resistant
- Applications: series production (automotive, aerospace, chemical and medical industries)
PET
Our next 3D printing material is PET, the material used to make plastic bottles, another alternative to ABS. Unlike ABS, PET does not stink when melted and is strong and flexible without the stench. More importantly, PET does not require heated print bed. The material gives a shiny surface, it is not hazardous to food, and this in some cases makes it a popular choice. Store PET materials for 3D printing in airtight bags or containers, the material is afraid of moisture.
- Technologies: FDM
- Characteristics: durable, food compatible, flexible, gives a smooth surface
- Applications: assembly models, mass production, functional models
PETG
PETG is a version of PET combined with glycol that has received a number of desirable properties in the 3D printing business, such as high transparency. What's more, PETG materials can be printed at lower temperatures and at higher flow rates (up to 100 mm/s), which speeds up production. PETG objects are not afraid of the weather, so they can often be found in gardens. Another commercial quality is food compatibility. Store PETG in airtight bags or containers, the material is afraid of moisture.
Don't Miss: Everything you need to know about 3D printing with PETG filament
- Technologies: FDM
- Features: Rugged, food grade, all weather, flame retardant
- Applications: concepts, assembly models, functional models, serial production
ULTEM
ULTEM is an amazing 3D printing material often found in demanding applications. On the one hand, the plastics of this family perfectly tolerate mechanical stresses, temperature fluctuations and chemical influences, but at the same time they are easy to process and obtain. The only problem is heat resistance, because the extrusion temperature in a 3D printer must reach +400 ° C, and for safety reasons, it is better not to do this work at home, but to entrust it to specialized 3D printing services. Due to its ruggedness, ULTEM is used in the most demanding applications in the automotive, aerospace, chemical and medical industries. It can be found in electrical circuits, medical instruments, and microchip sockets.
- Technologies: FDM, SLS
- Characteristics: biocompatible, very durable, heat resistant, wear resistant
- Applications: series production (automotive, aerospace, chemical and medical industries)
HIPS
HIPS has two main applications. First of all, it is often used in FDM or SLA printing as a backing material because it dissolves in a substance called limonene. With similar properties, HIPS works best in combination with ABS. But, if you decipher the name of this plastic, and HIPS is High-Impact Polystyrene, i.e. high-impact polystyrene, it becomes clear why it is also widely used for the manufacture of containers and in general where increased impact resistance is important. When printing, HIPS gives off fumes, so the room must be ventilated, especially at home. Like many other materials for 3D printing, this one is also capricious in relation to environmental conditions, so it must be stored tightly.
- Technologies: FDM, SLA
- Characteristics: soluble, soft to the touch
- Applications: assembly models, print stands, shipping containers
PVA
PVA, like HIPS, was designed as a soluble support material, but unlike all other similar materials, it dissolves in plain water. And, like most filaments, it needs to be stored in an airtight container.
- Technologies: FDM
- Characteristics: instant
- Applications: assembly models, printing supports
COMPOSITES
Composites are filaments made up of several materials and using the best qualities of each. PLA, for example, can be paired with everything from wood to metal. Other composites are targeted at specific industries or applications and are used, for example, in engineering applications.
Conductive
A relatively new addition to the filament shelf are 3D printed conductive materials that open up many interesting possibilities. Such materials can be used, for example, in touch panels or in MIDI instruments. Other uses for conductive composites are wearable electronics, computer-to-computer interfaces, Arduino boards, and more for DIY projects. Conductive filaments for 3D printing are usually based on PLA or ABS, each with its pros and cons. Conductive ABS is more durable and heat-resistant than PLA-based, but has the same odor issues as regular ABS.
- Technologies: FDM
- Features: conductive
- Applications: DIY projects
Metal-plastic filament
All "metal" filaments on the market are actually thermoplastics mixed with a small amount of metal. Such 3D printing materials allow you to create objects with the visual properties of these metals. Metal-plastic filaments are heavier than conventional thermoplastics. Popular composites for 3D printing are bronze, copper, steel, and iron. Keep in mind that these printouts require post-processing to make them look like metal. Also make sure your printer's nozzle can handle this material.
