Make your 3d printer
Discover the 3D printed 3D printer!
3D Learning Hub
See all categories
Contents:
- Introduction
- Can you 3D print a 3D printer?
- How does it work?
- Why should you build your 3D printer from scratch?
- RepRap, the first self-replicating 3D printer
- 3D printed 3D printer: Improving the technology with iterations like Prusa i3
- Building the future of self-replicating 3D printers: Spatial applications
Introduction
Can you 3D print a 3D printer?
Yes, it’s possible to 3D print a 3D printer! Some self-replicating 3D printers have been created, and there are already several versions of them. Though, these types of 3D printers can’t do the whole job themselves. You have to 3D print each part of the 3D printer individually, and then assemble them yourself. Also, there are still a few parts of a 3D printer that can’t be 3D printed as electronic components. So you can 3D print a 3D printer, but not totally for now.
This also stands for plastic 3D printing only. Other types of 3D printers such as metal 3D printers, liquid resin or ceramic 3D printing are not possible to be produced in this way.
How does it work?
3D printing a 3D printer is no different than the manufacturing method of any other 3D printed object. You can actually find the pieces online, but you might need 3D modeling or CAD software to make adjustments. Your parts would be 3D printed layer by layer, the process repeats. You should assure material extrusion runs smoothly and that it produces thin layers. You should also pay attention to the surface finish, although with FDM technology it won’t be the smoothest.
Why should you build 3D printed 3D printer?
Producing your own 3D printer can actually give you a lot of room to learn. It allows you to know the project inside out and dig really deep into all the mysteries of 3D printing. You will gain a lot of knowledge, but also become an expert in case of any repairs.
3D printing gives you new design freedom. Thanks to that you can customize and personalize your own 3D printer according to your needs. No other technology gives you the opportunity to produce a fully adjustable machine to produce your parts.
RepRap, the first self-replicating 3D printer
The first self-replicating 3D printer was invented by Dr. Adrian Bowyer through the RepRap project, senior lecturer at the Department of Mechanical Engineering at the University of Bath, who started his research in 2005. His first functional machine, called the RepRap “Darwin”, with 50% of self-replicated parts, was unveiled in 2008.
Here’s a video of Adrian Bowyer assembling the RepRap project:
The 3D printed 3D printers made by the RepRap project use the Fused Deposition Modeling FDM printing technology, with plastic 3D printing materials. They are desktop 3D printers, and thus they are limited in terms of applications compared to industrial Additive Manufacturing .
Moreover, they can’t totally print themselves. As they are plastic 3D printers made of plastic parts, they can 3D print some parts of themselves, just like they could totally build other 3D printed objects. You then need to assemble them yourself and to add the components who can’t be 3D printed, like electronics or metal parts (since it’s a plastic 3D printer).
3D printed 3D printer: Improving the technology with iterations like Prusa i3
Over the years, since the RepRap project is open-source, with all the 3D models available online, there have been many iterations of this printable 3D printer from various manufacturing aficionados. The Prusa i3 is part of these improvements, and it’s now one of the most used 3D printers in the world. It was designed by Josef Prusa in 2012. Two improved versions have been released since then: the Prusa i3 MK2 in 2016, and the Prusa i3 MK2S in 2017.
Why is it such a success? Its lower cost (you can find its 3D design files for free), and the ease of construction and of modification have made it a must-have for hobbyists, but also for some professionals (even if it doesn’t replace the performance of an industrial 3D printer). It’s popular also in the education field.
Like the previous versions of the RepRap project self-replicating 3D printers, it can only 3D print some of its parts, the ones that are in plastic, but not the metal parts, nor the electronic components. Indeed, it’s not suited yet for metal 3D printiers. But it can be used to create various 3D printed objects, for instance, consumer products, jigs and fixtures or even medical devices..
Building the future of self-replicating 3D printers: Spatial applications
A self-replicating desktop 3D printer is an interesting concept, but in the end, we could 3D print 3D printers for applications way more impacting. The most interesting one is clearly spatial exploration.
Indeed, there are many scientists trying to find a way to 3D print a 3D printer directly in space. One of these machines would be sent to the moon (as a first step), and then recreate itself from lunar materials. A team of researchers from the Department of Mechanical and Aerospace Engineering at Carleton University in Ottawa is currently working on this. Their goal is to then 3D print whole lunar bases, as well as conducting in-space manufacturing of satellites.
