Manufacturer of 3d printers
5 Biggest 3D Printing Companies
DDD, PRLB, and FARO lead the 5 biggest 3D printing companies list
By
Nathan Reiff
Full Bio
Nathan Reiff has been writing expert articles and news about financial topics such as investing and trading, cryptocurrency, ETFs, and alternative investments on Investopedia since 2016.
Learn about our editorial policies
Updated August 01, 2022
Reviewed by
Thomas Brock
Reviewed by Thomas Brock
Full Bio
Thomas J. Brock is a CFA and CPA with more than 20 years of experience in various areas including investing, insurance portfolio management, finance and accounting, personal investment and financial planning advice, and development of educational materials about life insurance and annuities.
Learn about our Financial Review Board
The manufacturing process known as 3D printing is one of the most promising and rapidly developing technologies with applications across a multitude of industries. 3D printing involves the additive layering of thin sheets of material that are fused together to create a physical product from a digital design. While the industry is currently hampered by relatively slow production times, advocates believe that 3D printing ultimately will have the capability to mass produce everything from medical equipment to automotive parts to airline components. Below, we look at the 5 biggest 3D printing companies by 12-month trailing (TTM) revenue. This list is limited to companies that are publicly traded in the U.S. or Canada, either directly or through ADRs. Some foreign companies may report semiannually, and so may have longer lag times. All data are from YCharts as of September 8, 2020.
- Revenue (TTM): $566.6 million
- Net Income (TTM): -$78.4 million
- Market Cap: $632.3 million
- 1-Year Trailing Total Return: -24.6%
- Exchange: New York Stock Exchange
3D Systems invented 3D printing in 1989 with the development and patenting of its stereolithography technology, which uses ultraviolet lasers to help create highly precise parts. DDD built on that by developing new technologies, including selective laser sintering, multi-jet printing, film-transfer imaging, color jet printing, direct metal printing, and plastic jet printing. 3D Systems has three business units: products, materials, and services. The products category offers 3D printers and software and includes small desktop and commercial printers that print in plastics and other materials.
- Revenue (TTM): $451.0 million
- Net Income (TTM): $58.6 million
- Market Cap: $3.9 billion
- 1-Year Trailing Total Return: 58.2%
- Exchange: New York Stock Exchange
Proto Labs was founded in 1999 with a focus on building automated solutions to develop plastic and metal parts used in the manufacturing process. The company expanded to launch an industrial-grade 3D printing service that allowed developers and engineers to move prototypes into the production process. The company's primary business services include injection molding, sheet metal fabrication and 3D printing.
- Revenue (TTM): $334.7 million
- Net Income (TTM): -$79.7 million
- Market Cap: $1.0 billion
- 1-Year Trailing Total Return: 20.6%
- Exchange: NASDAQ
FARO specializes in 3D measurement and other services for the fields of architecture, engineering, and construction. With a 40-year history, FARO' began before the advent of 3D printing. The company's products include coordinate measuring machines, laser trackers and projectors, mappers, scanners, and software. FARO also serves the aerospace, automotive, and power generation industries.
- Revenue (TTM): $205.3 million
- Net Income (TTM): -$2.7 million
- Market Cap: $1.9 billion
- 1-Year Trailing Total Return: 94.8%
- Exchange: NASDAQ
Belgian company Materialise has a 30-year history providing 3D printing solutions and related software. It provides platforms to facilitate the development of 3D printing applications in industries such as healthcare, automotive, aerospace, and art and design. Some of the company's first 3D printing activities included anatomical models in both dental and hearing aid products. Materialise also produces eyewear and automobile products.
- Revenue (TTM): $52.9 million
- Net Income (TTM): -$14.5 million
- Market Cap: $238.2 million
- 1-Year Trailing Total Return: 48.3%
- Exchange: NASDAQ
ExOne specializes in manufacturing 3D printing machines for customers across various industries. It also produces 3D printed products to specification for industrial customers. ExOne 3D printers utilize binder jetting technology, fusing powder particles of materials like metal or sand into molds, cores, and other products.
