Large 3d metal printer
Largest Metal 3D Printer Available | Industrial 3D Printing
With a maximum work envelope of 19' x 4' x 4' x 8’ (L x W x H x D, or round parts up to 96” diameter), the EBAM® 300 Series by Sciaky offers the largest build platform of any metal 3d printer commercially available.
Designed to additively manufacture large-scale parts and prototypes from high-value metals like titanium, tantalum, Inconel, niobium, and other alloys, the EBAM300 is the only 3D printer on the market that has produced a metal structure exceeding 10 feet in length.
Beyond size, the EBAM 300 is also one of the fastest industrial 3D printers commercially available with a deposition rate ranging from 7 to 20 lbs. per hour. It produced a 10-foot-long titanium aircraft structure in 48 hours at a rate of approximately 15 lbs. of metal per hour. In general, forgings that used to take 6-12 months to complete can be completed in 2 days with the EBAM 300.
This Electron Beam Additive Manufacturing (EBAM) system also provides an extremely high degree of control over part geometry and material composition because of its patented IRISS Closed-Loop Control Technology. Savings on raw materials—often precious metals—can be huge with EBAM (up to 80% for large-scale parts) because of the substantial reduction of material waste.
The EBAM 300 is used to create, improve, and repair next-generation end-use technology in the aerospace and defense industry, energy industry, metals industry, and many other verticals. It is a full-scale means of production for corporations and institutions in need of a system that can do more than build flimsy prototypes and/or headline-grabbing objects without real function.
This marks a sharp contrast between Sciaky and other 3D printing companies that say they sell “the largest 3D printer in the world” because it’s a marketable proposition.
The truth is: while there are indeed 3D printing systems that can print entire buildings, houses, car replicas, bikes, statues, etc., generally, the bigger the printer, the weaker the business case.
For example, if you run a Google search for “who makes the largest 3d printer?” you will find that most mega-scale 3D printers are a) not commercially available and b) are only useful to a small consortium of individuals and even fewer real-life applications. Why? In a nutshell, huge parts made out of sand, plastics, and other particle materials aren’t practical for most companies.
That’s not the case with Sciaky. We may not be able to say that we make the biggest 3d printer on the planet, but we do make the world’s largest 3d printer that is fit for the industrial/commercial production of functional metal parts.
Here’s how the EBAM 300 Series compares to some of the other largest 3D printers on the market:
Machine Name |
Type of Process |
Type of Materials
|
Build Envelope Size (L x W x H)
|
Chamber Dimensions
|
EBAM 300 Series by Sciaky |
Electron Beam Additive Manufacturing
|
Metals |
240” x 55” x 54” |
300” x 108” x 132” |
VX4000 by Voxeljet |
Sand Casting |
Particle Materials |
157. |
767.7” x 275.6” x 149.6” |
Objet 1000 by Stratasys |
Polyjet |
Plastics |
39.3” x 31.4” x 19.6” |
110.3” × 70.9” × 70.9”
|
Lens 850-R by Optomec
|
Laser |
Metals |
35.4” x 59” x 35.4” |
118” x 118” x 118” |
Projet 5000 by3D Systems |
Multijet Printing Process |
Plastics |
21” x 15” x 11. |
60.3” x 35.7” x 57.1” |
M400 by EOS
|
Laser |
Metals |
15.8” x 15.8” x 15.8” |
N/A |
Arcam Q20 by Arcam |
Electron Beam Melting |
Metals |
Apx. 13.7”×15” (LxW) |
90.5” x 51.2” x 102.4” |
To learn more about 3D printing large metal parts with Sciaky’s EBAM process, call us at 877-450-2518.
SLM Solutions to develop “world's largest” metal 3D printer for the US Air Force
0Shares
Laser Powder Bed Fusion (LPBF) system manufacturer SLM Solutions has announced plans to develop the “world’s largest” metal 3D printer on behalf of the US Air Force (USAF).
Having been subcontracted by the Concurrent Technologies Corporation (CTC), SLM Solutions now aims to build a version of its NXG XII 600 3D printer with a 1.5-meter Z-axis. Through developing what will be called the ‘NXG XIIE,’ the CTC says it could be possible to “overcome the limits of current additive manufacturing equipment,” when it comes to creating long parts with critical defense applications.
