Lockheed 3d printing
Ctrl + P: 3D Printing an F-35 Cockpit
Need a cockpit? Just hit Ctrl + P. Well, it’s not exactly that easy but it’s what the F-35 Training & Logistics team had in mind when they started working on how to 3D print the cockpit for the F-35 Full Mission Simulator (FMS).
After years of hard work, the team recently celebrated the shipment of the first two 3D printed cockpits, that were delivered to MCAS Cherry Point in 2022. Printing an additive cockpit is an intricate process that is performed at the Orlando, Florida, Rotary and Mission Systems site. The entire process takes about two months, but you can watch the print in less than a minute in the below time-lapse video.
“It’s a good representation of the capability of additive manufacturing and what the team can do when all of the functions work together.
It also paves the way for any future large additive programs. With F-35 and F-16, we have a good baseline for what our capabilities are, and now we are diving deep into understanding how we can eliminate defects, streamline processes and increase efficiency.”
Jared Stewart, Hardware Engineer Staff
The 3D printed cockpit is a key tenet of Digital Transformation. When the team started this initiative, they had to look at this extremely complex part and thoroughly redesign it with a focus on manufacturability so the benefits could be realized across the product lifecycle – quality, cost and schedule. This technology is now being leveraged on other platforms and will become the benchmark for training devices.
In addition, the team utilized digital twin technology to visualize the production floor and understand where the 3D printed cockpits can be inserted across the line. Given the decrease in time needed to produce the physical cockpit, advanced planning is needed to manage the flow of orders and deliver on time for customers.
“It’s great being part of a team that helps to get these resources out to the military and improving the overall cost and turnaround times for producibility. Now we will focus on leaning out the process, increasing the throughput and making it more efficient.”
Michael Scheidker, Senior Hardware Engineer
This effort can reduce the total lead time to obtain conventional parts by 75%. It also reduces the total part count of conventional metal parts by 70%. This significantly simplifies the manufacturability of the FMS and allows the team to rapidly increase the speed at which simulators can be delivered to the warfighter.
Production of the 3D printed FMS cockpit continues with deliveries having started in October 2022. The next delivery contract includes 26 FMS products with 14 of those being 3D printed cockpits.
F-35 Lightning IIF-35 Training Systems
First published on January 25, 2023
- Capabilities
- Products
- Employees
- International
- Investors
- Suppliers
- Contact Us
- Media Relations
- Multimedia
- Social Media
- Vulnerability Disclosures
- Careers
- Community
- Leadership
- Newsroom
- Sustainability
- Who We Are
How Lockheed Martin Is Using 3D Printing To Build The Next Starship
3D printing has come a long way in a short space of time, transforming from a scientific curiosity to a legitimate manufacturing tool with almost limitless potential.
3D printing takes many forms, but all involve a computer-guided process of joining or solidifying material to create a 3D object. Originally only suitable for minimally functional or purely aesthetic objects such as prototypes, 3D printing technology is now capable of building complex machines with working parts - even firearms.
When used as an industrial production tool, 3D printing is usually referred to as additive manufacturing, and Lockheed Martin is leading the way with a dedicated 3D printing manufacturing center.
Lockheed Martin
Global safety science company UL has announced that Lockheed Martin's dedicated Additive Design and Manufacturing Center (ADMC) in California has become the first organization to be certified to UL 3400. This accreditation demonstrates that Lockheed Martin has an evidence-based set of safety guidelines which address the various hazards associated with additive manufacturing (AM) facilities.
"Employers, employees, local regulators as well as insurance companies who have to underwrite additive manufacturing facilities, were not fully aware of the inherent material and technology risks," said UL's Additive Manufacturing Lead Development Engineer, Balu V. Nair. "Safety is designed rather than built. Not a single standard or statutory guideline was available that specifically focused on additive manufacturing. Other standards and guidelines were developed for conventional manufacturing processes. We decided to address this industry need by developing a set of guidelines with exclusive focus on additive manufacturing."