Article Sources
Investopedia requires writers to use primary sources to support their work. These include white papers, government data, original reporting, and interviews with industry experts. We also reference original research from other reputable publishers where appropriate. You can learn more about the standards we follow in producing accurate, unbiased content in our editorial policy.
YCharts. "YCharts."
3D Systems. "Our Story."
Materialise. "Timeline."
Industrial 3D Printing & Additive Manufacturing
Industrial 3D Printing & Additive Manufacturing - StratasysUSA & Canada
Select your country and region
- Americas
- English
- Español (México)
- Português (Brasil)
- EMEA
- English (United Kingdom)
- Deutsch
- Español
- Français
- italiano
- APAC
- 中文(简体)
- 日本語 (日本)
- 한국어(대한민국)
- English (India)
USA & Canada
The additive manufacturing leader
Stratasys provides complete polymer 3D printing solutions for every stage of the product life cycle, across design, manufacturing, and healthcare. Learn how Stratasys innovations help the world’s leading organizations change lives, gain business agility, and seize competitive advantage with additive manufacturing.
Learn More
We empower people to create without limits for an economical, personalized, and sustainable world.
We envision a world in which ideas become reality through 3D printing technology. The imagination of the human mind is unlimited. The limitations are physical ones that we can overcome. We are freeing engineers, manufacturers, educators, designers, doctors, and other creators from those constraints. Through the potential of additive technologies, impossible human challenges become possible.
About us
Solutions for your industry
Automotive
3D printing is helping Eckhart improve the lives of factory-floor workers.
Read More
Aerospace
INFN reduces costs by 90% with agile manufacturing.
Read More
Dental
Dynaflex use the J700 for accurate, high-output of clear aligners.
Read More
Medical
Children's Hospital Colorado turns to anatomical models to treat congenital heart disease.
Read More
Consumer Products
Kinetic Vision uses 3D printing to sell unique features of AeroFlexx liquid packaging.
Read More
Transportation
Angel Trains and DB ESG 3D-print spare train parts to reduce lead times by 94%.
Read More
Our Recycling + Returns Program is part of our commitment to Mindful Manufacturing™. It supports our users through a program that accepts used cartridges, canisters, spools, print engines and containers for return or recycle. With easy-to-follow return instructions and printable labels, we can all do our part for a more sustainable world.
Learn More
Stratasys has acquired Xaar 3D.
Stratasys has now acquired all outstanding shares of Xaar 3D, the joint venture behind SAF technology and our H Series solutions for production-scale additive manufacturing. The first 3D printer, the h450, is now available.
Learn more
Stratasys is Committed to Mindful Manufacturing™
We are proud to share our first Stratasys ESG & Sustainability Report. Our ESG strategy calls for advancing Mindful Manufacturing™, which is the thoughtful redesign of processes, parts and supply chains, utilizing 3D printing across the product lifecycle to maximize sustainability over time, all while supporting business growth.
Learn More
1960s supercars built with 21st century technology.
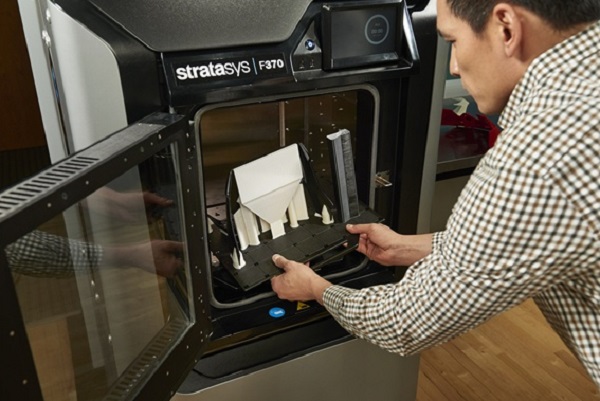
Radford Motors uses additive manufacturing from Stratasys to make their low-volume, highly customized specialty automobiles. But cars are complex. Learn how Radford uses multiple Stratasys 3D printing technologies to bring their iconic brand to life on the roads.
