Jewelry made with 3d printer
Top 3D Printed Jewelry on the Market
3D printing news News The Most Impressive 3D Printed Jewelry Designs on the Market
Published on April 2, 2022 by Jamie D.
Whether in jewelry or jewelry, additive manufacturing is a technique increasingly used by professionals in the sector because of its ability to design complex and unique parts, all more quickly. It is used in particular to produce molds used later for the lost wax casting; prototypes to allow better visualization of rings, necklaces, bracelets; but also finished parts directly integrated into a jewel. This variety of applications can be explained by the diversity of the printing processes used, but also the range of materials available. Stereolithography, for example, will be ideal for creating highly detailed prototypes; laser fusion, on the other hand, will allow us to work on finished metal parts, sometimes even precious metals. In order to understand all the possibilities of 3D technologies in this sector, here is a selection of 3D printed jewelry!
A Ring with 7,801 Diamonds
We start our selection with a project that broke a world record for the most diamonds in a ring: 7,801 at the time. Though what interests us most is not so much this astronomical number but more because additive manufacturing was involved in the development process of this unique jewel. The Indian service Imaginarium was behind the flower-shaped ring. It 3D printed a resin mold into which it cast the precious metal – in this case gold. So it’s not a 3D printed piece of jewelry per se, but without 3D printing, the ring would never have been this complex, the service noted that 3D printing was the only way to create a mold that could incorporate so many jewels. It is composed of 7 different sections – six flowers and the ring, with each flower layered on top of the other. The result? A ring with 7,801 diamonds that doesn’t go unnoticed!
Rings with Complex Geometries
Invaerso uses 3D printing primarily for prototyping purposes and in 2020 was even awarded for its innovative solutions. Thanks to 3D printing, the Italian company is able to quickly test whether a product works and is able to determine whether it needs to be modified or not. In addition, in combination with traditional techniques, additive manufacturing can speed up production processes. Maria Clelia Scuteri, the designer behind Invaerso, also says that 3D printing makes it possible to design rings and other types of jewelry with complex geometries.
Photo Credits: Invaerso
The Benefits of 3D Printing and Nylon According to Caroline Auraix
In France, too, the jewelry industry is using additive manufacturing to improve production processes. Parisian artist Caroline Auraix uses 3D technologies to meet the time constraints imposed by the industry. The jeweler works mainly with Rhinoceros 3D software, although she confides that she also uses free modeling software, allowing her to give her models “modeling clay” effects. As for the printing process used, Caroline Auraix explains that selective laser sintering, also known as SLS, is the technology best suited to her needs. The majority of these parts are made from nylon, because when this material is applied in a very thin layer, it allows light to pass through, which offers a luminous effect. In addition, its strength and lightness make it an ideal material for jewelry.
A brooch designed with 3D technologies. (photo credits: Caroline Auraix)
RADIAN Uses 3D Printing for Sustainable Jewelry
Next on the list has to be Berlin based label RADIAN who are known for their 3D printed, sustainable jewelry and home goods. According to the company, they wish to give jewelry that is straight forward with a twist, with artistic pieces that are intricate, edgy and organic. This is possible using 3D printing, notably SLS and binder jetting. They have three collections that interested buyers can choose from including the Solitaire collection which puts a focus on geometric and angular struts, the Cubetwist collection which as the name suggests combines a strong cubic pattern with bends and twists, and Nefertiti which is the company’s answer for what Ancient Egyptians would make using 21st century production methods. RADIAN points to 3D printing as a key factor in how they make their jewelry sustainable thanks to its ability to make products locally and to reduce waste.
The Solitaire Ring from RADIAN’s collection (photo credits: RADIAN)
Elements Lab Offers Unique Jewelry
Based in Taiwan, ElementsLab is a 3D printing service offering the ability to design custom jewelry. Founded by Ting Tang, the company is able to create silver and metal alloy parts, and mass-produce them. Compared to traditional metalworking, additive manufacturing allows for more complex designs to be created faster and more efficiently. ElementsLab offers customers the opportunity to realize their ideas and design custom parts. Although they are only prototypes, 3D printed items must meet durability standards and have certain mechanical features. Thus, each piece of jewelry has a unique touch and meaning.