The Outline of Investigation for Additive Manufacturing Facility Safety Management which makes up the UL 3400 was published last year, and the Lockheed Martin facility marks the first of its kind to meet the standards laid out within. The UL 3400 takes into consideration the safety standards of materials, equipment, and the facility itself. It also requires that all additive manufacturing machinery within the facility has been third-party accredited and that extensive and consistent workforce training be carried out regularly.
UL 3400 draws from existing safety standard frameworks laid out by the Occupational Safety and Health Administration (OSHA), the National Fire Protection Association (NFPA), UL, and ASTM International to name but a few.
Additive Manufacturing
The main purpose of the ADMC is to help bridge the gap between research and manufacturing, with additive manufacturing allowing concepts to be tested almost immediately and with relatively little expense. And the ADMC is putting this amazing technology to work building components for humanity's continued exploration of space.
Lockheed Martin's ADMC was used to create the Remote Interface Unit, an aluminum box which houses avionic circuits, which is to be installed on the latest US Air Force Advanced Extremely High-Frequency communications satellite - set to launch into space later in 2019.
The ADMC also recently completed quality testing on its biggest printed part to date - a dome which caps a spacecraft's high-pressure fuel tank. The fuel tanks are constructed by welding two of the 3D printed domes onto a traditionally manufactured titanium cylinder. Once the final approval is complete, Lockheed Martin will offer its aerospace clients the tanks as a standard option on its LM 2100 satellite bus - designed for 2,300 to 6,500-kilogram spacecraft.
"As more people get into the industry and companies invest more, the technology keeps getting better and better," said Engineering Senior Manager for Lockheed Martin Space Systems, Servando Cuellar. "There's a lot of new material innovation happening within industry but also here within Lockheed Martin. It's almost like computers - every three to five years, there is a new machine that's bigger and better. You must continue to invest in additive manufacturing equipment because otherwise you're going to fall behind. Ten or twenty years from now, I don't think engineers are going to be designing to machine stuff, they're going to design to print."
Final Thoughts
3D printing is presenting a great opportunity to companies involved in the manufacturing industry, empowering them to create components and parts quicker and more consistently than ever before. However, one of the most exciting applications is in closing the gap between research and manufacturing - especially in the field of aerospace engineering - such as is being demonstrated at Lockheed Martin's ADMC.
You can hear Lockheed Martin's Vice President of Digital Transformation, Jeffrey J. Wilcox speak at Connected Manufacturing Forum 2019, taking place in July at the Hilton Austin, Austin, TX.
Download the agenda today for more information and insights.
Best 3D Printing STL Files Lockheed・Cults
Madagscar 2 Plane (Version 3.0)
Free
X-33 Venture Star
Free
Lockheed C-130J Super Hercules
3 €
Lockheed SR-71 Blackbird
3 €
Lockheed P-3 Orion
3 €
Lockheed F-117 Nighthawk
3 €
Lockheed F-104 Starfighter
3 €
Lockheed C-5 Galaxy
3 €
F-22 Raptor
2 €
SR-71 Blackbird
1. 80 €
Boeing AC-130U
2.50 €
F-16
2.50 €
F-35
2.50 €
Lockheed P-38 Lightning
22 €
Lockheed Martin RQ-170 Sentinel
22 €
Lockheed Martin f-16 fighting falcon
12 €
Lockheed P-38 Lightning
13 €
F117 with Separated Halves
Free
Stealth-Themed Display Stand for F-117 Nighthawk
Free
Lockheed Martin Super Constellation
Free
Dh206 De Havilland Comet 1
Free
C47 Skytrain / DC3
Free
Desk Coin - Scotty-G Maker
Free
F22A Raptor
Free
General Electric F404
Free
General Electric F414
Free
F117 Nighthawk
Free
Simple P-80 Shooting Star (mod.