Watch Video
Fashion creativity unleashed.
Fashion designers are now producing one-of-a-kind garments with 3DFashion™ technology. Marvel at the complexity in design and optical illusions created by designers that are 3D printing their creations direct to textile. See unlimited creativity unleashed.
Learn More
patient care:
Digital Anatomy transforms lives.
Seattle Children’s is turning to Stratasys Digital Anatomy to plan complex pediatric surgical procedures. Synthetic digital twins of an actual patient’s anatomy, including the specific pathology in question, is transformative. Watch how it helped Nia.
View case study
Designer X
Designer XDesigner X is a high-performance professional-grade 3D printer, a tool for realizing any ideas.
The new printer combines the reliability of the legendary PICASO 3D Designer with the quality and stability of the new X platform. Designer X is always ready to go. The highest resolution (layer from 0.01 mm) and print productivity (up to 100 cm 3 / hour) make this printer unique.
Everything under control
Clogged nozzle, tangled plastic, uneven diameter, or broken bar will no longer ruin the model. Encoder system Flow Control monitors printing condition, ensuring stable results.
The Designer X encoder averages three measurements per second* (*at speed 60 mm/s, layer 0.2 mm)
This allows you to almost instantly pause printing ("Pause" mode) and automatically start the algorithm for solving the problem. If the abnormal situation is not resolved, the printer will wait for user intervention.
Plastic Feed Control
Detection of clogged or slipped plastic. Some blockages can be cleared automatically by the printer. The print result is saved (Pause mode), it can be continued after cleaning the nozzle or replacing it.
Plastic Inspection
Detects the end or break of plastic when printing. The print result is saved and can be continued after replacing the filament spool.
Print Surface Control
Detection of loose parts or surface artifacts that could damage the part (or the printer itself). The printer goes into "Pause" mode, saving time and material.
Heat sink temperature control
The maximum temperature of the heat sink is set in the profile of each plastic. If the sensor detects that the temperature is too high, the printer pauses, turns off the heating elements, and waits for the print head to cool down to operating temperature. This helps protect the printer from clogged nozzles and overheating.
Built-in plastic dryer
Printing can now be resumed even if there is a power outage. The printer will “remember” where printing stopped and will offer to resume it from the current moment. The only thing that is required of you is to make sure that during the downtime the part has not come unstuck from the printing platform.
Profile system
This system allows you to prepare a print job without reference to a specific material. ABS, PLA, Ultran or any other thermoplastic - the material is selected on the printer screen right before printing.
Alert system
Visual alert (with different backlight colors) for printer problems. A transparent understanding of the state of the device allows you to respond in a timely manner in case of any difficulties. Time is money.
First Layer Print Control
Automatic adjustment of the first layer print density according to the media.
Networking
Ability to manage all printers simultaneously from one computer over a network. Combining all X-line printers into one ecosystem.
Self-diagnosis
The printer performs self-diagnostics and detects possible problems.
Quality in detail
The quality of Designer X printing is our pride. Precision mechanics and X hardware platform help to achieve the highest results.
The minimum print layer is 10 microns. It is 10 times thinner than a human hair.
1
Double Sided Plastic Feeder
Double Sided Plastic Feeder provides maximum retention of the plastic in the feed gears. This reduces the chance of the gears breaking off the plastic in the event of a sharp increase in the thread pulling force.