Photo Credits: Elements Lab
3D Printed Optical Jewelry from F-elia
F-elia is a young French company making ‘optical jewelry’ thanks to 3D printing, giving them an original design. The frame combines both aesthetics, with complex and unique shapes, but also functionality. To achieve such a result, F-elia uses SLS technology and, as far as materials are concerned, it relies on polyamide, especially as it offers strength, flexibility and a smooth surface after the post-processing stages. Today, the company has diversified and offers accessories such as magnifying glasses and eyeglass necklaces in addition to its glasses.
F-elia places an emphasis on originality with its 3D printed glasses (photo credits: F-elia)
Nuovi Gioielli, Combining Traditional Know-How with Innovation
Founded in 1985, Nuovi Gioelli offers jewelry that combines traditional craftsmanship and innovation. In order to make its unique jewelry, Nuovi Gioielli uses different production processes, among which we find 3D metal printing. The company uses different metals, although the most common are steel and bronze, and aims to successfully 3D print gold and platinum. Like other companies in the industry using 3D technologies, the company praises the benefits of the technology in jewelry, especially in terms of design freedom. By combining new technologies with traditional methods, Nuovi Gioielli creates unique pieces and leaves no limits to its creativity.
Photo Credits: Nuovi Gioielli
Nervous System
Nervous System is an American design studio specializing in the creation of complex 3D printed objects. In order to make bracelets, necklaces and other types of jewelry, the company takes inspiration from natural phenomena and uses computer simulations to model them. Once the 3D file is ready, it is 3D printed and offered to customers. And with this method, Nervous System doesn’t just produce jewelry. The company also designs cups and vases, lamps and other sculptures.
Photo Credits: Nervous System
Endswell Jewelry
Rachel Gant and Andrew Deming, the designers behind Endswell Jewelry, have teamed up to use 3D printing in their solid gold rings. Their work focuses on beautiful, yet minimal, pieces that offer an alternative to traditional wedding rings. The designers came up with the design since they are an unmarried couple, and use 3D printing to create their precise designs.
Diana Law’s 3D printed Jewelry
Diana Law is a fashion and jewelry designer who studied in France before discovering 3D printing. 3D printing allowed Diana to create the stunning jewelry designs she wished to create, leading to her newly released collection. Her collections are made of plastics and stainless steel. The plastic jewelry is created using selective laser sintering, allowing her to create extremely fine layers of nylon. Inspired by life around her, Diana also prefers 3D printing due to the environmental benefits.
Ross Lovegrove
Designer Ross Lovegrove has developed a collection of 3D printed jewelry rings called Foliates. The collection of 6 rings are made of 18K gold, and are each made in an edition of 10 rings. These stunning rings are made with direct metal laser sintering in addition to combining 3D printing with wax casting.
The 3D Printed Pen from Pjotr
Not quite a piece of jewelry, but a stunning 3D printed accessory made of expensive material nonetheless, Pjotr have unveiled a solid 18K gold 3D printed pen. The pen, designed by Rein van der Mast, is named Spica Virginis. The first version of this 3D printed pen was a titanium version, which was still very luxurious. However, this solid gold variant is a new level of luxury. The pen is available for just €14,320, bargain?
What do you think of this 3D printed jewelry? Let us know in a comment below or on our Linkedin, Facebook, and Twitter pages! Don’t forget to sign up for our free weekly Newsletter here, the latest 3D printing news straight to your inbox! You can also find all our videos on our YouTube channel.
Guide to Jewelry 3D Printing
Two techniques have historically defined jewelry making: handcrafting and lost-wax casting. Both techniques require significant technical expertise, are highly time-intensive, and mistakes in the process can prove expensive.
But today, digital design and 3D printing are primed to disrupt these age-old practices in a major way. Supplementing traditional processes with digital techniques such as jewelry 3D printing brings new possibilities in design and production to jewelers, as well as exciting new customization options for customers.
White Paper
In this white paper, learn how to cast fine jewelry pieces from 3D printed patterns and how direct investment casting, or lost wax casting, works as a moldmaking technique.
Download the White Paper
3D printed jewelry production augments the principles of investment casting, or lost wax casting with the advantages of a digital design and manufacturing process.