“Partnering with the CTC, a premier research and development company, will help us achieve the goal of creating a new AM capability,” said SLM Solutions CEO Sam O’Leary. “We look forward to collaborating on an AM machine that will work much faster than existing equipment and feature the largest build envelope in the industry by far. ”
SLM Solutions in large-format AM
In subcontracting its USAF project to SLM Solutions, the CTC has chosen to partner with a Selective Laser Melting specialist that’s experienced in developing its own large volume machines. At Formnext Connect, for example, SLM Solutions unveiled the NXG XII 600, a 600 x 600 x 600 mm capacity system, which can be fitted with up to 12 lasers, enabling it to address demanding aerospace use cases.
Alongside the NXG XII 600, the company also markets its SLM 125, SLM 280, SLM 500 and SLM 800 3D printers, the larger of which continue to find adoption in this area. Earlier this year, Rolls Royce ordered two more SLM 500s, machines it uses to 3D print combustor tiles for Pearl 10X engines, power units which are set to fly with the Falcon 10X private jet from 2025.
In April 2021, SLM Solutions revealed that it had worked with Safran Landing Systems as well, to 3D print lightweight landing gear parts. Using an SLM 800, the firms were able to fabricate a large-format nose piece in a way that accelerated the qualification process, while enabling the rapid iteration of different prototypes to identify the ideal design.
Despite Nikon launching an SLM Solutions takeover bid just weeks ago, in a deal that could soon see the firm change ownership, it now appears its plans haven’t changed, and it aims to continue pushing the boundaries of PBF in aerospace.
SLM Solutions’ SLM 800 3D printer was used to produce a novel piece of landing gear in April 2021. Photo via SLM Solutions.A $5.2M US Air Force project
SLM Solutions has got involved in the USAF’s latest 3D printing initiative thanks to the CTC, which having won a $5.2 million contract to develop a new machine by the US Air Force Research Laboratory (AFRL), has tasked the firm with developing it.
A specialist in scientific R&D, the CTC is a non-profit with close ties to the Enterprise Ventures Corporation, an organization that works to help start-ups transition advanced technologies to market. Between them, the companies have over 400,000 square feet of office, lab and high-bay space, as well as cutting-edge product design, development, testing, prototyping and production facilities.
As a result, the pair have the capacity to meet US Department of Defense requirements on the fabrication of large-scale, first-of-a-kind prototype structures, and they often deploy this in aid of US government, private industry and public R&D programs. Moving forwards, having gained AFRL funding, the CTC plans to utilize these facilities alongside SLM Solutions, to develop the “world’s largest AM machine.”
“We are excited to play a role in this ground-breaking AM advancement,” added Edward J. Sheehan Jr, CTC President and CEO. “The technical work we are performing for this project includes elements of CTC’s full-service portfolio of AM capabilities including design, testing, post-processing, machining, and qualification.”
GE’s Atlas 3D printer is the current largest LPBF system to date.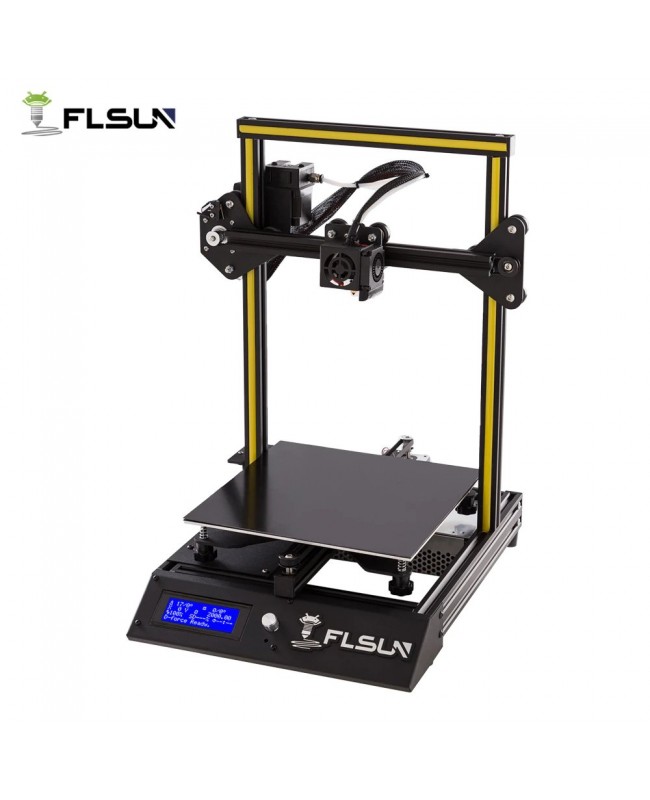
Will it really be the world’s largest?