2
Flow Control encoder sensor system
Consistent quality printing - synergy of various factors. Encoder system Flow Control - a set of executable algorithms and hardware solutions for detecting and correcting problems during the printing process
3
Plastic feed guide
This assembly ensures the stability of the printer with flexible materials
4
Heat sink temperature sensor
Radiator temperature sensor allows to control and prevent overheating of the print head
5
Plastic preload system
If necessary, allows you to adjust the force of the plastic pressure system in case of using very specific materials
6
take advantage of the capabilities of a single nozzle printer and print without support for parts with overhangs
6
Dual part blower system
Allows you to get the most out of a single nozzle printer and print without support for parts with overhangs
7
Multiple nozzle options
In addition to standard nozzles (0. 3 mm), Designer X0.2 can print with nozzles , 0.5 and 0.8 mm, as well as steel (for carbon-filled composites). For different tasks - different nozzles
Do you think you can print with any materials? And there is!
A new directional plastic feed system in the printhead and a wide operating temperature range of the mechanical components allow Designer X to work with a wide range of materials.
Print with any filament, including high melting engineering thermoplastics.
Another distinctive feature of the X platform is the Profile System. You no longer need to prepare a job for each plastic: the material is selected when printing is started on the printer.
Would you like to change temperature, cooling or other filament related parameters? No problem - you can do it both through Polygon X and on the 3D printer itself.
Printing with any materials is easy!
ESUN
PICASO 3D
REC
Filamentarno
Air flow control
The correct distribution of air flows is ensured by a system of two powerful and silent fans. They create the necessary microclimate for each specific material, which allows printing complex-shaped parts with high quality and stability.
PICASO 3D Ecosystem
Built-in networking features allow you to connect any number of your X-Line printers in a single interface to the updated POLYGON X.
Now you can easily manage the operation of each network printer from one PC.
Connection interfaces
Ethernet
Ease of operation with Polygon X
The new Polygon X will be equally convenient for both beginners and more advanced users. The ability to generate executable code in a few clicks is available in the quick mode, and for those who like experiments and their own settings, an advanced task preparation mode is available.
Create the history of the industry with Designer X
Industry
Aviation Engineering
Instrumentation
Robotics
Jewelry
Architecture, Design
Business
Medicine
9000Data sheet
Printing
Printing Technology
Fused Filament Fabrication [FFF]
Press area
201 x 210 mm
Press speed
to 100 cm 3 /h
Minimum layer thickness
10 micron
Plastic thread diameter
1. 75 ± 0.1 mm
Nozzle diameter
0.3 mm / (0.2-0.8 mm)
Media location
Inside the printer body
Maximum print temperature
410 °C
Maximum table temperature
150 ° C
System
Main systems
Plastic supply control
Monitoring the presence of plastic
Control of the first layer
Built -in system of profiles of the material
Auxiliary systems of drying of plastic
Printer Conday systems
Printer Auto Diagnostics
Mechanics
Outer Case
Aluminum [composite]
Frame
Steel
Print platform
aluminum, glass
Directors (ShVP)
steel
Physical characteristics / 15.6 kg
Electricity
Mains operation
220V±15% 50Hz
(option 110V±15% 60Hz)
Maximum input power
400W
Interfaces
USB [USB Flash Included], Ethernet
Media
ABS, PLA, HIPS, PVA, ULTRAN 630, ULTRAN 6130, ASA, ABS/PC, PET, PC, FRICTION, CAST, RELAX, ETERNAL, FLEX, RUBBER, SEALANT, PETG, AEROTEX, CERAMO, WAX, SBS, SBS PRO, PROTOTYPER SOFT, PRO-FLEX, TOTAL PRO, NYLON, PEEK and others
Software
Software
PICASO 3D Polygon X ™
File types
*. stl, *.plgx
Operating system
Windows XP and later
later
Order Designer X
Largest listed companies in the 3D printing sector
3D printing has been around since the late 1980s. At the end of 2018, the size of the 3D printing market, according to various estimates, reached from $9 trillion to $10 trillion. Calculations were made based on the cost of producing printers, components and 3D printing.
In the coming years, expert agencies (IMARC, Inkwood Reasearch, Marketwatch, etc.) predict a steady growth of at least 20% per year. In this scenario, by the end of 2025, the scale of the entire 3D printing segment will reach at least $ 32 trillion - 3.5 times higher than the current values.