With traditional lost-wax casting, jewelry designers hand-carve the original pattern in wax, place the wax pattern in a mold to be burned out, and then pour precious metals like gold or silver into the mold cavity to create the cast piece. To achieve its final appearance, designers polish and finish the cast piece to shine.
With the digital workflow, jewelers use CAD software tools for jewelry design to create the models digitally and a high-resolution 3D printer to produce the 3D printed jewelry patterns that can then be cast in a mold. After burnout of the positive pattern, the process follows the same path as traditional investment casting. Thanks to the digital techniques, the need for time-intensive manual labor is reduced and the design itself is easy to preserve, modify, and recreate when needed.
Sample part
Curious to see our materials firsthand? Click here and we'll ship you a free jewelry sample part printed on our 3D printer.
Request a Free Sample Part
Until now, the complexity of the design and production process made customized jewelry an expensive privilege. With digital tools, however, jewelers have already started offering personalized creations as part of their basic service or as a value add. If you go to a jeweler today and ask for an engagement ring, often you'll have the option to customize a unique design.
3D printed jewelry try-on pieces drastically shorten the feedback loop between designer and customer.
Jeweller and customer can discuss the design together, and an hour later, the customer can hold and try on a real, physical model of the ring. In jewelry retail, on-site digital design combined with the speed of 3D printing has drastically shortened the feedback loop between designer and customer.
Moving from design to production is easier and faster, as hand carving a precious one-off is no longer a requirement. The try-on pieces can be tailored based on the customer’s requests, 3D printed again, and then manufactured with lost-wax casting, which translates to a considerable reduction in the cost of making customized 3D printed jewelry.
With 3D printing, jewelry designers are able to produce designs that would be incredibly difficult to hand carve in the traditional manner. Breakthroughs in castable resins are setting new standards for the quality available through an affordable desktop 3D printer.
3D printing jewelry patterns in Formlabs’ Castable Wax 40 Resin combines the smooth surface finish characteristic of stereolithography (SLA) 3D printing technology with precise print settings. Thanks to a precisely controlled laser, extraordinary design details—delicate filigrees, raised text, and detailed pavé stone settings—can be captured with amazing sharpness.
Stereolithography 3D printing can reproduce complex features that’d be difficult to hand carve.
With these long-established design restrictions now removed, we're seeing entirely new genres of design emerging from jewelers who digital capabilities in the US as well as in South Asia and Asia Pacific, and the Middle East.
Webinar
In this webinar, Patrick Diggins, our Jewelry Vertical Manager, will teach you how Castable Wax 40 can help you push the boundaries of design and production efficiency.
Watch the Webinar
Digital tools are not only making jewelry easier to customize, but also simpler to mass-produce designs.
Vulcanized rubber molds are used to produce wax patterns in quantity for lost-wax casting, but the “master” pattern is traditionally made from an investment cast, hand-carved wax pattern.
3D printers can produce master models that are used to form room temperature vulcanization (RTV) molds and even durable high temperature vulcanized rubber molds.
Directly 3D printed jewelry patterns can be used for room temperature vulcanization (RTV) and vulcanization of high temp natural rubber.
“With the quality that you can get with SLA 3D printing for printing these jewelry pieces, you can jump straight from the 3D printed part to a master mold,” said Formlabs' Jewelry Vertical Product Manager Amos Dudley. “The surface finish is already so smooth that it doesn't require very much finishing. You can use that as the rubber mold for creating the final wax parts that go into production.”
White Paper
3D printing with high-performance materials allows designers and casters to leverage digital technology in their production processes. Read now to learn how 3D printing can be used in the production of small metal parts.
Download the White Paper
When new technology is finally made available to the public, it usually comes with a high price tag and a complicated interface, restricting it to users with deep pockets and technical savvy. Previous generations of jewelry 3D printers required both significant maintenance and a skilled operator in addition to thousands of dollars of investment that limited them to the largest jewelry manufacturers and casting houses. Nevertheless, Dudley notes, “3D printing has become much more affordable, offering unique opportunities to independent jewelry makers.”
