Diy 3d printer projects
Popular 3D Printing Projects - Instructables
A 3D Printed Kinetic Marble Machine. by gzumwalt in 3D Printing
5 375
Very Easy 3d Puzzle to Do DIY But Devilishly Difficult for Smart People by DanielC788 in 3D Printing
Judges Prize 21 2.6K
Helical Dissection Puzzles by voidbubble in 3D Printing
First Prize 33 3.0K
Customizable 3D Printed Stocking Ornament by Penolopy Bulnick in 3D Printing
22 1. 5K
Lampy: the Desk Buddy That Brightens Your Workspace by Forma Designs in 3D Printing
Runner Up 31 1.3K
Create Your Own Circular Puzzle!!! by dslrdiy in 3D Printing
Second Prize 34 1.3K
JEDA LAMP by 2306 in 3D Printing
Runner Up 54 2.6K
Custom Metal Printed Hotend! by JGJMatt in 3D Printing
45 3. 8K
Dancing Santa Clause Automata by Fay3dlab in 3D Printing
Runner Up 19 1.2K
Make a Cookie Cutter With Tinkercad by Penolopy Bulnick in 3D Printing
1 41 2.9K
Design and 3D Print a Sturdy Puzzle Box by BrittLiv in 3D Printing
Second Prize 38 6.5K
Concentric Rings Fidget Toy by voidbubble in 3D Printing
20 1. 2K
Best DIY Camera Lens Caps V2.0 by dslrdiy in 3D Printing
33 2.2K
3D Printed Pop Its by MrErdreich in 3D Printing
Runner Up 52 5.9K
The Simply Impossible Puzzle by TheMadWrapper in 3D Printing
Judges Prize 8 160 21K
PiBM PS/2 Model 25 - 3D Printing, Assembly, and Electronics by poprhythm in 3D Printing
Second Prize 106 21K
Penrose Triangle by NEW PEW in 3D Printing
2 31 18K
G Wagon - RC Scale Model by Rambros in 3D Printing
46 2. 8K
3D Printed IMac G3 Mini - Fully Functional Hackintosh Powered by Intel NUC by GregO29 in 3D Printing
Runner Up 46 3.0K
A New Perspective on 3D Printing! by Caelestis Cosplay in 3D Printing
Runner Up 47 12K
Marblevator, Clouds. by gzumwalt in 3D Printing
35 3.4K
Repurpose Old Earphones to Capture 3D Printing Time-Lapses by NirL in 3D Printing
Second Prize 1 109 11K
A 3D Printed Windup Car Using a "Runaway Escapement" Speed Regulator. by gzumwalt in 3D Printing
Second Prize 1 67 4.1K
3D Printed Universal Drill Holder by Timbertime in 3D Printing
72 4.3K
Diy Tape Measure Yagi Antenna for Ham Radio by Mikiah in 3D Printing
Runner Up 57 5.7K
Memory Lamp by Banhammer in 3D Printing
56 4. 0K
A 3D Printed Slinky Machine by gzumwalt in 3D Printing
3 59 4.0K
Hobby Lamp / Lampara Para Hobby by modelkitsdeluxe in 3D Printing
135 6.3K
Marblevator, "The Ferris Wheel at the Pumpkin Patch" by gzumwalt in 3D Printing
Runner Up 3 32 2. 6K
WINTURER: a Portable NP-F Battery Charger Wind Turbine by adriancubas in 3D Printing
Grand Prize 666 67K
3D Printed Wigglegram Lens (Sony E-mount / APSC) by scealux in 3D Printing
Runner Up 40 4.0K
Blastoise Humidifier by Fay3dlab in 3D Printing
First Prize 46 2.0K
Tens'EGG'rity - Halloween - 3D Printed by seabirdhh in Decorating
59 9. 9K
Faux Barbed Wire Choker and Bracelet - Flexible 3D Print by Penolopy Bulnick in 3D Printing
1 62 5.3K
Animatronic Robot by Nitin r in 3D Printing
1 768
Ultimate (On a Budget) Home Vacuum by Icelandian in 3D Printing
Runner Up 52 5.9K
Life Sized Talking BMO From Adventure Time (that's Also an Octoprint Server!) by katzcreates in 3D Printing
Grand Prize 129 10K
Forged Fabric Parts!!?. . With 3D Printed Compression Molds by JGJMatt in 3D Printing
Runner Up 116 5.5K
3D PRINT a STEAM TRAIN 🚂 With Live Camera Streaming and Wifi Controls by DIY Machines in 3D Printing
First Prize 277 41K
Cut 3D Print Times in Half With Negative Volume Printing by MechanicalMashup in 3D Printing
22 1.5K
Are Expensive Nozzles OVERRATED? by diyperspective in 3D Printing
16 16K
Marblevator, Golf by gzumwalt in 3D Printing
Judges Prize 2 43 3. 1K
Egg Topper -Tinkercad basics by sigritom in 3D Printing
First Prize 1 38 3.6K
Make an Ostrich Egg Lamp by alatorre in Reuse
Second Prize 42 7.2K
Jurassic Park Gate Remote Control by Fay3dlab in 3D Printing
Judges Prize 42 4.7K