This self-replication machine 3D prints a mix of materials such as plastic and iron, in varying proportions, depending on the part needed. The raw material needed to create a similar mixture could be extracted from the lunar regolith, a material covering almost the entire lunar surface.
One of the hardest parts to build when 3D printing a 3D printer is the motor. Alex Ellery, who is leading the project, said in June that the team was close to being capable of printing a fully functioning electric motor from a material similar to what can be sourced on the moon, which is a true revolution.
But there’s another prerequisite for a fully self-replication: electronics. Ellery explained that this one might take much longer to solve. Once it will be possible to use the exact same 3D printed 3D printers to create motors and electronics, these machines will allow the creation of any kind of manufacturing machine, like 3D printers, milling machines, drills or excavating machines. Thus, they will not just self-replicate, but also contribute to the creation of spatial manufacturing centers. And sending only one of these 3D printers to space will allow the creation of huge factories.
Apart from that, the potential applications of additive manufacturing from space are numerous. Indeed, it would also be possible to 3D print space-based solar panels on satellites turning sunlight into energy and to then send this solar power down to earth. Or even to build 3D printable space shields to protect the Earth against solar radiation to fight against global warming.
Related Topics
- Return to Top
Get the latest 3D printing news delivered right to your inbox
Subscribe to our weekly newsletter to hear about the latest 3D printing technologies, applications, materials, and software.
How to Build a 3D Printer From Scratch
If you are reading this article that means that you’ve probably decided to join the community of 3d printing enthusiasts and find out more about 3d printers, or maybe you have already got some experience in it and are ready to try to create your own 3d printer from scratch.
In this article you will find general understanding how 3D printers can be built as well as links to really useful resources where you can find more detailed information with step-by-step description.
Currently there is a big variety of 3d printers in the Internet that already assembled and are ready to print right after you unpack them from a box, of course you also need to buy a 3d printer filament for it. Do not forget that not all 3d printers can use the same filament types, so please read the instruction before you purchase it.
But for some people who love to make something new with their own hands can be more interesting to build their own 3d printer from scratch. Based on our research the 3D printing community is filled with many enthusiastic people so called DIY’ers (Do It Yourself’ers), who are fascinated with building 3d printers literally almost from scratch.
Good example of it is RepRap movement. RepRap is short for a Replicating Rapid-prototyper. In other words it is the self-replicating 3d printer. In fact most of today’s top consumer level 3D printers (picture above) are originated in one way or another from RepRap.
You can find a lot of examples on how to build a 3d printer from scratch on RepRap website, but we also want to describe some of more essential steps in order to give an overall understanding of what to expect if you really decide to make your own 3d printer.
The first step is to find and buy 3d printer DIY kit. Kits usually contain most of parts needed to assemble the printer and can be divided into two main types:
Scratch Built 3D Printer – This 3d printer DIY kit is for those who prefer to build thing from scratch, or in other words go to DIY RepRap route. Apart from some essential advantages this approach has also its disadvantages. In theory it can save you some money and since you build it from scratch you will know every nut and bolt in it by the time you can use it and successfully print your first object. Main disadvantage of this method is time. Literally it will take a lot of time to deal with all these hundreds of bolts, wires, belts and much other stuff. In the end you still need to select and purchase or build a controller board, but it depends on your skills level.
Kit Built 3D Printer – This type of kit is good if you want to save some money and at the same time not to deal with all challenges described in the 1st kit type. Many manufactures sell such kits with “easy-to-assemble” instructions included. I doubt that it will be as easy as assemble a chair from IKEA, so you still have to be mechanically inclined and able to understand basic geometry. Some of such kits contain not all parts and you may need to buy something in addition.
The next step will be to determine the design for your 3D printer. In my humble opinion most of DIY 3D printers have not very breathtaking and futuristic design in comparison with MakerBot and other brands. But it is also a matter of taste, for some people the design is not very important.
Once you have got your 3d print DIY kit and chosen the design you could go ahead and start the most fascinating and time consuming part – build your own 3d printer. Be prepared for sleepless nights and a lot of fun. Maybe you will make up something new and present your findings to RepRap community.