The lower cost and higher-quality jewelry 3D printing technology have made the digital workflow a viable method of manufacturing. “In the coming years, we're going to see a growing trend in that segment, with smaller jewelers adopting these technologies and becoming less centralized,” Dudley said.
This shift to increasingly competitive independent jewelers will continue as the industry becomes more familiar with castable resin 3D printing. Historically jewelry 3D printing has been dominated by complex and expensive wax 3D printers. With affordable desktop jewelry 3D printers like the Form 3+, the technology is becoming available to more jewelers, especially smaller independent ones.
Interactive
Try our interactive ROI tool to see how much time and cost you can save when 3D printing on Formlabs 3D printers.
Calculate Your Savings
Owing to the formerly high cost of large-scale jewelry 3D printers and the perceived barrier-to-entry of digital jewelry design, 3D printed jewelry, despite its potential, currently represents a relatively small fraction of the market.
Nevertheless, with increasingly easy to use and accessible jewelry 3D printers, the digital workflows in the jewelry market are poised for growth. Desktop stereolithography 3D printers are an important component in this expansion.
High-resolution desktop 3D printers, like the Formlabs Form 3+, have made jewelry 3D printing accessible for independent designers as well as large casting houses.
“SLA resins have a reputation for being cheaper, but also less functional than wax. At Formlabs, we're looking to break that impression with products that are more foolproof and eliminate some of the extra work that’s still present in the jeweler's workflow,” Dudley said.
New, easy-to-use materials like Castable Wax 40 Resin are easing the learning curve, leading to greater adoption of the workflow and the subsequent expansion of the market.
3D printed jewelry is not just a matter of technology. The newer cohorts of jewelry designers entering the industry have started education with digital methods, including training on 3D printers, as opposed to the traditional ones.
“They're going to be looking for the printer that really meets their needs,” Dudley said. “I think then we'll start to see more adoption as they take over from the currently embedded user base.”
3D printing in jewelry has a bright horizon. With the wider industry adoption of workflow techniques, the arrival of new generations of designers skilled in them, and the creation of new, more foolproof materials and hardware, we're seeing the stage set for a major positive disruption.
Request a Jewelry Sample Part
Printing jewelry on a 3D printer - an overview of the most interesting models
The times when 3D printing of jewelry seemed like something fantastic is over. Today, more and more designers are using 3D equipment to bring their ideas to life. Some printers work with filament, others use powder, and still others print with liquid resin or wax. 3D printed jewelry looks and feels exactly like traditionally molded pieces.
Highlights
White and black Gemino & Orbis Nylon earrings printed in nylon resin using SLS technology. The material has a very light weight, which makes the jewelry comfortable, ideal for everyday wear. An interesting design will organically fit into both a classic and a shocking image.
3D printed wedding rings. Original custom-made symbols of eternal love accurately convey the details that are important for the newlyweds. With a unique asymmetrical line and elegant twists, Ray's ring will appeal to fans of the original designs. For lovers of clean, minimalist silhouettes, the Clio is the way to go. For connoisseurs of unconventional solutions, the Amar diamond ring will suit, the design of which forms a loose knot of two lines that merge, symbolizing an unbreakable union. nine0003
Gorgeous 3D printed face jewelry by Iris van Herpen. Cellchemy 3D printed jewelry designs look like a mask and the way it sits on the face of the wearer looks like something otherworldly. The wire masks are printed with a high resolution multi-material printer. Each part of the mask, custom-designed for a specific runway model, was created using a generative design process after a 3D scan of her face. nine0003
Guinness World Record-listed diamond ring. India's major 3D printing service provider Imaginarium helped Kotti Shrikant win the Guinness World Record for having the most diamonds set in a single ring. The process of developing a masterpiece called "Divine - 7801 Brahma Vajra Kamalam" went through several iterations. The design team chose the Himalayan camellia flower, which strikes the perfect balance between traditional and contemporary forms. Computer-aided design (CAD) was then used to calculate the number of diamonds. Imaginarium managed to make petals of gold and helped to set the intended number of stones. nine0003
18K Gold Charm 3D print by Elizabeth Landis. The spectacular pendant reminds of natural harmony and succinctly complements the luxurious look. Honeycombs are formed into an openwork pattern, and the figure of a bee symbolizes wisdom, diligence, purity.