Brush and Display Together: Camera Lucida for Light Strokes by RichardGreene in Digital Graphics
Runner Up 25 1. 9K
Model Paint Shaker by Fay3dlab in 3D Printing
Runner Up 52 3.6K
Slidee: Non-motorized Automatic Camera Slider by Shivam Dehinwal in 3D Printing
Second Prize 110 6.4K
3D Printed Multi-Angle Drill Guide by Kartik_Nanduri in 3D Printing
108 7.2K
Smack Activated Cat Toy 🐈 by JGJMatt in 3D Printing
Runner Up 50 2. 3K
Pet Bowl Riser - 3D Printing by garweb in Pets
Runner Up 23 1.4K
Silent Omni-Directional Desk Fan by JGJMatt in 3D Printing
Runner Up 124 6.5K
Tool for Making Soil Blocks (3D Printed) by DonnaCohn in Gardening
Runner Up 1 80 5.2K
Cat and Dog Selective Feeder by tomasdiazwahl in 3D Printing
First Prize 95 8. 7K
3D Printer Enclosure - Wood With Acrylic Windows by poprhythm in 3D Printing
Runner Up 140 6.1K
217416670000000000000000000000:1 Cycloidal Drive by ShirdelY in 3D Printing
35 5.7K
Altoid Arcade by AndrewDuong01 in 3D Printing
Fourth Prize 107 8.7K
3D Printed - V6 Internal Combustion Engine by aseeshpaulbandaru in 3D Printing
Fourth Prize 51 3. 3K
MOTUS - Open-Source 3D Printed Robotic Arm by alatorre in 3D Printing
Grand Prize 239 10K
Custom Color Art Board by cfb70 in 3D Printing
First Prize 92 15K
67 Cool Things to 3D Print
3D printing is such a fun way to produce creative work—and it has totally taken off. Now, creators are using this amazing new technology to create all kinds of wild and wonderful 3D printer projects that were previously all but impossible to make at home.
These 3D printer projects are a great addition to your online design portfolio. This is such a hot space that shows your mastery of this chic craft could win you some big new clients. You can showcase a collection of cool things to 3D print and some of your best 3D printings too.
Want to get in on this cool 3D prints trend? We’ve compiled a list of 67 inspiring 3D printing ideas to fuel your next 3D printer design. So, what can you make with a 3D printer? Well, there’s something cool for everyone!
Next in our list of cool things to 3D print is a simple project that can be completed in approximately one hour and will produce a whistle. It can produce an eye-popping 118db sound, perfect for camping or sporting events.
If there’s one thing we can all agree on, it’s that earbud cords are a pain in the butt to keep organized. They constantly get tangled and eventually produce the dreaded earphone-crackle, rendering your treasured music-makers useless. This is a great example of what you can make with a 3D printer that can improve your everyday life.
A simple toy originally created for Settlers of Catan, this project is durable and (in our opinion) cute. This is one of those 3D printer projects you could use in a few ways: gaming, office desk decoration, children’s toy, you name it! Plus, T-Rexes are (always!) cool.
Organize your desk, and add a little flair at the same time! With these simple 3D printer designs, you’ll have all you need to generate truly unique desktop organizers that not only keep your stuff where it needs to be but look cool as well. You can 3D print a pencil holder that is unique to your own personality and have others mistaking your pencil holders again.
With a 3D printer you’ll be able to replace your dinnerware with new and original 3D printer designs in no time at all. Take this blueberry-themed bowl, for example. Why stop there? There are numerous other designs for plates and bowls out there to make eating at home a unique experience.
One of the cool things to 3D print is an abstract planter for your succulents and cacti. Why use traditional planters to hold your plants? There are cool 3D prints out there that don’t allow you to skip the traditional clay pots. These modular little guys are modern and fresh and guaranteed to make your mini-garden more attractive.