- Technologies: FDM
- Features: metal look
- Applications: fine arts
Alumide
This is a nylon variant with aluminum particles. In terms of durability and physical characteristics, it is very similar to nylon. The difference is that it is shiny, wear-resistant and has a porous surface. Objects printed with aluminium can be very precise in size, durable and long lasting. Alumide, like other similar materials for 3D printing, lends itself well to various kinds of post-processing, such as polishing and coating.
- Technologies: SLS
- Features: Rugged, heat resistant, high resolution
- Applications: DIY projects, functional prototypes, mass production
Wood
Human inquisitiveness knows no bounds, so it was only a matter of time before the engineers succeeded in adding wood fibers to plastic filament. Wood 3D prints can be processed like real ones, they can be sawn, sanded and painted. And while this kind of exotic 3D printing material is aesthetically pleasing, it doesn't have the same functional characteristics as the original. For example, you will not be able to make a chair out of it.
Interestingly, by changing the extrusion temperature, it is possible to change the shades of brown in the wood filament. 3D printing at a lower temperature produces a very light shade, while at a higher temperature it produces a solid dark brown. Therefore, if you decide to imitate growth rings in a printout, play with temperature. Depending on the brand of wood filament, the printing process may be accompanied by the smell of wood. Some manufacturers offer a wide selection of such material - birch, olive, bamboo, willow ...
- Technologies: FDM
- Characteristics: fragile
- Applications: concept models, fine arts
METALS
Our guide to 3D printing materials would be incomplete without metals. Metal 3D printing has gained particular popularity in the aerospace, automotive and medical industries for its ability to create complex designs that do not require additional welding or machining. The disadvantage of these materials is that they require a lot of experience in development and combination.
In addition, they cannot be printed at home because they require high temperatures and large, specialized printers.
Learn more about 3D printing with metals in our comprehensive article Everything you need to know about 3D printing with metals
Aluminum wide range of applications. Basically, we are talking about different alloys based on it. Aluminum elements can have thin walls and complex geometries, they tolerate physical stresses and high temperatures well, which is extremely important for low-cost prototypes, functional models, in particular for engines in the automotive and aerospace industries.
- Technologies: direct metal deposition, binder inkjet printing
- Characteristics: light, strong, heat-resistant, not afraid of corrosion
- Applications: functional models, mass production (automotive and aerospace)
Cobalt Chrome
The next material on the list is used for very serious applications. Chrome-cobalt is sometimes referred to as chromium-cobalt-molybdenum or cobalt-chromium, and sometimes simply as a superalloy. Its main use is in medical applications and in the aerospace industry, where it can be found in turbines and jet engines. It has outstanding strength, heat and corrosion resistance and is suitable for fine work.
- Technologies: direct metal laser sintering, SLM
- Characteristics: biocompatible, durable, corrosion resistant, heat resistant, wear resistant, low electrical conductivity
- Applications: series production (medical and aerospace)
Copper and Bronze
With rare exceptions, copper and bronze are used in investment casting processes and to a lesser extent in formed bed sintering. Due to their electrical conductivity, they are often used in electrical engineering. They are also very popular as art materials and with artisans.
- Technologies: investment casting, formed layer sintering, direct metal deposition
- Characteristics: electrical conductivity, wear resistance
- Applications: series production (electrical engineering), fine arts
Inconel
Inconel is a super alloy designed for the most extreme conditions. It consists mainly of nickel and chromium and is extremely heat resistant. Also resistant to extreme pressures, Inconel is indispensable in the production of aircraft black boxes and even rocket engine parts. Even more often, these features are used in solutions for the oil and chemical industries. The material is very strong and difficult to process, so direct laser sintering is preferred to obtain products of the desired shape.