Frog Ring 3D Gold Plated Brass Object by Peter Donders. The designer rejects classical forms and traditional solutions. He uses 3D printing to revolutionize the jewelry industry, be it in the areas of jewelry making or designing finishes. The frog ring emphasizes the grace, sense of humor of the fair sex. nine0003
A charming decoration that can effectively complement a creative look.
"Opposites" collection by Francesca Paolin "spring-summer 2015", printed in polyamide. The MA in Fashion Design from Domus Academy channeled her creativity into creating body jewelry from alternative materials using 3D technology. The author drew inspiration for the development of the collection from ancient history and culture.
Solar nylon bracelet. The Septem brand offers unique fashion items from designers around the world. All products are made on 3D printers. The customer can choose their favorite materials, colors, sizes from the list. The original bracelet attracts with its futuristic design and adds creativity to the image. nine0003
N-E-R-V-O-U-S necklace is a 3D printed necklace made up of 175 unique pieces. It is a 21st century piece of jewelry designed and manufactured using methods that did not exist until recently. The necklace is built in layers of durable yet flexible nylon using selective laser sintering technology. The design comes out of the printer fully assembled. The necklace attaches simply and securely with a hidden magnetic clasp.
Plumeria Nylon Earrings have a matte texture, ideal for original, bold looks. You can choose any color from 12 possible. Earrings with a floral pattern will appeal not only to young fashionistas, but also to elegant ladies.
Ide Bag Nylon is a stylish element of the look. A model that imitates openwork knitting will add charm to the ensemble, plus it will allow you to create a harmonious, feminine, exclusive look.
The Orbits Bracelet Nylon is your own galaxy on your wrist. 3D printed space-inspired jewelry is the choice of daring experimenters who are not afraid to try on new looks. Unusual material plus an innovative manufacturing method add enchantment and extravagance to the little thing. nine0003
Jewelry designers are constantly testing new materials and experimenting with different design approaches. Printing jewelry on a 3D printer has already become a popular production method. The technology allows you to implement bold ideas, make adjustments and see the results within a few hours.
Source
Tags:
3D printed jewelry, Orbits Bracelet Nylon, 3D printed space jewelry, Necklace by N-E-R-V-O-U-S - 3D printed necklace, 3D scan
Choice of technology and 3D printer for jewelry making, pros and cons
Currently, there are many new technologies that are designed to simplify production in various industries. Progress does not stand still and, despite some opponents, 3D printing has its own niche in the production of jewelry.
3D printing can speed up and reduce the cost of jewelry production due to the low cost of consumables. With 3D printers, jewelers have the ability to quickly change the design of a product and make prototypes at least several times a day. For many jewelry industries, 3D printing is becoming a good alternative or addition to milling machines and other equipment. nine0003
Until now, some believe that handmade is a sign of craftsmanship, especially when it comes to creative work, and models made using 3D modeling and printing are amateurish.
But many people forget that behind the computer is the same person who not only mechanically presses the buttons, but also puts his soul into his creation.
Benefits of 3D printing
In order to understand how justified the use of a 3D printer is, you need to know how jewelry is made. This is very painstaking work. No wonder the expression "jewelry work" appeared, denoting a very delicate and complex work. nine0003
Any decoration begins with a sketch. Usually several sketches are made in order to accurately determine the design and location of the inserts. Not only stones are used as decor, it can be elements made of wood, bone, precious metals, it all depends on the designer's imagination.
At the next stage, the product is drawn in a 3D editor. This allows not only to visualize the future product, but also to correct some errors and inaccuracies made at the design stage. nine0003
Ring model
Some craftsmen still carve "stencils" by hand.Such work requires certain skills and perseverance. Usually this is how products are made that will be cast in a single copy.
A finished 3D model can have several ways to be implemented in a physical version - this is milling or 3D printing.
Stencil milling
Currently, 3D printing is not much inferior in accuracy to a milling machine and often has a significant advantage in speed, despite the fact that after printing it is still necessary to separate the supports and clean up the points of contact with the model. Once a physical model has been obtained, it can be cast immediately if the material used is wax or a burnable polymer.