Measuring Cube
Get rid of those 72 measuring spoons from your utensil drawer and replace them all with a single implement! One of the most immediately useful and cool 3D prints in this list, it’ll make for an interesting tool that others will want when they see it.
Cable Holder
Stop the tyranny of cords taking over your desk and entertainment unit and 3D print some space-saving cable management devices. You’ll cut back on desk clutter and all that cord-related aggravation. These are the blessed 3D printed objects that make life a little less annoying!
Nearly everyone these days has a smartphone, and we’ve likely all had moments where we wanted to prop up our phones for viewing video or photos and had to resort to piled books or whatever else is on hand. And it rarely works out as well as we hope! That makes this tiny project one of the coolest 3D printed objects on the list. Plus, they look like cats. Cats are good.
A perennial childhood favorite, kids love them just as much today. Of course, adults can enjoy these toys, too. They could be just the ticket to break through some creative block!
A truly inspiring 3D printing idea, these pop-out business cards allow you to speak to clients in a way they won’t have experienced many times (if ever) before! Rather than a drab piece of cardboard, hand them a toy they can assemble that speaks much louder than a traditional printed card.
Can’t sit still? Searching for a 3D printer project to help you focus? Look no further. Fidget spinners are an excellent way to occupy your mind, and this 3D printed object will definitely do the trick.
This is probably one of the most fun and cool things to 3D print, these gimmicky little toys are quite literally affixed to food items found in your house. A lemon helicopter? A banana-car? Why not! Easy to print and awesome for providing hours of enjoyment to restless rainy-day kiddos.
Definitely among the most interesting and cool things to 3D print in this list (and showcasing a bit more complexity than other entries), the dragonfly is a tiny little flying machine you can whip up in a short time. It’s perfect for providing a little entertainment for your kids on a rainy day.
Why settle for boring cutlery in your drawer? With minimal effort, you can produce some decorative handles for your eating utensils and wow visitors to your humble abode. When they inevitably ask “so, what can you print with a 3D printer?”, you can tell them they’re eating with it!
Drop your phone into these useful little devices to amplify the sound from its speakers. They offer surprisingly high-quality sound—and now you don’t need to lug portable speakers around on picnics or at the beach.
If you’re looking for some more simple and cool 3D printing ideas, consider 3D printing a set of drink coasters. Thanks to simple 3D printer designs like this, we won’t need to spend our hard-earned cash on flimsy little discs anymore. Make your own coasters with whatever designs you want, and say goodbye to tacky freebies and over-priced novelty ones. This idea makes for one of the cool things to 3D print as gifts!
If you’re an audiophile, you’ll truly appreciate this entry as one of the best things to 3d print. By converting audio files, you can create your own records that will play on turntables. Why limit it to music? Record your own special messages to loved ones and send out the love!
Simple 3D printer designs like this are great to have on hand. Hinges are always useful, and come in handy all over the house. These particular designs are super-simple, even by 3D printing standards, requiring just a single step!
With a sliding clasp, these unique chip clip designs work quite well and are fantastically simple things to 3D print.
A larger-scale project than other 3D printing ideas, the Drawing Machine is quite unique: attach a pen and create works of art from files on your computer. This 3D printer project can help you produce invitations, cards or any other manner of drawings.
Some nostalgic old-timey engineering comes into play with these uber-neat 3D printing ideas. Relive the past and have your desk decorated with a sign that uses something other than LED or LCD displays!
When it comes to 3D printing metal, there are people who may choose to use a laser cutter instead. The reason is that 3D printed projects using metal can be costly and time-consuming. However, the two are quite different. 3D printing is an additive process, while laser cutting is a subtractive process. Depending on your needs, those that are looking to create multiple pieces at a quicker pace may choose the laser cutter as it can conveniently cut multiple materials and larger size.
With digital trends of raw and rustic design, you might be considering 3D printing cool things at home with metal. However, printing metal is extremely costly due to its process and the machinery required. If you’re looking for cool things to 3D print at home with a metal-looking finish, we recommend using materials on the market that can create metal-like 3D printed objects instead. These materials give the illusion that your 3D printed pencil holder or camera mount is made out of metal but without the actual cost.
Thanks to 3D printing, it has also made highly-customizable prosthesis possible. One of the coolest things about 3D printed prosthesis is that they can create custom fits for the patient and also a much lower cost. Instead of creating static designs that are “one size fits all”, 3D print gives companies the opportunity to create products that are affordable and personalized. What would have cost lots of money to create is now more accessible thanks to 3D printed prostheses.