When used to describe 3D printers in general, the CTC’s claims of working on the “world’s largest” could well be disputed. Being developed for the US Army, MELD and Ingersoll Machine Tools’ metal 3D printer is set to be large enough to create huge military vehicle parts. Sciaky also unveiled the world’s largest electron beam 3D printer earlier this year, which can create up to six-meter-long aerostructures.
Compared to other LPBF systems, on the other hand, the company’s claim appears slightly closer to the mark. With a 1,000 mm³ build volume, GE’s ATLAS 3D printer remains the world’s biggest LPBF machine, and despite being capable of producing large-format aerospace, automotive and oil & gas parts, its capacity could soon be superseded by that of SLM Solutions’ and the CTC’s system.
Once ready, the machine could also address what is a growing market for huge LPBF-3D printed rocket components. Velo3D, for example, launched its largest unit to date in June 2022, the SAPPHIRE XC 1MZ 3D printer. The firm supplies leading aerospace clients like SpaceX and Launcher, previously 3D printing E-2 rocket engine parts for the latter, thus the system’s size may well reflect demand.
To stay up to date with the latest 3D printing news, don’t forget to subscribe to the 3D Printing Industry newsletter or follow us on Twitter or liking our page on Facebook.
While you’re here, why not subscribe to our Youtube channel? featuring discussion, debriefs, video shorts and webinar replays.
Are you looking for a job in the additive manufacturing industry? Visit 3D Printing Jobs for a selection of roles in the industry.
Featured image shows SLM Solutions’ NXG XII 600 3D printer. Image via SLM Solutions.
Tags Concurrent Technologies Corporation Edward J. Sheehan Jr. Enterprise Ventures Corporation GE Ingersoll Machine Tools Launcher MELD NXG XII 600 NXG XIIE Safran Landing Systems Sam O’Leary SLM Solutions SpaceX US Air Force US Air Force Research Laboratory US Army US Department of Defense Velo3D
Paul Hanaphy
Paul is a history and journalism graduate with a passion for finding the latest scoop in technology news.
Laser 3D printer for metal, industrial 3D printers of a new generation, an overview of a printer that prints metal
Jewelry industry
Medicine
3D printers
Science and education
Author: Semyon Popadyuk:
3 9
Top 7 Benefits of Sharebot MetalONE | Applications and Consumables | How MetalONE was created | Key Features of the 3D Printer
Metal 3D printing is the most complex of additive technologies, but the path to it may be easier than you think. Freedom of design, the ability to optimize the design, reduce the weight of the product and the number of elements in the assembly, the use of materials with unique properties - all these advantages of the technology are invaluable for experimental and research work, the ultimate goal of which is to quickly and efficiently create new high-tech products (or upgrade existing ones), taking production capabilities to the next level. nine0003
The integration of metal 3D printers into the production process is associated with considerable difficulties. A metal printer is an installation that requires a large investment, a special facility, strict operating conditions, additional equipment, and a highly skilled operator.
However, recent trends suggest that metal printing can become, as they say, “closer to the people”. When we visited the largest Formnext exhibition in Frankfurt am Main in 2019, we noted the appearance of compact metal 3D printers. These machines have a simplified functionality and are focused primarily on the scientific and educational sphere and small and medium-sized businesses. nine0003
One of the most attractive installations in this category in terms of price and quality is called MetalONE and is based on the direct metal laser sintering (DMLS) method. This is a new product of the Italian company Sharebot, which has a solid experience in the development of several 3D printing technologies. The printer is designed for research, product testing and manufacturing of small and medium-sized parts.
Can 3D printing help you optimize production in your organization? nine0026 Book a consultation with iQB Technologies experts. Services such as 3D training, test 3D printing/3D scanning, site visits, diagnostics or ordering 3D equipment are also available.