When the hardware part of the 3d printer is ready you also need to add a software component to it. It basically does the following things: allows you to view and alter 3d graphical objects, as well as converts the 3d images into instructions that 3d printer can understand.
Finally you can 3d print your first object! If you do not have anything to print, you can find a big variety of objects on specialized marketplaces such as Shapeways, Thingiverse and others. Before printing make sure that the object you want to 3d print has the right size and fit on the printer frame.
At the end there is a list of some links where you can find more information about how to build your own 3d printer from scratch:
- RepRap options
- 3D Printer DIY: How to Build Your Own 3D Printer from Scratch
- 3D Printing: Build Your Own 3D Printer and Print Your Own 3D Objects
- Arduino Controlled CNC / 3D Printer Hybrid
- El34 World – 3D Printer Build using 1 inch T-Slot extrusions
- CNET 3D Printer Build Week
Also watch a video from Ben Heck in which he answers on some 3d printing related questions.
Related Articles:
- What is 3d printing – 3D printing technologies overview
- What is 3D Printing?
- History of 3D Printing
- Direct and Binder 3D Printing techniques
- Photopolymerization and Sintering
- 3D Printing Process
- 3D printing revolution
- 3D Printing Materials
- How to choose a right 3D printer filament type
- 3D Printer Filament Types Overview
- Types of 3D printers or 3D printing technologies overview
- How to find and buy a right 3D printer
- History of 3D printing in one picture
- Places to download 3D printer files and files formats overview
- 3D Printing Services Overview
- You Should Know These Important 3D Printing Concepts
Homemade 3D printer v3.
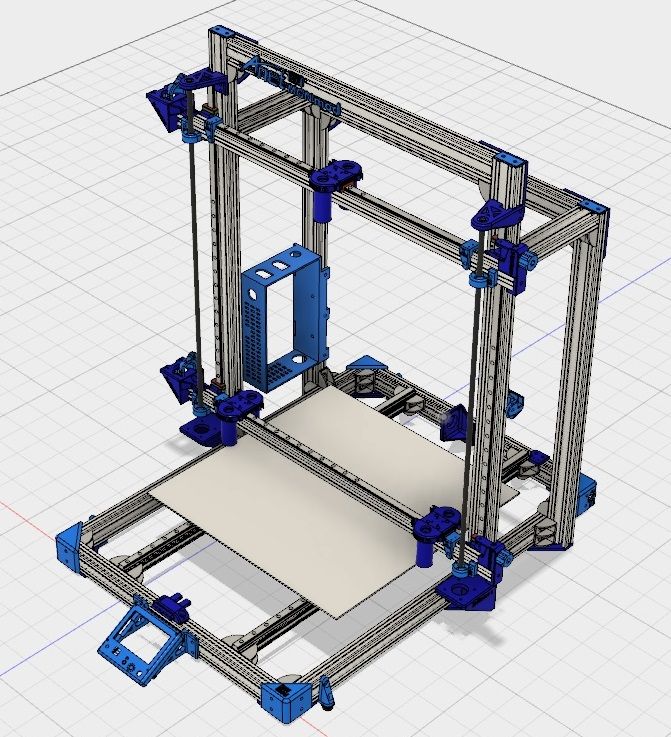
I present to your attention a homemade 3D printer. Assembled from plywood, aluminum, plastic and Arduino. This printer is unique in that its kinematics are peeped from Ultimaker, but made with quality improvements.
This is my third DIY 3D printer. The first was H-bot, the second was D-bot.
Ever since I learned about 3D printing, I wanted to make my own printer, but didn't really understand why I needed it. I bought the first part back in 2015, with thoughts that maybe someday I will make a printer. For three years, parts for the assembly imperceptibly accumulated, and in December 2017 I began the process. The first printing took place only at the end of February 2018. Since then, I have been addicted to 3D printing.
The first printer was the first pancake, i.e. lumpy. It was a good start, I gained invaluable experience and printed parts for the second printer. The second printer turned out better, but still did not suit me with its shortcomings in kinematics.
From the very beginning, I did not set myself the task of making a 3D printer for daily printing or printing on order. Purpose: to print plastic products for our own needs. Of course, I would like the print quality to be maximum and at the same time the price of the printer should not go off scale. Rail guides were immediately excluded from the estimate due to the price and difficulties of buying, besides, they are noisy. Round linear bearings like LM8UU will gnaw the guides over time, so after a long search & choice fell on 10 mm steel shafts and printed ABS plastic bushings.