The outlook for the sector makes it attractive to investors. Consider the largest and most stable companies in this segment, whose shares can be considered for purchase and take their rightful place in your portfolio.
1. HP Inc Capitalization: $29.3 billion
HP manufactures computers, printers, tablets and a number of other devices. The release of 3D printers is not the main specialization of the company, but HP occupies one of the leading positions in the 3D printing segment. In 2014, the company developed the Multi Jet Fusion technology, which allowed to increase productivity and reduce the cost of professional (industrial) 3D printers. The technology has been successfully applied in mass production of printers since 2016.
In 2017, HP opens the world's first 3D lab, equipped with printers in various build states and essential tools for device experimentation. The company has opened up the first opportunities to test new materials in 3D printers to increase efficiency.
In 2018, HP will open a joint manufacturing center with China's Guangdong in Guangdong, China, which is the largest such 3D printing project in Asia Pacific and Japan. The facility is equipped with ten high-tech next-generation HP Metal Jet printers to produce parts and prototypes for industrial customers.
2. Proto L abs (NYSE: PRLB). Capitalization: $2.56 billion
The company was founded in 1999 and has more than 10 production sites in seven countries. The head office is located in Minnesota. The company specializes in the production of parts for other manufacturing companies. The corporation positions itself as the fastest in the world in the production of custom prototypes and finished parts for industrial customers. In 2014, Proto Labs launched 3D printed parts.
In addition to 3D printing, the company produces CNC (Computer Numerical Control) parts, injection molding and sheet metal parts. In 2015, Proto Labs bought Alphaform (specializing in innovative 3D printing) with divisions in Germany, Finland and the UK. This allowed the company to expand its 3D printing business in Europe. To diversify its business and introduce sheet metal manufacturing, the company acquired Rapid Manufacturing in 2017 for $120 million.
3. 3 D Systems Capitalization: $1.01 billion
3D Systems was founded by inventor Chuck Hull in 1986, becoming the world's first 3D printing company. It produces 3D printers and components, including software, and also designs them. The company provides services at various stages of design, development and production of products for many large industries, including aerospace, automotive, medical, entertainment and other areas. It should be noted that the corporation also works with retail consumers. Business diversification within the 3D segment makes the company financially stable.
3D Systems is headquartered in Rock Hill, South Carolina, USA. The number of employees of the company exceeds 2600 (as of the end of 2018), which is twice as high as five years ago.
4. Stratasys ( NASDAQ: SSYS). Capitalization: $0.98 billion
The company was founded in 1989 by Scott Crump. The technology was based on the idea of creating the shape of a figure by layering after Scott decided in 1988 to make a toy for his daughter using a gun filled with glue. At 1992 Stratasys released its first 3D Modeler product.
Today, Stratasys manufactures industrial and desktop 3D printers and related accessories. The range of services includes installation, maintenance and training in working with printers. The company serves various industries by developing technologies for the production of prototypes and parts. The first public offering of Stratasys shares took place in 1994 at $5 per share and a total volume of $5.7 million. The head office is located in Minnesota.
5. Materialize Capitalization: $0.88 billion
Materialize was incorporated in Leuven, Belgium in 1990 and specializes in 3D printing services and software for 3D printers. Like other leaders in this sector, Materialize works with various major manufacturers around the world (Adidas, HP), but a significant share of the business is in cooperation with medical centers and institutions. The company's portfolio includes more than 150 medical patents. Materialize offices are located in 18 countries, including one office located in the CIS in Ukraine.
Comparison of issuers
The most valuable company among the leaders is HP, which is due to the scale and diversification of the company's business in the entire technology segment. 3D Systems, Stratasys and Materialize specialize exclusively in the 3D printing segment, while their capitalization is on the same level. Proto Labs has three businesses besides 3D printing and is in the middle of our list in terms of capitalization.
The most undervalued company in terms of EV/EBITDA is HP, but it is not correct to compare it with other issuers by this multiplier due to the differentiation of the company's products and services.