Beyond science, 3D printed homes and shelters have also become one of the cool things to 3D print across the world. To address the housing issue around the world, companies have been using this technology to print emergency shelters and 3D printed homes. With this technology, companies and cities can build a community in a much shorter amount of time and for a cost cheaper than traditional home building methods. Each home inside the community can then be purchased at a more affordable cost.
If you love architecture and buildings, companies have created kits that allow people to replicate architectural structures and other cool things with a 3D pen. For boardgame lovers, you 3D print your own figurines by drawing it with your 3D pen. You can also turn your favorite cartoon show characters or movie heroes into 3D. While a 3D pen allows you to draw 2D things to 3D, their limitation tends to be the size of the project you can make. If you’re looking to 3D print a life-size chair, it may be easier to use a printer because 3D pens may not be able to create something as durable.
- Tangram: A super easy and fun game to play with your kids or friends. If you’re going on a road trip or simply trying to pass time, this 3D printed tangram makes for portable entertainment.
- Klöts (Quick shoe ties): Some cool things to 3D print for your kids are these quick shoe ties.
With this project, you’ll spend less time worrying about their shoelaces being undone and risking a fall.
- Puzzle Keychain: This heart puzzle is perfect as a gift or personal use. If you’re tight on schedule for an anniversary or valentine’s day gift, this heart puzzle is one of the quickest things to 3D print.
- Door Stop: Some things to 3D print for practical uses are these door stops. Whether you’re using it at home or for your office, printing them is super easy and fast.
- Light Switch Locks: This definitely tops for cool things to 3D print, especially for parents. This awesome tool can prevent your kids from turning the lights on and off at home. Keep certain lights off to save energy.
Ready to build a design portfolio website that captures clients’ attention? From gorgeous themes to a built-in proofing tool, we’ve got designers covered. Start your free trial with Format today!
Now get out there, get creative, and start turning heads with amazing 3D creations!
Need some more design project inspiration?
How to Start a Creative Project by ADAMJK
5 Ways to Fund Your Personal Project
10 Steps to Building Your Perfect Online Portfolio
Build a home 3D printer with your own hands: recommendations from personal experience
3D printing and assembly of 3D printers is my hobby and passion. Here I will not share detailed diagrams and drawings, there are more than enough of them on specialized resources. The main goal of this material is to tell you where to start, where to dig and how to avoid mistakes in the process of assembling a home 3D printer. Perhaps one of the readers will be inspired by applied engineering achievements.
Why do you need a 3D printer? Use cases
I first came across the idea of 3D printing back in the 90s when I was watching the Star Trek series. I remember how impressed I was by the moment when the heroes of the cult series printed the things they needed during their journey right on board their starship. They printed anything: from shoes to tools. I thought it would be great someday to have such a thing too. Then it all seemed something incredible. Outside the window are the gloomy 90s, and the Nokia with a monochrome screen was the pinnacle of progress, accessible only to a select few. nine0003
Years passed, everything changed. Around 2010, the first working models of 3D printers began to appear on sale. Yesterday's fantasy has become a reality. However, the cost of such solutions, to put it mildly, discouraged. But the IT industry would not be itself without an inquisitive community, where there is an active exchange of knowledge and experience and who just let them delve into the brains and giblets of new hardware and software. So, drawings and diagrams of printers began to surface more and more often on the Web. Today, the most informative and voluminous resource on the topic of assembling 3D printers is RepRap - this is a huge knowledge base that contains detailed guides for creating a wide variety of models of these machines. nine0003
I assembled the first printer about five years ago. My personal motivation to build my own device is quite prosaic and based on several factors. Firstly, there was an opportunity to try to realize the old dream of having your own device, inspired by a fantasy series. The second factor is that sometimes it was necessary to repair some household items (for example, a baby stroller, car elements, household appliances and other small things), but the necessary parts could not be found. Well, the third aspect of the application is "near-working". On the printer, I make cases for various IoT devices that I assemble at home. nine0003
Agree, it is better to place your device based on Raspberry Pi or Arduino in an aesthetically pleasing "body", which is not a shame to put in an apartment or take to the office, than to organize components, for example, in a plastic bowl for food. And yes, you can print parts to build other printers :)
There are a lot of scenarios for using 3D printers. I think everyone can find something of their own.