MetalONE Metal 3D Printer: Top 7 Benefits of
- Compact working chamber (65 x 65 x 100 mm).
- High performance.
- Economy. nine0038
- Possibility of using argon and nitrogen.
- Intuitive, easy to edit print options.
- Easy to operate.
- Low maintenance cost.
Applications and Consumables
This metal 3D printer will be indispensable in the following industries:
- R&D;
- industry; nine0038
- dentistry;
- jewelry.
Sharebot CEO Arturo Donghi with MetalONE 3D printer and printed samples
The additive setup is ideal for exploring new materials, and thanks to its small build chamber and DMLS technology, it allows you to create objects from a small amount of metal powder - only 800 g. In addition, the user can edit all process parameters, which will be recorded in a log after printing is completed. With a 250W fiber laser and the ability to use both nitrogen and argon, virtually any powder can be tested. nine0003
For industrial applications, the printer is capable of prototyping small parts with incredible precision and producing them quickly and without significant difficulty. Unrivaled print repeatability ensures low-volume production with consistently high quality.
Cobalt-chromium alloys (CoCrMo), which are widely used in dentistry, are also applicable in MetalONE. For dental laboratories, this is a real boon: the 3D printer prints metal fillings, crowns and caps in less than an hour and is exceptionally easy to use. nine0003
Due to the compactness and special structure of paper filters, the printer will also be beneficial in the additive manufacturing of jewelry and other miniature products, as it allows you to quickly create objects with the highest degree of detail.
Sharebot's R&D department, in collaboration with several universities, has developed profiles for 316L steel and cobalt-chromium and continues to test new powders for metal laser 3D printer. Next in line are profiles for titanium and aluminum. nine0003
How MetalONE
was created Work on the metal printer project began in 2015. At the same time, Sharebot was developing SnowWhite, a machine for printing with thermoplastic powder using SLS technology. After the successful implementation of SnowWhite in different countries, Sharebot gained enough experience to launch a metal 3D laser printer project. It includes other types of powders, software, mechanical components, and build chamber design (involving the creation and maintenance of a modified environment), but this machine can be considered a direct continuation of SnowWhite. nine0003
In March 2019, the first prototype of the machine and the first samples were presented at the MECSPE exhibition in Parma. In the following months, various models were printed to test the metallurgical properties of the objects and their quality, as well as the reliability of the printer itself and the repeatability of printing. All parameters of the printing process are available to the user, allowing you to explore and explore new materials and applications.
So, Sharebot MetalONE will be a profitable solution if you need to research and test complex small-sized products, material properties, and also produce small series. nine0003
Key Features of
3D Printer- Construction chamber: 65 x 65 x 100 mm
- Layer thickness: 5-200 microns
- Laser: fiber, 250 W (1080 nm)
- Spot diameter: 40 microns
- Maximum speed: 5 m/s
- Software: Simplify 3D - Continuum
- Printer dimensions / weight: 740 x 630 x 1000 mm / 170 kg
MetalONE is available for order on sharebot. ru and iqb.ru websites (just like other Sharebot models) nine0003
Article published on 09/30/2020 , updated on 09/17/2021
How metal 3D printers work. Overview of SLM and DMLS technologies. additive manufacturing. 3D metal printing.
Metal 3D printing. Additive technologies.
SLM or DMLS: what's the difference?
Hello everyone, Friends! 3DTool is with you!
BLT metal 3D printer catalog nine0003
Selective laser melting ( SLM ) and direct metal laser sintering ( DMLS ) are two additive manufacturing processes that belong to the family of 3D printing , using the powder layering method. The two technologies have much in common: they both use a laser to selectively melt (or melt) metal powder particles, bonding them together and creating a pattern layer by layer. In addition, the materials used in both processes are metals in granular form. nine0003
The differences between SLM and DMLS come down to the basics of the particle bonding process: SLM uses metal powders with a single melting point and completely melts the particles, while in DMLS the powder consists of materials with variable melting points.
Specifically:
SLM produces single metal parts while DMLS produces metal alloy parts.