For a long time I wanted to learn how to model my own crafts in 3D, but there was not enough incentive. The first printer I tried to build in AutoCAD. After the first few printed plastic parts, I realized that something else was needed. So I got the kick to learn SolidWorks. In it, he developed all subsequent models. I was very inspired by this program, because I love to draw!
The printer first modeled on a computer in 3D, taking into account all the details. Creating a virtual model helps development a lot, many nodes are optimized even before they are actually implemented.
Based on my first experience with building a printer body from chipboard, I used 10mm plywood for this version. All parts were cut on a homemade CNC machine and painted with white car paint.
Perhaps the most interesting thing about this printer is the kinematics. I have been eyeing Ultimaker for a long time. It was bribed by the fact that his axles move rigidly, without distortions. Later I learned about the shortcomings. They consist in the radial rotation of the guides, along which the bushings also move. The key to high-quality printing with such kinematics is expensive and high-quality components. It didn't suit me. My printer should be made from cheap and readily available materials. In general, it is difficult to build a 3D printer yourself when almost all the parts have to be ordered from afar.
When designing the 3d model of the new printer, I separated the rotating and guiding rollers. So linear movement along the axes is carried out along fixed shafts of 10 mm. The belt drive is organized on separate shafts with a diameter of 8 mm. The attachment points of the belts on the moving parts are made in the same plane of movement of the axles so as not to create unnecessary levers, which, by the way, contribute to the wear of the bushings.
I set the task of being able to quickly replace any part of the kinematics without having to dismantle half of the printer. Also, all 4 motors and printer electronics are moved to the back of the printer in order to be able to make a thermal camera for 3D printing and not heat what should be cold.
Z-axis made from 16 mm furniture tubes and plastic-printed sliding plates. The table moves along the axis with the help of a conventional M8 threaded stud and a coupling. Rotation from the motor is transmitted to the stud through a belt drive.
Heated table consists of two parts. The base is made of plywood, it moves along the Z axis. An aluminum frame is attached to the base with four M4 screws and springs. The frame contains a silicone mat, heater and borosilicate glass.
It took a lot of time and effort to develop the moving/print head, cool it, and blow the part. I had to measure the details for a long time so that nothing touched anywhere during the movement. For cooling, I used coolers 40 * 10 mm. They run quietly at low speeds and give good airflow. The electronics are screwed on the back wall. There is also a cooler for cooling the motor drivers. The extruder cooler and the electronics cooler are powered in series and operate at half power, so the noise from them is very low. All electronics are powered by a 12 volt 25 amp power supply. The limit switches are all mechanical, they work to open.
I filled the thermoblock of the hot end with heat-resistant silicone. Whether it works well I can’t say, but what saves fingers from burns is for sure. I have not done any other modifications with the hotend yet, everything is standard.
The table is heated by a self-made heater made of textolite, the tracks were simply scratched with a cutter under the ruler, I was tormented, it would be better to etch it. According to experience, 2.5 amperes should be spent for every 10 * 10 cm of the table, then the table heats up to 100 degrees very quickly. The heater is switched on through a conventional electromagnetic relay.
At the moment, the 3D printer does not have a finished look, everything is at the assembly and testing stage. There are already many ideas on how to improve what is already there. In general, I am very pleased with the kinematics, the location of the elements, the body, the appearance and convenience.
About shortcomings and shortcomings.
Steel shafts must be used as guides. I did not have them, so I tried to put aluminum tubes. The first print showed that the long rails were bent due to the friction of the bushings and the insufficient rigidity of the aluminum tubes. Replacing the two long rails with steel improved the situation a little, but there was still a central rail. She hasn't been replaced yet.
Planned to use aluminum tubes as 8 mm belt shafts. They used to be on sale, then disappeared. I had to use threaded studs, and this gave a runout on the pulleys, which is transmitted to the belt and, accordingly, affects the print quality.
Bushings on the moving head I tried bronze self-lubricating ones. While there is nothing special to say about these bushings, I printed only a couple of models on the printer. I bought 10 pieces of bushings, 4 of them were with backlash. I think that these bushings are designed for radial rotation, they are hardly suitable for linear movement.