A complex part in terms of drawing that I printed on my printer. Yes, it's just a figurine, but it has many small elements
Ready solution vs custom assembly
When a technology has been tested, its value in the market decreases markedly. The same thing happened in the world of 3D printers. If earlier a ready-made solution cost just sky-high money, then today acquiring such a machine is more humane for the wallet, but nevertheless not the most affordable for an enthusiast. There are a number of solutions already assembled and ready for home use on the market, their price range ranges from $500-700 (not the best options) to infinity (adequate solutions start from a price tag of about $1000). Yes, there are options for $150, but we, for understandable, I hope, reasons, will not dwell on them. nine0003
In short, there are three cases to consider a finished assembly:
- when you plan to print not much and rarely;
- when print accuracy is critical;
- you need to print molds for mass production of parts.
There are several obvious advantages to self-assembly. The first and most important is cost. Buying all the necessary components will cost you a maximum of a couple of hundred dollars. In return, you will receive a complete 3D printing solution with the quality of manufactured products acceptable for domestic needs. The second advantage is that by assembling the printer yourself, you will understand the principles of its design and operation. Believe me, this knowledge will be useful to you during the operation of even an expensive ready-made solution - any 3D printer needs to be serviced regularly, and it can be difficult to do this without understanding the basics. nine0003
The main disadvantage of assembly is the need for a large amount of time. I spent about 150 hours on my first build.
What you need to assemble the printer yourself
The most important thing here is the presence of desire. As for any special skills, then, by and large, in order to assemble your first printer, the ability to solder or write code is not critical. Of course, understanding the basics of radio electronics and basic skills in the field of mechanics (that is, "straight hands") will greatly simplify the task and reduce the amount of time that needs to be spent on assembly. nine0003
Also, to start we need a mandatory set of parts:
- Extruder is the element that is directly responsible for printing, the print head.
There are many options on the market, but for a budget build, I recommend the MK8. Of the minuses: it will not be possible to print with plastics that require high temperatures, there is noticeable overheating during intensive work, which can damage the element. If the budget allows, then you can look at MK10 - all the minuses are taken into account there. nine0032
- Processor board. The familiar Arduino Mega is well suited. I didn't notice any downsides to this solution, but you can spend a couple of dollars more and get something more powerful, with a reserve for the future.
- Control board. I'm using RAMPS 1.4 which works great with the Arduino Mega. A more expensive but more reliable board is Shield, which already combines a processor board and a control board. In modern realities, I recommend paying attention to it. In addition to it, you need to purchase at least 5 microstep stepper motor controllers, for example - A4988. And it's better to have a couple of these in stock for replacement.
- Heated table. This is the part where the printed element will be located. Heating is necessary due to the fact that most plastics will not adhere to a cold surface. For example, for printing with PLA plastic, the required surface temperature of the table is 60-80°C, for ABS - 110-130°C, and for polycarbonate it will be even higher
There are also two options for choosing a table - cheaper and more expensive. Cheaper options are essentially printed circuit boards with preheated wiring. To operate on this type of table, you will need to put borosilicate glass, which will scratch and crack during operation. Therefore, the best solution is an aluminum table. nine0032 - Stepper motors. Most models, including the i2 and i3, use NEMA 17 size motors, two for the Z axis and one each for the X and Y axes. Finished extruders usually come with their own stepper motor. It is better to take powerful motors with a current in the motor winding of 1A or more, so that there is enough power to lift the extruder and print without skipping steps at high speed.
- Basic set of plastic fasteners.
- Belt and gears to drive it. nine0051
Examples of elements appearance: 1) MK8 extruder; 2) Arduino processor board; 3) RAMPS control board; 4) motor controllers; 5) aluminum heated table; 6) NEMA 17 stepper motor; 7) a set of plastic fasteners; 8) drive gears; 9) drive belt
This is a list of items to be purchased. Hardcore users can assemble some of them themselves, but for beginners, I strongly recommend purchasing ready-made solutions. nine0003
Yes, you will also need various small things (studs, bearings, nuts, bolts, washers ...) to assemble the case. In practice, it turned out that using a standard m8 stud leads to low printing accuracy on the Z axis. I would recommend immediately replacing it with a trapezoid of the same size.