Both SLM and DMLS technologies are used in industry to create final engineering products. In this article, we will use the term "metal 3D printing" to summarize the 2 technologies. We will also describe the main mechanisms of the manufacturing process that are necessary for engineers to understand the advantages and disadvantages of these technologies. nine0113 There are other manufacturing processes for producing dense metal parts, such as electron beam melting (EBM) and ultrasonic additive manufacturing (UAM). Their availability and distribution is rather limited, so they will not be presented in this article.
How metal 3D printing SLM or DMLS works.
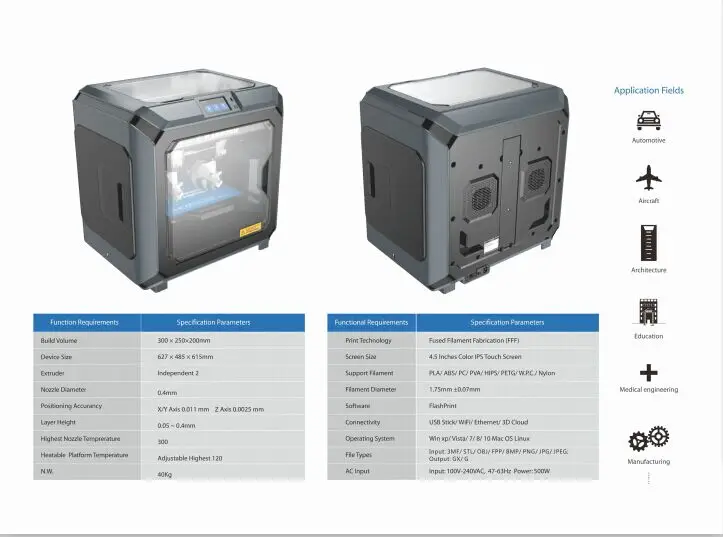
How does metal 3D printing work? The basic manufacturing process for SLM and DMLS is very similar.
1. The printing chamber is first filled with an inert gas (such as argon) to minimize the oxidation of the metal powder. It then heats up to the optimum operating temperature. nine0113 2. A layer of powder is spread over the platform, a powerful laser makes passes along a predetermined path in the program, fusing the metal particles together and creating the next layer.
3. When the sintering process is completed, the platform moves down 1 layer. Next, another thin layer of metal powder is applied. The process is repeated until the entire model is printed.
When the printing process is completed, the metal powder already has strong bonds in the structure. Unlike the SLS process, parts are attached to the platform via support structures. The support in metal 3D printing is created from the same material as the base part. This condition is necessary to reduce deformations that may occur due to high processing temperatures. nine0113 When the 3D printer's chamber cools down to room temperature, excess powder is removed manually, such as with a brush. The parts are then typically heat treated while they are still attached to the platform. This is done to relieve any residual stresses. They can then be further processed. The removal of the part from the platform occurs by means of sawing.
Scheme of operation of a 3D printer for metal.
In SLM and DMLS, almost all process parameters are set by the manufacturer. The layer height used in metal 3D printing varies from 20 to 50 microns and depends on the properties of the metal powder (fluidity, particle size distribution, shape, etc. ). nine0113 The basic size of the print area on metal 3D printers is 200 x 150 x 150 mm, but there are also larger sizes of the working area. Printing accuracy is from 50 - 100 microns. As of 2020, metal 3D printers start at $150,000. For example, our company offers 3D metal printers from BLT.
metal 3D printers can be used for small batch production, but the 3D printing capabilities of such systems are more like those of mass production on FDM or SLA machines. nine0113 The metal powder in SLM and DMLS is recyclable: typically less than 5% is consumed. After each impression, the unused powder is collected and sieved, and then topped up with fresh material to the level required for the next production.
Waste in metal printing, are supports (support structures, without which it will not be possible to achieve a successful result). With too much support on the manufactured parts, the cost of the entire production will increase accordingly. nine0113
Adhesion between coats.

3D metal printing on BLT 3D printers
SLM and DMLS metal parts have almost isotropic mechanical and thermal properties. They are hard and have very little internal porosity (less than 0.2% in 3D printed condition and virtually non-existent after processing).
Metal printed parts have higher strength and hardness and are often more flexible than traditionally made parts. However, such metal becomes “tired” faster. nine0003
3D model support structure and part orientation on the work platform.