- Technologies: direct metal laser sintering
- Characteristics: heat resistant, wear resistant
- Applications: petroleum, chemical and aerospace industries
Nickel
Nickel alloys are popular for 3D printing applications. Nickel alloy elements are stronger and more durable than traditional methods such as casting. This, in turn, allows engineers to create thinner parts, leading to more fuel-efficient aircraft, for example. There are many types of alloys that combine the characteristics of nickel and other materials such as monel or inconel.
- Technologies: formed bed sintering, direct metal deposition
- Features: strong, lightweight
- Applications: series production (automotive and aerospace)
Precious metals (gold, silver, platinum)
Most formed bed sintering firms can work with precious metals such as gold, silver and platinum. Here, in addition to the aesthetic qualities of materials, it is very important not to lose a single crumb of precious powder. Therefore, such parts are more often produced where a more easily controlled investment casting technology is used. Precious metals are used as materials for 3D printing in jewelry, medical solutions and electronics. Depending on the technology used, some of these materials may be used for casting.
- Technologies: Formed-bed sintering, investment casting, bonded inkjet printing
- Features: high resolution, smooth surface
- Applications: jewelry, dentistry, functional models
Stainless steel
If you're looking for cheaper metal in this guide to 3D printing materials, it's stainless steel. It is also very durable and can be used in many industrial and even artistic applications. Stainless steel alloys containing cobalt or nickel are extremely difficult to break, but have excellent elasticity and good magnetic properties. If you need a different color - please: steel can be coated, for example, with gold. The materials in question are mainly used for industrial purposes.
- Technologies: direct metal deposition, binder inkjet printing
- Characteristics: high resolution, corrosion resistance, some flexibility, strength
- Applications: tools, function models, mass production
Titanium
Pure titanium powder is often used in 3D printing. This is one of the most versatile materials - it is both durable and lightweight. They work with it using the technology of sintering in the formed layer or inkjet printing with a binder. It is most commonly found in demanding medical solutions, such as custom-made prostheses. Other uses for this material are parts and prototypes for aerospace, automotive and tool manufacturing. In addition to the price, it has another unpleasant feature - its powder explodes easily. Therefore, they print in a vacuum or in argon.
- Technologies: formed bed sintering, binder inkjet printing, direct metal deposition
- Features: biocompatible, high resolution, heat resistant, high wear resistance
- Applications: tools, function models, mass production (automotive, aerospace and medical)
CERAMIC
(Source: SONY DSC)
Ceramic is such a popular material for 3D printing in specialized services that custom-made coffee mugs, for example, have become commonplace. And with specialized extruders such as the WASP Clay 2.0, ceramics are also relevant in home 3D printing.
Clay consists of kaolinite and some other minerals, as well as a certain amount of water, which gives it plasticity. After the ceramic piece is printed, it is cured in an oven. The water evaporates and the minerals fuse together, maintaining the object's shape and strength. To make the printout shine, it is covered with glaze and placed in the oven again.
Ceramics can be printed using both conventional FDM technology and complex methods such as SLA. Beginning "potters" are offered a choice: glass, porcelain or carborundum (silicon carbide). The resulting products are distinguished by heat resistance and wear resistance and today most often act as works of art, as well as dishes and dentures.
- Technologies: FDM, binder inkjet, SLA
- Characteristics: heat resistance, wear resistance, brittleness, porous surface
- Applications: fine arts, serial production (dishes, dentistry)
WAX
Wax 3D prints are not usually the final product, but they are an important milestone in a long journey. They are relevant for very high resolution molding (0.025 mm), as well as for investment casting. They are often used in the creation of custom-made jewelry, and at a relatively low price. Another industry that uses this kind of 3D printing materials is dentistry. When creating complex structures, wax, due to its low melting point, is an excellent material for props.