M8 trapezoid stud for Z axis, which will save you a lot of time and nerves. Available for order on all major online platforms
nine0002 You also need to purchase customized plastic parts for the X axis, such as these from the MendelMax retrofit kit.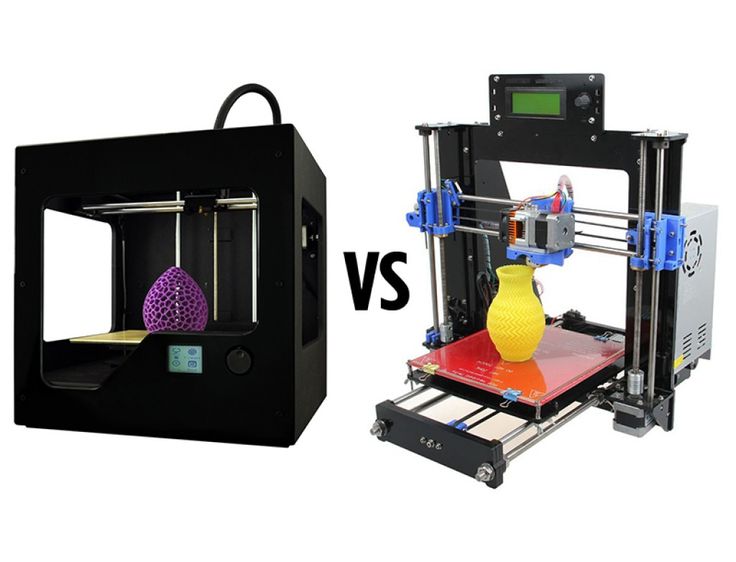
Most parts available at your local hardware store. On RepRap you can find a complete list of necessary little things with all sizes and patterns. The kit you need will depend on the choice of platform (we'll talk about platforms later).
What's the price
Before delving into some aspects of the assembly, let's figure out how much such entertainment will cost for your wallet. Below is a list of parts required for purchase with an average price. nine0003
Platform selection
The community has already developed a number of different platforms for assembling printers - the most optimal case designs and the location of the main elements, so you do not have to reinvent the wheel.
i2 and i3 are key platforms for self-assembly printer enclosures. There are also many modifications of them with various improvements, but for beginners, these two classic platforms should be considered, since they do not require special skills and fine-tuning. nine0003
Actually, illustration of platforms: 1) i2 platform; 2) i3 platform
On the plus side of i2: it has a more reliable and stable design, although it is a little more difficult to assemble; more opportunities for further customization.
The i3 variant requires more special plastic parts to be purchased separately and has a slow print speed. However, it is easier to assemble and maintain, and has a more aesthetically pleasing appearance. You will have to pay for simplicity with the quality of printed parts - the body has less stability than i2, which can affect print accuracy. nine0003
Personally, I started my experiments in assembling printers from the i2 platform. She will be discussed further.
Assembly steps, challenges and improvements
In this block, I will only touch on the key assembly steps using the i2 platform as an example. Full step by step instructions can be found here.
The general scheme of all the main components looks something like this. There is nothing particularly complicated here:
I also recommend adding a display to your design. Yes, you can easily do without this element when performing operations on a PC, but it will be much more convenient to work with the printer this way. nine0003
Understanding how all components will be connected, let's move on to the mechanical part, where we have two main elements - a frame and a coordinate machine.
Assembling the frame
Detailed frame assembly instructions are available on RepRap. Of the important nuances - you will need a set of plastic parts (I already talked about this above, but I'd better repeat it), which you can either purchase separately or ask your comrades who already have a 3D printer to print.
The frame of the i2 is quite stable thanks to its trapezoid shape.
This is how the frame looks like with parts already partially installed. For greater rigidity, I reinforced the structure with plywood sheets
Coordinate machine
An extruder is attached to this part. The stepper motors shown in the diagram above are responsible for its movement. After installation, calibration is required along all major axes.
Important - you will need to purchase (or make your own) a carriage for moving the extruder and a mount for the drive belt. Drive belt I recommend GT2. nine0003
The carriage printed by the printer from the previous picture after it has been assembled. The part already has LM8UU bearings for guides and belt mount (top)
Calibration and adjustment
So, we completed the assembly process (as I said, it took me 150 hours) - the frame was assembled, the machine was installed. Now another important step is the calibration of this very machine and extruder. Here, too, there are small subtleties.
Setting up the machine
I recommend calibrating the machine with an electronic caliper. Do not be stingy with its purchase - you will save a lot of time and nerves in the process.
The screenshot below shows the correct constants for the Marlin firmware, which must be selected in order to set the correct number of steps per unit of measure. We calculate the coefficient, multiply it, substitute it into the firmware, and then upload it to the board.
Marlin 9 firmware constants0022
For high-quality calibration, I recommend relying on larger numbers in measurements - take not 1-1.5 cm, but about 10. So the error will be more noticeable, and it will become easier to correct it.
Calibrating the extruder
When the frame is assembled, the machine is calibrated, we start setting up the extruder. Here, too, everything is not so simple. The main task of this operation is to correctly adjust the supply of plastic.