Now the printer prints badly, it is 100% dependent on the bushings and guides, as well as the stud with metric thread on the Z axis. There are ideas how to bring the print geometry to the ideal, but I will talk about this when I try everything in practice.
It has not yet been possible to make the kinematics quick-release. I will take this into account in the next update. Put motors on dampers to reduce noise. Not very nicely, I managed to make the wiring with wires. I don't like the long tube from the extruder to the hot end and I don't like that it sticks out of the printer, a glass cover was planned on top. From the front, the printer will be closed by a glass door while it is not there either. Behind the electronics will be closed with a plastic cover with slots for air movement.
There are four switches on the front panel on the right: mains, general light, light near the hot end, turning off the blowing of the part. Under the table there is a panel with holes for LEDs and switches, this is a know-how for turning off heating areas that are not used during printing. It is planned to make heating from several heaters that can be switched off, this saves a lot of electricity.
I made a desktop measuring 31*22 cm and planned to put a mirror. I decided to try borosilicate glass, I ordered a smaller glass size 200 * 213 mm, so there were empty spaces on the sides of the table. Printing on a borosilicate table without glue did not work. The plastic did not want to stick to this glass at all, so I will most likely return to using a mirror.
Initially, I thought that there would be windows with glass doors on the sides of the case. The first building made of laminated chipboard had these windows, but since the printer stands between the wall and the table, there is no sense from the windows. Therefore, the walls remained intact, inside on these walls there will be a mount for a coil with plastic.
Someone noticed that there is no screen with controls. You can set up a screen. I deliberately refused it, because. I just control from my computer. I didn’t have the need to print from a USB flash drive and it’s hardly expected.
That's all for now. And what was silent, I will answer in the comments. The printer has so far printed only a couple of seals at a speed of 100 mm / sec. The daughter is incredibly happy with the cats, which means the work has been done for the good. There is a whole list of several dozen models that I really want to print in good quality. Ahead of a lot of interesting improvements, it will be interesting. All the best!
I will participate in the competition 'My 3D printer', in the nomination '3D printer assembled by my own hands' from hardware and sticks for 200 bucks.
Building a DIY 3D printer at home: recommendations from personal experience
3D printing and assembly of 3D printers is my hobby and passion. Here I will not share detailed diagrams and drawings, there are more than enough of them on specialized resources. The main goal of this material is to tell you where to start, where to dig and how to avoid mistakes in the process of assembling a home 3D printer. Perhaps one of the readers will be inspired by applied engineering achievements.
Why do you need a 3D printer? Use cases
I first came across the idea of 3D printing back in the 90s when I was watching the Star Trek series. I remember how impressed I was by the moment when the heroes of the cult series printed the things they needed during their journey right on board their starship. They printed anything: from shoes to tools. I thought it would be great someday to have such a thing too. Then it all seemed something incredible. Outside the window are the gloomy 90s, and the Nokia with a monochrome screen was the pinnacle of progress, accessible only to a select few.
Years passed, everything changed. Around 2010, the first working models of 3D printers began to appear on sale. Yesterday's fantasy has become a reality. However, the cost of such solutions, to put it mildly, discouraged. But the IT industry would not be itself without an inquisitive community, where there is an active exchange of knowledge and experience and who just let them dig into the brains and giblets of new hardware and software. So, drawings and diagrams of printers began to surface more and more often on the Web. Today, the most informative and voluminous resource on the topic of assembling 3D printers is RepRap - this is a huge knowledge base that contains detailed guides for creating a wide variety of models of these machines.
I built my first printer about five years ago. My personal motivation to build my own device is quite prosaic and based on several factors. Firstly, there was an opportunity to try to realize the old dream of having your own device, inspired by a fantasy series. The second factor is that sometimes it was necessary to repair some household items (for example, a baby stroller, car elements, household appliances and other small things), but the necessary parts could not be found. Well, the third aspect of the application is "near-working". On the printer, I make cases for various IoT devices that I assemble at home.
Agree, it is better to place your device based on Raspberry Pi or Arduino in an aesthetically pleasing "body", which is not a shame to put in an apartment or take to the office, than to organize components, for example, in a plastic bowl for food. And yes, you can print parts to build other printers :)
There are a lot of scenarios for using 3D printers. I think everyone can find something of their own.