- Technologies: SLA, PolyJet
- Features: high resolution, smooth surface
- Applications: mass production (jewelry, dentistry)
PAPER
With Selective Deposition Lamination (SDL) technology, good old stationery around the corner finds its niche in 3D printing. SDL objects are tree-like, full-color, and this makes them popular in architectural and other conceptual models. On the other hand, parts made from SDL are not as strong as those made from other materials and do not have the level of detail that those made from PolyJet plastic or plaster.
- Technologies: Selective Deposition Lamination
- Features: Cost effective, Recyclable, Full color
- Applications: concept models, fine arts
SANDSTONE
Sandstone as a printing medium is sometimes referred to as gypsum (in fact, gypsum is a component of natural sandstone) and is used to create impressive full-color objects in one process. To enhance the color and add strength, the printouts are covered with a protective layer of epoxy, without this the moisture will do its job and the sandstone will discolour. Objects turn out to be fragile, like porcelain, and this must be taken into account at the design stage. Bearing in mind the capriciousness of sandstone, it is mainly used in architectural models, concept prototypes and art projects.
- Technologies: FDM, binder inkjet, formed bed sintering
- Features: fragile, full color
- Applications: concept models, fine arts
(PHOTO)POLYMERS
(Photo: Nervous System)
Photopolymers are a type of liquid resin that hardens when exposed to ultraviolet (UV) electromagnetic radiation or visible light. Today, they work mainly on two technologies - SLA (stereolithography) and PolyJet. SLA uses a UV laser to project a slice of an object onto the surface of a photopolymer poured into a bath, which solidifies into the shape of the object's layer. This is repeated for all layers.
PolyJet technology takes a different approach. The printer directs a jet of resin onto a substrate, on which the resin is continuously cured by a UV lamp. SLA prints layers no thinner than 0.1 mm, and PolyJet produces up to 16 microns. And although the methods are similar and they use similar materials, the big difference lies in the methods of working with materials.
All photopolymers are sensitive to sunlight.
SLA Resins
Many SLA Resins are designed to mimic the different properties of the "traditional" materials discussed above. For example, there are materials that are compatible with wax, they are used to create impressions in investment casting. And if biocompatibility is important, then there are thermoplastics for SLA, which are very similar to PLA. Other SLA plastics can be as strong as ABS. There are even composite materials for SLA printing that have the properties of ceramics: the objects obtained on the printer can be put in an oven and then treated like ceramic.
Resins are an excellent choice for functional and conceptual models. They are especially good if you want to get a large object in a short time, while with a high level of detail. Some polymers even become hard enough for machining after quenching. In addition, high-temperature polymers are a cost-effective replacement for mold materials for low-volume moldings.
The popularity of the SLA process lies in its excellent speed and accuracy. The downside is that polymers are still significantly more expensive than everything that was mentioned here.
SLA printers are sold, you can work with them both at home and in a small office and use very interesting materials for semi-professional 3D printing.
- Technologies: SLA
- Characteristics: smooth surface, some flexibility
- Applications: concept models, functional models, fine arts, tools (prototypes)
PolyJet resins
(Source: Printshow)
Like SLA resins, PolyJet materials mimic the different properties of "traditional" 3D printing materials. Most PolyJet resins have fairly descriptive names. For example, rigur is designed for strength and sounds similar to the Latin root for hardness. It is also called "simulated propylene" for the similarity of the surface and functionality. A number of 3D printing materials are referred to as "digital ABS" because they are heat resistant and durable. Rubber-like materials are designed for non-slip surfaces and to absorb vibrations. Since there are so many PolyJet polymers, we decided to refrain from a detailed description of each of them.
It should be noted, however, that PolyJet polymers differ from SLA in that they allow obtaining the so-called. digital materials. These are mixtures of up to three 3D printing materials to obtain specific properties (strength, heat resistance, transparency, etc.) for a specific part and in a specific color range. This is a bright path to radiant prospects. While other materials described in this review allow you to create only a visual imitation of "traditional" objects, objects from PolyJet can also imitate tactile sensations, actually replacing reality.