If underfeeding, the printed test item will have noticeable gaps, like test die 1. Conversely, the result will look bloated if plastic is overfed (dice 2)
Getting Started Printing
It remains for us to run some CAD or download ready-made .stl, which describe the structure of the printed material. Next, this structure needs to be converted into a set of commands understandable to our printer. For this I use the Slicer program. It also needs to be set up correctly - specify the temperature, the size of the extruder nozzle. After that, the data can be sent to the printer.
Slicer interface
As a raw material for printing, I recommend starting with regular ABS plastic - it is quite strong, products made from it are durable, and it does not require high temperatures to work with. For comfortable printing with ABS plastic, the table must be heated to a temperature of 110-130 ° C, and the extruder nozzle - within 230-260 ° C.
Some important details. Before printing, calibrate the machine along the Z axis. The extruder nozzle should be approximately half a millimeter from the table and ride along it without distortion. For this calibration, a regular sheet of A4 paper inserted between the nozzle and the surface of the heated table is best suited. If the sheet can be moved with little effort, the calibration is correct. nine0003
Another thing to keep in mind is the surface treatment of the heated table. Usually, before printing, the surface of the table is covered with something that hot plastic sticks to well. For ABS plastic, this can be, for example, Kapton tape. The disadvantage of adhesive tape is the need to re-glue it after several printing cycles. In addition, you will have to literally tear off the adhering part from it. All this, believe me, takes a lot of time. Therefore, if it is possible to avoid this fuss, it is better to avoid it. nine0003
An alternative option that I use instead of scotch tape is to apply several layers of ordinary light beer, followed by heating the table to 80-100 ° C until the surface is completely dry and re-applying 7-12 layers. It is necessary to apply the liquid with a cloth moistened with a drink. Among the advantages of this solution: ABS plastic separates from the table on its own when it cools down to about 50 ° C and is removed without effort, the table does not have to be peeled off, and one bottle of beer will last you for several months (if you use the drink only for technical purposes :)). nine0003
After we have collected and configured everything, we can start printing. If you have an LCD screen, then the file can be transferred for printing using a regular SD card.
The first results may have bumps and other artifacts - do not worry, this is a normal process of "grinding" the printer elements, which will end after a few print cycles.
Tips to make life easier (and sometimes save money)
In addition to the small recommendations given in the text above, in this section I will also give a short list of tips that will greatly simplify the operation of a 3D printer and the life of its owner. nine0003
- Do not experiment with nozzles. If you plan to immediately print from materials that require high temperatures, then it is better to immediately take the MK10 extruder. On MK8, you can "hang" special nozzles that support high-temperature conditions. But such modifications often cause difficulties and require special experience.
It is better to avoid this fuss on the shore by simply installing the right extruder for you.
- Add starter relay for heated table. nine0051 Improving the power supply system for this important printing part with a starter relay will help solve the known problem of RAMP 1.4 - overheating of the transistors that control the power of the table, which can lead to failure of the board. I made this upgrade after having to throw away a few RAMPS 1.4s.
- Select the correct filament diameter for printing. I recommend using 1.75mm plastic for MK8 and MK10. If we take plastic, for example, 3 mm, then the extruder simply does not have enough strength to push it at an acceptable speed - everything will be printed much longer, and the quality will drop. ABS plastic is ideal for MK8, MK10 will be able to produce products from polycarbonate. nine0032
- Use only new and precise X and Y guides. Print quality will be affected. It is difficult to count on good quality with bent or deformed guides along the axes.
- Take care of cooling. During my experiments with various extruders, the MK10 showed the best results - it prints quite accurately and quickly. The MK10 can also print plastics that require a higher print temperature than ABS, such as polycarbonate. Although it is not as prone to overheating as its younger brother MK8, I still recommend taking care of its cooling by adding a cooler to your design. It must be permanently enabled, this option can be configured in Slicer. You can also add coolers to keep the stepper motors at an acceptable temperature, however, make sure that their air flows do not fall on the printed part, as this can lead to its deformation due to too rapid cooling. nine0032
- Consider heat retention. Yes, on the one hand, we are struggling with overheating of the elements. On the other hand, a uniform temperature around the printer will contribute to high-quality printing (the plastic will be more pliable). To achieve a uniform temperature, you can put our printer, for example, in a cardboard box.
The main thing is to connect and configure the coolers before that, as described above.