A complex part in terms of drawing that I printed on my printer. Yes, it's just a figurine, but it has many small elements
Ready solution vs custom assembly
When a technology has been tested, its value in the market decreases markedly. The same thing happened in the world of 3D printers. If earlier a ready-made solution cost simply sky-high money, then today acquiring such a machine is more humane for the wallet, but nevertheless not the most affordable for an enthusiast. There are a number of solutions already assembled and ready for home use on the market, their price range ranges from $500-700 (not the best options) to infinity (adequate solutions start from a price tag of about $1000). Yes, there are options for $150, but we, for understandable, I hope, reasons, will not dwell on them.
In short, there are three cases to consider a finished assembly:
- when you plan to print not much and rarely;
- when print accuracy is critical;
- you need to print molds for mass production of parts.
There are several obvious advantages to self-assembly. The first and most important is cost. Buying all the necessary components will cost you a maximum of a couple of hundred dollars. In return, you will receive a complete 3D printing solution with the quality of manufactured products acceptable for domestic needs. The second advantage is that by assembling the printer yourself, you will understand the principles of its design and operation. Believe me, this knowledge will be useful to you during the operation of even an expensive ready-made solution - any 3D printer needs to be serviced regularly, and it can be difficult to do this without understanding the basics.
The main disadvantage of assembly is the need for a large amount of time. I spent about 150 hours on my first build.
What you need to assemble the printer yourself
The most important thing here is the presence of desire. As for any special skills, then, by and large, in order to assemble your first printer, the ability to solder or write code is not critical. Of course, understanding the basics of radio electronics and basic skills in the field of mechanics (that is, "straight hands") will greatly simplify the task and reduce the amount of time that needs to be spent on assembly.
Also, to start we need a mandatory set of parts:
- Extruder is the element that is directly responsible for printing, the print head.
There are many options on the market, but for a budget build, I recommend the MK8. Of the minuses: it will not be possible to print with plastics that require high temperatures, there is noticeable overheating during intensive work, which can damage the element. If the budget allows, then you can look at MK10 - all the minuses are taken into account there.
- Processor board. Well known to many Arduino Mega. I didn't notice any downsides to this solution, but you can spend a couple of dollars more and get something more powerful, with a reserve for the future.
- Control board. I'm using RAMPS 1.4 which works great with the Arduino Mega. A more expensive but more reliable board is Shield, which already combines a processor board and a control board. In modern realities, I recommend paying attention to it. In addition to it, you need to purchase at least 5 microstep stepper motor controllers, for example - A4988. And it's better to have a couple of these in stock for replacement.
- Heated table. This is the part where the printed element will be located. Heating is necessary due to the fact that most plastics will not adhere to a cold surface. For example, for printing with PLA plastic, the required surface temperature of the table is 60-80°C, for ABS - 110-130°C, and for polycarbonate it will be even higher
There are also two options for choosing a table - cheaper and more expensive. Cheaper options are essentially printed circuit boards with preheated wiring. To operate on this type of table, you will need to put borosilicate glass, which will scratch and crack during operation. Therefore, the best solution is an aluminum table. - Stepper motors. Most models, including the i2 and i3, use NEMA 17 size motors, two for the Z axis and one each for the X and Y axes. Finished extruders usually come with their own stepper motor. It is better to take powerful motors with a current in the motor winding of 1A or more, so that there is enough power to lift the extruder and print without skipping steps at high speed.
- Basic set of plastic fasteners.
- Belt and gears to drive it.
Examples of elements appearance: 1) MK8 extruder; 2) Arduino processor board; 3) RAMPS control board; 4) motor controllers; 5) aluminum heated table; 6) NEMA 17 stepper motor; 7) a set of plastic fasteners; 8) drive gears; 9) drive belt
This is a list of items you need to purchase. Hardcore users can assemble some of them themselves, but for beginners, I strongly recommend purchasing ready-made solutions.
Yes, you will also need various small things (studs, bearings, nuts, bolts, washers ...) to assemble the case. In practice, it turned out that using a standard m8 stud leads to low printing accuracy on the Z axis. I would recommend immediately replacing it with a trapezoid of the same size.
M8 trapezoid stud for the Z axis, the use of which will save you a lot of time and nerves. Available for order on all major online platforms
You also need to purchase customized plastic parts for the X axis, such as these from the MendelMax retrofit kit.