If it is necessary to cast a large batch of products, then a mold is made from the master model made with the help of special rubber for subsequent wax casting. There are many types of rubber that vary in hardness and curing temperature. Rubber is selected depending on the material from which the master model is made. nine0003
For pouring molds, a special machine is usually used - an injector. In some models, you can not only heat the wax, but also vacuum it or leave it under pressure. This helps to reduce the number and size of air bubbles for better pouring of the rubber mold.
In home workshops, silicone is used instead of special rubber. After all, a special machine is needed to vulcanize rubber. But rubber molds are too soft and short-lived for making a large batch of stencils. nine0003
After making the required number of stencils, they are collected in "Christmas trees". "Elks" are waxes soldered to a wax rod. To save space, the distance between them is very small and they resemble fluffy Christmas trees, hence the name. The finished Christmas tree is weighed to calculate the required amount of metal. In some places, stones are immediately inserted into the stencils, unless another mounting option is provided.
nine0003
Stencil Christmas trees
Ready "Christmas trees" are placed in a special cylindrical "cassette" without a bottom, which is called a flask, and filled with a gypsum-based molding mass. The flask with uncured gypsum must be evacuated to get rid of unnecessary air bubbles that can lead to defects on the surface of the finished casting.
After hardening, the gypsum flask is sent to a muffle furnace to melt the wax. nine0003
The calcination mode is selected depending on the material of the wax. For wax or burnout polymer, different modes are needed in order for the material to be completely removed from the gypsum!!!!!!
When all the wax is melted, cavities are formed inside the gypsum, repeating the contours of the wax. Metal is poured into these voids. After casting, the flask is cooled and the gypsum mold mass is washed out under the pressure of water. The result is a metal Christmas tree. nine0003
Herringbone after casting
Finished castings are cut from the Christmas tree and washed, polished, if necessary, blackened by the master until the desired appearance is achieved.
3D printers for jewelers
There are several 3D printing technologies that may be suitable for the needs of jewelers. Each has its pros and cons. Some 3D printers are ideal for a large workshop, and some are ideal for a small workshop. nine0003
SLA
SLA or stereolithography is based on the principle of layer-by-layer solidification of a photopolymer resin under the action of a UV beam. The UV beam is focused by means of mirrors on the surface of the resin and illuminates the model in layers.
How the SLA Printer Works
SLA 3D printers were the first to be noticed by jewelers. SLA devices are compact, while they have high printing accuracy. nine0003
Pluses and minuses
pros
Minuses
Print examples
From prototype to finished product
Cast and printed ring
Rating of printers.
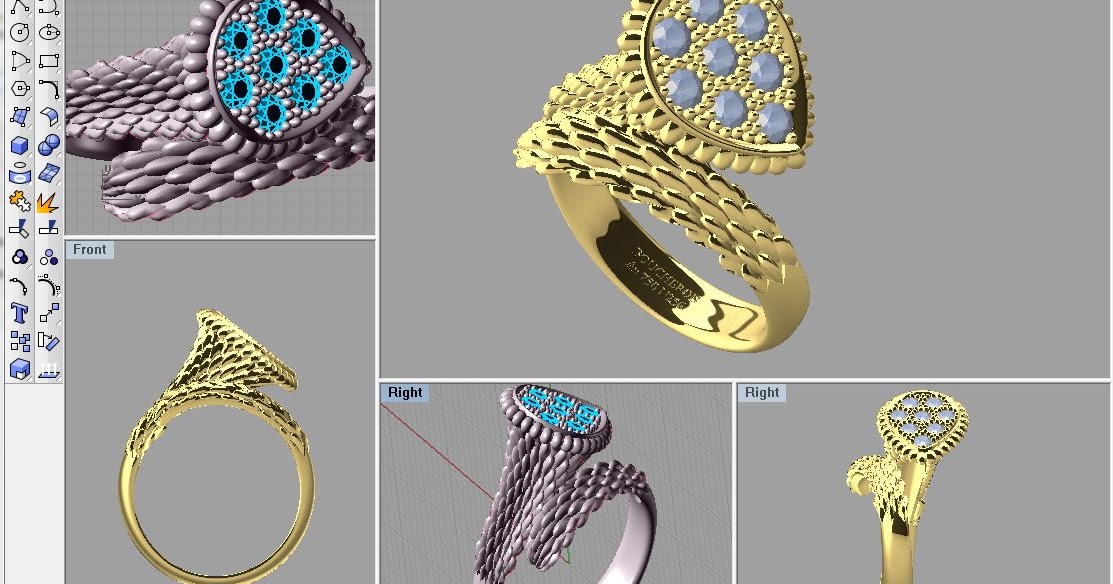
Leadership among the production of SLA 3D printers is held by Formlabs.