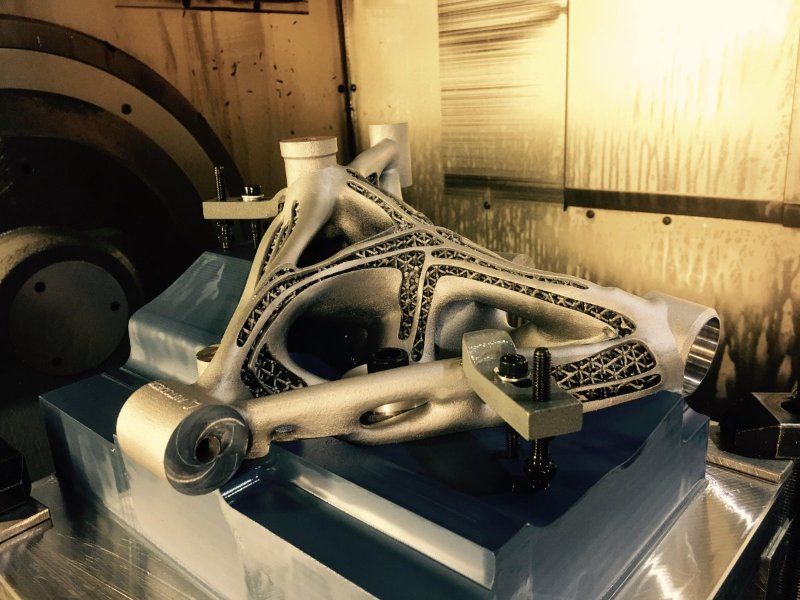
Free
Atlas IIAS
Free
1/60 Modular Atlas V
10.81 €
Lockheed SR-71 Blackbird
Free
X-33 / Venturestar (Spaceplane)
Free
Lockheed P38E Lightning
Free
Lockheed U2-R Dragon Lady
Free
Lockheed L9 Orion 1932 (1/72)
Free
Lockheed Vega 1932 (Amelia Earhart) (1/72)
Free
Lochkeed Martin C5 Galaxy
3.33 €
Lockheed SR-71 Blackbird
1 €
Lockheed U-2B/C Spyplane
1. 20 €
F-104 Starfighter pack
1,50 €
Lockheed C-130H Hercules
1,50 €
1/20 SCALE U-2R RC Model Test Files and Manual
Free
1/20 Scale U-2R RC Model Plane (1627mm Wingspan)
21.27 €
Lockheed SR-71 3D model
Free
Hercules c 130
7.55 €
Lockheed Martin patents 3D diamond printing / Habr
Products of any shape! The author wanted to insert a diamond tyrannosaurus rex, but Google did not find a suitable picture. Photo Source: Crystal Fox
Lockheed Martin, one of the world's largest aerospace manufacturers, filed for a patent on April 4 for a new 3D printing technology, artificial diamond 3D printing.
Material from 3dprintingindustry.com translated for you Top 3D Shop .
In a patent application, inventor David G. Findlay describes a new 3D printing process that uses a ceramic-bonding polymer and nanoparticle filler to create synthetic diamond objects in almost any shape imaginable.
About technology
David G. Findley:
“The method consists of layering layers of ceramic powder and bonding them with pre-dissolved polymer.
After layering is completed, the object is heated to at least the polymer decomposition temperature, which is lower than the powder sintering temperature.” Image: US Patent and Trademark Office, Lockheed Martin jewelers who can create diamonds of almost any shape.
About Lockheed Martin
Quiet supersonic vehicle for NASA. Source: Lockheed Martin
Headquartered in Bethesda, Maryland, USA, Lockheed Martin is a global security and aerospace company with approximately 98,000 employees worldwide. The company is engaged in research, design, development, production, integration and support of modern technological systems, products and services.
US Air Force F-35 fighter. Source: nationalinterest.org
What else do 3D printing and diamonds have in common? to increase the production of parts for diamond industry equipment.
The company used to cover its 3D printing needs with third parties, but the addition of two machines means round-the-clock production at its diamond research center in Maidenhead, UK.
3D printers are being used to create automated methods for checking and sorting diamonds, and to prototype parts for new equipment.
De Beers Technologies Senior Mechanical Engineer Andrew Portsmouth:
“Whenever I have an idea, my first thought is 'will it work'? Now we can print a prototype overnight, test it the next day, find out the features and flaws, make changes and print the corrected one by the next morning to repeat all the tests.
Learn more