Most parts available at your local hardware store. On RepRap you can find a complete list of necessary little things with all sizes and patterns. The kit you need will depend on the choice of platform (we'll talk about platforms later).
What's the price
Before delving into some aspects of the assembly, let's figure out how much such entertainment will cost for your wallet. Below is a list of parts required for purchase with an average price.
Platform selection
To assemble printers, the community has already developed a number of different platforms - the most optimal case designs and the location of the main elements, so you do not have to reinvent the wheel.
i2 and i3 are key platforms for self-assembly printer enclosures. There are also many modifications of them with various improvements, but for beginners, these two classic platforms should be considered, since they do not require special skills and fine-tuning.
Actually, illustration of platforms: 1) i2 platform; 2) i3 platform
On the plus side of i2: it has a more reliable and stable design, although it is a little more difficult to assemble; more opportunities for further customization.
The i3 variant requires more special plastic parts to be purchased separately and has a slow print speed. However, it is easier to assemble and maintain, and has a more aesthetically pleasing appearance. You will have to pay for simplicity with the quality of printed parts - the body has less stability than i2, which can affect print accuracy.
Personally, I started my experiments in assembling printers from the i2 platform. She will be discussed further.
Assembly steps, challenges and improvements
In this block, I will only touch on the key assembly steps using the i2 platform as an example. Full step by step instructions can be found here.
The general scheme of all the main components looks something like this. There is nothing particularly complicated here:
I also recommend adding a display to your design. Yes, you can easily do without this element when performing operations on a PC, but it will be much more convenient to work with the printer this way.
Understanding how all components will be connected, let's move on to the mechanical part, where we have two main elements - a frame and a coordinate machine.
Assembling the frame
Detailed frame assembly instructions are available on RepRap. Of the important nuances - you will need a set of plastic parts (I already talked about this above, but I'd better repeat it), which you can either purchase separately or ask your comrades who already have a 3D printer to print.
The frame of the i2 is quite stable thanks to its trapezoid shape.
This is how the frame looks like with parts already partially installed. For greater rigidity, I reinforced the structure with plywood sheets
Coordinate machine
An extruder is attached to this part. The stepper motors shown in the diagram above are responsible for its movement. After installation, calibration is required along all major axes.
Important - you will need to purchase (or make your own) a carriage for moving the extruder and a mount for the drive belt. Drive belt I recommend GT2.
The carriage printed by the printer from the previous picture after it has been assembled. The part already has LM8UU bearings for guides and belt mount (top)
Calibration and adjustment
So, we completed the assembly process (as I said, it took me 150 hours) - the frame was assembled, the machine was installed. Now another important step is the calibration of this very machine and extruder. Here, too, there are small subtleties.
Setting up the machine
I recommend calibrating the machine with an electronic caliper. Do not be stingy with its purchase - you will save a lot of time and nerves in the process.
The screenshot below shows the correct constants for the Marlin firmware, which must be adjusted to set the correct number of steps per unit of measure. We calculate the coefficient, multiply it, substitute it into the firmware, and then upload it to the board.
Marlin 9 firmware constants0082
For high-quality calibration, I recommend relying on larger numbers in measurements - take not 1-1.5 cm, but about 10. So the error will be more noticeable, and it will become easier to correct it.
Calibrating the extruder
When the frame is assembled, the machine is calibrated, we start setting up the extruder. Here, too, everything is not so simple. The main task of this operation is to correctly adjust the supply of plastic.
If underfeeding, the printed test item will have noticeable gaps, like test die 1. Conversely, the result will look bloated if plastic is overfed (dice 2)
Getting Started Printing
It remains for us to run some CAD or download ready-made .stl, which describe the structure of the printed material. Next, this structure needs to be converted into a set of commands understandable to our printer. For this I use the Slicer program. It also needs to be set up correctly - specify the temperature, the size of the extruder nozzle. After that, the data can be sent to the printer.
Slicer interface
As a raw material for printing, I recommend starting with regular ABS plastic - it is quite strong, products made from it are durable, and it does not require high temperatures to work with. For comfortable printing with ABS plastic, the table must be heated to a temperature of 110-130 ° C, and the extruder nozzle - within 230-260 ° C.