Formlabs Form 3
Formlabs Form 3
Specifications:
XY resolution: 25 µm
Laser spot size: 85 µm
Laser power: One 250mW laser
Working area size: 14.5×14.5×18.5cm
Layer thickness: 25 – 300 µm
A professional 3D printer that is popular with professional jewelers and dentists. nine0003
Formlabs Form 3L
Formlabs Form 3L
Specifications:
XY resolution: 25 µm
Laser spot size: 85 µm
Laser power: One 250mW laser
Working area size: 33.5×20×30cm
Layer thickness: 25 – 300 µm
Form 3L differs from younger models in its large print area, which allows you to produce truly large products without losing quality and accuracy. nine0003
DLP/LCD
DLP is very similar to SLA, only as a source of UV radiation, to illuminate the photopolymer resin, not a directed beam of light is used, but a DLP projector. DLP printers illuminate the entire work area at once, so they greatly outperform SLA in print speed.
How a DLP Printer Works
Today it is one of the most affordable photopolymer 3D printing technologies. In terms of cost, LCD printers have caught up with the price level of amateur FDM. DLP printers are much more expensive due to the use of an expensive projector as a UV source. nine0003
The projector is of course more expensive, but more durable, on the other hand, the LCD display is not so expensive and can be easily seen, unlike the projector. What to choose each user decides for himself.
Pros and cons.
pros
Minuses
Print examples
Comparison between 3D printed master model and molded part
nine0095
Burnout resin model and finished product
Demonstration of products cast with burnout resin
Rating of printers.
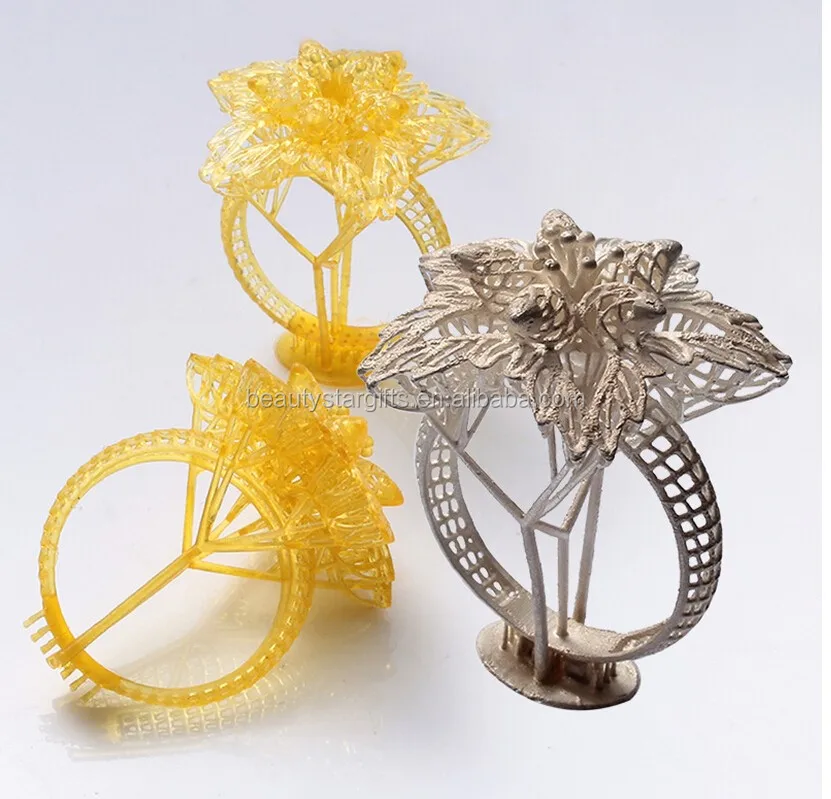
The print accuracy of LCD printers depends on the pixel size, so you should pay attention to this parameter when choosing a printer.