- Consider insulating your desk. Heated table heats up to high temperatures. And if part of this heat leaves properly, heating the printed part, then the second part (from below) just goes down. To concentrate the heat from the table onto the part, you can perform an operation to insulate it. To do this, I simply attach a cork mouse pad to its bottom using stationery clips. nine0032
Pins
I am sure that during the assembly process you will encounter a number of difficulties specific to your project. Neither this text nor even the most detailed guides will insure against this.
As I wrote in the introductory part, the above does not claim the status of a detailed assembly manual. It is almost impossible to describe all the stages and their subtleties within the framework of one such text. First of all, this is an overview material that will help you prepare for the assembly process (both mentally and financially), understand whether you personally need to bother with self-assembly - or give up on everything and buy a ready-made solution. nine0003
For me, assembling printers has become an exciting hobby that helps me solve some issues in home and work affairs, take my mind off programming and do something interesting with my own hands. For my children - entertainment and the opportunity to get unusual and unique toys. By the way, if you have children whose age allows them to mess around with such things, such an activity can be a good help for entering the world of mechanics and technology.
For everyone, the vectors of using 3D printers will be very different and very individual. But, if you decide to devote your personal time to such a hobby, believe me, you will definitely find something to print :)
I will be glad to answer comments, remarks and questions.
What to read/see
- what can be printed;
- 3D printer forum;
- RepRap community site with model descriptions and assembly instructions;
- printer that prints electronics.
Subscribe to the Telegram channel "DOU #tech" so you don't miss new technical articles.
Topics: DIY, embedded, tech
I want a house with a 3D printer! How to do it step by step
Mass-produced 3D printing of buildings is becoming a reality in the booming construction industry. Today we will talk about the technology and types of industrial 3D printers.
Technology
The principle of construction using a 3D printer is the extrusion (extrusion) of concrete, layer by layer, according to a given three-dimensional computer model. With the help of a complex for preparing and supplying a building mixture, concrete is mixed with water and other additives and pumped into a hose. The hose is connected to the printer head. Under the pressure of the pump, concrete is fed to the head, the mixture exits the nozzle and is applied to the surface of the site or previous printed layers. nine0003
Types of construction 3D printers
To build a building, you need a ready-made 3D model, quick-setting concrete and a construction site that can be leveled with standard construction equipment. Most of the 3D printers print according to the same principle - by layering the concrete mixture extruded from the extruder nozzle. There are exceptions, such as D-Shape printers, which print by layering powder material and then bonding across the entire width of the machine. nine0003
Construction 3D printers are diverse - these are machines with a polar scheme of operation (rotating 3D printers), and delta printers, and based on robotic arms. Concrete mixtures suitable for extrusion today make it possible to print elements of varying complexity and size - from small architectural forms, such as flower beds and benches, to entire buildings, bridges and even skyscrapers. Therefore, printers differ not only in device, but also in scale.
There are several types of construction printers:
XYZ printers (portal)
The equipment is a frame along which the head moves along the XY axes. Three portals are usually used to hang the print head. The portals are moved by stepper motors providing the highest precision. They are designed to print buildings in parts - in the shop; and for printing interior walls, when installing the printer inside a building under construction. Small buildings that fit entirely under the arch of the printer are printed entirely in one go. nine0003
Delta
Delta printers, unlike gantry printers, do not rely on 3D guides and can print more complex shapes. Here the print head is suspended on thin arms that are attached to vertical rails.
Robots
Robotic printer-handles - a robot or a group of robots of the industrial manipulator type, equipped with extruders and controlled by a computer. A special case of a robot printer is a 3D printer with a polar pattern of operation, which is located inside a building under construction, usually in the center. Examples of such robots are a tracked vehicle from MIT and a robot from the Russian company Apis Cor. nine0003
D-Shape
Technical features make D-Shape a separate class of construction printers - it prints not with a solution, but with dry powder material, each layer of which is laid to the desired thickness and compacted, and then impregnated with a binder from the nozzles printer. The finished part is cleaned of excess raw materials.
Mortars
The main printing material is concrete. nine0003
Construction printing concrete must be suitable for extrusion through the print head. This is not as simple as it might seem at first glance. The difficulty is that the concrete must be laid in regular, even layers without spreading, and set quickly enough to retain its shape, but not too quickly - the superimposed layers must remain chemically active in order to form a single structure at the point of contact. Reducing the setting rate is also important for maintaining the performance of the equipment - the nozzle should not be clogged with hardening concrete. nine0003
Fine-grained mixtures are used for printing, which are different from traditional concrete. Each company develops its own formulation, which corresponds to the device of the printer and its nozzle, as well as the specifics of the target products.