Some important details. Before printing, calibrate the machine along the Z axis. The extruder nozzle should be approximately half a millimeter from the table and ride along it without distortion. For this calibration, a regular sheet of A4 paper inserted between the nozzle and the surface of the heated table is best suited. If the sheet can be moved with little effort, the calibration is correct.
Another thing to keep in mind is the surface treatment of the heated table. Usually, before printing, the surface of the table is covered with something that hot plastic sticks to well. For ABS plastic, this can be, for example, Kapton tape. The disadvantage of adhesive tape is the need to re-glue it after several printing cycles. In addition, you will have to literally tear off the adhering part from it. All this, believe me, takes a lot of time. Therefore, if it is possible to avoid this fuss, it is better to avoid it.
An alternative option that I use instead of scotch tape is to apply several layers of ordinary light beer, followed by heating the table to 80-100 ° C until the surface is completely dry and re-applying 7-12 layers. It is necessary to apply the liquid with a cloth moistened with a drink. Among the advantages of this solution: ABS plastic separates from the table on its own when it cools down to about 50 ° C and is removed without effort, the table does not have to be peeled off, and one bottle of beer will last you for several months (if you use the drink only for technical purposes :)).
After we have collected and configured everything, we can start printing. If you have an LCD screen, then the file can be transferred for printing using a regular SD card.
The first results may have bumps and other artifacts - do not worry, this is a normal process of "grinding" the printer elements, which will end after a few print cycles.
Tips to make life easier (and sometimes save money)
In addition to the small recommendations given in the text above, in this section I will also give a short list of tips that will greatly simplify the operation of a 3D printer and the life of its owner.
- Do not experiment with nozzles. If you plan to immediately print from materials that require high temperatures, then it is better to immediately take the MK10 extruder. On MK8, you can "hang" special nozzles that support high-temperature conditions. But such modifications often cause difficulties and require special experience.
It is better to avoid this fuss on the shore by simply installing the right extruder for you.
- Add starter relay for heated table. Improving the power supply system of this important part for printing with a starter relay will help solve the known problem of RAMP 1.4 - overheating of the transistors that control the power of the table, which can lead to failure of the board. I made this upgrade after having to throw away a few RAMPS 1.4s.
- Select the correct media diameter for printing. I recommend using 1.75mm plastic for MK8 and MK10. If we take plastic, for example, 3 mm, then the extruder simply does not have enough strength to push it at an acceptable speed - everything will be printed much longer, and the quality will drop. ABS plastic is ideal for MK8, MK10 will be able to produce products from polycarbonate.
- Use only new and precise X and Y guides. Print quality will be affected. It is difficult to count on good quality with bent or deformed guides along the axes.
- Take care of cooling. During my experiments with various extruders, the MK10 showed the best results - it prints quite accurately and quickly. The MK10 can also print plastics that require a higher print temperature than ABS, such as polycarbonate. Although it is not as prone to overheating as its younger brother MK8, I still recommend taking care of its cooling by adding a cooler to your design. It must be permanently enabled, this option can be configured in Slicer. You can also add coolers to keep the stepper motors at an acceptable temperature, however, make sure that their air flows do not fall on the printed part, as this can lead to its deformation due to too rapid cooling.
- Consider heat retention. Yes, on the one hand, we are struggling with overheating of the elements. On the other hand, a uniform temperature around the printer will contribute to high-quality printing (the plastic will be more pliable). To achieve a uniform temperature, you can put our printer, for example, in a cardboard box.
The main thing is to connect and configure the coolers before that, as described above.
- Consider insulating your desk. Heated table heats up to high temperatures. And if part of this heat leaves properly, heating the printed part, then the second part (from below) just goes down. To concentrate the heat from the table onto the part, you can perform an operation to insulate it. To do this, I simply attach a cork mouse pad to its bottom using stationery clips.
Pins
I am sure that during the assembly process you will encounter a number of difficulties specific to your project. Neither this text nor even the most detailed guides will insure against this.
As I wrote in the introductory part, the above does not claim the status of a detailed assembly manual. It is almost impossible to describe all the stages and their subtleties within the framework of one such text. First of all, this is an overview material that will help you prepare for the assembly process (both mentally and financially), understand whether you personally need to bother with self-assembly - or give up on everything and buy a ready-made solution.