Anycubic Photon Mono
Anycubic Photon Mono
Specifications:
LCD display resolution: 2560x1620 (2K)
XY Positioning Accuracy: 0.051mm
UV wavelength: 405 nm
Working area size: 130x80x165 mm
Layer thickness: 0.01-0.15mm
The Anycubic Photon Mono is an inexpensive LCD machine ideal for hobby printing. The monochrome display allows you to reduce the exposure time and speed up printing. nine0003
Phrozen Sonic 4K
Phrozen Sonic 4K
Specifications:
LCD resolution: 6.1" 4K Mono LCD
XY positioning accuracy: 35 microns
UV wavelength: 405 nm
Working area size: 134x75x200 mm
Layer thickness: 0.01-0. 30mm
Phrozen Sonic 4K is specifically designed for use in the dental and jewelry industry. Despite its compact size, the printer is not inferior to professional machines in accuracy, and the exposure time of one layer is only a few seconds. nine0003
Phrozen Sonic Mighty 4K
Phrozen Sonic Mighty 4K
Specifications:
LCD resolution: 9.3" 4K Mono LCD
XY positioning accuracy: 52 microns
UV wavelength: 405 nm
Working area size: 200x125x220 mm
Layer thickness: 0.01-0.3mm nine0003
Phrozen Sonic Mighty 4K is a professional device with a large print area. This allows you to quickly produce small batches of models.
Phrozen Sonic XL 4K
Phrozen Sonic XL 4K
Specifications:
LCD resolution: 8.9" 4K Mono-LCD
XY positioning accuracy: 50 microns
UV wavelength: 405 nm
Working area size: 190x120x200 mm
Layer thickness: 0. 01-0.3mm
The Phrozen Sonic XL 4K is a professional machine with a large print area and a high resolution monochrome LCD display. This allows you to quickly produce batches of products with high accuracy.
Peopoly Phenom XXL
Peopoly Phenom XXL
Specifications:
LCD display resolution: 3840x2160 (23.8", 16:9, UHD 4K)
XY positioning accuracy: 137 µm
UV wavelength: 405 nm
Working area size: 527x296x550 mm
Layer thickness: 0.01-0.3mm
The Peopoly Phenom XXL is a device with a huge build area, which is ideal for serial production of not only jewelry. nine0003
Phrozen Sonic MEGA 8K
Phrozen Sonic MEGA 8K
Specifications:
LCD resolution: 15" 8K Mono LCD
XY Positioning Accuracy: 43 µm
UV wavelength: 405 nm
Working area size: 330 x 185 x 400 mm
Layer thickness: 0. 01-0.3mm
This is the first LCD printer with 8k monochrome matrix resolution, and a huge working area allows you to produce large batches of products in one print.
MJM/MJP
MJM (or similar PolyJet technology) is a technology for layering photopolymer or wax through many fine nozzles. Typically, the print head is located from 96 to 448, depending on the printer model.
If a photopolymer is used as a material, it is immediately cured by a UV lamp, which is located on the printer's head. nine0003
How the MJM printer works
In addition to photopolymer, MJM 3D printers can use wax as a material for printing.
MJM printers can print multiple materials at the same time. This allows you to print complex models with soluble or investment supports. This makes it possible to produce complex models with a smooth surface quickly and easily.
Pluses and minuses
pros
-
Ability to print multiple materials at the same time.
This means that another, soluble material can be used as a support. This allows you to save a lot of time on removing the support from the finished model and cleaning up the places where the supports come into contact with the print.
Minuses
-
To install the printer, most likely, you will need a separate room. 3D printers based on MJM technology are quite bulky in their dimensions, this is not a device that can simply be placed on a desktop or nightstand. nine0003
Print examples
Seal of a lot of stencils
Wax printed ring
Master models made on the MJM printer
Lot of jewelry stencils for further casting
Printer rating
FlashForge WaxJet 410
FlashForge WaxJet 410
Specifications:
Materials: Wax, support material.