Support structures are always required when printing with metal, due to the very high processing temperatures. They are usually built using a lattice pattern.
Supports in metal 3D printing perform 3 functions:
• They form the basis for creating the first layer of the part.
• They secure the part to the platform and prevent it from deforming.
• They act as a heat sink, removing heat from the model. nine0003
Parts are often oriented at an angle. However, this will increase the amount of support required, the printing time, and ultimately the overall cost.
Deformation can also be minimized with laser sintering templates. This strategy prevents the accumulation of residual stresses in any particular direction and adds a characteristic surface texture to the part.
Since the cost of metal printing is very high, software simulations are often used to predict how a part will behave during processing. These topology optimization algorithms are otherwise used not only to increase mechanical performance and create lightweight parts, but also to minimize the need for supports and the likelihood of part distortion. nine0003
Hollow sections and lightweight structures.
An example of printing on a BLT 3D printer
Unlike polymer powder melt processes such as SLS, large hollow sections are not typically used in metal printing as the support would be very difficult to remove, if at all possible.
For internal channels larger than Ø 8 mm, it is recommended to use diamond or tear-shaped cross-sections instead of round ones, as they do not require the construction of supports. More detailed recommendations on the design of SLM and DMLS can be found in other articles on this topic. nine0003
As an alternative to hollow sections, parts can be made with sheath and cores, which in turn are machined using different laser power and pass speeds, resulting in different material properties. The use of sheath and cores is very useful when making parts with a large solid section, as it greatly reduces printing time and reduces the chance of warping.
The use of a lattice structure is a common strategy in metal 3D printing to reduce part weight. Topology optimization algorithms can also help design organic lightweight shapes. nine0003
Consumables for 3D metal printing.
SLM and DMLS technologies can produce parts from a wide range of metals and metal alloys, including aluminum, stainless steel, titanium, cobalt, chromium and inconel. These materials meet the needs of most industrial applications, from aerospace to medical applications. Precious metals such as gold, platinum, palladium and silver can also be processed, but their use is of a minor nature and is mainly limited to jewelry making. nine0003
The cost of metal powder is very high. For example, a kilogram of 316 stainless steel powder costs approximately $350-$450. For this reason, minimizing part volume and the need for supports is key to maintaining optimal manufacturing cost.
The main advantage of metal 3D printing is its compatibility with high-strength materials such as nickel or cobalt-chromium superalloys, which are very difficult to process with traditional methods. Significant cost and time savings can be achieved by using metal 3D printing to create a near-clean shape part. Subsequently, such a part can be processed to a very high surface quality. nine0113
Metal post-processing.
Various post methods. treatments are used to improve the mechanical properties, accuracy and appearance of metal printed products.
Mandatory post-processing steps include the removal of loose powder and support structures, while heat treatment (heat annealing) is typically used to relieve residual stresses and improve the mechanical properties of the part.
CNC machining can be used for critical features (such as holes or threads). Sandblasting, plating, polishing, and micro-machining can improve the surface quality and fatigue strength of a metal printed part. nine0003
Advantages and disadvantages of metal 3D printing.
Pros:
1. Metal 3D printing can be used to make complex custom parts, with geometries that traditional manufacturing methods cannot provide.
2. Metal 3D printed parts can be optimized to increase their performance with minimal weight.
3. Metal 3D printed parts have excellent physical properties, metal 3D printers can print a wide range of metals and alloys. Includes difficult-to-machine materials and metal superalloys. nine0003
Cons:
1. Manufacturing costs associated with metal 3D printing are high. The cost of consumables is from $ 500 per 1 kg.
2. The size of the working area in metal 3D printers is limited.
Conclusions.
• Metal 3D printing is most suitable for complex, one-piece parts that are difficult or very expensive to manufacture using traditional methods, such as CNC.
• Reducing the need for building supports, will significantly reduce the cost of printing with metal. nine0113 • 3D printed metal parts have excellent mechanical properties and can be made from a wide range of engineering materials, including superalloys.
And that's all we have! We hope the article was useful to you.
Catalog of 3D printers for metal BLT
You can purchase metal 3d printers, as well as any other 3d printers and CNC machines, by contacting us:
• By email: Sales@3dtool.